1. 개요:
- 제목: 고압 다이캐스팅 제품의 결함 분류 제안 (PROPOSAL OF A CLASSIFICATION OF DEFECTS OF HIGH-PRESSURE DIECAST PRODUCTS)
- 저자: E. Gariboldi, F. Bonollo, M. Rosso
- 발행 연도: 2007년
- 발행 저널/학회: la metallurgia italiana
- 키워드: 고압 다이캐스팅, 결함, 분류 (high-pressire die-casting, defects, classification)
2. 연구 배경:
- 연구 주제의 사회적/학문적 맥락:
본 논문은 이탈리아 금속 협회(Italian Association of Metallurgy)의 TC "고압 다이캐스팅(High pressure diecasting)" 내 WG "고압 다이캐스팅(HPDC) 제품 품질(Quality of High Pressure DieCast (HPDC) products)"의 현재 활동 중 하나에 대한 소개를 제공합니다. 이 WG의 주요 목표 중 하나는 주조 공장에서 적절하고 비교 가능한 품질 표준을 정의할 수 있도록 공통 도구를 개발하고 보급하는 것입니다. 결함은 다이캐스팅 부품의 중요한 특징으로 인식되며, 그 특성과 기능에 상당한 영향을 미칩니다. 알루미늄 저압 및 고압 다이캐스팅 제품에서 결함의 유병률은 여러 연구에서 보고되었습니다 [1, 2, 3, 4a, 5]. 이탈리아 주조 공장 47곳과 연간 193,000톤의 알루미늄 합금을 포함하는 "고압 다이캐스팅 제품 품질" WG의 통계 분석 [6]은 HPDC 제품의 경제적 중요성과 응용 분야를 강조했습니다 (그림 1a). 이 조사는 HPDC 산업에서 표준화된 품질 관리의 필요성을 강조했습니다. - 기존 연구의 한계:
금속 다이캐스팅 부품의 기존 문헌 및 산업적으로 채택된 결함 분류에 대한 초기 조사에서 중요한 한계가 드러났습니다. 즉, 기하학적 기반 접근 방식과 원인 기반 접근 방식이 혼합되어 있다는 것입니다. 이러한 혼합은 종종 일관성이 없고 다양한 주조 공장 및 응용 분야에 균일하게 적용하기 어려운 광범위한 하이브리드 분류를 초래합니다. 또한 기존 분류는 HPDC 제품과 관련된 특정 요구 사항 및 제어 작업을 적절하게 다루지 못할 수 있습니다. - 연구의 필요성:
품질 표준 정의를 위한 공통 도구의 준비 및 보급은 WG의 중요한 목표입니다. 본 논문에서 다루는 기본적인 도구는 HPDC 제품의 결함에 대한 공통 용어 및 분류 시스템입니다. 표준화된 분류는 다음과 같은 여러 가지 이유로 필수적입니다.- 주조 공장에서 적절하고 비교 가능한 품질 표준을 정의하고 구현할 수 있도록 합니다.
- 주조 공장, 고객 및 연구원 간의 결함에 대한 명확한 의사 소통을 용이하게 합니다.
- 결함 데이터 분석 및 결함 유형, 분포 및 원인 간의 상관 관계 식별을 위한 기반을 제공하여 궁극적으로 공정 개선 및 제품 품질 향상으로 이어집니다.
- 다이캐스팅 부품의 결함 식별 및 불합격에 대한 명확한 기준을 설정하여 주조 공장과 고객 모두에게 이익이 됩니다.
3. 연구 목적 및 연구 질문:
- 연구 목적:
주요 연구 목적은 HPDC 제품의 결함에 대한 포괄적인 다단계 하이브리드 유형 분류 시스템을 제안하는 것입니다. 이 시스템은 HPDC 부품의 결함을 식별, 분류 및 이해하기 위한 구조화되고 실용적인 프레임워크를 제공하여 궁극적으로 다이캐스팅 산업 내에서 품질 관리 및 표준화 개선에 기여하는 것을 목표로 합니다. 본 논문은 제안된 분류의 레벨 II에서 정의된 일반적인 결함 클래스를 소개하는 데 중점을 둡니다. - 주요 연구 질문:
- 주조 공장 간의 일관된 품질 표준 정의를 지원하기 위해 HPDC 제품의 결함을 어떻게 효과적으로 분류할 수 있습니까?
- 결함의 위치/기하학적 구조와 근본적인 야금학적 원인을 모두 고려하는 결함 분류 시스템에 가장 적합한 구조는 무엇입니까?
- 일상적인 품질 관리 작업에서 결함 식별 및 분석을 용이하게 하여 주조 공장에 실용적이고 사용자 친화적인 분류 시스템을 어떻게 설계할 수 있습니까?
- 산업 내에서 의사 소통과 이해를 개선하기 위해 HPDC 결함에 대한 공통 용어를 확립할 수 있습니까?
- 연구 가설:
명시적으로 공식적인 가설로 진술되지는 않았지만, 연구는 다음과 같은 암묵적 가설을 기반으로 합니다.- 결함 위치와 야금학적 원인을 모두 통합하는 다단계 하이브리드 분류 시스템은 기존의 혼합 접근 방식에 비해 HPDC 결함 분류에 대한 보다 포괄적이고 실용적으로 유용한 프레임워크를 제공할 것입니다.
- 표준화된 용어 및 분류 시스템은 의사 소통을 향상시키고, 데이터 분석을 용이하게 하며, HPDC 산업 내에서 보다 일관성 있고 비교 가능한 품질 표준 확립에 기여할 것입니다.
- 분류에서 야금학적 원인에 초점을 맞추면 결함의 근본 원인을 식별하고 다이캐스팅 공정에서 효과적인 시정 조치를 구현하기 위한 귀중한 출발점을 제공할 것입니다.
4. 연구 방법론
- 연구 설계:
본 연구는 기존 문헌 및 산업적으로 채택된 주조 부품의 결함 분류에 대한 초기 조사로 시작하여 다각적인 접근 방식을 사용했습니다. 그 후 여러 이탈리아 주조 공장의 귀중한 기여를 통합하여 WG "고압 다이캐스팅 제품 품질" 내에서 광범위한 논의가 이루어졌습니다. 반복적인 프로세스에는 기존 접근 방식의 식별된 요구 사항 및 한계를 기반으로 새로운 분류 시스템을 개선하고 개발하는 과정이 포함되었습니다. 제안된 분류는 이러한 협력적이고 분석적인 설계 프로세스의 결과로 제시됩니다. - 자료 수집 방법:
자료 수집은 주로 다음을 포함했습니다.- 문헌 검토: 다이캐스팅 및 관련 분야의 출판된 연구 및 기존 결함 분류 시스템을 조사합니다.
- 산업 조사: 알루미늄 합금 주조에 대한 고객 및 주조 공장 사양을 포함하여 주조 공장에서 현재 사용 중인 결함 분류에 대한 정보를 수집합니다.
- 전문가 자문: 주조 공장 및 학계의 다양한 전문 지식을 대표하는 WG 구성원의 의견과 피드백을 수집합니다. 이탈리아 주조 공장의 HPDC 생산에 대한 통계 분석 [6]은 산업 환경에 대한 귀중한 맥락과 데이터도 제공했습니다.
- 분석 방법:
분석 방법은 주로 질적이었으며 다음 사항에 중점을 두었습니다.- 비교 분석: 다양한 기존 결함 분류 접근 방식을 분석 및 비교하고, 강점과 약점을 식별하고, 공통 주제와 하이브리드 방법론을 인식합니다.
- 시스템 종합: 문헌 검토, 산업 조사 및 전문가 자문에서 얻은 통찰력을 종합하여 새로운 분류 시스템을 개발합니다. 여기에는 분류를 여러 레벨로 구조화하고 결함 위치 및 야금학적 원인을 기반으로 범주를 정의하는 것이 포함되었습니다.
- 논리적 추론: 결함 원인, 발현 및 탐지 방법 간의 관계에 대해 추론하여 일관성 있고 실용적인 분류 프레임워크를 만듭니다.
- 연구 대상 및 범위:
본 연구는 알루미늄 합금으로 만든 고압 다이캐스팅(HPDC) 제품의 결함에 특별히 초점을 맞추었습니다. 범위는 야금학적 기반 결함으로 제한되었으며, 배출 후 작업(취급, 마감 및 가공)과 직접 관련된 결함은 제품 불합격에 대한 잠재적 기여도를 인정하더라도 분류에서 제외되었습니다. 분류는 이탈리아 다이캐스팅 산업 내의 광범위한 HPDC 부품 및 생산 시나리오에 적용하는 것을 목표로 합니다.
5. 주요 연구 결과:
- 주요 연구 결과:
연구의 주요 결과는 제안된 HPDC 제품 결함의 다단계 하이브리드 유형 분류이며, 그림 5 (이탈리아어 버전) 및 그림 6 (영어 버전)에 개략적으로 설명되어 있습니다. 이 분류 시스템은 세 가지 레벨로 구성됩니다.- 레벨 I: 결함 위치 (기하학적/위치 접근 방식): 결함은 구성 요소 내 위치와 탐지에 사용되는 일반적인 제어 작업을 기반으로 초기 그룹화됩니다. 이 레벨은 세 가지 광범위한 범주를 정의합니다.
- 내부 결함 (DIFETTI INTERNI / INTERNAL DEFECTS): 주조물의 벌크 내부에 위치한 결함.
- 표면 결함 (DIFETTI SUPERFICIALI / SURFACE DEFECTS): 표면 특징에 영향을 미치기에 충분히 가까운 표면 결함을 포함하여 주조물의 표면에서 관찰 가능한 결함.
- 기하학적 결함 (DIFETTI DI GEOMETRIA / GEOMETRAL DEFECTS): 주조물의 의도된 모양 및 치수에서 벗어난 것과 관련된 결함.
- 레벨 II: 야금학적 원인 접근 방식: 결함은 일반적인 야금학적 원인에 따라 클래스로 추가 분류됩니다. 내부 및 표면 결함 모두에 대해 유사한 클래스가 정의되어 공유된 원인을 강조합니다. 이러한 클래스에는 다음이 포함됩니다.
- 수축 결함 (Difetti da ritiro / Shrinkage defects): 응고 중 재료 부피 수축과 관련됨.
- 가스 관련 결함 (Difetti da gas / Gas-related defects): 가스 존재(예: 수소, 공기 혼입)와 관련됨.
- 충전 관련 결함 (Difetti di riempimento / Filling-related defects): 다이 충전 중 잘못되었거나 비정상적인 액체 금속 흐름과 관련됨.
- 원치 않는 상 (Fasi indesiderate / Undesired phases): 원하는 미세 구조와 다른 상의 존재와 관련됨.
- 열 수축 결함 (Difetti da contrazione termica contrastata / Thermal contraction defects): 응고 및 냉각 중 열 응력과 관련됨.
- 금속/다이 상호 작용 결함 (Difetti da interazione metallo/stampo / Metal/die interaction defects): (표면 결함만 해당) 용융 금속과 다이 재료 간의 상호 작용과 관련됨.
- 레벨 III: 특정 결함: 이 레벨은 각 레벨 II 클래스 내에서 특정 결함 유형에 대한 자세한 용어 및 정의를 제공합니다. 용어는 종종 야금학적 원인을 더욱 구체적으로 명시합니다. 예시는 다음과 같습니다.
- 레벨 II: 가스 관련 결함; 레벨 III (내부): 수소 기공, 공기/증기/다이 윤활제 혼입 기공.
- 레벨 II: 충전 관련 결함; 레벨 III (표면): 흐름 결함 (맥, 기공) 라미네이션, 냉간 접합.
- 레벨 II: 수축 결함; 레벨 III (내부): 수지상 간/층상 기공/블로우홀.
- 레벨 II: 금속/다이 상호 작용 결함; 레벨 III (표면): 침식, 이젝터 마크, 납땜, 다이 부식, 캐비티 빌드업.
- 레벨 I: 결함 위치 (기하학적/위치 접근 방식): 결함은 구성 요소 내 위치와 탐지에 사용되는 일반적인 제어 작업을 기반으로 초기 그룹화됩니다. 이 레벨은 세 가지 광범위한 범주를 정의합니다.
- 통계적/질적 분석 결과:
- 그림 1: 통계 분석 [6]에서 얻은 데이터를 보여줍니다.
- 그림 1a: Al 합금 HPDC 제품의 다양한 응용 분야에 대한 이탈리아 및 해외 시장의 매출액. 자동차 부문이 매출액의 상당 부분을 차지하고, 그 다음으로 전기 기계 및 가정용 기기가 뒤따릅니다.
- 그림 1b: 5가지 다이캐스팅 부품 제품군 간의 HPDC 생산 (원자재) 분포. "이전 제품군에 속하지 않는 기타 다이캐스팅"이 가장 큰 부분 (48.8%)을 차지하고, 그 다음으로 "얇은 벽 (0.8~3mm) 다이캐스팅" (23.2%) 및 "안전 부품용 다이캐스팅" (12.3%)이 뒤따릅니다.
- 그림 2: 두 가지 다른 HPDC 제품군 [6], 즉 "얇은 벽 (0.8~3mm) 다이캐스팅"과 "안전 부품용 다이캐스팅"에 대한 요구 사항 및 제어 방법을 보여줍니다. 압력 밀폐성, 안전성, 외관, 기계적 특성, 기공 부재 및 치수 요구 사항과 같은 요구 사항의 중요성이 제품군마다 다름을 강조합니다. 이에 따라 사용되는 제어 방법 (파괴 시험, 침투 탐상 시험, 압력 밀폐성, 치수 제어, X선, 외관 검사)도 강조점이 다릅니다.
- 그림 3: HPDC 제품의 불합격 원인 분석 결과 [7]를 보여줍니다. 불합격의 상당 부분이 가공된 표면의 육안으로 감지된 결함 (52%)과 가압 누출 시험 불합격 주조물 (28%)에 기인합니다. 분석은 가공 작업 중 불합격을 유발하는 결함과 가공/조립 중 파손을 유발하는 결함의 야금학적 원인을 추가로 분류하여 가스 기공, 냉간 접합 및 수축 기공의 유병률을 강조합니다. 예를 들어, 가스 기공은 가공 중 문제 발생 주조물 (75%), 가공 또는 조립 중 파손된 주조물 (85%) 및 육안으로 감지된 결함 (57.1%)의 주요 원인으로 확인되었습니다.
- 그림 4: 기존 결함 분류의 예시를 제시합니다.
- 그림 4a: Campbell [8]에 따른 주조 결함 분류. 이 분류는 결함을 가스 기공, 수축 기공 및 열간 균열, 균열로 광범위하게 분류합니다.
- 그림 4b: Cocks [9]에 따른 경합금 주조 결함 분류. 이 분류는 표면 결함 (냉간 접합, 매끄러운 불규칙성, 거친 표면) 및 내부 결함 (가스 기공, 수축 기공)으로 결함을 분류하고 각 범주 내에서 하위 유형을 추가로 분류하여 더 자세합니다.
- 그림 5 & 6: 제안된 HPDC 결함 분류를 각각 이탈리아어 및 영어 버전으로 제시하여 3단계 분류와 각 범주 내 결함 유형의 예시를 간략하게 설명합니다.
- 그림 1: 통계 분석 [6]에서 얻은 데이터를 보여줍니다.
- 데이터 해석:
제안된 분류 시스템은 다음과 같은 방식으로 주조 공장에 실질적인 관련성을 갖도록 설계되었습니다.- 레벨 I (위치): 일반적인 검사 작업과 결함 위치에 따른 기능적 영향 고려와 일치합니다.
- 레벨 II (야금학적 원인): 결함의 근본 원인에 대한 통찰력을 제공하여 공정 최적화 및 시정 조치를 위한 출발점을 제공합니다.
- 레벨 III (특정 결함): 정확한 결함 식별 및 의사 소통을 위한 자세하고 표준화된 용어를 제공합니다.
불합격 원인 분석 (그림 3)은 HPDC 제조에서 제품 불합격을 줄이기 위해 야금학적 결함, 특히 가스 기공, 수축 기공 및 냉간 접합을 해결하는 것의 중요성을 강조합니다. 기존 분류 (그림 4)는 보다 구조화되고 포괄적인 시스템의 필요성을 보여주며, 제안된 다단계 분류가 이를 제공하는 것을 목표로 합니다.
- 그림 이름 목록:
- 그림 1: a) Al 합금 HPDC 제품의 다양한 응용 분야에 대한 이탈리아 및 해외 시장의 매출액; b) 5가지 다이캐스팅 부품 제품군 간의 HPDC 생산 (원자재) 분포. [6].
- 그림 2: 두 가지 다른 HPDC 제품군에 대한 요구 사항 (상단) 및 제어 방법 (하단) [6].
- 그림 3: HPDC 제품의 불합격 원인 분석 결과 [7].
- 그림 4: Campbell 8 및 Cocks 9에 따른 주조 결함 분류.
- 그림 5: 제안된 HPDC 결함 분류 (이탈리아어 버전).
- 그림 6: 제안된 HPDC 결함 분류 (영어 버전).
- 그림 7: 가스 관련 내부 및 표면 결함의 예시.
- 그림 8: 충전 관련 내부 및 표면 결함의 예시.
- 그림 9: 수축 관련 내부 및 표면 결함의 예시.
- 그림 10: 금속/다이 상호 작용 표면 결함의 예시.
![Fig1. a) Fatturato relativo al mercato italiano ed estero nei diversi settori di applicazione dei prodotto pressocolati in lega di alluminio. b) Ripartizione dell’Impiego di lega di alluminio nelle 5 famiglie di getti pressocolati [6].](https://castman.co.kr/wp-content/uploads/Fig1.-a-Fatturato-relativo-al-mercato-italiano-ed-estero-nei-diversi-settori-di-applicazione-dei-prodotto-pressocolati-in-lega-di-alluminio-1024x317.webp)
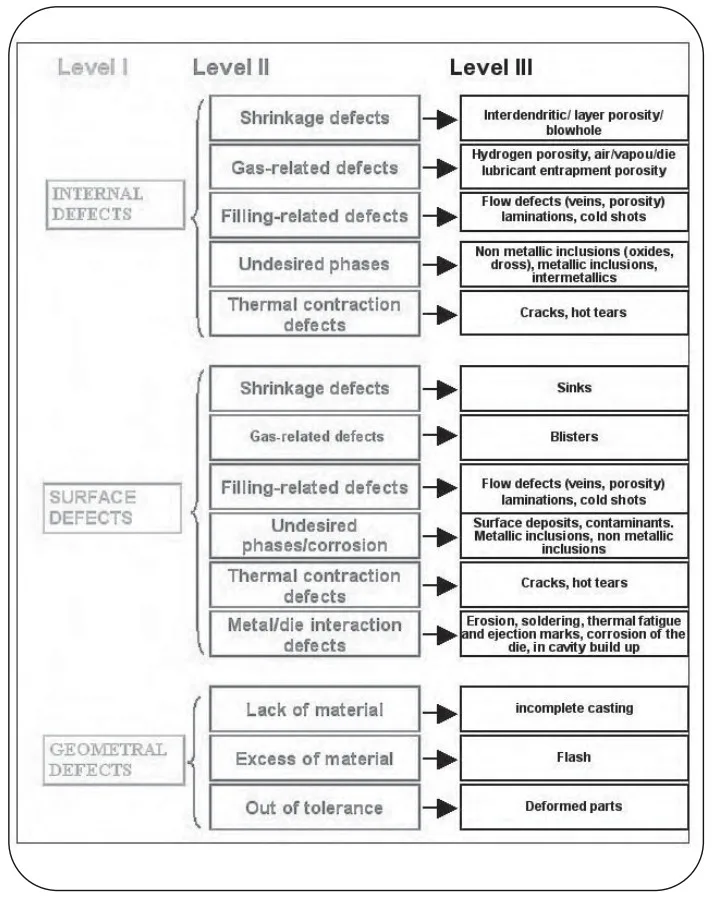
Classificazione proposta per difetti in getti pressocolati (versione inglese).
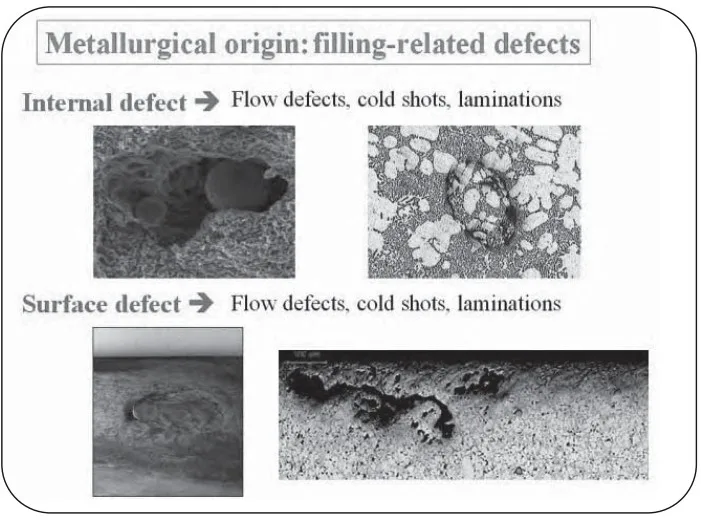
6. 결론 및 논의:
- 주요 결과 요약:
본 논문은 HPDC 제품의 결함에 대한 다단계 하이브리드 분류 시스템을 성공적으로 소개합니다. 이 시스템은 레벨 I에서 위치 (내부, 표면, 기하학적 구조)별로, 레벨 II에서 야금학적 원인 (가스 관련, 수축 관련, 충전 관련, 열 수축, 원치 않는 상, 금속/다이 상호 작용)별로, 마지막으로 레벨 III에서 특정 결함 유형에 대한 자세한 용어를 제공하여 결함을 분류합니다. 제안된 분류는 기존의 혼합 접근 방식의 한계를 해결하고 HPDC 산업에 보다 구조화되고 실용적인 도구를 제공하는 것을 목표로 합니다. - 연구의 학문적 의의:
본 연구는 HPDC 제품의 결함을 이해하고 분류하기 위한 체계적이고 포괄적인 프레임워크를 제공함으로써 학문 분야에 기여합니다. 기존 문헌에서 확인된 격차를 해결하고 단순한 기하학적 기반 또는 원인 기반 분류를 넘어 두 관점을 모두 통합하는 하이브리드 접근 방식을 제안합니다. 또한 이 연구는 다이캐스팅 연구 커뮤니티 내에서 결함 용어의 표준화에 기여합니다. - 실용적 의미:
제안된 분류 시스템은 HPDC 산업에 상당한 실용적 의미를 갖습니다. 주조 공장에 다음과 같은 귀중한 도구를 제공합니다.- 일관된 품질 표준 정의 및 구현.
- 결함 식별 및 의사 소통 개선.
- 결함 데이터를 분석하여 근본 원인을 식별하고 생산 공정 최적화.
- 결함 불합격에 대한 명확한 기준 설정으로 주조 공장과 고객 모두에게 이익.
- 결함 인식 및 예방과 관련된 교육 및 지식 공유 촉진.
- 연구의 한계:
본 논문은 제안된 분류가 결함/원인 상관 관계를 직접적으로 명시하지 않는다는 점을 인정합니다. 대신 결함의 야금학적 원인을 기반으로 잠재적 원인을 식별하기 위한 출발점을 제공합니다. 분류는 WG에서 개발 중인 제안으로 제시되며, WG의 활동은 다국어 용어 등가성을 마무리하고 공식 문서를 편집하기 위해 여전히 진행 중입니다. 더 넓은 산업 적용을 통한 추가 검증 및 개선이 예상됩니다.
7. 향후 후속 연구:
- 후속 연구 방향:
향후 연구 개발 노력은 다음 사항에 초점을 맞춰야 합니다.- 공식 문서 완성: 다국어 용어 등가성을 마무리하고 제안된 분류 및 용어 번역을 포함하는 공식 문서를 편집합니다.
- 산업 검증 및 개선: 제안된 분류를 산업 환경에서 구현 및 검증하여 실용성, 효과성을 평가하고 실제 적용을 기반으로 추가 개선이 필요한 영역을 식별합니다.
- 결함/원인 상관 관계 지침 개발: 특정 결함을 공정 매개변수 및 재료 특성과 연결하는 보충 자료 또는 데이터베이스 개발을 통해 결함/원인 상관 관계에 대한 보다 명시적인 지침을 포함하도록 분류 시스템을 확장합니다.
- 교육 자료 개발: 주조 공장에서 품질 관리 작업에 제안된 분류 시스템을 효과적으로 구현하고 활용할 수 있도록 교육 자료 및 리소스를 만듭니다.
- 추가 탐구가 필요한 영역:
다음 영역에서 추가 탐구가 필요합니다.- 다양한 결함 유형이 HPDC 부품의 기능적 성능에 미치는 영향 정량화.
- 제안된 분류를 기반으로 결함 탐지 및 특성화를 위한 표준화된 방법 개발.
- 스크랩률 감소 및 제품 품질 향상 측면에서 제안된 분류 시스템 구현의 경제적 이점 조사.
- 배출 후 작업 및 HPDC 제조 공정의 기타 측면과 관련된 결함을 포괄하도록 분류 시스템 확장.
8. 참고 문헌:
- [1] J.A. FRANCIS. G.M. DELPHINECANTIN. Mat. Sci. Eng., A407 (2005), p. 322.
- [2] C.H. CACARES, B.I. SELLING. Mater. Sci., A220 (1996) р. 109.
- [3] X. YANG, X. HANG, X. DAI, J. Campbell, R.J. Grant. Mater. Sci. Tech., 22 (2006) p. 561.
- [4] J. CAMPBELL. Castings. Butterworth Heinemann, Oxford, 2003. a) p. 204. b) p. 207.
- [5] E. DI RUSSO. "The atlas of microstructures of aluminium casting alloys", Edimet, Brescia 1993.
- [6] F. BONOLLO. Qualità dei getti pressocolati: I risultati di un'indagine svolta nelle fonderie italiane. AIM Seminar "Qualità del pressocolato", Piacenza, 12 April 2006.
- [7] 1, J. BREVICK, “Defect causing rejection of die-casting after machining". NADCA project summary. http://www.diecasting.org/research/results/pdf/ProcessTechnologies.pdf
- [8] J. CAMPBELL, R.A. HARDING. “Casting technology" in TALAT 2.0 cd-rom, EAA, Brossels (2000).
- [9] D.L. COCKS. A proposed simple qualitative classification for die-casting defects. Proceedings Die-casting Conference, Mountreaux, 1997.
- [10] F. BONOLLO, A. TIZIANI. Analisi difettologica di getti in lega leggera e in ghisa. Course AIM "Failure Analysis", Vicenza, 7-8 October 2003.
- [11] W.G. WALKINGTON. Die Casting defects – Causes and solutions, North American Die Casting Association; 1997.
- [12] E. GARIBOLDI. Classificazione di base dei getti pressocolati. Seminary AIM “Qualità del pressocolato: - la situazione attuale e le prospettive di una norma sulle condizioni di fornitura. Piacenza-12 Aprile 2006.
- [13] UNI EN 12258-1 Standard. Aluminiun and amuminium alloys -Terms and difinitions – general terms. February 2001.
9. 저작권:
- 본 자료는 E. Gariboldi, F. Bonollo, M. Rosso의 논문: 고압 다이캐스팅 제품의 결함 분류 제안 (PROPOSAL OF A CLASSIFICATION OF DEFECTS OF HIGH-PRESSURE DIECAST PRODUCTS)을 기반으로 합니다.
- 논문 출처: DOI URL (제공된 텍스트에서 DOI URL을 찾을 수 없습니다. )
본 자료는 위 논문을 기반으로 요약되었으며, 상업적 목적으로 무단 사용하는 것을 금지합니다.
Copyright © 2025 CASTMAN. All rights reserved.