본 소개 자료는 International Scientific Journal에서 발행한 "Temperature field and failure analysis of die-casting die" 논문의 연구 내용입니다.
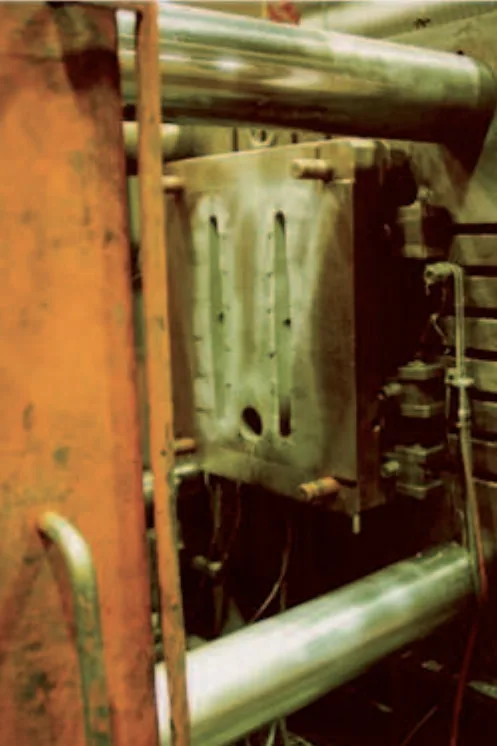
1. 개요:
- 제목: Temperature field and failure analysis of die-casting die (다이캐스팅 금형의 온도장 및 파손 분석)
- 저자: B. Kosec, G. Kosec, M. Soković
- 출판 연도: 2007
- 게재 저널/학회: Archives of Materials Science and Engineering, Volume 28, Issue 3, Pages 182-187.
- 키워드: Casting; Aluminium alloys; Die-casting die; Temperature field; Failure analysis (주조; 알루미늄 합금; 다이캐스팅 금형; 온도장; 파손 분석)
2. 초록
알루미늄 합금 다이캐스팅용 금형은 다양하고 동시에 작용하는 많은 요인으로 인해 파손됩니다. 그중 일부는 다이캐스팅 전문가에 의해 어느 정도 제어될 수 있습니다. 다이캐스팅 공정에서 주요 하중 원인은 온도의 주기적인 변화이며, 다른 하중의 영향은 상대적으로 미미합니다. 알루미늄 및 알루미늄 합금 다이캐스팅의 경제적인 생산을 위해서는 금형의 수명이 긴 것이 중요합니다.
3. 연구 배경:
연구 주제 배경:
다이캐스팅은 복잡하고 정밀한 알루미늄 제품을 대량으로 생산하는 비용 효율적인 방법입니다 [1]. 알루미늄 합금 다이캐스팅 제품은 자동차, 가전 제품, 전기 응용 분야 등 다양한 산업에서 사용됩니다 [2]. 전 세계 알루미늄 합금 주물의 약 절반이 다이캐스팅을 사용하여 만들어집니다 [3].
선행 연구 현황:
알루미늄 다이캐스팅 금형은 제조 중에 발생하는 응력과 작동 중에 발생하는 응력을 포함한 다양한 응력으로 인해 파손됩니다 [4]. 일반적인 파손에는 열 균열, 큰 균열, 모서리/날카로운 반경에서의 균열, 마모 또는 침식으로 인한 균열이 포함됩니다 [1]. 열 응력 피로로 인한 열 균열은 금형 파손의 주요 원인입니다 [8-11].
연구 필요성:
금형 교체는 비용과 시간이 많이 소요됩니다 [5-7]. 따라서 금형 파손에 기여하는 요인을 이해하는 것은 금형 수명을 연장하고 알루미늄 합금 다이캐스팅의 경제성을 개선하는 데 중요합니다.
4. 연구 목적 및 연구 질문:
연구 목적:
알루미늄 합금 다이캐스팅용 시험 금형의 작업 표면에서 발생하는 파손을 조사합니다.
핵심 연구:
- 비파괴 검사 방법을 사용하여 파손을 관찰합니다.
- 금형 예열 과정 동안 온도장과 균질성을 분석합니다.
- 온도 분포, 예열 절차 및 균열 형성 간의 관계를 식별합니다.
5. 연구 방법
이 연구의 실험 부분은 알루미늄 합금 다이캐스팅용 시험 금형의 고정된 절반의 작업 표면에서 파손을 관찰하는 것을 포함했습니다. 다음과 같은 비파괴 검사 방법이 사용되었습니다.
- 열화상 분석: 예열 중 금형 표면의 온도 분포와 균질성을 측정합니다.
- 침투제: 표면 균열을 드러내고 식별합니다.
- 고분자 복제물의 금속 조직 검사: 광학 현미경(OM)과 주사 전자 현미경(SEM)을 사용하여 미세 구조와 균열 특성을 검사합니다.
시험 다이캐스팅 금형은 그림 1에 나와 있습니다. 금형은 BOEHLER W300 ISODISC 고온 작업 공구강으로 제작되었습니다 [13]. 강철의 화학 조성은 표 2에 나와 있습니다.
6. 주요 연구 결과:
주요 연구 결과 및 제시된 데이터 분석:
- 다이캐스팅 공정에서 주요 하중 원인은 온도의 주기적인 변화입니다.
- 열화상 측정(그림 4 및 5) 결과 예열 과정 동안 필요한 온도와 온도장의 균질성이 달성되지 않은 것으로 나타났습니다.
- 금형 작업 표면에서 균열과 구덩이가 관찰되었으며(그림 6 및 7), 이는 식별 표시와 모서리/날카로운 가장자리에서 시작된 열 균열로 인한 것입니다.
- 금형의 실제 예열 시간이 불충분했습니다.
- 가열 오일의 유량을 증가시켜야 했습니다.
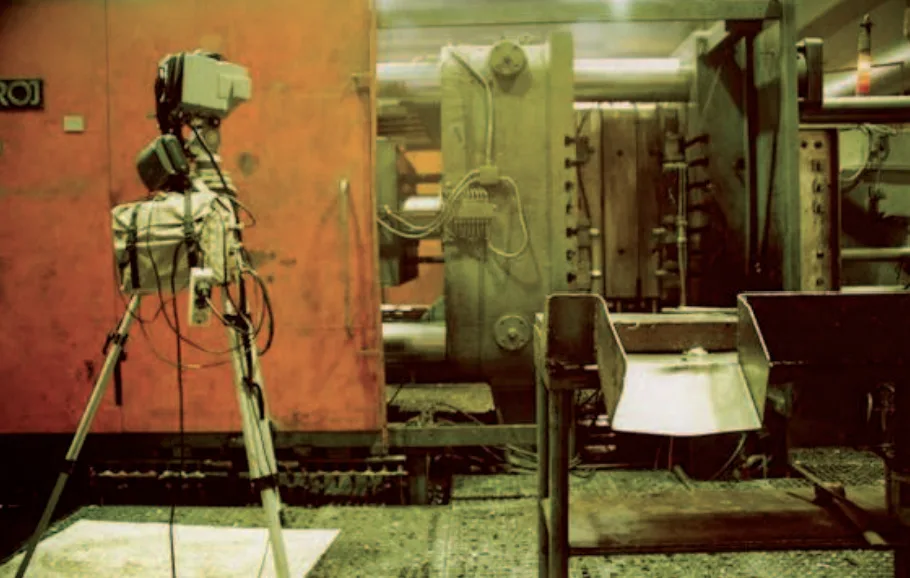
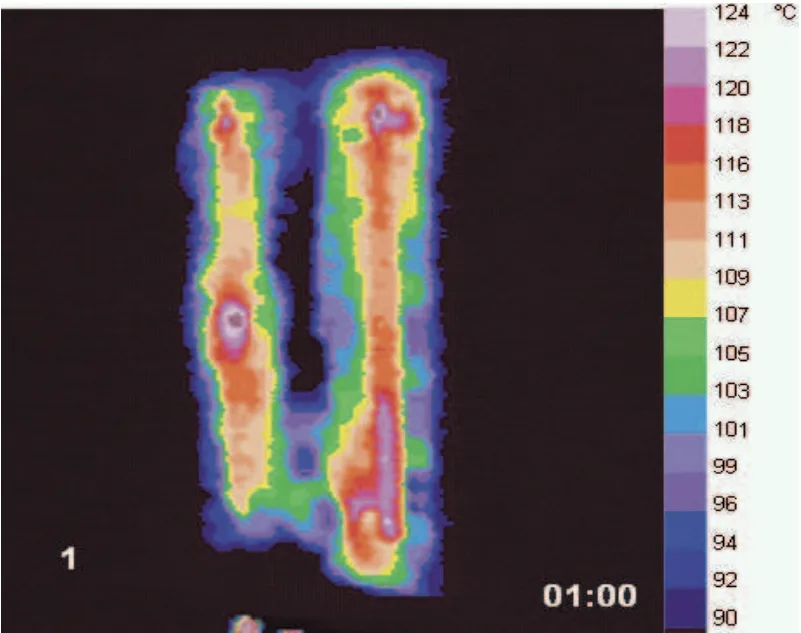
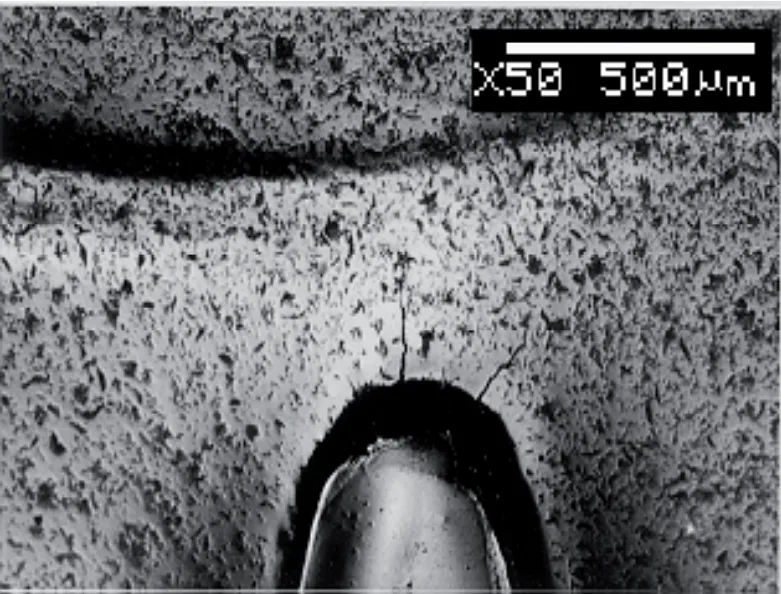
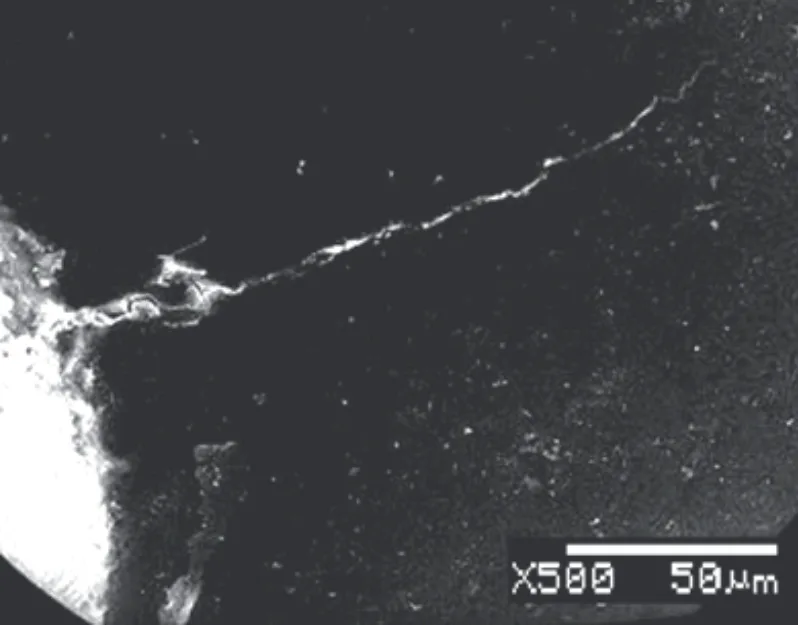
그림 이름 목록:
- Fig. 1. Fixed half of the testing die-casting die (시험 다이캐스팅 금형의 고정된 절반)
- Fig. 2. Hot dies produce more (고온 금형은 더 많은 생산량을 제공)
- Fig. 3. Position of the thermographic camera and the die-casting machine (열화상 카메라와 다이캐스팅 기계의 위치)
- Fig. 4. Working surface of the fixed part of testing die-casting die (see Figure 1, Table 3). Preheating process. Thermographs. (시험 다이캐스팅 금형의 고정된 부분의 작업 표면(그림 1, 표 3 참조). 예열 과정. 열화상.)
- Fig. 5. Working surface of the fixed part of testing die-casting die. At the beginning of preheating process (시험 다이캐스팅 금형의 고정된 부분의 작업 표면. 예열 과정 시작 시)
- Fig. 6. Working surface of the testing die-casting die. Surface pits and cracks at identification mark. OM (시험 다이캐스팅 금형의 작업 표면. 식별 표시에 있는 표면 구덩이와 균열. OM)
- Fig. 7. Working surface of the testing die-casting die. Surface crack and pits. SEM (시험 다이캐스팅 금형의 작업 표면. 표면 균열과 구덩이. SEM)
7. 결론:
주요 결과 요약:
알루미늄 합금용 다이캐스팅 금형의 균열은 여러 요인에 의해 발생하며, 그중 일부는 전문가가 제어할 수 있습니다. 금형 설계, 재료 선택, 열 응력 피로 외에도 금형의 불균일하고 낮은 초기 온도가 균열 형성에 기여합니다. 관찰된 금형 파손은 열 균열과 응력 집중 영역에서의 균열로 분류되었습니다.
제시된 열화상은 가열 방법과 금형 설계를 수정하지 않고는 필요한 온도와 온도장 균질성을 달성하는 것이 불가능함을 보여줍니다. 주요 하중 원인은 주기적인 온도 변화이며, 다른 하중의 영향은 미미합니다. 따라서 초기 해결책은 가열 및/또는 냉각 채널의 위치를 조정하여 금형의 작업 표면에 더 가깝게 이동시키는 것을 포함해야 합니다.
8. 참고 문헌:
- [1] S. Kalpakjian, Tool and die failures - source book, ASM International, Metals Park, Ohio, 1982.
- [2] B. Kosec, M. Sokovic, Failures on the working surface of aluminium die-casting die, Masinstvo 6 1 (2002) 23-28.
- [3] R.N. Lumby, R.G. O'Donnel, D.R. Gunasegaram, M. Girard, New Heat Treatment for Al high pressure die- castings, Heat Treating Progress 6 (2006) 31-37.
- [4] S.S. Manson, Thermal stress and low-cycle fatigue, McGraw - Hill, New York, 1996.
- [5] L.A. Dobrzański, Technical and economical issues of materials selection, Silesian University of Technology, Gliwice, 1997.
- [6] L.A. Dobrzański, Synergic effects of the scientific cooperation in the field of materials and manufacturing engineering, Journal of Achievements in Materials and Manufacturing Engineering 15 (2006) 9-20.
- [7] L.A. Dobrzański, Significance of materials science for the future development of societies, Journal of Materials Processing Technology 173 (2006) 133-148.
- [8] B. Smoljan, An analysis of combined cyclic heat treatment performance, Journal of Materials Processing Technology 155 (2004) 1704 -1707.
- [9] J.V. Tuma, J. Kranjc, The tempeature distribution in the superheater tube, forschung in ingenieurwessen Engineering Research 66 (2001) 153-156.
- [10] L. Gusel, I. Anzel, M. Brezocnik, Effect of lubrication on the stress distribution in an extruded material, International Journal of Advanced Manufacturing Technologies 25 (2005) 288-291.
- [11] L. Kosec, F. Kosel, Heat checking of hot work tools, Mechanical Engineering Journal 29 (1983) 151-158.
- [12] Handbook of case histories in failure analysis, Volume 1, ASM International, Materials Park, Ohio, 1992.
- [13] Böhler Edelstahlhandbuch auf PC V2.0, Kapfenberg, 1996.
- [14] M. Gojic, L. Lazic, B. Kosec, M. Bizjak, Application of mathematical modelling to hardenability testing of low alloyed Mn-Mo steel, Strojarstvo 47 (2005) 101-108.
- [15] L. Kosec, Tool steels from powders, IRT3000 1 (2006) 78-84 (in Slovene).
- [16] J.V. Tuma, Properties and fracture of structural steels with yield stress 373-737 MPa in ambient to nil ductility temperature, Journal of Materials Processing Technology, 121 (2002) 323-331.
- [17] L.A. Dobrzanski, M. Krupinski, J.H. Sokolowski, Computer aided classification of flows occured during casting of aluminium, Journal of Materials Processing Technology 167 (2005) 456-462.
- [18] L.A. Dobrzanski, M. Krupinski, P. Zarychta, R. Maniara, Analysis of influence of chemical composition of Al-Si-Cu casting alloy on formation of casting deffects, Journal of Achievements in Materials and Manufacturing Engineering 20 (2007) 475-478.
- [19] S. Kumar, R. Singh, A Knowledge - based system of progressive die components, Journal of Achievements in Materials and Manufacturing Engineering 21 (2007) 53-56.
- [20] B. Kosec, G. Kosec, Temperature field analysis on active working surface of the die-casting die, Metall 57 (2003) 134-136.
- [21] L. Masalski, K. Eckersdorf, J. McGhee, Temperature measurement, John Wiley & Sons, Chichester, 1991.
- [22] H. Haferkamp, F.W. Bach, M. Niemeyer, R. Veits, Thermogram Characteristics for process monitoring of permanent mould casting, Aluminium 75 (1999) 945-953.
- [23] B. Kosec, G. Kosec, M. Sokovic, Case of temperature field and failure analysis of die-casting die, Journal of Achievements in Materials and Manufacturing Engineering 20 (2007) 471-474.
- [24] B. Kosec, J. Kopac, L. Kosec, Analysis of casting die failures, Engineering Failure Analysis 8 (2001) 355 – 359.
- [25] B. Kosec, M. Sokovic, G. Kosec, Failure analysis of dies for aluminium alloys die-casting, Journal of Achievements in Materials and Manufacturing Engineering 13 (2005) 339-342.
9. 저작권:
- 본 자료는 "B. Kosec, G. Kosec, M. Soković"의 "Temperature field and failure analysis of die-casting die" 논문을 기반으로 합니다.
- 논문 출처: [DOI는 원본 문서에 제공되지 않음]
본 자료는 위 논문을 소개하기 위해 제작되었으며, 상업적 목적으로 무단 사용하는 것을 금합니다. Copyright © 2025 CASTMAN. All rights reserved.