SPH 시뮬레이션과 쇼트 샷 검증을 통해 HPDC 공정의 숨겨진 물리 현상(표면 스킨 파열)을 밝히다
이 기술 브리프는 Paul W. Cleary 등이 저술하여 2010년 Applied Mathematical Modelling에 게재한 학술 논문 "[Short shots and industrial case studies: Understanding fluid flow and solidification in high pressure die casting]"을 기반으로 합니다. HPDC 전문가들을 위해 CASTMAN의 전문가들이 요약 및 분석하였습니다.
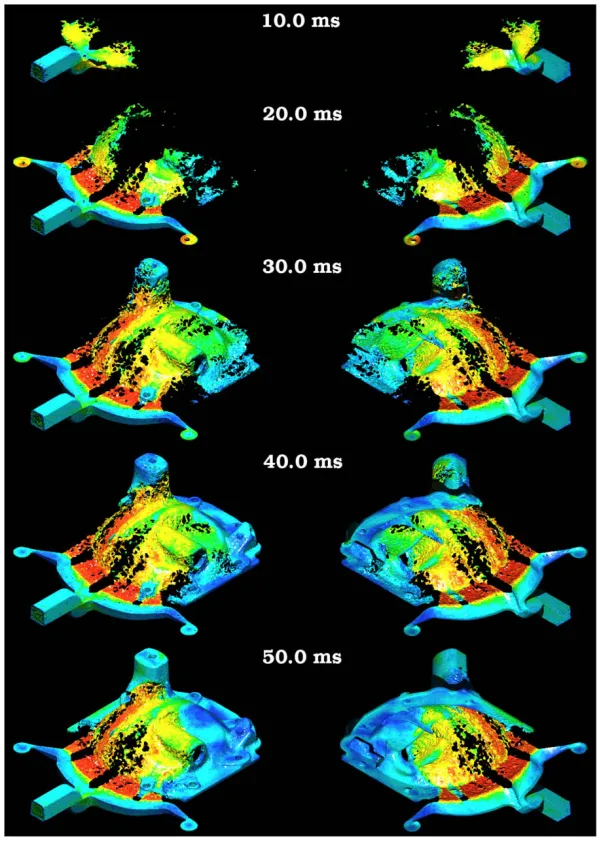
키워드
- Primary Keyword: 고압 다이캐스팅(HPDC) 유동 해석
- Secondary Keywords: SPH 시뮬레이션, 쇼트 샷, 응고 모델링, 주조 결함, 유동 검증, 표면 스킨 형성
Executive Summary
- 도전 과제: 고압 다이캐스팅(HPDC) 공정의 복잡하고 빠른 유동으로 인해 발생하는 기공과 같은 결함을 예측하고 제어하는 것은 매우 어렵습니다. 특히, 시뮬레이션 모델의 정확성을 검증하는 데에는 명확한 한계가 존재합니다.
- 연구 방법: 본 연구에서는 격자 없는 라그랑지안 기법인 SPH(입자 유체 역학)를 사용하여 HPDC 공정을 시뮬레이션했습니다. 또한, 금형 캐비티를 의도적으로 불완전하게 충전하는 '쇼트 샷(short shot)' 실험을 통해 유동 및 열전달/응고 모델의 예측 정확도를 검증했습니다.
- 핵심 발견: 시뮬레이션과 쇼트 샷 실험 결과 간의 불일치 분석을 통해, 충전 초기 단계에서 게이트에 형성된 얇은 '표면 스킨(고체 또는 산화막)'의 파열 현상이 실제 유동에 결정적인 영향을 미친다는 새로운 가설을 제시했습니다.
- 핵심 결론: HPDC 공정의 정확한 예측과 제어를 위해서는 기존 유체 역학 모델에 포함되지 않았던 표면 스킨의 형성 및 파열과 같은 미세 물리 현상에 대한 깊이 있는 이해와 모델링이 필수적입니다.
도전 과제: 이 연구가 HPDC 전문가에게 중요한 이유
고압 다이캐스팅(HPDC)은 자동차, 가전제품, 전자 산업에서 대량의 부품을 저비용으로 생산하는 핵심 공정입니다. 용융 금속(주로 알루미늄, 마그네슘, 아연)을 30-100 m/s의 고속으로 복잡한 형상의 금형에 주입하는 이 공정은 필연적으로 매우 복잡한 3차원 유동과 심한 유동 분열(fragmentation) 및 스플래싱(splashing)을 동반합니다.
이러한 복잡한 유동 패턴은 금형 내 공기 혼입을 유발하여 최종 제품에 기공(porosity)과 같은 결함을 발생시키는 주된 원인이 됩니다. 따라서 금형의 어느 부분이 먼저 채워지는지, 에어 벤트는 어디에 위치해야 하는지를 파악하는 것은 균일하고 결함 없는 부품을 생산하는 데 매우 중요합니다. 수치 시뮬레이션은 다양한 금형 설계와 충전 공정을 비용 효율적으로 연구할 수 있는 강력한 도구이지만, 그 예측의 신뢰성을 확보하는 것은 여전히 큰 과제로 남아있습니다. 본 연구는 바로 이 지점에서 시작하여, 최신 시뮬레이션 기법과 실험적 검증을 통해 HPDC 공정의 근본적인 물리 현상을 이해하고자 합니다.
접근 방식: 연구 방법론 분석
본 연구는 복잡한 HPDC 유동을 모델링하는 데 매우 효과적인 것으로 입증된 SPH(Smoothed Particle Hydrodynamics) 기법을 사용했습니다. SPH는 고정된 격자 대신 자유롭게 움직이는 입자로 재료를 근사화하는 라그랑지안(Lagrangian) 방식입니다. 이 기법은 다음과 같은 장점 때문에 HPDC 시뮬레이션에 특히 적합합니다.
- 복잡한 자유 표면의 거동과 유동 분열을 자연스럽게 모델링할 수 있습니다.
- 격자 기반 방식에서 발생하는 계단 현상(stair-stepping)과 같은 인위적인 오류가 없습니다.
- 운동량이 지배적인 고속 유동을 매우 효과적으로 처리합니다.
연구팀은 SPH 시뮬레이션의 예측력을 검증하기 위해 쇼트 샷(short shot) 이라는 강력한 실험 기법을 활용했습니다. 쇼트 샷은 의도적으로 용탕량을 줄이거나 주입을 중간에 멈춰 금형 캐비티를 부분적으로만 채우는 방법입니다. 이렇게 부분적으로 채워져 응고된 주물은 충전 순서와 각 단계에서 발생하는 유동 구조에 대한 귀중한 정보를 담고 있습니다. 연구팀은 이 실험적 쇼트 샷의 최종 형상과 SPH 시뮬레이션(유동, 열전달, 응고를 모두 고려)의 예측 결과를 비교하여 모델의 정확도를 평가했습니다.
핵심 발견: 주요 결과 및 데이터
본 연구는 3가지 산업 사례(자동차 디퍼렌셜 커버, 전자 하우징, 아연 도어록 플레이트)와 단순 코스터(coaster)의 쇼트 샷 분석을 통해 다음과 같은 중요한 발견을 했습니다.
- 발견 1: 산업 부품의 복잡한 충전 패턴 예측
SPH 시뮬레이션은 실제 산업 부품의 복잡한 3D 충전 패턴을 매우 상세하게 예측했습니다. 예를 들어, 자동차 디퍼렌셜 커버(Figure 1) 충전 시, 용탕이 게이트를 통과해 분사된 후 금형 벽을 따라 흐르다가 다시 게이트 방향으로 역류하는 '백 필링(back filling)' 현상이 명확하게 관찰되었습니다. 이러한 흐름은 공기가 빠져나갈 통로를 조기에 차단하여 내부에 공기를 가두고 기공을 형성할 가능성을 높입니다. - 발견 2: 쇼트 샷 검증을 통한 시뮬레이션 정확도 평가
단순 코스터의 쇼트 샷 비교에서, 충전율이 25% 이상일 경우 시뮬레이션은 실험 결과의 전반적인 형상을 잘 예측했습니다(Figure 6). 하지만 충전율이 10%로 매우 낮은 초기 단계에서는 시뮬레이션과 실험 결과 사이에 상당한 차이가 발견되었습니다(Figure 7). - 발견 3: '표면 스킨 파열' 가설의 제시
10% 충전율 쇼트 샷 실험에서는 시뮬레이션에서 예측된 대칭적인 유동과 달리, 비대칭적이고 긴 돌출부가 관찰되었습니다(Figure 7). 연구팀은 이 현상을 설명하기 위해 다음과 같은 가설을 제시했습니다: 러너가 채워지는 동안 좁은 게이트 입구에서 용탕의 표면장력과 냉각으로 인해 얇은 고체/산화 스킨(skin)이 형성된다. 이후 러너 내부 압력이 충분히 높아지면 이 스킨이 국부적으로 파열되면서 고압의 용탕이 구멍을 통해 분출된다. 이 '스킨 파열' 현상은 실험에서 관찰된 비대칭적이고 예측 불가능한 초기 유동 패턴을 설명할 수 있습니다. - 발견 4: 공정 변수가 쇼트 샷 형상에 미치는 영향 분석
시뮬레이션을 통해 용탕의 과열도(super-heat)와 금형 온도를 변화시키며 쇼트 샷 형상을 예측했습니다(Figure 8, 9). 이 결과를 실제 실험 결과와 비교함으로써, 실험 당시의 정확한 공정 조건을 역으로 추정할 수 있었습니다. 이는 공정 변수 제어의 중요성을 명확히 보여줍니다.
귀사의 HPDC 운영을 위한 실질적 시사점
본 연구 결과는 실제 HPDC 생산 현장에 다음과 같은 중요한 시사점을 제공합니다.
- 공정 엔지니어를 위해: Figure 1, 2, 3에서 볼 수 있듯이, SPH 시뮬레이션은 충전 패턴을 시각화하고 잠재적인 기공 발생 위치를 사전에 정확히 예측할 수 있습니다. 이를 통해 엔지니어는 양산 전에 게이트 시스템과 에어 벤트 설계를 최적화하여 결함 발생을 근본적으로 줄일 수 있습니다.
- 품질 관리를 위해: 쇼트 샷 검증은 충전 초기 단계의 문제를 진단하는 강력한 도구입니다. 특히, 본 논문에서 제시된 '스킨 파열' 가설은 소형 주물에서 발생하는 예측 불가능한 품질 변동이 단순한 공정 변수의 편차 때문이 아니라, 이러한 미세 물리 현상에 기인할 수 있음을 시사합니다.
- 금형 설계를 위해: 본 연구는 게이트의 역할을 다시 한번 강조합니다. '스킨 파열' 가설에 따르면, 게이트의 형상과 두께는 단순히 유량을 조절하는 것을 넘어, 초기 유동을 막는 '장벽'의 형성 및 강도에 직접적인 영향을 미칩니다. 따라서 더욱 정교한 게이트 설계가 초기 충전 안정성을 확보하는 데 핵심적일 수 있습니다.
Paper Details
Short shots and industrial case studies: Understanding fluid flow and solidification in high pressure die casting
1. 개요:
- 제목: Short shots and industrial case studies: Understanding fluid flow and solidification in high pressure die casting
- 저자: Paul W. Cleary, Joseph Ha, Mahesh Prakash, Thang Nguyen
- 발행 연도: 2010
- 게재 학술지: Applied Mathematical Modelling
- 키워드: High pressure die casting, SPH, Solidification, Short shot, Fluid flow, Casting defects
2. 초록:
고압 다이캐스팅(HPDC)에서 나타나는 기하학적 복잡성과 높은 유체 속도는 상당한 자유 표면 분열과 스플래싱을 동반하는 강한 3차원 유체 유동을 야기한다. HPDC 모델링에 특히 적합한 것으로 입증된 시뮬레이션 방법은 SPH(Smoothed Particle Hydrodynamics)이다. 재료는 고정된 격자가 아닌 자유롭게 움직일 수 있는 입자로 근사화되어, 복잡한 자유 표면 운동을 포함하는 유체 유동을 더 정확하게 예측할 수 있다. 본 논문에서는 SPH로 시뮬레이션한 HPDC 유동의 세 가지 실제 산업 사례 연구(자동차용 디퍼렌셜 커버, 전자 하우징, 아연 도어록 플레이트의 알루미늄 주조)를 제시한다. 이 연구들은 분열된 유체 자유 표면의 상당한 세부 사항을 보여주며, 주물 내 기공과 같은 결함을 생성하는 경향을 이해할 수 있게 한다. 열전달 및 응고와 결합된 유동 예측의 검증은 이러한 모델링에서 중요한 영역이다. 한 가지 강력한 접근법은 쇼트 샷을 사용하는 것인데, 이는 주조에 불충분한 금속을 사용하거나 주조 샷을 중간에 멈춰 금형 캐비티를 부분적으로만 채우는 것이다. 동결된 부분 주물은 충전 순서와 충전의 다른 단계에서 발생하는 유동 구조에 대한 중요한 세부 정보를 포착한다. 검증은 실험 및 시뮬레이션된 쇼트 샷을 일치시킴으로써 이루어질 수 있다. 여기서는 간단한 코스터 주조의 쇼트 샷에 대한 금형 온도, 금속 과열도 및 충전 부피의 영향을 탐구한다. 최종 고체 주물의 대규모 특징은 예측과 잘 일치하는 것으로 나타났지만, 미세한 세부 사항은 응고하는 금속의 표면 거동에 따라 달라지는 것으로 보인다. 이는 HPDC 모델링에 잠재적으로 중요한 영향을 미칠 수 있다.
3. 서론 요약:
HPDC는 자동차, 생활용품, 전자 산업에서 대량의 저비용 부품을 제조하는 중요한 공정이다. 용융 금속은 복잡한 게이트 및 러너 시스템을 통해 고속(30-100 m/s) 및 고압으로 금형에 주입된다. 금형의 기하학적 복잡성은 심한 자유 표면 분열과 스플래싱을 동반하는 강한 3차원 유체 유동을 유발한다. 금형의 다양한 부분이 채워지는 순서와 에어 벤트의 위치는 최소한의 공기 혼입이나 기공으로 균일한 주조 부품을 형성하는 데 매우 중요하다. 이는 게이팅 시스템의 설계와 금형의 기하학적 구조에 의해 영향을 받는다. 수치 시뮬레이션은 다양한 금형 설계와 충전 공정의 효율성을 연구하는 강력하고 비용 효율적인 방법을 제공하며, 궁극적으로 제품 품질과 생산성 향상으로 이어진다.
4. 연구 요약:
연구 주제의 배경:
HPDC 공정은 고속, 고압의 복잡한 유동 특성으로 인해 시뮬레이션하기 매우 까다롭다. 기존의 격자 기반 시뮬레이션 기법들은 복잡한 자유 표면과 유동 분열을 정확히 모사하는 데 한계가 있었다. SPH는 이러한 한계를 극복할 수 있는 대안으로 주목받아왔다.
이전 연구 현황:
Flow3D, MagmaSoft, Fluent와 같은 여러 격자 기반 기법들이 HPDC 시뮬레이션에 사용되어 왔다. 그러나 복잡한 3D 형상에서 계단 현상(stair-stepping)과 같은 인위적인 오류가 발생하는 문제가 있었다. SPH는 열유동 문제에 적용되어 왔으며, 특히 HPDC 공정 모델링에 사용되어 물 아날로그 실험을 통해 주로 검증이 이루어졌다.
연구 목적:
본 연구의 목적은 SPH를 사용하여 실제 산업 규모의 HPDC 공정의 충전 과정을 예측하고, 이를 통해 공기 혼입으로 인한 기공의 범위와 분포를 추론하는 것이다. 또한, 쇼트 샷 실험을 HPDC의 유동 및 열 예측 검증에 활용하고, 다양한 공정 변수가 최종 쇼트 샷 형상에 미치는 영향을 체계적으로 연구하는 것이다.
핵심 연구:
본 연구는 세 가지 산업 사례(디퍼렌셜 커버, 전자 하우징, 도어록 플레이트)에 대한 SPH 시뮬레이션을 수행하여 충전 패턴과 잠재적 결함 위치를 예측했다. 더 나아가, 단순 코스터 주물에 대한 쇼트 샷 실험과 시뮬레이션을 비교 분석했다. 이 과정에서 충전 부피, 금형 온도, 용탕 과열도와 같은 변수들이 최종 응고 형상에 미치는 영향을 조사하고, 시뮬레이션과 실험 간의 불일치를 통해 기존 모델이 포착하지 못하는 중요한 물리 현상(표면 스킨 파열)에 대한 가설을 수립했다.
5. 연구 방법론
연구 설계:
본 연구는 SPH 시뮬레이션과 실험적 검증을 결합한 방식으로 설계되었다.
- 산업 사례 연구: 3가지 실제 산업 부품에 대해 등온 SPH 시뮬레이션을 수행하여 충전 패턴을 분석했다.
- 쇼트 샷 검증 연구: 단순 코스터 금형을 사용하여 다양한 조건(충전 부피, 금형 온도, 용탕 과열도)에서 쇼트 샷 실험을 수행했다. 이와 동일한 조건으로 유동-열-응고가 연성된 SPH 시뮬레이션을 수행하고, 최종 응고 형상을 실험 결과와 정량적으로 비교했다.
데이터 수집 및 분석 방법:
- 시뮬레이션: SPH 방법을 사용하여 유동, 열전달, 응고를 계산했다. 운동량 방정식, 연속 방정식, 에너지(엔탈피) 방정식을 SPH 형태로 변환하여 사용했다. 알루미늄의 온도에 따른 점성, 비열, 잠열 등의 물성 데이터를 모델에 적용했다(Figure 4).
- 실험: 알루미늄을 사용하여 단순 코스터 금형에서 쇼트 샷을 제작했다. 의도적으로 충전량을 10%, 25% 등으로 조절하여 부분적으로 채워진 주물을 얻었다.
- 분석: 시뮬레이션으로 예측된 최종 응고 형상과 실험으로 얻은 쇼트 샷 주물의 형상을 시각적으로 비교 분석하여 일치점과 불일치점을 파악하고, 그 원인을 추론했다.
연구 주제 및 범위:
- SPH를 이용한 복잡한 HPDC 공정의 3차원 유동 시뮬레이션
- 산업 부품(디퍼렌셜 커버, 전자 하우징, 도어록 플레이트)의 충전 패턴 및 결함 발생 가능성 예측
- 쇼트 샷 실험을 통한 SPH 시뮬레이션의 유동 및 열-응고 모델 검증
- 금형 온도, 용탕 과열도, 충전 부피가 쇼트 샷 형상에 미치는 영향 분석
- 시뮬레이션과 실험의 불일치를 통한 새로운 물리 현상(표면 스킨 파열) 가설 제시
6. 주요 결과:
주요 결과:
- 산업 사례: SPH 시뮬레이션은 디퍼렌셜 커버(Figure 1), 전자 하우징(Figure 2), 도어록 플레이트(Figure 3)의 복잡한 충전 과정을 성공적으로 예측했다. 공통적으로 초기 제트 유동, 유동 분열, 금형 벽을 따른 레이스 트래킹(race tracking), 그리고 후반부의 역충전(back filling) 현상이 관찰되었으며, 이는 공기 혼입 및 기공 형성의 주요 메커니즘임을 보여주었다.
- 쇼트 샷 검증: 25% 충전율에서는 시뮬레이션과 실험이 전반적으로 잘 일치했다(Figure 6). 그러나 10% 충전율에서는 실험에서 비대칭적인 돌출부가 나타나는 등 큰 차이를 보였다(Figure 7).
- 표면 스킨 파열 가설: 10% 충전율에서의 불일치는 게이트에서 형성된 얇은 고체/산화 스킨이 파열되면서 용탕이 국부적으로 분출되는 현상으로 설명될 수 있다. 이 가설은 HPDC 공정, 특히 소형 주물에서 관찰되는 높은 변동성의 원인을 설명할 수 있다.
- 공정 변수 민감도: 용탕 과열도가 낮아질수록(-10°C 이하) 유동 분열이 현저히 감소하고 유동 전면이 매끄러워지는 경향을 보였다(Figure 8). 또한, 금형 온도가 낮을수록 용탕이 게이트 근처에서 빠르게 응고하여 더 짧은 거리까지만 전진했다(Figure 9). 이러한 비교를 통해 실제 실험 조건이 과열도 약 -10°C, 금형 온도 27°C(상온)에 가까웠을 것으로 추정했다.
Figure Name List:
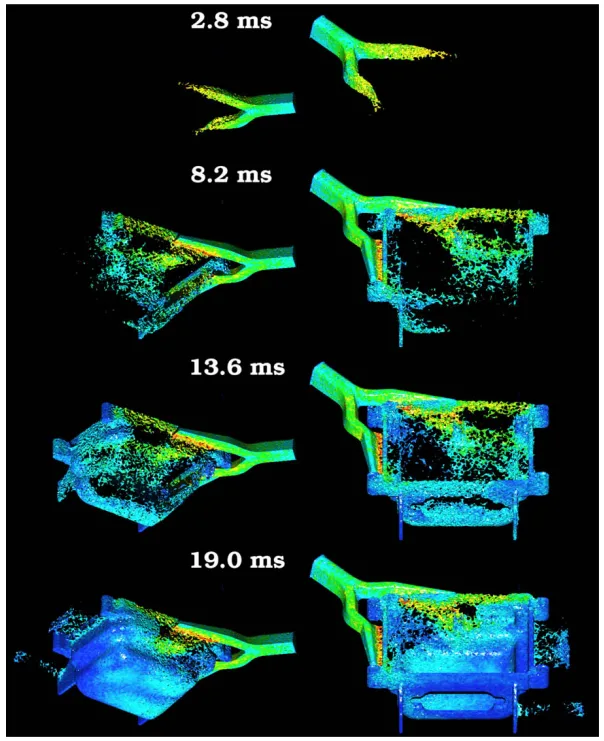
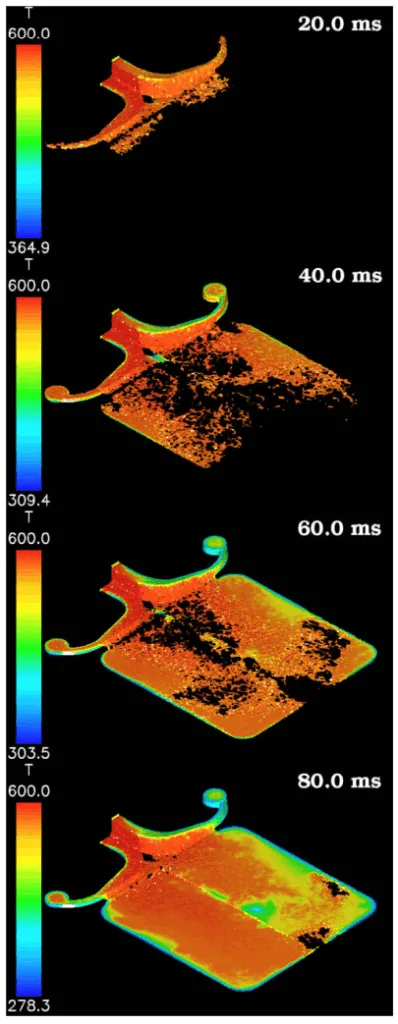
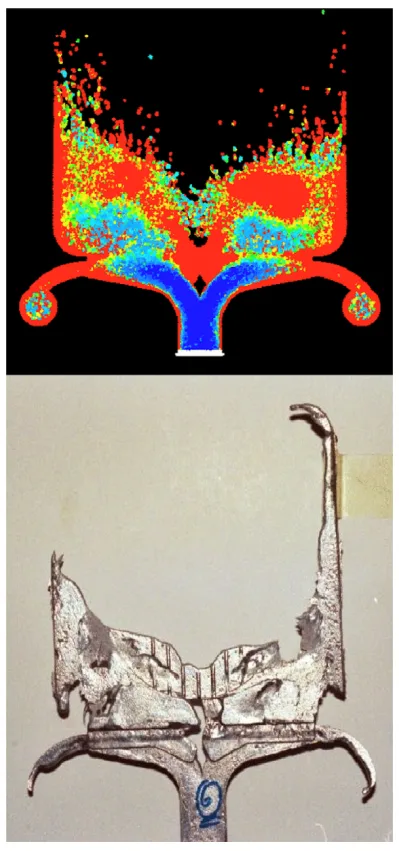
- Fig. 1. Filling of differential cover with the molten metal coloured by speed with blue being slow and red being fast. The casting is shown in top view on the left and bottom view on the right.
- Fig. 2. An electronic housing filled from a Y-shaped runner (coloured by speed).
- Fig. 3. Filling of the front and back plates of a zinc door lock (coloured by speed).
- Fig. 4. Variation of liquid aluminium properties with temperature; (a) viscosity and (b) enthalpy per unit mass.
- Fig. 5. Filling of coaster (including heat transfer and solidification) with fluid coloured by temperature.
- Fig. 6. Short shot with 25% volume fill: simulation (top) with colour representing viscosity, blue being low and red high; and experiment (bottom).
- Fig. 7. Short shot with 10% volume fill: simulation (top) and experiment (bottom).
- Fig. 8. Short shot variation for a 10% fill with different initial metal temperatures (degree of super-heat).
- Fig. 9. Short shot variation for a 10% fill for different initial die temperatures.
7. 결론:
본 연구는 SPH를 사용하여 아연 도어록부터 알루미늄 디퍼렌셜 커버에 이르는 세 가지 산업 부품의 HPDC 충전을 3D로 시뮬레이션했다. 모든 유동에서 초기 제트는 빠르고 매우 분열되며, 금형 반대편에 도달한 후 게이트 쪽으로 다시 채워지는 공통적인 특징을 보였다. 유동은 일반적으로 부품의 두꺼운 구조적 림을 따라 먼저 흐르며 충전 과정 초기에 배출구를 막아 많은 양의 공기를 가두게 된다. 이 갇힌 공기는 미세 기공을 보장하며, 후반 유동 패턴의 세부 사항이 이 기공의 분포를 결정한다.
검증 과정의 일환으로, 실험적 쇼트 샷을 SPH 시뮬레이션과 비교했다. 25% 이상의 충전율에서는 시뮬레이션이 실험적 쇼트 샷 형상의 상당 부분을 포착할 수 있었으나, 10% 충전율에서는 상당한 차이가 나타났다. 실험적 쇼트 샷의 특성은 러너 충전 단계에서 게이트를 가로질러 기계적 강도를 가진 고체 금속 또는 산화물 스킨이 형성됨을 시사한다. 러너가 충분히 가압되면 이 스킨이 파열되어 금형으로 유체를 분출한다. 이 스킨 파열 과정의 세부 사항이 금형 캐비티 내 유체 유동의 초기 세부 사항을 대부분 제어하는 것으로 보인다. 이 효과는 충전 초기와 게이트 근처에서 유동에 가장 강하게 영향을 미치며, 이는 HPDC, 특히 소형 부품에서 관찰되는 높은 변동성을 설명하는 데 도움이 된다. 이러한 표면 현상은 모델러와 실험가 모두에게 상당한 도전을 제기한다.
8. References:
- [1] T. Yoshimura, K. Yano, T. Fukui, S. Yamamoto, S. Nishido, M. Watanabe, Y. Nemoto, Optimum design of die casting plunger tip considering air entrainment, in: Proceedings of the 10th Asian Foundry Congress, Nagoya, Japan, 2008.
- [2] V. Kokot, P. Bernbeck, What is a good gating system? or Quantifying quality but how? Paper No.: 179041, in: Proceedings of the XX MCWASP Conference, France, 2006.
- [3] L.X. Kong, F.H. She, W.M. Gao, S. Nahavandi, P.D. Hodgson, Integrated optimisation system for high pressure die casting processes, J. Mater. Process. Technol. 201 (2008) 629-634.
- [4] J.J. Monaghan, Smoothed particle hydrodynamics, Ann. Rev. Astron. Astrophys. 30 (1992) 543-574.
- [5] J.J. Monaghan, Simulating free surface flows with SPH, J. Comput. Phys. 110 (1994) 399-406.
- [6] P.W. Cleary, M. Prakash, J. Ha, N. Stokes, C. Scott, Smooth particle hydrodynamics: status and future potential, Prog. Comput. Fluid Dynam. 7 (2007) 70-90.
- [7] P.W. Cleary, J.J. Monaghan, Conduction modelling using smoothed particle hydrodynamics, J. Comput. Phys. 148 (1999) 227-264.
- [8] P.W. Cleary, Modelling confined multi-material heat and mass flows using SPH, Appl. Math. Model. 22 (1998) 981-993.
- [9] W. Thorpe, P.W. Cleary, J. Ha, N. Stokes, V. Ahuja, M. Jahedi, Simulation of fluid flow within the die cavity in high pressure die casting using smooth particle hydrodynamics, in: Proceedings of the 20th International Die Casting Congress and Exposition, 1999, pp. 23-36.
- [10] P.W. Cleary, J. Ha, V. Ahuja, High pressure die casting simulation using smoothed particle hydrodynamics, Int. J. Cast Metal. Res. 12 (2000) 335-355.
- [11] P.W. Cleary, J. Ha, M. Prakash, T. Nguyen, 3D SPH flow predictions and validation for high pressure die casting of automotive components, Appl. Math. Model. 30 (2006) 1406-1427.
- [12] J. Ha, P.W. Cleary, Simulation of high pressure die filling of a moderately complex industrial object using Smoothed Particle Hydrodynamics, Int. J. Cast Metal. Res. 18 (2005) 81-92.
- [13] J. Ha, P.W. Cleary, Comparison of SPH simulations of high pressure die casting with the experiments and VOF simulations of Schmidt and Klein, Int. J. Cast Metal. Res. 12 (2000) 409-418.
- [14] J. Ha, P.W. Cleary, V. Alguine, T. Nguyen, Simulation of die filling in gravity die casting using SPH and MAGMAsoft, in: Proceedings of the Second International Conference on CFD in Minerals and Process Industries, Melbourne, Australia, 1999, pp. 423-428.
결론 및 다음 단계
이 연구는 HPDC 공정의 품질 향상을 위한 귀중한 로드맵을 제공합니다. 연구 결과는 품질을 개선하고 결함을 줄이며 생산을 최적화하기 위한 명확하고 데이터 기반의 경로를 제시합니다.
STI C&D는 고객의 가장 어려운 기술적 문제를 해결하기 위해 최첨단 산업 연구를 적용하는 데 전념하고 있습니다. 이 백서에서 논의된 문제가 귀사의 연구 목표와 일치한다면, 저희 엔지니어링 팀에 연락하여 이러한 고급 원칙을 귀사의 연구에 적용하는 데 어떻게 도움을 드릴 수 있는지 논의해 주십시오.
Expert Q&A:
- Q1: 왜 SPH 기법이 HPDC 공정 시뮬레이션에 적합한가요?
A1: SPH는 재료를 자유롭게 움직이는 입자로 근사화하는 라그랑지안(격자 없음) 방식이기 때문입니다. 이는 HPDC에서 흔히 발생하는 복잡한 자유 표면의 분열과 스플래싱을 격자 기반 방식의 인위적인 오류(예: 계단 현상) 없이 자연스럽고 정확하게 모델링할 수 있게 해줍니다. (출처: "Short shots and industrial case studies: Understanding fluid flow and solidification in high pressure die casting", Section 2) - Q2: '쇼트 샷(short shot)'이란 무엇이며, 시뮬레이션 검증에 왜 유용한가요?
A2: 쇼트 샷은 의도적으로 금형을 부분적으로만 채우는 실험 기법입니다. 이렇게 얻어진 부분 응고 주물은 충전 과정의 특정 시점에서 유동 패턴을 '동결'시켜 보여주는 역할을 합니다. 따라서 충전 순서, 유동 구조 등 시간에 따라 변하는 복잡한 현상에 대한 상세 정보를