본 소개 내용은 [IOS Press]에서 발행한 ["미적 복합 부품의 고압 다이캐스팅 공정 개선을 위한 가이드라인 설정"] 의 연구 내용입니다.
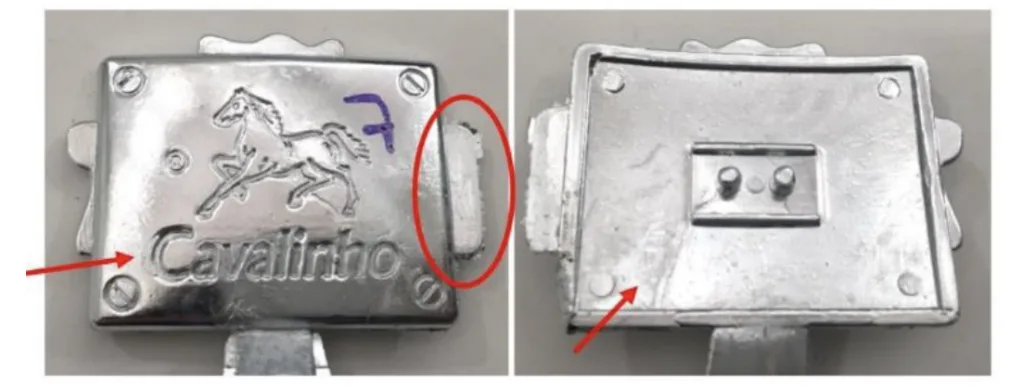
1. 개요:
- 제목: Establishing Guidelines to Improve the High-Pressure Die Casting Process of Complex Aesthetics Parts (미적 복합 부품의 고압 다이캐스팅 공정 개선을 위한 가이드라인 설정)
- 저자: F.J.G. SILVA, Raul D.S.G. CAMPILHO, Luís Pinto FERREIRA and Maria Teresa PEREIRA
- 출판 년도: 2018년
- 출판 저널/학회: Transdisciplinary Engineering Methods for Social Innovation of Industry 4.0, M. Peruzzini et al. (Eds.), IOS Press
- 키워드: Die casting, Casting, Casting defects, Zamak, Aesthetic parts. (다이캐스팅, 주조, 주조 결함, 자막, 미적 부품)
2. 초록 / 서론
본 논문은 마감 작업 최소화를 목표로 Zamak 합금 미적 부품의 고압 다이캐스팅(HPDC) 공정 최적화 문제를 다룹니다. Zamak 합금은 낮은 용융 온도로 인해 복잡한 형상 부품에 적합하지만, 미적 용도로 결함 없는 표면 마감을 얻기 위해서는 주입 변수와 금형 구성을 세심하게 제어해야 합니다. 본 연구에서는 SolidCast™ 소프트웨어를 사용한 수치 시뮬레이션과 경험적 테스트를 통해 HPDC 공정 및 변수를 조사하여 복잡한 미적 Zamak 부품의 주조에서 더 나은 결과를 얻기 위한 가이드라인을 설정합니다. 논문의 구조는 문헌 검토, 방법론, 실험 설정, 결과 및 논의, 그리고 향후 연구에 대한 제안과 함께 결론으로 구성됩니다.
3. 연구 배경:
연구 주제 배경:
경량 재료로 만들어진 복잡한 부품의 사용이 점점 보편화되고 있습니다. 고압 다이캐스팅(HPDC)은 이러한 부품을 신속하고 비용 효율적으로 생산하기 위해 자주 사용됩니다. 경량 합금인 Zamak은 기계 부품에 널리 사용되며 복잡한 마감 공정이 필요한 미적 부품에도 적용될 수 있습니다. 주요 목표는 미적 부품에 HPDC를 활용하여 마감 작업을 줄이거나 제거하고 최종 비용을 절감하는 것입니다.
기존 연구 현황:
기존 연구에서는 다이캐스팅을 특히 자동차 산업에서 기하학적으로 복잡한 금속 부품을 생산하는 주요 제조 기술로 인정하고 있습니다. HPDC 공정에는 용융 재료의 온도, 주입 압력, 주입 시간, 과압 및 응고 시간과 같은 여러 변수가 포함됩니다. 스프루, 게이트, 위치, 윤활, 두께 및 냉각 시스템과 같은 금형 설계 요소도 중요합니다. 이전 연구에서는 게이트 설계, 열 흐름, 이젝션 공정 및 주입 조건 최적화를 탐구했습니다. 유한 요소법(FEM) 기반 소프트웨어는 다이캐스팅 공정 시뮬레이션의 정확도를 향상시켰습니다. 그러나 주조 공정은 여전히 결함이 발생하기 쉬우므로 최적의 결과를 위해 변수, 열 전달 및 재료 흐름을 연관시키는 추가 연구가 필요합니다.
연구의 필요성:
시뮬레이션 및 공정 최적화의 발전에도 불구하고 HPDC 미적 부품에서 높은 표면 품질을 달성하는 것은 여전히 어려우며 종종 광범위한 마감 작업이 필요합니다. 표면 결함을 최소화하고 비용이 많이 드는 마감 공정을 줄이거나 제거하기 위해 미적 부품에 특화된 HPDC 변수 및 금형 조건을 최적화해야 할 필요성이 있습니다. 본 연구는 단일 주입 주조 공정으로 결함 없는 미적 Zamak 부품을 얻기 위한 실용적인 가이드라인을 설정하는 것을 목표로 합니다.
4. 연구 목적 및 연구 질문:
연구 목적:
본 연구의 목적은 Zamak 합금으로 만들어진 복잡한 미적 부품의 고압 다이캐스팅(HPDC) 공정을 개선하기 위한 가이드라인을 설정하는 것입니다. 목표는 단일 주조 공정에서 우수한 미적 외관을 가진 결함 없는 부품을 얻기 위해 주입 변수와 금형 구성을 최적화하여 후속 마감 공정을 최소화하는 것입니다.
핵심 연구:
핵심 연구는 다음 사항에 중점을 둡니다.
- Zamak 미적 부품의 표면 품질에 대한 주입 변수(압력, 주입 시간, 냉각 시간)의 영향 조사.
- 금형 내 재료 흐름을 이해하고 러너 시스템 및 벤팅을 포함한 금형 설계를 최적화하기 위한 수치 시뮬레이션 활용.
- 경험적 테스트와 고급 시뮬레이션을 결합하여 최적의 공정 변수 및 금형 구성을 식별하는 하이브리드 방법론 개발.
- 결함 및 마감 작업을 최소화하기 위해 복잡한 미적 Zamak 부품의 HPDC에 대한 실용적인 가이드라인 설정.
5. 연구 방법론
연구 설계:
본 연구에서는 "그림 1"에 제시된 바와 같이 "경험적 접근 방식(Empirical Approach)"과 "고급 접근 방식(Advanced Approach)"을 통합한 하이브리드 방법론을 채택했습니다. "경험적 접근 방식"은 압력, 주입 시간 및 냉각 시간과 같은 주입 변수를 체계적으로 조정하는 실험을 포함했습니다. "고급 접근 방식"은 SolidCast™ 소프트웨어를 사용한 수치 시뮬레이션을 활용하여 재료 흐름을 분석하고 금형 설계를 최적화했습니다.
자료 수집 방법:
경험적 데이터는 PR METAL, Ltd.에서 제조한 ZM3 장비를 사용한 일련의 다이캐스팅 시험을 통해 수집되었습니다. 첫 번째 주입 시험 라운드에 대해 "표 1"은 설정된 변수를 보여줍니다. 3! 요인 설계를 사용하여 각 변수 세트에 대해 3번의 시험을 수행하여 총 81번의 시험을 수행했습니다. 수치 시뮬레이션 데이터는 SolidCast™ 소프트웨어를 사용하여 생성되었으며, 다양한 금형 및 러너 구성에서 재료 흐름 및 응고를 모델링했습니다.
분석 방법:
주조 부품의 품질은 주로 표면 결함 및 금형 충전 완료 여부에 대한 육안 관찰을 통해 평가되었습니다. 시뮬레이션 결과를 분석하여 재료 흐름 패턴을 이해하고 잠재적인 결함 영역을 식별하며 금형 설계 수정의 영향을 평가했습니다. "Ishikawa 다이어그램"("그림 3")은 표면 품질 문제에 기여할 수 있는 잠재적 요인을 체계적으로 분석하는 데 사용되었습니다.
연구 대상 및 범위:
본 연구는 Zamak 5 합금의 고압 다이캐스팅에 초점을 맞추었습니다. 재료 조성은 3.8%Al, 0.95%Cu, 0.6%Mg, 0.04%Fe, 잔량 Zn이었습니다. 사례 연구 부품은 일반적으로 여성 지갑에 사용되는 미적 부품이었습니다. 실험은 단일 캐비티 금형을 사용하여 수행되었습니다. 본 연구에서는 압력, 주입 시간 및 냉각 시간의 영향을 탐구하는 동시에 금형 형상, 게이트 위치 및 벤팅 채널을 처음에는 일정하게 유지한 다음 시뮬레이션 결과를 기반으로 금형 설계를 수정했습니다.
6. 주요 연구 결과:
핵심 연구 결과:
본 연구는 미적 Zamak 부품의 HPDC 공정 개선을 위한 가이드라인 설정을 이끌었습니다. "표 2"는 첫 번째 시험 라운드의 특징적인 결과를 요약하여 다양한 변수 세트에서 "충전 부족(Lack of filling)", "작은 표면 함몰 및 균열(Small surface depression and crack)", "매우 나쁜 표면 품질(Really bad surface quality)"과 같은 결함을 보여줍니다. 시뮬레이션 및 반복적인 경험적 테스트를 통해 최적화된 변수 및 금형 설계를 식별했습니다. "표 3"은 최적화된 조건에서 가장 특징적인 결과를 제시하여 향상된 부품 품질을 달성했습니다. "그림 6"은 최적화된 금형 설계 및 변수로 얻은 부품을 보여주며, 코팅 전에 중간 마감 단계를 피할 수 있을 만큼 충분히 향상된 표면 품질을 입증합니다.
제시된 데이터 분석:
초기 경험적 시험("표 2") 결과 낮은 냉각 시간은 표면 품질 불량으로 이어지는 것으로 나타났습니다. 중간 냉각 시간에서도 결함이 나타났지만 직접적인 상관 관계를 결론짓기에는 불충분했습니다. 주입 시간은 처음에는 명확한 경향을 보이지 않았지만, 금속 속도를 높이는 주입 시간 단축은 난류 증가와 표면 품질 불량으로 이어졌습니다. 금형 충전 과정에서 난류를 줄이기 위해서는 낮은 압력이 중요한 것으로 확인되었습니다. 시뮬레이션("그림 4" 및 "그림 5") 결과 금형 위치를 반전시키고 중앙 러너를 사용하며 라이저를 통합하면 재료 흐름이 개선되고 난류가 감소하는 것으로 나타났습니다. 최적화된 변수(압력: 2 bar, 주입 시간: 0.5초, 냉각 시간: 1초)와 금형 수정이 결합되어 표면 품질이 크게 향상된 부품을 얻을 수 있었습니다.
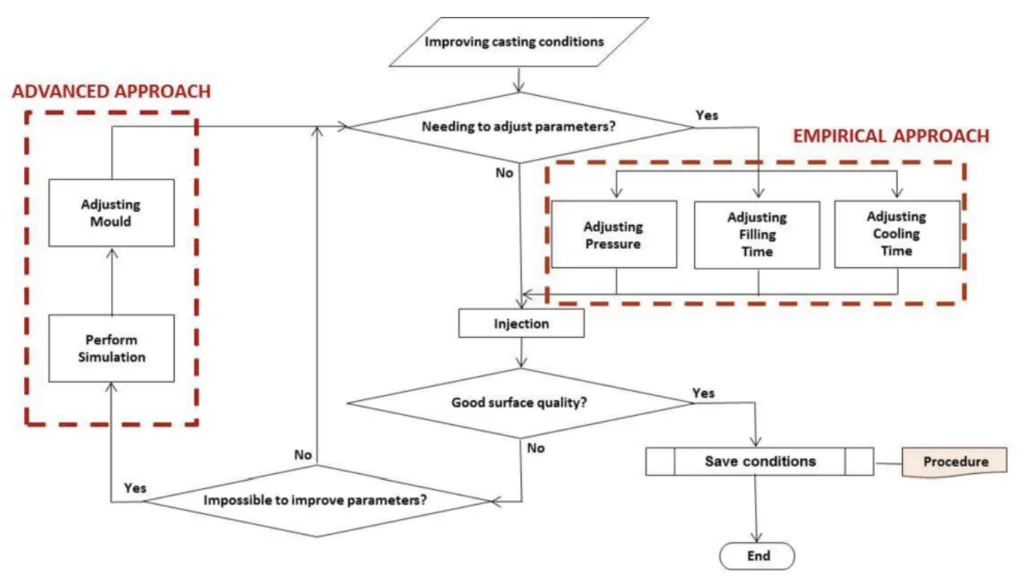
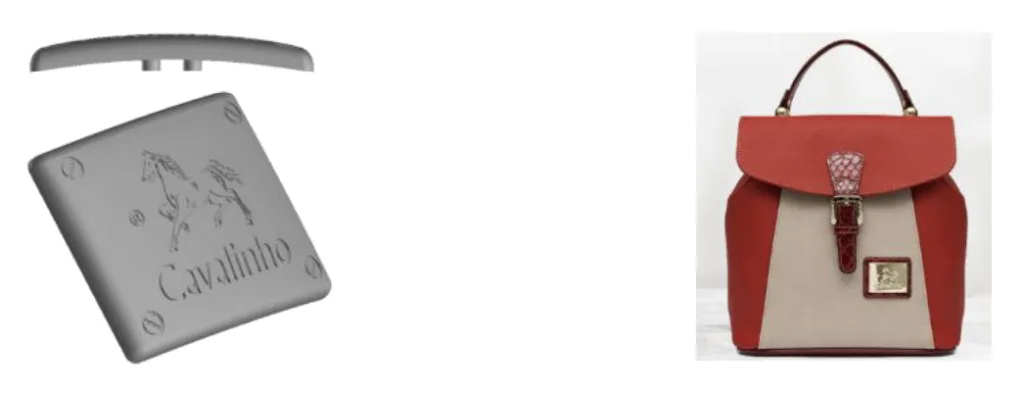
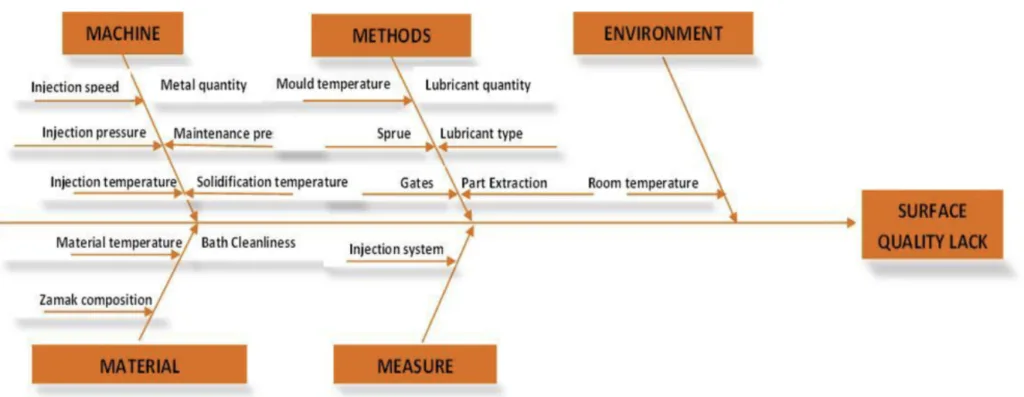
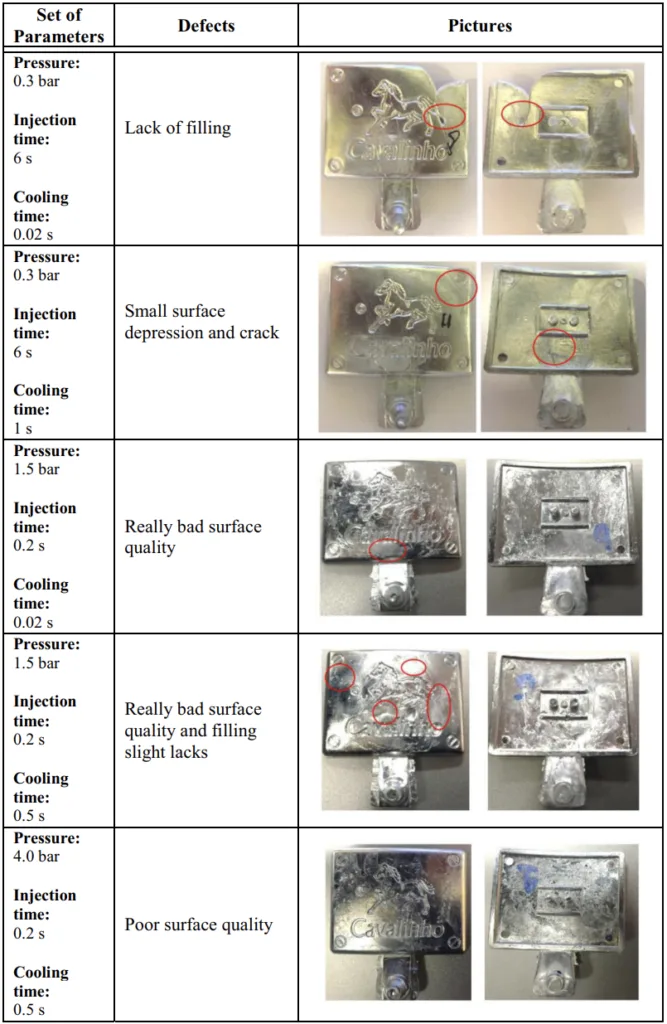
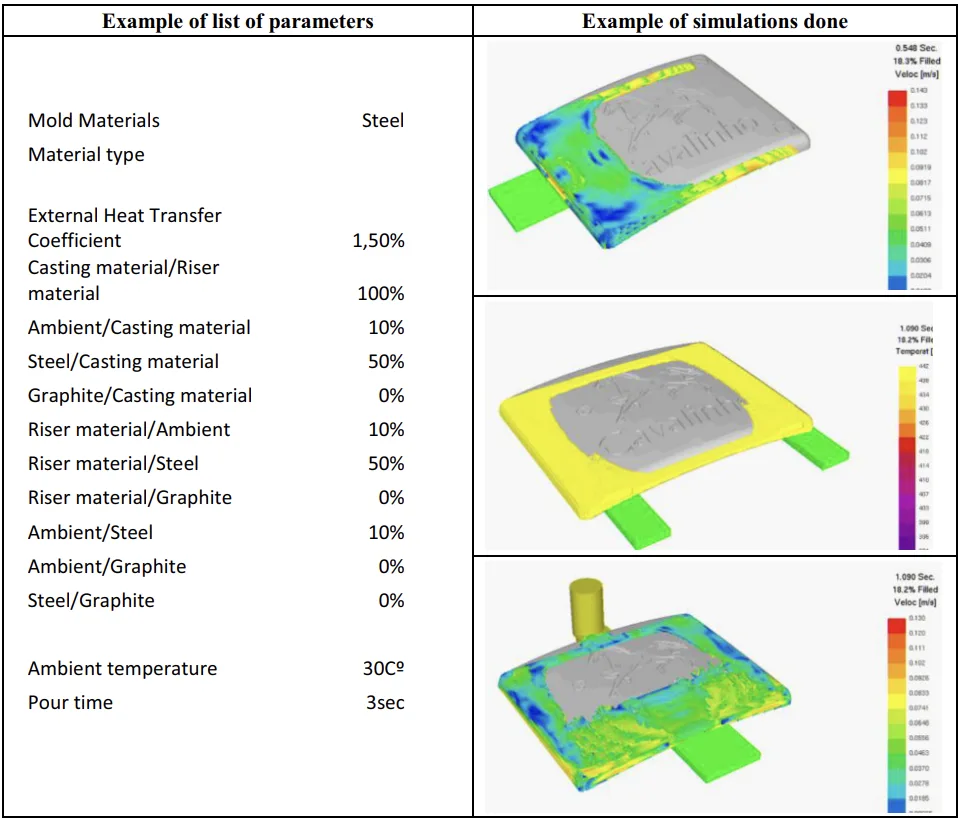
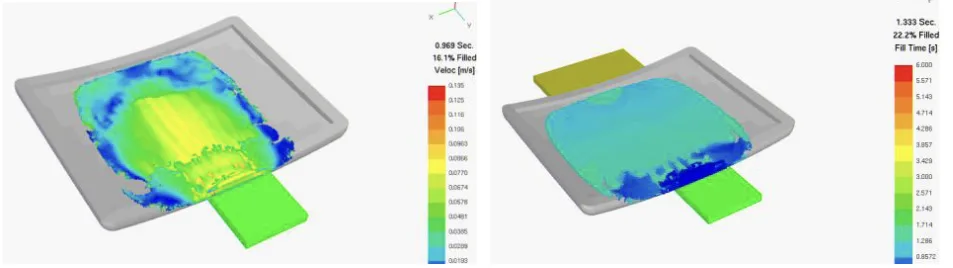
그림 목록:
- 그림 1. 본 연구에서 사용된 하이브리드 방법론의 흐름도.
- 그림 2. (a) 본 연구의 사례 연구에 사용된 부품. (b) 최종 제품에서 부품의 맥락화.
- 그림 3. 문제의 근본 원인 분석에 해당하는 Ishikawa 다이어그램.
- 그림 4. 시뮬레이션 과정에 사용된 변수와 다양한 러너 위치로 수행된 일부 테스트.
- 그림 5. (오른쪽) 금형을 반전시키고 중앙 러너를 사용한 후의 시뮬레이션; (왼쪽) 금형을 반전시키고 중앙 러너와 후방 라이저를 사용한 후의 시뮬레이션.
- 그림 6. 금형의 역 위치, 중앙 러너 및 부품의 다른 면에 있는 3개의 라이저로 얻은 부품. 부품이 완벽하지는 않지만 코팅 전에 중간 단계를 피할 수 있을 만큼 품질이 충분합니다.
7. 결론:
주요 결과 요약:
본 연구는 미적 Zamak 부품을 위한 HPDC 변수를 최적화하기 위한 하이브리드 접근 방식을 성공적으로 개발하고 검증했습니다. 설정된 주요 가이드라인은 다음과 같습니다.
- 재료 정의: 재료 유동성 및 충전 중 재료 분포에 직접적인 영향을 미치기 때문에 올바른 재료 선택이 매우 중요합니다.
- 압력: 특히 복잡한 부품 형상의 경우 난류를 최소화하기 위해 낮은 압력이 권장됩니다.
- 충전 시간: 약 25g 부품과 같이 짧은 충전 시간(약 0.5초)이 적합합니다.
- 냉각 시간: 부품 응고를 위해서는 중간 냉각 시간이 필요합니다.
- 금형 설계: 곡선 부품의 경우 중앙 부분을 아래쪽으로 향하게 하면 재료 흐름이 금형의 윗부분으로 원활하게 이동합니다. 금형 설계 최적화에는 시뮬레이션이 필수적입니다.
- 러너 설계: 중앙 러너는 여러 러너에 비해 난류를 최소화하는 데 더 적합합니다.
- 라이저: 라이저는 특히 면적 대 두께 비율이 높은 영역에서 난류가 발생하기 쉬운 부품에 고려해야 합니다.
연구의 학문적 의의:
본 연구는 HPDC와 같은 복잡한 제조 공정을 최적화하기 위해 경험적 테스트와 고급 시뮬레이션을 결합한 하이브리드 방법론의 효과를 입증합니다. 다이캐스팅 문제 해결에 대한 체계적인 접근 방식을 제공하고 미적 부품의 품질에 대한 변수 상호 작용 및 금형 설계 영향에 대한 이해에 기여합니다.
실용적 의미:
설정된 가이드라인은 다이캐스팅 엔지니어와 제조업체가 미적 Zamak 부품의 HPDC 공정을 개선하는 데 실용적인 통찰력을 제공합니다. 이러한 가이드라인을 구현하면 다음과 같은 결과를 얻을 수 있습니다.
- 주조 부품의 표면 품질 향상.
- 블라스팅 및 수동 연마와 같은 중간 마감 작업의 감소 또는 제거.
- 생산 시간 및 비용 절감.
- HPDC 부품에서 원하는 미적 결과를 달성하는 효율성 향상.
연구의 한계 및 향후 연구 분야:
본 연구는 한계를 인정하고 다음과 같은 향후 연구 방향을 제시합니다.
- 재료 흐름을 더욱 최적화하고 결함을 줄이기 위해 다양한 벤팅 위치의 영향 탐구.
- 부품 표면 품질을 향상시키기 위한 금형 캐비티의 표면 처리 조사.
- 향후 연구에서는 이러한 가이드라인을 다양한 미적 부품 형상 및 Zamak 합금에 적용하는 것을 탐구할 수 있습니다.
8. 참고 문헌:
- [1] V. Nunes, F.J.G. Silva, M.F. Andrade, R. Alexandre and A.P.M. Baptista Increasing the lifespan of high-pressure die cast molds subjected to severe wear, Surface and Coatings Technology, Vol. 332, 2017, pp. 319-331.
- [2] J. Santos, R.M. Gouveia and F.J.G. Silva, Designing a new sustainable approach to the change for lightweight materials in structural components used in truck industry, Journal of Cleaner Production, Vol. 64, 2017, pp. 115-123.
- [3] F.J.G. Silva, J. Santos and R. Gouveia Dissolution of Grain Boundary Carbides by the Effect of Solution Annealing Heat Treatment and Aging Treatment on Heat-Resistant Cast Steel HK30, Metals, Vol. 7, 2017, pp. 251-263.
- [4] F. Casarotto, A.J. Franke and R. Franke High-pressure die-cast (HPDC) aluminium alloys for automotive applications, Advanced Materials in Automotive Engineering, Vol. 6, 2012, pp. 109-149.
- [5] B. Zabala, A. Igartua, V. Scarpis, G. Timelli, F. Girot and R. Nevshupa Multiparametric study of Leidenfrost point and wettability of lubricants on high-pressure die-casting dies, International Journal of Thermal Sciences, 125, (2015). 66-73.
- [6] C. Favi, M. Germani and M. Mandolini, Analytical cost estimation model in High Pressure Die Casting, Procedia Manufacturing, Vol. 11, 2017, pp. 526-535.
- [7] W., Z. Yuan, Z. Guo and S. Xiong Characterization of A390 aluminum alloy produced at different slow shot speeds using vacuum assisted high pressure die casting, Transactions of Nonferrous Metals Society of China, Vol. 27(12), 2017, pp. 2529-2538.
- [8] H. Pinto and F. J. G. Silva, Optimisation of die casting process in Zamak alloys, Procedia Manufacturing, Vol. 11, 2017, pp. 517-525.
- [9] X. Li, Z. Guo and S. Xiong Influence of melt flow on the formation of defect band in high pressure die casting of AZ91D magnesium alloy, Materials Characterization, Vol. 129, 2017, 344-352.
- [10] K.Ch. Apparao, A.K Birru, QFD-Taguchi based hybrid approach in die casting process optimization, Transactions of Nonferrous Metals Society of China, Vol. 27(11), 2017, pp. 2345-2356.
- [11] L.X. Kong, F.H. She, W.M. Gao, S. Nahavandi and P.D. Hodgson Integrated optimization system for high pressure die casting processes, Journal of Materials Processing Technology, Vol. 201, 2008, pp. 629-634.
- [12] M.S. Dargusch, G. Dour, N. Schauer, C.M. Dinnis and G. Savage The influence of pressure during solidification of high pressure die cast aluminium telecommunications components, Journal of Materials Processing Technology, 180(1-3), 2006, pp. 37-43.
- [13] R.V. Rao, D.P.Rai, Optimization of Selected Casting Processes Using Jaya algorithm, Materials Today Proceedings, Vol. 4(10), 2017, pp. 11056-11067.
- [14] A. Hamasaiid, G. Dour, T. Loulou and M.S. Dargusch A predictive model for the evolution of the thermal conductance at the casting-die interfaces in high pressure die casting, International Journal of Thermal Sciences, Vol. 49(2), 2010, pp. 365-372.
- [15] S.H. Wu, J.Y.H. Fuh and K.S.Lee Semi-automated parametric design of gating systems for die-casting die, Computers & Industrial Engineering, Vol. 53(2), 2008, pp. 222-232.
- [16] R. Helenius, O. Lohne, L. Arnberg and H.I. Laukli The heat transfer during filling of a high-pressure die-casting shot sleeve, Materials Science and Engineering A, Vol. 413-414, 2005, pp. 52–55.
- [17] M.T. Alonso Rasgado and K. Davey Thermal models for copper-alloyed dies in pressure die casting, Applied Mathematical Modelling, Vol. 33, 2009, pp. 61–80.
- [18] P. Terek, L. Kovačević, A. Miletić, P. Panjan, S. Baloš, B. Škorić and D. Kakaš Effects of die core treatments and surface finishes on the sticking and galling tendency of Al-Si alloy casting during ejection, Wear, Vol. 356-357, 2016, pp. 122-134.
- [19] R.V. Rao, V.D. Kalyankar and G. Waghmare Parameters optimization of selected casting processes using teaching-learningbased optimization algorithm, Appl. Math. Modelling, 2014, doi: http://dx.doi.org/10.1016/j.apm.2014.04.036.
- [20] P.W. Cleary, J. Ha, M. Prakash and T. Nguyen Short shots and industrial case studies: Understanding fluid flow and solidification in high pressure die casting, Applied Mathematical Modelling, Vol. 34, 2010, pp. 2018-2033.
- [21] G.O. Verran, R.P.K. Mendes and L.V.O. DallaValentina DOE applied to optimization of aluminum alloy die castings, Journal of Materials Processing Technology, 200(1-3), 2008, pp. 120-125.
- [22] M.A. Martinez Page and S. Hartmann, Experimental characterization, material modeling, identification and finite element simulation of the thermo-mechanical behavior of a zinc die-casting alloy, Internacional Journal of Plasticity, 2017, doi: 10.1016/j.ijplas.2017.10.010.
- [23] K.-D. Bouzakis, G. Maliaris and A. Tsouknidas FEM supported semi-solid high pressure die casting process optimization based on rheological properties by isothermal compression tests at thixo temperatures extracted, Computational Materials Science, Vol. 59, 2011, pp. 133-139.
- [24] K. Domkin, J.H. Hattel and J. Thorborg Modeling of high temperature- and diffusion-controlled die soldering in aluminum high pressure die casting, Journal of Materials Processing Technology, Vol. 209, 2009, pp. 4051-4061.
- [25] H. Zhao, Y. Bai, X. Ouyang and P. Dong Simulation of mold filling and prediction of gas entrapment on practical high pressure die castings, Transactions of Nonferrous Metals Society of China, Vol. 20, 2010, pp. 2064-2070.
- [26] G.O. Verran, R.P.K. Mendes and M.A. Rossi Influence of injection parameters on defects formation in die casting All2Si1,3Cu alloy: Experimental results and numeric simulation, Journal of Materials Processing Technology, Vol. 179, 2006, pp. 190–195.
- [27] C. Tiana, J. Lawb, J. van der Touwc, M. Murraya, J.-Y. Yaod, D. Grahamd and D. St. John Effect of melt cleanliness on the formation of porosity defects in automotive aluminium high pressure die castings, Journal of Materials Processing Technology, Vol. 122, 2002, pp. 82-93.
- [28] S.G. Lee and A.M. Gokhale Formation of gas induced shrinkage porosity in Mg-alloy high-pressure die-castings, Scripta Materialia, Vol. 55, 2006, pp. 387-390.
9. 저작권:
- 본 자료는 "[F.J.G. SILVA et al.]"의 논문: "[Establishing Guidelines to Improve the High-Pressure Die Casting Process of Complex Aesthetics Parts]"을 기반으로 합니다.
- 논문 출처: doi: 10.3233/978-1-61499-898-3-887
본 자료는 위 논문을 소개하기 위해 제작되었으며, 상업적 목적으로 무단 사용하는 것을 금지합니다.
Copyright © 2025 CASTMAN. All rights reserved.