본 논문 요약은 ['Università di Bologna'에서 발행한 'DESIGNING AN INNOVATIVE MODULAR PLATFORM FOR SPORTS CARS USING THE GENERATIVE DESIGN METHOD'] 논문을 기반으로 작성되었습니다.
1. 개요:
- 제목: 혁신적인 스포츠카 모듈형 플랫폼의 생성적 디자인 방법론을 이용한 설계 (DESIGNING AN INNOVATIVE MODULAR PLATFORM FOR SPORTS CARS USING THE GENERATIVE DESIGN METHOD)
- 저자: 메르베 살리 (Merve Sali)
- 발행 연도: 2024년
- 발행 학술지/학회: 볼로냐 대학교 (Università di Bologna) 기계 및 첨단 공학 박사 과정 (DOTTORATO DI RICERCA IN MECCANICA E SCIENZE AVANZATE DELL'INGEGNERIA)
- 키워드: 제공된 문서에 명시적으로 나열되어 있지는 않지만, 제목과 초록에서 추론할 수 있는 키워드는 다음과 같습니다: 모듈형 플랫폼 (Modular Platform), 스포츠카 (Sports Cars), 생성적 디자인 방법 (Generative Design Method), 자동차 섀시 (Automotive Chassis), 경량 설계 (Lightweight Design), 애자일 방법 (Agile Method), 스크럼 (Scrum).
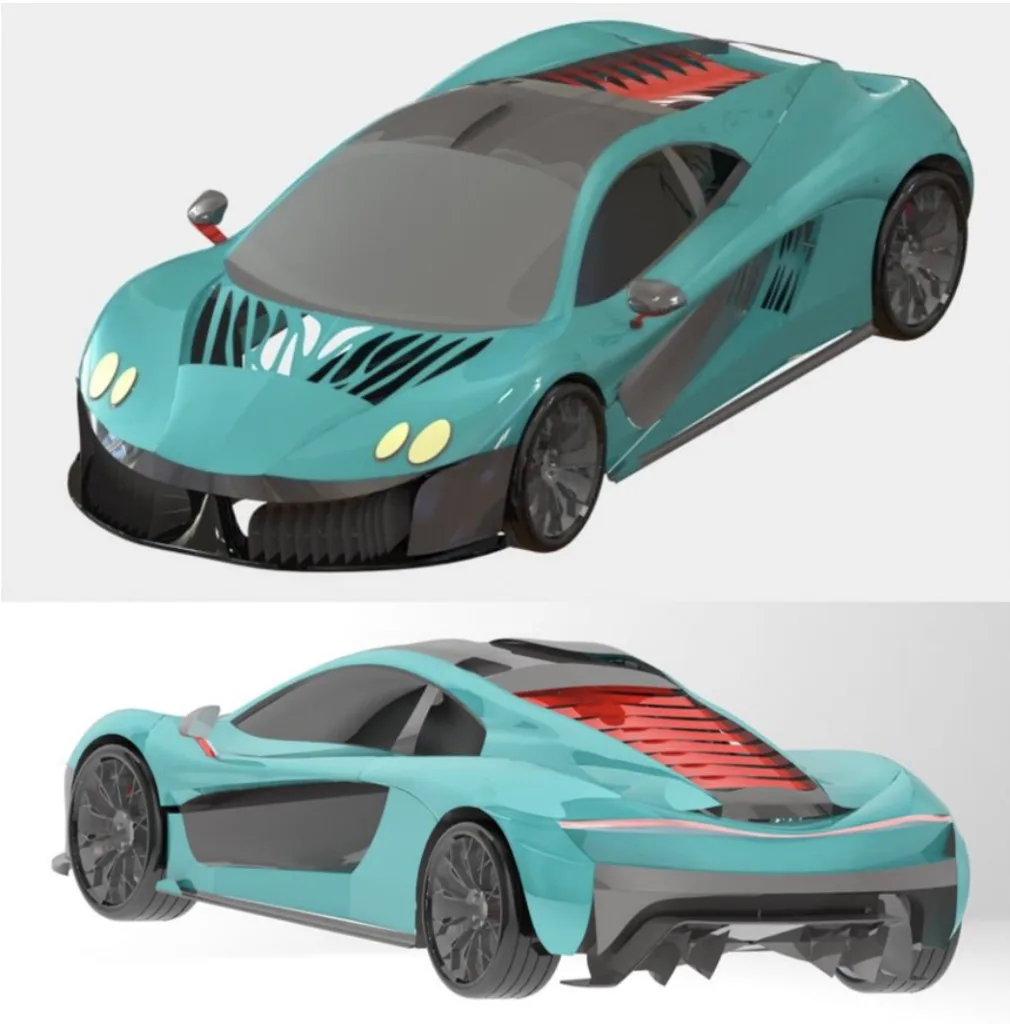
2. 초록
전통적인 방법은 각 차량 유형에 맞게 섀시 부품을 맞춤 제작하여 유연성과 효율성이 부족합니다. 현재 모듈형 플랫폼의 개념은 서로 다른 모델에서 부품을 재사용하여 생산 비용을 절감하고 적응성을 향상시킵니다. 그러나 현재 상황에서 이러한 솔루션은 스포츠카 부문에서는 일반적이지 않습니다.
본 연구는 스포츠카 맥락에서 모듈형 플랫폼이 제기하는 과제와 기회를 탐구하고, 주행 역학, 디자인 미학 및 미래 혁신에 대한 잠재적 영향을 강조합니다. 본 프로젝트는 표준화된 디자인 섹션을 유지하면서 다양성을 제공하고, 유연성 외에도 부품의 상호 교환성을 강조하며, 최첨단 디자인 방법을 사용하는 모듈형 플랫폼 접근 방식에 중점을 둡니다.
본 연구는 생성적 디자인 방법을 사용하여 경량 및 고강성 설계를 목표로 하는 반복적인 스프린트를 통해 다양한 드라이브트레인 및 파워트레인 구성에 적합한 모듈형 플랫폼을 만드는 것을 목표로 합니다. 디자인 결과 개선 외에도 기존 워크플로우(IDeS) 내에서 생성적 디자인 방법의 단계를 적용하고, 애자일 방법론 변형인 스크럼과의 협력을 통해 프로젝트 개발에 중요한 결과 필터링을 확립함으로써 창의성을 향상시키기 위한 노력이 이루어졌습니다.
또한 생성적 디자인 애플리케이션을 통해 얻은 새로운 부품으로 생성된 대체 모듈형 플랫폼에 적용되었습니다. 얻어진 결과는 모델의 기계적 특성 측면에서 평가되었습니다. 이러한 새로운 부품은 기하학적으로 더 효율적일 뿐만 아니라 다른 재료를 사용하더라도 동일한 기계적 결과를 산출할 수 있습니다.
시뮬레이션의 수치적 결과는 생성된 부품(파트 1, 파트 3, 파트 4)과 초기 부품으로 생성된 최종 어셈블리에 대해 비교됩니다. 특히, 생성적 디자인 방법을 사용함으로써 파트 3(결과 7)의 부품에 대해 강철 합금 대신 알루미늄 합금을 사용하여 동등한 강도 값을 달성할 수 있음이 입증되었습니다.
비틀림 및 굽힘 강성 테스트는 생성적 디자인 프로세스 전후에 각 모델에 대해 수행되었습니다. 생성하기로 결정된 부품은 후방-중간 및 전방 모듈형 플랫폼 레이아웃에 대한 충돌 테스트로 결정되었습니다.
결과를 비교한 결과 응력 분포가 유사하다는 것을 발견했으며, 이는 우리가 생성한 부품이 모양, 무게 및 기계적 특성과 같은 새로운 디자인에 충분하다는 것을 의미합니다.
3. 연구 배경:
연구 주제 배경:
기존의 자동차 섀시 설계 방식은 각 차량 유형에 맞춰 부품을 맞춤 제작하기 때문에 유연성과 효율성이 떨어집니다. 현재의 모듈형 플랫폼은 여러 모델에서 부품을 재사용하여 생산 비용을 절감하고 적응성을 높일 수 있습니다. 그러나 이러한 솔루션은 스포츠카 부문에서는 흔하지 않습니다. 본 연구는 스포츠카 분야에서 모듈형 플랫폼이 가져올 수 있는 도전 과제와 기회를 탐구하며, 주행 역학, 디자인 미학, 미래 혁신에 미치는 잠재적 영향을 강조합니다. 본 프로젝트는 스포츠카용 모듈형 플랫폼을 개발하는 것을 목표로 하며, 최첨단 설계 방법을 사용하여 다양성, 표준화된 설계, 부품 호환성 및 유연성을 강조합니다.
기존 연구 현황:
기존 연구에서는 자동차 산업에서 모듈형 플랫폼의 이점, 즉 비용 절감 및 유연성 향상을 인정하고 있습니다 (Florea et al., 2016; Lampón et al., 2015). 문헌 검토에서는 미쓰비시가 개척한 공유 플랫폼 (Cusumano & Nobeoka, 1998) 부터 PSA 그룹의 표준화 노력 (Holweg, 2008; Patchong et al., 2003) 에 이르기까지 플랫폼 전략의 진화를 강조합니다. 또한, 경량 자동차 부품을 위한 생성적 디자인 및 적층 제조의 적용 (Junk & Rothe, 2022; Fenoon et al., 2021; Dalpadulo et al., 2020) 을 탐구하여 섀시 개발에서 혁신적인 설계 및 재료 활용 추세를 보여줍니다.
연구의 필요성:
본 연구는 스포츠카 부문에서 모듈형 플랫폼의 잠재적 이점에도 불구하고 적용이 제한적이기 때문에 필요합니다. 자동차 제조의 유연성, 효율성 및 적응성에 대한 요구 증가와 경량 설계 및 지속 가능한 관행의 필요성이 결합되어 모듈형 스포츠카 플랫폼을 위한 생성적 디자인과 같은 혁신적인 접근 방식을 모색해야 합니다. 또한 기후 변화에 대처하고 CO2 배출량을 줄여야 할 필요성 (European Parliament and the Council of the European Union, 2019) 은 자동차 산업을 모듈형 및 지속 가능한 솔루션으로 이끌고 있습니다.
4. 연구 목적 및 연구 질문:
연구 목적:
본 연구는 생성적 디자인 방법을 사용하여 경량 및 고강성 설계를 목표로 하는 반복적인 스프린트를 통해 다양한 드라이브트레인 및 파워트레인 구성에 적합한 모듈형 플랫폼을 만드는 것을 목표로 합니다. 디자인 결과 개선 외에도 기존 워크플로우(IDeS) 내에서 생성적 디자인 방법의 단계를 적용하고, 애자일 방법론 변형인 스크럼과의 협력을 통해 프로젝트 개발에 중요한 결과 필터링을 확립함으로써 창의성을 향상시키기 위한 노력이 이루어졌습니다.
핵심 연구:
- 다양한 드라이브트레인 및 파워트레인 구성에 적응 가능한 스포츠카용 모듈형 플랫폼 제작.
- 경량 및 고강성 설계를 달성하기 위한 생성적 디자인 방법 적용.
- 산업 디자인 구조 (Industrial Design Structure, IDeS) 워크플로우 내 생성적 디자인 통합.
- 생성적 디자인 결과물을 관리하고 필터링하기 위한 스크럼 방법론 구현.
- 모듈형 플랫폼의 기계적 특성 및 성능 평가.
연구 가설:
본 논문에는 연구 가설이 명시적으로 언급되어 있지 않습니다. 그러나 연구 목적 및 핵심 연구 질문을 바탕으로 암묵적인 가설은 다음과 같습니다:
- 생성적 디자인 방법은 모듈형 스포츠카 플랫폼을 위한 기하학적으로 효율적이고 경량인 부품을 만들 수 있습니다.
- 생성적 디자인으로 설계된 모듈형 플랫폼은 기존 방법으로 설계된 플랫폼에 비해 동등하거나 향상된 기계적 특성을 달성할 수 있습니다.
- 스크럼 방법론을 IDeS 워크플로우 및 생성적 디자인과 통합하면 모듈형 플랫폼의 설계 프로세스의 효율성과 창의성을 향상시킬 수 있습니다.
- 생성적으로 설계된 부품에 알루미늄 합금을 사용하면 무게를 줄이면서 강철 합금 부품과 동등한 강도를 얻을 수 있습니다.
5. 연구 방법론
연구 설계:
본 연구는 생성적 디자인을 사용하여 혁신적인 모듈형 플랫폼 개발에 초점을 맞춘 디자인 기반 연구 접근 방식을 채택합니다. 산업 디자인 구조 (IDeS) 워크플로우와 스크럼 방법론 및 생성적 디자인 기술을 통합합니다. 설계 프로세스는 반복적이며, 분석 및 테스트를 기반으로 스프린트 및 적응을 포함합니다.
자료 수집 방법:
자료 수집 방법은 본 요약에서 명시적으로 자세히 설명되어 있지는 않지만 다음과 같이 추론할 수 있습니다:
- 문헌 검토: 모듈형 플랫폼, 생성적 디자인 및 자동차 섀시 설계에 대한 기존 연구를 이해합니다.
- 시장 분석 데이터: 시장 동향, 고객 요구 사항 및 경쟁사 분석을 이해합니다.
- 시뮬레이션 데이터: 기계적 특성을 평가하기 위한 시뮬레이션 (비틀림, 굽힘, 충돌 테스트) 의 수치 결과.
- 전문가 인터뷰: 업계 전문가 프로필 분석 (Figure 3.1 참조).
분석 방법:
- 품질 기능 전개 (Quality Function Deployment, QFD): 고객 요구 사항을 분석하고 설계 파라미터로 변환합니다.
- 의존성/독립성 매트릭스 및 상대적 중요도 매트릭스: 고객 요구 사항의 우선 순위를 정합니다.
- 벤치마킹: 기존 스포츠카 모델을 비교하고 설계 파라미터를 식별합니다.
- 유한 요소 해석 (Finite Element Analysis, FEA): SolidWorks Simulation을 사용하여 기계적 응력 분석 (비틀림 강성, 굽힘 강성, 정면 충돌 분석) 을 수행하고 모듈형 플랫폼 및 생성적으로 설계된 부품의 성능을 평가합니다.
- 비교 분석: 초기 및 생성적으로 설계된 부품, 그리고 다양한 구성 및 재료의 플랫폼의 시뮬레이션 결과를 비교합니다.
연구 대상 및 범위:
- 연구 대상: 스포츠카용 모듈형 플랫폼의 설계 및 분석. 엔진실 (파트 1), 운전석 하부 (파트 3), 전기 모터실 (파트 4) 용 생성적으로 설계된 부품.
- 연구 범위: 모듈형 플랫폼, 특히 섀시 부품의 구조 설계 및 기계적 성능에 중점을 둡니다. 스타일링 및 광범위한 차량 개발 측면도 고려되지만 구조적 및 모듈형 설계 측면이 우선입니다. 재료 범위는 주로 강철 및 알루미늄 합금입니다.
6. 주요 연구 결과:
핵심 연구 결과:
- 생성적 디자인 방법이 모듈형 플랫폼 (파트 1, 파트 3, 파트 4) 용 경량 부품을 성공적으로 만드는 데 적용되었습니다.
- 알루미늄 합금을 사용하여 생성적으로 설계된 부품은 특히 파트 3 (결과 7) 의 경우 상당한 무게 감소와 함께 초기 강철 합금 부품과 동등한 강도 값을 달성했습니다.
- 초기 및 생성적으로 설계된 모듈형 플랫폼에 대해 비틀림 및 굽힘 강성 테스트를 수행하고 비교하여 새로운 설계의 타당성을 입증했습니다.
- 생성적 디자인 방법 및 IDeS 워크플로우와 통합된 새로운 스크럼 워크플로우 모델이 개발 및 적용되었습니다.
- 모듈형 플랫폼 설계는 다양한 엔진 레이아웃 (후방-중간 및 전방 엔진) 및 파워트레인 구성에 대한 적응성을 허용합니다.
제시된 데이터 분석:
- 비틀림 강성: 초기 및 생성적으로 설계된 플랫폼 모두 비틀림 강성 값이 유사한 범위 내에 있지만, 생성적으로 설계된 후방-중간 엔진 플랫폼 (9179.317 Nm/deg) 이 초기 후방-중간 엔진 플랫폼 (9705.0857 Nm/deg) 보다 약간 낮습니다.
- 굽힘 강성: 굽힘 강성 값도 초기 및 생성적으로 설계된 플랫폼 간에 유사하며, 생성적으로 설계된 후방-중간 플랫폼이 초기 후방-중간 플랫폼 (25786.02 Nm/deg) 보다 약간 낮은 값 (21773.6 Nm/deg) 을 나타냅니다.
- 중량 감소: 생성적 디자인 및 알루미늄 합금 사용으로 부품에서 상당한 중량 감소가 발생했으며 (Table 3.14), 특히 알루미늄 합금 결과 7은 초기 강철 합금 부품에 비해 3.932 kg의 질량을 달성했습니다.
- 응력 분포: 응력 분포 분석 결과 최대 응력 위치는 초기 및 생성적으로 설계된 플랫폼 모두에서 유사하며, 주로 연결 지점 및 하중 집중 영역에서 발생합니다.
그림 목록:
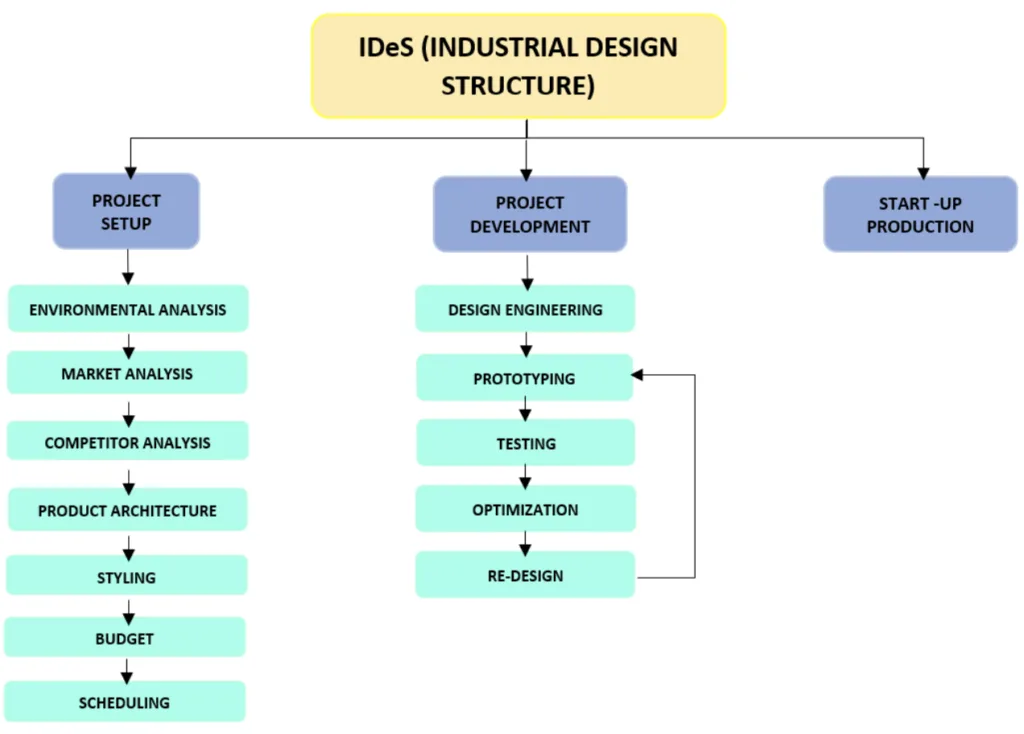
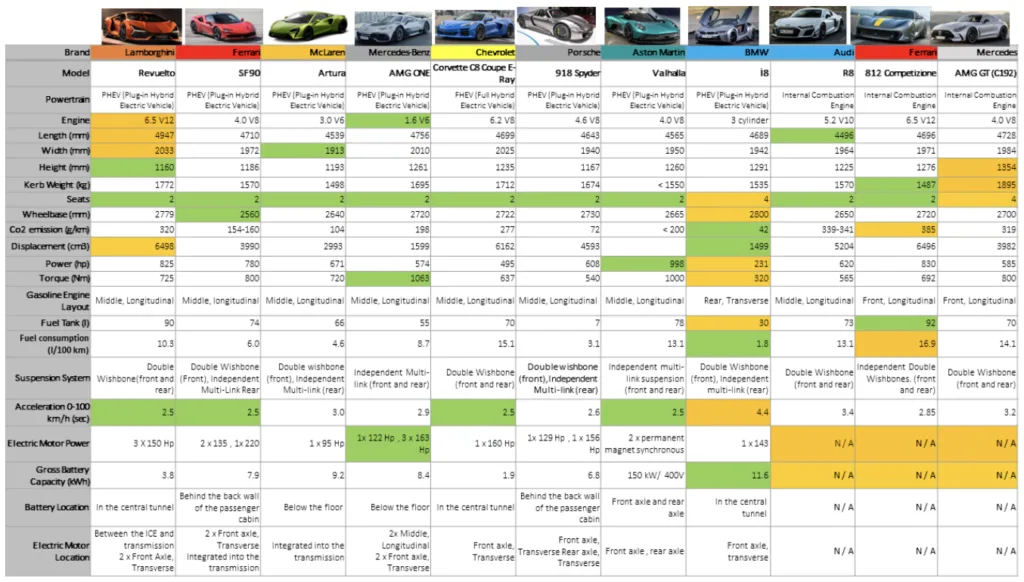
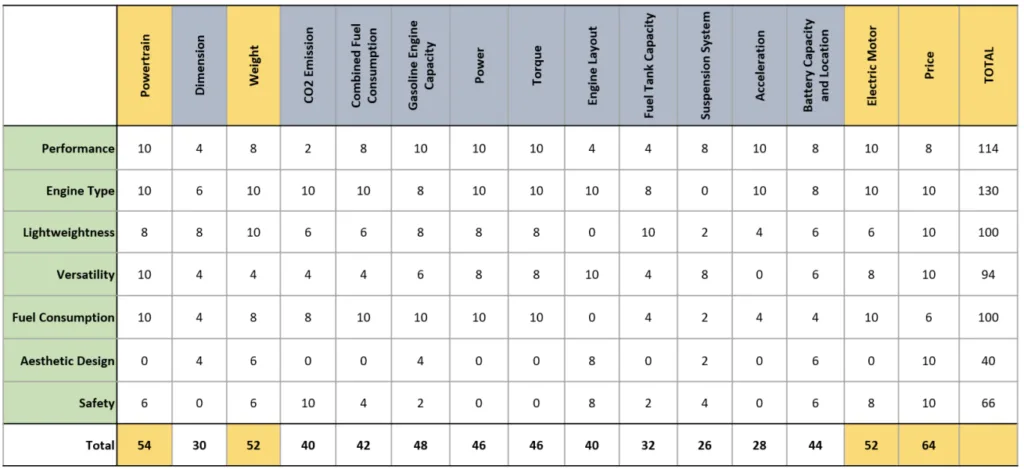
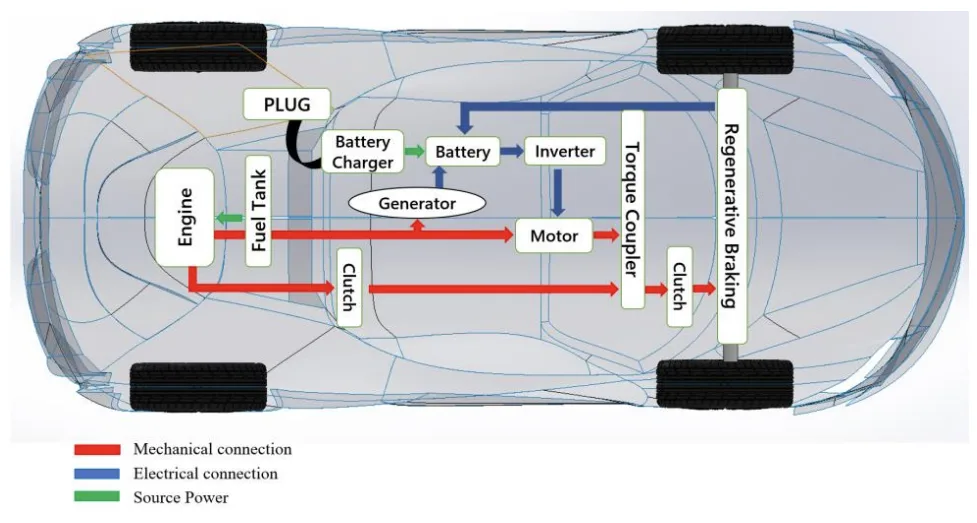
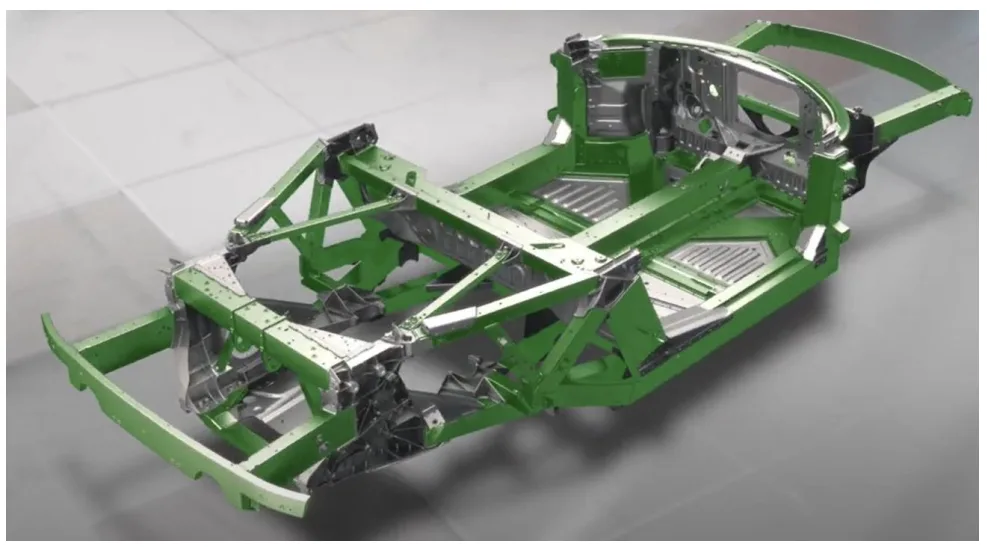
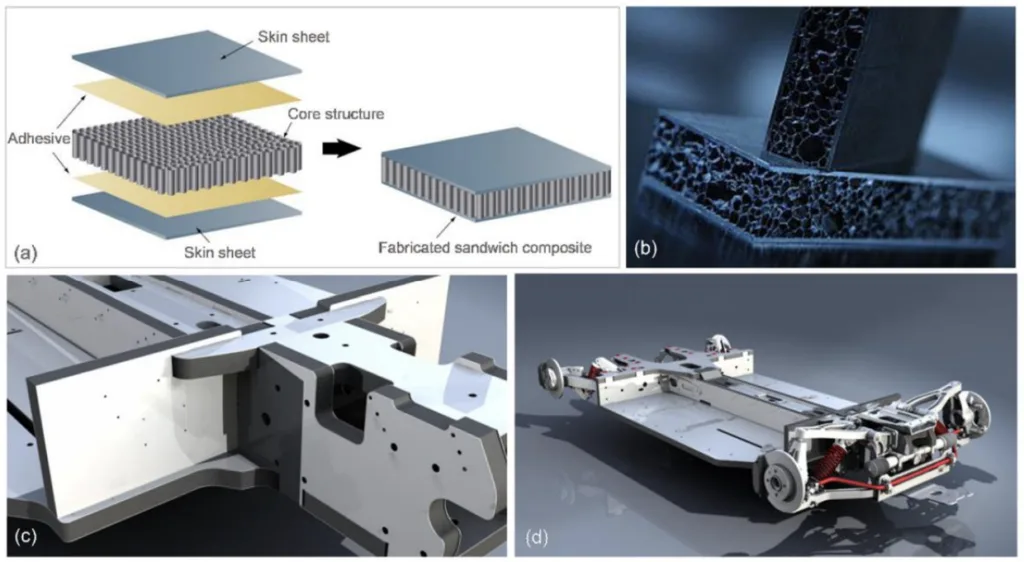
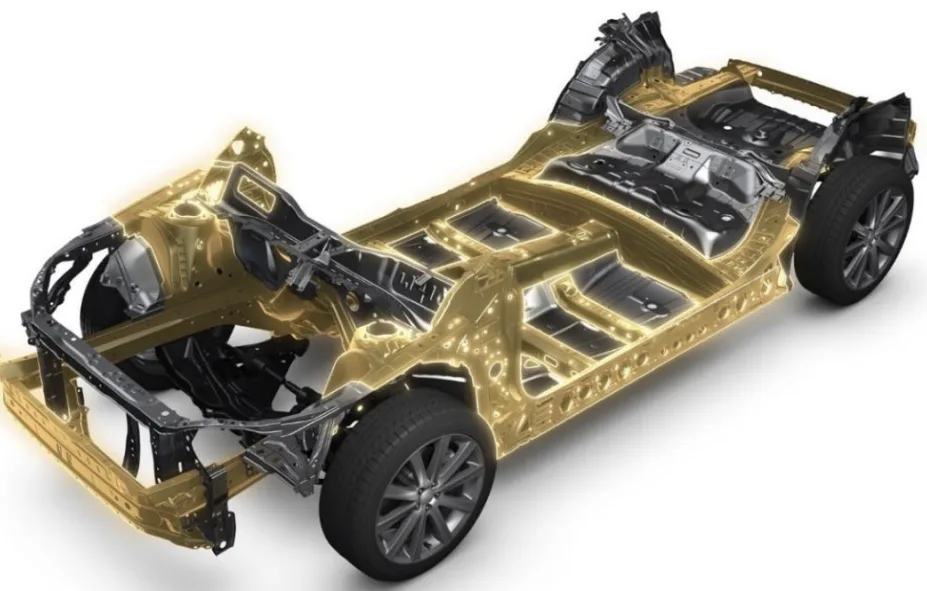
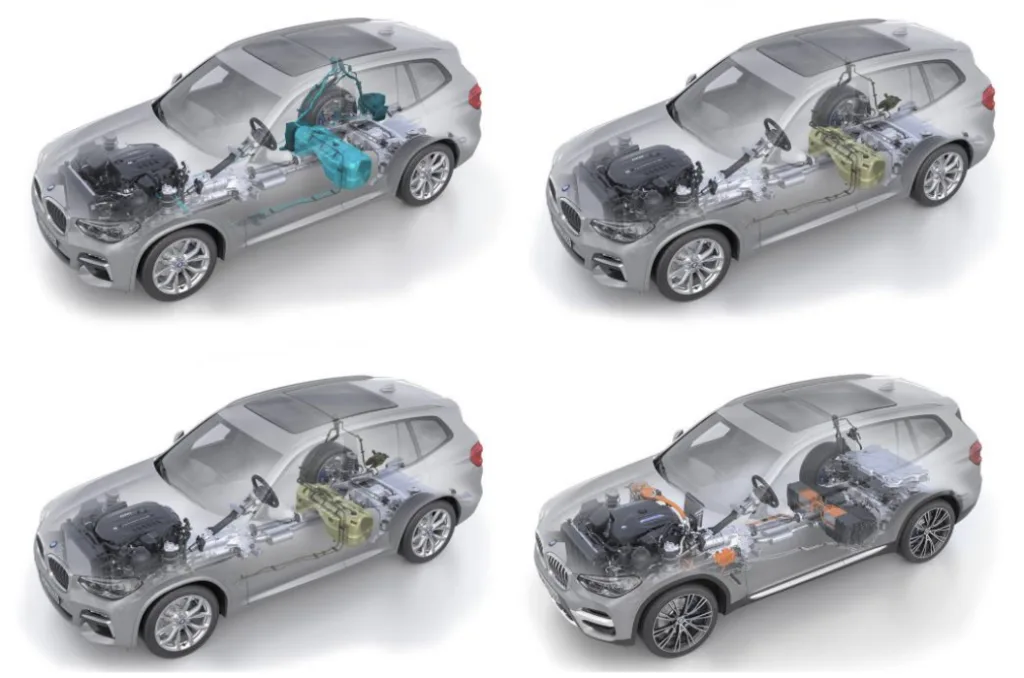
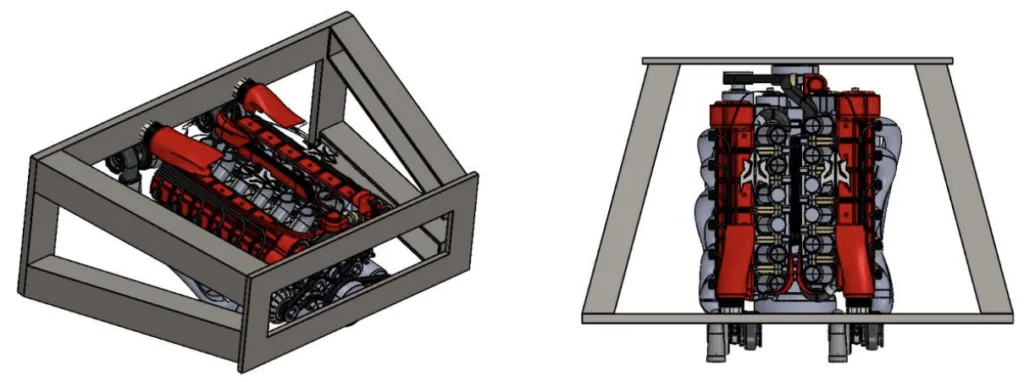
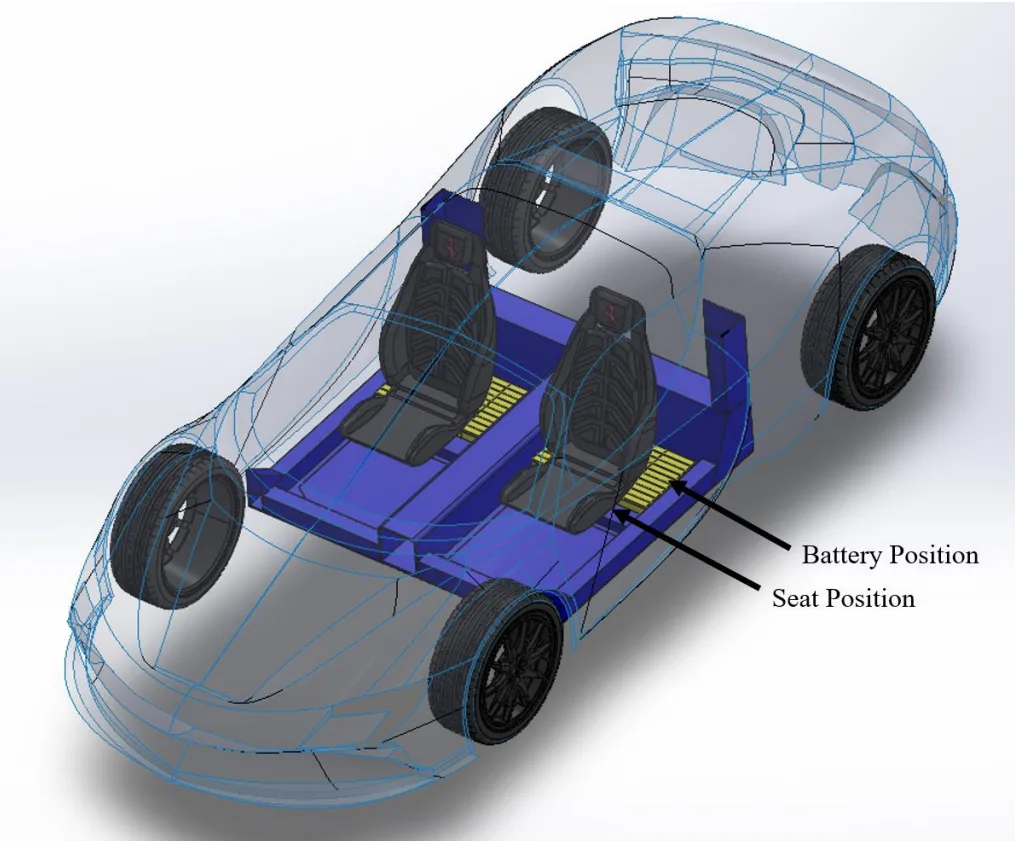
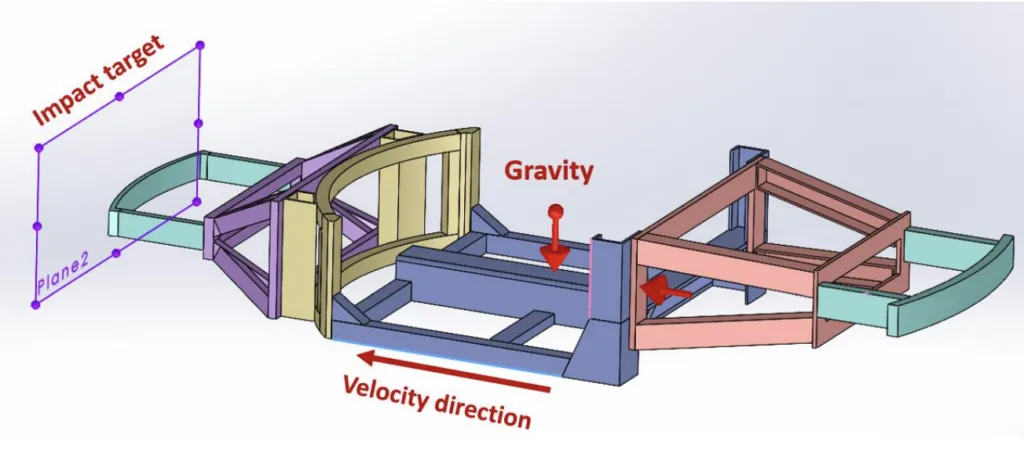
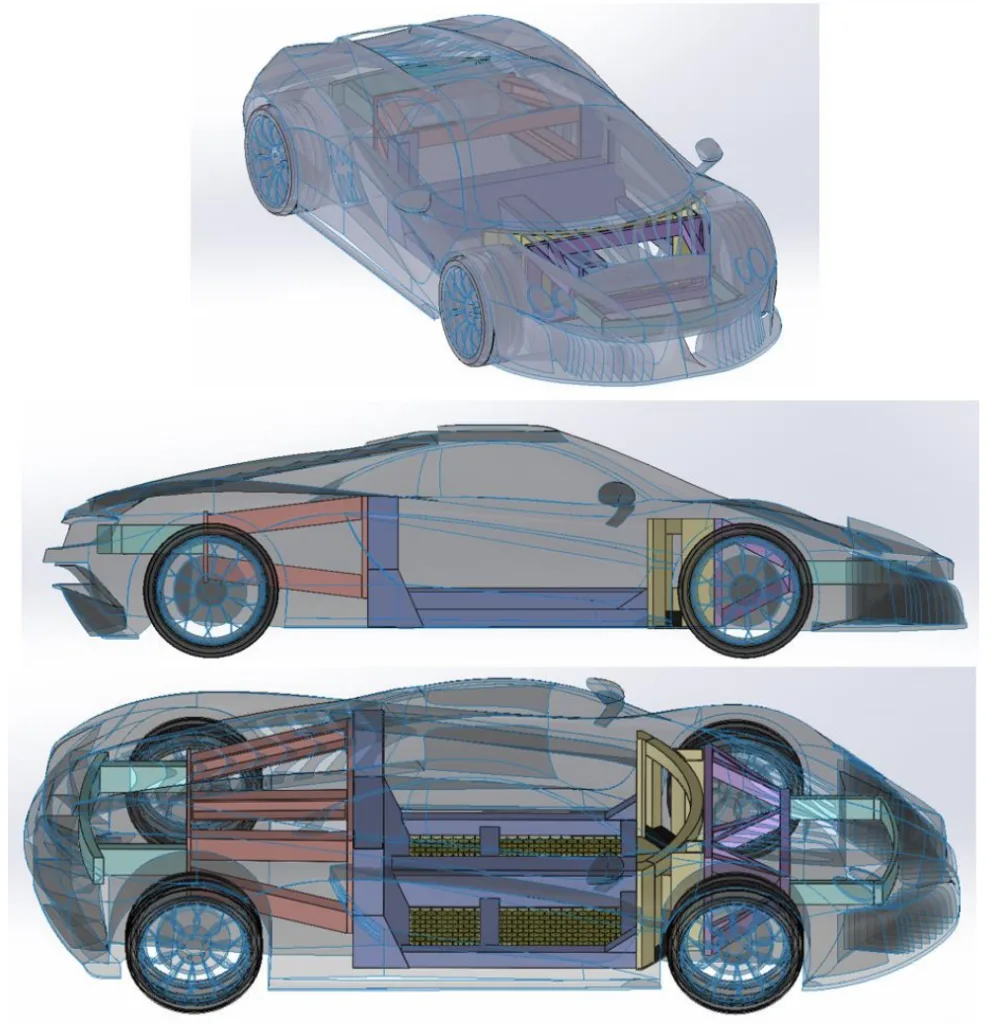
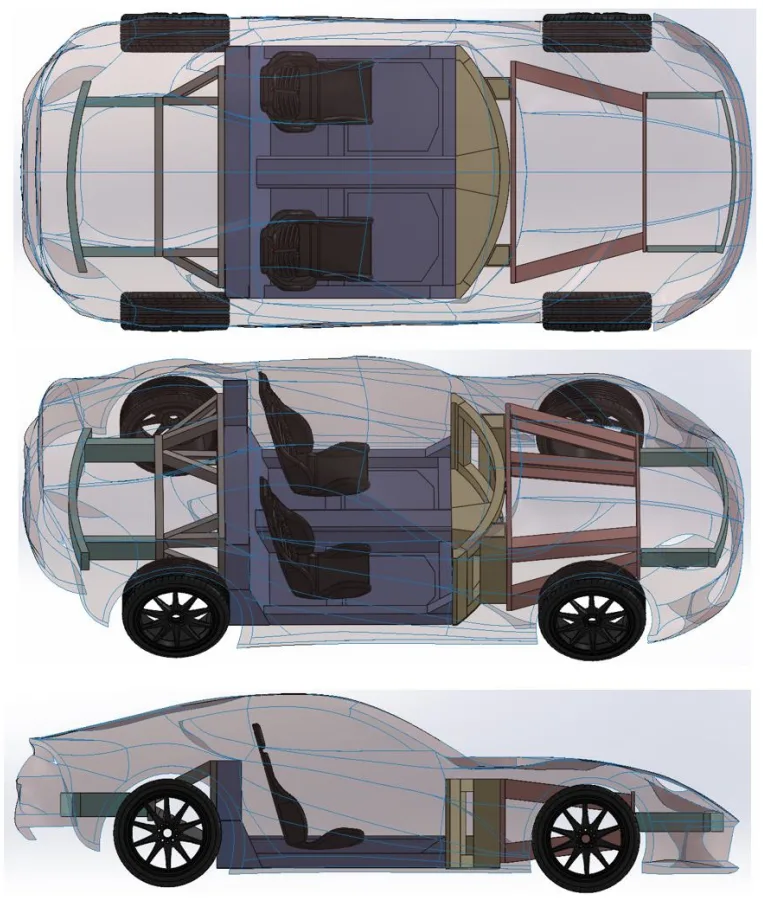
- Figure 1.1: 산업 디자인 구조 (Industrial Design Structure)
- Figure 3.1: 산업 전문가 프로필 분석 (Break-up of the profiles of industry experts)
- Figure 3.2: 아시아 태평양 자동차 섀시 시장 규모, 2019-2030년 (미화 백만 달러) (The market size of the Automotive Chassis in the Asia Pacific, 2019-2030(USD Billion))
- Figure 3.3: 섀시 유형별 글로벌 자동차 섀시 시장 점유율, 2022년 (Global automotive chassis market share by chassis type, 2022)
- Figure 3.4: 품질의 집 템플릿 (House of quality template)
- Figure 3.5: QFD - 6가지 질문 (QFD- Six Questions)
- Figure 3.6: 의존성/독립성 매트릭스 (Dependence / Independence matrix)
- Figure 3.7: 상대적 중요도 매트릭스 (Relative importance matrix)
- Figure 3.8: What-How 매트릭스 (What-How matrix)
- Figure 3.9: 다양한 드라이브트레인 구성의 전방 엔진 레이아웃 (Front Engine layouts with different drivetrain configurations)
- Figure 3.10: 전륜 구동 구성의 전방 엔진 레이아웃 (Front Engine layout with all wheel drive configuration)
- Figure 3.11: 다양한 드라이브트레인 구성의 후방 엔진 레이아웃 (Rear Engine layouts with different drivetrain configurations)
- Figure 3.12: 직렬 HEV 구성 (Series HEV configuration)
- Figure 3.13: 병렬 하이브리드 파워트레인 구성 (Parallel hybrid powertrain configuration)
- Figure 3.14. 직렬-병렬 분할 하이브리드 파워트레인 구성 (Series-Parallel split hybrid powertrain configuration)
- Figure 3.15: 플러그인 직렬 하이브리드 전기 자동차 구성 (Plug-in series hybrid electric vehicle configuration)
- Figure 3.16: 플러그인 병렬 하이브리드 전기 자동차 구성 (Plug-in parallel hybrid electric vehicle configuration)
- Figure 3.17: 플러그인 직렬/병렬 하이브리드 전기 자동차 구성 (Plug-in series / Parallel hybrid electric vehicle configuration)
- Figure 3.18: 생성적 디자인 반복 프로세스 예시 (Generative design iterative process example)
- Figure 3.19: CAD 및 생성된 모듈 사용 모델 예시 (Example of CAD and generated module used model)
- Figure 3.20: 압출을 통해 생산된 부품 (Parts produced through extrusion)
- Figure 3.21: 기존 고강도강의 극한 인장 강도와 총 연신율 간의 관계 (The relationship between ultimate tensile strength and total elongation in traditional high-strength steels)
- Figure 3.22: 자동차 서브프레임에 적용된 샌드위치 구조 복합재 (Sandwich structured composite application in automotive sub-frame)
- Figure 3.23: PSA 공통 모듈형 플랫폼 (PSA Common modular platform)
- Figure 3.24: 폭스바겐 MQB 모듈형 플랫폼 (Volkswagen MQB modular platform)
- Figure 3.25: 토요타 (TNGA) 모듈형 플랫폼 (Toyota (TNGA) modular platform)
- Figure 3.26: 스바루 (SGP) 모듈형 플랫폼 (Subaru (SGP) modular platform)
- Figure 3.27: 르노-닛산 CMF 모듈형 플랫폼 (Renault-Nissan CMF modular platform)
- Figure 3.28: BMW (CLAR) 모듈형 플랫폼 (BMW (CLAR) modular platform)
- Figure 3.29: 모듈형 차량 플랫폼 (Modular vehicle platform)
- Figure 3.30: 파트 1: 엔진실 치수 (Part 1: Engine compartment dimensions)
- Figure 3.31: 종방향 위치의 V6 쉐보레 엔진 (V6 Chevrolet engine for longitudinal position)
- Figure 3.32: 종방향 위치의 V6 재규어 엔진 (V6 Jaguar engine for longitudinal position)
- Figure 3.33: 종방향 위치의 V8 엔진 (V8 Engine for longitudinal position)
- Figure 3.34: 횡방향 위치의 V8 엔진 (V8 Engine for transverse position)
- Figure 3.35: 변속기가 있는 종방향 위치의 V12 엔진 (V12 Engine for longitudinal positioning with transmission)
- Figure 3.36: 종방향 위치의 V12 엔진 (V12 Engine for longitudinal position)
- Figure 3.37: 자동차에 그림으로 나타낸 좌석 배치 치수 파라미터 (Dimensional parameters of seat arrangement illustrated on a car)
- Figure 3.38: 스포츠카 좌석 적합 파라미터 치수 (Sports car seat dimensions of fit parameters)
- Figure 3.39: 모듈형 플랫폼의 배터리 위치 (Battery positioning on modular platform)
- Figure 3.40: 파트 2: 승객 공간 치수 (Part 2: Passenger zone dimensions)
- Figure 3.41: 파트 3: a) 후방-중간 엔진 구성 b) 전방 엔진 구성 어셈블리 (Part 3: Assembly with a) Rear-Mid engine configuration b) Front engine configuration)
- Figure 3.42: 파트 3: 운전석 하부 치수 (Part 3: Cockpit underbody dimensions)
- Figure 3.43: 파트 4: 더블 전기 모터 어셈블리 (Part 4: Assembly with double electric motor)
- Figure 3.44: 파트 4: 전기 모터실 치수 (Part 4: Electric motor compartment dimensions)
- Figure 3.45: 모듈형 플랫폼 설계 최종 모델 및 치수 (Modular platform design final model and dimensions)
- Figure 3.46: 자동차 움직임 중의 힘 (Forces during the car motion)
- Figure 3.47: 종방향 비틀림 (Longitudinal torsion)
- Figure 3.48: 비틀림 강성 하중 케이스 (Torsional stiffness load case)
- Figure 3.49: 수직 굽힘 (Vertical bending)
- Figure 3.50: 굽힘 강성 하중 케이스 (Bending stiffness load case)
- Figure 3.51: 측면 굽힘 (Lateral bending)
- Figure 3.52: 수평 로젠징 (Horizontal lozenging)
- Figure 3.53: 후방-중간 모듈형 플랫폼의 경계 조건 (Boundary conditions on rear-mid modular platform)
- Figure 3.54. 후방-중간 모듈형 플랫폼에 대한 비틀림 테스트의 변위 결과 (Displacement results of torsional test for rear-mid modular platform)
- Figure 3.55. 후방-중간 모듈형 플랫폼의 비틀림 응력 분포 (Torsional stress distribution of rear-mid modular platform)
- Figure 3.56: 전방 모듈형 플랫폼의 경계 조건 (Boundary conditions on front modular platform)
- Figure 3.57: 전방 모듈형 플랫폼에 대한 비틀림 테스트의 변위 결과 (Displacement results of torsional test for front modular platform)
- Figure 3.58: 전방 모듈형 플랫폼의 비틀림 응력 분포 (Torsional stress distribution of front modular platform)
- Figure 3.59: 굽힘 테스트를 위한 후방-중간 모듈형 플랫폼의 경계 조건 (Boundary conditions on rear-mid modular platform for bending test)
- Figure 3.60: 굽힘 테스트를 위한 후방-중간 모듈형 플랫폼의 변위 결과 (Displacement results of bending test for rear-mid modular platform)
- Figure 3.61: 후방-중간 모듈형 플랫폼의 굽힘 응력 분포 결과 (Bending stress distribution results of rear-mid modular platform)
- Figure 3.62: 굽힘 테스트를 위한 전방 모듈형 플랫폼의 경계 조건 (Boundary conditions on front modular platform for bending test)
- Figure 3.63: 굽힘 테스트를 위한 전방 모듈형 플랫폼의 변위 결과 (Displacement results of bending test for front modular platform)
- Figure 3.64: 전방 모듈형 플랫폼의 굽힘 응력 분포 결과 (Bending stress distribution results of front modular platform)
- Figure 3.65: 후방-중간 모듈형 플랫폼의 충격 테스트 설정 (Impact test settings for rear-mid modular platform)
- Figure 3.66: 충격 테스트 결과 (a) 변위 결과, (b) 변형 분포 결과 (Impact test results (a) Displacement results, (b) Deformation distribution results)
- Figure 3.67: 파트 3 및 파트 4의 부품 개발을 위해 정의된 섹션 (Defined sections for part development on Part 3 and Part 4)
- Figure 3.68: 전방 모듈형 플랫폼의 충격 테스트 설정 (Impact test settings for front modular platform)
- Figure 3.69: 충격 테스트 결과 (a) 변위 결과, (b) 변형 분포 결과 (Impact test results (a) Displacement results, (b) Deformation distribution results)
- Figure 3.70: 파트 1의 부품 개발을 위해 정의된 섹션 (Defined section for the part development on Part 1)
- Figure 3.71: 복고풍 디자인 (Retro design)
- Figure 3.72: 스톤 디자인 (Stone design)
- Figure 3.73: 돛새치의 등지느러미에서 영감을 받은 자연 디자인 (Natural design inspired from the dorsal lines of the sailfish)
- Figure 3.74: 자연 디자인 (Natural design)
- Figure 3.75: 첨단 디자인 (Advanced design)
- Figure 3.76: 최종 디자인을 위해 선택된 세부 사항 표현 (Representation of the details selected for the final design)
- Figure 3.77: 최종 디자인 스케치 (Final design sketching)
- Figure 3.78: 최종 스케치 청사진 (Blueprint of final sketch)
- Figure 3.79: 최종 스케치 원본 디자인 (Raw design of final sketch)
- Figure 3.80: 최종 3D 디자인 (Final 3D design)
- Figure 3.81: 렌더링된 최종 디자인 (Rendered final design)
- Figure 3.82: 모듈형 플랫폼 및 최종 디자인 어셈블리 (Modular platform and final design assembly)
- Figure 3.83: 스크럼 프로세스 (Scrum process)
- Figure 3.84: 생성적 디자인 워크플로우 (Generative design workflow)
- Figure 3.85: 방법 비교 a) 스프린트 단계 (Srivastava et al., 2017) b) 생성적 디자인 프로세스 단계 (Comparison of methods a) Sprint steps (Srivastava et al., 2017) b) Generative design process steps)
- Figure 3.86: 생성적 디자인 방법이 적용된 새로운 스크럼 워크플로우 모델 (New scrum workflow model with generative design method)
- Figure 3.87: 스크럼 및 생성적 디자인 방법을 사용한 수정된 IDeS 워크플로우 (Modified IDeS workflow using Scrum and Generative Design method)
- Figure 3.88: 재료 세부 정보가 포함된 폭스바겐 MQB 플랫폼 (Volkswagen MQB platform with material details)
- Figure 3.89: 플랫폼 섹션 경계 (Boundaries of platform sections)
- Figure 3.90: 모듈형 플랫폼 어셈블리 분해 도면 (Exploded view of the modular platform assembly)
- Figure 3.91: 후방-중간 엔진용 모듈형 플랫폼 (Modular platform for rear-mid engine)
- Figure 3.92: 전방 엔진용 모듈형 플랫폼 (Modular platform for front engine)
- Figure 3.93: 모듈형 플랫폼의 볼트 조인트 (Bolted joints of the modular platform)
- Figure 3.94: 생성적 디자인을 위해 정의된 영역 (Areas defined for generative design)
- Figure 3.95: 엔진실 경계 조건 (파트 1) (Boundary conditions of engine compartment (Part1))
- Figure 3.96: 운전석 하부 경계 조건 (파트 3) (Boundary conditions of cockpit underbody (Part3))
- Figure 3.97: 전기 모터실 경계 조건 (파트 4) (Boundary conditions for electric motor compartment (Part 4))
- Figure 3.98: 파트 1의 구조적 제약 및 하중 (Structural constraints and loads on Part 1)
- Figure 3.99: 파트 3의 구조적 제약 및 하중 (Structural constraints and loads on Part 3)
- Figure 3.100: 파트 4의 구조적 제약 및 하중 (Structural constraints and loads on Part 4)
- Figure 3.101: 생성적 디자인 결과 강철 합금 적용 파트 1 (Generative design results steel alloys applied Part 1)
- Figure 3.102: 생성적 디자인 결과 강철 합금 적용 파트 3 (Generative design results steel alloys applied Part 3)
- Figure 3.103: 생성적 디자인 결과 강철 합금 적용 파트 4 (Generative design results steel alloys applied Part 4)
- Figure 3.104: 생성적 디자인 결과 알루미늄 합금 적용 파트 1 (Generative design results aluminium alloys applied Part 1)
- Figure 3.105: 생성적 디자인 결과 알루미늄 합금 적용 파트 3 (Generative design results aluminium alloys applied Part 3)
- Figure 3.106: 생성적 디자인 결과 알루미늄 합금 적용 파트 4 (Generative design results aluminium alloys applied Part 4)
- Figure 3.107: 생성적 디자인 적용 "이상적인 모듈형 플랫폼" (Generative design applied “Ideal Modular Platform”)
- Figure 3.108: 이상적인 모듈형 플랫폼의 빔 모델 (Beam model of ideal modular platform)
- Figure 3.109: 후방-중간 엔진 레이아웃을 위한 이상적인 모듈형 플랫폼의 변위 결과 (Displacement results of ideal modular platform for rear-mid engine layout)
- Figure 3.110: 후방-중간 엔진 레이아웃을 위한 이상적인 모듈형 플랫폼의 비틀림 응력 분포 (Torsional stress distribution of ideal modular platform for rear-mid engine layout)
- Figure 3.111: 전방 이상적인 모듈형 플랫폼의 경계 조건 (Boundary conditions on front ideal modular platform)
- Figure 3.112: 전방 엔진 레이아웃을 위한 이상적인 모듈형 플랫폼의 변위 결과 (Displacement results of ideal modular platform for front engine layout)
- Figure 3.113: 전방 엔진 레이아웃을 위한 이상적인 모듈형 플랫폼의 비틀림 응력 분포 (Torsional stress distribution of ideal modular platform for front engine layout)
- Figure 3.114: 굽힘 테스트를 위한 후방-중간 이상적인 모듈형 플랫폼의 경계 조건 (Boundary conditions on rear-mid ideal modular platform for bending test)
- Figure 3.115: 굽힘 테스트를 위한 후방-중간 이상적인 모듈형 플랫폼의 변위 결과 (Displacement results of bending test for rear-mid ideal modular platform)
- Figure 3.116: 후방-중간 이상적인 모듈형 플랫폼의 굽힘 응력 분포 결과 (Bending stress distribution results of rear-mid ideal modular platform)
- Figure 3.117: 굽힘 테스트를 위한 전방 이상적인 모듈형 플랫폼의 경계 조건 (Boundary conditions on front ideal modular platform for bending test)
- Figure 3.118: 굽힘 테스트를 위한 전방 이상적인 모듈형 플랫폼의 변위 결과 (Displacement results of bending test for front ideal modular platform)
- Figure 3.119: 굽힘 테스트를 위한 전방 이상적인 모듈형 플랫폼의 굽힘 응력 분포 결과 (Bending stress distribution results of front ideal modular platform)
7. 결론:
주요 연구 결과 요약:
본 연구에서는 스크럼을 통합한 수정된 IDeS 워크플로우 내에서 생성적 디자인 방법을 사용하여 스포츠카용 모듈형 플랫폼을 성공적으로 설계했습니다. 생성적 디자인은 특히 알루미늄 합금을 사용할 때 경량 부품을 만들 수 있게 했으며, 기계적 성능을 유지하거나 개선했습니다. 모듈형 플랫폼은 다양한 엔진 레이아웃 및 파워트레인 구성에 적응할 수 있어 다용도성을 입증했습니다. 스크럼 방법론의 통합은 반복적이고 효율적인 설계 프로세스를 촉진했습니다.
연구의 학문적 의의:
본 연구는 자동차 섀시 설계, 특히 스포츠카의 모듈형 플랫폼에 생성적 디자인 및 애자일 방법론 (스크럼) 을 효과적으로 적용한 사례를 제시함으로써 학문 분야에 기여합니다. 또한 이러한 최첨단 기술을 구조화된 설계 워크플로우 (IDeS) 내에 통합하기 위한 자세한 방법론을 제공합니다. 본 연구는 경량 및 고성능 자동차 구조를 달성하기 위한 생성적 디자인에서 재료 선택 및 최적화에 대한 이해를 넓힙니다.
실용적 의미:
본 연구의 실용적 의미는 자동차 산업, 특히 스포츠카 제조업체에 매우 중요합니다. 개발된 모듈형 플랫폼 설계는 생산 비용 절감, 차량 적응성 향상, 경량화를 통한 연비 개선을 위한 실행 가능한 솔루션을 제공합니다. 생성적 디자인 및 적층 제조 기술을 사용하면 보다 혁신적이고 효율적인 섀시 설계를 얻을 수 있습니다. 스크럼 방법론의 통합은 제품 개발 프로세스를 간소화하여 변화하는 시장 요구에 보다 민첩하고 대응적으로 만들 수 있습니다.
연구의 한계 및 향후 연구 분야:
본 연구는 섀시의 하부와 빔 모델 시뮬레이션에 초점을 맞추고 있어 전체 차량 섀시를 단순화했다는 한계가 있습니다. 얻어진 비틀림 강성 값은 기존 스포츠카의 전체 섀시 값과 직접 비교할 수 없습니다. 향후 연구는 다음 사항에 초점을 맞춰야 합니다:
- 전체 차량 시뮬레이션 및 물리적 프로토타입 제작을 통한 모듈형 플랫폼 설계 검증.
- 생성적 디자인에서 더 넓은 범위의 재료 및 제조 공정 탐색.
- 향상된 성능 및 지속 가능성을 위한 다목적 최적화와 생성적 디자인의 통합 연구.
- 다양한 자동차 설계 프로젝트를 위한 스크럼-IDeS 워크플로우를 더욱 개선하고 더 넓은 적용 가능성을 평가합니다.
- 생성적으로 설계된 부품 및 모듈형 플랫폼의 기계적 특성에 대한 실험적 검증 수행.
8. 참고 문헌:
- [참고 문헌 목록은 영문 요약본의 8번 항목을 참조하세요.]
9. 저작권:
- 본 자료는 "Merve Sali"의 논문: "DESIGNING AN INNOVATIVE MODULAR PLATFORM FOR SPORTS CARS USING THE GENERATIVE DESIGN METHOD"를 기반으로 합니다.
- 논문 출처: DOI URL은 문서에 제공되지 않았습니다.
본 자료는 상기 논문을 기반으로 요약되었으며, 상업적 목적으로 무단 사용하는 것을 금지합니다.
Copyright © 2025 CASTMAN. All rights reserved.