본 논문 요약은 ['Hong-Kyu Kwon']이 ['MDPI']에서 발행한 ['Layout Design and Die Casting Using CAE Simulation for Household Appliances'] 논문을 기반으로 작성되었습니다.
1. 개요:
- 제목: 가정용 기기를 위한 CAE 시뮬레이션을 이용한 레이아웃 설계 및 다이캐스팅 (Layout Design and Die Casting Using CAE Simulation for Household Appliances)
- 저자: 홍규권 (Hong-Kyu Kwon)
- 발행 연도: 2021년
- 발행 학술지/학회: 응용 과학 (Applied Sciences) (MDPI)
- 키워드: 게이트 시스템 (gate system); 고압 다이캐스팅 (high pressure die casting); CAE 시뮬레이션 (CAE simulation); 유동 해석 (flow analysis); 쿠킹 그릴 (cooking grill)
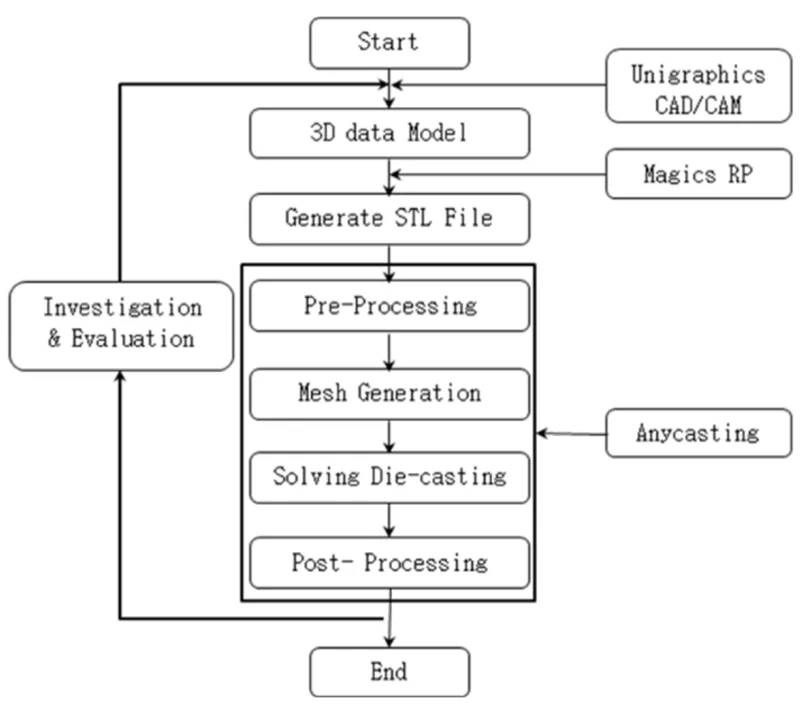
2. 초록 또는 서론
본 연구는 가정용 기기, 특히 쿠킹 그릴의 고압 다이캐스팅(HPDC)에 컴퓨터 지원 엔지니어링(CAE) 기술을 적용하는 것을 탐구합니다. 본 연구는 다양한 산업 분야에서 알루미늄 합금 부품에 대한 수요 증가와 생산 비용 절감 및 제품 품질 향상을 위한 효율적인 주조 레이아웃 설계의 필요성을 다룹니다.
주조 산업에서 금형 설계자의 경험과 지식에 크게 의존하는 전통적인 주조 레이아웃 설계는 급변하는 기술 발전과 경제적 압력에 대응하기에 점점 더 불충분해지고 있습니다. CAE 기술은 주조 결함을 예측하고 금형 설계 단계에서 충전 및 응고 해석을 수행하여 금형 개발 및 제작 과정에서 시행착오를 최소화함으로써 최적의 금형 설계 방법을 가능하게 하는 솔루션으로 제시됩니다.
본 연구는 제품 품질을 보장하고 생산 비용을 절감하기 위해 CAE 시뮬레이션을 사용하여 가정용 기기 금형을 위한 건전한 주조 레이아웃을 확립하는 것을 목표로 합니다.
3. 연구 배경:
연구 주제 배경:
과학 기술의 발전과 산업화로 인해 알루미늄 합금의 활용이 증가했습니다. 자원 보존, 에너지 효율 및 환경 문제에 대한 관심이 높아짐에 따라 주조 산업, 특히 고압 다이캐스팅(HPDC)에서 알루미늄 제품이 주철 부품을 대체하는 추세가 늘고 있습니다. HPDC는 복잡한 부품을 한 번에 대량 생산할 수 있는 경제적인 대량 생산 기술이며, 고품질, 저비용 및 짧은 납기를 요구하는 소비재, 자동차 및 전자 산업에서 중요한 제조 기술로 인정받고 있습니다. 그러나 HPDC는 용융 금속의 고온, 금형 표면의 고압, 제품 형상의 복잡성과 정밀성으로 인해 더욱 발전된 금형 제작 기술을 필요로 합니다.
기존 연구 현황:
기존 연구에서는 HPDC에서 주조 레이아웃 설계 및 게이팅 시스템의 중요한 역할을 인정하고 있으며, 이는 전통적으로 금형 설계자의 경험에 의존해 왔습니다. CAE 기술의 적용은 경험 기반 설계의 한계를 해결하기 위해 빠르게 증가하고 있습니다. 선행 연구에서는 박막 하우징[10]의 응고 시뮬레이션, 연료 전지 분리판[11]의 충전 및 응고 해석, 자동차 기어 하우징[13]의 최적화, 박막 부품[14]의 LPDC 파라미터 최적화 등 다양한 주조 공정 분석에서 CAE의 효과가 입증되었습니다. 또한, 컴퓨터 지원 파라메트릭 설계를 이용한 반자동 게이팅 시스템 설계[15]에 대한 연구도 진행되었습니다. 이러한 연구들은 주조 공정 설계 및 결함 예측을 향상시키기 위해 CAE 시뮬레이션을 활용하는 추세를 강조합니다.
연구의 필요성:
전통적인 시행착오 방식의 주조 레이아웃 설계 및 금형 제작은 시간과 비용이 많이 소요됩니다. CAE 기술의 발전은 이러한 경험적 방법에 대한 의존도를 줄일 수 있는 중요한 기회를 제공합니다. 주조 중 충전 및 응고 과정을 신속하고 정확하게 예측하여 견고하고 비용 효율적인 생산 방법을 확립할 수 있는 방법론이 필요합니다. 특히 쿠킹 그릴과 같은 가정용 기기의 경우 CAE 시뮬레이션을 통해 주조 레이아웃을 최적화하면 금형 개발 및 제작과 관련된 생산 비용과 시간을 줄이면서 공기 기공 및 수축과 같은 결함을 최소화하여 제품 품질을 보장할 수 있습니다.
4. 연구 목적 및 연구 질문:
연구 목적:
본 연구의 주요 목적은 가정용 기기(쿠킹 그릴)의 다이캐스팅에서 충전 및 응고 과정을 예측하기 위해 CAE 시뮬레이션 기술을 활용하는 것입니다. 이는 생산 비용을 최소화하고 제품 품질을 보장하는 건전한 주조 방법을 확립하는 것을 목표로 합니다. 본 연구는 금형 충전 및 응고 과정을 분석하여 결함 제어 방법을 개발하고 다이캐스팅 금형 설계 및 제작 공정에 대한 최적의 주조 방법을 결정하고자 합니다.
핵심 연구:
핵심 연구는 ADC12 합금으로 만들어진 쿠킹 그릴에 대한 세 가지 다른 주조 레이아웃을 분석하기 위해 CAE 시뮬레이션 소프트웨어(AnyCasting)를 적용하는 데 중점을 둡니다. 본 연구는 내부 공기 기공 및 수축 결함을 최소화하여 주조 품질과 안정성을 보장하기 위해 게이팅 시스템 설계가 용융 금속 흐름 및 응고 패턴에 미치는 영향을 조사합니다.
연구 가설:
본 연구는 CAE 시뮬레이션을 사용하고 게이팅 시스템 설계를 체계적으로 수정함으로써, 특히 다중 인게이트 시스템(Case 1)에서 링 게이트 시스템(Case 2 및 3)으로 전환하고 비스킷 설계를 더욱 개선(Case 3)함으로써, 보다 균형 잡힌 용융 금속 흐름을 달성하고, 공기 기공 고립을 줄이고, 역류 및 와류 현상을 최소화하고, 응고를 최적화하여 다이캐스팅 쿠킹 그릴의 수축 결함을 줄일 수 있다고 가정합니다. 본 연구는 개선된 게이팅 및 비스킷 설계를 갖춘 Case 3이 Case 1 및 Case 2에 비해 우수한 주조 성능을 보일 것으로 예상하며, 이는 최적의 주조 레이아웃으로 이어질 것입니다.
5. 연구 방법론
연구 설계:
본 연구는 가정용 기기(쿠킹 그릴)에 대한 세 가지 다른 주조 레이아웃의 성능을 분석하고 비교하기 위해 CAE 소프트웨어(AnyCasting)를 사용하는 시뮬레이션 기반 실험 설계를 채택합니다. 본 연구는 재료 속성, 공정 매개변수 및 금형 설계 변형에 의해 정의된 제어 조건 하에서 용융 금속 흐름 및 응고 과정의 수치 해석에 중점을 둡니다.
자료 수집 방법:
자료는 AnyCasting 소프트웨어를 사용하여 수행된 CAE 시뮬레이션을 통해 수집됩니다. 시뮬레이션 과정은 3D CAD 모델의 전처리, 메쉬 생성, 다이캐스팅 공정 방정식 풀이, 결과 시각화 및 분석을 위한 후처리를 포함합니다. 소프트웨어는 PM(다공성 매체) 방법과 Cut-Cell 방법을 결합한 하이브리드 수치 해석 방법을 사용합니다. 시뮬레이션 결과에는 다양한 충전 단계에서 용융 금속 흐름 패턴의 시각적 표현과 응고 진행 상황, 그리고 공기 기공 및 수축 결함의 예측 위치가 포함됩니다.
분석 방법:
분석 방법은 세 가지 주조 레이아웃에 대한 시뮬레이션 결과의 비교 평가를 포함합니다. 유동 해석 결과는 용융 금속 흐름 균일성, 미충전 또는 냉각 랩의 존재, 공기 기공 고립 및 역류 현상을 기준으로 평가됩니다. 응고 해석 결과는 예측된 수축 결함의 위치와 범위를 기준으로 평가됩니다. 시뮬레이션 결과의 질적 및 시각적 분석, 특히 그림 3-11을 사용하여 각 주조 레이아웃의 성능을 비교하고 최적의 설계를 식별합니다.
연구 대상 및 범위:
연구 대상은 ADC12 알루미늄 합금으로 만들어진 가정용 쿠킹 그릴의 다이캐스팅 공정입니다. 연구 범위는 AnyCasting 소프트웨어를 사용한 세 가지 특정 주조 레이아웃 설계(Case 1, Case 2 및 Case 3)의 수치 시뮬레이션 분석으로 제한됩니다. 재료 속성, 공정 매개변수(사출 속도, 온도) 및 금형 재료(SKD61)는 일반적인 HPDC 조건을 기반으로 정의됩니다. 분석은 충전 및 응고 단계에 초점을 맞추어 결함 최소화 및 품질 향상을 위해 게이팅 시스템 및 전체 주조 레이아웃을 최적화하는 것을 목표로 합니다.
6. 주요 연구 결과:
핵심 연구 결과:
- 유동 해석:
- Case 1 (8개 인게이트): 불균형 유동 및 잠재적인 공기 기공 고립 현상 (그림 4).
- Case 2 (링 게이트): Case 1에 비해 유동 균형이 개선되었지만 비스킷(스프루)에서 와류 형성 및 역류 현상 발생 (그림 6).
- Case 3 (둥근 비스킷 특징으로 수정된 링 게이트): 가장 균일한 용융 금속 흐름을 보였고, 역류 및 와류 현상을 최소화했으며, 공기 기공을 감소시킴 (그림 8, 그림 11).
- 응고 해석:
- Case 3에 대한 응고 해석 결과 두꺼운 영역에서 잠재적인 수축 결함이 나타남 (그림 9, 그림 10).
- AnyCasting의 모듈식 방법을 사용하여 수축 결함 영역을 식별함.
- 연구에서는 수축 기공을 완화하기 위해 금형 온도 제어 및 상세 냉각 설계 구현을 제안함.
제시된 데이터 분석:
- 그림 3: 모든 세 가지 케이스(Case 1, 2, 3)의 용융 금속 충전 과정을 다양한 비율(25%, 45%, 60%, 80%, 93%, 96%)로 보여줍니다. Case 2와 3은 Case 1에 비해 더 균일한 충전을 나타냅니다.
- 그림 4: Case 1의 93% 및 96% 충전 단계에서 불균형 유동 및 예상되는 고립된 공기 기공 영역을 강조합니다.
- 그림 5: Case 1과 Case 2의 96% 충전 거동을 비교하여 게이팅 시스템 재설계로 인해 Case 2에서 유동 균형이 개선되고 고립된 영역이 감소했음을 보여줍니다.
- 그림 6: Case 2의 45% 및 60% 충전 단계에서 비스킷의 와류 형성을 보여주며 잠재적인 역류 문제를 나타냅니다.
- 그림 7: Case 2와 Case 3 간의 게이트 시스템 설계 차이점을 보여주며, 역류를 최소화하기 위해 Case 3의 비스킷에 추가된 둥근 특징을 강조합니다.
- 그림 8: Case 3의 45% 및 60% 충전 단계에서 개선된 용융 금속 흐름을 보여주며, 설계 수정으로 인해 와류 및 역류가 최소화되었음을 입증합니다.
- 그림 9: Case 3의 다양한 응고 비율(5%, 15%, 30%, 40%, 50%, 65%)에 대한 응고 시뮬레이션 결과를 제시하며, 응고 고립 영역을 나타냅니다.
- 그림 10: AnyCasting의 모듈식 방법을 사용하여 Case 3의 65% 응고에서 예상되는 수축 결함 영역을 자세히 보여줍니다.
- 그림 11: Case 3의 최종 주조 레이아웃 시뮬레이션 결과(고정측 및 이동측)를 다양한 충전 비율(30%, 45%, 75%, 85%, 95%)로 표시하며, 최소화된 와류 흐름과 잠재적인 미세기공을 보여줍니다.
그림 목록:
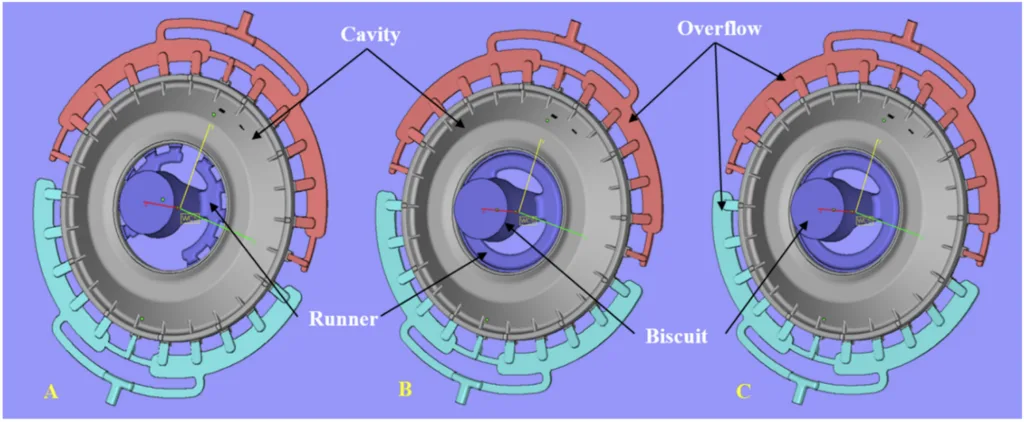
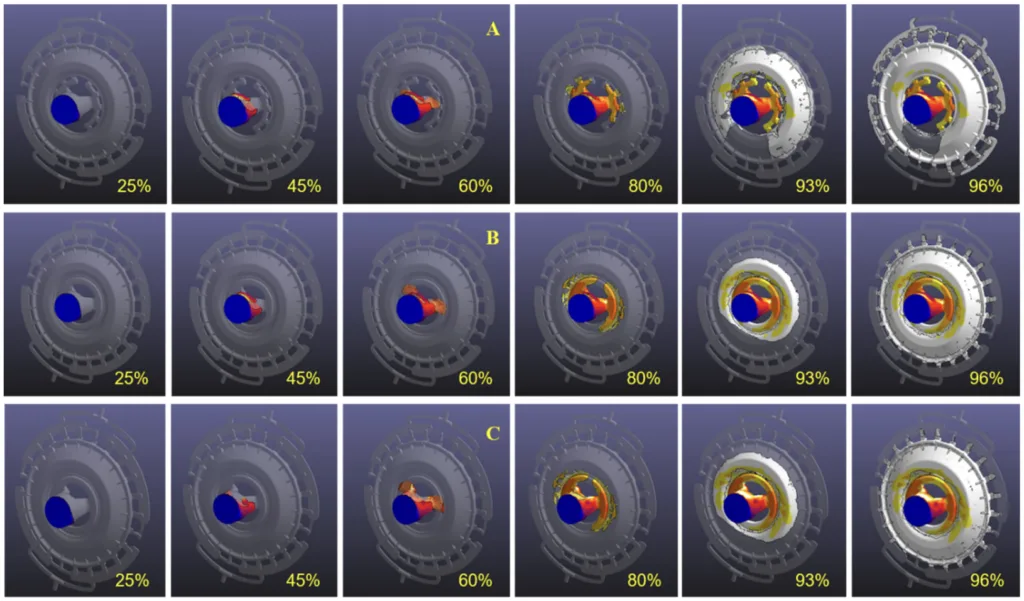
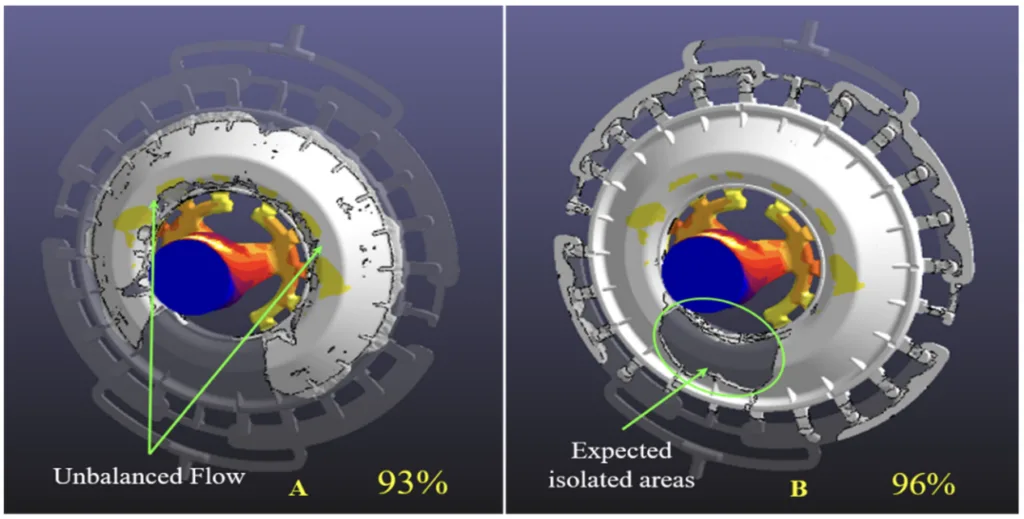
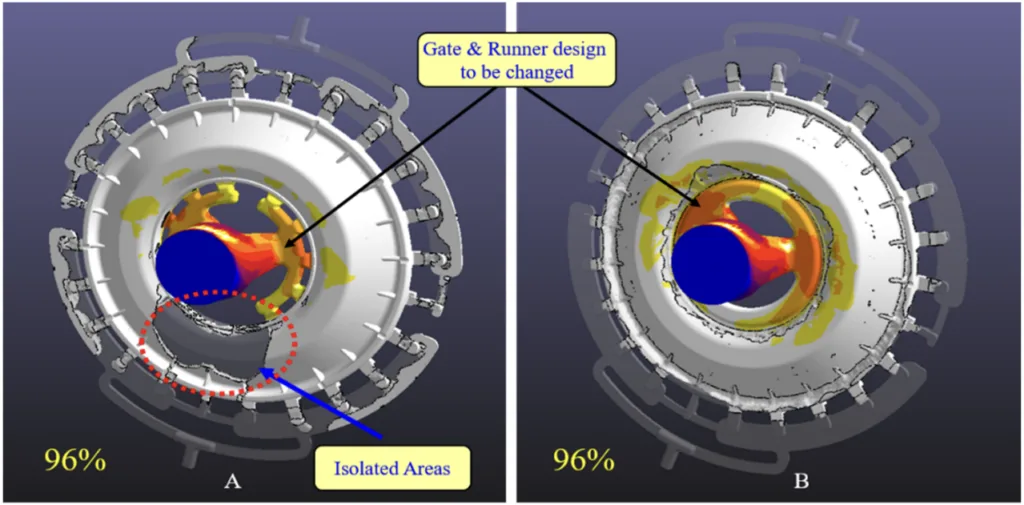
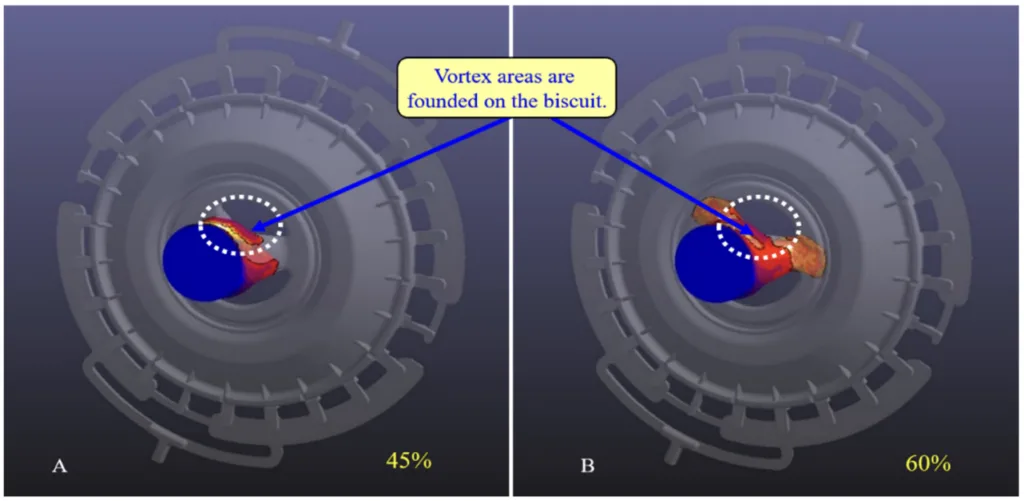
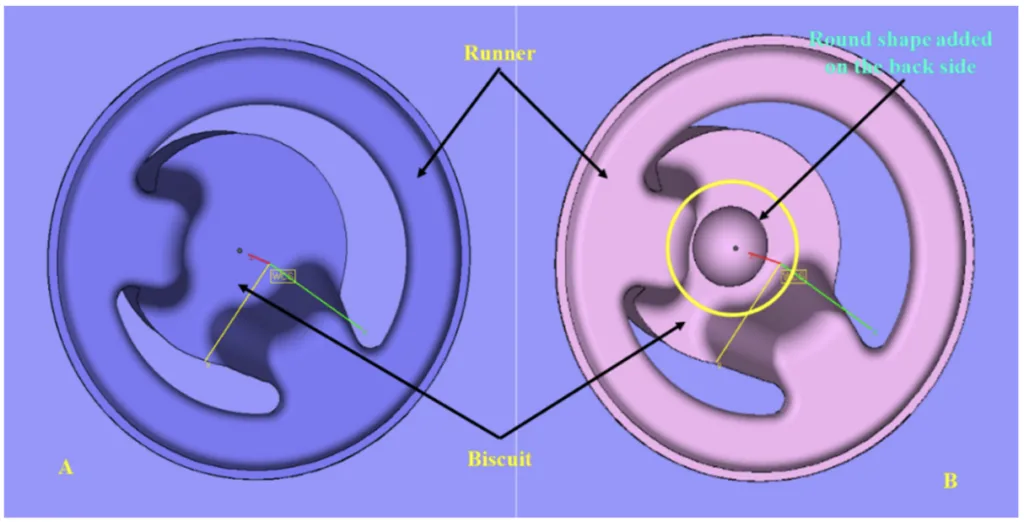
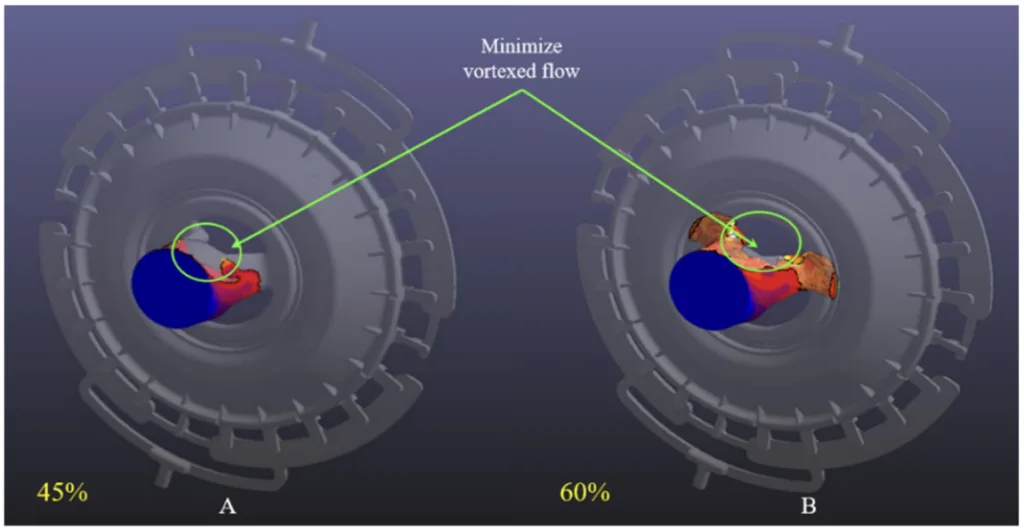
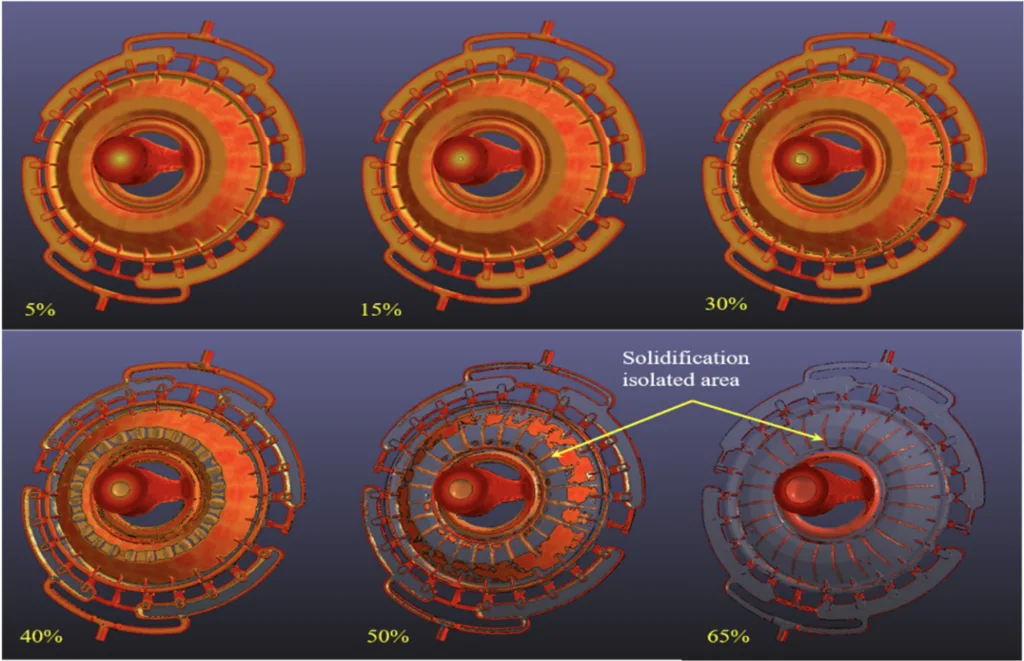
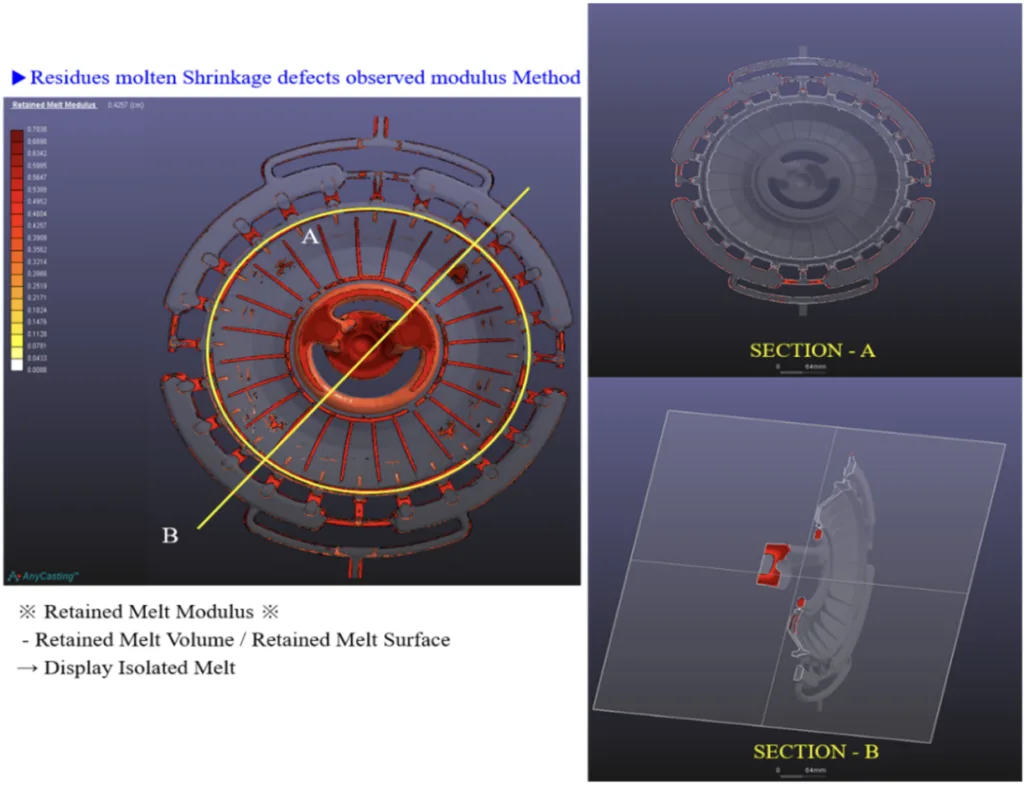
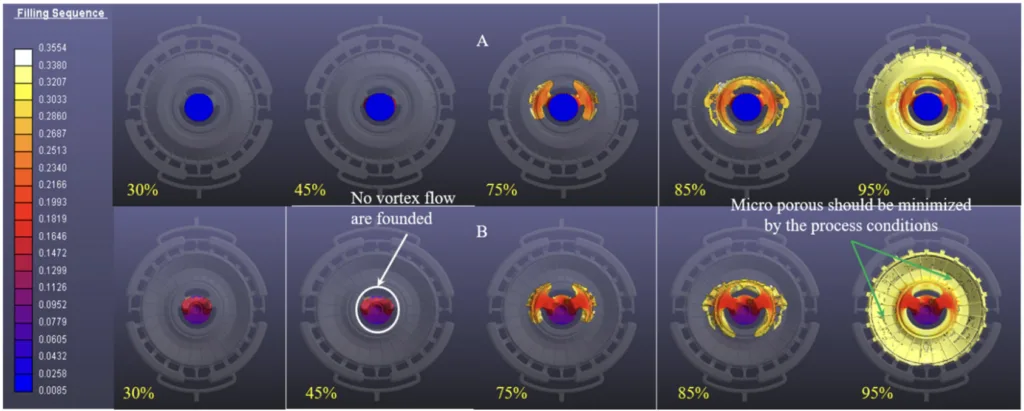
- 그림 1. CAE 시뮬레이션 흐름도. (Figure 1. Flow Chart of CAE simulation.)
- 그림 2. 쿠킹 그릴 주조 모델: (A) Case 1; (B) Case 2; (C) Case 3. (Figure 2. Casting model of cooking grill: (A) Case 1; (B) Case 2; (C) Case 3.)
- 그림 3. 용융 금속 충전 과정 시뮬레이션 결과: (A) Case 1; (B) Case 2; (C) Case 3. (Figure 3. Simulation results of the melt filling process: (A) Case 1; (B) Case 2; (C) Case 3.)
- 그림 4. Case 1의 용융 금속 흐름 시뮬레이션 결과: (A) 93% 충전; (B) 96% 충전. (Figure 4. Simulation results of the melt flow for Case 1: (A) 93% filling; (B) 96% filling.)
- 그림 5. 용융 금속 흐름 시뮬레이션 결과: (A) Case 1의 96% 충전; (B) Case 2의 96% 충전. (Figure 5. Simulation results of the melt flow: (A) 96% filling of case 1; (B) 96% filling of case 2.)
- 그림 6. Case 2의 용융 금속 흐름 시뮬레이션 결과: (A) 45% 충전; (B) 60% 충전. (Figure 6. Simulation results of the melt flow for case 2: (A) 45% filling; (B) 60% filling.)
- 그림 7. 게이트 시스템: (A) Case 2; (B) Case 3. (Figure 7. Gate system: (A) case 2; (B) case 3.)
- 그림 8. Case 3의 용융 금속 흐름 시뮬레이션 결과: (A) 45% 충전; (B) 60% 충전. (Figure 8. Simulation results of the melt flow for Case 3: (A) 45% filling; (B) 60% filling.)
- 그림 9. Case 3의 응고 시뮬레이션 결과. (Figure 9. Simulation results of the solidification for case 3.)
- 그림 10. Case 3의 65% 응고에서 예상되는 수축 결함 영역. (Figure 10. Expected shrinkage defect area for Case 3 at 65% solidification.)
- 그림 11. 최종 주조 레이아웃의 시뮬레이션 결과: (A) 고정측; (B) 이동측. (Figure 11. Simulation results with the final casting layout: (A) Fixed side; (B) Moving side.)
7. 결론:
주요 연구 결과 요약:
본 연구는 CAE 시뮬레이션이 HPDC 공정의 주조 레이아웃 최적화에 효과적이라는 결론을 내립니다. 유동 해석은 게이팅 시스템의 반복적인 설계 수정을 통해 불균형 유동, 공기 기공 및 역류 문제를 식별하고 해결했습니다. 링 게이트와 수정된 비스킷 설계를 특징으로 하는 Case 3은 Case 1과 Case 2에 비해 가장 균일한 용융 금속 흐름을 보였고 역류 및 공기 기공을 최소화했습니다. Case 3에 대한 응고 해석 결과 두꺼운 부분에서 잠재적인 수축 결함이 나타났으며, 이는 최적화된 냉각 전략의 필요성을 강조합니다.
연구의 학문적 의의:
본 연구는 다이캐스팅 레이아웃 설계에 CAE 시뮬레이션을 실제로 적용하여 잠재적인 주조 결함을 예측하고 완화하는 능력을 입증합니다. 수치 해석을 사용하여 복잡한 형상에 대한 게이팅 시스템을 최적화하는 체계적인 접근 방식을 보여줌으로써 순전히 경험 기반 설계 방법에서 벗어나 지식 체계에 기여합니다. 본 연구는 고품질 다이캐스팅 부품을 달성하기 위해 설계 단계에서 유동 및 응고 시뮬레이션을 통합하는 것의 중요성을 강조합니다.
실용적 의미:
본 연구 결과는 가정용 기기 및 유사 부품의 게이팅 시스템을 설계하는 다이캐스팅 엔지니어에게 실용적인 지침을 제공합니다. AnyCasting과 같은 CAE 시뮬레이션 도구를 활용하면 금형 개발 과정에서 시행착오를 크게 줄여 설계 주기 단축 및 생산 비용 절감으로 이어질 수 있습니다. 최적화된 주조 레이아웃(Case 3)은 유사한 쿠킹 그릴 설계에 대한 템플릿을 제공하며, 개선된 냉각 전략의 필요성을 확인한 것은 다이캐스팅 금형 설계에서 포괄적인 열 관리의 중요성을 강조합니다.
연구의 한계 및 향후 연구 분야:
본 연구는 수치 시뮬레이션에 국한되어 있으며 시뮬레이션 결과에 대한 실험적 검증은 포함하지 않습니다. 향후 연구에서는 Case 3의 예측된 주조 성능을 검증하고 주조 공정 매개변수를 더욱 개선하기 위해 물리적 실험을 수행하는 데 초점을 맞춰야 합니다. 식별된 수축 결함 영역을 해결하고 보다 균일한 응고를 달성하기 위해 최적화된 냉각 채널 설계와 주조 레이아웃과의 통합에 대한 추가 연구가 권장됩니다. 또한, CAE 시뮬레이션을 사용하여 공정 매개변수 변화가 주조 품질에 미치는 영향을 탐구하는 것은 본 연구의 가치 있는 확장이 될 것입니다.
8. 참고 문헌:
- [1] Hu, B.; Tong, K.; Niu, X.; Pinwill, I. Design and optimisation of runner and gating systems for the die casting of thin-walled magnesium telecommunication parts through numerical simulation. J. Mater. Process. Technol. 2000, 105, 128-133. [CrossRef]
- [2] Park, J.-Y.; Kim, E.-S.; Park, Y.-H.; Park, I.-M. Optimization of Casting design for automobile transmission gear housing by 3D filling and solidification simulation in local squeeze diecasting process. Korean J. Mater. Res. 2006, 16, 668-675. [CrossRef]
- [3] Kim, E.; Park, J.; Jeon, E.; Park, I. Current state and technology trend of domestic diecasting industry for automotive parts. J. Korea Foundry Soc. 2007, 27, 13–19.
- [4] Jeong, B.-G.; Kwon, H.-K. A case study on developing automotive part (housing) by filling and solidification analysis. J. Soc. Korea Ind. Syst. Eng. 2015, 38, 44-51. [CrossRef]
- [5] Cho, G.-S.; Choe, K.-H. Study on the rationalization of aluminium casting alloys for automobiles components. J. Korea Foundry Soc. 2011, 31, 319-325. [CrossRef]
- [6] Jeong, W.; Yoon, H.; Hong, S.; Park, I. Optimal gating system design of escalator step die casting part by using Taguchi method. J. Korea Foundry Soc. 2000, 20, 97-103.
- [7] Fu, M.; Yong, M. Simulation-enabled casting product defect prediction in die casting process. Int. J. Prod. Res. 2009, 47, 5203-5216. [CrossRef]
- [8] Jeon, E.; Park, J.; Park, I. Application trend of aluminum castings in automotive component. J. Korea Foundry Soc. 2007, 27, 20-23.
- [9] Lee, D.; Kang, C.; Lee, S. Prediction defect of automotive components by filling and solidification analysis. J. Korea Foundry Soc. 2000, 20, 159-166.
- [10] Kim, Y.; Choi, S.; Cho, J.; Jeong, C.; Kang, C. Optimization of thin-walled aluminum die casting design by solidification simulation. J. Korea Foundry Soc. 2008, 28, 190–194.
- [11] Jin, C.-K.; Kang, C.-G. Fabrication process of aluminum bipolar plate for fuel cell using vacuum die casting. J. Korea Foundry Soc. 2011, 31, 71-78. [CrossRef]
- [12] Gramegna, N.; Della Corte, E.; Poles, S. Manufacturing process simulation for product design chain optimization. Mater. Manuf. Process. 2011, 26, 527-533. [CrossRef]
- [13] Park, J.; Kim, E.; Park, I. Die casting process design of automobile gear housing by metal flow and solidification simulation. J. Korea Foundry Soc. 2004, 24, 347-355.
- [14] Zhang, L.; Li, L.; Zhu, B. Simulation study on the LPDC process for thin-walled aluminum alloy casting. Mater. Manuf. Process. 2009, 24, 1349-1353. [CrossRef]
- [15] Wu, S.; Fuh, J.; Lee, K. Semi-automated parametric design of gating systems for die-casting die. Comput. Ind. Eng. 2007, 53, 222-232. [CrossRef]
- [16] AnyCasting. User Manual Version 6.5; AnyCasting Software: Seoul, Korea, 2019; pp. 55-62.
- [17] Kwon, H.; Kwon, H. Computer aided engineering (CAE) simulation for the design optimization of gate system on high pressure die casting (HPDC) process. Robot. Comput. Integr. Manuf. 2019, 55, 147–153. [CrossRef]
- [18] Kim, T.G.; Choi, J.K.; Hong, J.P.; Lee, Z.H. Reduction of computing time through FDM using implicit method and latent heat treatment in solidification analysis. J. Korea Foundry Soc. 1993, 13, 323-332.
- [19] Xun, S.; Junqing, W.; Hwang, H.Y.; Choi, J.K. Numerical simulation of mold filling process of castings by using of predictor-two step Corrector-VOF. J. Korea Foundry Soc. 2002, 22, 299-303.
- [20] Lee, Y.C.; Choi, J.K.; Hong, C.P. Development of an Integrated Simulation System and its Application to Casting Design. J. Korea Foundry Soc. 1997, 17, 552–559.
- [21] Kwon, H.Y.; Yoon, T.H.; Lee, B.J. Computer simulation on the High-Pressure Die Casting (HDPC) process by filling and solidification analysis. Int. J. Appl. Eng. Res. 2015, 10, 142–145. [CrossRef]
- [22] Jin, C.-K.; Jang, C.-H.; Kang, C.-G. Vacuum die casting mold design of fuel cell bipolar plate using die filling simulation and experimental verification. J. Korea Foundry Soc. 2012, 32, 65–74. [CrossRef]
- [23] Hosseini, S.M.; Utlu, Z. Design optimization of clutch housing mold by fluid flow and solidification simulation. J. Mech. Sci. Technol. 2016, 30, 2731-2742. [CrossRef]
9. 저작권:
- 본 자료는 "[Hong-Kyu Kwon]"의 논문: "[Layout Design and Die Casting Using CAE Simulation for Household Appliances]"을 기반으로 합니다.
- 논문 출처: https://doi.org/10.3390/app112110128
본 자료는 상기 논문을 요약한 것으로, 상업적 목적으로 무단 사용하는 것을 금지합니다.
Copyright © 2025 CASTMAN. All rights reserved.