본 소개 자료는 [Hindawi Publishing Corporation]에서 발행한 ["Experimental and Theoretical Studies on the Effect of Die Temperature on the Quality of the Products in High-Pressure Die-Casting Process"] 논문의 연구 내용입니다.
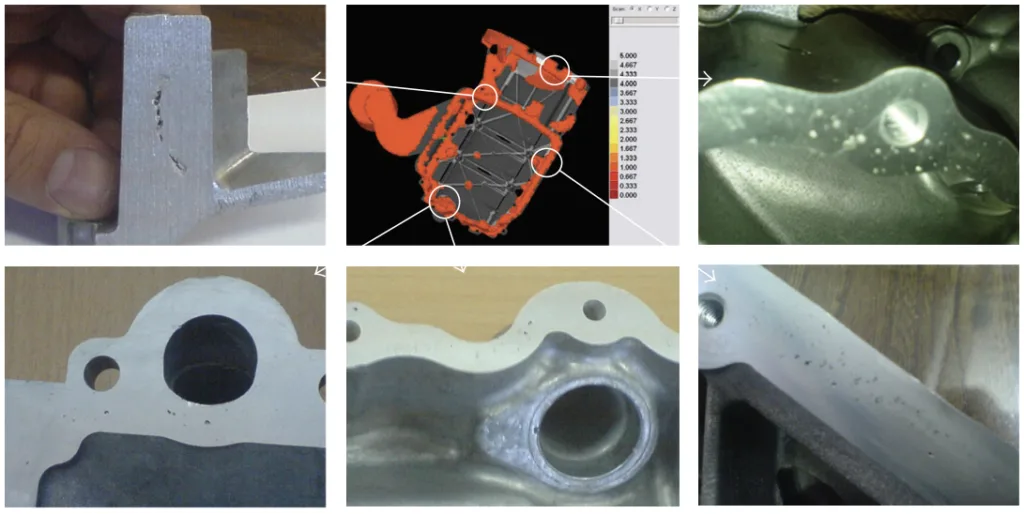
1. 개요:
- 제목: 고압 다이캐스팅 공정에서 금형 온도가 제품 품질에 미치는 영향에 대한 실험 및 이론적 연구 (Experimental and Theoretical Studies on the Effect of Die Temperature on the Quality of the Products in High-Pressure Die-Casting Process)
- 저자: Mohammad Sadeghi and Jafar Mahmoudi
- 출판 연도: 2012
- 게재 저널/학회: Advances in Materials Science and Engineering
- 키워드: 고압 다이캐스팅(HPDC), 금형 온도, A380 합금, 수치 시뮬레이션, ProCAST, 응고, 주조 결함.
2. 초록
A380 합금의 고압 다이캐스팅에서 금형 온도는 실험적 관찰 및 수치 시뮬레이션을 통해 최적화되었습니다. 매우 복잡한 형상을 가진 래더 프레임(새로운 모터 EF7의 한 부분)이 실험 샘플로 선택되었습니다. 양호한 부품을 생산하기 위해 금형 온도와 용탕 온도를 조사했습니다. 초기 단계와 최종 충진 위치에서 금형 온도를 측정하고 이들 값 사이의 차이를 계산했습니다. ProCAST 소프트웨어를 사용하여 부품의 유체 흐름 및 응고 단계를 시뮬레이션했으며, 그 결과는 실험 측정으로 검증되었습니다. 이 합금에 적합한 금형 온도는 200°C 이상인 것으로 나타났습니다.
3. 연구 배경:
연구 주제의 배경:
고압 다이캐스팅(HPDC)은 특히 자동차 산업에서 높은 치수 정확도와 생산성을 가진 부품을 생산하는 데 널리 사용되는 제조 공정입니다 [1-7].
선행 연구 현황:
이전 연구는 공정 변수 최적화 [14-16], 충진 및 응고 시뮬레이션 [10, 11, 12], 공정 변수가 결함에 미치는 영향 연구 [6, 7, 8, 9, 13]에 초점을 맞추었습니다. 그러나 산업 응용 분야에서 발견되는 복잡한 형상에 대한 연구는 제한적입니다.
연구의 필요성:
품질을 개선하고 결함을 줄이기 위해 복잡한 자동차 부품, 특히 금형 온도에 대한 공정 변수 최적화가 필요합니다.
4. 연구 목적 및 연구 질문:
연구 목적:
A380 합금으로 만들어진 복잡한 자동차 부품(래더 프레임)에 대한 HPDC 공정에서 금형 온도를 최적화합니다.
핵심 연구:
금형 온도가 주조 제품의 품질, 특히 결함 형성에 미치는 영향을 조사합니다.
5. 연구 방법
- 연구 설계: 실험 및 수치 시뮬레이션 결합.
- 데이터 수집:
- 실험: 열전대 및 레이저 고온계(모델 chy 110)를 사용하여 금형 및 용탕 온도 측정. IDRA1600 다이캐스팅 머신을 사용하여 주조 시험을 수행했습니다.
- 수치: ProCAST 소프트웨어를 사용하여 유체 흐름 및 응고 시뮬레이션.
- 분석 방법: 실험 온도 측정값과 시뮬레이션 결과 비교. 금형 온도와 관련된 결함 형성 분석.
- 연구 대상 및 범위: 복잡한 형상을 가진 A380 알루미늄 합금으로 만들어진 래더 프레임(새로운 모터 EF7의 부품). 이 연구는 금형 온도의 영향에 초점을 맞췄습니다.
- 지배 방정식:
일련의 편미분 방정식이 해결됩니다.
질량 균형. 방정식 (1).
운동량 균형. 방정식 (2).
엔탈피 공식으로 작성된 에너지 균형. 방정식 (3).
응고를 설명하기 위해 ph는 방정식 (4)로 작성됩니다.
자유 표면 모델링은 스칼라 변수 Φ를 사용하여 달성됩니다. 방정식 (5).
6. 주요 연구 결과:
주요 연구 결과 및 제시된 데이터 분석:
- 이 응용 분야에서 A380 합금에 대한 최적의 금형 온도는 200°C 이상입니다.
- 낮은 금형 온도(예: 150°C)는 냉류 결함 및 기공 결함의 가능성을 증가시킵니다(그림 1-3, 5).
- ProCAST를 사용한 시뮬레이션 결과는 실험 관찰에 의해 검증된 결함 위치를 정확하게 예측했습니다(그림 9, 11, 12).
- 주입 시작 및 종료 시 용탕 온도 차이는 낮은 금형 온도에서 크게 증가했습니다(그림 4).
- 특히 구멍과 같은 형상 주변의 난류 흐름 패턴은 공기 유입 및 기공 형성에 기여합니다(그림 8).
- 표 1: 재료 속성.
- 표 2: 초기 및 경계 조건.
- 표 3: 샷 슬리브의 초기 주입 및 최종 주입 최종 충진 위치에서의 용탕 온도.
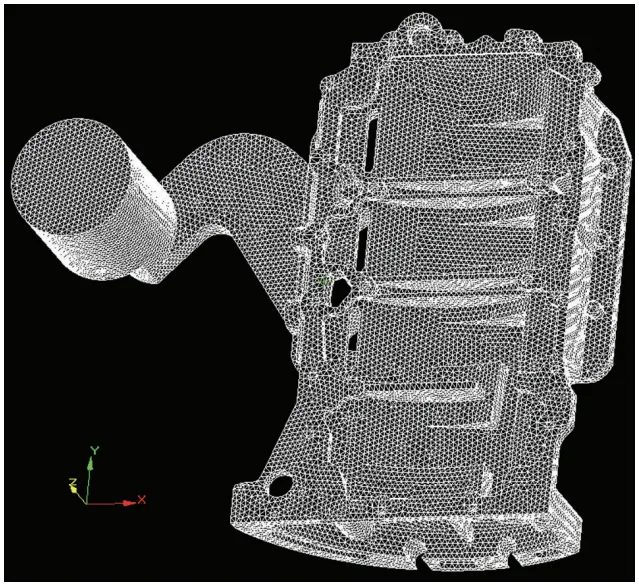
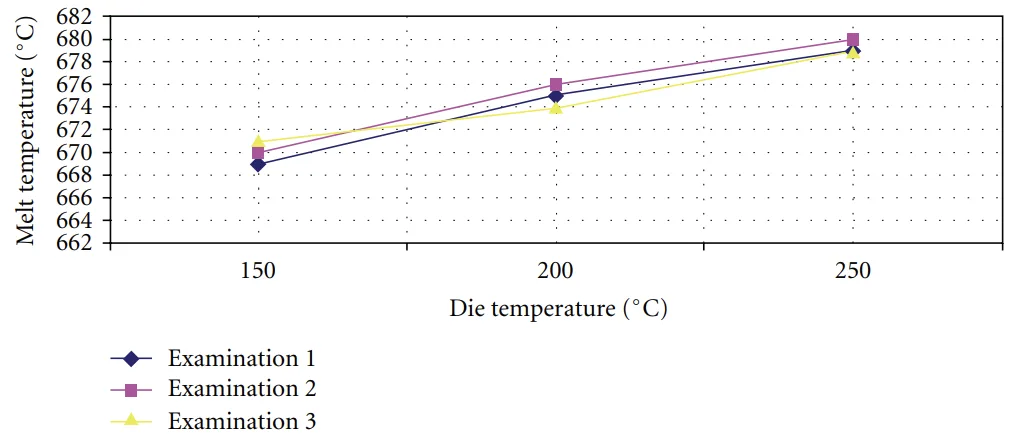
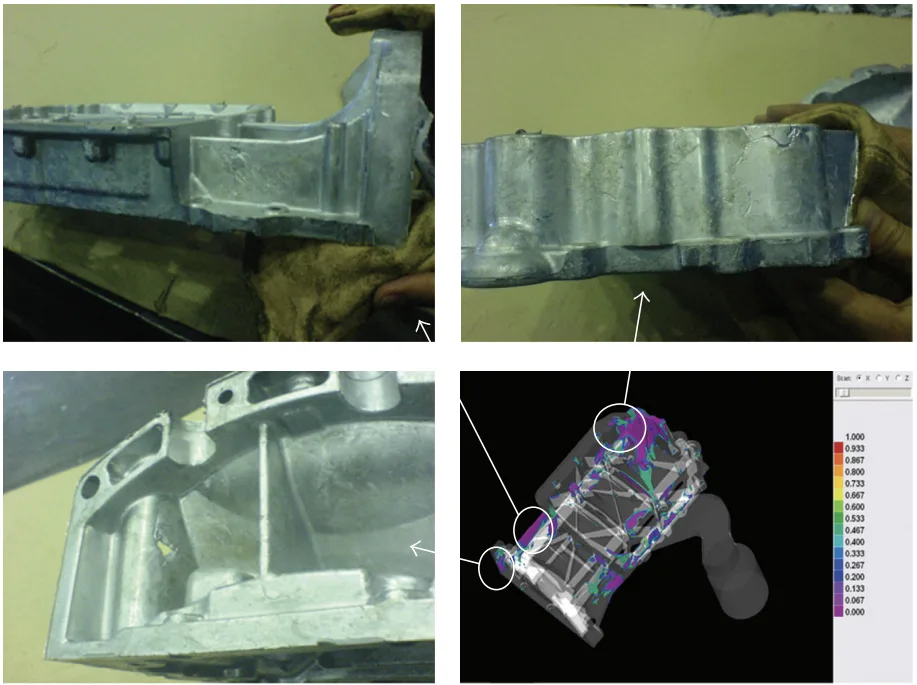
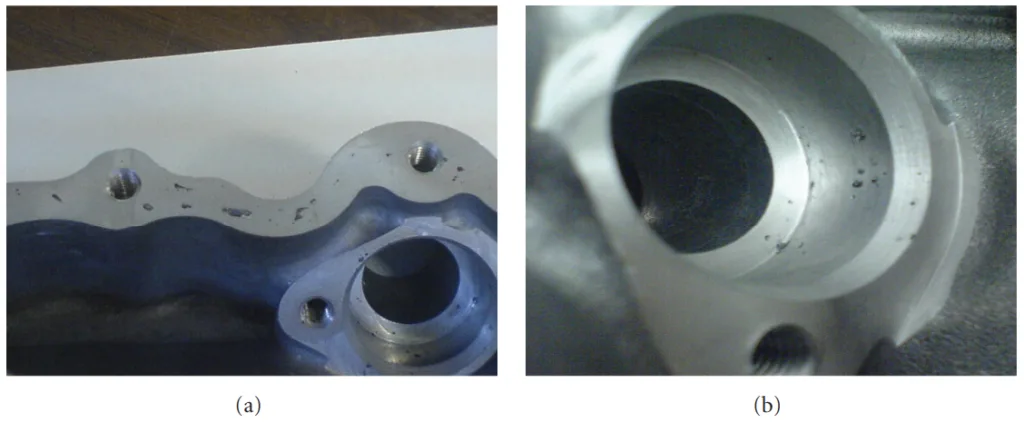
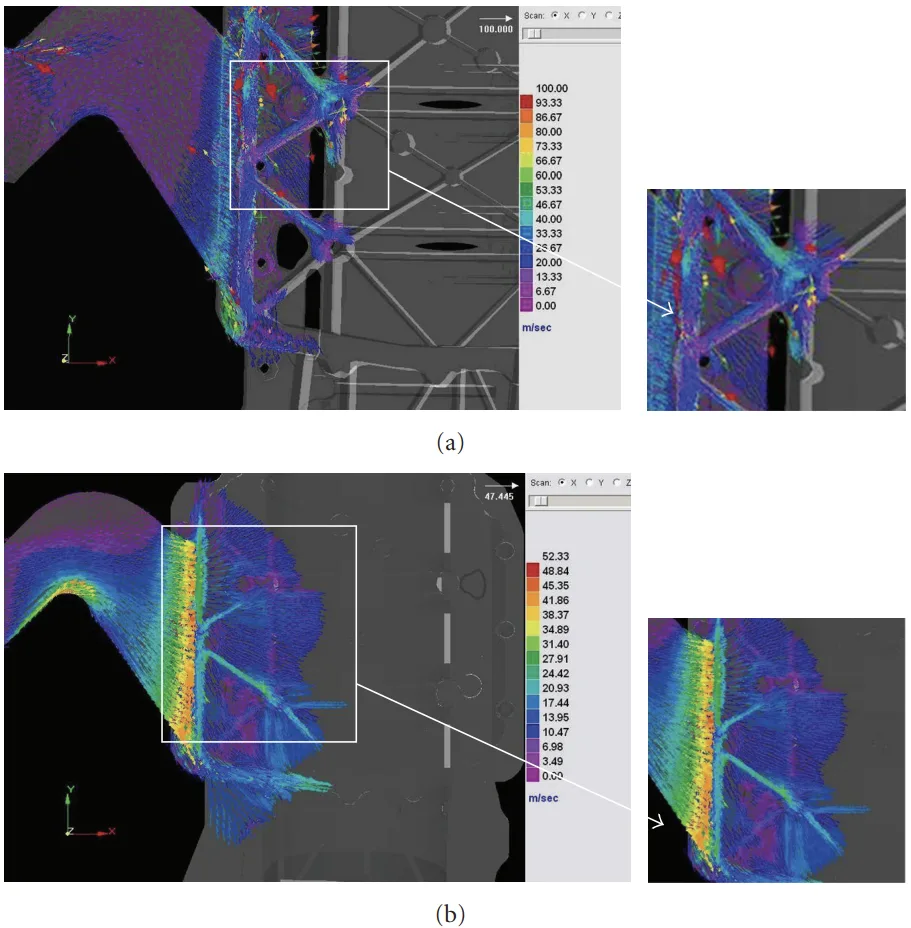
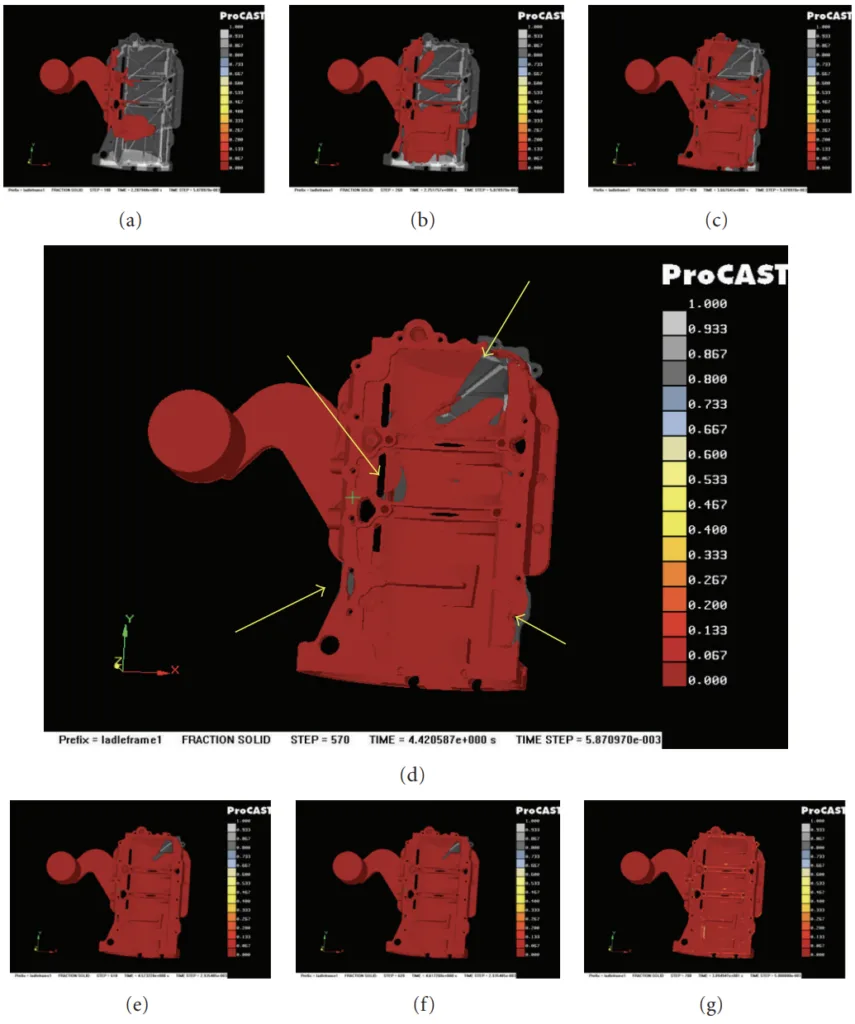
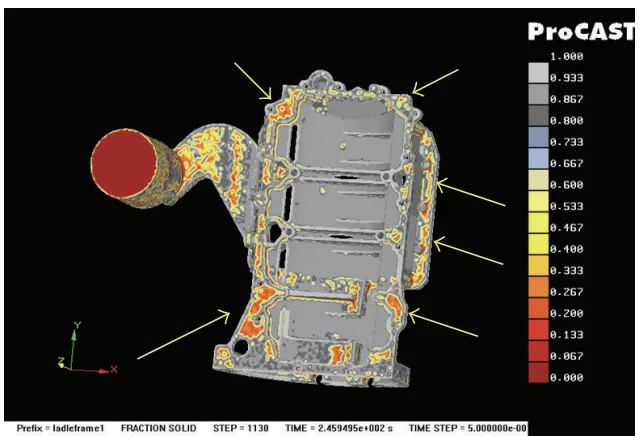
그림 이름 목록:
- 그림 1: 래더 프레임 제품의 형상.
- 그림 2: 금형 입구 및 주입 시작 시 용탕 온도 대 금형 온도.
- 그림 3: 금형 끝 및 주입 종료 시 용탕 온도 대 금형 온도.
- 그림 4: 초기 및 주입 종료 시 다양한 금형 온도에서 용탕 온도의 감소.
- 그림 5: 최종 충진 위치에서의 냉류 표면 결함.
- 그림 6: 금형에 추가된 오버플로우 위치.
- 그림 7: 일부 기공 결함.
- 그림 8: 게이트 앞의 세 구멍에서 용탕의 속도 벡터.
- 그림 9: 용탕에 의해 채워진 금형 단계 및 끝점 표시.
- 그림 10: 금형 온도에 따른 용탕의 흐름 패턴 (a) 150°C 및 (b) 250°C (동일 시간). 시간 a1 = b1, a2 = b2, a3 = b3.
- 그림 11: 주조 결함에 취약한 응고 단계 종료 시의 핫스팟.
- 그림 12: 최종 응고 위치에서 발생한 결함.
7. 결론:
주요 결과 요약:
- 실험 및 시뮬레이션 결과의 비교는 부품의 결함이 시뮬레이션에서 예측된 위치에 배치됨을 나타냅니다.
- H13 금형 재료에 대한 A380 합금의 최적 금형 온도는 약 200°C입니다.
- 금형 온도가 최적 온도 범위에서 감소하면 냉류 결함 및 기공 결함의 가능성이 증가합니다.
- 시뮬레이션을 통해 오버플로우의 최적화된 위치를 결정하면 냉간 샷 및 기공과 같은 일부 주조 결함이 감소합니다.
- 금형 설계에서 이러한 결함 영역 근처에 오버플로를 배치하여 냉류 결함 및 기공을 줄일 수 있습니다.
8. 참고 문헌:
- [1] M. S. Dargusch, G. Dour, N. Schauer, C. M. Dinnis, and G. Savage, "The influence of pressure during solidification of high pressure die cast aluminium telecommunications components," Journal of Materials Processing Technology, vol. 180, no. 1-3, pp. 37–43, 2006.
- [2] Z. W. Chen and M. Z. Jahedi, "Die erosion and its effect on soldering formation in high pressure die casting of aluminium alloys," Materials and Design, vol. 20, no. 6, pp. 303–309, 1999.
- [3] P. W. Cleary, J. Ha, M. Prakash, and T. Nguyen, "3D SPH flow predictions and validation for high pressure die casting of automotive components," Applied Mathematical Modelling, vol. 30, no. 11, pp. 1406–1427, 2006.
- [4] K. J. Laws, B. Gun, and M. Ferry, "Effect of die-casting parameters on the production of high quality bulk metallic glass samples," Materials Science and Engineering A, vol. 425, no. 1-2, pp. 114–120, 2006.
- [5] D. McBride, T. N. Croft, and M. Cross, "A coupled finite volume method for the computational modelling of mould filling in very complex geometries," Computers & Fluids, vol. 37, no. 2, pp. 170–180, 2008.
- [6] C. C. Tai and J. C. Lin, “The optimal position for the injection gate of a die-casting die,” Journal of Materials Processing Technology, vol. 86, no. 1-3, pp. 87–100, 1998.
- [7] S. W. Youn, C. G. Kang, and P. K. Seo, "Thermal fluid/solidification analysis of automobile part by horizontal squeeze casting process and experimental evaluation," Journal of Materials Processing Technology, vol. 146, no. 3, pp. 294–302, 2004.
- [8] J. X. Zhou, L. L. Chen, D. M. Liao, and R. X. Liu, "High pressure diecasting module of InteCAST software and its applications," Journal of Materials Processing Technology, vol. 192-193, pp. 249–254, 2007.
- [9] S. Yue, G. Wang, F. Yin, Y. Wang, and J. Yang, “Application of an integrated CAD/CAE/CAM system for die casting dies,” Journal of Materials Processing Technology, vol. 139, no. 1-3, pp. 465–468, 2003.
- [10] A. Kermanpur, S. Mahmoudi, and A. Hajipour, "Numerical simulation of metal flow and solidification in the multi-cavity casting moulds of automotive components," Journal of Materials Processing Technology, vol. 206, no. 1-3, pp. 62–68, 2008.
- [11] S. Schneiderbauer, S. Pirker, C. Chimani, and R. Kretz, "Studies on flow characteristics at high-pressure die-casting," in Proceedings of the 3rd International Conference on Advances in Solidification Processes.
- [12] M. F. V. T. Pereira, M. Williams, and W. B. du Preez, "Reducing non value adding aluminium alloy in production of parts through high pressure die casting," in Proceedings of the Light Metals Conference, 2010.
- [13] J. K. Rai, A. M. Lajimi, and P. Xirouchakis, "An intelligent system for predicting HPDC process variables in interactive environment," Journal of Materials Processing Technology, vol. 203, no. 1-3, pp. 72–79, 2008.
- [14] B. S. Sung and I. S. Kim, “The molding analysis of automobile parts using the die-casting system,” Journal of Materials Processing Technology, vol. 201, pp. 635–639, 2008.
- [15] V. Ilotte, "Die casting for chassis components," in Proceedings of the 4th International High Tech Die Casting Conference, Montichiari, Italy, April 2008.
- [16] Z. Brown, C. Barnes, J. Bigelow, and U. S. Contech, "Squeeze cast automotive applications and design considerations," in Proceedings of the 4th International High Tech Die Casting Conference, Montichiari, Italy, April 2008.
- [17] J. P. Papai, Contact heat transfer coefficients in aluminum alloy die casting: an experimental and numerical investigation? [Ph.D. thesis], The Ohio State University, 1994.
9. 저작권:
- This material is a paper by "Mohammad Sadeghi and Jafar Mahmoudi": Based on "Experimental and Theoretical Studies on the Effect of Die Temperature on the Quality of the Products in High-Pressure Die-Casting Process".
- Source of paper: [doi:10.1155/2012/434605]
본 자료는 위 논문을 소개하기 위해 작성되었으며, 상업적 목적으로 무단 사용을 금합니다. Copyright © 2025 CASTMAN. All rights reserved.