본 기사에서는 ResearchGate에서 발행한 논문 ['고성능 자동차의 경쟁력 및 에너지 절감 향상을 위한 새로운 브레이크 캘리퍼 개발']을 소개합니다.
1. 개요:
- 제목: New Generation of Brake Callipers to Improve Competitiveness and Energy Savings in Very High Performance Cars (고성능 자동차의 경쟁력 및 에너지 절감 향상을 위한 새로운 브레이크 캘리퍼 개발)
- 저자: Ivano Gattelli, Gianluigi Chiarmetta, Marcello Boschini, Renzo Moschini, Mario Rosso, Ildiko Peter
- 출판 연도: 2014년 9월
- 출판 저널/학회: Solid State Phenomena
- 키워드: semi-solid casting (반용융 주조), rheocasting (레오캐스팅), brake callipers (브레이크 캘리퍼), ceramic cores (세라믹 코어), high performance cars (고성능 자동차)
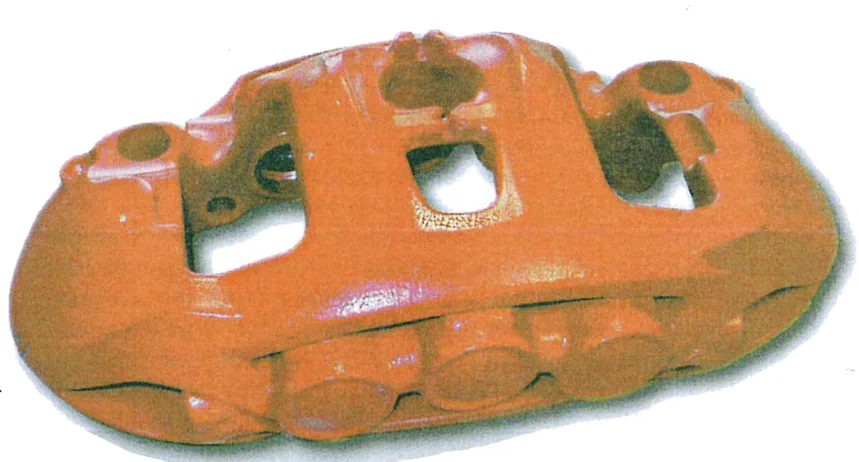
2. 초록 또는 서론
최근 재료 과학 및 생산 공정 연구는 에너지 소비 및 중량 감소에 초점을 맞추고 있습니다. 경합금 및 반용융 공정은 자동차 및 항공 산업 응용 분야에 유망한 기술로 부상했습니다. 효과적인 미세 구조 제어는 부품의 기계적 거동에 매우 중요합니다. 단조는 최적의 방법이지만 비용이 많이 듭니다. 주조는 경제적이지만 결함이 발생할 수 있습니다. 반용융 공정은 주조와 단조 사이의 격차를 줄여 결함 제어를 개선합니다. 스퀴즈 캐스팅, 틱소포밍, 레오캐스팅과 같은 새로운 반용융 방법은 단조와 유사한 수준의 물성을 가진 부품을 생산할 수 있습니다. 반세기 동안의 발전에도 불구하고 더 자세한 유변학적 데이터가 필요합니다. 이러한 공정은 결함을 줄이고 표면 품질과 치수 정확도를 향상시킵니다. 주요 과제는 연구실의 기술을 저렴한 대량 생산으로 이전하는 것입니다. 본 논문에서는 고성능 산업 부품, 특히 브레이크 캘리퍼의 경쟁력과 에너지 절감을 개선하기 위해 특수 세라믹 로스트 코어를 사용하여 레오캐스팅 공정의 추가 최적화 단계를 제시합니다. 이 방법은 중력 주조에 비해 향상된 기계적 물성과 심미적 특성을 제공하면서도 적절한 강도를 유지하여 고성능 자동차 및 미래 응용 분야에 유리합니다.
3. 연구 배경:
연구 주제 배경:
본 연구는 특히 산업 자동차 및 항공 응용 분야에서 재료 과학 및 생산 공정의 에너지 소비 및 중량 감소에 대한 요구 증가라는 맥락에 위치합니다. 경합금 및 반용융 공정은 이러한 요구를 충족하는 유망한 솔루션으로 확인되었습니다. 미세 구조 제어는 생산된 부품의 기계적 거동을 결정하는 데 매우 중요하다고 강조됩니다.
기존 연구 현황:
단조는 고성능 부품 생산에 가장 적합한 방법으로 인정받고 있지만 가장 비용이 많이 드는 방법이기도 합니다. 주조 기술은 경제적으로 더 경쟁력이 있지만 전통적으로 기공, 공동, 개재물 및 산화물과 같은 결함이 발생하기 쉽고 단조와 동일한 성능 수준을 달성하지 못합니다. 반용융 공정은 이러한 격차를 해소하고 개선된 결함 제어를 제공하는 방법으로 부상하고 있습니다. 기존 연구에서는 스퀴즈 캐스팅, 틱소포밍 및 레오캐스팅과 같은 반용융 방법을 탐구하여 새로운 제조 경로를 통해 단조와 유사한 성능을 달성하고 있습니다. 그러나 이러한 공정을 더욱 최적화하기 위해서는 더 자세한 유변학적 데이터에 대한 지속적인 요구가 있습니다.
연구의 필요성:
지난 반세기 동안 반용융 주조 분야에서 상당한 발전이 있었음에도 불구하고 이러한 공정을 최적화하기 위해서는 추가적이고 더 자세한 유변학적 데이터에 대한 요구가 여전히 존재합니다. 연구실에서 산업계로의 기술 이전은 저렴한 대량 생산을 위한 핵심 과제로 남아 있습니다. 특히 브레이크 캘리퍼와 같은 고성능 자동차 응용 분야에서 경쟁력과 에너지 절감을 향상시키기 위해 생산 공정을 최적화해야 할 필요성이 있습니다. 본 연구는 고성능 부품의 대량 생산에 적합한 레오캐스팅 공정을 더욱 개발하고 최적화하여 이러한 요구 사항을 해결하는 것을 목표로 합니다.
4. 연구 목적 및 연구 질문:
연구 목적:
본 연구의 주요 목적은 최적화된 레오캐스팅 공정을 사용하여 새로운 세대의 브레이크 캘리퍼를 개발함으로써 고성능 자동차의 경쟁력과 에너지 절감을 향상시키는 것입니다. 여기에는 브레이크 캘리퍼에 적절한 강도를 유지하면서 중력 주조에 비해 향상된 기계적 물성과 우수한 심미적 특성을 달성하는 것이 포함됩니다.
핵심 연구:
핵심 연구는 레오캐스팅 공정을 사용한 브레이크 캘리퍼 생산과 제조 공정에 특수 세라믹 로스트 코어 구현에 중점을 둡니다. 본 연구에서는 이러한 레오캐스트 브레이크 캘리퍼의 기계적 물성, 미세 구조 및 대량 생산 가능성을 조사합니다.
5. 연구 방법론
연구 설계:
본 연구는 브레이크 캘리퍼 생산을 위한 레오캐스팅 공정의 개발 및 최적화에 초점을 맞춘 실험적 설계를 채택합니다. 여기에는 ATS Company에서 개발한 혁신적인 레오캐스팅 공정과 TCS 수직 유압 프레스 Rotorone 400톤 모델을 사용하는 것이 포함됩니다. 공정에는 A357 합금과 세라믹 로스트 코어가 사용됩니다.
자료 수집 방법:
자료는 다음을 통해 수집되었습니다.
- 방사선 투과 분석: 시편의 무결성을 확인하고 결함을 감지합니다.
- 미세 구조 특성 분석: 광학 현미경(OM, Zeiss Observer Dim 모델)을 사용하여 생산된 캘리퍼의 미세 구조를 분석합니다.
- 기계적 특성 분석: 인장 시험(Galdabini Sun 5 모델)을 포함하여 기계적 물성을 평가하고 비파괴 검사(NDT, Bosello SRE MAX 225 KVtype)를 통해 건전성을 연구합니다.
분석 방법:
분석 방법은 다음과 같습니다.
- 미세 구조 비교: 중력 주조 및 레오캐스팅으로 생산된 브레이크 캘리퍼의 미세 구조를 비교합니다.
- 기계적 물성 평가: 인장 시험 데이터를 분석하여 레오캐스트 시편의 강도와 연신율을 평가하고 표준 요구 사항(UNI EN 1706/2010)과 비교합니다.
- 방사선 투과 이미지 분석: 방사선 투과 이미지를 해석하여 주조물의 결함을 식별하고 평가합니다.
연구 대상 및 범위:
연구 대상은 세라믹 로스트 코어를 사용한 레오캐스팅 공정을 통해 A357 알루미늄 합금을 사용하여 생산된 브레이크 캘리퍼입니다. 연구 범위는 이러한 브레이크 캘리퍼의 대량 생산을 위한 레오캐스팅 공정을 최적화하고 기계적 및 심미적 물성을 평가하는 데 중점을 둡니다.
6. 주요 연구 결과:
핵심 연구 결과:
- 세라믹 코어를 사용한 레오캐스팅 공정이 브레이크 캘리퍼 생산에 성공적으로 구현되었습니다.
- 레오캐스트 브레이크 캘리퍼는 중력 주조 캘리퍼의 수지상 미세 구조와 대조적으로 구상 및 미세 미세 구조를 나타냈습니다 (Figure 2).
- 세라믹 코어를 사용하여 강성, 굽힘 및 압축 강도 측면에서 향상된 기계적 물성이 달성되었습니다.
- 중력 주조에 비해 우수한 심미적 특성이 얻어졌습니다.
- 기존 방법에 비해 약 5%의 중량 감소가 달성되었습니다.
- 레오캐스트 A357 T6 합금의 인장 시험 결과는 사형 및 칠형 주조 A357 T6 열처리 합금에 대한 표준 요구 사항(UNI EN 1706/2010)을 초과했습니다 (Table 2).
- 방사선 투과 분석 결과 레오캐스트 부품의 결함이 감소한 것으로 나타났습니다 (Figure 3).
- 검증 벤치 테스트 및 가혹한 제동 사이클 테스트에서 경미한 결함이 있는 경우에도 레오캐스트 부품의 높은 파괴 인성 및 신뢰성이 입증되었습니다.
제시된 데이터 분석:
- Table 1은 브레이크 캘리퍼 생산에 사용된 A357 합금의 화학 조성(wt.%)을 보여주며, Si, Fe, Cu, Mn, Mg, Zn, Ti 및 Al의 중량 백분율을 명시합니다.
- Table 2는 UTS (340±14 MPa), 항복 강도 (302±4 MPa) 및 연신율 (4.135±2.7%)을 포함하여 레오캐스트 A357 T6 시편의 평균 인장 물성을 나타냅니다. 이러한 값은 사형 및 칠형 주조 A357 T6 열처리 합금에 대한 표준 요구 사항(UNI EN 1706/2010)과 비교하여 측정값이 표준 임계값을 초과함을 보여줍니다.
- Figure 1은 레오캐스팅 공정을 사용하여 생산된 Brembo 브레이크 캘리퍼의 사진입니다.
- Figure 2는 중력 주조 (a) 및 레오캐스팅 (b)으로 생산된 브레이크 캘리퍼의 미세 구조를 비교하여 (a)에서는 수지상 구조를, (b)에서는 구상 및 미세 미세 구조를 보여줍니다.
- Figure 3은 브레이크 캘리퍼의 방사선 투과 이미지로, 조사된 시편에서 유의미한 결함이 없음을 보여줍니다.
- Figure 4는 "최악의 경우" 주조물의 스크랩의 미세 구조를 보여주며, 일부 결함(bifilms)의 존재를 나타냅니다.
Figure 이름 목록:
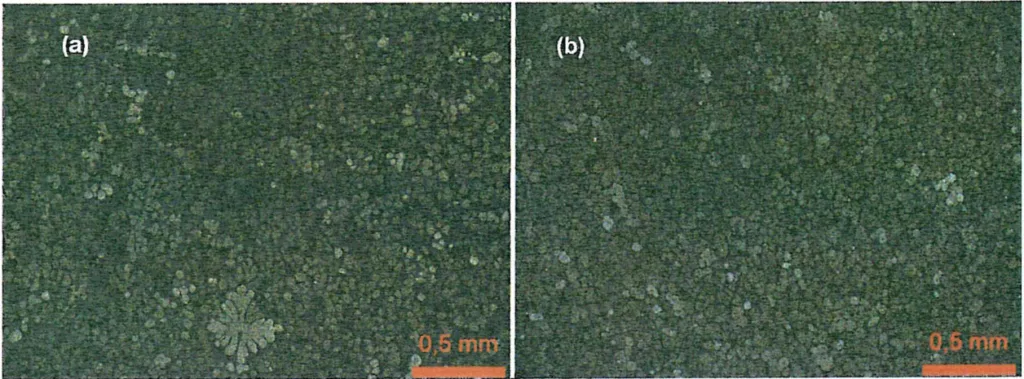
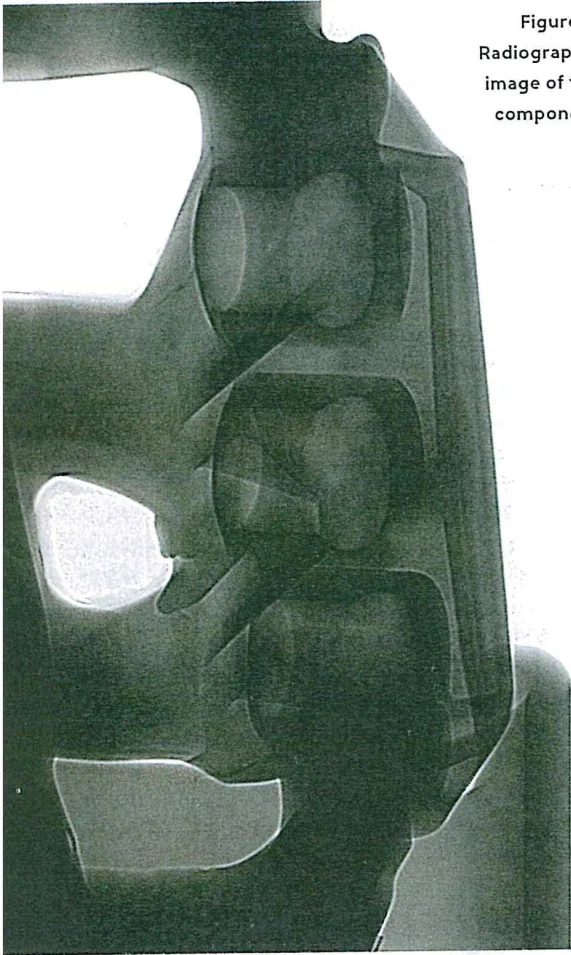
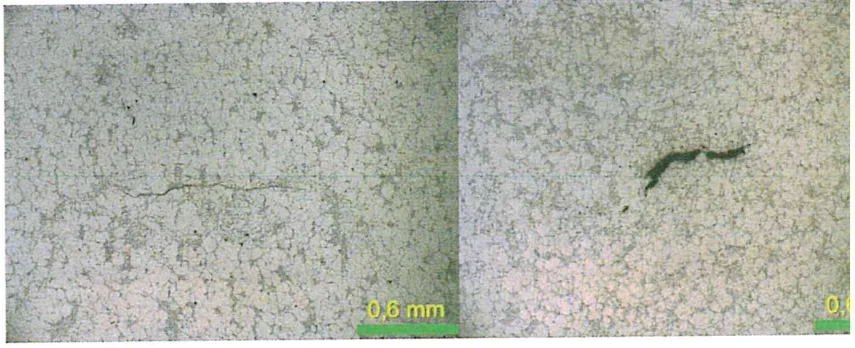
- Figure 1: Photograph of the produced Brembo brake calliper (생산된 Brembo 브레이크 캘리퍼 사진)
- Figure 2: Microstructure of the brake calliper produced by gravity casting process (a) and by rheocasting process (b) (중력 주조 공정 (a) 및 레오캐스팅 공정 (b)으로 생산된 브레이크 캘리퍼의 미세 구조)
- Figure 3: Radiographic image of the component (부품의 방사선 투과 이미지)
- Figure 4: Microctructures of scraps showing the presence of some defects (bifilms) (일부 결함(bifilms)의 존재를 보여주는 스크랩의 미세 구조)
7. 결론:
주요 연구 결과 요약:
본 연구에서는 세라믹 로스트 코어를 사용한 최적화된 레오캐스팅 공정을 사용하여 새로운 세대의 브레이크 캘리퍼 생산을 성공적으로 입증했습니다. 레오캐스트 캘리퍼는 중력 주조 부품에 비해 개선된 미세 구조, 향상된 기계적 물성, 우수한 심미성 및 중량 감소를 나타냈습니다. 세라믹 코어를 사용하면 복잡한 형상과 향상된 구조적 무결성을 얻을 수 있습니다. 테스트 결과 경미한 결함이 있는 경우에도 높은 파괴 인성 및 신뢰성이 확인되었습니다.
연구의 학문적 의의:
본 연구는 고성능 자동차 부품 제조를 위한 레오캐스팅 및 세라믹 코어 기술의 응용에 대한 추가적인 통찰력을 제공함으로써 학문 분야에 기여합니다. 반용융 공정이 주조와 단조 사이의 성능 격차를 줄이는 데 효과적임을 입증합니다. 또한 본 연구는 레오캐스트 A357 합금의 기계적 물성 및 미세 구조에 대한 귀중한 데이터를 제공하여 반용융 야금 분야의 지식 체계를 확장합니다.
실용적 의미:
본 연구의 실용적 의미는 자동차 산업, 특히 고성능 차량 제조에 매우 중요합니다. 개발된 레오캐스팅 공정은 에너지 효율성과 경쟁력이 향상된 경량 고성능 브레이크 캘리퍼의 대량 생산을 위한 실행 가능한 경로를 제공합니다. 세라믹 코어를 사용하면 보다 복잡하고 최적화된 설계를 통해 브레이크 시스템 성능과 심미성을 향상시킬 수 있습니다.
연구의 한계 및 향후 연구 분야:
본 논문에서는 연구의 한계나 향후 연구 분야를 명시적으로 언급하지 않았습니다. 그러나 암묵적으로 향후 연구는 다음 사항에 초점을 맞출 수 있습니다.
- 다양한 합금 및 부품 형상에 대한 레오캐스팅 공정 매개변수의 추가 최적화.
- 실제 주행 조건에서 레오캐스트 브레이크 캘리퍼의 장기적인 내구성과 성능 탐구.
- 기존 방법에 비해 세라믹 코어와 레오캐스팅을 사용한 대량 생산의 비용 효율성 조사.
- 이 공정의 다른 고성능 자동차 부품 및 산업 분야로의 응용 확대.
8. 참고 문헌:
- [1] Campbell F.C., Manufacturing technology for aerospace structural materials. Elsevier; 2006.
- [2] Warren A.S., Developments and challenges for aluminium - A Boeing perspective. Mater Forum 2004, 28 pp. 24-31.
- [3] Blanco M.I., The economics of wind energy. Renewable and Sustainable Energy Reviews 2009, 13, pp. 1372-1382.
- [4] Atkinson H.V., Liu D., (2008) "Microstructural coarsening of semi-solid aluminium alloys" Materials Science and Engineering A, Volume 496, 1-2, 25, pp. 439-446.
- [5] Barnes H., (1997) "Thixotropy - a review", Journal of Non-Newtonian Fluid Mechanics, 70, pp.1-33.
- [6] Cetin, A., Kalkanli, A., (2009) " Investigation of microporosity formation mechanisms in A356 aluminium alloy castings", International Journal of Microstructure and Materials Properties, Vol. 4, No.3, pp.377-385.
- [7] Curle U. A., Govender G., (2010), "Semi-solid rheocasting of grain refined aluminum alloy 7075", Transaction of nonferrous metals. Society of China 20, pp 832-836.
- [8] Rosso M., Peter I., Villa, R., (2008), "Effects of T5 and T6 heat treatments applied to rheocast A356 parts for automotive applications", Journal of Solid State Phenomena Vol. 141-143, pp. 237-242.
- [9] Rosso M., Peter I., "New frontiers for thixoforming", International Journal of Microstructure and Materials Properties, Vol. 8, Issue 1-2, 2013, pp. 113-124
- [10] Zhen Z., Ma Qian, Ji S., Fan Z., "The effects of rheo-diecasting on the integrity and mechanical properties of Mg-6Al-1Zn", Scripta Materialia 54 (2006), 207-211, ISSN 1359-6462.
- [11] Kaufmann H., Wabusses H., Uggowitzer J., "Aspects of the NRC semi-solid casting technology", Journal of Metallurgical and processing Technology, vol. 76, no1-2, pp. 70-75.
- [12] Rosso, M., Peter, I., Chiarmetta, G., Gattelli, 1., (2010), "Development of industrial components by advanced squeeze casting", Proceedings of the 11th International Conference on Semi-Solid Processing of Alloys and Composites, Beijing, 16th - 18th September.
- [13] Rosso M., Peter I., Chiarmetta G., Gatelli I., "Extremely light weight rheocast components for auto motive", Diffusion and Defect Data Pt.B: Solid State Phenomena 192-193, 2012, pp. 545-550.
- [14] Moschini R., Molina R., "Production of hollow components in high pressure die casting through the use of ceramic cores". HTDC, Vicenza Feb 2012.
- [15] Campbell J., Castings 2nd edn., pp. 443-452; 2003, Oxford, Butterworth-Heinemann.
- [16] Campbell J., Casting practice, 2004, Oxford, Butterworth Heinemann.
9. 저작권:
- 본 자료는 "[Ivano Gattelli]"의 논문: "[New Generation of Brake Callipers to Improve Competitiveness and Energy Savings in Very High Performance Cars]"을 기반으로 작성되었습니다.
- 논문 출처: DOI: 10.4028/www.scientific.net/SSP.217-218.471
본 자료는 위에 제시된 논문을 요약한 것이며, 상업적 목적의 무단 사용을 금지합니다.
Copyright © 2025 CASTMAN. All rights reserved.