본 기사에서는 [International Journal of Metalcasting]에서 발행한 논문 ["INFLUENCE OF INJECTION PARAMETERS ON THE POROSITY AND TENSILE PROPERTIES OF HIGH-PRESSURE DIE CAST AI-SI ALLOYS: A REVIEW"]를 소개합니다.
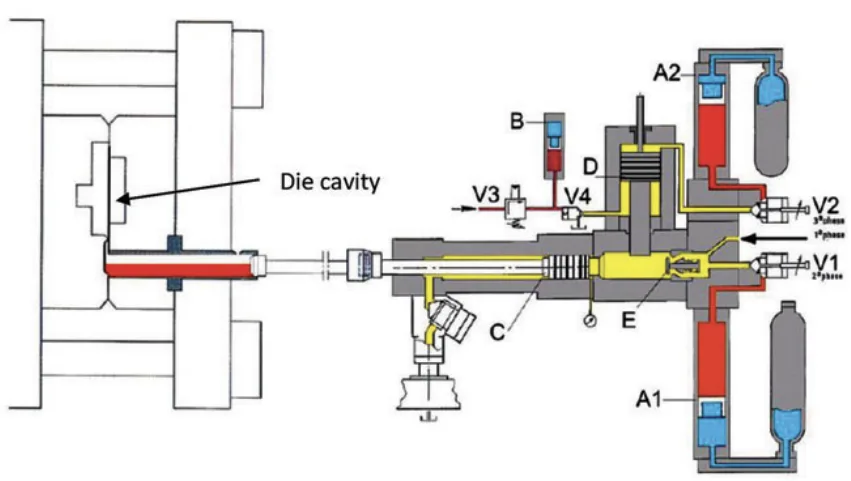
1. Overview:
- 제목: INFLUENCE OF INJECTION PARAMETERS ON THE POROSITY AND TENSILE PROPERTIES OF HIGH-PRESSURE DIE CAST AI-SI ALLOYS: A REVIEW
- 저자: Anilchandra R. Adamane, Lars Arnberg, Elena Fiorese, Giulio Timelli, Franco Bonollo
- 발행년도: 2015년
- 출판 저널/학회: International Journal of Metalcasting/Volume 9, Issue 1, 2015
- 키워드: foundry aluminum alloys, high-pressure die casting, injection parameters, porosity, tensile properties, HPDC
2. 초록 또는 서론
알루미늄-실리콘 합금은 Al 주조 합금으로 광범위하게 사용되며 자동차 부품의 고압 다이캐스팅(HPDC)에 널리 활용됩니다. 건전하고 신뢰성 있는 주조품을 얻기 위해서는 HPDC 공정 중 여러 공정 변수를 제어해야 합니다. 다양한 공정 변수 중에서도 게이트 속도 및 증압(intensification pressure, IP)과 같은 사출 변수의 결정 및 제어는 HPDC 공정 전반에 걸쳐 핵심 요구 사항으로 남아 있습니다. 본 연구에서는 사출 변수가 다이캐스팅의 기공률 및 인장 특성에 미치는 영향을 비판적으로 검토합니다. 문헌 검토 결과를 요약하고 게이트 속도 및 IP에 대한 최적 값을 제시합니다.
3. 연구 배경:
연구 주제 배경:
고압 다이캐스팅(HPDC)은 높은 치수 정확도로 대량의 주조품을 생산하는 데 비용 효율적인 방법으로 강조됩니다. HPDC의 주요 과제는 다이캐비티 충전 중 난류 금속 흐름으로 인해 가스와 산화물이 혼입되어 기공률이 증가하고 주조 품질이 저하되는 것입니다. 콜드 챔버 HPDC의 사출 공정은 유압 피스톤-실린더 시스템을 사용하여 용융 금속을 다이캐비티로 주입하는 것을 포함합니다. 밸브와 가스 어큐뮬레이터를 통해 플런저 움직임을 정밀하게 제어할 수 있습니다.
기존 연구 현황:
Al-Si 합금의 HPDC에 대한 기존 문헌은 주로 미세 구조 및 인장 거동에 영향을 미치는 주조 변수, 특히 사출 단계 변수에 초점을 맞추고 있습니다. 게이트 속도와 증압은 주요 사출 변수로 확인되었습니다. 벤트 및 오버플로우 설계는 주조 품질에 매우 중요하지만, 벤트 설계를 기공률 분포 또는 인장 특성과 직접적으로 연결하는 연구는 제한적입니다. 많은 매개변수가 상호 연관되어 있으며 수치 시뮬레이션 소프트웨어를 사용하여 최적화할 수 있습니다.
연구의 필요성:
HPDC Al-Si 합금 주조품의 품질을 향상시키려면 사출 변수를 이해하고 최적화하는 것이 중요합니다. 사출 변수가 기공률 및 인장 특성에 미치는 영향에 대한 포괄적인 검토는 공정 최적화를 안내하고 주조 신뢰성을 개선하는 데 필요합니다.
4. 연구 목적 및 연구 질문:
연구 목적:
주요 연구 목적은 기존 문헌을 기반으로 고압 다이캐스트 Al-Si 합금의 기공률 및 인장 특성에 대한 사출 변수, 특히 게이트 속도 및 증압의 영향을 비판적으로 검토하고 요약하는 것입니다.
주요 연구 질문:
- HPDC Al-Si 합금의 기공률 및 인장 강도에 대한 게이트 속도의 영향을 분석합니다.
- HPDC Al-Si 합금의 기공률 및 인장 강도에 대한 증압의 영향을 조사합니다.
- HPDC에서 용융 금속 흐름 및 주조 품질에 대한 러너 및 게이트 설계의 영향을 검토합니다.
- 문헌을 기반으로 게이트 속도 및 증압에 대한 최적 범위를 식별합니다.
연구 가설:
논문의 내용을 바탕으로 다음과 같은 가설이 암묵적으로 설정됩니다.
- 최적점까지 게이트 속도가 증가하면 HPDC Al-Si 합금의 기공률이 감소하고 인장 특성이 향상됩니다.
- 증압이 증가하면 HPDC Al-Si 합금의 기공률이 감소하고 인장 특성이 향상됩니다.
- 러너 및 게이트 설계는 용융 금속 흐름 패턴에 상당한 영향을 미쳐 기공률 분포 및 주조 품질에 영향을 미칩니다.
5. 연구 방법론
연구 설계:
본 연구는 문헌 검토 설계를 채택합니다. 사출 변수가 고압 다이캐스트 Al-Si 합금의 특성에 미치는 영향과 관련된 기존 연구 논문, 기술 기사 및 산업 출판물의 결과를 체계적으로 조사하고 종합합니다.
자료 수집 방법:
자료 수집 방법은 HPDC 및 사출 변수와 관련된 실험 연구, 수치 시뮬레이션 및 산업 관행에 초점을 맞춘 출판된 문헌에서 정보를 수집하는 것을 포함합니다. 출처는 다이캐스팅 및 야금 분야의 학술 저널, 학회 회의록, 기술 보고서 및 핸드북을 포함합니다.
분석 방법:
분석 방법은 질적이며 수집된 문헌에 대한 비판적 검토 및 종합을 포함합니다. 저자는 다양한 연구 결과에서 추세, 모순 및 게이트 속도, 증압 및 러너/게이트 설계가 기공률 및 인장 특성에 미치는 영향에 대한 합의를 식별하기 위해 분석하고 비교합니다. 검토는 현재 지식 상태를 요약하고 분석된 문헌을 기반으로 최적의 매개변수 범위를 제안하는 것을 목표로 합니다.
연구 대상 및 범위:
본 연구는 알루미늄-실리콘(Al-Si) 합금의 고압 다이캐스팅(HPDC)에 초점을 맞춥니다. 범위는 사출 변수, 특히 게이트 속도 및 증압, 그리고 이러한 합금의 기공률 및 인장 특성에 대한 러너/게이트 설계의 영향으로 제한됩니다. 검토는 이 특정 영역 내에서 실험 결과, 시뮬레이션 연구 및 실제 적용에 대해 논의하는 문헌을 포함합니다.
6. 주요 연구 결과:
주요 연구 결과:
- 게이트 속도 효과:
- 게이트 속도를 높이면 일반적으로 캐비티 충전 시간이 단축됩니다.
- 기공률을 최소화하는 최적의 게이트 속도가 존재합니다. 과도하게 낮거나 높은 속도는 모두 기공률을 증가시킬 수 있습니다.
- 게이트 속도가 높을수록 인장 강도와 연성이 향상되고 강도 값의 편차가 감소하는 경향이 있습니다.
- 작은 기공(< 20µm)의 비율은 게이트 속도에 따라 증가하는 반면, 큰 기공(> 100µm)은 더 높은 속도에서 제거될 수 있습니다.
- 증압(IP) 효과:
- 높은 IP는 기공률을 크게 줄이고 주조 밀도를 향상시킵니다.
- 기공률을 최소화하려면 적절한 게이트 두께와 IP를 결합하는 것이 중요합니다.
- 높은 IP는 게이트 근처의 미세 구조에 전단 밴드를 유발할 수 있습니다.
- 높은 IP는 기공률 제어에 용융 금속 속도보다 더 효과적입니다.
- 러너 및 게이트 설계:
- 러너-게이트 시스템 설계는 용융 금속 흐름 및 주조 품질을 제어하는 데 매우 중요합니다.
- 다양한 러너-게이트 유형(선형, 팬형, T자형, 분할형)은 다이캐비티 충전 패턴 및 기공률 분포에 영향을 미칩니다.
- 팬형 게이트는 다이캐비티 벽을 따라 더 높은 속도와 특정 영역에서 가스 혼입을 유발할 수 있습니다.
- 접선형 게이트 공급 시스템은 균일한 충전 및 난류 감소에 더 효율적일 수 있습니다.
제시된 데이터 분석:
- 기공률 대 게이트 속도 (Figure 5): Figure 5는 다양한 게이트 속도에 따른 기공률 변화를 보여줍니다. Gunasegaram et al. [17] 및 Ghomashchi [19]의 데이터는 기공률이 초기에는 게이트 속도 증가에 따라 감소하지만 매우 높은 속도에서는 정체되거나 약간 증가할 수 있음을 나타냅니다. 이는 기공률을 최소화하는 최적의 게이트 속도 범위가 있음을 시사합니다.
- 인장 특성 대 게이트 속도 (Figure 6 & 7): Figure 6과 7은 게이트 속도 증가에 따른 인장 강도 및 연성 향상을 보여줍니다. Figure 6은 다양한 게이트 속도에서 인장 시험 곡선을 보여주며, 더 높은 속도에서 더 높은 강도와 연신율을 나타냅니다. Figure 7은 여러 연구의 데이터를 요약하여 게이트 속도가 증가함에 따라 인장 특성이 일관되게 향상됨을 보여줍니다.
- 밀도 대 증압 (Figure 10 & 11): Figure 10은 밀도가 증압 증가에 따라 증가함을 보여줍니다. 다른 곡선은 다양한 사출 플런저 속도를 나타내며, 더 높은 IP가 일관되게 더 높은 밀도를 유도함을 보여줍니다. Figure 11은 "최악" 및 "최고" 밀도 조건에서 생산된 주조품을 시각적으로 비교하여 더 높은 밀도(더 높은 IP로 달성)에서 가시적인 기공률이 감소함을 강조합니다.
- 게이트 응고 시간 (Figure 12): Figure 12는 증압 및 게이트 속도가 게이트 응고 시간에 미치는 영향을 보여줍니다. IP를 증가시키면 게이트 응고 시간이 증가하는 반면, 게이트 속도를 증가시키면 초기에는 감소했다가 정체됩니다. 이는 IP가 게이트 응고 시간을 연장하는 데 게이트 속도보다 더 효과적임을 나타냅니다.
Figure 목록:
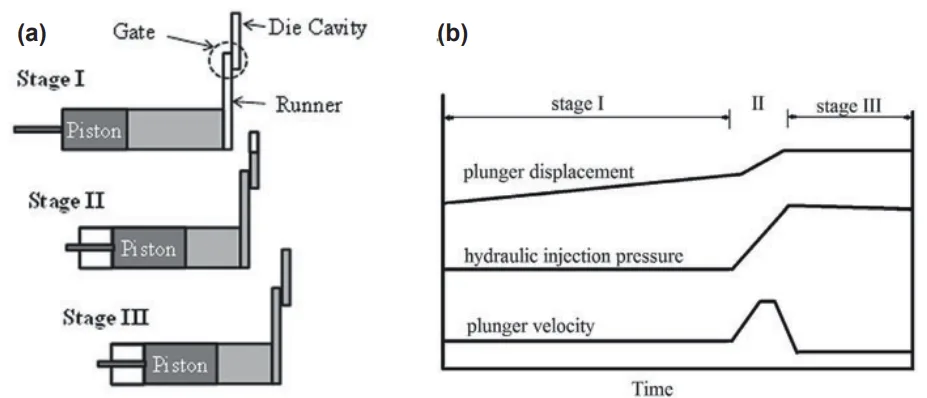
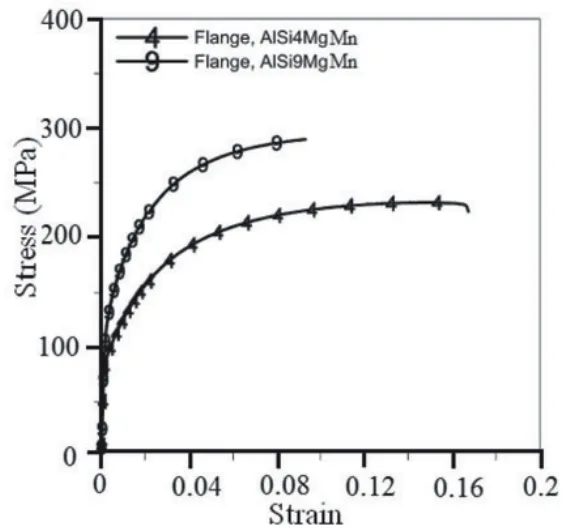

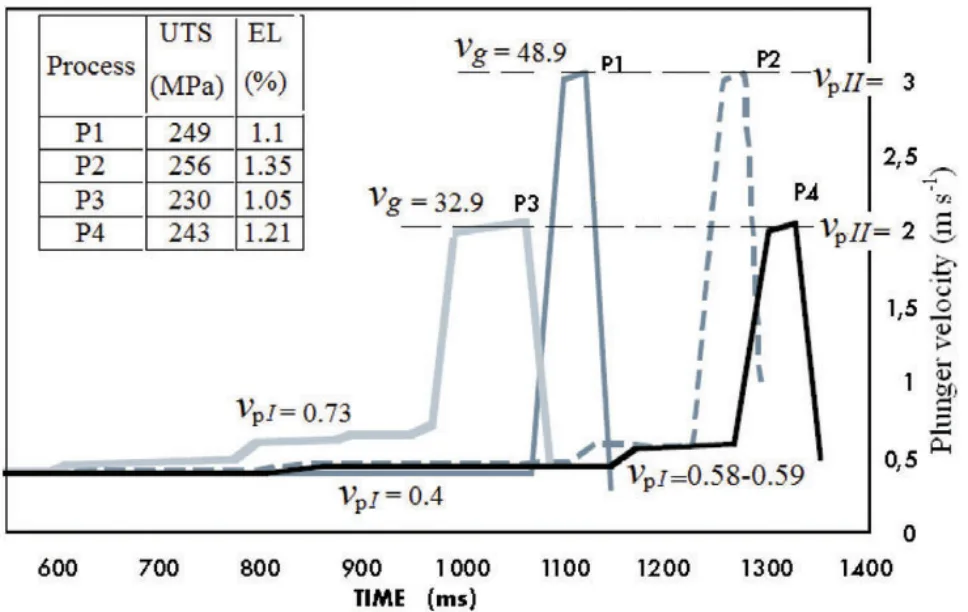
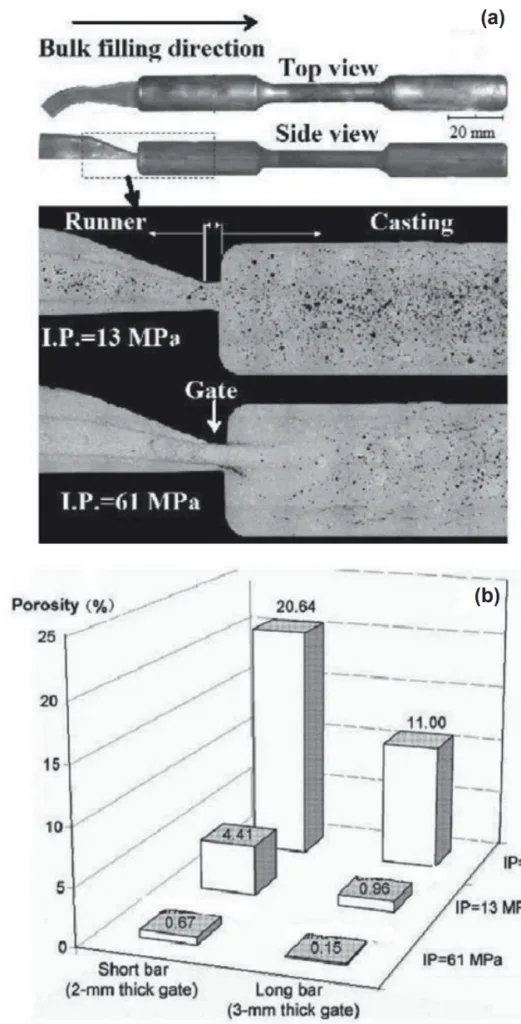

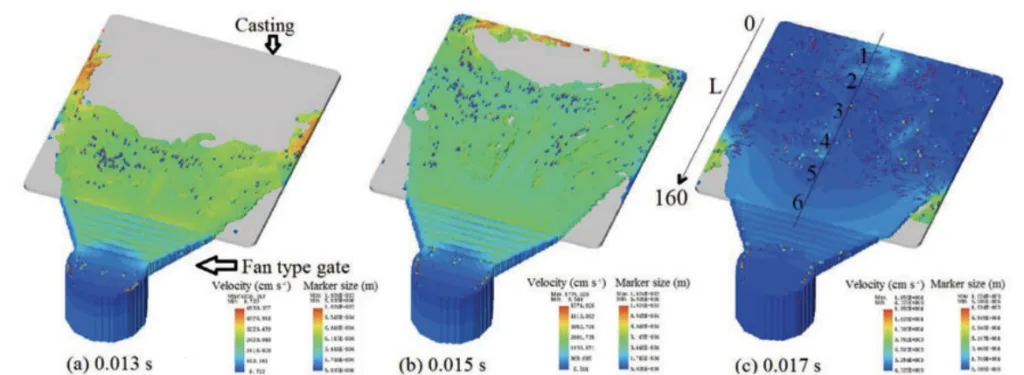
- Figure 1. Schematic illustration of hydraulic injection system.¹
- Figure 2 (a) Schematic representation of the plunger movement during HPDC and (b) the corresponding change in velocity and pressure at different stages.
- Figure 3. Engineering stress-strain curves of high pressure die-cast AlSi4MgMn and AlSi9MgMn alloys.³
- Figure 4. Tensile stress-strain curves of three different AlSi9Cu3(Fe) castings with density values indicated within the parentheses (g cm³).⁴ Lower density castings show reduced strength properties owing to higher casting defects.
- Figure 5. Change of porosity content with different gate velocity in HPDC.
- Figure 6. Tensile test curves of specimens cast with three different gate velocities: porosity content (%) are also indicated in the brackets.¹⁷
- Figure 7. Effect of gate velocity on the tensile properties of die cast Al-Si alloys.
- Figure 8. Plot depicting the effect of varying plunger velocity on the tensile properties of Al-9Si alloy equivalent to US A380 aluminum alloy.²²,²³
- Figure. 9 Effect of different IP on the (a) microstructure of the die castings³⁰ and (b) percentage porosity.³¹
- Figure 10. Density as a function of different IP levels: the curves refer to different injection plunger velocities.
- Figure 11. Photographs showing the double cylinder cover casting under Worst and (b) Best density values.³³
- Figure 12. Effect of (a) intensification pressure and (b) gate velocity, on the gate freezing time.¹⁶
- Figure 13. Different types of runner-gate systems used by Itamura et al.³⁶ The gate angle in the Fan-type and the gate width in the T-shaped systems were varied.
- Figure 14. The simulation results of melt flow velocity and gas entrapment (represented by marker size) at different time of injection. Markers with different colors indicate entrapped gas with different size. Sampling location for tensile and porosity measurements is indicated in (c).³⁷
- Figure 15. Tensile properties and porosity measurements made at different locations along the length of the casting (L) as shown in Fig. 13c .³⁷
- Figure 16. (a,b,c) Schematic of the three gate types along with the corresponding (d,e,f) temperature distribution during die filling.³⁸
- Figure 17. Runner-gate systems investigated by Dargush et al.³⁹
- Figure 18. Projected area of the die in the parting surface.
7. 결론:
주요 결과 요약:
본 검토에서는 더 높은 게이트 속도와 증압이 HPDC Al-Si 합금에서 기공률을 줄이고 인장 특성을 개선하는 데 중요한 사출 변수라는 결론을 내립니다. 기공률을 최소화하는 최적의 게이트 속도가 존재하며, 더 높은 IP는 주조 밀도를 일관되게 향상시키고 기공률을 감소시킵니다. 러너 및 게이트 설계는 용융 금속 흐름 및 주조 품질에 상당한 영향을 미치며, 접선형 게이트 시스템은 균일한 충전에 유리한 것으로 나타났습니다. 난류를 최소화하기 위해 스테이지 I에서 플런저 속도를 스테이지 II보다 약 10배 낮게 유지하는 것이 좋습니다.
연구의 학문적 의의:
본 연구는 HPDC의 사출 변수 영향에 대한 기존 문헌에 대한 포괄적인 검토를 제공하여 다양한 연구 노력의 결과를 통합합니다. 사출 변수, 기공률, 인장 특성 및 러너/게이트 설계 간의 복잡한 상호 작용을 강조하여 다이캐스팅 분야의 연구자 및 학계에 귀중한 통찰력을 제공합니다.
실용적 의미:
본 연구 결과는 다이캐스팅 엔지니어 및 실무자가 주조 품질 향상을 위해 사출 변수를 최적화하는 데 실용적인 지침을 제공합니다. 특히, 검토에서는 다음의 중요성을 강조합니다.
- 기공률을 최소화하고 인장 특성을 향상시키기 위해 최적 범위 내에서 게이트 속도를 제어합니다.
- 기공률을 줄이고 주조 건전성을 개선하기 위해 높은 증압을 활용합니다.
- 균일한 다이캐비티 충전을 보장하고 난류를 최소화하기 위해 러너 및 게이트 시스템을 신중하게 설계합니다.
- 조기 응고를 피하기 위해 얇은 게이트(1-3mm)와 높은 게이트 속도를 고려하면서 잠재적인 문제를 관리합니다.
연구의 한계 및 향후 연구 분야:
본 연구는 기존 문헌 검토에 국한됩니다. 독창적인 실험 작업이나 수치 시뮬레이션은 포함하지 않습니다. 향후 연구 분야는 다음과 같습니다.
- 특정 Al-Si 합금 및 주조 형상에 대한 최적의 게이트 속도 범위에 대한 추가 연구.
- 게이트 속도, 증압 및 러너/게이트 설계 간의 상호 작용에 대한 상세 연구.
- 기공률을 더욱 최소화하고 주조 품질을 개선하기 위한 고급 러너 및 게이트 설계 연구.
- 캐비티 압력 피드백 및 용융 금속 흐름 모니터링을 기반으로 한 사출 변수에 대한 실시간 제어 전략 탐색.
8. 참고 문헌:
- Benini, A., "High-Pressure Die-Casting Technology – Casting Process and Machines Through the Analysis of Some Case Histories,” Brochure of Italpresse (BS - Italy) (2009).
- Vinarick, E.J., “Die Casting Processes,” John Wiley & Sons Inc., NJ, USA (2003).
- Dørum, C., Laukli, H.I., Hopperstad, O.S., Langseth, M., "Structural Behaviour of Al-Si Die-castings: Experiments and Numerical Simulations," European Journal of Mechanics - A/Solids, vol. 28, issue 1, pp. 1-13 (2009).
- Avalle, M., Belingardi, G., Cavatorta, M. P., Doglione, R., "Static and Fatigue Strength of a Die Cast Aluminium Alloy under Different Feeding Conditions," Proceedings of the Institution of Mechanical Engineers, Part L: Journal of Materials Design and Applications, pp. 25-30 (2002).
- Avalle, M., Belingardi, G., Cavatorta, M.P., Doglione, R., "Casting Defects and Fatigue Strength of a Die Cast Aluminium Alloy: A Comparison Between Standard Specimens and Production Components,” Int. J. Fatigue, vol. 24, pp. 1–9 (2002).
- Srivastava, M.C., “High Pressure Die Casting of Aluminium and Magnesium Alloys," Ph.D.Thesis, NTNU-Norway, 2009:207 (2009).
- Kotadia, H.R., Babu, N.H., Zhang, H., Arumuganathar, S., Fan, Z., "Solidification Behavior of Intensively Sheared Hypoeutectic Al-Si Alloy Liquid," Metall. Mater. Trans. A, vol. 42, pp. 1117-1126 (2011).
- Joshi, V., Srivastava, A., Shivpuri, R., Rolinski, E., “Investigating Ion Nitriding for the Reduction of Dissolution and Soldering in Die-casting Shot Sleeves," Surf. Coat. Technol., vol. 163–164, pp. 668–673 (2003).
- Helenius, R., Lohne, O., Arnberg, L., Laukli, H.I., "The Heat Transfer During Filling of a High-Pressure Die-casting Shot Sleeve," Mater. Sci. Eng., A, vol. 413–414, pp. 52-55 (2005).
- Verran, G.O., Mendes, R.P.K., Rossi, M.A., “Influence of Injection Parameters on Defects Formation in Die Casting Al12Si1, 3Cu Alloy: Experimental Results and Numeric Simulation,” J. Mater. Process. Technol., vol. 179, pp. 190-195 (2006).
- Ward, M., “Gating Manual,” NADCA, USA (2006).
- Jian, X., Wu, G., “An Experimental Investigation on the Flow Behavior of Liquid Aluminium Inside Pressure Die-casting Dies Using High-Speed Photography," SPIE Proceedings, vol. 1358, 19th International Congress on High-Speed Photography and Photonics, pp. 1237-1244 (1990).
- Hartmann, G.C., Chadwick, G., Lindeberg, B., "Process Analysis, Computer Modelling and Production Development of High Pressure Die Casting," EUR 15230EN (1995).
- Karban, R., "The Effects of Intensification Pressure, Gate Velocity, and Intermediate Shot Velocity on the Internal Quality of Aluminum Die Castings,” PhD thesis, Purdue University, West Lafayette, IN, USA (2000).
- Davis, A.J., Robinson, P.M., “Production of Aluminum Die Castings Using a Fan Gate, Part 2. The Effect of Flow Conditions at the Gate on Casting Quality," Trans. Society of Diecasting Engineers, Paper No. G-T75-122, Detroit, MI, USA (1975).
- Niu, X.P., Tong, K.K., Hu, B.H., Pinwill, I., “Cavity Pressure Sensor Study of the Gate Freezing Behaviour in Aluminium High Pressure Die Casting," Int. J. Cast Met. Res., vol. 11, pp. 105-112 (1998).
- Gunasegaram, D.R., Finnin, B.R., Polivka, F.B., “Melt Flow Velocity in High Pressure Die Casting: Its Effect on Microstructure and Mechanical Properties in an Al-Si Alloy," Mater. Sci. Technol., vol. 23, pp. 847-856 (2007).
- Caceres, C.H., Selling, B.I., "Casting Defects and the Tensile Properties of an Al-Si-Mg Alloy," Mater. Sci. Eng. A, vol. 220, pp. 109-116 (1996).
- Ghomashchi, M.R., “High-Pressure Die Casting: Effect of Fluid Flow on the Microstructure of LM24 Die-Casting Alloy," J. Mater. Process. Technol., vol. 52, pp. 193-206 (1995).
- Ghomashchi, R., Proceedings of the 9th International Conference on Aluminium Alloys (ed. J. F. Nie et al.), Melbourne, Institute of Materials Engineering Australasia Ltd. pp.1290–1296 (2004).
- Lumley, R., Deeva, N., Gershenzon, M., “An Evaluation of Quality Parameters for High Pressure Die Castings," Int. J. of Metalcasting, vol. 5, issue 3, pp. 37-56 (2011).
- Timelli, G., Bonollo, F., “Quality Mapping of Aluminium Alloy Diecastings," Metallurgical Science and Technology, vol. 26, no.1, pp. 2-8 (2008).
- Timelli, G., "Constitutive and Stochastic Models to Predict the Effect of Casting Defects on the Mechanical Properties of High Pressure Die Cast AlSi9Cu3(Fe) Alloys," Metallurgical Science and Technology, vol. 28, no. 2, pp. 9-17 (2010).
- Gunasegaram, D.R., Givord, M., O'Donnel, R.G., Finnin, B.R., "Improvements Engineered in UTS and Elongation of Aluminum Alloy High Pressure Die Castings Through the Alteration of Runner Geometry and Plunger Velocity," Mater. Sci. Eng., A, vol. 559, pp 276-286 (2013).
- Pitsaris, C., Savage, G., Abbott, T., Proc. 22nd NADCA International Die Casting Cong., Indianapolis, IN, USA, pp.195-203 (2003).
- Klein, F., Proc. 51st Annual World Magnesium Conf., Berlin, Germany, Inter. Magnesium Association (USA), pp. 35-43 (1994).
- Herman, E.A., "Gating Die Casting Dies,” NADCA, Rosemont, IL, pp. 1-3 and 73-93 (1996).
- Dargusch, M.S., Wang, G., Schauer, N., Dinnis, C.M., Savage, G., "Manufacture of High Pressure Die-Cast Radio Frequency Filter Bodies,” Int. J. Cast Met. Res., vol. 18, issue 1, pp. 47-54 (2005).
- Dargusch, M.S., Dour, G., Schauer, N., Dinnis, C.M., Savage, G., "The Influence of Pressure During Solidification of High Pressure Die Cast Aluminium Telecommunications Components,” J. Mater. Process. Technol., vol. 180, pp. 37-43 (2006).
- Schaffer, P.L., Laukli, H.I., “Recent Developments in Aluminum High Pressure Die Castings,” Die Casting Engineer, pp. 20-22 (May 2012).
- Otarawanna, S., Laukli, H.I., Gourlay, C.M., Dahle, A.K., "Feeding Mechanisms in High-Pressure Die Castings," Metall. Mater. Trans. A, vol. 41, pp. 1836-1846 (2010).
- Otarawanna, S., Gourlay, C.M., Laukli, H.I., Dahle, A.K., "Microstructure Formation in AlSi4MgMn and AlMg5Si2Mn High-Pressure Die Castings," Metall. Mater. Trans. A, vol. 40, pp. 1645-1659 (2009).
- Verran, G.O., Mendes, R.P.K., Rossi, M.A., "Influence of Injection Parameters on Defects Formation in Die Casting Al12Si1,3Cu Alloy: Experimental Results and Numeric Simulation," J. Mater. Process. Technol., vol. 179, pp. 190-195 (2006).
- Verran, G.O., Mendes, R.P.K., Valentina, L.V.O.D., "DOE Applied to Optimization of Aluminum Alloy Die Castings,” J. Mater. Process. Technol., vol. 200, pp. 120-125 (2008).
- Herman, E., “Searching for the Perfect Gate Velocity," Die Casting Engineer, pp. 58-61 (March 2004).
- Itamura, M., Murakami, K., Harada, T., Tanaka, M., Yamamoto, N., "Effect of Runner Design on Metal Flow Into Cavity," Int. J. Cast Met. Res., vol. 15, pp. 167-172 (2002).
- Zhao, H.D., Wang, F., Li, Y.Y., Xia, W., “Experimental and Numerical Analysis of Gas Entrapment Defects in Plate ADC12 Die Castings,” J. Mater. Process. Technol., vol. 209, pp. 4537-4542 (2009).
- Kim, Y.C., Kang, C.S., Cho, J.I., Jeong, C.Y., Choi, S.W., Hong, S.K., “Die Casting Mold Design of the Thin-walled Aluminum Case by Computational Solidification Simulation," J. Mater. Sci. Technol., vol. 24 (3), pp. 383-388 (2008).
- Dargusch, M.S., Wang, G., Schauer, N., Dinnis, C.M., Savage, G., "Manufacture of High Pressure Die-cast Radio Frequency Filter Bodies,” Int. J. Cast Met. Res., vol. 18, pp. 47–53 (2005).
- Ward, M., “Gating Manual,” NADCA, USA, (2006).
- Herman, E., “Searching for the Perfect Gate Velocity," Die Casting Engineer, pp. 58-61 (March 2004).
- Kim, C.H., Kwon, T.H., "A Runner-Gate Design System for Die Casting," Mater. Manuf. Processes, vol. 16 (6), pp. 789-801 (2001).
- Lin, C.B., Ma, C.L., Chung, Y.W., “Microstructure of A380-SiC(p) Composites for Die Casting," J. Mater. Process. Technol., vol. 48, pp. 236–246 (1998).
- Chen, Z.W., “Skin Solidification During High Pressure Die Casting of Al–11Si-2Cu-1Fe Alloy," Mater. Sci. Eng., A, vol. 348, pp. 145-153 (2003).
- Ji, S., Wang, Y., Watson, D., Fan, Z., “Microstructural Evolution and Solidification Behavior of Al-Mg-Si Alloy in High-Pressure Die Casting,” Metall. Mater. Trans. A, vol. 44, pp. 3185-3197 (2013).
- Niu, X.P., Tong, K.K., Hu, B.H., Pinwill, I., "Cavity Pressure Sensor Study of the Gate Freezing Behaviour in Aluminium High Pressure Die Casting," Int. J. Cast Met. Res., vol. 11, pp. 105–112 (1998).
9. 저작권:
- 본 자료는 "[Anilchandra R. Adamane, Lars Arnberg, Elena Fiorese, Giulio Timelli, Franco Bonollo]"의 논문: "[INFLUENCE OF INJECTION PARAMETERS ON THE POROSITY AND TENSILE PROPERTIES OF HIGH-PRESSURE DIE CAST AI-SI ALLOYS: A REVIEW]"를 기반으로 작성되었습니다.
- 논문 출처: https://doi.org/10.1007/s40962-015-0008-x
본 자료는 위 논문을 소개하기 위해 제작되었으며, 상업적 목적으로 무단 사용하는 것을 금지합니다.
Copyright © 2025 CASTMAN. All rights reserved.