この論文サマリーは、['熱処理中の高圧ダイカストにおける気孔膨張挙動の3D特性評価']論文に基づき、['SSRN']に発表されたものです。
1. 概要:
- タイトル:熱処理中の高圧ダイカストにおける気孔膨張挙動の3D特性評価 (3D characterization of pores expansion behavior in high pressure die castings during heat treatment)
- 著者:Yihu MA, Wenbo YU, Zihao YUAN, Chaosheng MA, Wantong Chen, Mengwu WU, Shoumei XIONG
- 発行年:Preprint (プレプリント)
- 発行ジャーナル/学会:SSRN
- キーワード:高圧ダイカスト (High pressure die casting); 気孔膨張 (Pores expansion); 熱処理 (Heat treatment); 3D再構成 (3D reconstruction)
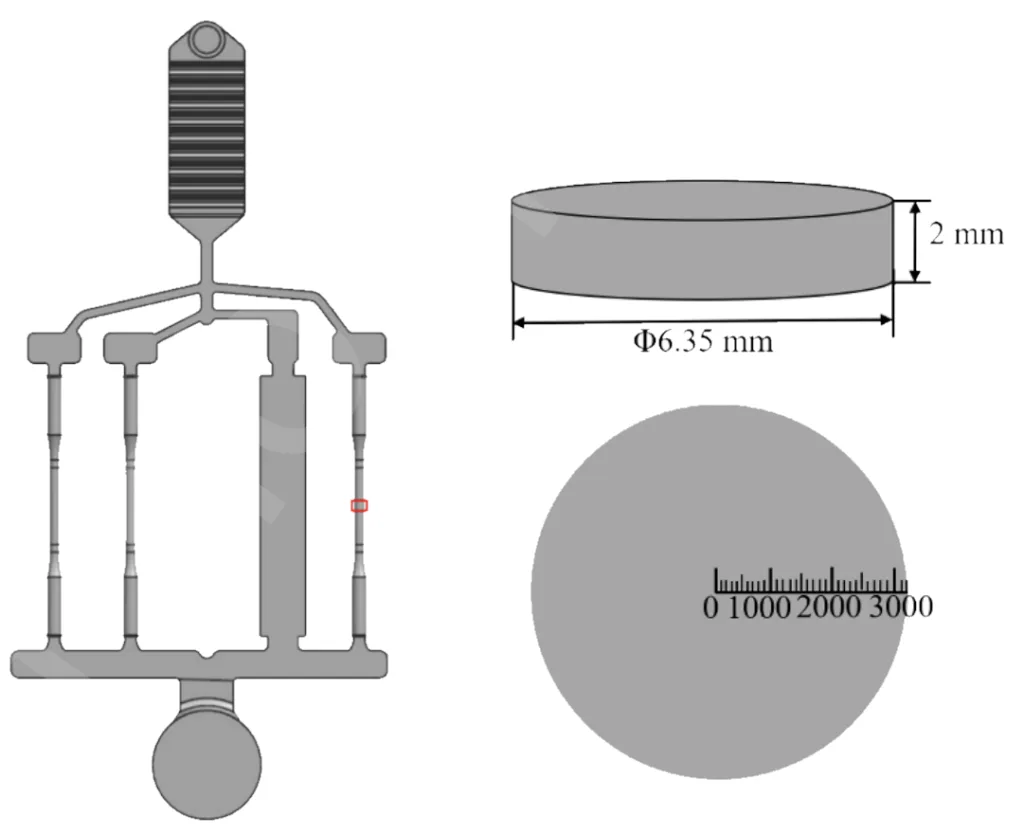
2. 研究背景:
研究テーマの背景:
熱処理は、相組成および形態を修正することにより、鋳造品の機械的特性を向上させる効率的な方法です。しかし、高圧ダイカスト (HPDC) 部品は、内在する気孔のために熱処理の適用が困難です。HPDC における熱処理中の気孔膨張は、この有益な後処理技術の適用を制限する最も重要な問題として知られています。
既存研究の現状:
既存の研究では、HPDC の気孔膨張、特に表面気孔膨張によるブローホール欠陥に焦点を当てて広範囲に研究が行われてきました。これらの表面欠陥は、部品の健全性を損ない、破損を引き起こす可能性があります。研究者らは、表面ブローホールを特性評価し、内部圧力、軸比、気孔サイズ、温度、および熱処理時間などの影響要因を特定しました。しかし、HPDC 鋳造品内部の気孔の膨張挙動に関する研究は、応力集中による機械的特性への重大な影響にもかかわらず、限られていました。
研究の必要性:
表面気孔膨張は比較的よく研究されていますが、HPDC 内部気孔の膨張挙動と鋳造品内の空間的変化はまだ十分に解明されていません。内部気孔は応力集中を引き起こし、機械的性能を低下させる可能性があるため、熱処理中の内部気孔の膨張挙動に関する包括的な理解が重要です。本研究は、鋳造品の中心領域とエッジ領域の気孔挙動を具体的に比較することにより、HPDC 鋳造品の異なる領域における気孔膨張の3D特性評価に焦点を当て、知識のギャップを解消することを目的としています。
3. 研究目的と研究課題:
研究目的:
本研究の主な目的は、HPDC 部品の熱処理中の気孔膨張現象を明らかにすることです。本研究は、高度な 3D 再構成技術を使用して、鋳造品の異なる領域、特に中心領域とエッジ領域に位置する気孔の膨張挙動を詳細に分析し、比較することを目的としています。
主要な研究内容:
本研究は、以下の事項に焦点を当てています。
- X線コンピュータ断層撮影 (XCT) 技術を使用して、真空アシスト (WV) および非真空アシスト (WOV) HPDC 鋳造品の気孔率に関する 3D 再構成を実行。
- 熱処理後の鋳造品の中心領域とエッジ領域に位置する気孔の膨張挙動を調査および比較。
- 異なる領域における個々の気孔形態の変化および体積膨張を分析。
研究仮説:
公式な仮説として明示されていませんが、本研究は以下の前提に基づいて進められます。
- 熱処理中の気孔膨張挙動は、HPDC 鋳造品内の位置 (中心 vs. エッジ領域) によって大きく異なるだろう。
- HPDC 中の真空アシストは、初期気孔率と潜在的に熱処理中の後続の気孔膨張挙動に影響を与えるだろう。
4. 研究方法論
研究デザイン:
本研究では、実験的研究デザインを採用しています。YL112 合金を使用して、真空アシストおよび非真空アシスト HPDC 引張バー鋳造品を製作しました。その後、試験片を制御された熱処理工程に適用しました。気孔膨張を評価するために、熱処理の前後で 3D 気孔特性評価を実施しました。
データ収集方法:
非破壊 3D 気孔イメージングのために、シンクロトロン X 線マイクロトモグラフィーを活用しました。実験は、中国上海シンクロトロン放射光施設 (Shanghai Synchrotron Radiation Facility, China) の BL13W1 ビームラインステーションで、30 keV の X 線エネルギーを使用して実施されました。
分析方法:
取得した XCT 画像は、phoenix datos|x 2 および Avizo 再構成ソフトウェアを使用して、気孔率の 3D 再構成を生成しました。統計分析を実施して、試験片の半径方向に沿って 100 µm 厚の円形リングにおける気孔の数密度および体積を定量化しました。熱処理前後の個々の気孔形態および体積変化も分析しました。
研究対象と範囲:
研究対象は、YL112 合金で製作された HPDC 鋳造品です。範囲は、水平コールドチャンバー高圧ダイカスト機 (TY BD-350V5) を使用して製作された引張バー試験片に限定されました。熱処理は、490°C の固溶化温度で 30 分間実施されました。分析は、引張バーの半径方向に沿った中心領域とエッジ領域の気孔膨張の比較に焦点を当てました。
5. 主要な研究結果:
主要な研究結果:
- 差次的気孔膨張: HPDC 鋳造品のエッジ領域に位置する気孔は、中心領域の気孔と比較して、熱処理中に大幅に大きな膨張を示しました。
- 定量化された膨張値: 統計分析の結果、エッジ領域の単一気孔に対する膨張値は約 120 倍であり、中心領域では約 1.5 倍でした。
- 初期気孔率に対する真空効果: 真空 (WV) で製作された鋳造品は、非真空 (WOV) で製作された鋳造品と比較して、特に中心領域において初期気孔率が低いことが示されました。
- 気孔率に対する熱処理の影響: 熱処理は、WV および WOV 試験片の両方で気孔の量とサイズを大幅に増加させました。
- 気孔率分布の均一性: 熱処理後、気孔形態分布は、初期真空条件に関係なく、中心領域からスキン層まで鋳造断面全体でより均一になりました。
データ解釈:
エッジ領域と中心領域間の気孔膨張の差は、内部圧力および凝固中の気孔形成メカニズムの変化に起因すると考えられます。著者らは、この現象をシャルルの法則 (Charles' law) を使用して説明しています。シャルルの法則は、一定の圧力下で気体の体積は温度に正比例するという法則です。熱処理中の温度上昇は、気孔内部圧力を上昇させ、膨張を誘導します。エッジ領域における大幅に大きな膨張は、中心領域と比較して、この領域の気孔の初期状態が異なることを示唆しています。
図リスト:
- Fig. 1. 中心に直径 6.4mm の引張バー 3 本と厚さ 2.5mm の板状試験片 1 個を含む鋳造概略図 (casting schematic including three tensile bars with one diameter of 6.4 mm at the center and one plate sample with a thickness of 2.5 mm)
- Fig. 2. 真空 (WV) および非真空 (WOV) で製作された鋳造品の溶体化処理前後の 3D 再構成画像 (3-D reconstructed images of castings fabricated without vacuum (WOV) and with vacuum (WV) before and after solution treatment)
- Fig. 3 WV および WOV 試験片における気孔の数密度と体積の関係 (The relationship between the number density and volume of pores in WV and WOV specimens.)
- Fig. 4. 引張バーの半径方向に沿った (a) 数密度、(b) 分率、(c) 平均気孔サイズの変化 (The variation of (a) number density, (b) fraction, and (c) average size of porosity along the radial direction in tensile bars.)
- Fig. 5: 引張バーの中心に位置する気孔の熱処理前後の形態 (The morphologies of pores locating in the center of tensile bars before and after heat treatment)
- Fig. 6: 引張バー表面付近に位置する気孔の熱処理前後の形態 (The morphologies of pores near surface of tensile bars before and after heat treatment)
- Fig. 7: さまざまな温度における YL112 の降伏強度 (Yield strength of YL112 at different temperature)
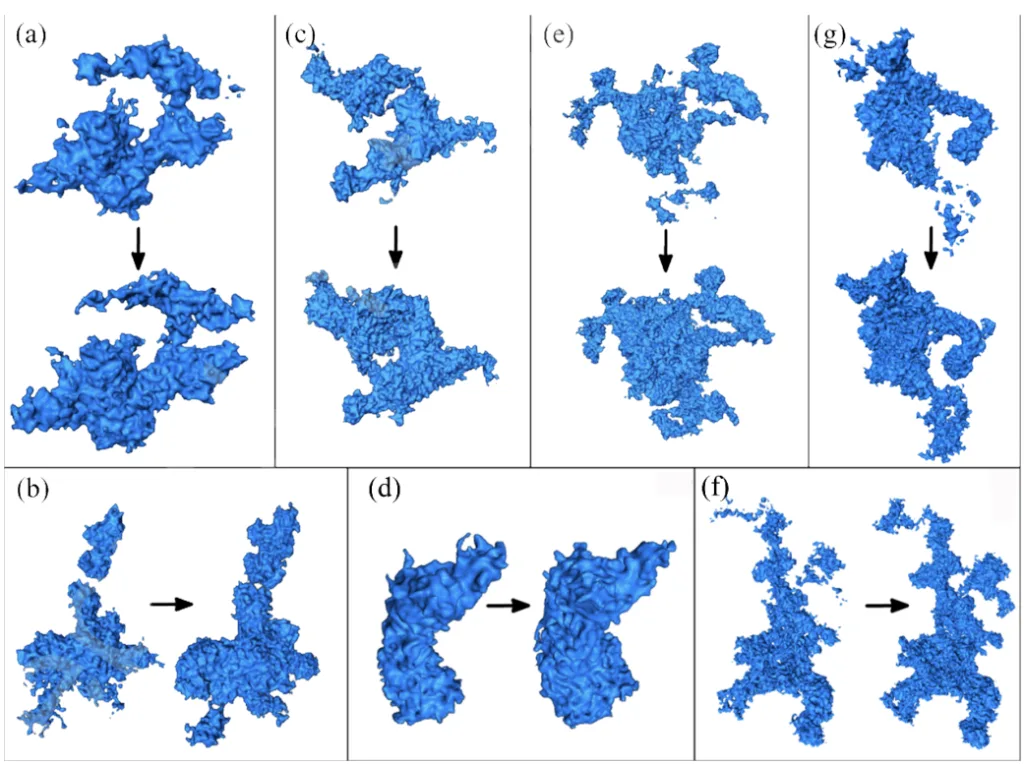
6. 結論:
主要な結果の要約:
本研究では、3D XCT を効果的に活用して、熱処理中の HPDC 鋳造品の気孔膨張挙動を特性評価しました。主な発見は、エッジ領域と中心領域間の気孔膨張に大きな違いがあり、エッジ気孔がはるかに劇的に膨張することです。鋳造中の真空適用は初期気孔率を減少させますが、後続の熱処理中の気孔膨張を防ぐことはできません。
研究の学術的意義:
本研究は、HPDC 部品における空間的に変化する気孔膨張の特性に関する貴重な洞察を提供します。詳細な 3D 特性評価および定量的分析は、熱処理中の気孔率の進化と鋳造品内の気孔位置に依存する依存性に関するより深い理解に貢献します。本研究は、熱処理後の部品性能の正確な予測のために、気孔挙動の領域別変化を考慮することの重要性を強調しています。
研究の実践的意義:
本研究の結果は、HPDC プロセスおよび熱処理パラメータの最適化に実際的な意味を持ちます。エッジ領域における強化された気孔膨張を理解することで、これらの重要な領域における気孔率を最小限に抑えるための戦略開発、潜在的には局所的なプロセス調整または修正された熱処理サイクル開発を導くことができます。これは、特に表面欠陥の減少および機械的健全性の向上という点で、鋳造品質の向上につながる可能性があります。
研究の限界点
本研究は、特定のアルミニウム合金 (YL112) と定義された熱処理条件のセットに焦点を当てています。これらの結果の他の合金、鋳造形状、および熱処理パラメータへの一般化可能性は、さらなる研究が必要です。また、本研究は膨張挙動の違いを説明していますが、異なる鋳造領域間の気孔膨張の不均衡を引き起こす根本的なメカニズムを完全に解明するためには、追加の研究が必要です。
7. 今後のフォローアップ研究:
- 今後の研究方向
今後の研究では、より広範囲の HPDC 合金と、さまざまな温度や時間などのさまざまな熱処理パラメータ下での気孔膨張挙動を調査する必要があります。射出速度や増圧などの HPDC プロセスパラメータが気孔膨張の空間分布に及ぼす影響を調査することも有益です。 - さらなる探求が必要な領域
局所的な凝固条件、ガス含有量、および応力分布などの要因を考慮して、HPDC における気孔膨張挙動を予測できる詳細な数値モデルを開発するためのさらなる探求が必要です。熱処理中のその場観察技術は、気孔膨張メカニズムとその空間的変化に関するより直接的な証拠を提供できる可能性があります。
8. 参考文献:
- [1] A. Mohamed, F.H. Samuel, A Review on the Heat Treatment of Al-Si-Cu/Mg Casting Alloys, (2012).
- [2] A.J. Ardell, Precipitation hardening, Metallurgical Transactions A, (1985).
- [3] L. Wang, P. Turnley, G. Savage, Gas content in high pressure die castings, Journal of Materials Processing Technology, 211 (2011) 1510-1515.
- [4] S.O. Wanna, H.I. Laukli, C.M. Gourlay, Feeding Mechanisms in High-Pressure Die Castings.
- [5] X. Li, S.M. Xiong, Z. Guo, Improved mechanical properties in vacuum-assist high-pressure die casting of AZ91D alloy, Journal of Materials Processing Technology, 231 (2016) 1-7.
- [6] G. Li, W. Yang, W. Jiang, G. Feng, Z. Fan, The role of vacuum degree in the bonding of Al/Mg bimetal prepared by a compound casting process, Journal of Materials Processing Technology, 265 (2018).
- [7] X. Dong, X. Zhu, S. Ji, Effect of super vacuum assisted high pressure die casting on the repeatability of mechanical properties of Al-Si-Mg-Mn die-cast alloys, Journal of Materials Processing Technology, 266 (2019) 105-113.
- [8] LUMLEY, N. R., O'DONNELL, G. R., GUNASEGARAM, R. D., GIVORD, Blister free heat treatment of high pressure die-casting alloys, Materials Science Forum, (2006).
- [9] R. Lumley, HEAT TREATMENT FOR HIGH-PRESSURE DIE-CASTING, Advanced manufacturing technology: Robotics, Rapid Prototyping, Assembly, (2008) 29.
- [10] R.N. Lumley, R.G. O'Donnell, D.R. Gunasegaram, T. Kittel-Sherri, I.J. Polmear, The role of alloy composition in the heat treatment of aluminium high pressure die castings, metallurgical science & tecnology, (2013).
- [11] 0. Ozhoga-Maslovskaja, E. Gariboldi, J.N. Lemke, Conditions for blister formation during thermal cycles of Al–Si–Cu–Fe alloys for high pressure die-casting, Materials & Design, 92 (2016) 151-159.
- [12] C. Xghab, D. Qza, E. Spma, C. Hva, C. Hbd, A. Fz, B. Ylk, Blistering in semi-solid die casting of aluminium alloys and its avoidance, Acta Materialia, 124 (2017) 446-455.
- [13] S. Midson, Q. Zhu, Y. He, H. Lu, D. Li, Controlling and Minimizing Blistering during T6 Heat Treating of Semi-Solid Castings, Diffusion and Defect Data. Solid State Data, Part B. Solid State Phenomena, (2016).
- [14] H. Toda, P.C. Qu, S. Ito, M. Kobayashi, K. Uesugi, 3D/4D observation of the micro-mechanism of blister deformation, (2012).
- [15] H. Toda, P.C. Qu, S. Ito, K. Shimizu, M. Kobayashi, Formation behaviour of blister in cast aluminium alloy, Cast Metals, 27 (2014) 369-377.
- [16] C.H. Caceres, On the effect of macroporosity on the tensile properties of the Al-7%Si-0.4%Mg casting alloy, Scripta Metallurgica et Materialia, 32 (1995).
- [17] W. Yu, C. Ma, Y. Ma, S. Xiong, Correlation of 3D defect-band morphologies and mechanical properties in high pressure die casting magnesium alloy, Journal of Materials Processing Technology, (2020) 116853.
- [18] Y.H. Ma, W.B. Yu, Y.Q. Zhou, S.M. Xiong, Influence of different high pressure die casting processes on 3D porosity distribution of Mg-3.0Nd-0.3Zn-0.6Zr alloy,中国铸造:英文版, (2021).
- [19] A. Cm, B. Wya, A. Tz, A. Zz, A. Ym, C. Sx, The effect of slow shot speed and casting pressure on the 3D microstructure of high pressure die casting AE44 magnesium alloy, Journal of Magnesium and Alloys, (2021).
- [20] V.K. Venkatasamy, Analysis Of In-cavity Thermal And Pressure Characteristics In Aluminum Alloy Die Casting, (1996).
- [21] M.S. Dargusch, G. Dour, N. Schauer, C.M. Dinnis, G. Savage, The influence of pressure during solidification of high pressure die cast aluminium telecommunications components, Journal of Materials Processing Tech, 180 (2006) 37-43.
- [22] X., P., Niu, K., K., Tong, B., H., Hu, I., Cavity pressure sensor study of the gate freezing behaviour in aluminium high pressure die casting, International Journal of Cast Metals Research, 11 (2016) 105-112.
- [23] X. Li, S.M. Xiong, Z. Guo, Correlation between Porosity and Fracture Mechanism in High Pressure Die Casting of AM60B Alloy,材料科学技术:英文版, (2016) 8.
- [24] A. Committe, Properties and selection : nonferrous alloys and special-purpose materials, Metals Handbook, 2 (1990).
9. 著作権:
- 本資料は「Yihu MA 他」の論文:「熱処理中の高圧ダイカストにおける気孔膨張挙動の3D特性評価」に基づき作成されました。
- 論文ソース:https://ssrn.com/abstract=4328099
本資料は上記の論文に基づいて要約されており、商業目的で無断使用することを禁じます。
Copyright © 2025 CASTMAN. All rights reserved.