この論文概要は、['軽量電気自動車の設計 (Design of Lightweight Electric Vehicles)']論文に基づいており、['ワイカト大学']に提出されました。
1. 概要:
- タイトル:軽量電気自動車の設計 (Design of Lightweight Electric Vehicles)
- 著者:トラビス・デ・フルイター (Travis de Fluiter)
- 発行年:2008年3月
- 発行ジャーナル/学会:ワイカト大学 (修士論文)
- キーワード:軽量電気自動車 (lightweight electric vehicles)、ウルトラコミューター (Ultracommuter)、チタンアルミナイド (titanium aluminide)、自動車産業 (automotive industry)、電気自動車設計 (electric vehicle design)
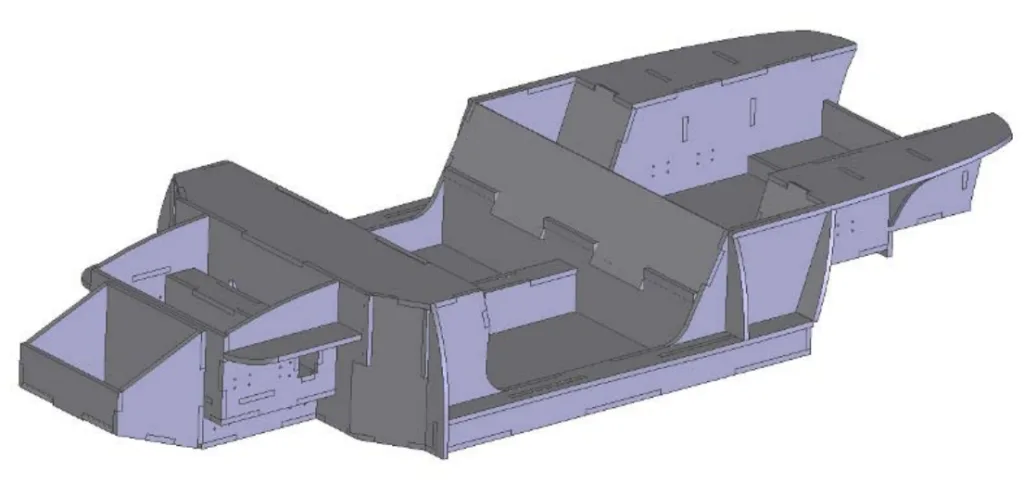
2. 研究背景:
研究テーマの背景:
本研究は、ガソリン価格の高騰とガソリン車排出ガスの環境への影響により、軽量電気自動車の重要性が増している背景から始まりました。軽量電気自動車の設計と製造は、継続的な輸送問題に対する解決策として提示されています。
既存研究の現状:
電気自動車に関する既存の研究と文献をレビューし、電気自動車の歴史、設計、開発に焦点を当てています。文献レビューでは、ハイブリッド車 (hybrid vehicles)、水素燃料電池車 (hydrogen fuel cell vehicles)、バイオ燃料 (bio-fuels)、バッテリー式電気自動車 (battery electric vehicles) など、さまざまな車両オプションを取り上げ、1880年代から21世紀までの電気自動車の開発段階に関する詳細な歴史的概要を提供します。また、軽量車両設計 (lightweight vehicle design)、自動車産業における軽量合金 (light weight alloys)、基本的な車両力学 (fundamental vehicle mechanics) についても触れています。
研究の必要性:
本研究は、原油資源の有限性と輸送部門からのCO2排出量削減の緊急性によって必要性が提起されました。ニュージーランドの個人輸送への依存度と、世界的に強化される排出規制および燃費基準は、電気自動車のような代替車両技術の必要性を強調しています。本研究は、軽量設計と高度な材料が電気自動車の実用性を向上させる可能性を探求することを目的としています。
3. 研究目的と研究課題:
研究目的:
本研究の主な目的は、輸送問題の解決策として、ウルトラコミューター (Ultracommuter) という軽量電気自動車の動作可能なプロトタイプを設計および製作することです。副次的な目的は、バッテリー式電気自動車におけるガンマチタンアルミナイド部品 (gamma titanium aluminide components) の使用の可能性を調査することです。
主要な研究内容:
主要な研究内容は以下のとおりです。
- 軽量電気自動車プロトタイプの設計と製作。
- さまざまな車両部品とシステムを統合的な設計に統合。
- 軽量化と効率向上のための高度な材料と製造技術の活用。
- ウルトラコミューターの性能と走行特性のテスト。
- 自動車部品、特に電気自動車用のガンマチタンアルミナイドの潜在的な応用分野の探求。
研究仮説:
明示的に仮説として提示されていませんが、本研究は以下の前提の下に進められます。
- 統合設計アプローチ (integrated design approach) は、成功する電気自動車開発に非常に重要です。
- 軽量設計 (lightweight design) は、電気自動車の効率を改善し、排出量を削減するために不可欠です。
- 仮想エンジニアリング技術 (virtual engineering techniques) は、電気自動車の設計と最適化に大きく貢献できます。
- チタンアルミナイド部品 (titanium aluminide components) は、軽量および材料特性により、特定の電気自動車の応用分野で性能上の利点を提供できます。
4. 研究方法論
研究設計:
本研究では、機能的な電気自動車プロトタイプの作成を中心とした設計および開発アプローチを採用しています。これには、概念設計、CAE (Computer Aided Engineering) ツールを使用した詳細なエンジニアリング設計、材料選定、製造、テストが含まれます。
データ収集方法:
データ収集方法は、研究プロセスを通じて暗示的に示されており、以下を含みます。
- 文献レビュー: 電気自動車、軽量設計、材料に関する既存の知識の収集。
- エンジニアリング設計とシミュレーション: SolidWorks および FloWorks を活用して、CAD モデリング、FEA、CFD 解析を実行。
- プロトタイプテスト: ウルトラコミューターのシャーシと車両の性能テスト、ワールドソーラーチャレンジ (World Solar Challenge) 中の走行性能評価を含む。
- 材料特性分析: チタンアルミナイドおよびその他の材料に関する既存のデータレビュー。
分析方法:
分析方法は以下のとおりです。
- エンジニアリング分析: 基本的な車両力学と物理学の原理を適用して、設計と性能を計算。
- 有限要素解析 (FEA): SolidWorks を使用して、サスペンションマウントやブレーキキャリパーなどの部品の構造解析。
- 数値流体力学 (CFD): FloWorks を使用して、空力解析と最適化。
- 性能評価: 設計仕様と実走行テストに基づいて、ウルトラコミューターの性能を評価。
- コスト分析: さまざまな生産量に対する製造コストの見積もり。
研究対象と範囲:
主な研究対象は、本研究の一環として設計および製作された軽量電気自動車プロトタイプであるウルトラコミューターです。範囲は、この車両の設計、製造、テスト、および電気自動車におけるチタンアルミナイドの潜在的な応用分野の調査を含みます。研究は、個人輸送と自動車産業の文脈、特に電気自動車技術と軽量化戦略に関連する内容に焦点を当てています。
5. 主な研究結果:
主要な研究結果:
- ウルトラコミュータープロトタイプの開発: ワールドソーラーチャレンジ (World Solar Challenge) に参加できる機能的な軽量電気自動車プロトタイプ、ウルトラコミューターの設計と製作に成功。
- 軽量設計と材料選定: シャーシにアルミニウムハニカム (aluminium honeycomb)、車体シェルにグラスファイバーを効果的に使用し、大幅な軽量化を達成。
- 空力最適化: 丸みを帯びたフロントエンド、ウィンドスクリーン設計、ファストバック (fastback) リアエンド、フルアンダーボディ、ホイールスパッツ (wheel spats) などの空力特性を実装し、低い抗力係数 (Cd 0.24〜0.25と推定) を達成。
- 電気駆動システムの統合: インホイールモーター (in-wheel motor) とトリチウムウェーブスカルプター (Tritium Wavesculptor) コントローラーの統合に成功し、高い効率を実証。
- バッテリーシステムの性能: サンダー スカイ (Thundersky) リチウムイオンバッテリーを活用し、テスト中に良好なエネルギー貯蔵と熱性能を実証。
- チタンアルミナイドの潜在力: 特にブレーキシステムやモーター部品において、軽量かつ高強度な特性を持つチタンアルミナイド部品 (titanium aluminide components) の電気自動車への潜在的な応用分野を特定。
データ解釈:
- ウルトラコミューターのテスト結果は、ハンドリングと加速の点で内燃機関車に匹敵する走行性能を示しましたが、乗り心地と高速安定性はさらなる改良が必要であることが示唆されました。
- 空力解析と効率数値は、ウルトラコミューターが低い抗力プロファイル (drag profile) を達成し、エネルギー効率に貢献していることを示唆しています。
- バッテリーテストは、サンダー スカイ (Thundersky) リチウムイオンバッテリーの満足のいく性能を示しましたが、バッテリー管理と信頼性は改善が必要な領域として特定されました。
- ブレーキキャリパー設計の FEA 解析の結果、アルミニウムと比較してチタンアルミナイドを使用した場合に達成可能な潜在的な軽量化と安全率の向上を示しました。
図リスト:
- 図 4.1 ウルトラコミューターシャーシ設計 (Ultracommuter Chassis design)
- 図 4.2 SolidWorks モデルに配置されたシャーシピースとウォータージェットカットアルミニウムハニカム (Chassis pieces laid out in SolidWorks model, and water jet cut aluminium honeycomb)
- 図 4.3 建設中のアルミニウムハニカムシャーシ (Aluminium honeycomb chassis under construction)
- 図 4.4 ロールケージ設計 (Roll cage design)
- 図 4.5 マイク・デューク博士とジン・ジャオによるシャーシテスト (Chassis testing by Dr Mike Duke and Jing Zhao)
- 図 4.6 ウルトラコミューターのインテリアモデル (Interior models of the Ultracommuter)
- 図 4.7 ウルトラコミューターインテリア (Ultracommuter Interior)
- 図 4.8 ウルトラコミューターフロントプロファイル (Ultracommuter front profile)
- 図 4.9 ウィンドスクリーンバブル (Windscreen bubble)
- 図 4.10 大型湾曲Aピラーとウィンドスクリーン遷移 (Large curved A-pillar and windscreen transitions)
- 図 4.11 ウルトラコミューターのリアエンド、クラシックファストバックデザイン (The rear end of the Ultracommuter, a classic fastback design)
- 図 4.12 FloWorks 解析 (FloWorks analysis)
- 図 4.13 ウルトラコミューター表面積 (Ultracommuter surface area)
- 図 4.14 プロトタイプヘンプ複合材ボディシェル (Prototype hemp composite body shell)
- 図 4.15 a) AlphaCam 切断プログラムの作成 b) エンジニアがウルトラコミューターボディシェルの仮想ミルをシミュレート (a) AlphaCam creating a cutting program b) An engineer simulates a virtual mill of the Ultracommuter body shell.)
- 図 4.16 a) 5軸CNC粗削り b) 仕上げ削り (a) The 5-axis CNC creates a rough cut b) the finishing cut)
- 図 4.17 モールドを取り外した後、モックシャットラインのあるプラグ (Plug after molds have been lifted with mocked shut lines on it)
- 図 4.18 グラスファイバー層でコーティングされたウルトラコミューターモールド、ブルーゲルコート (Ultracommuter mold, blue gelcoat coated by fibreglass layers)
- 図 4.19 a) モールドから取り出したばかりのウルトラコミューターボディ b) アルミニウム補強バーをラミネート (a) Ultracommuter body fresh from the mold b) Aluminium strengthening bars laminated in)
- 図 4.20 ウルトラコミュータースプリットライン (Ultracommuter Split lines)
- 図 4.21 車両に取り付けられたウルトラコミューターボディシェル (Ultracommuter bodyshell fitted to vehicle)
- 図 4.22 赤で完成したウルトラコミューターボディシェル (The Ultracommuter body shell completed in red)
- 図 4.23 ウルトラコミューターフロントサスペンション (Ultracommuter front suspension).
- 図 4.24 リアサスペンション設計 (Rear suspension design).
- 図 4.25 ホイールモーターと従来のドライブシャフトのトルクアプリケーション (Torque application of wheel motor vs conventional driveshaft)
- 図 4.26 ウルトラコミューターのアッカーマンステアリングジオメトリ (Ackerman steering geometry of the Ultracommuter)
- 図 4.27 ウルトラコミューターステアリングのピボットポイント (Pivot points of Ultracommuter steering)
- 図 4.28 ウルトラコミューターホイールとタイヤ (Ultracommuter wheel and tyre)
- 図 4.29 高電力システム概略図 (High power system schematic)
- 図 4.30 電子レイアウト (Electronics layout)
- 図 4.31 ウルトラコミューターモーター (Ultracommuter motor)
- 図 4.32 トリチウムウェーブスカルプター効率プロット (Tritium Wavesculptor efficiency plot) (www.tritium.com.au)
- 図 4.33 亜鉛空気問題の出典: www.electric-fuel.com (Zinc Air Issue source: www.electric-fuel.com)
- 図 4.34 バッテリーテストリグ (Battery testing rig)
- 図 4.35 サンダースカイセルのセル放電曲線 (Cell discharge curves for Thundersky cells).
- 図 4.36 ウルトラコミューターバッテリーパック (Ultracommuter battery pack)
- 図 4.37 WSC でのウルトラコミューター充電 (Ultracommuter Charging on WSC)
- 図 4.38 ウルトラコミューターバッテリーモニタリング – Labview および DAQ カード (Ultracommuter battery monitoring – Labview and DAQ card)
- 図 4.39 ウルトラコミューターレンジ対速度グラフ (Ultracommuter range verse velocity graph)
- 図 4.40 ウルトラコミューター LPE 照明 (Ultracommuter LPE lighting)
- 図 5.1 WSC 2007 でのウルトラコミューター走行 (Ultracommuter driving on WSC 2007)
- 図 6.1 γ-TiAl 構造 (γ-TiAl structure) (Leyens & Peters, 2006)
- 図 6.2 軽量材料の比較 (Comparisons of lightweight materials) (Leyens & Peters, 2006)
- 図 6.3 チタン製のボディを持つ 1956 年型チタンファイアバード II (The 1956 Titanium Firebird II with a body made completely from titanium source:http://www.diseno-art.com/images/firebird_II_rear.jpg)
- 図 6.4 ウルトラコミューターブレーキキャリパー FEA 比較 (Ultracommuter Brake calliper FEA comparison)
- 図 7.1 ロータスシャーシのウルトラコミューター (HybridAuto 提供) (Ultracommuter on a lotus chassis (courtesy of HybridAuto))
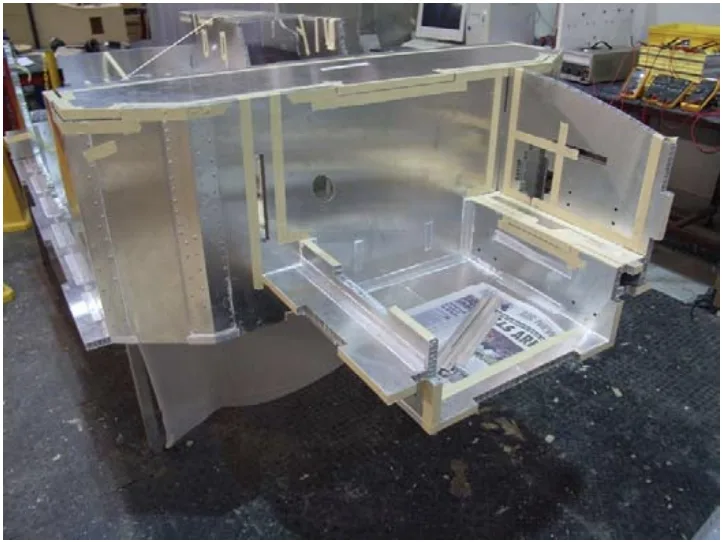
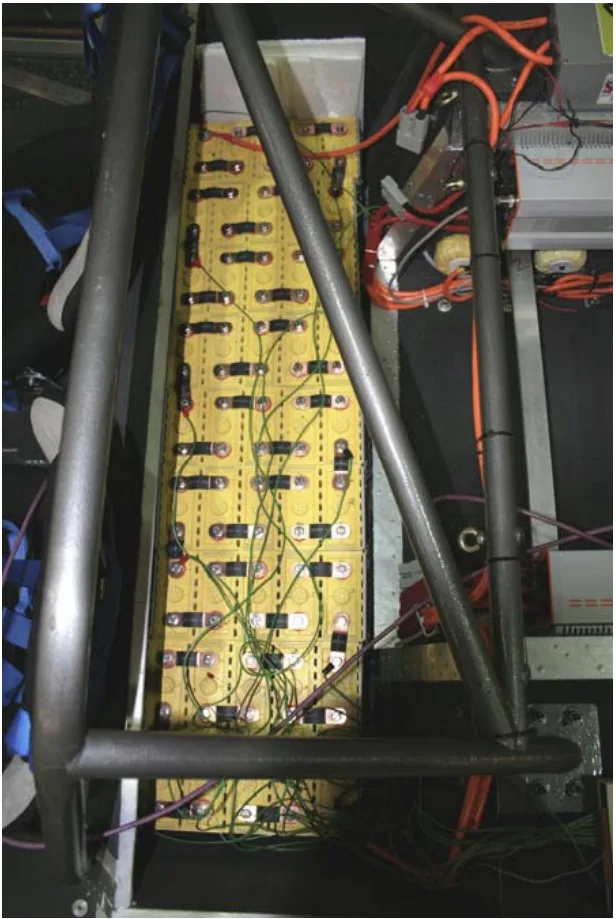
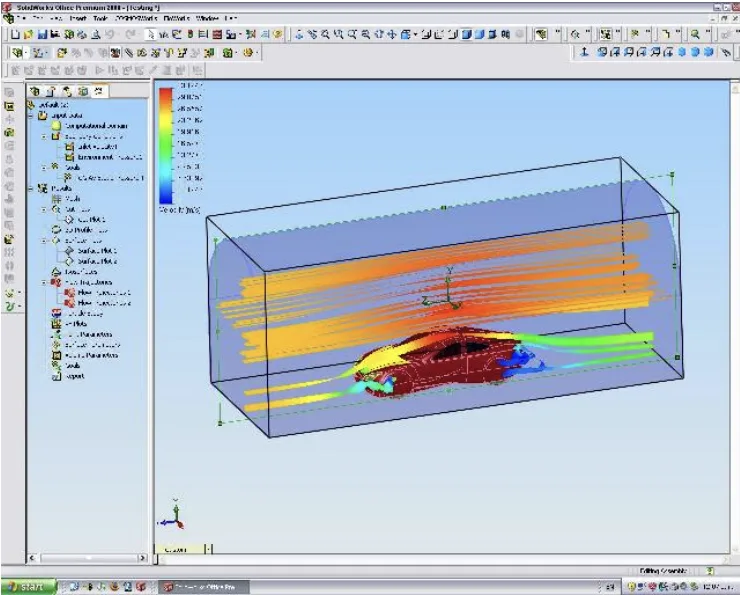
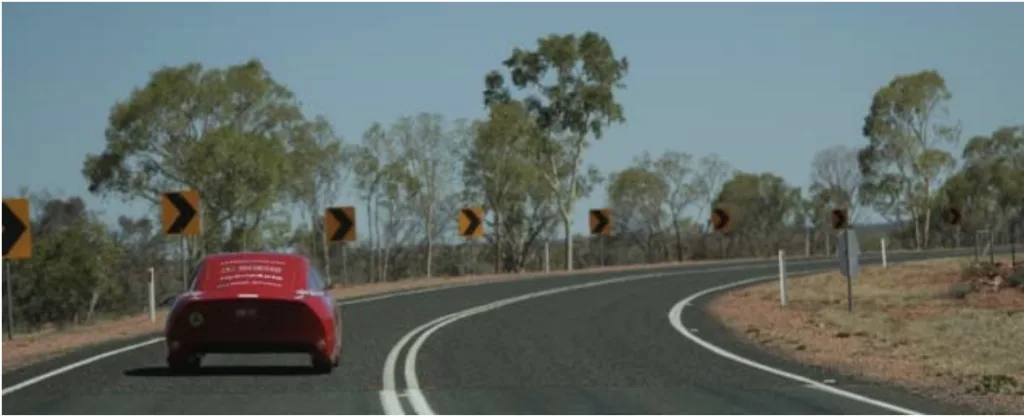
6. 結論:
主な結果の要約:
本研究は、統合設計、高度な材料、仮想エンジニアリングの活用がエネルギー効率の達成に貢献することを示す、軽量電気自動車プロトタイプであるウルトラコミューターの設計と製造に成功しました。車両はワールドソーラーチャレンジ (World Solar Challenge) に参加し、その機能性と厳しい条件下での性能を検証しました。また、本研究では、チタンアルミナイドが、特に電気自動車のブレーキシステムやモーター部品において、軽量性と高強度特性により潜在的な応用分野があることを明らかにしました。
研究の学術的意義:
本研究は、統合設計手法と高度な材料の応用に関する実践的な例を提供することにより、軽量電気自動車設計に関する知識体系に貢献しています。効率的な電気自動車の開発において、車両力学、空力特性、材料科学を考慮することの重要性を強調しています。ウルトラコミュータープロジェクトに関する詳細なドキュメントは、この分野における将来の研究開発にとって貴重なケーススタディとなります。
実用的な意味合い:
本研究は、入手可能な技術と製造技術を使用して、機能的で比較的高性能な軽量電気自動車を製造することが可能であることを示しています。この調査結果は自動車産業に実際的な意味を持ち、より効率的で持続可能な電気自動車を開発するための道筋を示唆しています。チタンアルミナイドの応用分野の探求は、車両性能の向上と軽量化のための潜在的な材料ソリューションに関する洞察を提供します。
研究の限界:
本研究では、ウルトラコミュータープロジェクト中のコストと経験の制約に関連する限界を認めています。具体的には、電子システムの信頼性が改善が必要な領域として特定されました。ハンドリングと乗り心地もさらなる改良が必要です。また、チタンアルミナイドの高コストにより、現在のところ広範な応用が制限されており、製造の最適化とコスト削減のためのさらなる研究が必要であると指摘しています。
7. 今後のフォローアップ研究:
- フォローアップ研究の方向性
今後の研究方向には以下が含まれます。- バッテリー技術の進歩: より高いエネルギー密度、改善されたバッテリー管理システム、および強化された信頼性を実現するためのバッテリー技術に関する継続的な研究。
- 統合設計の最適化: 車体シェルとシャーシの統合、および軽量化と構造効率のための部品統合の改善に焦点を当てた、統合車両設計のさらなる最適化。
- 空力特性の改良: 特にホイールスパッツ、スプリットライン、ホイールアーチ、キャビンエアフローなどの領域における詳細な空力最適化により、エネルギー消費をさらに最小限に抑える。
- チタンアルミナイド材料の研究: 鋳造および PM チタンアルミナイド部品の製造および生産方法に関する集中的な研究、ならびに自動車用途における材料の摩耗および熱特性に関する包括的なテスト。
- サスペンションとハンドリングの改善: 乗り心地と高速安定性を向上させるためのサスペンションシステムのさらなる開発と改良。
- さらなる探求が必要な分野
- 電気自動車の部品およびシステムの長期的な信頼性と耐久性試験。
- 軽量電気自動車および高度な材料の費用対効果の高い製造方法。
- 材料生産、車両運転、および使用済み廃棄物処理を考慮した電気自動車の包括的なライフサイクル評価。
- 機械式ブレーキシステムを置き換え、ばね下質量をさらに削減するための回生ブレーキシステムの探求。
8. 参考文献:
- [参考文献リストは英語の原文を参照]
9. 著作権:
- 本資料は "[トラビス・デ・フルイター (Travis de Fluiter)]" の論文: "[軽量電気自動車の設計 (Design of Lightweight Electric Vehicles)]" に基づいています。
- 論文ソース: http://waikato.researchgateway.ac.nz/handle/10289/219
本資料は上記の論文に基づいて要約されたものであり、商業目的での無断使用は禁止されています。
Copyright © 2025 CASTMAN. All rights reserved.