이 기술 요약은 Dirk Lehmhus, Christoph Pille, Dustin Borheck 등이 Giesserei(2018)에 발표한 학술 논문 "Leakage-free cooling channels for Die-cast housing components"를 기반으로 합니다. 이 내용은 CASTMAN의 전문가들이 Gemini, ChatGPT, Grok과 같은 LLM AI의 도움을 받아 HPDC 전문가를 위해 분석하고 요약했습니다.
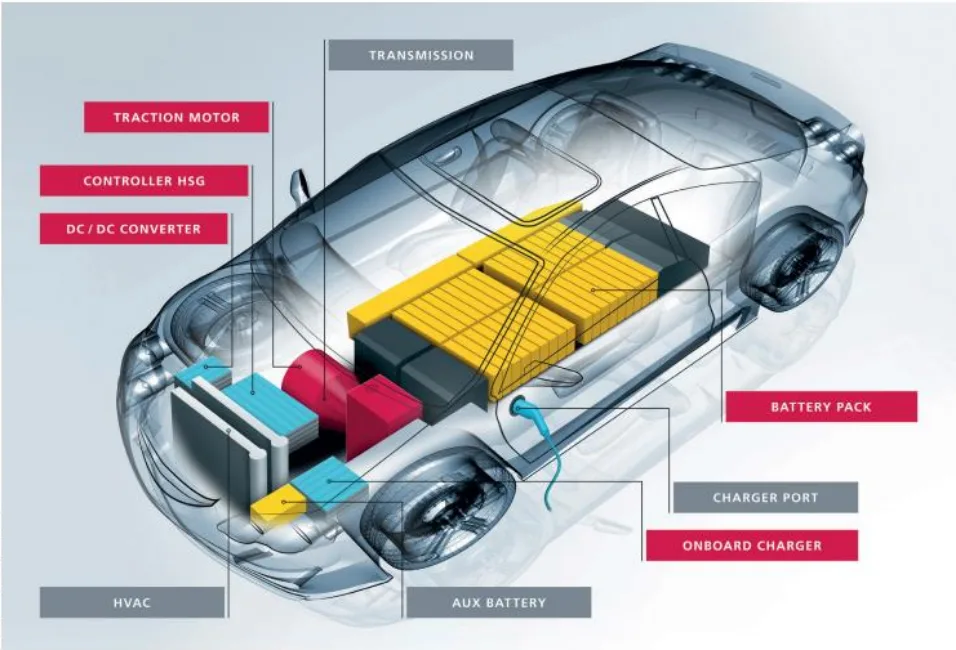
키워드
- 핵심 키워드: 다이캐스팅 냉각 채널
- 보조 키워드: E-모빌리티용 HPDC, ZLeak 튜브 기술, 다이캐스팅 열 관리, 주조 시뮬레이션(WinCast), 알루미늄 튜브 인서트, 전기 모터 하우징 주조, 다이캐스팅 열전달 계수
핵심 요약
- 핵심 과제: E-모빌리티의 부상은 배터리 및 모터와 같은 부품에 대한 고급 열 관리를 요구합니다. 튜브 붕괴나 값비싼 다중 부품 조립에 의존하지 않고, 복잡하고 누수 없는 냉각 채널을 단일 피스 고압 다이캐스팅(HPDC) 하우징에 통합하는 것은 주요 제조 장애물이었습니다.
- 연구 방법: "CoolCast" 프로젝트의 연구원들은 안정화 및 제거가 가능한 이중층 충전재를 가진 특수 알루미늄 튜브 인서트인 "ZLeak 튜브" 기술에 대한 광범위한 실험을 수행했습니다. 그들은 다양한 합금, 벽 두께 및 HPDC 공정 변수를 테스트했으며, 물리적 실험과 고급 WinCast expert 주조 시뮬레이션을 모두 사용하여 결과를 분석했습니다.
- 핵심 성과: 이 연구는 ZLeak 튜브 기술이 HPDC 응용 분야에서 실현 가능할 뿐만 아니라 예측 가능성이 매우 높다는 것을 성공적으로 증명했습니다. 결정적으로, 주조 시뮬레이션은 파이프 압축 및 변위를 정확하게 모델링할 수 있어 설계자가 강철을 가공하기 전에 견고하고 복잡한 냉각 경로를 설계하고 금형 및 공정을 최적화할 수 있도록 합니다.
- 핵심 결론: 이 연구는 복잡하고 통합된 냉각 시스템을 갖춘 일체형 다이캐스팅 부품을 생산하기 위한 강력하고 새로운 방법을 검증합니다. 이는 차세대 전기차에 필수적인 고성능, 열적으로 최적화된 부품을 제조하기 위한 명확하고 데이터 기반의 경로를 제공합니다.
과제: 이 연구가 HPDC 전문가에게 중요한 이유
자동차 산업이 E-모빌리티로 전환함에 따라 효과적인 열 관리가 무엇보다 중요해졌습니다. 배터리 팩, 파워 일렉트로닉스, 트랙션 모터와 같은 핵심 부품은 상당한 열을 발생시키며 최적의 성능과 수명을 유지하기 위해 정교한 냉각이 필요합니다(초기 이미지). 고압 다이캐스팅(HPDC)은 이러한 부품에 필요한 경량의 복잡한 하우징을 생산하는 데 이상적인 공정이지만, 내부 냉각 채널을 통합하는 것은 항상 중요한 과제였습니다.
수십 년 동안 엔지니어들은 실망스러운 한계에 직면해 왔습니다. 보강되지 않은 표준 알루미늄 튜브를 주조에 삽입하려는 시도는 종종 용융 금속의 엄청난 압력과 열로 인해 붕괴됩니다(Image 1). 대안적인 해결책들은 각각의 단점을 가지고 있습니다:
- 2피스 하우징: 추가 금형, 복잡한 접합 및 밀봉 공정이 필요하며, 접합부의 열 응력에 취약하여 비용과 잠재적 고장 지점을 증가시킵니다.
- 강철 튜브 인서트: 주조 공정을 견딜 수는 있지만, 알루미늄 주물과의 열팽창 불일치를 일으켜 틈새 형성, 열전달 감소 및 잠재적인 부식 문제를 야기합니다.
이 연구는 단일 다이캐스팅 부품 내에 기하학적으로 복잡하고 누수 없는 냉각 채널을 직접 생성하여 성능과 경제적 효율성을 결합하는 새로운 접근법을 검증함으로써 이 중요한 산업적 요구를 해결합니다.
연구 방법: 방법론 분석
이 과제를 해결하기 위해 "CoolCast" 프로젝트는 튜브 기술 개발사인 MH Technologies, 다이캐스팅 전문 기업인 ae group ag, 금형 제작사인 Schaufler Tooling GmbH, 시뮬레이션 전문 기업인 RWP GmbH를 비롯하여 Fraunhofer IFAM과 협력하여 업계 리더들을 모았습니다.
연구의 핵심은 특허받은 ZLeak 튜브 기술이었습니다. 이 혁신적인 접근법은 독특한 이중층 코어로 채워진 알루미-늄 튜브 인서트를 사용합니다: 수용성 외부층과 입자가 굵고 유체가 투과할 수 있는 내부 코어(Image 2). 이 충전재는 HPDC 공정을 견디는 데 필요한 구조적 안정성을 제공하며, 나중에 쉽게 씻어낼 수 있습니다.
연구팀은 Bühler-SC/N-66 다이캐스팅 기계를 사용하여 엄격한 실험 프로그램을 수행했습니다. 그들은 특수 금형(Image 3)에서 다양한 튜브 인서트를 테스트하며 주요 매개변수를 변경했습니다:
- 파이프 재질: 알루미늄 합금 EN AW-6063 및 EN AW-3003.
- 파이프 형상: 외경 12mm, 벽 두께 1mm, 1.5mm, 2mm.
- 공정 변수: 600 ~ 1200 bar의 주조 압력, 2.5 ~ 4.5 m/s의 주조 피스톤 속도, 상온 ~ 200°C의 파이프 예열 온도.
물리적 실험과 병행하여, 팀은 WinCast expert 시뮬레이션 소프트웨어를 사용하여 금형 충전, 응고 및 열 응력을 모델링했습니다. 시뮬레이션 결과는 용융물 흐름 진행을 검증하기 위한 단속 사출(interrupted shot) 테스트를 포함한 실험 데이터와 비교하여 검증되었습니다(Image 4).
핵심 성과: 주요 연구 결과 및 데이터
이 연구는 산업 응용을 위한 이 기술의 실행 가능성과 예측 가능성을 입증하는 몇 가지 중요한 결과를 도출했습니다.
- 성과 1: 파이프 압축은 예측 가능하며 압력에 따라 달라짐. 실험 결과, 최대 주조 압력과 튜브의 압축(내경 감소) 사이에는 거의 선형적인 관계가 있음이 밝혀졌습니다. Image 5에서 볼 수 있듯이, 1mm 벽 두께의 파이프는 1.5mm 또는 2mm 벽의 파이프보다 훨씬 더 많이 압축되었습니다. 또한 EN AW-3003 합금 튜브는 EN AW-6063으로 만든 유사한 튜브보다 압축률이 낮아 재료 선택의 중요성을 강조했습니다.
- 성과 2: 변위는 열적 효과와 기계적 제약에 의해 발생. 예상과 달리, 재압축 압력은 금형 내 파이프의 변위(이동)에 미미한 영향을 미쳤습니다. 지배적인 요인은 용융물 흐름의 열적 영향과 기계적 설정이었습니다. Image 6에서 볼 수 있듯이, 파이프를 예열하면 변위가 크게 감소했습니다. 파이프의 한쪽 끝에 가동형 베어링을 사용하는 것도 위치 이동을 완화하는 데 효과적인 것으로 입증되었습니다.
- 성과 3: 시뮬레이션은 실제 거동을 정확하게 모델링함. 이 프로젝트의 핵심 성과 중 하나는 주조 시뮬레이션의 검증입니다. 소프트웨어는 파이프의 어느 지점에서든 시간-온도 곡선을 예측할 수 있었으며, 최고 온도가 530°C에 도달하여 재료 강도가 크게 손실됨을 보여주었습니다(Image 7). 가장 중요한 것은 시뮬레이션으로 예측된 파이프 변위와 주조 부품에서 실제로 측정된 변위 사이에 강한 상관관계가 있었다는 것입니다(Image 8). 이는 설계 및 공정 엔지니어링을 위한 도구의 신뢰성을 입증합니다.
- 성과 4: 열전달은 정량화 및 최적화가 가능함. 맞춤형 테스트 장비(Image 9)를 사용하여 연구원들은 튜브와 주물 사이의 열전달 계수(HTC)를 측정했습니다. Image 10의 결과는 EN AW-6063의 경우 HTC가 재압축 압력과 함께 증가하는 경향이 있으며, EN AW-3003의 값이 일반적으로 더 높다는 것을 보여줍니다. 이 연구는 또한 계면에서 미세한 틈이 형성될 수 있음을 인정하며(Image 11, Image 13), 이는 열 성능에 영향을 미치고 추가 최적화가 필요한 영역임을 나타냅니다.
HPDC 제품을 위한 실질적인 시사점
이 연구는 첨단 다이캐스팅 부품을 연구하는 엔지니어와 설계자에게 즉시 적용 가능한 통찰력을 제공합니다.
- 공정 엔지니어를 위해: 연구 결과는 공정 제어를 위한 명확한 가이드를 제공합니다. 파이프 압축은 예측 가능한 범위 내에서 재압축 압력을 조정하여 관리할 수 있습니다(Image 5). 파이프 이동을 최소화하고 위치 정확도를 보장하기 위해서는 압력 조정에만 의존하기보다는 인서트 예열 및 용융물 흐름 최적화와 같은 열 관리 전략에 집중해야 합니다(Image 6).
- 품질 관리팀을 위해: 검증된 시뮬레이션 모델(Image 8)은 강력한 예측 품질 도구입니다. 가상 센서(Image 7)를 사용하여 엔지니어는 첫 번째 부품을 주조하기 전에 파이프의 측정하기 어려운 영역에서 열 조건을 모니터링하고 응력을 예측하여 시간을 절약하고 불량률을 줄일 수 있습니다.
- 금형 설계자를 위해: 이 기술은 설계자에게 새로운 자유를 부여합니다. 직경의 1.5배에 불과한 굽힘 반경을 가진 파이프를 생성할 수 있는 능력은 전기 모터 하우징 프로토타입에서 입증된 바와 같이(Image 12), 매우 복잡하고 효율적인 냉각 채널 레이아웃을 가능하게 합니다. 설계자는 이제 예측 가능한 수준의 파이프 압축 및 변위를 CAD 모델에 통합하여 최종 부품이 모든 기하학적 공차를 충족하도록 보장할 수 있습니다.
논문 상세 정보
Leakage-free cooling channels for Die-cast housing components
1. 개요:
- 제목(Title): Leakage-free cooling channels for Die-cast housing components
- 저자(Author): DIRK LEHMHUS, CHRISTOPH PILLE, DUSTIN BORHECK, BREMEN, FELICIA BUMBU, THOMAS SCHWEGLER, LAI CHINGEN, JUSTIN LEE, JINHO YOO, IN CHEON, KOREA, PETER LUTZE, GERS TUNGEN AND REINHARD VOMHOF, KONRAD WEISS, ROETGEN
- 발표 연도(Year of publication): 2018
- 학술지/학회(Journal/academic society of publication): Giesserei
- 키워드(Keywords): Electro mobility, Die-cast, Cooling channels, Housing components, ZLeak Tube, Casting simulation
2. 초록 (Abstract):
전기차 부품의 출력 밀도 증가는 고급 열 관리 솔루션을 필요로 합니다. 본 논문은 희생 충전재를 사용한 알루미늄 튜브 인서트인 "ZLeak 튜브" 기술을 사용하여 고압 다이캐스팅(HPDC) 부품에 복잡한 유체 이송 냉각 채널을 직접 통합하는 것의 타당성을 조사합니다. 물리적 주조 실험과 수치 시뮬레이션의 조합을 통해, 연구는 주조 압력, 피스톤 속도, 예열과 같은 공정 변수가 튜브 인서트의 안정성, 압축 및 변위에 미치는 영향을 분석합니다. 연구는 이 기술이 HPDC 조건에서 안정적이며 그 거동이 시뮬레이션 도구를 사용하여 예측 가능하다는 것을 검증하여, 전기 모터 및 파워 일렉트로닉스 하우징과 같은 응용 분야를 위한 통합되고 누수 없는 냉각 기능을 갖춘 단일 피스 경량 하우징의 설계 및 제조 길을 열어줍니다.
3. 서론 (Introduction):
E-모빌리티의 발전은 새로운 설계 과제를 제시하며, 주된 초점은 순수한 출력 밀도에서 열 조건의 최적화로 이동하고 있습니다. 기하학적으로 복잡한 냉각 채널은 배터리, 파워 일렉트로닉스, 모터용 하우징에 제조 공정 중에 통합되어야 합니다. 이는 성능과 경제성을 모두 만족시키는 새로운 개념을 필요로 합니다. 지지되지 않은 알루미늄 튜브를 주조하거나 다중 부품 하우징을 사용하는 것과 같은 전통적인 방법들은 상당한 단점을 가지고 있습니다. 본 연구는 현대 전기 구동계의 열적 요구를 충족시키기 위해 일체형 HPDC 부품에 통합 냉각 채널을 생성하는 새로운 접근법을 탐구합니다.
4. 연구 요약 (Summary of the study):
연구 주제의 배경:
열 관리는 전기차의 수많은 어셈블리에서 핵심 설계 포인트입니다. 특히 배터리 소자, 파워 일렉트로닉스, 트랙션 모터에서 최적의 온도를 보장하고 전력 및 용량 손실을 방지하기 위해 열 방출을 제어해야 합니다. HPDC는 이러한 하우징을 생산하는 데 선호되는 방법이지만, 필요한 중공 채널 구조를 통합하는 것은 상당한 제조 과제입니다.
이전 연구 현황:
하우징에 냉각 채널을 만드는 이전 접근법으로는 저압 또는 중력 주조와 샌드 코어(생산성 저하), 2피스 HPDC 하우징(고가, 추가 가공 및 접합 공정 필요), 강철 파이프 주조 삽입(열팽창 불일치) 등이 있었습니다. 유압 라인에 튜브를 주조 삽입하는 방식이 사용되지만, 냉각용으로 보강되지 않은 알루미늄 튜브를 사용하는 것은 HPDC 공정에서 안정적이지 않기 때문에 문제가 있습니다(Image 1). Combicore 접근법과 같은 충전재 기반 개념이 존재하며, 본 연구는 대안적인 특허 충전재 기술을 기반으로 합니다.
연구 목적:
"CoolCast" 프로젝트는 HPDC 부품에 냉각 채널을 만들기 위한 ZLeak 튜브 기술의 사용을 조사하고 검증하는 것을 목표로 했습니다. 주요 목적은 공정 한계를 결정하고, 공정 변수가 파이프 압축 및 변형에 미치는 영향을 이해하고, 이러한 효과를 표현하는 주조 시뮬레이션의 능력을 검증하고, 결과적인 냉각 채널의 응용 관련 특성을 평가하는 것이었습니다.
핵심 연구:
연구는 다른 알루미늄 합금(EN AW-6063, EN AW-3003)과 벽 두께로 만들어진 직선 및 곡선형 ZLeak 튜브 인서트를 사용한 주조 실험을 포함했습니다. 이 실험들은 주조 압력, 피스톤 속도, 인서트 예열 온도를 변화시키면서 HPDC 기계에서 수행되었습니다. 결과적인 주조물은 파이프 압축 및 변위에 대해 분석되었습니다. 물리적 결과는 WinCast expert 시뮬레이션 소프트웨어의 예측과 비교되었습니다. 또한, 파이프와 주물 사이의 열전달 계수가 실험적으로 결정되었습니다. 마지막으로, 이 지식은 전기 모터 하우징을 닮은 데모 부품에 적용되었습니다.
5. 연구 방법론 (Research Methodology)
연구 설계:
연구는 물리적 실험과 수치 시뮬레이션을 결합했습니다. 간단한 테스트 형상(직선 파이프, Image 3a)에서 시작하여 더 복잡한 형상(곡선 파이프, Image 3b), 그리고 최종적으로 완전한 데모 부품(Image 12)으로 진행되는 다단계 프로젝트 구조가 사용되었습니다. 이를 통해 공정 변수와 주조 결과 사이의 상관관계를 체계적으로 결정할 수 있었습니다.
데이터 수집 및 분석 방법:
데이터는 주조 부품의 X-선 분석을 통해 파이프 압축 및 변위를 결정하여 물리적 측정을 통해 수집되었습니다. 공정 데이터(압력, 속도)는 다이캐스팅 기계에서 기록되었습니다. 맞춤형 테스트 장비(Image 9)가 파이프와 주물 사이의 열전달 계수를 측정하기 위해 제작되었습니다. 시뮬레이션 소프트웨어 WinCast expert는 용융물 흐름, 온도 프로파일, 응력 및 변형에 대한 예측 데이터를 생성하는 데 사용되었습니다. 실험 및 시뮬레이션 데이터는 정량적으로 비교되었습니다(Image 8).
연구 주제 및 범위:
범위는 다음을 포함합니다:
- 파이프 재질: EN AW-6063, EN AW-3003.
- 파이프 형상: 외경 12mm, 벽 두께 2mm, 1.5mm, 1mm.
- 변화된 공정 변수: 주조 압력(600-1200 bar), 피스톤 속도(2.5-4.5 m/s), 파이프 예열(상온, 100°C, 200°C).
- 파이프 압축, 변위 및 열전달 계수 분석.
- 실험 결과에 대한 주조 시뮬레이션 예측 검증.
- 나선형 냉각 채널이 있는 데모 부품에 적용.
6. 주요 결과 (Key Results):
주요 결과:
- 파이프 압축은 최대 주조 압력에 거의 선형적으로 의존하며, EN AW-3003 합금은 EN AW-6063보다 적은 압축을 보입니다(Image 5).
- 파이프 변위는 주로 열적 요인(용융물 흐름, 예열 온도)과 기계적 제약(베어링 유형)에 의해 영향을 받으며, 재압축 압력은 미미한 영향을 미칩니다(Image 6).
- WinCast expert를 사용한 주조 시뮬레이션은 충전 중 파이프 온도(최대 530°C)와 파이프의 최종 변위를 정확하게 예측하여 예측 엔지니어링에 대한 사용을 검증합니다(Image 7, Image 8).
- 파이프와 주물 사이의 열전달 계수는 측정이 가능하며 EN AW-6063의 경우 재압축 압력과 함께 증가하는 경향이 있습니다. 계면에서의 미세 틈새 존재는 열전달에 영향을 미치는 핵심 요소입니다(Image 10, Image 11).
- 이 기술은 나선형 냉각 채널이 있는 데모 전기 모터 하우징에 성공적으로 적용되어 복잡한 부품 생산의 타당성을 입증했습니다(Image 12, Image 13).
그림 목록 (Figure Name List):
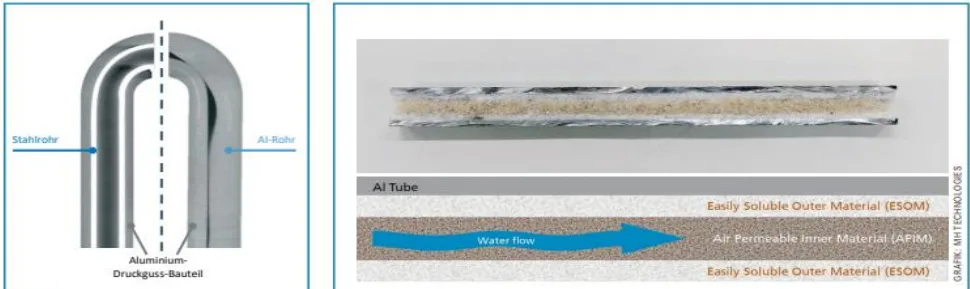
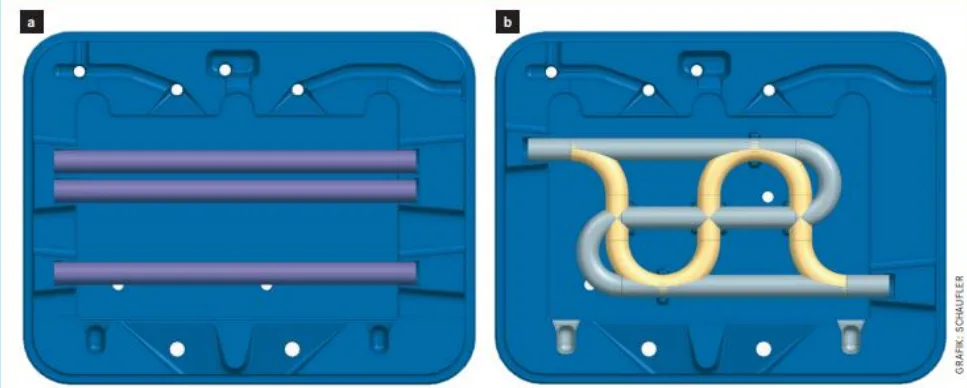
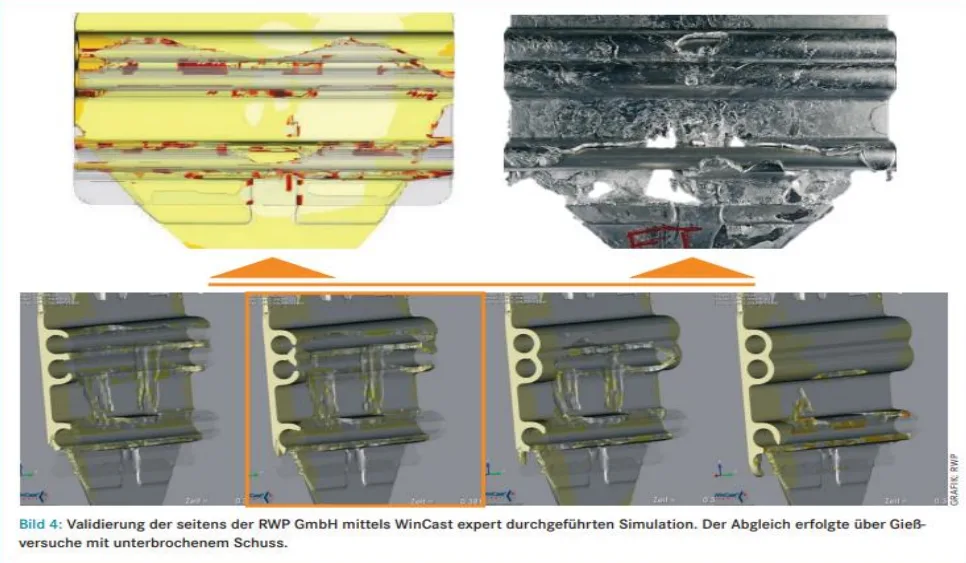
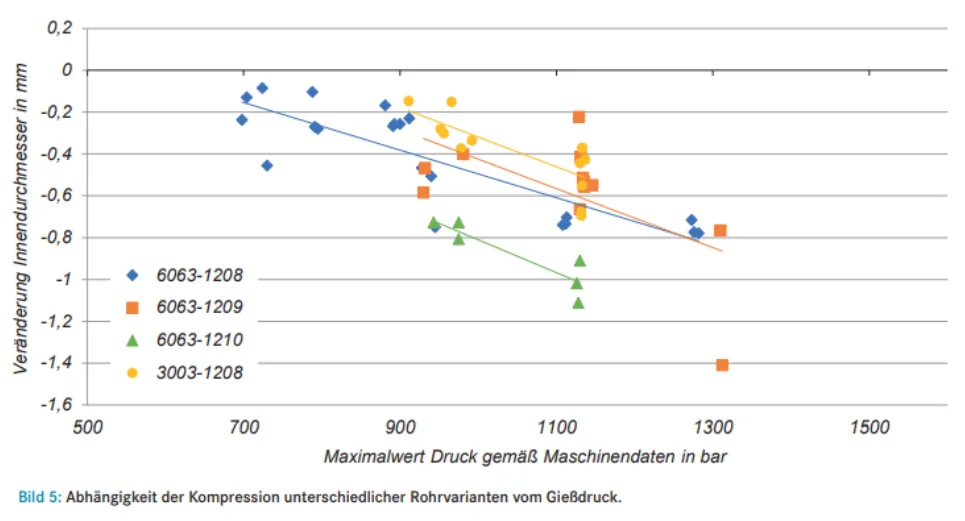
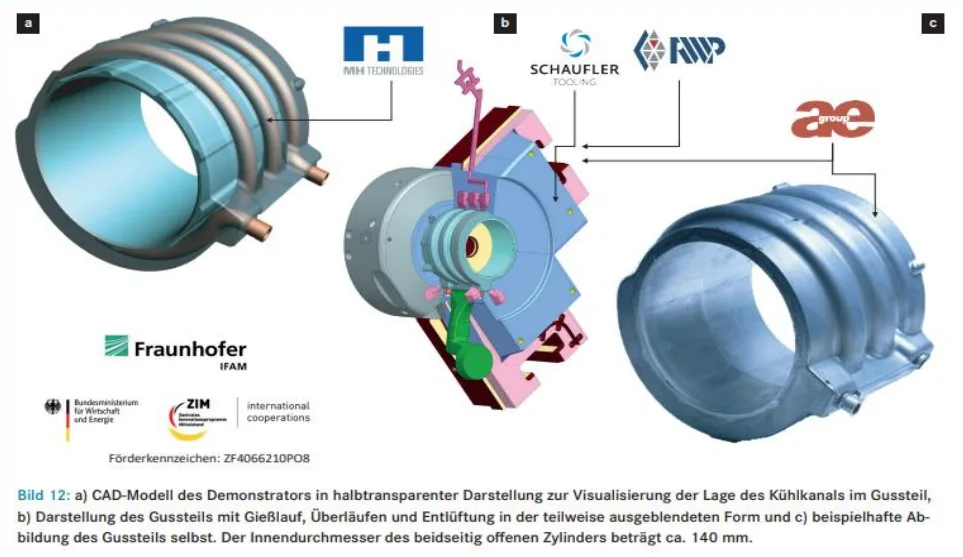
- Image 1: Pipes cast in for cooling engine components. The Steel pipe (left) withstands the manufacturing process; the aluminum tube (right) collapsed.
- Image 2: ZLeak Tube Technology: The two-component structure with a porous inner cross-section makes it much easier to remove the filler: a) Filled tube in cross section, b) a schematic representation of the principle of filler removal.
- Image 3: Mold inserts to determine the influence of different process parameters on stability, compression and deformation of ZLeak Tube pipes in the die casting process (developed and manufactured by Schaufler Tooling).
- Image 4: Validation of the simulation carried out by RWP GmbH using WinCast expert. The comparison was carried out using pouring tests with an interrupted shot.
- Image. 5: Dependency of the compression of different pipe variants on the casting pressure.
- Image 6: Dependence of the displacement of different pipe variants on the parameters or boundary conditions: a) recompression pressure, b) plunger speed, c) preheating temperature of the pipes, d) type of bearing.
- Image. 7: The simulation allows the determination of temperature-time curves for any position both in the cast part and in the depositors. In this specific case, temperatures of up to 530°C occur in the area of the pipe during the course of the mold filling and solidification, with a corresponding loss of strength.
- Image. 8: Comparison between the predicted and measured displacement of the pipe next to the gate under standard conditions, which is predicted by the casting simulation, meaning Pipe material EN AW-6063, wall thickness 2 mm (6063-1208), casting pressure nominal 800 bar, casting piston speed 2.5 m / s, temperature of mold and melt 220° C respectively 730 ° C, no preheating of the pipes, both side fixed bearing.
- Image. 9: Functional principle of the test setup for determining the heat transfer coefficient between pipe and casting. The embedded sketch illustrates which section of the casting was used for the measurements.
- Image. 10: Measurement results for the dependence of the heat transfer coefficient on the compression pressure, casting piston speed and preheating for the material variant EN AW-6063 and on the compression pressure for EN AW-3003.
- Image. 11: Problem of gap formation and its influence on the effective heat transfer coefficient.
- Image 12: a) CAD model of the demonstrator in a semi-transparent representation to visualize the position of the cooling channel in the casting, b) Representation of the cast part with pouring runner, overflows and ventilation in the partially hidden form and c) exemplary illustration of the cast part itself. The inner diameter of the cylinder, which is open on both sides, is approx. 140 mm.
- Image 13: CT-shot of the demonstrator with clearly visible gap between pipe and cast (compare enlarged detail on the right). The embedded picture shows the position of the cutting plane.
7. 결론 (Conclusion):
CoolCast 프로젝트의 결과는 다이캐스팅에서 ZLeak 튜브 기술의 타당성과 예측 가능성을 증명합니다. 이 새로운 솔루션은 다이캐스팅 부품에 알루미늄 튜브 기반의 유체 이송 채널을 구현하는 데 사용될 수 있으며, 정밀한 온도 제어가 필요한 전기 구동계의 핵심 부품 생산에 유망한 전망을 열어줍니다. 파이프는 최대 1200 bar의 재압축 압력까지 안정적입니다. 직경의 약간의 감소와 파이프의 열적 위치 이동은 주조 시뮬레이션을 통해 정확하게 예측될 수 있으며, 따라서 부품 설계에 반영될 수 있습니다. 이 기술은 설계자에게 더 큰 자유를 부여하여 재료 절약 및 더 큰 냉각 채널 직경을 가능하게 합니다. 채널과 주물 사이의 열적 연결에 대한 추가 최적화가 가능하지만, 이 기술은 이미 목표 요구 사항을 충족하며 E-모빌리티 응용 분야에서 HPDC의 매력을 높입니다.
8. 참고 문헌 (References):
- [1] Giesserei 105 (2018), [No.3], pp. 32-37
- [2] Heiselbetz, C.; Feikus, F. J.; Kniewallner, L.; Rafetzeder, M.; Luszczak, M. Challenges posed by E-Drive components:Casting solutions. Conference fee Casting technology in engine construction 2017, 01.-02. February 2017, Magdeburg.
- [3] SAE International Journal of Engines 2(2009), [No. 1], pp. 314-326.
- [4] Lahaye-Geusen, M. Light and compact housing for eight-speed automatic transmission lots of functionalities in a small space. https://automobilgestaltung.industrie. de / general / much-function-in-little space / (accessed 19.07.2021)
- [5] Foundry experience exchange 3/4 (2013) pp. 6-9.
- [6] www.mhrnd.com (accessed July 19, 2021)
- [7] Kim, J. S.; Yoo, J. High Pressure Die Casting Core and Preparation Method of High Pressure Die Casting Core. Korean patent KR101965669B1, date of Publication 04/04 2019.
전문가 Q&A: 자주 묻는 질문에 대한 답변
Q1: ZLeak 튜브 기술이 일반 중공 알루미늄 튜브를 주조하는 것보다 나은 이유는 무엇인가요?
A1: 일반 중공 알루미늄 튜브는 Image 1에서 볼 수 있듯이 HPDC 공정의 극심한 압력과 온도 하에서 붕괴됩니다. ZLeak 튜브의 혁신적인 이중층 충전재는 주조 중 이러한 힘을 견디는 데 필요한 내부 구조적 지지를 제공합니다. 그 후, 충전재는 쉽고 완벽하게 씻어낼 수 있도록 설계되어 완벽하게 형성된 누수 없는 채널을 남깁니다(Image 2).
Q2: 주조 중 파이프가 움직이는 것이 걱정됩니다. 제어해야 할 가장 큰 요인은 무엇인가요?
A2: 연구에 따르면, 파이프 변위에 가장 큰 영향을 미치는 요인은 용융물 흐름의 열적 효과와 파이프가 고정되는 방식(베어링)의 기계적 제약입니다. 연구는 파이프 인서트를 예열하고 한쪽 끝에 가동형 베어링을 사용하는 설계가 변위를 줄이는 데 매우 효과적이라는 것을 명확히 보여줍니다. 이러한 요인들은 재압축 압력을 조정하는 것보다 더 큰 영향을 미쳤습니다(Image 6).
Q3: 특정 금형 설계에서 이러한 튜브 인서트가 어떻게 작동할지 시뮬레이션으로 예측할 수 있나요?
A3: 네, 그렇습니다. 이 프로젝트의 핵심 성과 중 하나는 주조 시뮬레이션 소프트웨어의 강력한 검증이었습니다. 연구는 WinCast expert 소프트웨어로 예측된 파이프 변위와 실제 주조물의 측정 결과 사이에 탁월한 상관관계가 있음을 발견했습니다(Image 8). 이는 시뮬레이션이 이러한 인서트의 거동을 예측하는 신뢰할 수 있는 도구임을 증명하며, 금형 설계와 공정 변수를 자신 있게 최적화할 수 있도록 합니다.
Q4: 이 충전된 튜브는 어느 정도의 재압축 압력을 견딜 수 있나요?
A4: 이 연구는 최대 1200 bar의 재압축 압력을 테스트했습니다. ZLeak 튜브는 이 전체 범위에서 안정성을 유지했습니다. 결과는 압력 증가에 따라 예측 가능하고 거의 선형적인 압축(직경 감소)을 보여주며(Image 5), 이는 설계 단계에서 고려될 수 있습니다. 이는 까다로운 고압 다이캐스팅 공정에 대한 적합성을 확인시켜 줍니다.
Q5: 튜브용 알루미늄 합금 선택이 주조 성능에 어떤 영향을 미치나요?
A5: 논문에서 EN AW-6063과 EN AW-3003 합금을 비교한 결과 중요한 차이점이 드러났습니다. 동일한 형상에 대해 EN AW-3003 튜브는 압력 하에서 더 적은 압축을 보였고(Image 5), 주물과의 열전달 계수가 더 높았습니다(Image 10). 이는 튜브 합금의 선택이 최대 안정성 또는 열 성능을 위해 최적화할 수 있는 중요한 설계 변수임을 시사합니다.
Q6: 튜브의 벽 두께가 주조 중 안정성에 큰 영향을 미치나요?
A6: EN AW-6063 합금에 대해 연구된 범위 내에서, 1.5mm와 2mm 버전을 비교했을 때 안정성은 벽 두께에 크게 의존하지 않았습니다. 그러나 훨씬 얇은 1mm 벽은 더 뚜렷한 직경 감소를 보였습니다(Image 5). 이는 주어진 안정성 요구 사항에 대해, 주조 공정 중 인서트의 무결성을 손상시키지 않으면서 재료를 절약하거나 더 큰 내부 채널 직경을 설계하기 위해 더 얇은 벽(예: 1.5mm)을 사용할 수 있음을 시사합니다.
결론 및 다음 단계
이 연구는 HPDC 부품의 열 관리를 향상시키기 위한 귀중한 로드맵을 제공하며, 이는 E-모빌리티의 미래를 위한 중요한 원동력입니다. 연구 결과는 ZLeak 튜브 기술을 복잡하고 통합된 냉각 채널을 만드는 견고하고 예측 가능한 방법으로 검증하여, 전기 구동계 부품의 품질을 개선하고 제조 복잡성을 줄이며 성능을 최적화하기 위한 명확하고 데이터 기반의 경로를 제공합니다.
CASTMAN은 고객의 가장 어려운 다이캐스팅 문제를 해결하기 위해 최신 산업 연구를 적용하는 데 전념하고 있습니다. 귀사의 운영 목표와 이 논문에서 논의된 문제가 관련이 있다면, 저희 엔지니어링 팀에 연락하여 귀사의 부품에 이러한 첨단 원리를 적용하는 방법에 대해 논의해 보십시오.
저작권
- 이 자료는 "Dirk Lehmhus, Christoph Pille, Dustin Borheck, et al."의 논문입니다. "Leakage-free cooling channels for Die-cast housing components"를 기반으로 합니다.
- 논문 출처: https://www.ifam.fraunhofer.de/ (CoolCast 프로젝트의 일부, 펀딩 코드 ZF4066210PO8)
이 자료는 정보 제공 목적으로만 사용됩니다. 무단 상업적 사용을 금지합니다. Copyright © 2025 CASTMAN. All rights reserved.