본 논문 요약은 ['Surface & Coatings Technology']에서 발행한 ['Increasing the Lifespan of High-Pressure Die Cast Molds Subjected to Severe Wear'] 논문을 기반으로 작성되었습니다.
1. 개요:
- 제목: 고압 다이캐스팅 금형의 수명 연장: 심각한 마모 조건 하에서 (Increasing the Lifespan of High-Pressure Die Cast Molds Subjected to Severe Wear)
- 저자: V. Nunes, F.J.G. Silva, M.F. Andrade, R. Alexandre, A.P.M. Baptista
- 발행 연도: 2017년
- 발행 저널/학회: Surface & Coatings Technology
- 키워드: 마모 (Wear), 연마 (Abrasion), 침식 (Erosion), 고압 다이캐스팅 (High-pressure die casting), 금형 마모 (Mold wear), 마모 메커니즘 (Wear mechanisms), 금형 수명 (Mold lifespan)
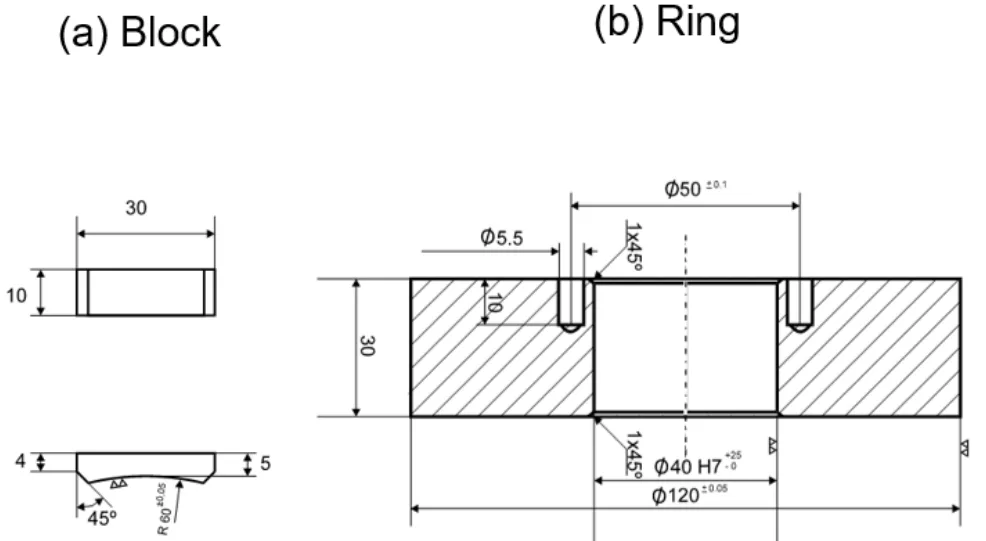
2. 초록 또는 서론
차량 부품에 복합 재료의 사용이 증가하고 있음에도 불구하고, 고압 다이캐스팅은 복잡한 형상의 자동차 부품을 비용 효율적으로 얻는 데 가장 유용한 제조 기술 중 하나로 남아 있습니다. 자동차 산업은 높은 생산 속도와 고품질의 제품을 요구하는 것으로 잘 알려져 있습니다. 따라서 생산 및 관리 측면을 최적화하기 위한 체계적인 접근 방식이 지속적으로 이루어지고 있습니다.
연료 펌프 본체, 스로틀 바디, EGR 밸브, 지지 브래킷 등과 같은 자동차 부품에 일반적으로 사용되는 알루미늄 합금은 일반적으로 높은 연마성을 나타내는 실리콘을 함유하고 있습니다. 고온 및 고속의 알루미늄 흐름은 금형에 심각한 마모를 유발하며, 이는 종종 연마 및 침식 효과의 조합으로 인해 발생합니다.
본 연구에서는 전형적인 심각한 마모 문제를 가진 두 개의 금형을 선정하여 관련된 마모 메커니즘을 심층적으로 연구했습니다. 그 후, 이 목적에 가장 적합한 코팅을 신중하게 선택하고 금형의 가장 중요한 부분에 코팅을 적용하여 코팅 적용의 잠재적인 효과를 테스트하고, 내마모 거동 및 관련된 마모 메커니즘을 분석했습니다. 병행하여 실험실 테스트와 산업 테스트 간의 상관 관계를 도출할 수 있는지 확인하기 위해 마찰학적 테스트도 수행했습니다. 주사 전자 현미경(SEM) 및 에너지 분산 분광법(EDS)을 집중적으로 사용하여 코팅 및 관찰된 마모 메커니즘을 특성화했습니다. 실험실 마찰학적 테스트는 각각 접촉면에 낮은 하중과 중간 하중을 가하기 위해 볼 스캐터링 및 블록-온-링 테스트를 포함했습니다. 특정 코팅이 이 응용 분야에서 다른 코팅보다 더 나은 거동을 나타낸다는 결론을 내릴 수 있는 유망한 결과가 얻어졌습니다.
3. 연구 배경:
연구 주제 배경:
차량 부품에 복합 재료의 통합이 증가하고 있음에도 불구하고, 고압 다이캐스팅은 복잡한 형상의 자동차 부품을 비용 효율적으로 얻는 데 여전히 가장 유용한 제조 기술 중 하나입니다. 그러나 이러한 부품을 생산하는 데 사용되는 금형은 고압, 급격한 온도 변동, 고속으로 이동하는 용융 금속으로부터의 침식과 같은 매우 가혹한 조건에 지속적으로 노출됩니다.
고압 다이캐스팅 공정에서 다음 단계들을 고려할 수 있습니다: 샷 슬리브 채우기, 고속 캐비티 채우기, 추가적인 고압 적용, 냉각 및 응고, 금형 개방 및 부품 배출, 새로운 사출 사이클을 위한 금형 냉각 및 해당 윤활 [1]. 일반적인 용융 금속 주입 속도는 20-60 m/s이며, 알루미늄 합금 유형에 따라 온도는 약 700°C입니다 [2]. 이러한 금형의 유지 보수 또는 교체에는 막대한 비용이 소요되므로 생산자들은 수명을 늘리기 위한 최상의 해결책을 찾아야 합니다.
산업 환경 및 작업 조건은 침식, 부식, 마모 및 열 피로와 같은 열간 금형강의 일부 파손 메커니즘을 유발할 가능성을 높입니다 [3].
기존 연구 현황:
지난 몇 년 동안 여러 연구가 다양한 유형의 파손 메커니즘을 이해하기 위해 진행되었습니다 [2, 4-7]. 다이에 알루미늄을 사출하는 것은 알루미늄 솔더링 메커니즘으로 인해 가장 가혹한 공정 중 하나입니다. 용융 알루미늄은 다이 표면과 화학 반응을 일으켜 알루미늄 다이캐스팅에서 파손 메커니즘을 유발합니다 [4, 8]. 이러한 이유로 금형 수명을 단축시키는 메커니즘을 방지하기 위한 코팅 개발에 대한 많은 연구가 진행되었습니다 [1, 3, 9-16].
세라믹 코팅은 일반적으로 열 균열 발생과 같은 일부 파손 메커니즘을 방지하는 데 사용됩니다. 그러나 다른 코팅도 금형 수명을 개선하는 데 기여할 수 있으며 비용이 이러한 종류의 응용 분야에서 가장 중요한 요소가 아닐 수 있습니다 [11].
1997년 Wang [14]은 코팅이 금형 수명을 어떻게 개선할 수 있는지에 대한 광범위한 연구를 발표했으며, 당시의 코팅, 즉 TiN, TiAlN 및 CrN을 사용하여 다양한 열간 금형강 및 마레이징강을 사용하여 용융 알루미늄 부식, 인성 저항, 경도 및 열 변화와 같은 다양한 측면을 분석했습니다.
이 연구를 통해 TiN은 낮은 산화 온도로 인해 좋은 해결책이 아니라는 것을 알게 되었으며, 코팅된 H13 또는 Marlok 강은 특히 충격 인성, 부식 및 침식 거동의 개선이 필요한 경우 고압 사출 성형에 고려될 수 있다고 결론지었습니다. 이 연구는 Park과 Kim [16]에 의해 뒷받침되었으며, 그들은 TiN이 500°C에서 산화되기 시작하는 반면, 다른 연구된 코팅(TiAlN 및 TiSiN)은 최대 700°C까지 훨씬 더 나은 산화 저항성을 보였다고 결론지었습니다. 또한 TiN은 600°C 이상의 온도에서 분해되는 경향이 있는 것으로 잘 알려져 있습니다 [17, 18].
이러한 최신 코팅은 우수한 기계적 특성을 나타냈지만, TiSiN은 중간 온도에 더 적합하고 TiAlN 코팅은 고온에 가장 적합합니다. 그러나 Dobrzanski 등이 수행한 테스트 [10]은 TiN 코팅이 실온에서 동일한 핀-온-디스크 테스트 조건에서 X37CrMoV5-1 유형의 열간 금형강보다 5배 더 큰 내마모성을 달성했다고 밝혔습니다.
유사한 연구가 Tentardini 등에 의해 수행되었습니다 [8]. 알루미늄 다이캐스팅과 관련하여 동일한 TiN 및 CrN 코팅을 사용했지만, 이번에는 H13 강과 Anviloy® 1150을 기판으로 사용했습니다. 이 연구자들은 CrN 코팅이 주조 공정에서 알루미늄 합금과의 솔더링 메커니즘과 관련하여 TiN 코팅보다 더 나은 거동을 나타낸다는 것을 발견했습니다.
더욱이 Guzilia 등 [1]은 솔더링 현상을 조사하여 TiN, CrN 및 TiCN 코팅을 사용하면 알루미늄 합금과 강철 금형 사이의 솔더링을 방지할 수 있으며, 금형 손상을 줄이고 급격한 열화를 방지하는 주조 알루미늄 합금의 축적층을 관찰할 수 있다고 결론지었습니다. 코팅은 용융 알루미늄과 금형 강철 표면 사이의 반응을 방지하는 물리적 장벽 역할을 하기 때문입니다. 또한 Heim 등 [12]은 알루미늄 다이캐스팅의 솔더링 현상을 연구하여 TiN, TiCN, TiBN 및 TiAlCN과 같은 코팅이 이러한 심각한 문제를 방지한다는 결론을 내렸습니다.
동일한 코팅을 기반으로 일부 새로운 코팅 구조가 테스트되었으며, 특히 다층 코팅 [19]을 사용했습니다. 서로 다른 층은 열 장벽(외부 층 – 희토류 산화물 코팅), 확산 장벽(중간 층 – TiAlN 코팅) 및 얇은 접착층(내부 층 – Ti 코팅)과 같은 서로 다른 역할을 가정하도록 의도되었습니다. 이러한 방식으로 기판의 열 피로 저항성은 액체 알루미늄으로 4000회 열 사이클 후 관찰할 수 있듯이 크게 향상되었습니다.
Bobzin 등이 유사한 접근 방식을 수행했습니다 [20]. AISI H11 강철 기판에 다층 CrN/AlN/Al2O3 코팅을 테스트했으며, Al2O3가 최상층입니다. 또한 산업용 테스트를 포함하여 동일한 테스트 조건에서 두 가지 산업용 코팅이 연구에 사용되었습니다. 알루미늄 다이캐스팅 기계에서 5884회의 알루미늄 샷을 사용한 산업용 테스트가 포함되었습니다. CrN/AlN/Al2O3는 다른 코팅에 비해 흥미로운 거동을 보였으며 금형 수명을 크게 개선했습니다. 코팅의 상 변형은 금형에서 도달한 온도에 기인하는 것으로 보고되었습니다.
그러나 Muller [15]가 연구한 약간 다른 접근 방식은 금형 표면의 플라즈마 질화 전처리, TiBN, CrN 및 W-C:H 필름과 같은 PVD 또는 PACVD 코팅을 사용했으며, 플라즈마 질화 전처리가 동일한 PVD 또는 PACVD 코팅을 점선으로 표시한 표면에 비해 표면 거시 경도 및 임계 하중을 상대적으로 개선한다고 결론지었습니다.
반면에 Rodríguez-Baracaldo [21]는 질화 전처리와 (Ti0.7Al0.3)N 코팅의 조합을 연구하여 두 개의 질화 전처리된 강철과 (Ti0.6Al0.4)N 코팅만 제공된 다른 강철과 비교하여 상온 및 고온(600°C)에서 마모 테스트를 수행했습니다.
상온에서는 마모 거동에 큰 차이가 없었지만, 고온에서는 질화 전처리된 강철이 (Ti0.6Al0.4)N 코팅으로 제공된 강철이 사전 처리되지 않은 강철과 비교하여 최상의 마모 거동을 보였으며, (Ti0.6Al0.4)N 코팅으로 코팅된 사전 처리되지 않은 강철은 최악의 마모 거동을 보였습니다. 또한 Tomaslewski 등이 조사한 다른 접근 방식 [22]은 AISI M2 동급 고속도강을 기판으로 사용하여 Mo를 TiAlN과 함께 공동 증착했습니다. 얻어진 준 다층은 TiAlN/(TiAl)1-x - MoxN으로 Mo 함량이 약 8%이며, 강철에 대한 마찰 계수를 0.8에서 0.5로 개선하고 마모율을 10^15 m³/N·m 미만으로 감소시켰습니다.
이 연구는 TiAlN의 별개의 층과 Mo 층이 혼합된 순수 다층 시스템에 대한 다른 저자들의 유사한 접근 방식에 선행되었습니다 [23-25]. 보다 최근에는 Reenwinkel 등이 수행한 또 다른 연구 [26]에서 TiAlN 및 WNx의 탄성 특성에 대한 TiAlN-WNx 코팅의 탄성 특성을 다양한 농도로 사용하여 연구했습니다.
이 연구는 W의 농도가 높을수록 영률이 낮아진다는 것을 보여주었으며, 이는 마모 거동으로 외삽될 수 있습니다.
보다 최근에는 다른 고급 코팅이 내마모성 개선과 관련하여 연구되었습니다. Park 등 [27]은 TiB2 증착 전 H13 강철의 질화 전처리의 영향을 연구했습니다. 그들은 이 질화 공정에 의해 코팅의 기판에 대한 접착력이 30 N보다 높은 값으로 증가했지만 경도는 20-30 GPa 사이의 값으로 감소했다고 결론지었습니다.
그러나 이 전처리는 코팅과 기판의 경도 차이로 인해 고경도(>60 GPa) 코팅에는 적용할 수 없으므로 고경도 코팅의 접착력을 개선하기 어렵습니다. TiB2 유사 코팅은 다른 저자들에 의해 연구되었으며 [28], 이러한 코팅은 해당 작업(미세 연마 마모 테스트 구성)에 사용된 테스트 조건과 관련하여 매우 우수한 접착력과 내마모성을 나타낸다고 결론지었습니다.
더욱이 Maaza 등 [29, 30]은 Ni 및 B4C와 같은 일부 다른 원소 또는 화합물의 확산을 감소시키려고 시도했습니다. Ti에 다양한 표면 처리를 사용하여 일부 표면 다층 시스템에서 사용했습니다.
플라스틱 사출 금형은 코팅 과학에 대한 몇 가지 과제를 나타내며, 주로 유리 섬유 팁에 의해 촉진되는 연마를 고려하여 유리 섬유 강화 플라스틱(GFRP) 사출에 사용되는 금형입니다. 그러나 이러한 경우 알루미늄 사출에서와 동일한 문제는 없는데, 이는 일반적으로 알루미늄 합금을 용융하는 데 사용되는 온도가 플라스틱 재료에 비해 상당히 높기 때문입니다 [31].
이 분야에서 TiAlSiN [32] 및 TiAlCrSiN [33]과 같은 미세 연마 마모 테스트를 사용하여 보다 복잡한 코팅도 연구되었으며, 접착력 및 내마모성 측면에서 유망한 특성을 보였습니다. 그러나 이러한 경우 작동 온도는 고려 사항이 아니었습니다.
연구의 필요성:
기존 연구를 바탕으로 고압 다이캐스팅 금형의 수명을 향상시키고 가혹한 마모 조건에서 성능을 개선하기 위해 코팅을 탐색하고 최적화해야 할 필요성이 분명히 있습니다. 본 연구는 이러한 요구를 해결하기 위해 두 가지 다른 TiAlN 코팅을 비교하는 데 중점을 둡니다.
4. 연구 목적 및 연구 질문:
연구 목적:
본 연구에서는 고압 다이캐스팅 금형의 이동 부품 및 캐비티에 대한 적용 가능성과 관련하여 두 가지 다른 TiAlN 코팅(Ti0.4Al0.6N 및 Ti0.5Al0.5N)을 조사했습니다. 이러한 필름은 다양한 조건에서 마모에 저항하는 능력을 평가하기 위해 심층적으로 특성화되고 테스트되었습니다.
주요 연구 내용:
- 두 가지 다른 TiAlN 코팅(Ti0.4Al0.6N 및 Ti0.5Al0.5N)의 특성화.
- 고압 다이캐스팅을 시뮬레이션하는 조건에서 이러한 코팅의 내마모성 평가.
- 실험실 및 산업 환경 모두에서 두 TiAlN 코팅의 성능 비교.
- 알루미늄 합금과 코팅된 금형 사이의 마모 메커니즘 및 재료 이동 분석.
연구 가설:
본 논문에서는 연구 가설을 명시적으로 언급하지 않습니다. 그러나 암묵적으로 본 연구는 TiAlN 코팅의 조성에 따라 고압 다이캐스팅 응용 분야에서 내마모성 및 성능이 달라질 것이며, TiAlN 코팅이 다이캐스팅 금형의 수명을 개선할 수 있다는 가설을 테스트하는 것을 목표로 합니다.
5. 연구 방법론
연구 설계:
본 연구에서는 실험실 및 산업 환경 모두에서 두 가지 다른 TiAlN 코팅(Ti0.4Al0.6N 및 Ti0.5Al0.5N)을 서로 비교하고 코팅되지 않은 금형강과 비교하는 비교 실험 설계를 채택했습니다.
데이터 수집 방법:
- 실험실 마찰학적 테스트: 블록-온-링 마찰계 테스트를 수행하여 마모 및 마찰 거동을 시뮬레이션했습니다.
- 산업 테스트: TiAlN으로 코팅된 코어 핀을 실제 다이캐스팅 공정에서 30,000회 사출 사이클 동안 테스트했습니다.
- 재료 특성 분석:
- 주사 전자 현미경(SEM) 및 에너지 분산 분광법(EDS)을 사용하여 형태, 두께 및 조성 분석.
- 초미세 경도 시험(Fisherscope H100)을 사용하여 경도 및 영률 측정.
- 스크래치 테스트(CSM REVETEST)를 사용하여 접착력 평가.
- 프로필로미터(MAHR PERTHOMETER M2) 및 원자력 현미경(AFM)을 사용하여 표면 거칠기 특성화.
분석 방법:
- 정량적 분석: 코팅 두께, 경도, 접착 강도, 표면 거칠기, 마찰 계수 및 마모 부피 측정.
- 정성적 분석: SEM 및 EDS 분석을 사용하여 마모 흔적, 재료 이동 및 마모 메커니즘 분석.
- 비교 분석: 두 TiAlN 코팅의 성능 비교 및 실험실 테스트 결과와 산업 테스트 결과 간의 상관 관계 분석.
연구 대상 및 범위:
- 기판 재료: AISI H13 강철 (DIN X40CrMoV5-1).
- 코팅 재료: PVD로 증착된 Ti0.4Al0.6N 및 Ti0.5Al0.5N 코팅.
- 알루미늄 합금: A380 (AlSi9Cu3(Fe)) 및 A13 (AlSil2Cul(Fe)) 알루미늄-실리콘-구리 합금.
- 범위: 고압 다이캐스팅 금형용 TiAlN 코팅 평가, 내마모성 및 수명 개선에 중점.
6. 주요 연구 결과:
주요 연구 결과:
- 코팅 특성 분석: Ti40Al60N 및 Ti50Al50N 필름은 각각 약 3 µm 및 2 µm 두께의 단층 박막으로 증착되었습니다. 두 코팅 모두 균질했습니다.
- 표면 형태: Ti50Al50N 코팅이 Ti40Al60N보다 더 매끄러운 것으로 나타났습니다.
- 거칠기 분석: PVD 증착 후 거칠기는 기판에 비해 약간 감소했습니다. Ti50Al50N은 Ti40Al60N(0.066 µm 감소)보다 낮은 거칠기 값(0.02 µm 감소)을 보였습니다.
- 접착력: 두 코팅 모두 우수한 접착력을 보였습니다. Ti50Al50N은 Ti40Al60N(각각 31 N 및 47 N)에 비해 응집(33 N) 및 접착(49 N) 파손에 대한 임계 하중이 약간 더 높았습니다.
- 경도 및 영률: Ti40Al60N은 Ti50Al50N(각각 23.57 GPa 및 320.05 GPa)보다 높은 경도(33.63 GPa) 및 영률(469.88 GPa)을 보였습니다.
- 마찰학적 거동: 실험실 테스트에서 Ti40Al60N은 A380 및 A13 알루미늄 합금 모두에 대해 Ti50Al50N보다 낮은 마찰 계수를 나타냈습니다.
- 산업 테스트: Ti40Al60N으로 코팅된 코어 핀은 Ti50Al50N에 비해 30,000회 사출 사이클 후 마모가 덜했습니다. Ti50Al50N 코어 핀은 코팅 파손 및 더 심각한 마모의 증거를 보였습니다.
제시된 데이터 분석:
- SEM 및 EDS 분석을 통해 마모 트랙에서 알루미늄 합금이 Ti40Al60N 및 Ti50Al50N 코팅 모두의 표면으로 재료 이동이 발생했음을 확인했습니다.
- Ti50Al50N은 A380에 비해 A13 알루미늄 합금의 이동이 더 강하게 나타났으며, 이는 더 높은 야금학적 친화력을 시사합니다.
- Ti40Al60N은 표면이 약간 더 거칠었음에도 불구하고 더 나은 내마모성과 낮은 마찰을 나타냈으며, 이는 더 높은 경도와 영률에 기인합니다.
- 산업 테스트는 실험실 결과를 뒷받침하여 Ti40Al60N이 실제 다이캐스팅 조건에서 더 나은 성능을 보임을 나타냅니다.
그림 목록:
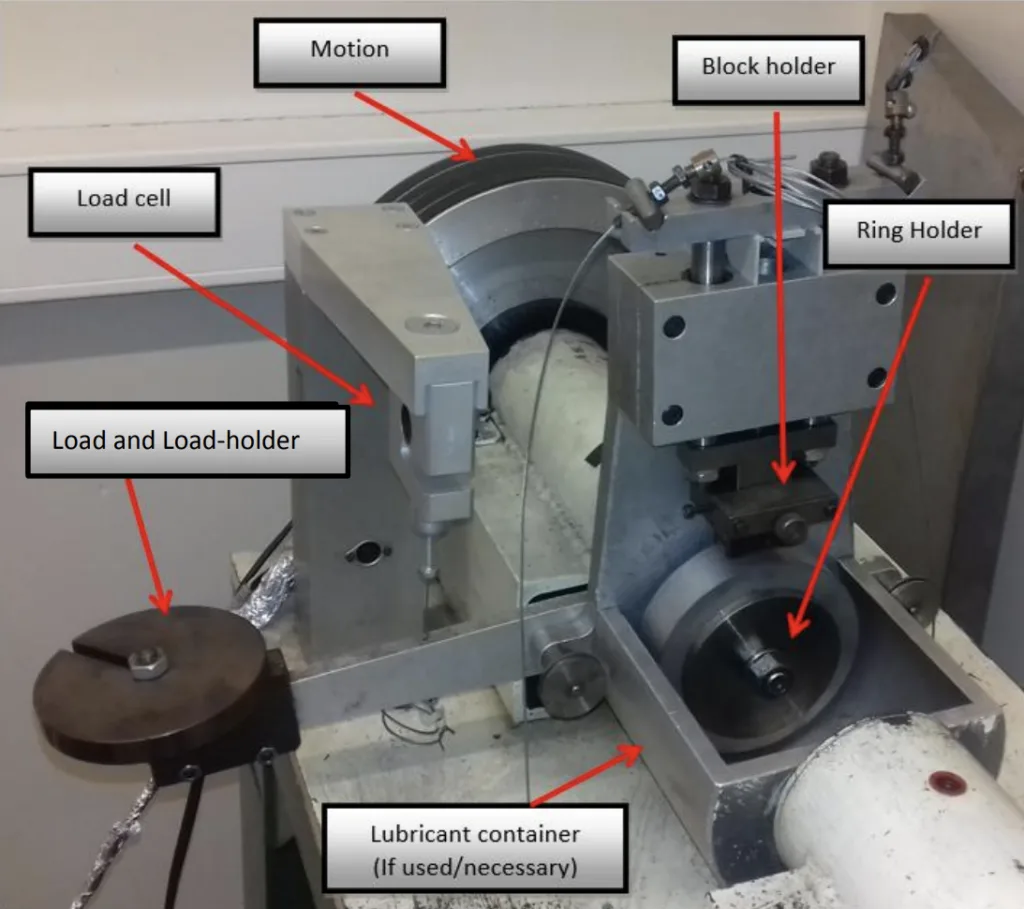

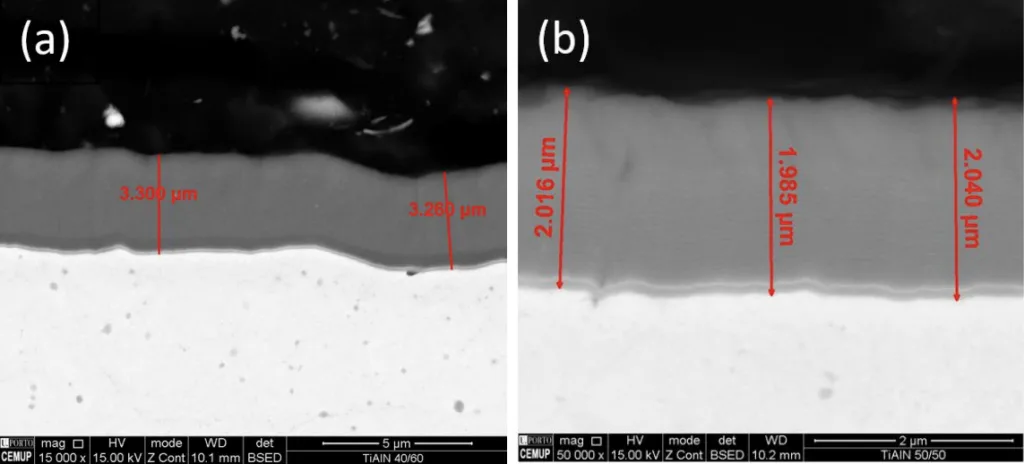
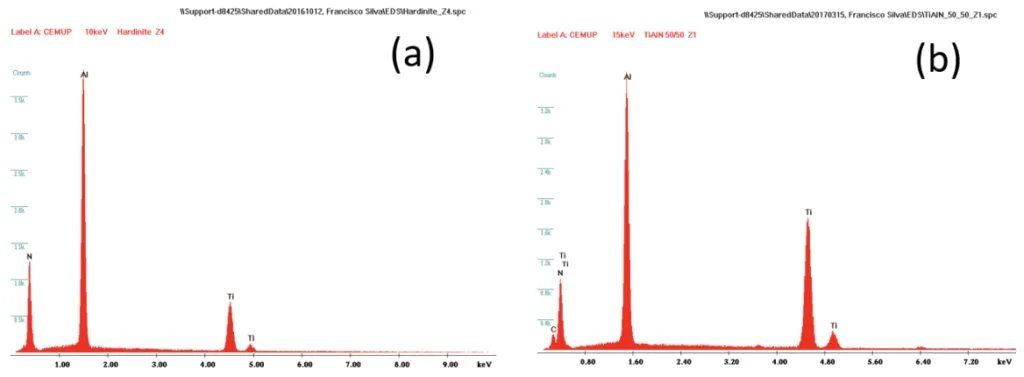
𝑇𝑖40𝐴𝑙60𝑁 and (b) 𝑇𝑖50𝐴𝑙50N
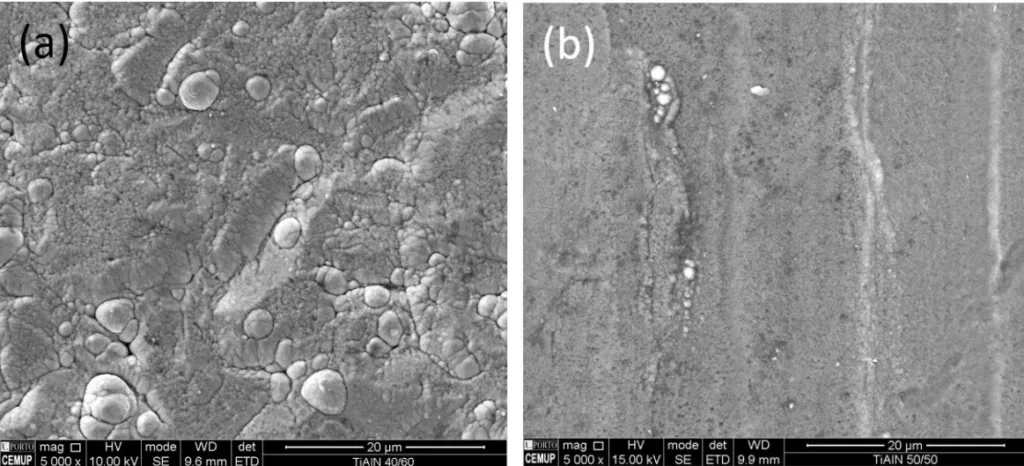
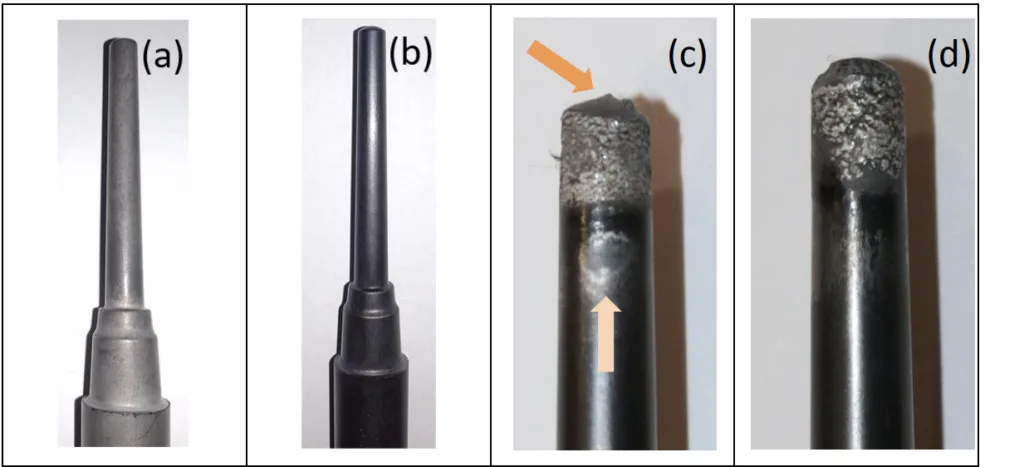
- Figure 1 - 블록 (a) 및 링 (b) 시편 형상 (Block (a) and ring (b) samples geometry)
- Figure 2 - 블록-온-링 마찰계의 모습 (View of the block on ring tribometer used in tribological tests)
- Figure 3 - 산업 테스트를 위해 코어 핀이 조립된 금형의 모습 (View of the mold were the core pins were assembled for industrial tests)
- Figure 4 - 코팅 두께 측정을 위한 코팅의 단면도 (Ti40Al60N (a) 및 Ti50Al50N (b)) (Cross-section views of the coatings (Ti40Al60N (a) and Ti50Al50N (b)) allowing measure the coatings thickness)
- Figure 5 - SEM 관찰 중 수집된 EDS 스펙트럼으로 코팅 조성 확인: (a) Ti40Al60N 및 (b) Ti50Al50N (EDS spectra collected during SEM observations allowing confirm the composition coatings: (a) Ti40Al60N and (b) Ti50Al50N)
- Figure 6 - 코팅 형태학적 특성 분석 (a) Ti40Al60N 및 (b) Ti50Al50N (상면도) (Coatings morphological characterization (a) Ti40Al60N and (b) Ti50Al50N (top view))
- Figure 7 - Ti40Al60N (a) 및 Ti50Al50N (b) 코팅된 링 표면에 대한 AFM 표면 형태 분석 (AFM topography analysis on Ti40Al60N (a) and Ti50Al50N (b) coated ring surface)
- Figure 8 - Ti40Al60N 코팅의 스크래치 테스트 임계 하중 (a) 응집 파손 및 (b) 접착 파손 이벤트 (Scratch-test critical loads (a) cohesive and (b) adhesive failure events on Ti40Al60N coating)
- Figure 9 - Ti50Al50N 코팅의 스크래치 테스트 임계 하중 (a) 응집 파손 및 (b) 접착 파손 이벤트 (Scratch-test critical loads (a) cohesive and (b) adhesive failure events on Ti50Al50N coating)
- Figure 10 - 블록-온-링 마찰계에서 마모 마찰학적 테스트 후 서로 다른 알루미늄 합금((a) A380 및 (b) A13)과 접촉한 Ti40Al60N 코팅된 링 표면의 SEM 이미지. 슬라이딩 방향은 화살표로 표시 (SEM images collected of Ti40Al60N coated ring surface in contact with different aluminum alloy ((a) A380 and (b) A13) after wear tribological tests on block on ring tribometer. Sliding direction represented by arrows)
- Figure 11 - 블록-온-링 마찰계에서 마모 마찰학적 테스트 후 서로 다른 알루미늄 합금((a) A380 및 (b) A13)과 접촉한 Ti50Al50N 코팅된 링 표면의 SEM 이미지. 슬라이딩 방향은 화살표로 표시 (SEM images collected of Ti50Al50N coated ring surface in contact with different aluminum alloy ((a) A380 and (b) A13) after wear tribological tests on block on ring tribometer. Sliding direction represented by arrows)
- Figure 12 - Ti40Al60N 코팅된 링 표면(a, b, c)에 블록에서 이동된 A13 알루미늄 합금의 SEM 관찰 및 스펙트럼. 슬라이딩 방향은 화살표로 표시 (SEM observation and spectra of transferred A13 aluminum alloy from the block to Ti40Al60N coated ring surface (a, b, c). Sliding direction represented by arrow)
- Figure 13 - Ti40Al60N 코팅된 링 표면(a, b, c)에 A380 알루미늄 합금의 SEM 관찰 및 스펙트럼. 슬라이딩 방향은 화살표로 표시 (SEM observation and spectra of transferred A380 aluminum alloy on Ti40Al60N coated ring surface (a, b, c). Sliding direction represented by arrow)
- Figure 14 - Ti50Al50N 코팅된 링 표면(a, b, c)에 A13 알루미늄 합금의 SEM 관찰 및 스펙트럼. 슬라이딩 방향은 화살표로 표시 (SEM observation and spectra of transferred A13 aluminum alloy on Ti50Al50N coated ring surface (a, b, c). Sliding direction represented by arrow)
- Figure 15 - Ti50Al50N 코팅된 링 표면(a, b, c)에 A13 알루미늄 합금의 SEM 관찰 및 스펙트럼. 슬라이딩 방향은 화살표로 표시 (SEM observation and spectra of transferred A13 aluminum alloy on Ti50Al50N coated ring surface (a, b, c). Sliding direction represented by arrow)
- Figure 16 - 다이캐스팅 금형에 사용된 코어 핀 시편 (a) 코팅되지 않은 핀, (b) Ti40Al60N 코팅된 핀, (c) Ti50Al50N 코팅으로 30,000회 샷 후, (d) Ti40Al60N 코팅으로 30,000회 샷 후 (Core pin samples used on die-casting mold (a) uncoated pin, (b) Ti40Al60N coated pin, (c) after 30,000 shots with Ti50Al50N coating, (d) after 30,000 shots with Ti40Al60N coating)
7. 결론:
주요 연구 결과 요약:
본 연구에서는 고압 다이캐스팅 금형용으로 두 가지 TiAlN 코팅인 Ti40Al60N과 Ti50Al50N을 비교했습니다. Ti40Al60N은 실험실 및 산업 테스트 모두에서 우수한 내마모성을 입증했으며, 더 낮은 마찰과 30,000회 사출 사이클 후 코어 핀의 마모가 덜했습니다. Ti50Al50N은 실험실 환경에서 우수한 내마모성을 보였지만, 산업 테스트에서는 코팅 파손 및 더 큰 알루미늄 접착의 증거와 함께 더 낮은 성능을 보였습니다. Ti40Al60N의 약간 더 거친 표면에도 불구하고 더 높은 경도와 영률이 더 나은 성능에 기여했습니다.
연구의 학문적 의의:
본 연구는 고압 다이캐스팅 응용 분야에서 TiAlN 코팅 조성, 미세 구조 및 마모 성능 간의 관계에 대한 이해에 기여합니다. 코팅 성능을 검증하기 위해 실험실 및 산업 테스트를 모두 고려하는 것의 중요성을 강조합니다. 본 연구는 코팅된 다이캐스팅 금형에서 발생하는 마모 메커니즘 및 재료 이동 현상에 대한 귀중한 통찰력을 제공합니다.
실용적 의미:
연구 결과는 Ti40Al60N 코팅이 Ti50Al50N에 비해 고압 다이캐스팅 금형의 수명을 늘리는 데 더 효과적인 솔루션임을 시사합니다. 이는 다이캐스팅 산업에 실질적인 의미를 가지며, 금형 마모를 줄이고 유지 보수 비용을 절감하며 생산성을 향상시킬 수 있는 잠재적인 코팅 솔루션을 제공합니다. 본 연구는 심각한 마모를 받는 금형의 인서트 또는 이동 부품에 Ti40Al60N을 사용하는 것을 뒷받침합니다.
연구의 한계 및 향후 연구 분야:
본 연구는 두 가지 특정 TiAlN 조성과 두 가지 알루미늄 합금으로 제한되었습니다. 향후 연구에서는 코팅 성능을 더욱 최적화하기 위해 더 넓은 범위의 코팅 조성, 다층 코팅 및 다양한 알루미늄 합금을 탐색할 수 있습니다. 코팅의 수명 한계를 완전히 평가하려면 30,000회 사이클을 초과하는 장기간의 산업 테스트가 필요합니다. 특정 마모 메커니즘과 코팅 성능에 대한 표면 거칠기의 역할에 대한 추가 조사도 유익할 것입니다.
8. 참고 문헌:
- [1] S. Gulizia, M.Z. Jahedi, E.D. Doyle, Performance evaluation of PVD coatings for high pressure die casting, Surf. Coatings Technol., 140(3) (2001) 200–205. DOI: 10.1016/S0257-8972(01)01037-4.
- [2] A. Persson, S. Hogmark, J. Bergström, Thermal fatigue cracking of surface engineered hot work tool steels, Surf. Coatings Technol., 191(2-3) (2005) 216–227. DOI: 10.1016/j.surfcoat.2004.04.053.
- [3] I. Peter, M. Rosso, and F.S. Gobber, Study of protective coatings for aluminum die casting molds, Appl. Surf. Sci., 358 (2015) 563–571. DOI: 10.1016/j.apsusc.2015.08.013.
- [4] Z.W. Chen, M.Z. Jahedi, Die erosion and its effect on soldering formation in high-pressure die casting of aluminum alloys, Mater. Des., 20(6) (1999) 303–309. DOI: 10.1016/S0261-3069(99)00035-7.
- [5] A. Persson, S. Hogmark J. Bergström, Simulation and evaluation of thermal fatigue cracking of hot work tool steels, Int. J. Fatigue, 26(10) (2004) 1095–1107. DOI: 10.1016/j.ijfatigue.2004.03.005.
- [6] D. Klobčar, J. Tušek, Thermal stresses in aluminum alloy die casting dies, Comput. Mater. Sci., 43(4) (2008) 1147–1154. DOI: 10.1016/j.commatsci.2008.03.009.
- [7] D. Klobčar, L. Kosec, B. Kosec, J. Tušek, Thermo fatigue cracking of die casting dies, Eng. Fail. Anal., 20 (2012) 43-53. DOI: 10.1016/j.engfailanal.2011.10.005.
- [8] E.K. Tentardini, A.O. Kunrath, C. Aguzzoli, M. Castro, J.J. Moore, and I.J.R. Baumvol, Soldering mechanisms in materials and coatings for aluminum die casting, Surf. Coatings Technol., 202(16) (2008) 3764-3771. DOI: 10.1016/j.surfcoat.2008.01.019.
- [9] O. Knotek, F. Löffler B. Bosserhoff, PVD coatings for diecasting moulds, Surf. Coatings Technol., 62(1-3) (1993) 630-634. DOI: 10.1016/0257-8972(93)90310-K.
- [10] L.A. Dobrzanski, M. Polok, P. Panjan, S. Bugliosi, M. Adamiak, Improvement of wear resistance of hot work steels by PVD coatings deposition, J. Mater. Process. Technol., 155-156(1-3) (2004) 1995-2001. DOI: 10.1016/j.jmatprotec.2004.04.405.
- [11] B. Navinšek, P. Panjan, I. Urankar, P. Cvahte, F. Gorenjak, Improvement of hot-working processes with PVD coatings and duplex treatment, Surf. Coatings Technol., 142-144 (2001) 1148-1154. DOI: 10.1016/S0257-8972(01)01098-2.
- [12] D. Heim, F. Holler, C. Mitterer, Hard coatings produced by PACVD applied to aluminium die casting, Surf. Coatings Technol., 116–119 (1999) 530-536. DOI: 10.1016/S0257-8972(99)00104-8.
- [13] C. Mitterer, F. Holler, F. Üstel, D. Heim, Application of hard coatings in aluminium die casting - soldering, erosion and thermal fatigue behaviour, Surf. Coatings Technol., 125(1-3) (2000) 233-239. DOI: 10.1016/S0257-8972(99)00557-5.
- [14] Y. Wang, A study of PVD coatings and die materials for extended die-casting die life, Surf. Coatings Technol., 94-95(97) (1997) 60-63. DOI: 10.1016/S0257-8972(97)00476-3.
- [15] K.B. Müller, Deposition of hard films on hot-working steel dies for aluminium, J. Mater. Process. Technol., 130-131 (2002) 432-437. DOI: 10.1016/S0924-0136(02)00715-X.
- [16] I.-W. Park, K.H. Kim, Coating materials of TiN, Ti-Al-N, and Ti-Si-N by plasma-enhanced chemical vapor deposition for mechanical applications, J. Mater. Process. Technol., 130-131 (2002) 254-259. DOI: 10.1016/S0924-0136(02)00807-5.
- [17] N.J.M Carvalho, E. Zoestbergen, B.J Kooi, J.Th.M De Hosson, Stress analysis and microstructure of PVD monolayer TiN and multilayer TiN/(Ti,Al)N coatings, Thin Solid Films, 429(1-2) (2003)179-189. DOI: 10.1016/S0040-6090(03)00067-1.
- [18] J. Musil, H. Hrubý, Superhard nanocomposite Til-xAlxN films prepared by magnetron sputtering, Thin Solid Films, 365 (2000) 104-109. DOI: 10.1016/S0040-6090(00)00653-2.
- [19] A. Srivastava, V. Joshia, R. Shivpuria, R. Bhattacharya, S. Dixit, A multilayer coating architecture to reduce heat checking of die surfaces, Surf. Coatings Technol., 163-164 (2003) 631-636. DOI: 10.1016/S0257-8972(02)00690-4.
- [20] K. Bobzin, T. Brögelmann, U. Hartmann, N.C. Kruppe, Analysis of CrN/AlN/Al2O3 and two industrially used coatings deposited on die casting cores after application in an aluminum die casting machine, Surf. Coatings Technol., vol. 308 (2016) 374-382. DOI: 10.1016/j.surfcoat.2016.09.040.
- [21] R. Rodríguez-Baracaldo, J.A. Benito, E.S. Puchi-Cabrera, M.H. Staia, High temperature wear resistance of (TiAl)N PVD coating on untreated and gas nitrided AISI H13 steel with different heat treatments, Wear, 262 (2007) 380-389. DOI: 10.1016/j.wear.2006.06.010.
- [22] Ł. Tomaszewski, W. Gulbinski, A. Urbanowicz. T. Suszko, A. Lewandowski, W. Gulbinski, TiAlN based wear resistant coatings modified by molybdenum addition, Vacuum 121 (2015) 223-229. DOI: 10.1016/j.vacuum.2015.08.027.
- [23] C.J. Tavares, L. Rebouta, M. Andritschky, F. Guimaraes, A. Cavaleiro, Mechanical and surface analysis of Ti0.4A10.6N/Mo multilayers, Vacuum 60 (2001) 339-346. DOI: 10.1016/S0042-207X(00)00413-9.
- [24] C.J. Tavares, L. Rebouta, J.P. Rivière, J. Pacaud, H. Garem, K. Pischow, Z. Wang, Microstructure of superhard (Ti,Al)N/Mo multilayers, Thin Solid Films, 398-399 (2001) 397-404. DOI: 10.1016/S0040-6090(01)01349-9.
- [25] C.J. Tavares, C. Vidrago, L. Rebouta, J.P. Rivière, E. Le Bourhis, M.F. Denanot, Optimization and thermal stability of TiAlN/Mo multilayers, Surf. Coat. Technol. 200 (2005) 288-292. DOI: 10.1016/j.surfcoat.2005.02.099.
- [26] T. Reeswinkel, D.G. Sangiovanni, V. Chirita, L. Hultman, J.M. Schneider, Structure and mechanical properties of TiAlNeWNx thin films, Surf. Coat. Technol. 205 (2011) 4821-4827. DOI: 10.1016/j.surfcoat.2011.04.066.
- [27] B. Park, D.-H. Jung, H. Kim, K.-C. Yoo, J.-J. Lee, J. Joo, Adhesion properties of TiB2 coatings on nitrided AISI H13 steel, Surf. Coat. Technol. 200 (2005) 726-729. DOI: 10.1016/j.surfcoat.2005.01.064.
- [28] F.J.G. Silva, R.C.B. Casais, R.P. Martinho, A.P.M. Baptista, Mechanical and Tribological Characterization of TiB2 Thin Films, J. Nanosci. Nanotechnol., 12 (2012) 9187–9194. DOI: 10.1166/jnn.2012.6759.
- [29] M. Mâaza, C. Sella, J. P. Ambroise, M. Kâabouchi, M. Milôche, F. Wehling and M. Groos, Determination of diffusion coefficient D and activation energy Qa of nickel into titanium in Ni-Ti multilayers by grazing-angle neutron reflectometry, J. Appl. Cryst. 26 (1993) 334-342. DOI: 10.1107/S0021889892010355.
- [30] M. Mâaza. A. Menelle. J.P. Chauvineau. B. Pardo. A. Raynal. F. Bridou. C. Sella. T. Megademini. Monochromation and anodization with Ti-B4C multilayers in neutron optics, Physica B, 198(1-3) (1994) 231-234. DOI: 10.1016/0921-4526(94)90167-8.
- [31] K. Bobzin, T. Brögelmann, R.H. Brugnara, N.C. Kruppe, S. Chromy, Influence of HPPMS pulse parameters on the reactive gas N2 and on the properties of (Cr, Al)N coatings, Surf. Coat. Technol. 293 (2016) 28-34. DOI: 10.1016/j.surfcoat.2015.12.072.
- [32] M.F.C. Andrade, R.P. Martinho, F.J.G. Silva, R.J.D. Alexandre, A.P.M. Baptista, Influence of the abrasive particles size in the microabrasion wear tests of TiAlSiN thin coatings, Wear 267 (2009) 12–18. DOI: 10.1016/j.wear.2008.12.114.
- [33] R.P. Martinho, M.F.C. Andrade, F.J.G. Silva, R.J.D. Alexandre, A.P.M. Baptista, Microabrasion wear behaviour of TiAlCrSiN nanostructured coatings, Wear 267 (2009) 1160-1165. DOI: 10.1016/j.wear.2008.12.063.
- [34] Francisco J. G. Silva, Revestimentos duros ultra-finos executados por P.V.D. (in Portuguese), Master Thesis, Faculty of Engiineering, University of Porto, Porto, 1997.
- [35] Arnaldo M. G. Pinto, Influência do Comportamento Dinâmico da Máquina de Ensino nos Resultados de Atrito e Desgaste, (in Portuguese), Master Thesis, Faculty of Engineering, University of Porto, Porto, 2001.
- [36] F. Silva, A. T. Ribeiro, L. A. Ferreira, A comparative study of the tribological behaviour of TiN and ZrN PVD coatings, Lubrication at the frontier, D. Dowson et al. (Eds), Tribology Series, Elsevier, Amsterdan, pp 141-147.
- [37] P. Terek, L. Kovacevic, A. Miletic, P. Panjan, S. Balos, B. Skoric, Effects of die core treatments and surfaces finishes on the sticking and galling tendency of Al-Si alloy casting during ejection, Wear, 356-357 (2016) 122-134. DOI: 10.1016/j.wear.2016.03.016.
- [38] E. Lugscheider, C. Barimani, S. Guerreiro, K. Bobzin, Corrosion tests of PVD coatings with die lubricant used for Al high-pressure die-casting dies, Surf. Coat. Technol., 108-109 (1998) 408-412. DOI: 10.1016/S0257-8972(98)00624-6.
- [39] J.L. Mo, M.H. Zhu, B. Lei, Y.X. Leng, N. Huang, Comparison of tribological behaviours of AlCrN and TiAlN coatings - Deposited by physical vapor deposition, Wear, 263 (2007) 1423-1429. DOI: 10.1016/j.wear.2007.01.051.
- [40] A. Drnovsek, P. Panjan, M. Panjan, M. Cekada, The influence of growth defects in sputter-deposited TiAlN hard coatings on their tribological behavior, Surf. Coat. Technol., 288 (2016) 171-178. DOI: 10.1016/j.surfcoat.2016.01.021.
- [41] B. Wang, G.R. Bourne, A.L. Korenyi-Both, A.K. Monroe, S.P. Midson, M.J. Kaufman, Method to evaluate the adhesion behavior of aluminum-based alloys on various materials and coatings for lube-free die casting, J. Mater. Process. Technol., 237 (2016) 386-393. DOI: 10.1016/j.jmatprotec.2016.06.031.
9. 저작권:
- 본 자료는 "V. Nunes, F.J.G. Silva, M.F. Andrade, R. Alexandre, A.P.M. Baptista"의 논문: "고압 다이캐스팅 금형의 수명 연장: 심각한 마모 조건 하에서"를 기반으로 합니다.
- 논문 출처: doi:10.1016/j.surfcoat.2017.05.098
본 자료는 상기 논문을 요약한 것으로, 상업적 목적으로 무단 사용하는 것을 금지합니다.
Copyright © 2025 CASTMAN. All rights reserved.