본 논문 요약은 ['Proceedings, 4th International Conference on Molten Aluminum Processing, AFS'에 의해 출판된 'Improving Die Casting Melt Quality and Casting Results with Melt Quality Analysis and Filtration'] 논문을 기반으로 작성되었습니다.
1. 개요:
- 제목: 용융 금속 품질 분석 및 여과를 통한 다이캐스팅 용탕 품질 및 주조 결과 개선 (Improving Die Casting Melt Quality and Casting Results with Melt Quality Analysis and Filtration)
- 저자: 데이비드 V. 네프 박사 (Dr. David V. Neff)
- 출판 연도: 논문 내 명시되지 않음
- 출판 저널/학회: 컨퍼런스 Proceedings: 4th International Conference on Molten Aluminum Processing, AFS
- 키워드: 다이캐스팅, 용탕 품질, 여과, 본디드 파티클 필터, 알루미늄, 개재물, 용탕 청정도, 감압 시험, 퀄리플래시, 프리필 풋프린터, PodFA, K-몰드, 타투어 시험, 기계적 시험 (die casting, melt quality, filtration, bonded particle filter, aluminum, inclusions, melt cleanliness, reduced pressure test, Qualiflash, Prefil Footprinter, PodFA, K-Mold, Tatur test, mechanical testing)
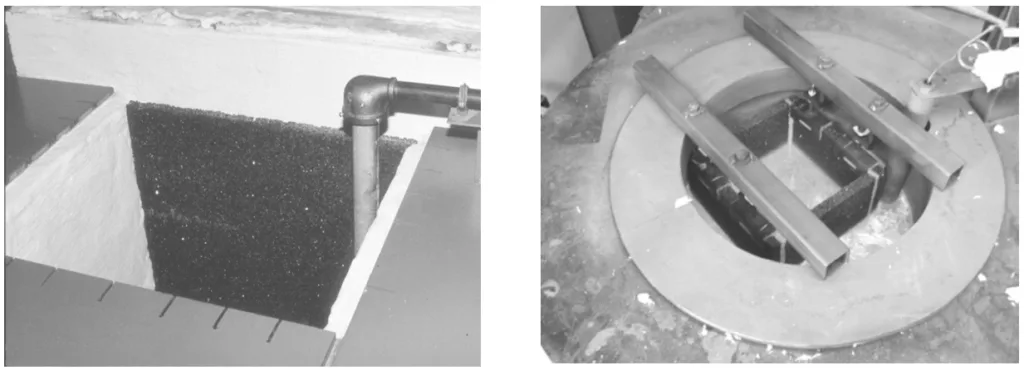
2. 초록 또는 서론
초록 (ABSTRACT)
자동차 부품에 알루미늄 주조품의 사용이 꾸준히 증가하고 있습니다. 대량 생산 요구 사항은 고압, 저압, 영구 금형 및 정밀 사형 주조 공정으로 충족됩니다. 이러한 응용 분야에 대한 엔지니어링 요구 사항은 높은 수준의 주조 건전성을 요구하며, 이는 알루미늄 합금 용탕 조건에서 시작됩니다.
본 논문에서는 특히 개재물과 관련하여 용탕 품질 청정도를 평가하기 위한 여러 현장 및 실험실 방법과 본디드 파티클 필터를 사용하는 지속적인 사용, 용광로 내 여과 시스템에서 얻을 수 있는 이점에 대한 정보를 제시합니다.
본디드 파티클 필터 여과를 활용하여 최소한의 비용, 노력 및 위험으로 가공 결함 감소, 표면 조도 개선, 연신율 증가, 누설 감소 및 전체 스크랩 감소에 상당한 이득을 얻을 수 있습니다.
서론 (INTRODUCTION)
알루미늄 주조 생산 및 공정 기술의 성장은 지난 10년 동안 매우 두드러졌습니다. 엔진 부품, 구조 부품, 휠 및 기타 기능성 주조품에 대한 자동차 사용량 증가는 이러한 성장의 주요 구성 요소입니다. 이러한 주조품의 더 높은 물성 요구 사항은 금속 청정도를 보다 엄격하게 제어하기 위한 우수한 금속 품질 및 용탕 처리 공정을 요구했습니다. 이는 다공성/미세 기공성을 최소화하기 위한 개재물 및 수소 함량 제어를 포함합니다. 깨끗한 금속을 생산하기 위한 용탕 처리에는 플럭싱 및/또는 플럭스 주입, 탈기 및 여과가 포함됩니다. 여과 공정은 현재 거의 모든 알루미늄 형상 주조 작업에 사용됩니다. 예상 및 달성되는 일반적인 이점에는 (1) 주조 공정 중 더 나은 금속 유동성 및 공급 능력, (2) 더 높은 주조 물성, (3) 향상된 가공성, (4) 더 나은 표면 조도, (5) 전체 스크랩 및 불량 주조품 감소가 포함됩니다.
압력 다이캐스팅, 특정 중력 다이캐스팅 또는 영구 금형 공정, 그리고 대량 생산 그린 또는 화학 결합 사형 주조 공정에서는 절대적인 주입 지점, 즉 금형 내 여과를 제공하는 것이 종종 실용적이지 않습니다. 따라서 남은 선택 사항은 용해/재용해 용광로 및 주조 용광로에서 주조 지점에 최대한 가깝게 필터를 사용하는 것입니다. 본디드 파티클 필터는 대부분의 경우 이러한 용광로 내 응용 분야에서 선호되는 필터로 부상했습니다 (Neff, 1995). 이 필터는 장기간 용융 알루미늄에서 어떠한 열화에도 저항하는 독점적인 세라믹 바인더로 결합된 탄화 규소의 집합체입니다. 탄화 규소 재료는 또한 매우 내구성이 뛰어나고 열전도성이 뛰어나 장기간 지속적으로 사용하기에 가장 적합합니다. 본디드 파티클 필터의 낮은 다공성, 내부 구조의 굴곡성, 그리고 개재물을 포착하고 유지하는 바인더 시스템의 친화성은 전체 개재물 제거 효율을 향상시킵니다.
일반적인 구성에는 수직 게이트 필터 (그림 1a)가 포함되며, 이는 주조 용광로 또는 '박스 필터' (그림 1b)에서 노상과 딥아웃 웰을 분리합니다. 후자는 용광로 형상 및 국자 크기에 맞게 다양한 기하학적 모양과 크기로 구성될 수 있으며, 더 넓은 표면적을 제공한다는 장점이 있습니다. 주조될 금속은 유지 용광로 또는 도가니 용광로에 배치된 필터 용기 내부에서 자동 국자로 뜨거나 수동으로 담급니다.
3. 연구 배경:
연구 주제 배경:
알루미늄 주조 산업, 특히 자동차 응용 분야에서 상당한 성장을 경험했습니다. 이러한 확장은 고압 다이캐스팅, 저압 다이캐스팅, 영구 금형 주조 및 정밀 사형 주조와 같은 공정을 사용하여 복잡한 부품을 대량 생산하려는 요구에 의해 주도됩니다. 이러한 응용 분야에는 알루미늄 주조품에 우수한 건전성이 요구되며, 이는 근본적으로 알루미늄 합금 용탕의 품질에 달려 있습니다. 높은 주조 건전성을 달성하려면 용탕 조건, 특히 용탕 청정도에 대한 세심한 관리가 필요합니다.
기존 연구 현황:
플럭싱, 탈기 및 여과를 포함한 용탕 처리 공정은 깨끗한 알루미늄 용탕을 생산하는 데 매우 중요합니다. 특히 여과는 거의 모든 알루미늄 형상 주조 작업에서 표준 관행이 되었습니다. 본디드 파티클 필터는 용광로 내 여과 응용 분야에 선호되는 기술이 되었습니다. 독점적인 세라믹 바인더로 결합된 탄화 규소 집합체로 구성된 이러한 필터는 용융 알루미늄에서 열화에 대한 저항성을 제공하며 지속적이고 연속적인 사용을 위해 설계되었습니다. 낮은 다공성 및 굴곡성을 포함한 구조적 특성은 바인더의 개재물 친화성과 결합하여 개재물 제거 효율을 향상시키는 데 기여합니다.
연구의 필요성:
여과가 널리 채택되었지만, 그 효과와 그 결과로 인한 용탕 품질 개선을 정량화하는 것은 여전히 중요합니다. 다이캐스터는 육안 관찰을 넘어 여과 성능을 평가할 수 있는 방법이 필요합니다. 생산 및 실험 환경 모두에서 본디드 파티클 여과를 통해 달성한 용탕 청정도 개선을 평가하기 위한 정량적 및 반정량적 기술이 필요합니다. 이러한 평가는 주조 공정을 최적화하고 결함을 줄이며 다이캐스팅 부품의 전반적인 품질을 향상시키는 데 필수적입니다.
4. 연구 목적 및 연구 질문:
연구 목적:
주요 연구 목적은 다이캐스팅 용탕 품질 및 후속 주조 결과 개선에 있어 본디드 파티클 여과의 효능을 입증하고 정량화하는 것입니다. 본 연구는 용탕 청정도 및 주조 성능에 대한 엄격한 평가를 통해 본디드 파티클 필터를 사용하는 용광로 내 여과 시스템의 이점을 보여주는 것을 목표로 합니다.
핵심 연구:
본 연구는 다이캐스팅 맥락에서 용융 금속 청정도를 평가하기 위한 다양한 기존 및 새로운 기술을 평가하는 데 중점을 둡니다. 연구에서는 다음과 같은 방법의 적용을 조사합니다.
- 감압 시험 (Reduced Pressure Test)
- 실제 수소 측정 (알스캔, 하이스캔, 레코 분석) (Actual hydrogen measurement (Alscan, Hyscan, Leco analysis))
- 퀄리플래시 유동성 시험 (Qualiflash fluidity test)
- 프리필 풋프린터 시험 (Prefil Footprinter test)
- PodFA (다공성 디스크 여과 장치) 또는 LAIS (액체 알루미늄 개재물 샘플러) 시험 (PodFA (Porous Disc Filtration Apparatus) or LAIS (Liquid Aluminum Inclusion Sampler) test)
- 기계적 시험 (Mechanical testing)
- 타투어 시험 (Tatur test)
- K-몰드 시험 (K-Mold test)
연구의 핵심은 이러한 기술을 적용하여 생산 규모 실험 및 지속적인 생산 환경에서 본디드 파티클 여과로 인한 용탕 품질 개선을 평가하는 것입니다.
연구 가설:
본디드 파티클 여과를 구현하면 용융 금속 청정도가 크게 향상될 것이라는 가설을 세웠습니다. 이러한 개선은 다음 사항에서 나타날 것으로 예상됩니다.
- 다이캐스팅 중 향상된 금속 유동성 및 공급 능력.
- 우수한 주조 기계적 물성, 특히 연신율.
- 다이캐스팅 부품의 향상된 가공성.
- 주조품의 향상된 표면 조도.
- 다이캐스팅 생산에서 전체 스크랩 및 불량률 감소.
5. 연구 방법론
연구 설계:
본 연구는 본디드 파티클 여과의 영향을 종합적으로 평가하기 위해 실험실 규모 평가와 생산 주조 공장 시험을 결합하여 사용합니다. 실험실 실험은 통제된 환경에서 산업 조건을 시뮬레이션하기 위해 생산 규모 용탕에서 수행되었습니다. 생산 시험은 실제 제조 환경에서 실험실 결과를 검증하기 위해 실제 압력 및 중력 다이캐스팅 주조 공장에서 수행되었습니다.
자료 수집 방법:
용탕 품질 데이터는 다음과 같은 다양한 분석 기술을 사용하여 수집되었습니다.
- 감압 시험 (Reduced Pressure Test): 전체 용탕 청정도를 평가하고 수소 함량을 추정합니다.
- 알스캔 (Alscan): 용융 금속에서 수소 함량을 실시간으로 측정합니다.
- 퀄리플래시 (Qualiflash): 용융 금속 유동성을 평가합니다.
- 프리필 풋프린터 (Prefil Footprinter): 축적된 산업 벤치마크와 관련된 금속 청정도를 실시간으로 분석합니다.
- PodFA: 시험 필터에 농축된 개재물의 금속 조직학적 평가를 위해 사용됩니다.
- 기계적 시험 (Mechanical Testing): 주조 시험편을 사용하여 인장 및 항복 강도, 연신율 및 피로 강도를 결정합니다.
- 타투어 시험 (Tatur Test): 수축 및 기공 분포를 측정합니다.
- K-몰드 시험 (K-Mold Test): 파단된 시편에서 육안으로 거시적 결함을 검사하는 현장 시험입니다.
스크랩률, 가공 결함 및 표면 조도 품질과 같은 주조 성능 데이터도 생산 시험에서 수집되었습니다.
분석 방법:
알스캔, 프리필 풋프린터, 기계적 시험 및 타투어 시험과 같은 기술에서 얻은 정량적 데이터는 여과로 인한 개선의 유의성을 결정하기 위해 통계적으로 분석되었습니다. 감압 시험, 퀄리플래시, PodFA 및 K-몰드와 같은 반정량적 방법은 용탕 청정도 및 결함 수준에 대한 비교 평가를 제공하는 데 사용되었습니다. 여과된 용탕과 여과되지 않은 용탕의 결과를 비교하여 본디드 파티클 여과의 이점을 정량화했습니다. 금속 조직학적 검사 및 이미지 분석은 PodFA 시험에서 개재물 평가에 활용되었습니다.
연구 대상 및 범위:
조사 대상의 주요 재료는 다이캐스팅에 일반적으로 사용되는 합금인 LM24 (A380) 알루미늄 합금이었습니다. 본 연구는 본디드 파티클 필터의 한 유형인 8 그리트 메탈릭스 박스 필터 (8 grit Metaullics Box Filters)를 사용하는 용광로 내 여과 시스템에 초점을 맞췄습니다. 연구 범위는 실험실 시뮬레이션과 압력 및 중력 다이캐스팅 주조 공장 내 실제 생산 환경 모두에서 용탕 품질 및 주조 결과 평가를 포함했습니다.
6. 주요 연구 결과:
핵심 연구 결과:
본 연구는 본디드 파티클 여과가 다이캐스팅 용탕 품질 및 주조 결과를 크게 개선한다는 것을 입증했습니다. 주요 결과는 다음과 같습니다.
- 향상된 용탕 청정도: 프리필 풋프린터 시험 (그림 9a, 9b), PodFA 분석 (그림 10, 11) 및 K-몰드 시험 (그림 12a, 12b)은 여과되지 않은 용탕 및 산업 표준과 비교하여 본디드 파티클 여과를 통해 용탕 청정도가 향상되었음을 일관되게 보여주었습니다.
- 향상된 금속 유동성: 퀄리플래시 시험 (그림 13a) 및 프리필 풋프린터 곡선 (그림 9a, 9b)은 여과된 용탕에서 향상된 금속 유동성을 나타내어 더 나은 금형 충전 능력을 시사했습니다.
- 연신율 증가: 기계적 시험 (표 2) 결과, 여과된 시편에서 연신율이 크게 향상되었으며, 이는 구조용 주조품에 중요한 물성입니다. 인장 강도와 항복 강도는 적당히 깨끗한 용탕의 경우 예상대로 크게 영향을 받지 않았습니다.
- 결함 감소: 생산 주조 공장 데이터 (표 3) 및 K-몰드 결과 (그림 12b)는 여과된 금속을 사용할 때 가공 작업에서 경점, 누설, 스크랩률 및 공구 파손이 감소했음을 나타냅니다.
- 타투어 시험 개선: 타투어 시험 결과 (표 1)는 여과된 재료에서 수축 부피가 3% 감소하고 공급 거리가 10% 증가하여 공급 특성이 개선되었음을 시사했습니다.
제시된 데이터 분석:
- 프리필 풋프린터 곡선 (그림 9a, 9b): 여과된 금속이 더 가파른 곡선을 나타내어 더 빠른 유속과 더 나은 유동성을 나타내며 '깨끗한 금속' 산업 표준에 부합함을 보여주었습니다. 생산 주조 공장 프리필 결과 (그림 9b)는 여과를 통해 상당한 개선이 있음을 확인했습니다.
- PodFA 결과 (그림 10, 11): 20 ppi 세라믹 폼 필터 및 여과되지 않은 용탕과 비교하여 8 그리트 본디드 파티클 필터에서 총 개재물 함량이 감소했음을 입증했습니다. 그림 11은 플럭스 주입 후에도 여과로 달성한 개선을 더욱 강조했습니다.
- K-몰드 시험 결과 (그림 12a, 12b): 여과된 용탕과 여과되지 않은 용탕을 명확하게 구별했으며, 여과된 시편은 K-팩터 값 (결함 감소)이 일관되게 낮았습니다. 생산 다이캐스터 K-몰드 결과 (그림 12b)는 380 합금에서 우수한 결과를 보여주며 이러한 결과를 뒷받침했습니다.
- 퀄리플래시 결과 (그림 13a): 실험실 환경에서 박스 필터를 사용하여 유동성 (더 높은 Q 레벨)이 크게 향상되었음을 입증했습니다.
- 타투어 시험 결과 (표 1): 여과된 재료가 수축 부피 감소 및 공급 거리 개선을 보여주어 여과가 수축 및 공급 특성에 긍정적인 영향을 미쳤음을 나타냅니다.
- 기계적 물성 데이터 (표 2): 여과된 시편에서 연신율이 눈에 띄게 증가한 반면, 인장 강도와 항복 강도는 거의 영향을 받지 않았음을 강조했습니다.
- 주조 공장 이점 데이터 (표 3): 용광로 내 본디드 파티클 여과로 인해 경점 제거, 누설 감소, 공구 수명 연장 및 스크랩률 감소와 같은 이점을 경험한 주조 공장의 실제 사례를 제공했습니다.
그림 목록:
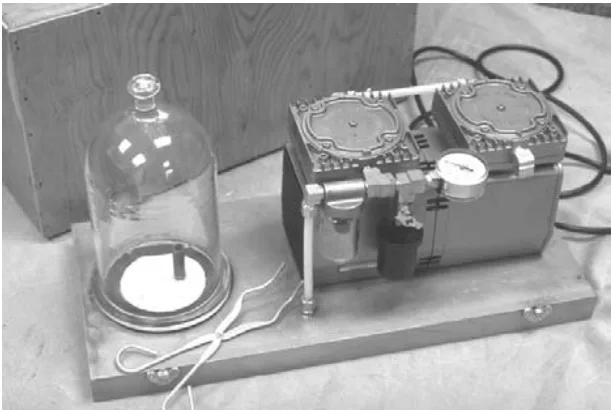
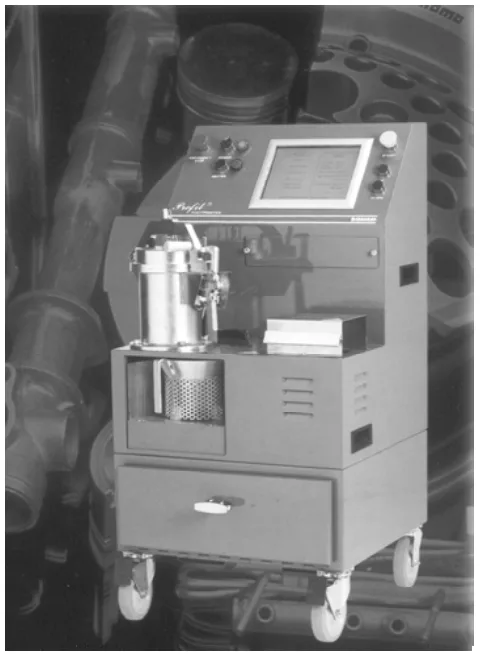
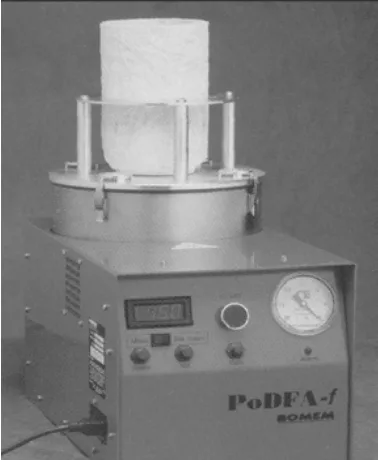
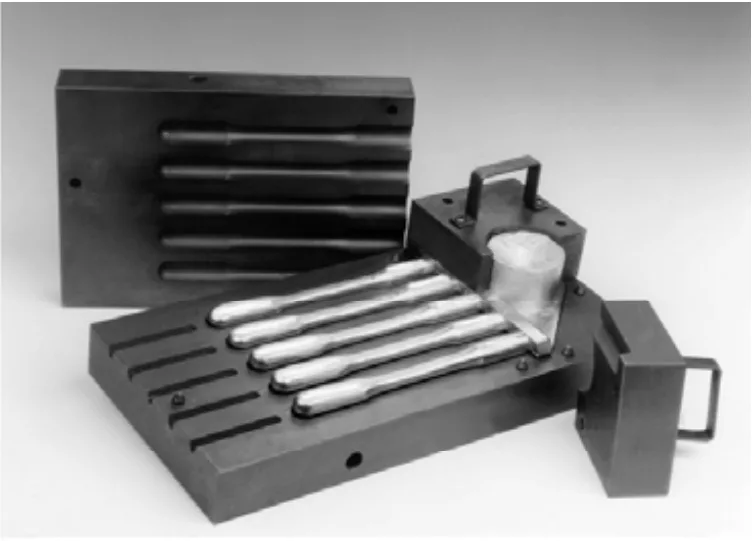
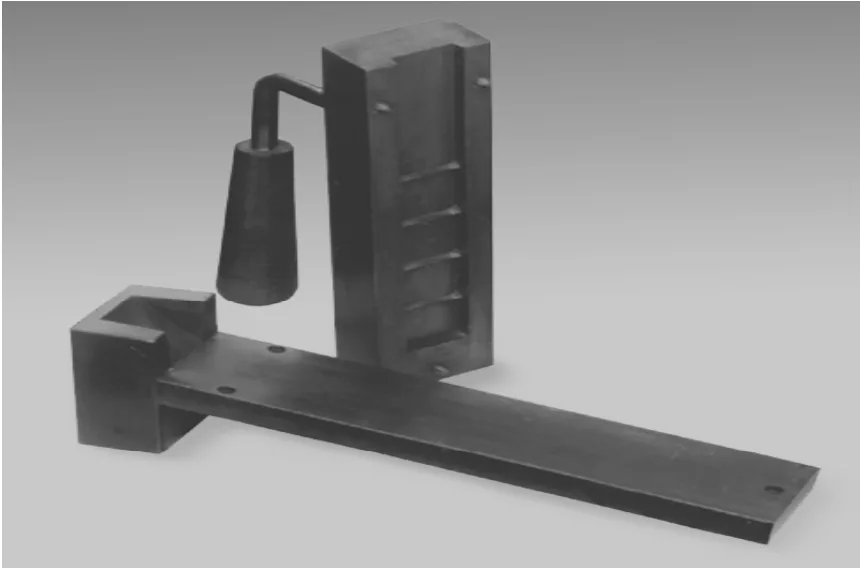
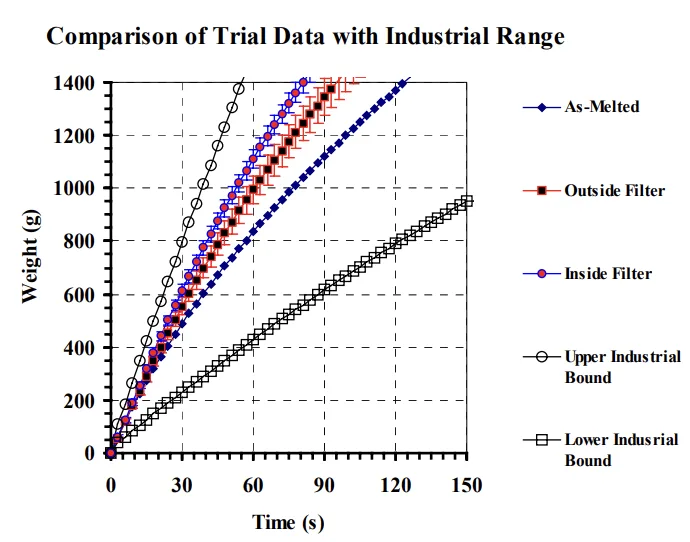
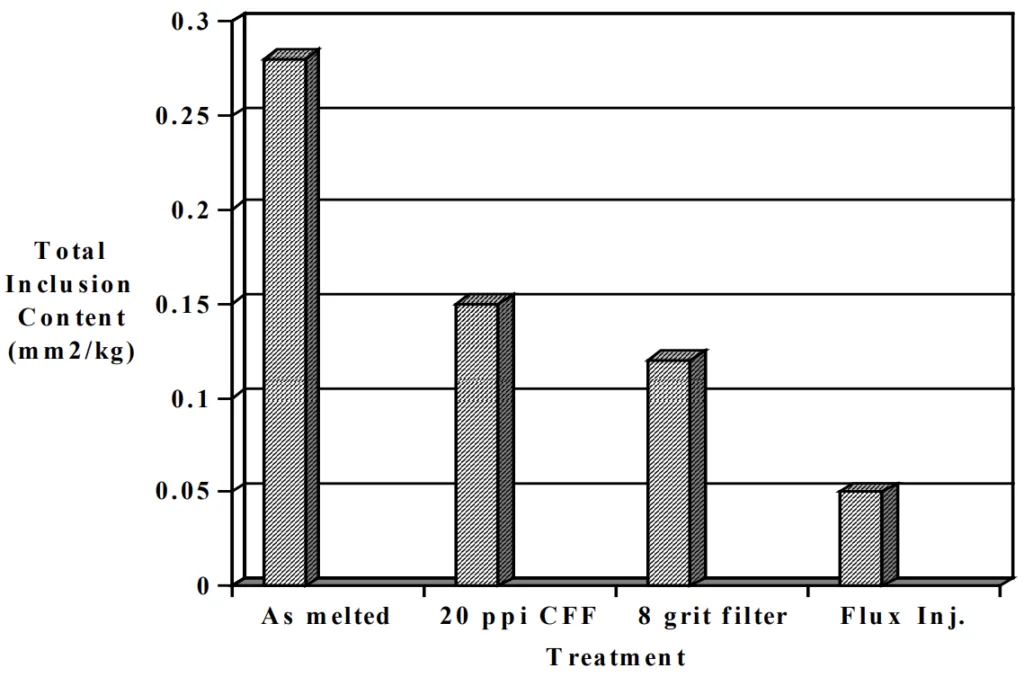
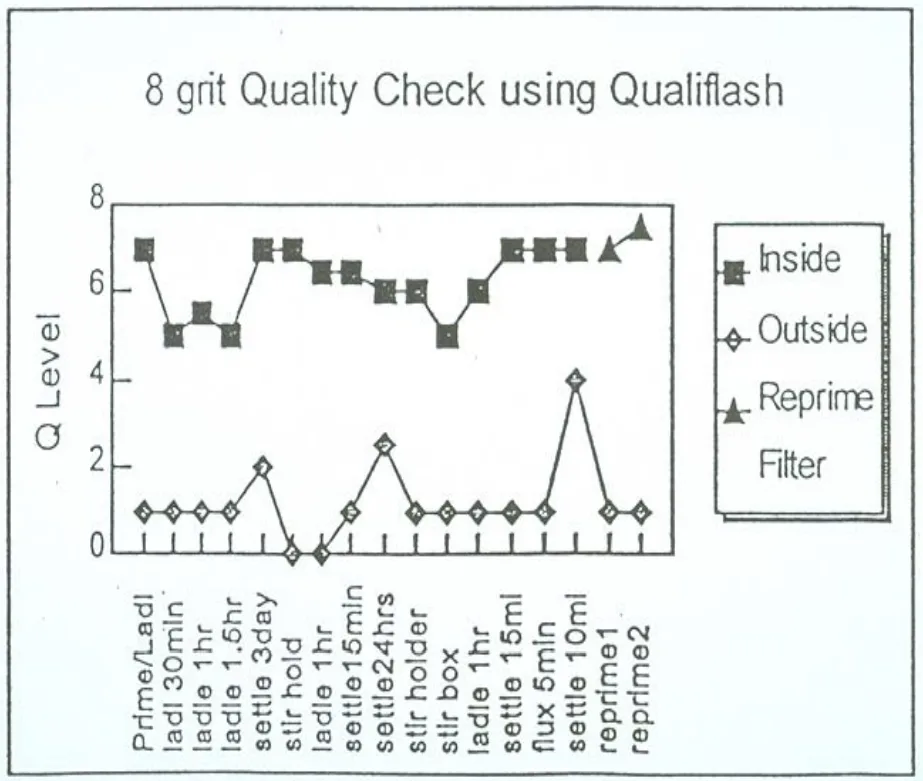
- 그림 1a: 수직 게이트 필터는 주조 용광로의 배출구 웰 또는 딥웰에 배치됩니다. (Figure 1a: Vertical Gate Filters are placed in the outlet well or dipwell of a casting furnace.)
- 그림 1b: 박스 필터는 도가니 용광로 또는 기타 용광로 유형의 딥웰에 유용합니다. (Figure 1b: A box filter is useful in crucible furnaces our dipwells of other furnace types.)
- 그림 2: 감압 시험은 주조 공장 및 다이캐스터가 금속 품질을 평가하는 데 가장 일반적으로 사용되는 도구입니다. (Figure 2: The Reduced Pressure Test is the most common tool used by foundries and diecasters to assess metal quality.)
- 그림 3: 퀄리플래시 시험은 용융 금속 유동성을 반정량적으로 측정합니다. (Figure 3: The Qualiflash test measures molten metal fluidity semi-quantitatively.)
- 그림 4: 프리필 풋프린터는 축적된 산업 데이터와 관련된 금속 청정도의 실시간 분석을 제공합니다. (N-Tec) (Figure 4: The Prefil Footprinter provides real-time analysis of metal cleanliness relative to accumulated industry data. (N-Tec))
- 그림 5: PodFA 시험은 수집된 시편의 금속 조직학을 사용하여 금속 청정도를 평가하는 일반적인 방법입니다. (Figure 5: The PodFA test is a common method to evaluate metal cleanliness using metallography on the collected sample.)
- 그림 6: 다중 시험편 금형은 기계적 시험용 시편을 주조하는 데 사용됩니다. (N-Tec) (Figure 6: A multiple test bar mold is used to cast specimens for mechanical testing. (N-Tec))
- 그림 7: 타투어 시험은 수축 및 기공성을 측정합니다. (N-Tec). (Figure 7: The Tatur test measures shrinkage and porosity. (N-Tec).)
- 그림 8: K-몰드는 거시적 청정도를 평가하는 간단한 현장 실시간 시험입니다. (Figure 8: The K-Mold is a simple shop-floor, real-time test which evaluates macro-cleanliness.)
- 그림 9a: 프리필 곡선은 정상 산업 데이터와 비교하여 필터로 개선된 유동성을 보여줍니다. (Figure 9a: The Prefil curve demonstrates improved fluidity with the filter compared with normal industry data.)
- 그림 9b: 생산 주조 공장 프리필 결과는 여과의 이점을 검증합니다. (Figure 9b: Production foundry Prefil results verify benefits of filtration.)
- 그림 10: PodFA 결과는 20 ppi 세라믹 폼 필터보다 8 그리트 본디드 파티클 필터의 개선을 보여줍니다. (Figure 10: PodFA results show improvement of 8 grit bonded particle filter over 20 ppi ceramic foam filter.)
- 그림 11: PodFA 결과는 플럭스 주입 후 여과에 의한 추가 개선을 보여줍니다. (Figure 11: PodFA results show further improvement by filtration after flux injection.)
- 그림 12a: 동일한 금속을 지속적으로 재사용 한 후의 실험실 K-몰드 결과. (Figure 12a: Laboratory K-mold results after continuous re-use of the same metal.)
- 그림 12b: 생산 다이캐스터 K-몰드 결과는 380 합금에서 우수한 결과를 보여줍니다. (Figure 12b: Production diecaster K-Mold results show excellent results on 380 alloy.)
- 그림 13a: 퀄리플래시를 사용한 실험실 결과는 박스 필터로 상당한 개선을 보여줍니다. (Figure 13a: Laboratory results with Qualiflash show significant improvement with the box filter.)
7. 결론:
주요 결과 요약:
본 연구는 본디드 파티클 여과가 다이캐스팅 용탕 품질 및 주조 성능에 미치는 유익한 영향을 결정적으로 입증합니다. 다양한 용탕 품질 평가 기술 및 생산 데이터를 활용하여 본 연구는 본디드 파티클 필터를 사용한 용광로 내 여과가 용탕 청정도를 효과적으로 향상시키고, 금속 유동성을 개선하며, 연신율을 증가시키고, 주조 결함 및 스크랩률을 감소시킨다는 것을 확인합니다. 이러한 개선은 다이캐스팅 작업에서 실질적인 이점으로 이어져 더 높은 품질의 주조품과 생산 비용 절감에 기여합니다.
연구의 학문적 의의:
본 연구는 다이캐스팅 맥락에서 다양한 용탕 품질 평가 방법론에 대한 포괄적인 평가를 제공합니다. 또한 우수한 알루미늄 용탕 품질을 달성하기 위한 중요한 용탕 처리 공정으로서 본디드 파티클 여과의 효과를 과학적으로 검증합니다. 본 연구는 여과가 용탕 청정도에 미치는 영향과 그에 따른 주조 물성에 미치는 영향에 대한 기본적인 이해에 기여합니다.
실용적 의미:
본 연구 결과는 다이캐스팅 산업에 중요한 실용적 의미를 제공합니다. 본 연구는 주조 품질 및 운영 효율성을 향상시키기 위한 최상의 방법으로 본디드 파티클 필터를 사용한 용광로 내 여과를 채택할 것을 강력히 옹호합니다. 본 연구는 공정 모니터링 및 최적화를 위해 용탕 품질 평가 기술을 사용하는 것의 중요성을 강조합니다. 다이캐스터는 이러한 결과를 활용하여 효과적인 여과 전략을 구현하고, 결함을 줄이고, 가공성을 개선하며, 궁극적으로 주조품의 시장성을 향상시킬 수 있습니다.
연구의 한계 및 향후 연구 분야:
본 연구는 본디드 파티클 여과의 이점에 대한 강력한 증거를 제공하지만, 특정 결과는 주조 공장별 조건, 합금 유형 및 주조 공정에 따라 다를 수 있음을 인정합니다. 향후 연구에서는 다음 사항을 탐구할 수 있습니다.
- 다양한 합금 및 주조 응용 분야에 대한 여과 매개변수 (예: 필터 기공 크기, 유속) 최적화.
- 산업 환경에서 본디드 파티클 필터의 장기적인 성능 및 내구성 평가.
- 다양한 다이캐스팅 작업에서 용광로 내 여과 구현에 대한 상세한 비용-편익 분석.
- 본 연구에서 평가한 것 외에 다른 주조 결함 및 기계적 물성에 대한 여과의 영향 조사.
- 여과 공정과 통합된 실시간 용탕 품질 모니터링 및 제어 시스템 개발.
8. 참고 문헌:
- 1. Neff, D., "continuous, Sustained, “Re-useable” Filtration Systems for Aluminum Foundries and Diecasters, Proceedings, 4th International Conference on Molten Aluminum Processing, AFS, Orlando, November, 1995, р.121
- 2. Law, J., Tian, C., Murray, M., “Experiences in the Measurement of Molten Metal Quality in a High Pressure Diecasting Foundry", Transacations, NADCA 1999, p.235
- 3. Evans, C., Willmert, W., “Qualiflash as it Relates to Filtration and Degassing for Foundry and Extrusion Alloys" Proceedings, Fifth International Conference, Molten Aluminum Processing, AFS, Orlando, November, 1998, p. 349
9. 저작권:
- 본 자료는 "Dr. David V. Neff"의 논문: "Improving Die Casting Melt Quality and Casting Results with Melt Quality Analysis and Filtration"을 기반으로 합니다.
- 논문 출처: 논문 내 명시되지 않음.
본 자료는 상기 논문을 기반으로 요약되었으며, 상업적 목적으로 무단 사용하는 것을 금지합니다.
Copyright © 2025 CASTMAN. All rights reserved.