기술 문서
- 오픈 액세스
- 게시된 날짜:2024년 5월 17일
- 이 기사를 인용하세요
- 루카스 브루크마이어 ,
- 아론 링겔 ,
- 마빈 에르크 ,
- 데이비드 베일리 ,
- 커스틴 밥진 ,
- 헨드릭 하이네만 &
- 안드레아스 뷔릭-폴라첵
초록
경량 설계는 특히 연료 집약적인 운송 부문에서 CO 2 배출을 줄이고 에너지 효율성을 향상시킬 수 있습니다. 다중 재료 설계 접근 방식은 효과적인 경량 설계를 위해 재료의 특정 특성을 결합할 수 있습니다. 산업계에서 널리 사용되는 두 가지 금속으로 만든 다중 재료 구성 요소는 알루미늄의 매우 가벼운 특성과 강철의 강도 및 구조적 무결성을 결합할 수 있습니다.
그러나 알루미늄과 강철을 결합하는 것은 서로 다른 열물리적 특성과 부서지기 쉬운 금속간 상이 형성될 수 있기 때문에 어려운 작업입니다. 하이브리드 주조에서는 고압 다이 캐스팅 공정을 통해 강판 인서트 주위에 알루미늄을 주조하여 복잡한 부품을 생산합니다. 첫 번째 접근 방식에서는 인서트에 냉가스 분사 알루미늄 코팅을 강철 기판과 용융 알루미늄 사이의 결합제로 테스트했습니다.
접합은 야금학적 결합과 마이크로 클램핑을 결합하여 이루어졌습니다. 두 번째 옵션으로, 수정된 냉간 압연을 통해 언더컷이 있는 표면 구조를 강판에 적용했는데, 이를 통해 용융된 알루미늄이 채널로 흘러 들어가 견고한 강과 맞물릴 수 있었습니다.
인서트 구조의 다양한 방향을 테스트했습니다. 또한, 전처리 기술의 긍정적인 효과를 잠재적으로 향상시키기 위해 두 가지 접근법의 조합이 사용되었습니다. 접합 강도의 중요성을 고려하여 이러한 접근법의 품질은 정적 인장 테스트와 동적 피로 테스트를 통해 테스트되었습니다.
결과는 코팅에 의한 접합이 공정 온도에 크게 영향을 받는다는 것을 보여줍니다. 표면 구조에 의한 접합 개선은 용융 흐름 방향에 따라 달라집니다.
복합 주조 및 마찰 교반 용접을 통한 주조 알루미늄과 강철의 하이브리드 접합
제 16조 2023년 1월
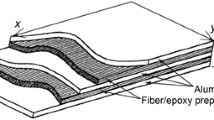
하이브리드 판금 부품의 공정 설계
2015년 12월 12 일
소개
항공우주 및 자동차 산업의 에너지 효율적인 혁신 요구 사항을 충족하려면 상당한 중량 감소가 필수적입니다. 경량 설계로 CO 2 배출을 줄이거나 차량 주행 거리를 늘릴 수 있습니다. 경량 설계를 달성하는 한 가지 방법은 다중 재료 구성 요소를 개발하는 것입니다. 1 이러한 구성 요소는 다양한 재료의 유리한 특성을 결합합니다. 일반적인 응용 분야는 차체나 항공기에 사용되는 다용도 강철과 알루미늄으로 만들어진 다중 재료 구성 요소입니다. 강철의 강도와 연성과 낮은 밀도의 알루미늄이 결합되어 경량 설계에 큰 잠재력을 제공합니다. 서로 다른 열물리적 및 야금학적 특성과 알루미늄과 강철의 부서지기 쉬운 금속간 상 형성으로 인해 융합 용접과 같은 일반적인 접합 기술을 사용할 수 없습니다. 2 따라서 강철과 알루미늄으로 만들어진 다중 재료 구성 요소에는 틈 없는 접합으로 안정적인 연결을 가능하게 하는 새로운 접합 기술 이 필요합니다.
최신 기술
서로 다른 재료의 접합은 종종 성형 공정을 통해 이루어지며, 이는 야금학적 접합 공정과 기계적 접합 공정으로 나눌 수 있습니다. 4 냉간 또는 마찰 교반 용접과 같은 공정을 통해 기존 융합 용접의 문제 없이 야금학적 접합이 가능합니다. 클린칭, 리벳팅 또는 헤밍과 같은 공정에서 재료는 변형되어 기계적 인터로크를 생성합니다. 그러나 이러한 프로세스는 일반적으로 설계 유연성이 제한되거나 국부적인 연결만 제공합니다. 복합 부품의 복잡한 형상의 경우 금속을 사용한 하이브리드 주조는 큰 잠재력을 제공합니다. 5 폴리머를 이용한 하이브리드 성형으로 알려진 6 이 공정은 일반적으로 고체 인서트의 전처리와 액체 성분의 조립이라는 두 단계로 구성됩니다. 인서트의 표면 구조화가 필요한 기계적 인터록을 통해 연결에 도달할 수 있습니다. 여기에는 미세 가공, 천공 7개 , 스탬핑 8개, 전자 및 레이저 빔 조각 10 과 같은 절삭 공정과 인서트 표면에 볼 헤드 핀 11 또는 나노스파이크 12 를 생성하기 위한 선택적 레이저 용융과 같은 추가 공정이 포함됩니다. 또한 하이브리드 주조는 야금학적 결합 가능성을 제공합니다. 강철 인서트에 다양한 코팅을 사용하여 알루미늄 주물에 7.7MPa의 전단 결합 강도를 달성했습니다. 13
이 작업에서는 강판으로 만든 성형 부품을 주조 금형에 직접 삽입하고 그 주위에 용융 알루미늄을 주조하여 구조 부품을 생산하는 고압 다이 캐스팅(HPDC) 공정을 사용했습니다. 14 다이 캐스팅 공정 14 의 짧은 응고 시간과 알루미늄과 강철 15 의 서로 다른 팽창 거동으로 인해 접합 공정이 복잡해집니다. 반면, 공정 시간이 짧기 때문에 금속간 상이 형성될 위험은 무시할 수 있습니다. 국부적인 접합 대신 대면적 접합을 생성하기 위해 열 분사(TS) 코팅 과 언더컷 (17) 이 있는 표면 구조가 연구되었습니다.
표면 납땜된 Cu 코팅 및 저온 가스 분사(CGS) EN AW-7075 코팅은 복합 주조 응용 분야에서 결합 접착력을 높이기 위한 접근 방식으로 조사되었습니다. 16 , 18 이 연구에서는 코팅 형태와 특성에 대한 포괄적인 분석이 수행되었으며 TS가 HPDC 응용 분야에 코팅을 적용하는 데 매우 적합한 것으로 나타났습니다. EN AW-7075로 제작된 코팅의 경우 강철 기판에 대한 결합은 기계적 마이크로 클램핑을 통해 이루어졌습니다. 조사된 코팅을 열처리하면 연성이 크게 증가할 수 있는 것으로 나타났습니다. 19 마지막으로, 알루미늄 다이캐스팅과 코팅의 금속학적 결합은 액체 금속과 고체 코팅 사이의 확산 과정을 통해 이루어집니다. 이러한 방식으로 강철과 알루미늄 다이캐스팅의 접합이 가능해집니다. 복합 주물 생산에 대해 실험실 규모의 테스트가 수행되었으며 복합재 구역이 단면에서 관찰되었습니다. 첫 번째 결과는 이미 이러한 코팅의 높은 잠재력을 나타냈습니다. 20 에서는 알루미늄 다이캐스팅 합금의 습윤 거동을 코팅되지 않은 부품과 코팅된 부품에 대해 조사했습니다. 코팅으로 인해 젖음 각도가 상당히 작아질 수 있으며 이는 HPDC 응용 분야에 긍정적인 효과입니다.
대안적인 다중 패스 압연 공정에서 프로파일 롤러는 첫 번째 패스에서 직사각형 채널 구조를 각인합니다(그림 1 ). 연속 패스에서는 플랫 롤러로 리브를 평평하게 만듭니다. 리브 팁이 수평으로 퍼져서 다이캐스트 용융물과 맞물리는 언더컷을 만듭니다. 17
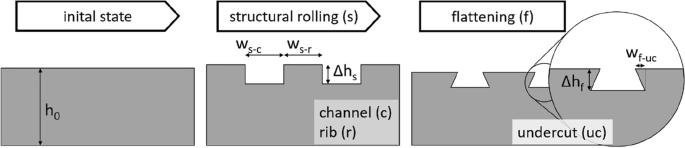
다이캐스트 금속은 채널로 유입될 수 있으며 응고되자마자 연동 연결이 설정됩니다. 또한, 연동은 알루미늄 용융물의 수축을 방지할 수 있습니다. 16 결과적인 접합 강도는 언더컷 폭에 따라 결정적으로 달라집니다.승에프-유씨. 실험실 규모 표본에 대한 전단 테스트 결과는 최대 결합 강도가 45 MPa인 것으로 나타났습니다. 21 또한 냉간 압연을 통해 냉간 분사 EN AW-7075 코팅의 성형성을 조사한 결과 최대 16%의 두께 감소가 달성되었습니다. 22
하이브리드 주조의 다양한 접합 공정에 대한 이전 및 추가 조사를 위해 고압 다이 캐스팅 공정에 대한 산업 중심의 시연 부품이 Foundry Institute(GI)에서 개발되었습니다(그림 2e ). 8 현재 연구에서는 시연 부품에 대한 두 가지 다른 전처리 접근법을 사용하여 강철과 알루미늄 사이의 신뢰성 있고 틈 없는 접합에 중점을 둡니다. 복합 주물의 강도 특성은 차체 구조에 사용하는 데 매우 중요합니다. 따라서 코팅 및 구조화된 강판 인서트가 포함된 하이브리드 부품의 인장 강도 및 동적 하중 용량을 테스트했습니다(그림 2a ,b). 한편, EN AW-7075 합금 코팅은 CGS를 사용하여 강철 인서트에 적용되었습니다. 용융물과 코팅 사이의 야금학적 결합에 대한 온도 영향을 조사하기 위해 용융물과 다이 온도의 변화가 수행되었습니다. 한편, 기계적 맞물림이 가능하도록 냉간 압연 공정을 통해 표면 구조화를 수행하였다. 표면구조의 크기는 인장강도와 선형적으로 상관관계가 있는 것으로 가정된다. 따라서 더 넓은 구조를 테스트했습니다(그림 2c ). 또한 구조의 방향(주 충전 방향에 대한 세로 또는 가로)이 복합 강도 및 하중 지지 능력에 영향을 미치는지 여부는 알 수 없습니다(그림 2d ). 더욱이, 두 접근법의 조합은 전처리 기술의 긍정적인 효과를 향상시키기 위해 테스트되었습니다(그림 2e ).
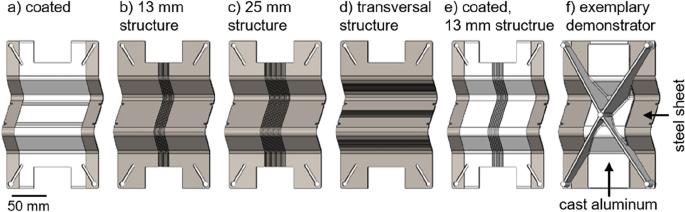
재료 및 방법
재료
시연 부품의 사용 사례에는 강하고 연성인 기본 재료가 필요합니다. 연구의 초점은 부품의 전체 하중 지지 능력이 아니라 복합 강도에 있기 때문에 강판 인서트에는 성형성이 좋은 2mm 두께의 DC04 시트가 선택되었습니다. 그럼에도 불구하고, 이 접근법을 다양한 고강도 강철에도 적용할 수 있도록 하는 것이 목적입니다. 구부러지지 않은 강판 인서트의 외부 윤곽은 길이 203.5mm, 너비 109mm였습니다(그림 3 ). 코팅에는 고강도 알루미늄 합금 EN AW-7075가 사용되었습니다. 23 독일 Bitterfeld-Wolfen 소재 Eckart TLS GmbH의 분말은 +63 -20 µm의 입자 분율을 가졌습니다. 코팅은 CGS 공정으로 적용되었으며, 이는 높은 밀도와 균질성, 우수한 기계적 특성을 제공합니다. 다이캐스팅에는 1차 알루미늄 합금 EN AC-43500 24 가 사용되었으며, 이는 강도가 좋고 밀도가 낮으나 열처리를 하지 않으면 연성이 낮습니다.
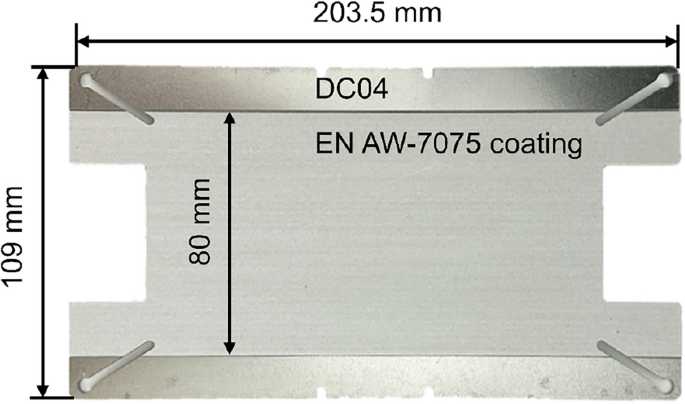
강판의 저온 가스 분사
준비를 위해 시트를 p = 6 bar의 압력에서 F20 그레인 커런덤으로 양면에서 분사한 다음 에탄올로 세척했습니다. 이 공정은 표면에 산화물과 불순물이 미치는 영향을 최소화하기 위해 필요합니다. 동시에, 표면이 거칠어지고, 결과적으로 생긴 거칠기에 기계적 클램핑을 통해 알루미늄 코팅을 더욱 강력하게 접착할 수 있습니다. EN AW-7075 코팅은 CGS에 의해 강판에 적용되었습니다. 이 공정은 높은 입자 속도와 낮은 온도를 특징으로 하여 산화물 함량이 낮고 밀도가 높은 코팅이 생성됩니다. 새로 형성되는 산화물의 영향을 더욱 줄이기 위해 표면 활성화 직후에 코팅을 적용했습니다. 코팅 공정에 사용된 매개변수는 표 1 에 나와 있습니다 .표 1 용사 공정 CGS의 공정 매개변수
CGS 공정에는 스위스 Pfäffikon 소재 Oerlikon Metco의 Kinetics 8000 콜드 스프레이 시스템이 사용되었습니다. 80mm 너비의 중앙 스트립이 시트 전체 길이를 따라 양면에 코팅됩니다(그림 3 ). 코팅의 경우 균일하고 평평한 코팅을 적용하기 위해 로봇의 도움으로 CGS 건을 강판 위에서 구불구불한 패턴으로 움직였습니다.
강판 인서트 생산
강판 인서트는 4가지 공정 단계로 생산되었습니다. 폭 160mm, 길이 500mm의 코팅되지 않은 시트와 코팅된 시트를 먼저 압연하여 구조화했습니다. 그런 다음 시트를 길이 203.5mm, 너비 109mm의 형상으로 워터젯 절단했습니다. 그 후, 다이캐스팅을 위해 시트를 인서트 형상으로 구부렸습니다. 중간 단계에서는 인서트의 가장자리를 디버링하고 표면을 초음파 욕조에서 세척한 후 인서트를 다이캐스팅으로 가공했습니다.
강판의 구조적 압연
압연은 독일 Schopfheim 소재 Dreistern GmbH & Co. KG의 P3.160 롤 성형 기계에서 수행되었습니다. 첫 번째 패스에는 반경 92.5mm, 구조적 폭 13mm의 프로파일 롤러가 사용되었습니다(그림 4 ). 프로파일은 각각 너비가 1.0mm, 깊이가 0.5mm인 7개의 리브와 6개의 채널로 구성됩니다. 더 넓은 구조의 경우 중간 구조화 단계가 수행됩니다. 이 롤러는 첫 번째 패스와 동일한 리브 및 채널 형상을 사용하여 기존 구조의 양쪽에 추가로 6mm의 구조적 폭을 각인했습니다. 평탄화 패스에는 반경 93.0mm의 플랫 롤러가 사용됩니다. 압연 속도는 5.8m/min으로 설정되었습니다.
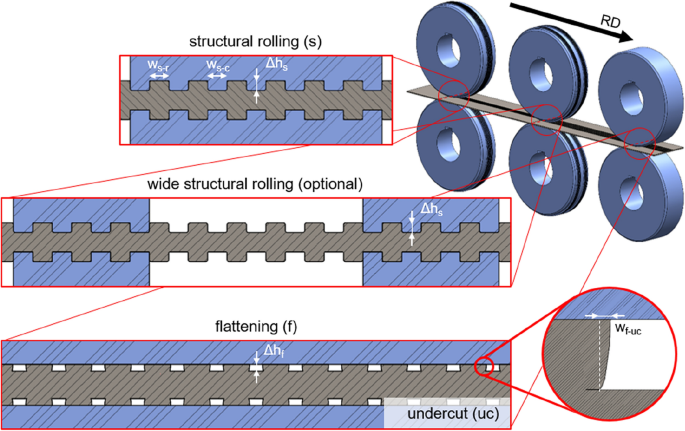
Keyence VHX-7000(일본 오사카) 디지털 현미경을 사용하여 기하학적 측정을 위해 단면 샘플을 채취했습니다. 첫 번째 패스에서는 약 깊이의 채널이 사용됩니다. 479μm(Δ시간에스)이 시트 표면에 각인되었습니다. 생성된 리브는 편평해졌으며 평균 채널 깊이는 다음과 같습니다.Δ시간에프=333 µm 및 평균 언더컷 폭승에프-유씨=58μm. 그러나 현미경 사진 준비(그림 5a )에서는 바로 바깥쪽 채널이 안쪽에만 언더컷을 형성한 것으로 나타났습니다. 따라서 각 측면에서 채널 너비의 절반을 빼서 12mm의 인터로킹에 효과적인 구조 너비가 되었습니다. 이러한 외부 채널은 더 넓은 구조의 선택적인 두 번째 구조화 단계에서 다시 형성되었습니다. 그러나 두 개의 구조적 롤링 패스 정렬의 정확성은 밀의 정밀도에 의해 제한되었습니다. 이로 인해 첫 번째와 두 번째 구조화 패스 사이에 언더컷 형성이 감소된 전이 영역이 생겼습니다(그림 5b ). 더 넓은 구조의 경우 다가오는 복합 강도 분석을 위해 24mm의 유효 폭이 가정되었습니다. 도금 강판을 조직화할 때 도금의 플레이킹이 관찰되었습니다. 따라서 통계적으로 유의미한 기하학적 측정값을 얻을 수 없습니다. 다가오는 화합물 강도 분석을 위해 50mm 코팅과 12mm 구조의 평균 화합물 폭은 31mm로 계산되었습니다(그림 6 ).
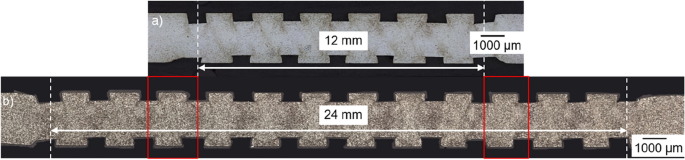
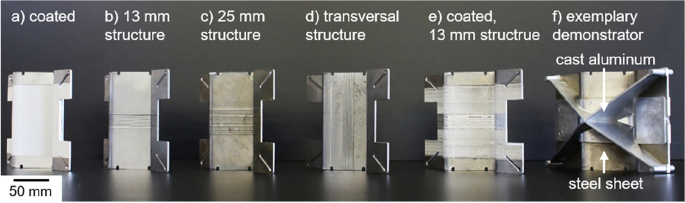
강판 인서트의 굽힘
강철 시트 인서트는 Trumpf Trumabend V50(Ditzingen, Germany) 프레스 브레이크에서 구부러졌습니다. 형상에는 82°와 133°의 두 배로 4번의 굽힘 작업이 필요했습니다. 반경이 5.0mm인 펀치와 개구부가 16mm인 다이가 사용되었습니다. 굽힘 후, 굽힘 곡률에서 가장자리를 디버링했습니다.
데몬스트레이터 부품의 고압 다이캐스팅
주조 시험은 공칭 잠금력이 6,900kN인 Bühler H630-SC 저온 챔버 고압 다이캐스팅 기계에서 수행되었습니다. 상업적인 상표명 Silafont-36 및 Trimal-05, 18을 갖는 AA 365로도 알려진 알루미늄 합금 EN AC 43500 은 저항로에서 용융된 후 아르곤을 이용한 회전 탈기 처리로 1.0 미만의 밀도 지수로 처리되었습니다. 진공 밀도 테스트. 화학적 조성은 표 2 에 제시되어 있다 .표 2 주조 알루미늄 EN AC 43500의 화학 성분
기존의 고압 스프레이 공정으로 이형제를 도포한 후 인서트를 실온에서 다이에 배치했습니다(그림 7 ). 그런 다음 하이브리드 부품용 인서트 주변의 보강 구조를 주조하기 전에 Wollin 용융 투입 장치에 부착된 예열된 세라믹 복합 래들을 사용하여 계량 공정을 수행했습니다.
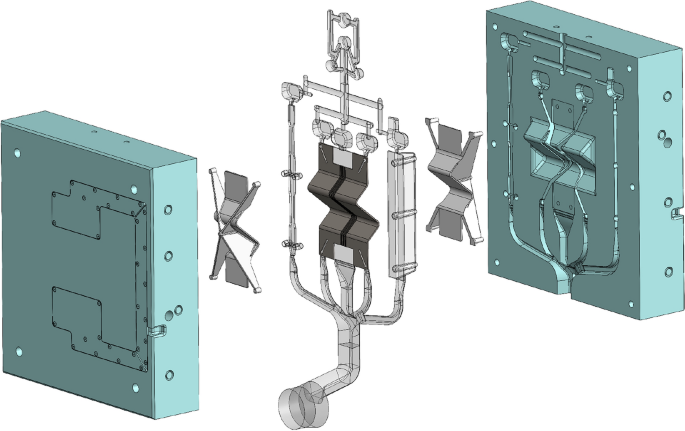
샷 슬리브와 다이 모두 온도 조절 유체인 오일을 사용하여 온도 조절되었으며 온도는 내장된 열전대로 확인되었습니다. 수행된 주조 시험의 매개변수는 표 3 에 나열되어 있습니다 .표 3 전도 캐스팅 시험의 경계 조건
테스트된 각 매개변수 세트에 대한 ID를 제공하는 실험 설계가 표 4 에 표시되어 있습니다 . ID 1은 코팅이나 표면 구조화 공정이 적용되지 않은 기준으로 사용됩니다. 다양한 용융 및 공구 온도에서 EN AW-7075 코팅의 금속 결합 기여도를 결정하는 데 사용된 실험은 ID 2-4입니다. 또한 ID 5-7은 구조의 다양한 방향과 너비의 영향을 조사합니다. 마지막으로 ID 8은 표면 코팅과 구조를 모두 결합합니다.표 4 코팅 및 구조의 영향을 분석하기 위한 실험 설계
데모 부품의 동적 및 정적 테스트
동적 테스트를 위해 시연 부품을 Schenk의 250kN 서보 유압 기계의 3점 굽힘 고정 장치에 배치했습니다(그림 8 ). 시편의 짧은 면을 원통형 막대 위에 놓고 돔을 펀치로 하중을 가했습니다. 20Hz의 주파수에서 16.5kN의 중심 하중과 13.5kN의 진폭. 선택한 매개변수의 경우 샘플의 온도 증가가 관찰되지 않았습니다. 변위 증가에 의해 균열 발생이 감지될 때까지의 하중 사이클 수를 측정합니다.
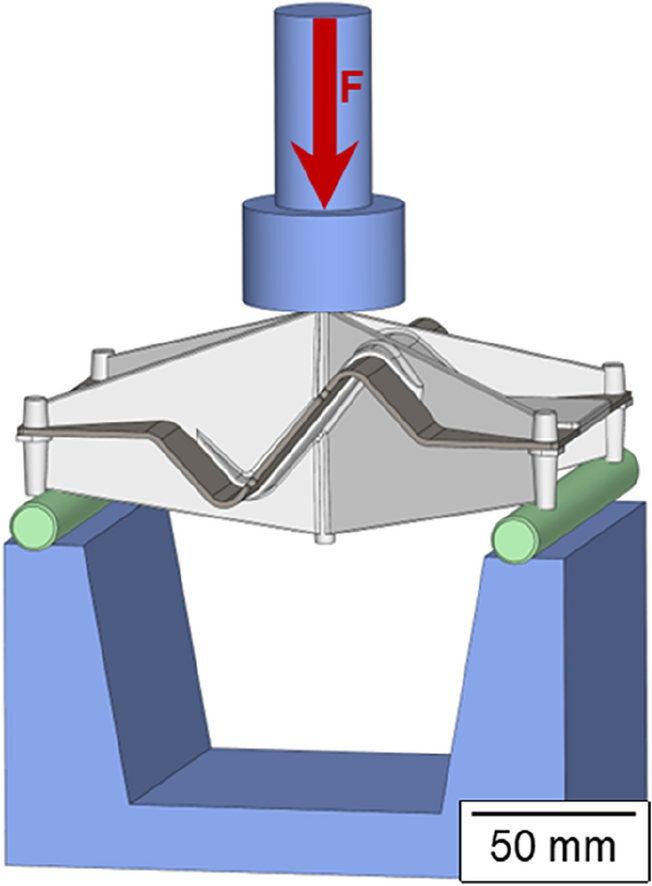
정적 테스트를 위해 이전에 표시된 대로 최소 힘 적용을 위해 제어된 유압 피드가 있는 수평 띠톱을 사용하여 시연 부품(그림 9 ) 의 중앙 섹션에서 샘플을 추출했습니다 . 25 형상이 평면 결합 영역을 가지므로 다음이 가능했습니다. 법선 방향으로 명시적으로 화합물 강도를 테스트합니다. 형상 일치 그립을 사용하여 Zwick Z100 인장 시험기에 샘플을 설치했습니다. 시편에 파손 지점까지 하중을 가하고 힘 강하를 감지하여 최대 힘을 측정했습니다.
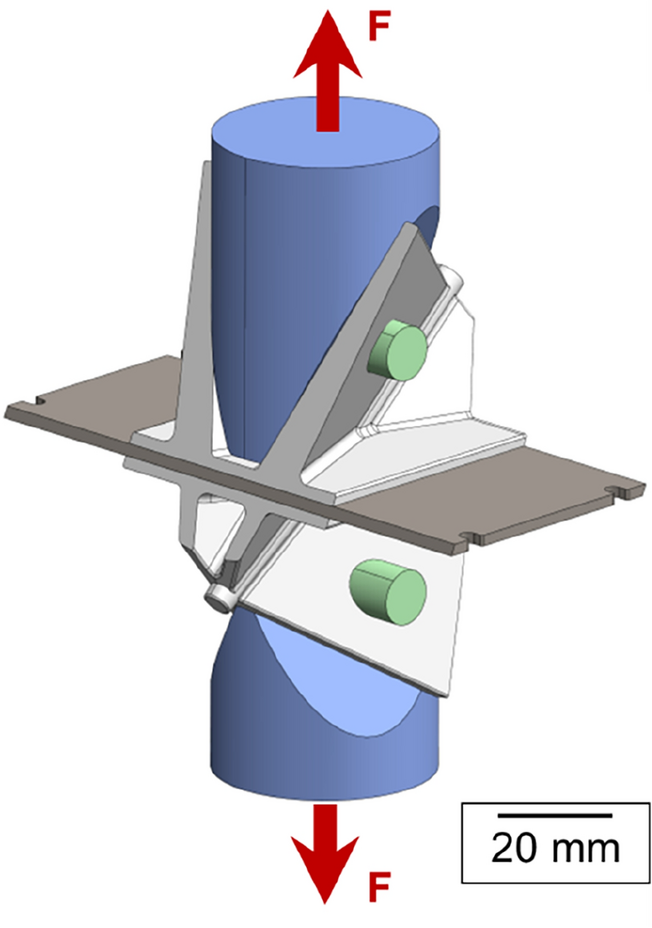
결과 및 토론
동적 및 정적 테스트의 측정 결과를 평가했습니다. 다양한 인서트 변형에 대한 복합 강도 간의 비교가 제시됩니다. 정적 테스트의 경우, 비교 가능한 결과를 제공하기 위해 복합 강도를 구조물의 하중 지지 영역으로 정규화했습니다. 동적 테스트를 위해 전체 부품을 테스트했기 때문에 하중 지지 영역에 대한 정규화가 불가능했습니다.
데모 부분의 동적 테스트
동적 테스트는 720°C 용융 및 200°C 다이 온도에서 생산된 시연 부품(ID 1, 2 및 5-8)에 대해 수행되었습니다. 그림 10은 코팅, 다양한 구조 및 두 가지의 조합이 파손까지의 로드 사이클 수에 미치는 영향을 보여줍니다. 각 매개변수 세트에 대해 양수 및 음수 방향의 하나의 표준 편차가 오차 막대로 추가되었습니다.
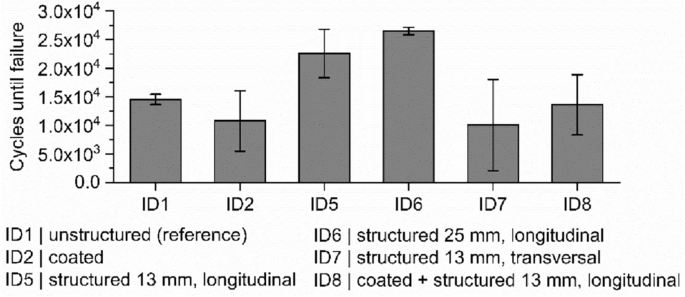
참조 부품은 파손까지 평균 14,550회의 굽힘 주기를 달성했습니다(그림 10 , ID1). 코팅된 인서트의 굽힘 주기 횟수가 감소했다는 점은 흥미롭습니다(그림 10 , ID2). 한 가지 가설은 저온 가스 분사 코팅의 높은 표면 거칠기로 인해 노치 효과가 증가한다는 것입니다. 13mm 폭의 종방향 구조는 복합 강도의 상당한 개선을 보여주었습니다(그림 10 , ID5). 굽힘 주기 횟수가 약 55% 증가했습니다. 25mm의 더 넓은 구조(그림 10 , ID6)는 굽힘 주기 수를 더욱 향상시켰지만 그 범위는 17%에 그쳤습니다. 세로형 구조와 비교하여 가로형 구조(그림 10 , ID7)는 굽힘 주기 횟수를 약 31% 줄이므로 내하력에 부정적인 영향을 미치는 것으로 보입니다. 그림 11 과 12 의 단면 준비는 가로 채널 구조의 충전이 감소됨을 보여줍니다. 이는 용융 흐름에 대한 채널의 직교 방향으로 인해 발생했을 가능성이 높으며, 이로 인해 구조 언더컷(그림 12a )의 충진이 상당히 악화되고 추가적인 주조 결함(그림 12b )이 발생합니다. 또 다른 가능성은 접촉 면적이 다르기 때문에 알루미늄의 하중 경로가 다르다는 것입니다. 코팅과 구조(그림 10 , ID8)의 조합은 기준과 비교하여 매우 유사한 수의 하중 사이클을 보여주기 때문에 복합 강도에 유익한 효과를 갖는 것으로 보이지 않습니다. 구조화 실험에서 코팅은 매우 작은 변형성을 나타냈습니다. 언더컷 구조가 생성될 때 코팅의 박리가 관찰되었습니다. 이는 화합물의 맞물림을 감소시키는 것이 가능합니다.
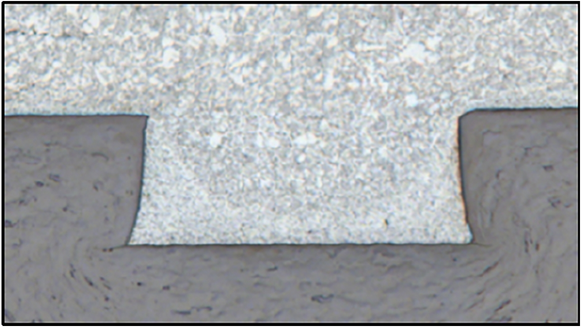
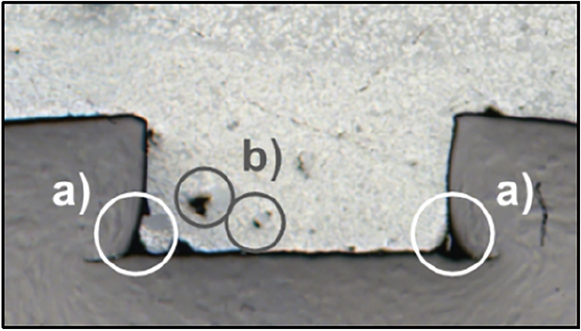
데모 부분의 정적 테스트
정적 테스트에서 다양한 인서트 변형을 비교하기 위해 인장 테스트에서 측정된 기계적 하중은 등가 응력 값 σ eq 로 변환됩니다 . 톱질 후 각 샘플에 대해 샘플 길이를 측정했습니다. 코팅되지 않고 구조화되지 않은 참조 부품은 절단 중에 이미 파손되었으며 이는 참조 응력이 σ = 0 MPa임을 나타냅니다. 코팅된 인서트의 경우 50mm의 복합 너비가 선택되었습니다. 이는 주조 재료로 덮힌 인서트의 너비이기 때문입니다. 구조화된 인서트의 경우 유효 구조 너비가 사용되었습니다(그림 5 ). 각 표본에 대해 개별 복합 면적은 길이와 복합 너비를 기준으로 계산되었습니다. 등가 응력 σ eq는 측정된 인장력과 개별 화합물 면적의 비율로 계산되었습니다.
코팅된 표면과의 접합을 위한 주조 온도
첫 번째 연구에서는 코팅된 인서트가 있는 화합물에 대해 용융 및 캐비티 온도의 영향을 테스트했습니다(그림 13 ). 결과는 온도가 높을수록 화합물의 강도가 향상된다는 것을 보여줍니다.
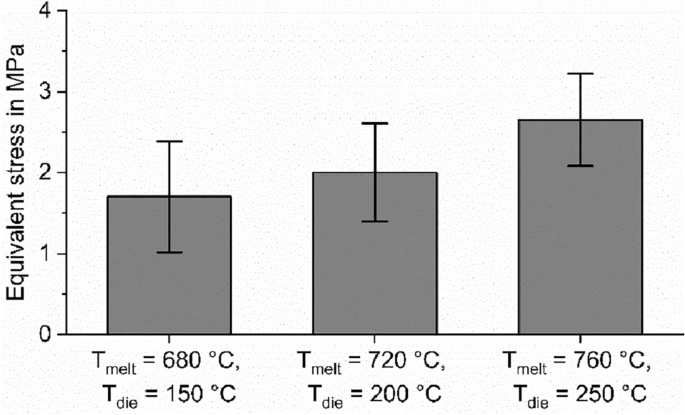
시편의 SEM 분석(그림 14 )에서 알 수 있듯이 용융물 및 공구 온도가 높을수록 용융물이 코팅 표면의 산화물 층에 더 쉽게 침투할 수 있어 야금학적 결합이 개선되는 데 기여했습니다. 그에 따라 온도가 높을수록 국지적인 용융 및 결합 영역이 증가할 수 있습니다. AlSiMn9 합금을 사용한 16 에서도 유사한 효과가 관찰되었습니다 . 기준과 비교하여 강철 인서트와 다이캐스트 알루미늄 사이의 야금학적 연결이 달성되어 하중을 전달할 수 있다는 것이 분명합니다.
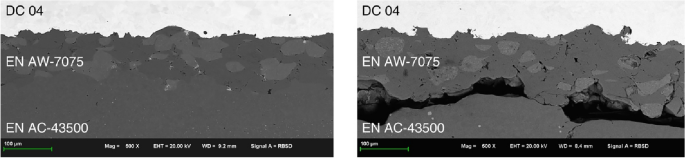
채널 구조의 영향
채널 구조가 있는 인서트의 경우 13mm 폭의 세로 구조에 대해 6.9MPa의 최대 등가 응력이 얻어졌습니다(그림 15 ). 동적 테스트에서 알 수 있듯이 횡단 구조는 강도를 감소시킵니다. 접합 강도는 복합 면적에 의해 정규화되고 하중 조건은 비슷하므로 복합 강도의 차이는 충전 조건의 결과여야 합니다. 용융 흐름에 대해 횡방향 배향을 갖는 채널은 구조의 충진을 상당히 악화시키는 결과를 가져왔습니다. 25mm 세로 구조는 5.1MPa의 등가 응력을 달성합니다. 13mm 구조에 비해 이러한 감소는 동적 테스트에서도 발견되었습니다. 이는 첫 번째 구조화 패스와 두 번째 구조화 패스 사이의 전이 영역 때문일 수 있습니다. 이 영역에서는 언더컷 형성이 감소한 것으로 나타났습니다(그림 5 ).
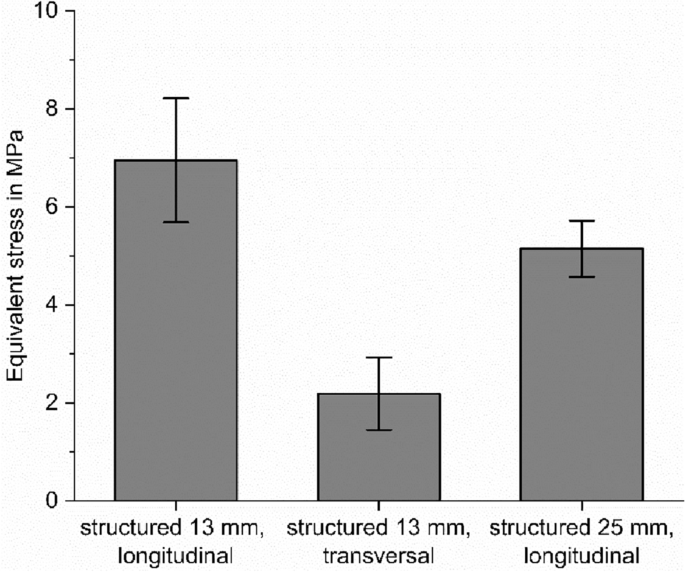
코팅, 구조 및 조합 비교
그림 16은 코팅된 인서트와 세로 방향으로 13mm 구조의 인서트를 비교한 것입니다. 화합물의 면적을 기준으로 채널 구조의 인서트는 코팅된 인서트에 비해 조인트 면적당 더 높은 하중을 허용합니다. 코팅과 구조화의 조합은 접합 강도를 향상시키지 않습니다.
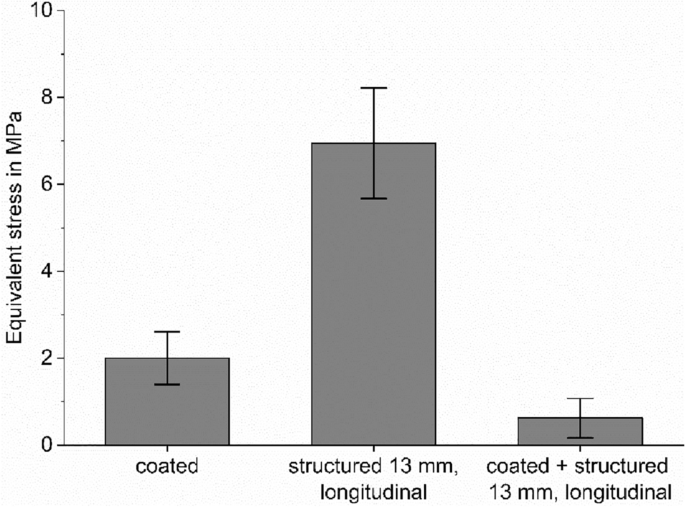
코팅과 구조화가 결합된 부품의 접합 강도가 낮아지는 메커니즘이 그림 17 에 나와 있습니다 . 코팅층 c 는 강철 인서트 a 의 언더컷을 채웠다 . 따라서 주조알루미늄 (b) 은 구조화되어 변형된 도금층과만 상호작용할 수 있을 뿐, 강판과 기계적인 맞물림을 형성하여 하중을 전달할 수는 없다. 코팅과 강철 기판 재료 사이의 조기 파손으로 인해 화합물이 파손됩니다.
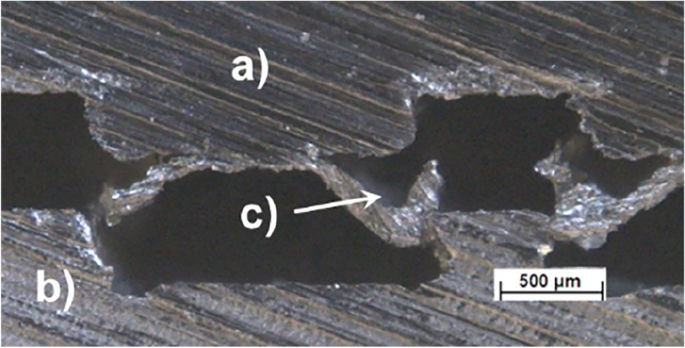
결론 및 전망
본 연구에서는 알루미늄 고압 다이캐스팅으로 제작된 하이브리드 부품용 강판 인서트의 다양한 전처리 방법을 분석했습니다. 한편, 다이캐스트 알루미늄과의 야금학적 결합을 위해 알루미늄 코팅을 적용하기 위해 저온 가스 분사가 사용되었습니다. 반면, 다이캐스트와의 기계적 결합을 위해 언더컷 표면 구조가 강판 인서트에 각인되었습니다. 결과적으로 다이캐스팅의 복합 강도를 동적으로, 정적으로 테스트했습니다. 다음과 같은 결론이 도출되었습니다.
- 냉간 스프레이 코팅이 적용된 판금 인서트는 연속 생산에 가까운 고압 다이캐스팅 공정에서 다이캐스트 알루미늄과 기계적으로 탄력 있는 결합을 형성할 수 있습니다. 저온 가스 분사 공정은 강판에 대한 미세 클램핑과 알루미늄 주물에 대한 야금학적 결합을 제공합니다.
- EN AW-7075 코팅을 사용할 때 용융물과 다이의 온도가 높을수록 알루미늄 다이캐스트와 강철 사이의 복합 강도를 높이는 데 도움이 됩니다.
- 용융 흐름을 따라 흐르는 채널 구조의 인서트는 화합물 강도를 향상시킵니다. 정적 테스트에서는 최대 6.9MPa의 등가 응력이 측정되었습니다.
- 더 넓은 구조는 절대 강도를 향상시키지만 주어진 테스트에서 등가 응력은 감소했습니다. 그 이유는 두 구조 롤링 패스 간의 전환으로 인해 구조 형상의 정확도가 감소했기 때문일 수 있습니다.
- 채널 구조와 용융 흐름 사이의 정렬은 다이캐스팅 공정 설계에서 매우 중요합니다. 용융 흐름을 가로지르는 채널의 강도가 크게 감소했기 때문입니다.
- 코팅과 구조의 조합으로 인해 주어진 상황에서는 개선이 이루어지지 않았습니다.
다이캐스트에 대한 코팅의 접착력을 더욱 향상시키기 위해 연삭과 같은 기계적 전처리를 조사할 수 있습니다. 구조화된 영역이 더 넓은 경우 압연 공정을 수정하면 구조 형상의 정확성이 향상되고 접합 강도가 일정하게 유지될 수 있습니다. 코팅과 구조화 간의 결합된 접근 방식은 프로세스 체인을 변경하여 달성할 수 있습니다. 코팅 전에 구조화하면 코팅이 벗겨지는 현상이 발생하지 않습니다. 그러나 이것이 알루미늄 용융물과의 결합에 어떤 영향을 미칠지는 확실하지 않습니다.
참고자료
- Bundesministerium für Wirtschaft und Energie(2021) Leichtbaustrategie für den Industriestandort Deutschland, Bundesministerium für Wirtschaft und Energie(BMWi), 베를린.
- G. Meschut, V. Janzen, T. Olfermann, 다중 재료 경량 차체 구조를 위한 혁신적이고 생산성이 높은 접합 기술. J. Mater. 영어 공연하다. 23 (5), 1515~1523(2014). https://doi.org/10.1007/s11665-014-0962-3기사 카스 구글 학술검색
- K. Mori, Y. Abe, 소성 변형에 의한 알루미늄과 고강도 강판의 기계적 접합에 대한 검토. 국제 J. 경량 교인. 제조. 1 (1), 1–11 (2018). https://doi.org/10.1016/j.ijlmm.2018.02.002기사 구글 학술검색
- K. Mori, N. Bay, L. Fratini, F. Micari, AE Tekkaya, 소성 변형에 의한 결합. CIRP 앤. 제조. 기술. 62 (2), 673–694(2013). https://doi.org/10.1016/j.cirp.2013.05.004기사 구글 학술검색
- T. Noguchi, K. Asano, S. Hiratsuka, H. Miyahara, 일본의 복합 주조 기술 및 주조 접합 기술 동향. 국제 J. 캐스트 멧. 결의안. 21 (1–4), 219–225(2008). https://doi.org/10.1179/136404608X361981기사 카스 구글 학술검색
- EE Feistauer, JF dos Santos, ST Amancio-Filho, 두께를 통해 강화된 금속-폴리머 복합 복합 구조의 직접 조립에 대한 검토. 폴리엠. 영어 과학. 59 (4), 661–674(2019). https://doi.org/10.1002/pen.25022기사 카스 구글 학술검색
- Y. Ma, G. Zhang, S. Cao, Z. Huo, J. Han, S. Ma, Z. Huang, 미세 구조 표면의 제조 방법 및 보조 기술의 발전에 대한 검토. 프로세스 11 (5), 1337(2023). https://doi.org/10.3390/pr11051337기사 카스 구글 학술검색
- D. Joop, Präzisionsbestimmende Faktoren bei der Herstellung blechverstärkter Hybridstrukturen im Druckguss: Grenzflächenanalyse und Verzugsoptimierung (Gießerei-Institut, RWTH Aachen University, Diss., 2018)구글 학술검색
- S. Müller, M. Brand, K. Dröder, D. Meiners, 혁신적인 기계적 연동 효과를 통해 하이브리드 플라스틱-금속 부품의 구조적 무결성 향상. 교배. 과학. 포럼 825–826 , 417–424 (2015). https://doi.org/10.4028/www.scientific.net/MSF.825-826.417기사 구글 학술검색
- AL Buxton, A. Ferhati, RJ Glen, BG Dance, D. Mullen, T. Karayiannis, 고성능 열 교환기를 위한 EB 표면 엔지니어링. 진행 FIEBWC. 17 , 1 (2009)구글 학술검색
- S. Ucsnik, R. Gradinger, A. Becirovic, A. Waldhör, 냉간 금속 이송을 통해 강철-알루미늄 주조 노드의 성능이 향상되었습니다. 교배. 과학. 포럼 765 , 736–740(2013). https://doi.org/10.4028/www.scientific.net/MSF.765.736기사 카스 구글 학술검색
- H. Abe, JC Chung, T. Mori, A. Hosoi, KM Jespersen, H. Kawada, 알루미늄과 탄소 섬유 강화 열가소성 수지 사이의 직접 결합 강도 특성에 대한 나노스파이크 구조의 효과. 작곡. B엔. 172 , 26–32(2019). https://doi.org/10.1016/j.compositesb.2019.05.025기사 카스 구글 학술검색
- X. Fang, J. Gundlach, JJ Schipperges, X. Jiang, 모래 주조에 의한 강철-알루미늄 하이브리드 주조에 대하여. J. Mater. 영어 공연하다. 27 (12), 6415–6425(2018). https://doi.org/10.1007/s11665-018-3717-8기사 카스 구글 학술검색
- Oberschelp, C (2012) Hybride Leichtbaustrukturen für den Karosseriebau Gusswerkstofforientierte Anwendungsuntersuchungen für das Druckgießen. Diss., Hochschulbibliothek Rheinisch-Westfälische Technische Hochschule; Gießerei-Inst, Aachen, pp 294.
- Lao, B (2013) Druckgegossene Metallhybridstrukturen für den Leichtbau-Prozess, Werkstoffe und Gefüge der Metallhybriden. Diss., Hochschulbibliothek der Rheinisch-Westfälischen Technischen Hochschule Aachen, 아헨.
- K. Bobzin, M. Öte, S. Wiesner, L. Gerdt, 알루미늄/강철 하이브리드 주조를 위한 브레이징 및 냉간 분사로 증착된 코팅 분석. 진행하다. 국제 브레이징 솔더. 회의 2018 , 229–233 (2018)구글 학술검색
- S. Senge, J. Brachmann, G. Hirt, A. Bührig-Polaczek 구조화된 강판과 고압 다이캐스트 알루미늄으로 만들어진 복합 재료 연동 부품, in: ESAFORM. 아일랜드 더블린에서 열린 재료 성형에 관한 제20회 국제 ESAFORM 회의 간행물. 26-28, p 190007 (2017)
- K. Bobzin, M. Öte, S. Wiesner, L. Gerdt, S. Senge, G. Hirt, 냉간 스프레이 구리 코팅 강판의 냉간 압연 및 구조화에 대한 조사. IOP 컨퍼런스 Ser. 교배. 과학. 영어 181 , 12028(2017). https://doi.org/10.1088/1757-899X/181/1/012028기사 구글 학술검색
- K. Bobzin, W. Wietheger, J. Hebing, L. Gerdt, 어닐링 중 냉간 스프레이 알루미늄 기반 코팅 AA1200 및 AA7075의 연화 거동. J.Therm. 스프레이 기술. 30 (1–2), 358–370(2021). https://doi.org/10.1007/s11666-020-01121-7기사 카스 구글 학술검색
- K. Bobzin, H. Heinemann, M. Erck, J. Körner 강철/Al 복합 주조물 결합을 위한 솔루션으로 열 분사 코팅(허용). 열 스프레이 황소. (2023)
- S. Senge, J. Brachmann, G. Hirt, A. Bührig-Polaczek 구조화된 1.0338 강판과 고압 다이캐스트 AlMg5Si2 사이의 연동 결합 강도 평가, in: ESAFORM. 이탈리아 팔레르모에서 열린 재료 성형에 관한 제21회 국제 ESAFORM 회의 간행물. 2018년 4월 23~25일, 40019페이지(2018)
- S. Senge, L. Gerdt, S. Wiesner, M. Öte, K. Bobzin, G. Hirt 하이브리드 부품의 전처리로서 코팅 강판의 냉간 압연, in: 3. International Konferenz Hybrid - 재료 및 구조, 브레멘. 2019년 4월 18일-19일, 290-295페이지 (2019).
- EV DIN Deutsches Institut für Normung DIN EN 573-3, 알루미늄 및 알루미늄 합금 - 화학적 조성 및 가공 제품의 형태 - 3부: 화학적 조성 및 제품 형태, Beuth Verlag GmbH, 베를린(2022)
- EV DIN Deutsches Institut für Normung DIN EN 1706:2020-06, 알루미늄 및 알루미늄 합금 - 주조 - 화학적 조성 및 기계적 특성, Beuth Verlag GmbH, 베를린(2021)
- L. Bruckmeier, A. Ringel, U. Vroomen, D. Bailly, A. Bührig-Polaczek, 언더컷 판금이 포함된 하이브리드 부품의 복합 강도에 대한 고압 다이 캐스팅 공정 매개변수의 영향. 금속 13 (10), 1717(2023). https://doi.org/10.3390/met13101717기사 카스 구글 학술검색
감사의 말
Deutsche Forschungsgemeinschaft(DFG, 독일 연구 재단)의 자금 지원—Project-ID 245566034. IEHK의 동적 피로 테스트에 대해 Niklas Fehlemann, Manuel Henrich 및 Marc Grümmer에게 특별히 감사드립니다.
자금 조달
Projekt DEAL을 통해 오픈 액세스 자금 지원이 활성화되고 구성되었습니다.
작가 정보
저자 및 소속
- 파운드리 연구소(GI), RWTH Aachen University, Intzestraße 5, 52072, Aachen, Germany루카스 브루크마이어 & 안드레아스 뷔릭-폴라체크
- 금속 성형 연구소(IBF), RWTH Aachen University, Intzestraße 10, 52072, Aachen, Germany아론 링겔 & 데이비드 베일리
- IOT(표면 공학 연구소), RWTH Aachen University, Kackertstraße 15, 52072, Aachen, Germany마빈 에르크, 커스틴 보진, 헨드릭 하이네만