결함 없는 구조용 부품의 비밀: 고청정 다이캐스팅 공정 및 금형 설계 혁신
이 기술 브리핑은 Varun Nandakumar가 2014년 The Ohio State University에 제출한 학위 논문 "[Process and Tool Design for the High Integrity Die Casting of Aluminum and Magnesium Alloys]"를 기반으로 합니다. HPDC 전문가를 위해 CASTMAN의 전문가들이 요약 및 분석하였습니다.

키워드
- 주요 키워드: 고청정 다이캐스팅 (High Integrity Die Casting)
- 보조 키워드: 진공 다이캐스팅, 알루미늄 합금, 마그네슘 합금, 용탕 품질, 가스 기공, 칠 블록 설계, 응고 시뮬레이션
Executive Summary
- 과제: 기존의 고압 다이캐스팅(HPDC) 공정은 내부 기공 문제로 인해 열처리가 어렵고, 자동차의 구조용 부품과 같은 고강도, 고연성 부품에 적용하기 어려웠습니다.
- 방법: 본 연구는 두 가지 핵심적인 접근법을 사용했습니다. 첫째, 회전식 탈가스 장치를 사용하여 용탕 내 수소 가스를 제거함으로써 용탕 품질을 향상시켰습니다. 둘째, 시뮬레이션과 실험계획법(DOE)을 통해 금형 내 공기를 효과적으로 제거하는 진공 보조 시스템용 '칠 블록(Chill Block)'을 설계하고 검증했습니다.
- 핵심 성과: 통제된 조건(10-15분)의 용탕 탈가스 처리가 기공을 크게 줄여 열처리가 가능한 부품 생산의 길을 열었습니다. 또한, 구리 소재와 더 작은 갭을 가진 칠 블록이 금형 내 가스 배출에 가장 효과적임을 데이터로 입증하며, 최적의 진공 시스템 설계 워크플로우를 제시했습니다.
- 결론: 이 연구는 용탕 품질 관리와 진공 시스템 설계를 통합하여, 기존 HPDC의 한계를 뛰어넘어 고강도 구조용 부품을 생산할 수 있는 실용적인 프레임워크를 제공합니다.
과제: 왜 이 연구가 HPDC 전문가에게 중요한가?
자동차 산업의 연비 향상과 배출가스 규제 강화 요구에 따라 강철 부품을 알루미늄이나 마그네슘과 같은 경량 합금으로 대체하려는 움직임이 가속화되고 있습니다. 특히 차체 프레임, 필러 등 안전과 직결된 구조용 부품의 경량화가 핵심 과제로 떠올랐습니다.
하지만 기존의 고압 다이캐스팅(HPDC) 공정은 용탕 주입 시 발생하는 가스 혼입과 응고 수축으로 인한 기공 결함을 피하기 어려웠습니다. 이 기공은 부품의 기계적 특성(특히 연신율)을 저하시키고, 열처리 시 블리스터링(blistering) 현상을 유발하여 구조용 부품으로의 적용을 가로막는 가장 큰 장벽이었습니다(Twarog, 2011, Figure 11). 엔지니어들은 수십 년간 이 문제를 해결하기 위해 고군분투해왔으며, 본 연구는 이 근본적인 문제에 대한 체계적인 해결책을 제시합니다.
접근법: 연구 방법론 분석
연구진은 고청정 다이캐스팅 부품 생산이라는 목표를 달성하기 위해 두 가지 핵심 영역에 집중했습니다.
용탕 품질 개선: 알루미늄 용탕의 가장 큰 문제인 수소 가스 기공을 줄이기 위해 회전식 임펠러 탈가스 장치(PYROTEK® STAR 300®, Figure 29)를 도입했습니다. 아르곤(Ar) 가스를 취입 가스로 사용하여 탈가스 실험을 진행했으며, 감압 응고 시험기(RPT, Figure 31)와 아르키메데스법을 이용한 밀도 측정을 통해 탈가스 효과를 정량적으로 평가했습니다.
진공 시스템 금형 설계: 금형 캐비티 내에 갇힌 공기를 제거하기 위해 진공 보조 시스템을 설계했습니다. 특히 유지보수가 용이하고 비용 효율적인 밸브리스(valve-less) 방식인 '칠 블록' 설계에 초점을 맞췄습니다.
- MAGMA 시뮬레이션: 먼저 주조 공정 시뮬레이션을 통해 칠 블록 입구에서의 용탕 온도와 속도 등 초기 조건을 도출했습니다(Figure 40).
- 실험계획법(DOE) 및 ANSYS 해석: 칠 블록의 핵심 설계 변수(재질: H13 vs. 구리, 갭 두께: 0.02인치 vs. 0.04인치, 열전달계수)가 용탕의 동결 시간에 미치는 영향을 분석하기 위해 2³ 실험계획법을 적용하고 ANSYS 열 해석을 수행했습니다(Figure 42, Table 3).
핵심 성과: 주요 발견 및 데이터
본 연구를 통해 고청정 다이캐스팅을 위한 몇 가지 중요한 성과를 도출했습니다.
성과 1: 최적의 탈가스 조건 확립
A380 및 다른 알루미늄 합금을 대상으로 한 실험에서, 약 10~15분간의 회전식 탈가스 처리가 용탕의 밀도를 크게 향상시키는 것으로 나타났습니다(Figure 33). 이렇게 처리된 용탕으로 제작된 시편은 485°C에서 3시간 동안 열처리를 해도 블리스터링이 발생하지 않았습니다(Figure 34). 이는 용탕 내 가스 함량이 매우 낮은 수준으로 제어되었음을 의미하며, HPDC 부품의 열처리 가능성을 실증적으로 보여줍니다.성과 2: 칠 블록 설계의 핵심 인자 규명
ANOVA(분산분석) 결과, 칠 블록의 성능(용탕 동결 시간)에 가장 큰 영향을 미치는 요인은 재질과 갭 두께인 것으로 밝혀졌습니다(Table 6). 열전도율이 높은 구리가 H13 공구강보다 용탕을 더 빨리 동결시켰으며, 갭 두께가 좁을수록 동결 시간이 단축되었습니다. 반면, 열전달계수(HTC)는 본 연구의 형상에서는 통계적으로 유의미한 영향을 미치지 않는다는 흥미로운 결과를 얻었습니다.성과 3: 데이터 기반의 최적 칠 블록 설계 완료
시뮬레이션과 실험계획법 결과를 종합하여, 최종적으로 구리 재질에 0.03인치의 갭 두께를 가진 칠 블록 설계를 최적 안으로 도출했습니다. 이 연구는 초기 개념 구상부터 시뮬레이션, 최적화, 최종 CAD 설계 및 가공에 이르는 칠 블록 설계의 전 과정을 체계적인 워크플로우로 제시했습니다(Figure 44).
HPDC 제품을 위한 실질적인 시사점
본 연구 결과는 실제 다이캐스팅 생산 현장에 다음과 같은 중요한 시사점을 제공합니다.
공정 엔지니어를 위해: 논문에서 제시된 회전식 탈가스 장치의 운용 조건(탈가스 시간, 가스 유량 등)을 참고하여 용탕 처리 공정을 표준화함으로써 수소 기공 결함을 획기적으로 줄일 수 있습니다. 이는 제품의 기계적 물성 안정화로 이어집니다.
품질 관리를 위해: 감압 응고 시험(RPT)과 밀도 측정은 생산 현장에서 용탕의 청정도를 신속하게 모니터링할 수 있는 효과적인 도구입니다. 데이터 기반의 용탕 관리를 통해 최종 제품의 품질을 예측하고 불량률을 낮출 수 있습니다.
금형 설계를 위해: 본 연구는 비용 효율적인 진공 시스템인 '칠 블록'의 설계 및 검증에 대한 완벽한 가이드를 제공합니다. 특히 구조용 부품과 같이 고품질이 요구되는 신규 금형 개발 시, Figure 44에 제시된 설계 프로세스를 적용하여 개발 기간을 단축하고 초기 품질 문제를 예방할 수 있습니다.
논문 상세 정보
알루미늄 및 마그네슘 합금의 고청정 다이캐스팅을 위한 공정 및 금형 설계
1. 개요:
- 제목: Process and Tool Design for the High Integrity Die Casting of Aluminum and Magnesium Alloys
- 저자: Varun Nandakumar
- 발표 연도: 2014
- 발행 기관: The Ohio State University
- 키워드: High Integrity Die Casting, Aluminum, Magnesium, Process Design, Tool Design, Vacuum, Degassing
2. 초록:
자동차 산업의 효율 증대 및 배출가스 저감 요구는 강철 부품을 알루미늄, 마그네슘과 같은 경량 합금으로 대체할 필요성을 증대시켰다. 특히 구조용 부품에 적용하기 위해서는 기존 고압 다이캐스팅(HPDC) 공정의 고질적인 문제인 가스 혼입 문제를 해결해야 한다. 본 논문은 전통적인 HPDC 공정을 개선하여 알루미늄 및 마그네슘 합금의 고청정 주조품을 생산하는 방법을 기술하고 시험한다. 용탕 품질 개선을 위해 회전식 탈가스 장치를 사용한 실험을 수행했으며, 기존 설비에 진공 시스템을 통합하기 위한 방법을 연구하고 칠 블록을 포함한 진공 보조 시스템의 툴링을 완전히 설계했다. 칠 블록 설계는 MAGMA 및 ANSYS 시뮬레이션 툴을 사용하여 기초부터 수행되었으며, 설계 변수의 영향을 이해하기 위해 실험계획법을 완료했다. 최종적으로 최적 설계는 3D CAD 소프트웨어로 완성되고 사내에서 제작되었다.
3. 서론:
고압 다이캐스팅(HPDC)은 원자재로부터 최종 제품까지 가장 짧은 공정으로 불릴 만큼 생산성이 높은 공정이다. 특히 자동차 산업에서 경량화를 위한 알루미늄 및 마그네슘 부품 생산에 널리 사용된다. 그러나 기존 HPDC 공정은 용탕 주입 시 발생하는 가스 혼입 및 응고 수축으로 인한 기공 결함이 발생하기 쉬워, 높은 연신율과 강도를 요구하는 구조용 부품(Structural parts)에 적용하는 데 한계가 있었다. 본 연구는 이러한 한계를 극복하고 HPDC 공정으로 고청정(High Integrity) 부품을 생산하기 위한 공정 및 금형 설계 기술을 개발하는 것을 목표로 한다.
4. 연구 요약:
연구 주제의 배경:
HPDC 제품의 가장 큰 결함 원인은 기공(Porosity)이며, 이는 가스 기공과 응고 수축 기공으로 나뉜다. 가스 기공은 주로 용탕에 용해된 수소나 주입 과정에서 혼입된 공기에 의해 발생하며, 이는 부품의 열처리 가능성을 제한하고 기계적 특성을 저하시킨다.
이전 연구 현황:
기공 문제를 해결하기 위해 진공 다이캐스팅, 스퀴즈 캐스팅, 반용융 주조 등 다양한 고청정 공정이 개발되었다. 특히 진공 다이캐스팅은 금형 내 가스를 제거하여 기공을 줄이는 효과적인 방법으로, 밸브를 사용하는 방식과 칠 블록(Chill Block)과 같은 밸브리스(valve-less) 방식으로 나뉜다.
연구의 목적:
본 연구의 목적은 오하이오 주립대학교 다이캐스팅 연구실의 기존 설비를 활용하여, 고청정 알루미늄 및 마그네슘 다이캐스팅 부품을 생산할 수 있는 통합적인 프레임워크를 구축하는 것이다. 이를 위해 (1) 용탕 품질 개선 기술을 도입 및 최적화하고, (2) 진공 시스템을 적용할 수 있도록 기존 금형을 재설계하는 두 가지 세부 목표를 설정했다.
핵심 연구:
- 용탕 품질 개선: 회전식 탈가스 장치를 사용하여 알루미늄 용탕(A380 등)의 수소 가스를 제거하고, 감압 응고 시험(RPT) 및 밀도 측정을 통해 그 효과를 정량적으로 평가하여 최적의 공정 조건을 도출했다.
- 진공용 금형 설계: 밸브리스 방식의 칠 블록을 이용한 진공 시스템을 설계했다. MAGMA 유동 해석을 통해 칠 블록 입구의 경계 조건을 설정하고, ANSYS 열 해석과 실험계획법(DOE)을 통해 칠 블록의 핵심 설계 변수(재질, 갭 두께 등)를 최적화했다.
5. 연구 방법론
연구 설계:
본 연구는 실험적 접근과 시뮬레이션 기반 설계를 결합했다. 용탕 품질 개선 파트에서는 두 종류의 알루미늄 합금을 대상으로 탈가스 시간에 따른 밀도 변화를 측정하는 관찰 연구를 수행했다. 칠 블록 설계 파트에서는 3가지 인자(재질, 갭, 열전달계수)를 2수준으로 설정한 2³ 요인 실험계획법(factorial designed experiment)을 설계했다.
데이터 수집 및 분석 방법:
- 용탕 품질 평가: Palmer® 감압 응고 시험기(RPT)로 시편을 채취하고, 아르키메데스 원리를 이용해 밀도를 측정했다.
- 칠 블록 설계 검증: MAGMA 소프트웨어로 주조 유동 해석을 수행하여 초기 조건을 얻고, ANSYS 소프트웨어로 2D 열전달 과도 해석(thermal transient analysis)을 수행하여 각 설계 조건에서의 용탕 동결 시간을 계산했다. Minitab을 사용하여 분산분석(ANOVA)을 실시하고 유의미한 인자를 식별했다.
연구 주제 및 범위:
연구는 OSU의 250톤 Buhler 콜드챔버 다이캐스팅 머신을 기준으로 진행되었다. 용탕 품질 연구는 알루미늄 합금에 초점을 맞췄으며, 진공 시스템 설계는 마그네슘 합금(AZ91 물성치 사용)을 대상으로 한 시뮬레이션을 기반으로 했다.
6. 주요 결과:
주요 결과:
- 회전식 탈가스 장치를 이용해 10-15분간 용탕을 처리했을 때, 수소 가스가 효과적으로 제거되어 밀도가 크게 향상되었고, 후속 열처리 시 블리스터링이 발생하지 않았다.
- 칠 블록의 용탕 동결 성능에는 재질(구리 > H13)과 갭 두께(좁을수록 좋음)가 결정적인 영향을 미쳤다.
- 구리 재질과 0.03인치의 갭 두께를 가진 칠 블록이 최적의 설계로 결정되었다.
- 초기 개념부터 시뮬레이션, 최적화, 최종 제작에 이르는 체계적인 칠 블록 설계 프로세스를 성공적으로 수립했다.
Figure Name List:
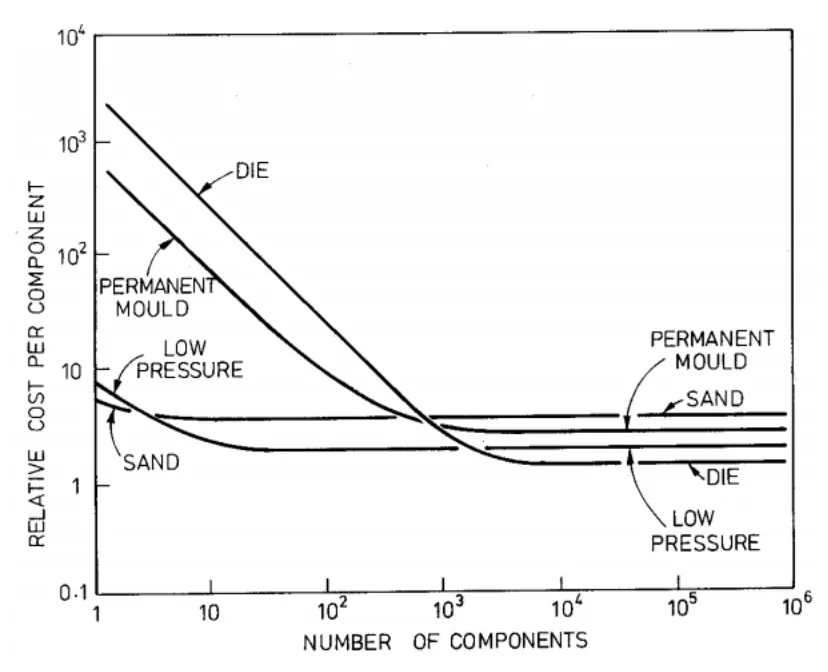
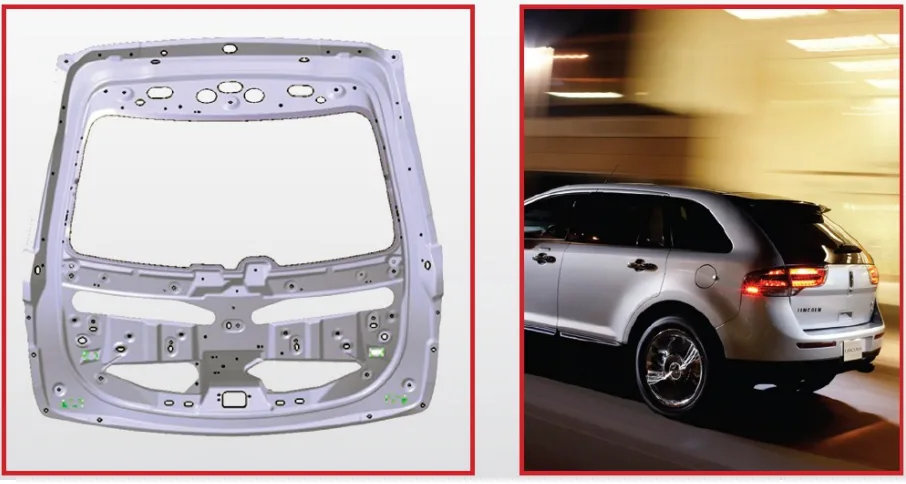
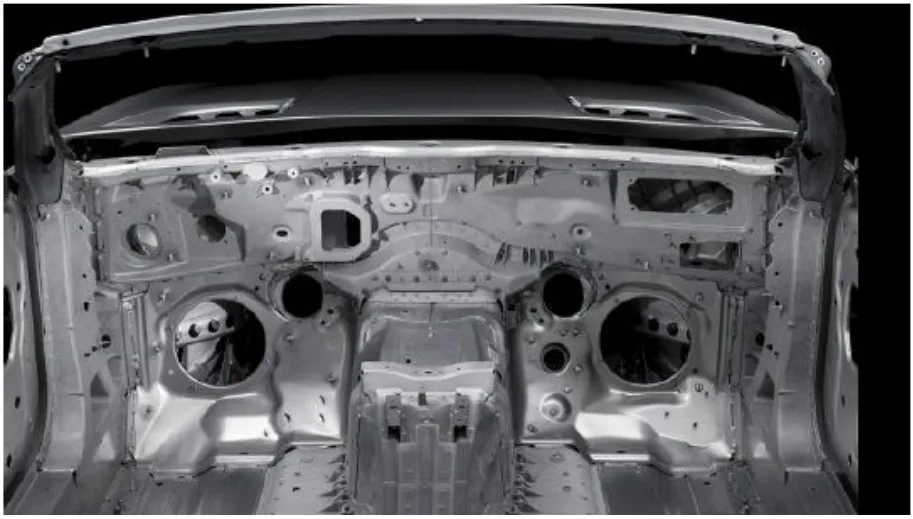
- Figure 1. Relationship of various casting processes to pressure and velocity (Anderson, 2004)
- Figure 2. Steps in a HPDC process (NADCAdesign)
- Figure 3, Advantages of High Pressure Die Casting (Twarog, 2011)
- Figure 4. Cold Chamber Process (Groover, 2007)
- Figure 5. The Hot Chamber Process (Groover, 2007)
- Figure 6, Graph howing the relative cost of a component manufactured by different casting processes (Kalpakjian, 2009)
- Figure 7, Magnesium Lincoln MKT lift gate (Die Casting Engineer, 2010)
- Figure 8, Upper Fire wall (European Aluminium Association)
- Figure 9, Audi Space frame, Showing Structural Die Castings in Red (Hartlieb, 2013)
- Figure 10, Fe rich needle like phase that causes low elongation and flow capabilities (Hartlieb, 2013)
- Figure 11, Major sources of defects in a HPDC product (Twarog, 2011)
- Figure 12, Solubility of Hydrogen drops drastically as the aluminum solidifies, not so much a problem with Magnesium (Campbell, 2011)
- Figure 13, Protection of the surface of the melt by the addition of liquid Argon
- Figure 14, Surface protection by delivery of argon gas parallel to the surface of the melt
- Figure 15, Efficiencies of three different techniques to degassing
- Figure 16, Coupling flux injection with rotor degassing (Neff, 2002)
- Figure 17, For a given size of a bubble, (a) larger oxides are easily floated out while (b) smaller ones follow the streamlines of the rising bubble and so do not collect the bubble (Campbell, 2011)
- Figure 18 Vss- Critial Slow Shot Velocities (Anderson, 2004)
- Figure 19, Illustration showing Atomized flow that is typical in a conventional HPDC (Vinarcik, 2002 )
- Figure 20, Left - Close to eutectic with a small mushy zone, Right - bigger mushy zone (NADCAdesign)
- Figure 21 Conventional Vacuum Die Casting Process (PFIEFER Vacuum, 2006)
- Figure 22, Difference time in vacuum application for Vacural vs. others (Jorstad, 2008 )
- Figure 23, Vacuural Process schematic (Jorstad, 2008 )
- Figure 24, Residual gas content a seen on X-ray (Jorstad, 2008 )
- Figure 25, Valve and Valve less technology for creating vacuum inside the die cavity
- Figure 26, Erroneous Cavity vacuum reading in case of chill blocks (Bagnoud & Bigger, 2008)
- Figure 27, Comparison between Chill Blocks and Valves, (Adapted from (Bagnoud & Bigger, 2008))
- Figure 28, 250 T Cold Chamber die casting Machine at OSU
- Figure 29, PYROTEK® STAR 300® Rotary Degasser
- Figure 30, Specially designed mounts on the furnace to receive the Rotary degasser
- Figure 31, Palmers® Reduced Pressure Tester
- Figure 33, Density measurement after degassing, yellow points indicate that degassing was done
- Figure 34, Four Heat treated samples and one as cast on the extreme right, no blistering observed
- Figure 35, Ejector and cover die with inserts
- Figure 36, Available design space on the cover die half was 4X2X.5 in
- Figure 37, Outer envelope of chill block and initial concept design
- Figure 38, ISO view and section view of entire chill block assembly showing internal trapezoidal passages and required area for venting into vacuum tank
- Figure 39, Initial geometry for chill profile with a cut away (.52X.40in) for consistent vent area
- Figure 40, MAGMA simulation Parameters
- Figure 41, Temperature and Flow lengths at an arbitrary 84% fill, Stars showing location of control points
- Figure 42, Boundary Conditions (BC1 and BC2) & Thermal loads for the 2D Model
- Figure 43, Main effect plots for the factors
- Figure 44, Chill Block design process
- Figure 45, CAD model section view showing the vent passage in the ejector die and hole on the cover die
- Figure 46, Ejector die vent cutout area
- Figure 47, Design criteria for Sealant; to determine optimal sealing.
- Figure 48, Sealant Path on the cover die
7. 결론:
본 연구는 알루미늄 및 마그네슘 합금의 고청정 다이캐스팅을 위한 통합적인 프레임워크를 성공적으로 제시했다. 용탕 품질 관리 기술과 진공 보조 시스템의 칠 블록 설계를 체계적으로 연구하고 검증했다. 특히 실험계획법과 시뮬레이션을 통해 칠 블록 설계의 핵심 인자를 규명하고 최적의 설계를 도출함으로써, 데이터 기반의 금형 설계 방법론을 확립했다. 이 연구 결과는 기존 HPDC 공정의 한계를 극복하고, 자동차 구조용 부품과 같은 고부가가치 시장으로 진출하는 데 중요한 기술적 토대를 제공한다.
8. 참고 문헌:
- [List the references exactly as cited in the paper, Do not translate and omit.]
전문가 Q&A: 자주 묻는 질문
Q1: 이 연구에서 칠 블록의 성능 개선에 가장 결정적인 요인은 무엇이었나요?
A1: 연구 결론에 따르면 칠 블록의 재질과 갭 두께가 가장 영향력 있는 요인이었습니다. 특히 열전도율이 높은 구리(Copper)를 사용하고 갭 두께를 줄이는 것이 용탕을 빠르게 동결시켜 가스 배출 효율을 높이는 데 결정적이었습니다. 이는 "Analysis of Variance" 섹션과 Table 6의 데이터로 뒷받침됩니다.
Q2: 이 연구의 접근법은 기공 문제를 다루는 전통적인 방법과 어떻게 다른가요?
A2: 논문의 Introduction
에 따르면, 전통적인 HPDC는 어느 정도의 기공을 감수하는 공정이었습니다. 반면 이 연구는 (1) 용탕 처리 단계에서 적극적으로 수소 가스를 제거하고, (2) 주입 단계에서 진공 시스템(칠 블록)으로 공기 혼입을 원천적으로 차단하는 통합적인 접근법을 도입했습니다. 이를 통해 열처리가 가능한 수준의 고청정 부품 생산 가능성을 입증했습니다.
Q3: 이 연구 결과는 모든 종류의 합금에 적용 가능한가요, 아니면 특정 합금에만 해당되나요?
A3: Experiment
섹션에 기술된 바와 같이, 탈가스 실험은 A380과 다른 알루미늄 합금을 대상으로 수행되었습니다. 칠 블록 설계를 위한 시뮬레이션은 마그네슘 합금인 AZ91의 물성치를 사용했습니다. 따라서 이 연구의 원리는 알루미늄과 마그네슘 합금에 폭넓게 적용될 수 있으나, 다른 특정 합금에 적용하기 위해서는 추가적인 검증이 필요할 수 있습니다.
Q4: 연구진이 이 결론에 도달하기 위해 사용한 구체적인 측정 또는 시뮬레이션 기법은 무엇인가요?
A4: 연구진은 용탕 품질 평가를 위해 PYROTEK® STAR 300® 회전식 탈가스 장치와 Palmer® 감압 응고 시험기를 사용했습니다. 칠 블록 설계 및 최적화를 위해서는 Research Methodology
섹션에 설명된 바와 같이 MAGMA 유동 해석, ANSYS 열 해석, 그리고 2³ 실험계획법(Designed Experiment)을 활용했습니다.
Q5: 논문에 따르면, 이 연구의 주된 한계점이나 향후 연구 분야는 무엇인가요?
A5: 저자들은 Future Work
섹션에서, 본 연구는 칠 블록 자체의 설계에 집중했으므로 향후 과제는 진공 트랩과 제어 시스템 등 나머지 진공 보조 시스템을 완성하고 실제 주조 시험을 통해 그 효과를 검증하는 것이라고 밝혔습니다. 또한 ANSYS 해석의 근사치를 MAGMA 해석으로 검증하는 것도 제안했습니다.
Q6: 이 논문이 다이캐스팅 생산 현장에 주는 직접적이고 실용적인 교훈은 무엇인가요?
A6: 핵심 교훈은 체계적인 접근을 통해 부품 품질을 크게 향상시킬 수 있다는 것입니다. 즉, 첫째, 통제된 탈가스 공정을 통해 용탕 품질을 확보하고, 둘째, 본 논문에서 검증된 칠 블록과 같은 진공 시스템을 설계하여 공기 혼입을 최소화하는 것입니다. 이는 논문 "[Process and Tool Design for the High Integrity Die Casting of Aluminum and Magnesium Alloys]"의 전반적인 결과가 강력하게 뒷받침하는 결론입니다.
결론 및 다음 단계
이 연구는 HPDC 공정에서 부품의 품질과 신뢰성을 향상시키기 위한 귀중한 로드맵을 제공합니다. 연구 결과는 결함을 줄이고 생산성을 최적화하기 위한 명확하고 데이터에 기반한 경로를 제시합니다.
CASTMAN은 최신 산업 연구를 적용하여 고객의 가장 어려운 다이캐스팅 문제를 해결하는 데 전념하고 있습니다. 이 논문에서 논의된 문제들이 귀사의 운영 목표와 관련이 있다면, 저희 엔지니어링 팀에 연락하여 이러한 고급 원리를 귀사의 부품에 어떻게 구현할 수 있는지 논의해 보십시오.
저작권
- 이 자료는 "Varun Nandakumar"의 논문 "[Process and Tool Design for the High Integrity Die Casting of Aluminum and Magnesium Alloys]"를 기반으로 합니다.
- 논문 출처: The Ohio State University
이 자료는 정보 제공 목적으로만 사용됩니다. 무단 상업적 사용을 금합니다.
Copyright © 2025 CASTMAN. All rights reserved.