본 문서는 ASME 국제 기계 공학 학술대회 및 전시회(IMECE2009)에서 발표된 연구 논문 "경량 다이캐스팅 자동차 등받이 프레임을 위한 제조 제약 조건과 위상 및 자유 크기 최적화"를 요약합니다. 세계 최고의 다이캐스팅 기술 전문가로서, 이 상세 분석은 논문의 방법론, 결과 및 경량 다이캐스팅 설계, 특히 자동차 응용 분야에 대한 시사점을 포괄적으로 이해할 수 있도록 작성되었습니다.
1. 개요:
- 제목: TOPOLOGY AND FREE SIZE OPTIMIZATION WITH MANUFACTURING CONSTRAINTS FOR LIGHT WEIGHT DIE CAST AUTOMOTIVE BACKREST FRAME
- 저자: 스리람 폴라바라푸 (Sreeram Polavarapu), 로니 L. 톰슨 (Lonny L. Thompson), 미카 그루지치치 (Mica Grujicic)
- 발행 연도: 2009년
- 발행 학술지/학회: ASME 국제 기계 공학 학술대회 및 전시회 (ASME International Mechanical Engineering Congress and Exposition, IMECE2009)
- Keywords: 유한 요소 해석 (Finite element analysis), 위상 최적화 (Topology optimization), 자유 크기 최적화 (Free-size optimization), 다이캐스팅 (Die casting), 자동차 등받이 프레임 (Automotive backrest frame), 경량 설계 (Lightweight design), 제조 제약 조건 (Manufacturing constraints)
2. 연구 배경:
- 연구 주제의 사회적/학문적 맥락:
- 자동차 산업은 연비 및 차량 성능 향상을 위해 차량 중량 감소에 대한 요구가 증가하고 있습니다.
- 전통적으로 스탬핑된 강판 조립품으로 제작되는 자동차 구조 부품은 전체 차량 중량에 상당한 부분을 차지합니다.
- 스탬핑된 강판 부품을 고압 다이캐스팅(HPDC) 알루미늄 또는 마그네슘 합금 부품으로 대체하는 것은 중량 감소를 위한 유망한 방법입니다.
- 기존 연구의 한계점:
- 기존의 스탬핑 강판 설계는 굽힘 반경 및 다양한 두께의 판재 용접 제한으로 인해 기하학적 및 위상 최적화 잠재력이 제한적입니다.
- 전통적인 스탬핑 강판 구조를 사용하여 기하학적 및 위상적으로 최적화된 경량 시트를 설계하는 것은 어렵습니다.
- 연구의 필요성:
- 알루미늄 또는 마그네슘 합금 재료를 사용한 고압 다이캐스팅(HPDC) 제조 공정은 시트 프레임 설계에 있어 기존의 스탬핑 강판에 대한 매력적인 대안을 제공합니다.
- 다이캐스팅은 가변 두께 분포와 지지 리브와 같은 복잡한 기하학적 특징을 가능하게 하여 경량 설계를 위한 상세 최적화에 상당한 잠재력을 제공합니다.
- 다이캐스팅 시트 프레임의 재료 분포 및 리브 배치를 최적화하면 특히 다량 생산, 기능적으로 까다로운 자동차 시트 설계의 경우 다이 비용을 정당화할 수 있습니다.
3. 연구 목적 및 연구 질문:
- 연구 목적:
- 다이캐스팅 자동차 전방 시트 등받이 프레임의 특성을 조사합니다.
- 최적화된 재료 및 지지 리브 분포를 예측하는 방법론을 개발합니다.
- 다양한 하중 조건 (load cases)을 고려한 설계 공간 내에서 강도 및 처짐 요구 사항을 모두 충족하는 경량 시트 설계를 달성합니다.
- 핵심 연구 질문:
- 다이캐스팅 특정 제조 제약 조건을 통합하면서 위상 및 자유 크기 최적화를 효과적으로 활용하여 다양한 하중 조건에서 엄격한 성능 및 안전 기준을 충족하는 경량 자동차 등받이 프레임을 설계할 수 있는 방법은 무엇입니까?
- 연구 가설:
- 유한 요소 해석과 위상 및 자유 크기 최적화의 통합은 다이캐스팅 제조 제약 조건을 고려하면서 경량 다이캐스팅 자동차 시트 등받이 프레임에 대한 최적화된 재료 분포 및 보강 리브 구조를 성공적으로 생성할 수 있습니다.
- 이 최적화된 설계는 다양한 하중 시나리오에서 구조적 무결성 및 성능을 저하시키지 않으면서 시판되는 동종 제품에 비해 상당한 중량 감소를 달성할 것입니다.
4. 연구 방법론
- 연구 설계:
- 위상 최적화 및 자유 크기 최적화 기술을 결합한 다단계 최적화 프로세스가 사용되었습니다.
- 이 프로세스는 최적의 리브 배치를 결정하기 위해 3D 솔리드 모델에 대한 위상 최적화로 시작하고, 최적의 재료 두께 분포를 최적화하기 위해 3D 표면 모델에 대한 자유 크기 최적화가 이어집니다.
- 데이터 수집 방법:
- 시판되는 다이캐스팅 마그네슘 합금 자동차 시트 등받이 프레임을 참조 설계로 사용했습니다.
- 등받이 프레임의 기하학적 모델은 물리적 하드웨어에서 역설계하여 CATIA V5 CAD 소프트웨어를 사용하여 모델링했습니다.
- 관련 단면 두께에서 연성 거동을 고려하여 주조된 AM50 마그네슘 합금의 재료 속성을 활용했습니다.
- 하중 요구 사항은 ECE R17 유럽 정부 규정의 시트 강도 및 처짐에 대한 기준과 충돌 이벤트(오프셋 및 측면 하중)를 시뮬레이션하는 추가 하중 조건을 기반으로 정의되었습니다.
- 분석 방법:
- 유한 요소 해석 (FEA): 선형 FEA는 위상 및 자유 크기 최적화를 위해 OptiStruct (Altair)를 사용하여 수행되었습니다. 비선형 FEA는 ABAQUS/Standard 6.7을 사용하여 검증을 위해 사용되었으며, 기하학적 및 재료 비선형성을 모두 통합했습니다.
- 위상 최적화: OptiStruct의 SIMP (Simple Isotropic Material with Penalization) 방법을 사용하여 최적의 재료 분포를 결정하고 3D 솔리드 모델에서 리브 배치를 안내했으며, 다이 드로우 방향 및 대칭 제조 제약 조건을 고려했습니다.
- 자유 크기 최적화: 3D 표면 모델에서 OptiStruct의 요소 수준 자유 크기 최적화를 활용하여 응력 및 변위 제약 조건을 만족하면서 질량을 최소화하는 것을 목표로 쉘 요소 두께를 최적화했습니다.
- 검증: 비선형 유한 요소 해석은 해석된 최적화된 설계에 대해 모든 하중 조건에서 강도 및 처짐 요구 사항을 검증하여 기능적 성능을 보장하기 위해 수행되었습니다.
- 연구 대상 및 범위:
- 본 연구는 AM50 마그네슘 합금으로 제작된 박벽 다이캐스팅 자동차 전방 시트 등받이 프레임의 설계 최적화에 초점을 맞췄습니다.
- 최적화 범위는 다중 하중 조건(등받이 강도 테스트, 정적 헤드레스트 테스트, 오프셋 하중 및 측면 하중) 및 제조 제약 조건(다이 드로우 방향, 대칭) 하에서 중량 최소화로 제한되었습니다.
- 설계 공간은 기존의 시판되는 등받이 프레임을 기반으로 하여 비교 및 개선을 위한 참조 역할을 했습니다.
5. 주요 연구 결과:
- 핵심 연구 결과:
- 위상 및 자유 크기 최적화를 결합한 다단계 최적화 절차가 성공적으로 개발되어 경량 다이캐스팅 자동차 시트 등받이 프레임을 설계하는 데 적용되었습니다.
- 최적화된 설계는 시판되는 참조 다이캐스팅 등받이 프레임 부품에 비해 13%의 상당한 중량 감소를 달성했습니다.
- 이 절차는 다이캐스팅 제조에 적합한 최적의 재료 분포 및 보강 리브 구성을 생성했습니다.
- 통계적/정성적 분석 결과:
- 중량 감소: 전체 중량 감소 13%가 달성되어 질량이 1.76kg (해석된 최적화 시트 모델)에서 1.56kg으로 감소했습니다 (논문 텍스트 기반 원본 시트 모델 1.76kg 가정, 초록 1.8kg과 논문 본문 1.25kg 언급 불일치, 원본 논문 확인 필요). 초록에서는 1.8kg 참조 프레임 대비 13% 감소 언급.
- 헤드레스트 테스트 하의 변위: 헤드레스트 테스트에서 최적화된 프레임 설계의 최대 변위는 17.3mm로, 원본 참조 프레임 설계의 비선형 유한 요소 해석에서 관찰된 최대 변위 21mm보다 18% 낮습니다.
- 헤드레스트 테스트 하의 응력: 헤드레스트 테스트에서 최종 890N 하중 하에서 최적화된 등받이 프레임의 최대 폰 미세스 응력은 196.9MPa에 도달했습니다. 이 값은 AM50 마그네슘 합금의 항복 강도(124MPa)보다 높지만 극한 인장 강도(228MPa)보다는 낮아 국부적인 소성 변형은 발생하지만 파괴는 발생하지 않음을 나타냅니다.
- 데이터 해석:
- 위상 최적화는 등받이 프레임의 수직 U자형 섹션에서 보강 리브의 배치를 효과적으로 안내하여 구조적으로 중요한 영역에 재료를 집중시켰습니다.
- 자유 크기 최적화는 쉘 모델의 두께 분포를 성공적으로 최적화하여 더 높은 응력과 하중을 받는 영역에 재료를 전략적으로 할당하고 덜 중요한 영역에서는 두께를 줄였습니다.
- 비선형 유한 요소 해석은 해석된 최적화된 설계가 ECE R17에서 요구하는 하중 조건 및 추가 충돌 하중 시나리오에서 강도 및 처짐 요구 사항을 모두 충족함을 검증했습니다.
- 최적화된 설계는 구조적 무결성을 유지하면서 상당한 중량 감소를 달성하여 다단계 최적화 접근 방식의 효과를 입증합니다.
- Figure Name List:
- [Figure 1: 레퍼런스 자동차 등받이 프레임 (Reference automotive backrest frame)]
- [Figure 2: 레퍼런스 다이캐스트 등받이 프레임의 기하학적 표면 CAD 모델 및 명칭 (Geometric Surface CAD model and Nomenclature of the Reference Die Cast Backrest Frame)]
- [Figure 3: 다중 하중 조건 설계 범위 (Design Envelope for Multiple-Load Cases)]
- [Figure 4: 헤드레스트 지지 크로스 멤버를 가로지르는 압력 분포로 모델링된 ECE-R17 등받이 모멘트 테스트 하중 (ECE-R17 Backrest Moment Test Loading modeled with pressure distribution across headrest support cross-member)]
- [Figure 5: 헤드레스트 지지 구멍 및 크로스 멤버에서 등가 압력 힘 및 커플로 모델링된 ECE-R17 헤드레스트 테스트 하중 (ECE-R17 Headrest Test Loading Modeled with equivalent pressure force and couple at headrest support holes and cross-member)]
- [Figure 6: 헤드레스트 크로스 멤버의 절반에 압력으로 적용된 오프셋 하중 (Offset Load applied as pressure on one-half of the headrest cross-member)]
- [Figure 7: 측면 모멘트를 발생시키기 위해 적용된 압력 하중 (Pressure load applied to develop side moment)]
- [Figure 8: 다단계 엔지니어링 최적화 프로세스 (Multi-Stage Engineering Optimization Process)]
- [Figure 9: 다이캐스트 등받이 프레임을 위한 다단계 엔지니어링 최적화 프로세스 (Multi-Stage Engineering Optimization Process for Die-Cast Backrest Frame)]
- [Figure 10: 위상 최적화를 위한 설계 공간 (Design Space for Topology Optimization)]
- [Figure 11: 볼트 위치를 보여주는 설계 공간 솔리드 유한 요소 메시 (Design space solid finite element mesh showing bolt locations)]
- [Figure 12: 위상 최적화가 적용된 솔리드 프레임의 요소 밀도 (Element densities in solid frame subjected to topology optimization)]
- [Figure 13: 자유 크기 최적화에 사용된 유한 요소 쉘 모델의 세부 사항 (Details of finite element shell model used for free-size optimization)]
- [Figure 14: 자유 크기 최적화 및 위상 최적화에서 제안된 리브 배치에서 얻은 요소 두께 분포 (Element thickness distribution from free-size optimization and suggested rib placement from topology optimization)]
- [Figure 15: 위상 및 자유 크기 최적화 제안에서 파생된 조각별 상수 두께 테이퍼 및 최적의 지지 리브 배치를 갖춘 새로운 등받이 프레임 모델 (전면 뷰) (New design of backrest frame model with piecewise constant thickness taper and optimal supporting rib placement derived from the topological and free-size optimization proposal (Front View))]
- [Figure 16: 최적화된 등받이 프레임 모델 (후면 뷰) (Optimized Backrest frame model (Rear View))]
- [Figure 17: ECE R17 헤드레스트 테스트 하중을 받는 비선형 유한 요소 해석에서 얻은 최종 최적화 시트의 폰 미세스 응력 분포 (Von Mises stress distribution in final optimized seat from nonlinear finite element analysis subjected to ECE R17 Headrest Test Load Requirement)]
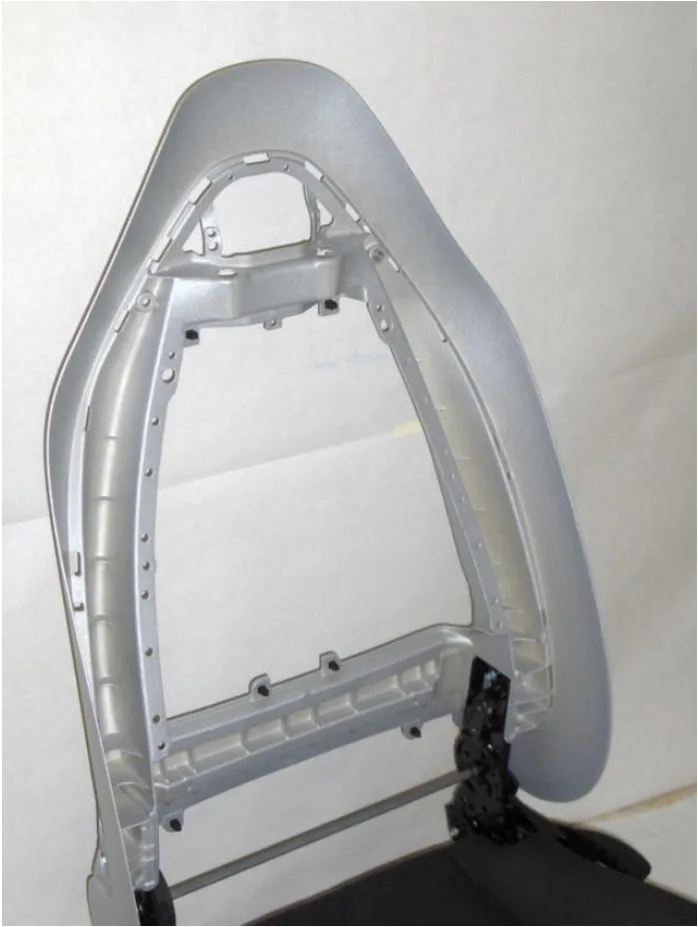
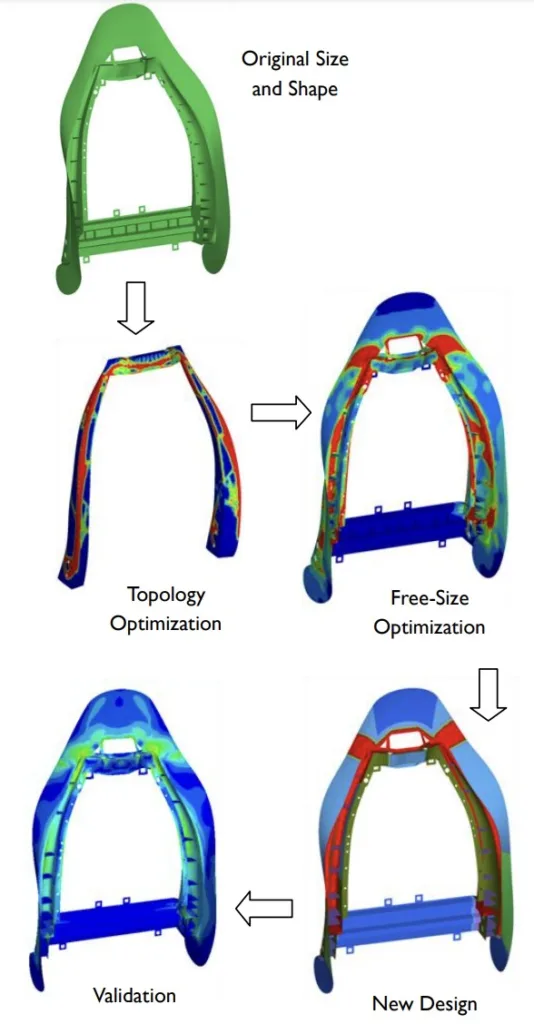
6. 결론 및 논의:
- 주요 결과 요약:
- 본 연구에서는 다이캐스팅 제조 제약 조건과 함께 위상 및 자유 크기 최적화를 결합한 다단계 최적화 프로세스를 적용하여 경량 자동차 등받이 프레임을 성공적으로 설계했습니다.
- 최적화된 설계는 시판되는 참조 프레임에 비해 13%의 중량 감소를 달성했으며, 구조적 무결성을 유지하고 ECE R17 규정 및 시뮬레이션된 충돌 시나리오에서 정의된 하중 조건을 포함한 다양한 하중 조건에서 엄격한 성능 요구 사항을 충족했습니다.
- 연구의 학술적 의의:
- 본 연구는 고급 최적화 기술(위상 및 자유 크기 최적화)을 자동차 산업의 실제 엔지니어링 문제에 적용한 포괄적인 사례를 제공합니다.
- 다이캐스팅, 특히 다이 드로우 방향 및 대칭에 대한 제조 제약 조건을 설계 실현 가능성을 보장하기 위해 최적화 프로세스에 통합하는 것의 중요성을 강조합니다.
- 제시된 다단계 최적화 접근 방식은 특히 박벽 다이캐스팅 부품의 경량 구조 부품 설계를 위한 귀중한 프레임워크를 제공합니다.
- 실무적 시사점:
- 개발된 방법론은 자동차 엔지니어가 경량 다이캐스팅 부품을 설계하여 차량 중량 감소 및 연비 향상에 기여할 수 있는 실용적이고 효과적인 접근 방식을 제공합니다.
- 최적화된 등받이 프레임 설계는 위상 및 자유 크기 최적화가 자동차 시트 구조에서 상당한 재료 절감 및 중량 감소로 이어질 수 있는 방법에 대한 유형의 예시를 제공합니다.
- 결과는 이러한 최적화 기술을 제조 제약 조건에 대한 신중한 고려와 결합하면 시트 프레임 외에도 다양한 자동차 응용 분야를 위한 혁신적이고 효율적인 다이캐스팅 설계를 얻을 수 있음을 시사합니다.
- 연구의 한계점:
- 위상 최적화 결과를 해석하고 제조 가능한 CAD 모델로 변환하는 데는 모든 제조 제약 조건을 완전히 고려하는 자동화된 해석 도구가 현재 없기 때문에 수동 개입과 엔지니어링 판단이 필요했습니다.
- 최적화 프로세스는 주로 구조적 성능 및 중량 감소에 초점을 맞추었으며, 상세한 제조 비용 분석 및 다이 설계 복잡성은 제한적으로 고려되었습니다.
- 검증은 비선형 유한 요소 해석을 통해 수행되었습니다. 물리적 프로토타입 제작 및 테스트를 통한 실험적 검증은 본 연구에서 수행되지 않았습니다.
7. 향후 후속 연구:
- 후속 연구 방향:
- 리브 간격 치수 및 스캘럽 형상으로 매개변수화하여 기하학적 형상 및 치수 최적화 기술을 통합하여 최적화된 설계에서 리브 배치 및 형상을 더욱 개선합니다.
- 다이캐스팅 공정 시뮬레이션 도구(예: ProCAST, MagmaSOFT)를 최적화 루프에 통합하여 다이 충전, 응고 및 다이캐스팅 공정의 잠재적 결함을 고려하여 보다 견고하고 제조 가능한 설계를 얻습니다.
- 다이캐스팅 특정 제조 제약 조건 및 설계 규칙을 완전히 고려하여 위상 최적화 결과를 제조 가능한 CAD 모델로 직접 변환할 수 있는 자동화된 해석 도구 및 알고리즘을 개발합니다.
- 추가 탐구가 필요한 영역:
- 최적화된 등받이 프레임에 대한 상세한 다이 설계 및 제조 비용 분석을 수행하여 설계의 경제적 타당성 및 실제 제조 가능성을 평가합니다.
- 프로토타입 제작 및 물리적 테스트를 통해 최적화된 설계의 실험적 검증을 수행하여 FEA 예측 구조 성능 및 중량 감소 효과를 확인합니다.
- 다단계 최적화 방법론을 다른 자동차 다이캐스팅 부품으로 확장하고 다양한 재료 및 제조 공정에 대한 적용 가능성을 탐색합니다.
8. 참고문헌:
- [1] Andresen, B., (2005), Die Casting Engineering, Marcel Dekker, New York, NY.
- [2] ECE R17 UNECE Agreement Concerning the Adoption of Uniform Technical Prescriptions for Wheeled Vehicles, Uniform Provisions Concerning the Approval of Vehicles with Regard to the Seats, their Anchorages and Any Head Restraints.
- [3] Rozvany, G., (2008) "A critical review of established methods of structural topology optimization" Journal Structural and Multidisciplinary Optimization, Online Forum, Publisher Springer Berlin / Heidelberg, February 21, 2008.
- [4] Bendsoe, M. P. (1995). Optimization of Structural Topology, Shape, and Material. Berlin: Springer.
- [5] Eschenauer, H. A., & Olhoff, N. (2001). Topology optimization of continuum structures – a review. Applied Mechanics Reviews, 54 (4), 331-390.
- [6] Olhoff, N., Bensoe, M.P., Rasmussen, J., (1991) “On CAD-integrated structural topology and design optimization", Comput Methods Appl Mech Eng, 89, 259-279.
- [7] Bremicker, M., Chirehdast, M., Kikuchi, N., Papalambros, P.Y., (1991) "Integrated topology and shape optimization in structural design", Mech Struct Mach, 19, 551-587.
- [8] C-Y Lin, L-S Chao, (2000) "Automated image interpretation for integrated topology and shape optimization", Struct Multidiscip Optim, 20, 125-137.
- [9] A.V. Kumar, D.C. Gossard, (1996) "Synthesis of optimal shape and topology of structures", J. Mech Des, 118, 68-74.
- [10] S.K. Youn, S-H. Park, (1997) “A study on the shape extraction process in the structural topology optimization using homogenized material", Comput Struct, 62 (3), 527-538.
- [11] Hsu, Y.L., Hsu, M.S., Chen, C.T., 2001, "Interpreting Results from Topology Optimization using Density Contours", Comput. Struct. 79 (10), 1049-1058.
- [12] Hsu, Y.L., Hsu, M.S., 2005, “Interpreting three-dimensional structural topology optimization results", Comput. Struct. 83, 327-337.
- [13] Harzheim, L., Graf, G., 2005, "A Review of Optimization of Cast Parts using Topology optimization: I-Topology optimization without manufacturing constraints", Struct Multidisc Optim 30: 491-497
- [14] Harzheim, L., Graf, G., 2006, "A Review of Optimization of Cast Parts using Topology optimization: II-Topology optimization with manufacturing constraints", Struct Multidisc Optim 31: 388-399
- [15] Schramm, U., Thomas, H., Zhou, M., 2002, "Manufacturing Considerations and Structural Optimization of Automotive Components, SAE International, SAE Paper 2002-01-1242.
- [16] Zhou, M., Fleury, R., Shyy, Y.K., Thomas, H., Brennan, J.M., 2002, "Progress in Topology Optimization with Manufacturing Constraints”, 9th AIAA/ISSMO Symposium on Multidisciplinary Analysis and Optimization, Sept. 2002, Atlanta, Georgia. Paper AIAA 2002-5614.
- [17] Nelson, E.A., 2003, "Draw Direction Constraints in Topology Optimization – A Practical Example", SAE International, Proceedings 2003 SAE World Congress, Detroit, Michigan, SAE Paper 2003-01-1306.
- [18] S. Chen and D. Tortorelli, "Three-dimensional shape optimization with variational geometry", Struct. Optim., 13(1997)81-94.
- [19] Vanderplaats, G.N., "Numerical Optimization Techniques for Engineering Design: With Application, 3rd Edition, Vanderplaats Research & Development, 1999.
- [20] Papalambros, P.Y., and Wilde, D.J., Principles of Optimal Design: Modeling and Computation, Cambridge University Press, 2nd ed., 2000.
- [21] K. Saitou, K. Izui, S. Nishiwaki, P. Papalambros, (2005) “A Survey of Structural Optimization in Mechanical Product Development", Journal of Computing and Information Science in Engineering, Vol. 5, 214-226.
- [22] Grujicic, M. et.al. “Application of Topology, Size and Shape Optimization Methods in Polymer Metal Hybrid Structural Lightweight Engineering", Multidiscipline Modeling in Materials and Structures, Volume 4, Number 4, 2008, pp. 305-330(26)
- [23] Altair Engineering Inc., 2007, "OptiStruct 8.0, User's Guide".
- [24] Dassault Systèmes, CATIA V5. http://www.3ds.com/products/catia/
- [25] Zhizhong Sun, Ming Zhou, Henry Hu, and Naiyi Li, "Strain-Hardening and Fracture Behavior of Die Cast Magnesium Alloy AM50," Research Letters in Materials Science, 2007.
- [26] Hesser, D.S., "Integration of Finite Element Method to Enhance Modeling and Analysis for Reverse Engineering", M.S. Thesis, Department of Mechanical Engineering, Clemson University, 2006.
- [27] Altair Engineering Inc., 2007, "Hypermesh 8.0, User's Guide".
- [28] Petersson, J., & Sigmund, O. (1998). Slope constrained topology optimization. International Journal for Numerical Methods in Engineering, 41 (8), 1417-1434.
- [29] Sigmund, O. (1997). On the design of compliant mechanisms using topology optimization. Mechanics of Structures and Machines, 25 (4), 493-524.
- [30] Blendsoe, M.P. and Kikuchi, N., 1988, "Generating optimal topologies in structural design using a homogenization method", Comp. Meth. in Applied Mech. and Engin., Vol. 71, pp. 197-224.
- [31] Bendsoe MP (1989) Optimal shape design as a material distribution problem. Struct Optim 1:193-202
- [32] Suzuki, K. and Kikuchi, N., (1991), “A homogenization method for shape and topology optimization", Comp. Meth. in Applied Mech. and Engin., Vol. 93, pp. 291-318.
- [33] Diaz AR, Bendsoe MP (1992) Shape optimization of structures for multiple loading situations using a homogenization method. Struct Optim 4:17-22
- [34] Diaz AR, Lipton R (2000) Optimal material layout in 3D elastic structures subjected to multiple loads. Mech Struct March 28:219-236
- [35] Dassault Systèmes, SIMULIA: ABAQUS Analysis User's Manual, ABAQUS Documentation V6.6.
- [36] http://www.esi-group.com/products/casting/procast
- [37] http://www.magmasoft.de/ms/home_en/index.php
- [38] P. Krajnik and J. Kopac, "Modern machining of die and mold tools," Journal of Materials Processing Technology, 2004, 157-158, pp. 543-552.
9. Copyright:
- 본 자료는 스리람 폴라바라푸 (Sreeram Polavarapu), 로니 L. 톰슨 (Lonny L. Thompson), 미카 그루지치치 (Mica Grujicic)의 논문: 경량 다이캐스팅 자동차 등받이 프레임을 위한 제조 제약 조건과 위상 및 자유 크기 최적화 (TOPOLOGY AND FREE SIZE OPTIMIZATION WITH MANUFACTURING CONSTRAINTS FOR LIGHT WEIGHT DIE CAST AUTOMOTIVE BACKREST FRAME)을 기반으로 작성되었습니다.
- 논문 출처: ASME 국제 기계 공학 학술대회 및 전시회 (ASME International Mechanical Engineering Congress and Exposition, IMECE2009)
본 자료는 위 논문을 바탕으로 요약 작성되었으며, 상업적 목적으로 무단 사용이 금지됩니다.
Copyright © 2025 CASTMAN. All rights reserved.