この入門記事は、"[Publisher]"によって公開された論文 "[Data Models for Casting Processes – Performances, Validations and Challenges]" に基づいています。
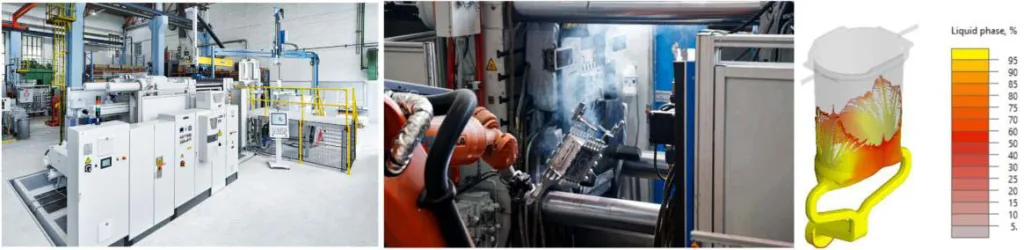
1. 概要:
- タイトル: Data Models for Casting Processes – Performances, Validations and Challenges (鋳造プロセス用データモデル – 性能、検証、そして課題)
- 著者: A M Horr, R Gómez Vázquez, and D Blacher
- 出版年: 2024年
- 出版ジャーナル/学会: IOP Conference Series: Materials Science and Engineering
- キーワード: データ駆動モデル、データ学習、データ訓練、軽金属鋳造プロセス、垂直ダイレクトチル鋳造、HPDCアプリケーション、データベース構築、データ変換、サンプリング、リアルタイムモデル構築、検証、データソルバー、インターポレーター、機械学習スキーム。
2. 抄録:
データ駆動モデルとそれに関連するデータ学習および訓練スキームは、軽金属鋳造プロセスに活用できます。本論文では、垂直ダイレクトチル鋳造および高圧ダイカスト (HPDC) アプリケーションのためのデータ訓練および学習演習とともに、データモデル構築プロセスの基礎を紹介します。効率的なデータベース構築、データ変換とサンプリング、およびリアルタイムモデル構築と検証の概念について簡単に説明します。厳密な性能研究は、2つの実世界のケーススタディに対して追加で実施されました。モデル構築手法には、データソルバーとインターポレーターのさまざまな組み合わせが適用され、データ訓練には機械学習スキームが使用されています。
3. 導入:
データ駆動型およびハイブリッド物理-データ駆動型技術は、プロセスモデリングスキームをよりデジタル指向およびサイバーベースの製造プロセスへと変革しています。これらのデジタル化変革は、より迅速かつ効果的なモデリングを通じて、エネルギー効率、生産性、およびイノベーションを促進します。鋳造プロセスは、金属およびプラスチック部品を製造するために使用されてきた最も伝統的な材料プロセスの1つです。アルミニウムやマグネシウムのような軽金属の場合、さまざまな鋳造プロセスが、妥当な強度を備えた高品質の部品を製造するために使用されています [1]。データリアルタイムおよび縮小モデルは、初期設計のペースを上げ、鋳造機械を制御することにより、これらの鋳造プロセスのデジタル化において重要な役割を果たすことができます [2]。これにより、ダウンタイムの準備とコストのかかる反復的な試行錯誤が削減され、新しいプロセス設計のための材料とコストが節約されます [3]。連続ダイレクトチル鋳造のような材料プロセスを改善する機会は数多くあります。たとえば、新しい鋳造セットアップ (合金成分など) の計画中や、適切なパラメータセットを選択する際などです。数値シミュレーションはこれらのプロセスを最適化するのに役立ちますが、単一のプロセスパラメータセットの結果を評価するには計算コストが高くなります [4]。
本論文では、効率的なデータモデルの作成、その性能、検証、および鋳造プロセスにおける課題の概要を示します。適切なデータソルバーとインターポレーターの組み合わせの役割、データ学習と訓練の効果が検討され、適用可能性と信頼性の問題が精査されました。垂直ダイレクトチル鋳造 (VDCC) および多サイクル高圧ダイカスト (HPDC) の2つの実世界のケーススタディが検討されました。プロセス入力パラメータの変動に基づく応答の予測と推定の可能性が、さらなるプロセス最適化と制御のために検討されました。
4. 研究の概要:
研究トピックの背景:
本研究は、プロセスモデリングをデジタル指向およびサイバーベースの製造へと変革する上で、データ駆動型およびハイブリッド物理-データ駆動型技術の重要性が増していることに取り組んでいます。伝統的な材料プロセスである鋳造は、データモデルによるデジタル化がエネルギー効率、生産性、およびイノベーションを向上させることができる分野として特定されました。
先行研究の状況:
洗練された多物理的有限要素 (FE) および数値流体力学 (CFD) 技術を使用した数値シミュレーションが鋳造プロセスモデリングに利用されていますが、特にさまざまなプロセスパラメータを評価するには計算コストが高くなります。この制限は、迅速なプロセス最適化と設計を妨げます。
研究の目的:
本論文の目的は、鋳造プロセス用の効率的なデータモデルの作成、性能、検証、および課題の概要を提供することです。データソルバーとインターポレーターの役割、データ学習と訓練の効果、および鋳造におけるデータモデルの適用可能性と信頼性を調査します。
コアスタディ:
本研究の核となるのは、垂直ダイレクトチル鋳造 (VDCC) と多サイクル高圧ダイカスト (HPDC) という2つの異なる鋳造プロセスに焦点を当てたケーススタディを検討することです。この研究では、さまざまなデータソルバーとインターポレーターの組み合わせを検討し、データ訓練に機械学習スキームを採用することにより、プロセス応答を予測および推定するデータモデルの可能性を探ります。この研究では、産業用鋳造アプリケーションの文脈におけるこれらのデータモデルの性能、検証、および精度を精査します。
5. 研究方法論
研究デザイン:
本研究では、垂直ダイレクトチル鋳造 (VDCC) と高圧ダイカスト (HPDC) という2つの異なる鋳造プロセスに焦点を当てたケーススタディのアプローチを採用しています。VDCCの場合、オープンソースソルバー directChillFoam を使用した流体-熱 CFD シミュレーションフレームワークが設定されました。HPDCの場合、商用CFDパッケージである NovaFlow&Solid を使用してシミュレーションを実行しました。データ駆動型モデリング手法は、両方のケーススタディに適用されました。
データ収集と分析方法:
CFD分析から得られたオフライン検証済みのシミュレーション結果を使用して、データモデル構築用のデータベースを生成しました。データ分析には、特異値分解 (SVD)、主成分分析 (PCA)、回帰分析、およびクラスタリングを含むさまざまな手法が採用されました。クリギング、放射基底関数 (RBF)、および逆距離加重法 (InvD) などのデータ補間法が活用されました。ニューラルネットワークスキームもデータ訓練のために検討されました。性能は、データモデルの予測とCFDシミュレーションの結果を比較することにより、精度と信頼性に焦点を当てて評価しました。
研究トピックと範囲:
本研究は、VDCCおよびHPDCプロセスにおける温度変化を予測するためのデータモデルの構築と検証に焦点を当てています。範囲は以下を含みます。
- CFDシミュレーションデータを使用した鋳造プロセス用データベースの構築。
- モデル構築のためのデータソルバー (SVD、PCA) およびインターポレーター (クリギング、RBF、InvD) の適用。
- 機械学習 (ニューラルネットワーク) を使用したデータ訓練の検討。
- CFDシミュレーションに対するデータモデルの性能評価と検証。
- データ感度、データベースサイズ、および検証の厳密性に関連する、鋳造プロセスへのデータモデルの適用における課題と限界の分析。
6. 主要な結果:
主要な結果:
- データモデル、特にクリギングまたは InvD インターポレーターと組み合わせた SVD を使用するデータモデルは、VDCC および HPDC プロセス両方においてリアルタイム温度予測の可能性を示しています。
- VDCCの場合、データモデルは信頼性の高い温度予測を示しましたが、凝固フロント付近など、熱勾配の高い領域では精度が低下しました。
- HPDCの場合、データベースサイズが限られているため、データモデルは温度傾向を予測できましたが、特に凝固時間を正確に予測することが困難なため、周期的な温度予測に時間ずれが見られました。
- 本研究では、急速に変化するデータを処理する必要性、データベースサイズとデータサンプリングの影響、およびさまざまなプロセス条件にわたる検証に必要な厳密性など、鋳造プロセスへのデータモデルの適用における課題を強調しました。
- ニューラルネットワーク訓練は、精度と信頼性を向上させるための潜在的な手段として提案されました。
図の名前リスト:
- Figure 1. schematic views of; a) vertical; b) horizontal and c) curved die chill casting processes (図1。概略図; a) 垂直; b) 水平; c) 曲線ダイレクトチル鋳造プロセス)
- Figure 2. HPDC machine at LKR laboratory with its typical numerical simulation (図2。典型的な数値シミュレーションを備えたLKR研究所のHPDCマシン)
- Figure 3. Basic contour results used to generate main database; a) 2D contours from simulation scenarios; b) Data processing strategy to minimize sudden thermal discontinuities between rows; c) Side view of wedge domain. (図3。メインデータベースの生成に使用される基本的な輪郭結果; a) シミュレーションシナリオからの2D輪郭; b) 行間の急激な熱的不連続性を最小限に抑えるためのデータ処理戦略; c) ウェッジドメインの側面図。)
- Figure 4. Typical CFD results for multi-cycle temperature time-history for HPDC process (six filling cycles) (図4。HPDCプロセス (6回の充填サイクル) の多サイクル温度時間履歴の典型的なCFD結果)
- Figure 5. Temperature results for computational points along contour lines; a) DOE2 and; b) DOE3. (図5。輪郭線に沿った計算点に対する温度結果; a) DOE2; b) DOE3。)
- Figure 6. Normalised error for computational points along contour lines; a) DOE2 and b) DOE3. (図6。輪郭線に沿った計算点に対する正規化誤差; a) DOE2; b) DOE3。)
- Figure 7. Time-history temperature results for CFD and data models at; a) sensor 1 and; b) sensor 4 (図7。a) センサー1およびb) センサー4におけるCFDおよびデータモデルの時間履歴温度結果)
- Figure 8. Time-history temperature results with overlying descending temperature curves; a) sensor 1, DOE 1 and; b) sensor 4, DOE 2. (図8。下降温度曲線が重なった時間履歴温度結果; a) センサー1、DOE 1; b) センサー4、DOE 2。)
7. 結論:
材料プロセスモデリングのためのデータモデルの活用は、既存のプロセスの最適化を強化し、将来のプロセス設計を加速することができます。本論文では、これらの高速データモデルに関連する性能、検証、および課題を精査し、材料鋳造プロセスに対するそれらの精度と性能を評価しました。原稿の最初の部分では、ダイレクトチル鋳造およびHPDCプロセス、ならびにそれらのモデリングおよびシミュレーション技術の簡単な表現を示し、これらのプロセスのいくつかの技術的特性について説明しました。鋳造プロセスのデータモデルの基本概念と、それに関連するデータベース構築スキームを次に示し、データソルバー-インターポレーターの組み合わせの効率的な使用について説明しました。論文の次の部分では、VDCCおよびHPDC多サイクル充填プロセスの2つの産業ケーススタディについて説明し、それらの技術的なモデリングの課題を検討しました。原稿の最後の部分では、プロセスデータモデルの性能、検証、および精度を精査し、これらの高速モデルの利用に関連する主要な課題について議論しました。
提示された結果から、データソルバーとインターポレーターの適切な組み合わせが満足のいく結果を生み出すことができることが観察できます。ただし、鋳造プロセス中の高い加熱/冷却速度の問題は、データモデルにとってある程度問題となる可能性があります。それにもかかわらず、さらなるデータ訓練と学習により、高い勾配の加熱/冷却速度を持つプロセスでも、より良い結果を達成することが可能です。最高の性能を発揮する「ソルバー-インターポレーター」の組み合わせに関するより詳細な調査の結果は、今後の出版物のトピックとなるでしょう。
8. 参考文献:
- [1] Luo, A. A. (2021). Recent advances in light metals and manufacturing for automotive applications. CIM Journal, 12(3), 79-87. https://doi.org/10.1080/19236026.2021.1947088.
- [2] Horr A. M. (2021). Optimization of Manufacturing Processes Using ML-Assisted Hybrid Technique, Journal of Manufacturing Letter, https://doi.org/10.1016/j.mfglet.2021.10.001.
- [3] Horr A. M. (2020). Notes on New Physical & Hybrid Modelling Trends for Material Process Simulations, Journal of Physics: Conference Series, 1603(1), https://doi.org/10.1088/1742-6596/1603/1/012008.
- [4] Weckman D.C., Niessen P. (1982). A numerical simulation of the D.C. continuous casting process including nucleate boiling heat transfer. Metall Trans B 13, 593-602. https://doi.org/10.1007/BF02650017.
- [5] Horr A. M, Kronsteiner J. (2021). Dynamic material process simulations: Hybrid-evolving technique, Journal of Metals, 11(12), 1884; https://doi.org/10.3390/met11121884.
- [6] Horr, A.M.; Kronsteiner, J. (2020). On Numerical Simulation of Casting in New Foundries: Dynamic Process Simulations. Metals, 10, 886. https://doi.org/10.3390/met10070886.
- [7] Lebon B. (2023). directChillFoam: an OpenFOAM application for direct-chill casting. Journal of Open Source Software, 8(82), 4871, https://doi.org/10.21105/joss.04871.
- [8] OpenFOAM-10 (2022). The OpenFOAM Foundation: https://openfoam.org.
- [9] Vreeman C.J., Schloz J.D. & Krane M.J.M. (2002). Direct Chill Casting of Aluminium Alloys: Modelling and Experiments on Industrial Scale Ingots, J. Heat Transfer 124 947-953. https://doi.org/10.1115/1.1482089.
- [10] directChillFoam Documentation. (2023). https://blebon.com/directChillFoam.
- [11] NovaFlow&Solid (2022). NovaCast Systems AB. https://www.novacast.se/product/novaflowsolid/.
9. 著作権:
- This material is a paper by "A M Horr et al". Based on "Data Models for Casting Processes – Performances, Validations and Challenges".
- Source of the paper: https://doi.org/10.1088/1757-899X/1315/1/012001
この資料は上記の論文に基づいて要約されたものであり、商業目的での無断使用は禁止されています。
Copyright © 2025 CASTMAN. All rights reserved.