본 소개 자료는 "[한국소성가공학회지]"에 게재된 "[고효율 전동기용 Cu Rotor의 반응고 성형과 공정변수 제어]" 논문을 기반으로 작성되었습니다.
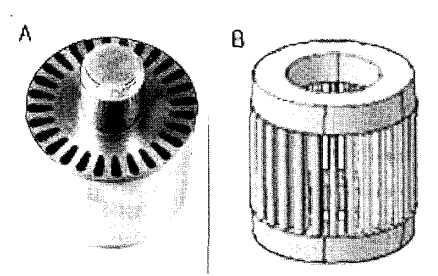
1. 개요:
- 논문 제목: 고효율 전동기용 Cu Rotor의 반응고 성형과 공정변수 제어 (Process Control and Thixoforming of Cu Rotor for High Efficiency Motors)
- 저자: 정우성, 이상용, 신평우 (W. S. Jung, S. Y. Lee, P. W. Shin)
- 발행 연도: 2005
- 게재 학술지/학회: 한국소성가공학회지 (Transactions of Materials Processing)
- 키워드: Cu Rotor, Thixoforming, Semi-solid Metal Forming, High Conductivity Copper Alloy, SIMA Process, Cu-Ca Alloy
2. 초록 (Abstract):
중소형 유도 전동기의 로터는 일반적으로 알루미늄 다이캐스팅으로 제조되어 왔다. 유도 전동기의 효율을 향상시키기 위해 새로 개발된 Cu-Ca 합금에 대한 연구가 진행되었다. 1.0wt% 미만의 Ca를 함유한 Cu 합금의 전기 전도도는 80% IACS 이상이었다. Cu-Ca 합금은 150°C 이상의 넓은 반용융 구간을 가지므로 반응고 성형 공정에 바람직하다. 본 연구에서는 기존의 알루미늄 다이캐스팅 로터를 대체하기 위해 반응고 성형 공정을 이용한 Cu-로터를 개발하였다. 반응고 성형된 로터의 미세조직 분석을 수행하였다. 불완전 충전이 유도 전동기 효율에 미치는 영향에 대해 논의하였다.
3. 서론 (Introduction):
전동기는 전기에너지를 로터의 회전에 의하여 기계적 에너지로 바꾸어 주는 장치로서 가정뿐만 아니라 산업분야에 광범위하게 사용되고 있다. 에너지 변환과정에서 전동기 종류에 따라 7~25%의 에너지 손실이 발생하므로, 전동기 효율 향상은 에너지 절약에 중요하다. 유도전동기의 효율은 로터의 전기 전도도에 크게 영향을 받는다. 현재 상업적으로 생산되는 중소형 전동기 로터는 주로 순수 알루미늄을 다이캐스팅으로 제조하는데, 이는 알루미늄의 저렴한 가격, 복잡 형상 제조 용이성, 동합금 다이캐스팅 대비 긴 금형 수명 때문이다. 그러나 알루미늄의 전기 전도도는 순동의 60% 수준이므로, 효율 향상을 위해 로터 소재를 전기 전도도가 높은 동합금으로 전환하는 것이 바람직하다. 동합금은 우수한 기계적 성질(강도, 내피로성, 내크립성)을 가져 에너지 효율, 내구성, 성능이 우수한 전동기 제조를 가능하게 한다. 하지만 동합금은 높은 융점(1083℃)으로 인해 다이캐스팅 시 금형 마모가 심하여 경제적인 금형 수명을 기대하기 어렵다[2]. 이러한 문제점을 해결할 방안으로 Al 및 Mg 합금 부품 제조에 많이 사용되는 반응고 성형법(Thixoforming)이 있다. 반응고 성형은 고액공존구역에서 성형이 이루어져 액상선보다 100℃ 이상 낮은 온도에서 성형하므로 다이캐스팅에 비해 금형 마모율이 작고 주조 결함이 적은 이점이 있다. 본 연구에서는 넓은 고액공존구간을 가지는 Cu-Ca 합금을 사용하고, SIMA 공정(Strain Induced Melt Activated)을 통해 구상화 조직을 형성한 후, 공정 변수 제어를 통해 고효율 전동기용 로터의 반응고 성형을 수행하였다. 성형된 시제품의 효율 측정을 통해 유도 전동기의 효율 상승에 대해 논의하고자 한다.
4. 연구 요약:
연구 주제의 배경:
에너지 소비 절감을 위해 고효율 전동기에 대한 요구가 증가하고 있다. 기존 유도 전동기 로터는 알루미늄 다이캐스팅으로 제작되어 알루미늄의 낮은 전기 전도도로 인해 효율이 제한된다. 구리는 우수한 전도성과 기계적 특성을 가지지만, 높은 융점으로 인한 금형 손상 문제로 전통적인 다이캐스팅 적용이 어렵다.
기존 연구 현황:
알루미늄 다이캐스팅은 로터 생산의 표준 공정이다. 반응고 성형(Thixoforming)은 Al, Mg 합금에서 공정 온도 감소 및 결함 감소를 위해 사용되는 기술이다. Cu-Ca 합금의 전기 전도도 및 반용융 특성에 대한 연구가 있었다[3]. SIMA 공정은 반응고 성형에 적합한 구상 미세조직을 얻는 방법으로 알려져 있다[4-5].
연구 목적:
본 연구는 기존의 알루미늄 다이캐스트 로터를 대체하여 유도 전동기 효율을 향상시키기 위해, Cu-Ca 합금을 이용한 반응고 성형 공정으로 구리 로터를 개발하는 것을 목표로 하였다. 연구는 반응고 성형 공정 변수 제어, 결과 미세조직 및 충전 특성 분석, 그리고 이러한 요인들이 최종 모터 효율에 미치는 영향을 평가하는 데 중점을 두었다.
핵심 연구 내용:
본 연구의 핵심 내용은 다음과 같다:
- 전기 전도도와 가공성을 고려하여 적합한 Cu-Ca 합금(Cu-0.5%Ca) 선정 (Table 1).
- 반응고 성형에 적합한 미세하고 균일한 구상 미세조직을 얻기 위해 SIMA 공정(15% 압축 변형 후 1050°C에서 재가열) 적용 (Fig 1.1, Fig 1.2).
- 800톤 프레스를 사용하여 3HP 모터 로터에 대한 반응고 성형 공정 개발 및 최적화 (빌렛 가열: 유도가열로 ~1075°C, 금형 예열: 400°C, 성형 변수 포함) (Fig 3).
- 초기 시험에서 관찰된 충전 결함(역방향 충전, 기공 등) 조사 및 완화 (Fig 4, Fig 5).
- 성형성 개선 및 결함 감소를 위한 공정 변수 제어, 특히 빌렛 가열(온도 균일성, 비대칭 가열 프로파일 - Fig 6) 및 빌렛 형상 제어 (Fig 9).
- 성형된 로터의 내부 건전성을 비파괴 검사(RT)를 통해 평가 (Fig 7).
- 반응고 성형된 Cu-로터(Fig 8)의 효율을 측정하고 표준 Al D/C 로터와 비교 (Fig 10).
5. 연구 방법론
연구 설계:
본 연구는 실험적 접근 방식을 사용하였다. 재료 선정(Cu-Ca 합금) 및 진공유도용해(VIM)와 SIMA 공정을 이용한 준비로 시작하였다. 3HP 로터 형상에 대해 가열 조건 및 빌렛 형상과 같은 공정 변수를 변경하며 반응고 성형 시험을 수행하였다. 결함 분석은 육안 검사, 단면 절단 및 현미경 관찰을 포함하였다. 내부 품질 평가를 위해 비파괴 검사(RT)를 사용하였다. 최종적으로 생산된 Cu-로터의 효율을 측정하여 기준 알루미늄 다이캐스트(Al D/C) 로터와 비교하였다.
데이터 수집 및 분석 방법:
- 재료 준비: 초기 Cu-Ca 빌렛 주조를 위한 VIM. SIMA 공정에서 예비 변형을 가하기 위한 압축 시험.
- 미세조직 제어: 예비 변형 후 열처리. 광학 현미경을 이용한 결정립 크기 측정 (Fig 1.1).
- 반응고 성형: 열전대 모니터링을 통한 빌렛의 50kW 유도 가열 (Fig 6). 성형을 위한 800톤 유압 프레스 (Fig 3).
- 결함 분석: 육안 검사, 로터 단면 절단, 충전 및 미충전 영역의 미세조직 검사를 위한 광학 현미경 관찰 (Fig 5). 내부 충전 평가를 위한 방사선 투과 검사(RT) (Fig 7).
- 성능 측정: 합금의 전기 전도도 측정 (Table 1, Fig 1.2). 최종 로터 시제품의 모터 효율 시험 (Fig 10).
연구 주제 및 범위:
본 연구는 유도 전동기 로터 생산을 위한 Cu-Ca 합금, 특히 Cu-0.5%Ca의 반응고 성형성에 초점을 맞췄다. 적합한 반용융 미세조직을 얻기 위한 SIMA 공정 적용을 조사하였다. 범위는 특정 3HP 로터 설계(Fig 2)에 대한 반응고 성형 파라미터(가열 온도, 가열 프로파일, 빌렛 형상) 최적화를 포함하였다. 연구는 일반적인 충전 결함(Fig 4)과 공정 변수 및 미세조직과의 관계(Fig 5)를 분석하였다. 궁극적인 범위는 기존 Al D/C 로터에 비해 반응고 성형을 통해 더 높은 효율의 Cu-로터를 생산할 수 있음을 입증하는 것이었다.
6. 주요 결과:
주요 결과:
- Ca 함량이 1.0wt% 미만인 Cu-Ca 합금은 80% IACS 이상의 전기 전도도를 보였으며, Ca 함량이 낮을수록 전도도가 높았다 (Table 1). 연구에는 Cu-0.5%Ca (95.1% IACS)가 선정되었다.
- 15% 이상의 압축 변형 후 열처리(1050°C에서 4분)를 포함하는 SIMA 공정은 Cu-0.5%Ca 합금에서 반응고 성형에 적합한 미세하고 균일한 구상 미세조직을 성공적으로 생성했다 (Fig 1.1). 이 처리 후 전기 전도도는 약 0.5%Ca 조성에서 최적이었다 (Fig 1.2).
- 초기 반응고 성형 시험에서는 주로 역방향 충전(back-filling)과 기공(porosity)과 같은 충전 결함이 발생했으며, 이는 슬러리와 코어 어셈블리 간의 온도 차이, 유동 저항, 그리고 잠재적으로 갇힌 공기로 인한 조기 응고에 기인한 것으로 분석되었다 (Fig 4).
- 미세조직 분석 결과, 충전 중 액상/고상 분리가 관찰되었으나(슬롯 상부에서 액상이 더 많이 관찰됨), 이것이 충전 결함의 주된 원인은 아닌 것으로 간주되었다 (Fig 5).
- 빌렛 가열 온도(경험적으로 약 1075°C로 결정) 및 프로파일(상부를 더 뜨겁게 유지하기 위한 비대칭 가열 사용, Fig 6)을 포함한 공정 변수 제어를 통해 성형성이 개선되고 충전 결함이 감소하였다.
- 빌렛 형상을 단순한 원통형(Fig 9A)에서 로터 축에 맞는 홈이 있는 형상(Fig 9B)으로 수정하자 슬롯으로의 재료 유동이 개선되어 더 나은 충전(NDT로 확인, Fig 7, Fig 8)과 더 높은 효율을 보였다.
- 비교 효율 시험 결과, 반응고 성형된 Cu-Ca 로터는 표준 알루미늄 다이캐스트(Al D/C) 로터보다 1% 이상 높은 효율을 달성했다 (Fig 10).
그림 제목 목록:
- Fig. 1.1 Grain size of Cu-Ca alloy specimens compressed to various deformation levels at room temperature followed by heat treatment at 1050 °C for 4 minutes
- Fig. 1.2 Electrical conductivity of Cu-Ca alloy specimens compressed to various deformation levels at room temperature followed by heat treatment at 1050℃ for 4 minutes
- Fig. 2 Rotor core assembly (A) and squirrel cage (B)
- Fig. 3 Die for Cu-rotor thixoforming and thixoformed Cu-Rotor
- Fig. 4 Filling defects of thixoformed Cu-rotor (A) upper end ring (B) lower end ring
- Fig. 5 Microstructures of as-thixoformed Cu-rotor slot at the various positions
- Fig. 6 Heating curves measured at (#1) 5 mm (#2) 20 mm, apart from surface
- Fig. 7 Results of non-destructive testing
- Fig. 8 Thixoformed Cu-rotor for efficiency test
- Fig. 9 Billet shape (A) cylinder type (B) modified type
- Fig. 10 Thixoformed Cu-rotor efficiency
7. 결론 (Conclusion):
고효율 전동기용 Cu-Ca 합금의 반응고 성형 및 효율 측정 결과를 바탕으로 다음과 같은 결론을 얻었다.
(1) SIMA 공정을 통해 전기 전도도 면에서 더 나은 낮은 Ca 함량의 합금을 Ca 함량이 높은 합금과 비슷한 결정립 크기를 가진 구상 입자로 만들 수 있었다.
(2) 미충전 슬롯이 효율 저하의 가장 큰 원인이었으며, 가열 조건 및 성형의 공정 변수 제어로 성형성을 개선하고 충전 결함을 줄일 수 있었다.
(3) 개량한 빌렛이 더 높은 효율의 결과를 보였으며, 이는 설계의 개선(빌렛 또는 코어 어셈블리 형상 등)을 통해 더 나은 성형성과 높은 효율을 얻을 수 있음을 시사한다.
(4) Al D/C rotor와 효율 동시 비교 측정에서 Cu-rotor의 효율이 1% 이상 높게 측정되었다.
8. 참고문헌 (References):
- [1] D. H. Kang, H. D. Ha, K. C. Chang, D. H. Goo, et al, 1998, Planning of long-term technology for the development of high efficiency motors, Report for the Ministry of Commerce, Republic of Korea, p. 250.
- [2] R. G. R. Sellors, J. G. Heyes, 1979, Engineering, Vol. 219, No.11, pp. 1434~1437.
- [3] E. Y. Lee, B. M. Kang, S. Y Lee, 2003, J. of the Korean Society for Heat Treatment, Vol. 16, No. 5, pp. 267~274.
- [4] S. Kleiner, O. Beffort, M. Fuchs, P. J. Uggowitzer, 2003, Advanced Semi-solid Processing of Alloys and Composites, Proceedings of the 7th S2P, pp. 257~262.
- [5] Lee Sang-Yong, Lee Jung-Hwan, Lee Young-Sun, 2001, Journal of Materials Processing Technology, 4845, 1-6.
- [6] Keun Yong Sohn, Dong Woo Seo, and Sang Yong Lee, 2003, AMPT, pp. 1497~1500.
- [7] 윤성원, 서판기, 강충길, 2003, 고액공존재료의 변형거동에서 재료의 크기가 액상편석에 미치는 영향, 한국소성가공학회지, 제12권 제2호, pp. 94~101.
- [8] J. C. Lee, H. K. Seok, H. I Lee, 2003, Effect of the Gate Geometry and the Injection Speed on the Flow Behaviors of a Semi-Solid A356 Al Alloy, Metals and Materials Int., Vol.9, No. 4, pp. 351~357.
9. 저작권 (Copyright):
- 본 자료는 "정우성, 이상용, 신평우" 저자의 논문입니다. "[고효율 전동기용 Cu Rotor의 반응고 성형과 공정변수 제어]" 논문을 기반으로 합니다.
- 논문 출처: [원 논문에 DOI URL이 제공되지 않음]
본 자료는 상기 논문을 바탕으로 요약되었으며, 상업적 목적의 무단 사용을 금지합니다.
Copyright © 2025 CASTMAN. All rights reserved.