본 논문 요약은 ['Politecnico di Torino']에서 발행한 ['Self hardening aluminum alloys for automotive applications'] 논문을 기반으로 작성되었습니다.
1. 개요:
- 제목: 자동차 응용 분야를 위한 자가 경화 알루미늄 합금 (Self hardening aluminum alloys for automotive applications)
- 저자: Christian Castella
- 발행 연도: 논문에서 명시되지 않음. (저자의 출판 목록을 기반으로 2014년으로 추정)
- 발행 저널/학술 단체: Politecnico di Torino, Facoltà di Ingegneria, 재료 과학 및 기술 박사 학위 논문
- 키워드: 자가 경화 알루미늄 합금, 자동차 응용 분야, Al-Zn-Si-Mg 합금, 너클 부품, 내식성, 기계적 특성, 열처리 비용
![Figure 26: Aluminum applications in a car [30].](https://castman.co.kr/wp-content/uploads/image-650-png.webp)
2. 초록
본 박사 학위 논문은 토리노 근처 카르마뇰라에 위치한 알루미늄 주조 공장인 Teksid Aluminum과의 협력으로 수행되었습니다. 본 연구는 다양한 산업 분야, 특히 운송 산업에서 광범위하게 응용될 수 있는 높은 기계적 특성을 나타내는 혁신적인 경량 알루미늄 합금 종류인 자가 경화 알루미늄 합금(Al-Zn-Si-Mg 합금)에 초점을 맞추고 있습니다. 주요 특징은 열처리 없이도 우수한 성능을 달성할 수 있다는 점이며, 약 7~10일의 보관 기간 후 상온에서 자연 시효 경화됩니다. 열처리 생략은 생산 비용, 에너지 소비 및 부품 변형 위험을 상당히 줄이는 중요한 이점을 제공합니다. 본 논문은 자동차 부품 생산을 위해 실제로 사용되는 T6 열처리된 A356 합금을 대체할 수 있는 솔루션을 찾는 것을 목표로 하며, 특히 너클 서스펜션 부품에 자가 경화 합금의 개발 가능성을 평가합니다. 열처리 생략으로 인한 에너지 절감과 관련된 경제적 고려 사항도 탐구합니다. 본 논문의 상당 부분은 너클 서스펜션 부품 생산에 최적의 합금 조성을 정의하기 위해 Mg 함량 및 냉각 속도의 영향을 조사하여 자가 경화 알루미늄 합금의 구조적 특징, 기계적 특성 및 내식성을 연구합니다.
3. 연구 배경:
연구 주제 배경:
알루미늄 합금은 경량성으로 인해 자동차 산업에서 점점 더 많이 활용되고 있으며, 이는 차량 중량 감소와 연비 향상에 기여합니다. 논문에서 언급했듯이, "알루미늄은 경량 금속이며 지구상에서 가장 풍부한 금속 원소 중 하나입니다… 알루미늄은 매우 중요한 경제적 경쟁자가 되었고 알루미늄 산업은 기하급수적인 성장을 겪었습니다 [2-3]." 이러한 경량화 추세는 "자동차의 연료 소비를 완화하고 동시에 가스, 특히 CO2 배출을 줄여야 할 필요성"에 의해 더욱 촉진됩니다.
기존 연구 현황:
현재 너클 부품을 포함한 자동차 부품 생산에는 T6 열처리된 A356 합금이 사용됩니다. 논문은 "본 박사 학위 논문의 목표는 자동차 부품 생산을 위해 실제로 사용되는 T6 열처리된 A356 합금을 대체할 수 있는 솔루션을 찾는 것이었습니다."라고 명시합니다. 열처리는 일반적으로 알루미늄 합금의 기계적 강도를 향상시키는 데 사용되지만, 에너지 집약적이며 제조 복잡성을 야기할 수 있습니다. 문서는 "일반적으로 열처리는 알루미늄 주조 공장에서 알루미늄 합금의 기계적 강도를 높이기 위해 널리 사용됩니다. 실제로 환경에 미치는 영향을 최소화하기 위해 에너지 소비를 최소화하려는 경향이 높습니다."라고 지적합니다.
연구의 필요성:
본 연구는 부품 성능을 유지하거나 향상시키면서 자동차 제조의 에너지 소비와 생산 비용을 줄여야 할 필요성을 다룹니다. 자가 경화 알루미늄 합금은 에너지 집약적인 열처리 필요성을 없애 잠재적인 해결책을 제시합니다. 논문은 "열처리 생략 가능성은 일부 부품의 생산 비용과 제조 공정에 투입되는 에너지 양을 상당히 줄이는 데 기여하는 중요한 이점을 나타냅니다. 또한 열처리 없이 생산 중 부품 변형 위험이 완전히 제거됩니다."라고 강조합니다. 본 연구는 자동차 응용 분야에서 기존의 열처리된 합금을 대체할 수 있는 실행 가능하고 비용 효율적인 대안으로서 자가 경화 알루미늄 합금을 탐구하고 최적화하는 데 매우 중요합니다.
4. 연구 목적 및 연구 질문:
연구 목적:
주요 연구 목적은 "자동차 부품 생산을 위해 실제로 사용되는 T6 열처리된 A356 합금을 대체할 수 있는 솔루션을 찾는 것"입니다. 여기에는 너클 서스펜션 부품 생산을 위해 자가 경화 알루미늄 합금을 대체 재료로 평가하는 것이 포함됩니다.
핵심 연구:
핵심 연구 분야는 다음과 같습니다.
- "자가 경화 알루미늄 합금의 구조적 특징 및 기계적 특성 연구"
- "내식성 조사"
- "Mg 함량 및 냉각 속도가 세 가지 다른 자가 경화 알루미늄 합금의 미세 구조에 미치는 영향"
- "너클 서스펜션 부품 생산에 최적의 합금 조성 정의 목표"
연구 가설:
공식적인 가설로 명시되지는 않았지만, 연구는 다음과 같은 전제하에 진행됩니다.
- 자가 경화 Al-Zn-Si-Mg 합금은 자동차 부품에서 T6 열처리된 A356 합금을 대체할 수 있을 만큼 충분하거나 그에 상응하는 기계적 특성을 달성할 수 있습니다.
- 자가 경화 합금으로 열처리를 생략하면 제조 비용 및 에너지 절감 효과가 클 것입니다.
- 자가 경화 Al-Zn-Si-Mg 합금의 미세 구조, 기계적 특성 및 내식성은 주조 중 Mg 함량 및 냉각 속도를 조정하여 최적화할 수 있습니다.
5. 연구 방법론
연구 설계:
본 연구는 대표적인 자동차 부품인 "너클 부품"에 초점을 맞춘 실제 사례 연구 접근 방식을 채택합니다. 여기에는 다이캐스팅으로 생산된 "자가 경화" 알루미늄 합금의 실험적 조사 및 최적화가 포함됩니다.
데이터 수집 방법:
다음과 같은 데이터 수집 방법이 활용되었습니다.
- 미세 구조 분석: "미세 구조 분석을 위한 시편은 표준 금속 조직 기술로 준비되었으며… 그 후 시편은 광학 현미경(OM, MeF4 Reichart-Jung)과 에너지 분산형 X선 분광기(EDS, Oxford microprobe)가 장착된 주사 전자 현미경(SEM, Leo 1450VP)을 통해 조성 분석을 위해 조사되었습니다." X선 회절도 사용되었으며, 이는 "그림 56: AlZn10Si8Mg 자가 경화 합금의 X선 회절도"에서 확인할 수 있습니다.
- 기계적 특성 시험: 기계적 성능은 "인장 시험 및 브리넬 경도 시험"을 통해 평가되었습니다. 추가적인 기계적 특성 평가는 "3점 굽힘 시험, 샤르피 충격 시험 및 비커스 경도 시험"을 포함했습니다. 피로 특성은 "피로 시험기(TESTRONIC 100K RUMUL)"를 사용하여 평가되었습니다.
- 내식성 평가: 내식성은 "ISO 9227 표준에 따라 수행된 염수 분무 부식 시험"과 "BS 11846, 방법 B [79]에 따른 입계 부식 시험"을 사용하여 평가되었습니다.
분석 방법:
분석에는 다음이 포함되었습니다.
- 정량적 미세 구조 분석: "2차 수지상 팔 간격(SDAS)" 측정 및 "면적(A), 원형도(R) 및 등가 직경(Deq.)"을 사용하여 실리콘 입자 특성 분석.
- 기계적 특성 비교: 획득한 기계적 특성은 "Teksid에서 현재 사용 중인 T6 열처리된 A356 합금의 특성 및 너클 부품에 필요한 특성과 비교"되었습니다.
- 부식 거동 평가: 육안 검사, SEM 분석 및 EDS 분석을 사용하여 부식을 평가하고, 입계 부식 시험을 위해 "부식 깊이" 및 "부식으로 인한 중량 손실"을 측정했습니다.
- 통계 분석: 계단식 방법은 피로 한계 평가에 사용되었습니다.
연구 대상 및 범위:
본 연구는 특정 조성의 "자가 경화 알루미늄 합금(Al-Zn-Si-Mg 합금)"에 초점을 맞추었습니다: "AlZn10Si8Mg", "AlZn10Si8Mg1" 및 "AlZn10Si8Mg3". 범위는 "너클 부품"에 특정 초점을 두고 "자동차 응용 분야"에 대한 이러한 합금 평가로 제한되었습니다. "Mg 함량"(0.3-0.5 wt%에서 최대 3 wt%) 및 "냉각 속도"의 영향이 조사되었습니다.
6. 주요 연구 결과:
핵심 연구 결과:
- 미세 구조 진화: "주조 상태와 7일간의 자연 시효 경화 후의 미세 구조 사이에서 밝혀진 주요 차이점은 2차 수지상 팔 간격(SDAS) 값과 관련이 있습니다… 7일간의 자연 시효 경화 후 미세 구조는 주조 상태보다 더 미세하게 나타납니다." 냉각 속도가 증가함에 따라 미세 구조가 더 미세해지고 SDAS 값이 낮아졌습니다. "Mg 함량이 증가함에 따라 더욱 두드러진 수지상 형태의 발달이 관찰될 수 있습니다."
- 기계적 특성: "AlZn10Si8Mg 자가 경화 알루미늄 합금의 기계적 특성은 T6 열처리된 A356 (AlSi7Mg0.3) 알루미늄 합금의 기계적 특성과 유사합니다." 그러나 "AlZn10Si8Mg 합금의 파단 연신율 A%는 약간 다른 값을 나타내며 해당 부품에 적합하지 않습니다." AlZn10Si8Mg1은 가장 높은 굽힘 강도를 나타냈습니다. Mg 함량이 1wt% (AlZn10Si8Mg3)를 초과하여 증가하면 굽힘 강도 및 충격 에너지가 감소했습니다.
- 내식성: "이러한 결과는 연구된 합금이 A356 합금을 대체할 수 있는 기계적 관점에서 유망한 후보로 보일지라도 AlZn10Si8Mg의 내식성은 적절하지 않음을 보여줍니다." 그러나 "AlZn10Si8Mg1 및 AlZn10Si8Mg3 합금은 부식 환경에 더 강한 것으로 보입니다." AlZn10Si8Mg3은 가장 우수한 입계 부식 저항성을 나타내며, "중량 손실과 침투 깊이 모두에서 가장 낮은 값"을 나타냈습니다.
- 피로 특성: "AlZn10Si8Mg1 자가 경화 알루미늄 합금은 약 92 MPa의 피로 한계를 갖는 것으로 관찰될 수 있습니다. 이 피로 한계 값은 T6 열처리 및 영구 금형 주조 기술 [3]을 거친 A356 (AlSi7Mg0.3) 합금의 피로 한계 값과 유사합니다."
제시된 데이터 분석:
미세 구조 이미지, 기계적 특성 그래프 및 부식 시험 결과를 포함하여 논문에 제시된 데이터는 자가 경화 Al-Zn-Si-Mg 합금에서 Mg 함량 및 냉각 속도 변화에 따른 기계적 특성과 내식성 간의 상충 관계를 일관되게 나타냅니다. 일반적으로 냉각 속도가 빠를수록 미세 구조가 미세해지고 기계적 특성이 향상됩니다. Mg 함량이 증가하면 초기에는 강도가 향상되지만, 더 높은 수준(3wt%)에서는 연성 및 충격 저항성에 부정적인 영향을 미치면서 내식성이 향상될 수 있습니다. 수축 기공은 기계적 성능, 특히 피로 수명에 영향을 미치는 반복적인 결함으로 확인되었습니다.
그림 목록:
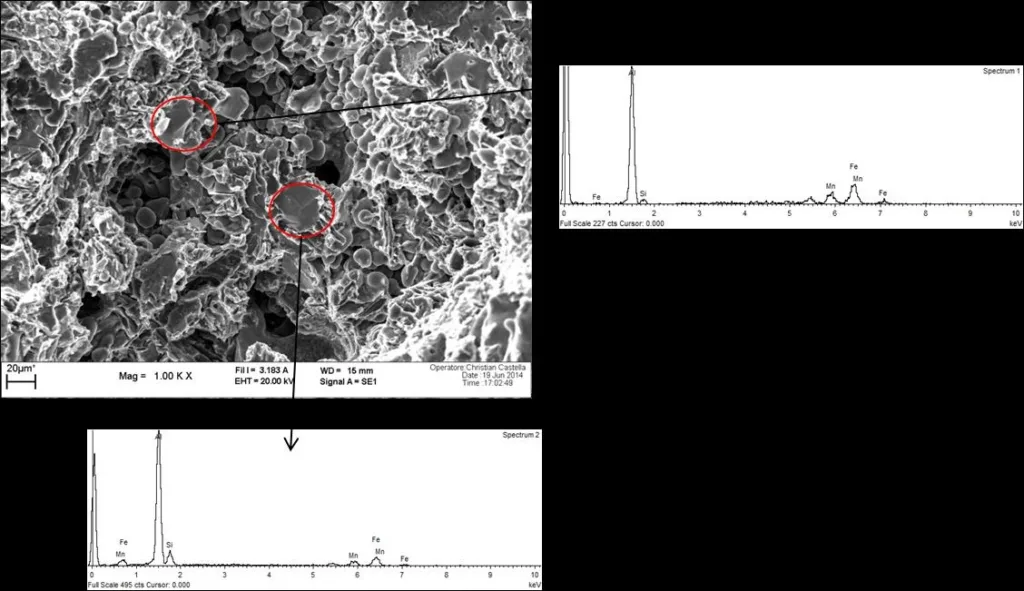
![Figure 25: Components realized with aluminum in a modern car [31].](https://castman.co.kr/wp-content/uploads/image_28-1.webp)
![Figure 27: Relative mass saving, absolute mass saving and market penetration
obtainable with aluminum alloys [32].](https://castman.co.kr/wp-content/uploads/image_30-1024x441.webp)
![Figure 28: Final result of the SLC project based on the "multi-material design" concept
[32].](https://castman.co.kr/wp-content/uploads/image_31-1024x459.webp)
![Figure 44: Car's door panel produced with UNIFONT-90 self-hardening aluminum
alloy [70].](https://castman.co.kr/wp-content/uploads/image_53.webp)
![Figure 49: Knuckle component [71].](https://castman.co.kr/wp-content/uploads/image_58-1024x492.webp)
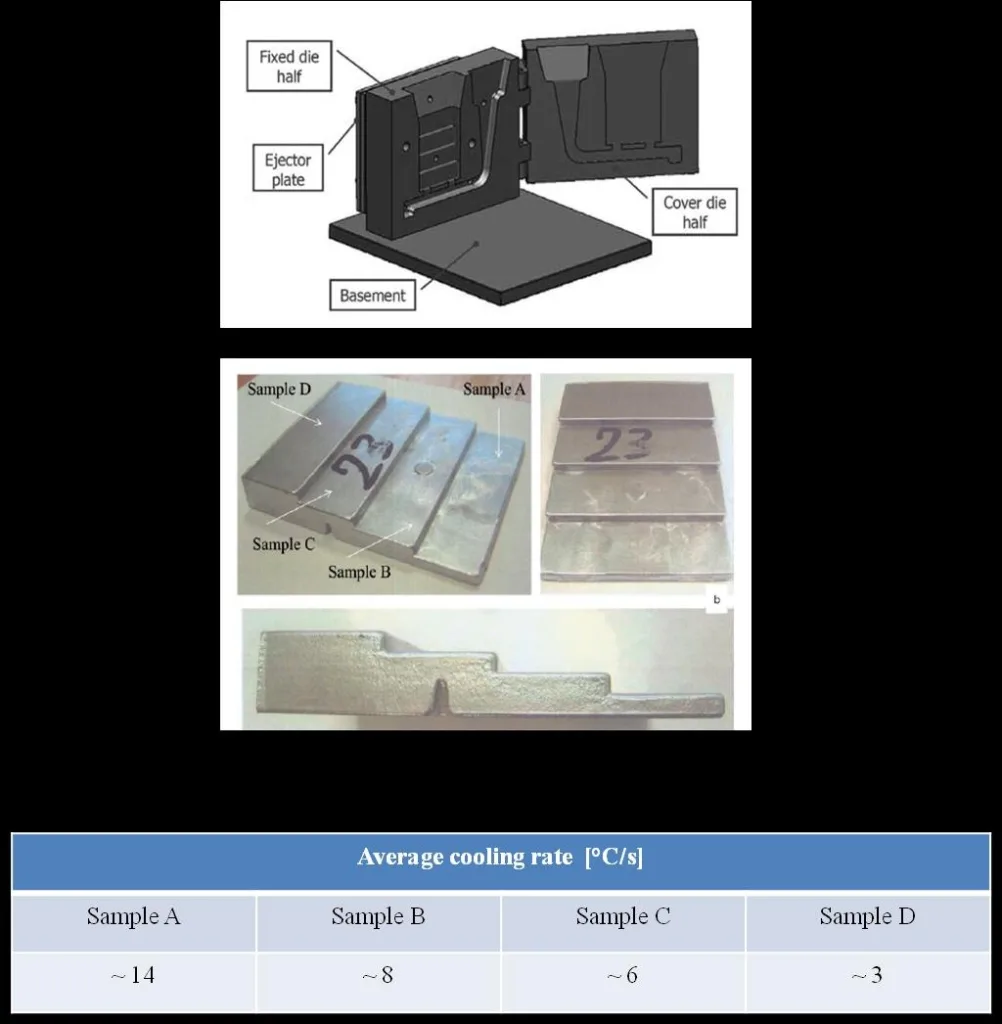
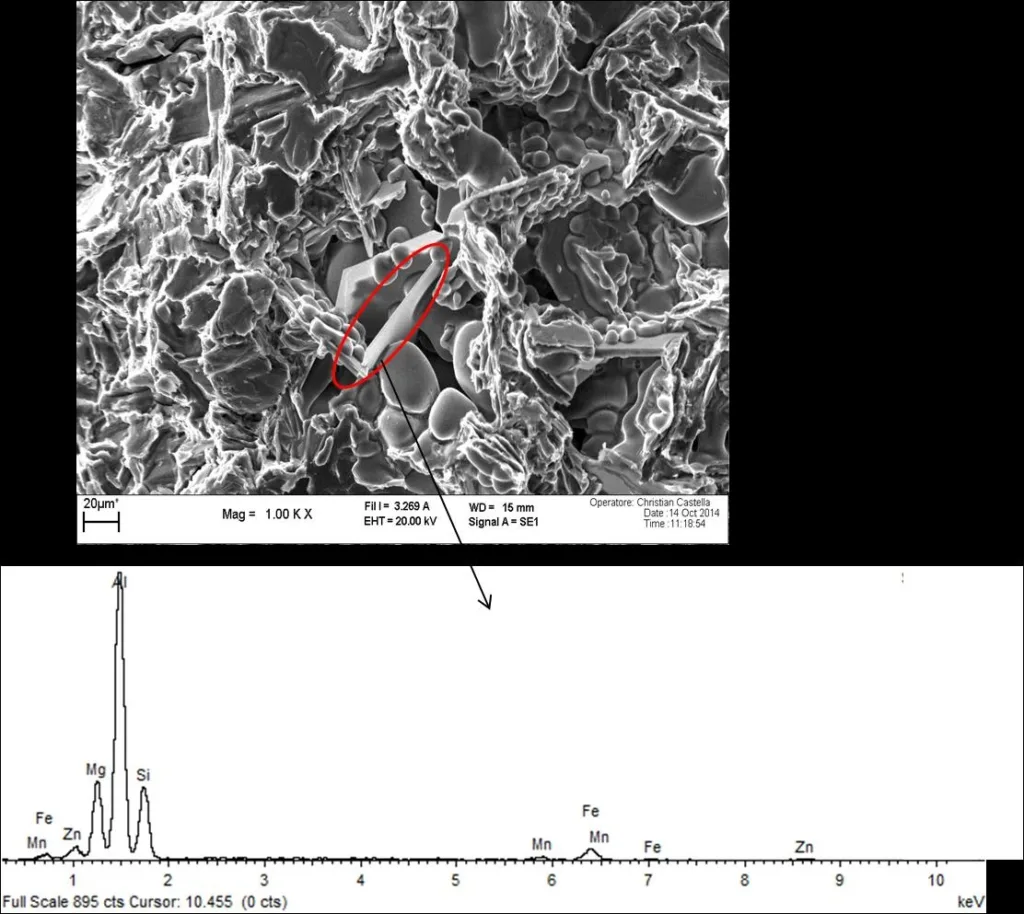
- 그림 1: 미세 구조: a) 중국 문자 형태의 α-Al15(Fe,Mn)3Si2 상 및 b) β-Al5FeSi 판상 조직 [7].
- 그림 2: Al-Cu 합금 [12]의 용체화, 급냉 및 시효와 관련된 메커니즘 표현.
- 그림 3: a) 기존 및 b) 급경사 급냉 공정 [15]의 온도 대 시간 다이어그램.
- 그림 4: 전위가 석출물을 우회하는 메커니즘: a) Friedel 효과 또는 b) Orowan 메커니즘. c) 강도 대 입자 반경 다이어그램 [10].
- 그림 5: 시효 시간의 로그 함수로서의 강도 및 경도 [16].
- 그림 6: Al-Si-Cu 합금 [16]의 석출 순서.
- 그림 7: 다른 시효 온도 [16]에서 얻은 경도-인장 강도-시간 곡선.
- 그림 8: Cocks [17]에 따른 주조 결함 분류.
- 그림 9: Campbell [18]에 따른 주조 결함 분류.
- 그림 10: Sievert 법칙 다이어그램.
- 그림 11: 가스 기공 (Teksid Aluminum 제공).
- 그림 12: 수축 기공 (Teksid Aluminum 제공).
- 그림 13: 피로 균열의 핵 생성 부위로 작용하는 수축 기공 (Teksid Aluminum 제공).
- 그림 14: 산화물 입자 (Teksid Aluminum 제공).
- 그림 15: Bifilm 생성 메커니즘 [26].
- 그림 16: A354 알루미늄 합금에서 개별화된 일부 bifilm (Teksid Aluminum 제공).
- 그림 17: A354 알루미늄 합금에서 개별화된 일부 bifilm (Teksid Aluminum 제공).
- 그림 18: 일부 알루미늄 부품에서 나타난 냉간 접합 [19].
- 그림 19: 알루미늄 시편의 파단면에서 개별화된 균열 (Teksid Aluminum 제공).
- 그림 20: β-Al5FeSi, α-Al15(FeMn)3Si2 [28]를 보여주는 광학 미세 구조.
- 그림 21: 알루미늄 시편의 파단면에서 α-Al15(FeMn)3Si2 철 금속간 화합물 (Teksid Aluminum 제공).
- 그림 22: 수축 기공 근처에서 검출된 알루미늄 시편의 파단면에서 α-Al15(FeMn)3Si2 철 금속간 화합물 (Teksid Aluminum 제공).
- 그림 23: 지난 40년 동안 자동차의 알루미늄 함량 추세 [30].
- 그림 24: 자동차 이동에 대한 저항력 [30].
- 그림 25: 현대 자동차 [31]에서 알루미늄으로 제작된 부품.
- 그림 26: 자동차 [30]의 알루미늄 응용 분야.
- 그림 27: 알루미늄 합금 [32]으로 얻을 수 있는 상대적 질량 절감, 절대적 질량 절감 및 시장 침투율.
- 그림 28: "다중 재료 설계" 개념 [32]을 기반으로 한 SLC 프로젝트의 최종 결과.
- 그림 29: 알루미늄 표면 [36]에 형성된 보호 산화막 구조.
- 그림 30: 25°C [37]에서 Al-H2O 시스템의 Pourbaix 다이어그램.
- 그림 31: 순수 Al 및 AA2024-T3를 0.1M NaCl에 7일 동안 노출시킨 후 1mV/s-1 [37]에서 수집한 분극 곡선.
- 그림 32: 일부 합금 원소가 알루미늄의 전해 용액 전위에 미치는 영향. 전위는 고순도 2원 합금 용체화 열처리 및 급냉에 대한 것입니다. 데이터는 25°C [2]에서 유지된 53 g/l NaCl + 3 g/l H2O2 용액을 사용하여 얻었습니다.
- 그림 33: 1.0M NaNO3 용액에서 알루미늄 99.999%의 반구형 피트 (E¼1.84 VSHE [39]).
- 그림 34: AlOOH/Al2O3 층 [40] 내 SiO2 입자의 존재 및 합금-용액 계면을 보여주는 개략도.
- 그림 35: 2xxx 알루미늄 합금 [38]의 결정립계 영역 개략도.
- 그림 36: 7055 알루미늄 합금 [47]의 결정립계 영역 개략도.
- 그림 37: 0.5M NaCl 탈기 용액에서 −685mVSCE에서 노출된 7075-T6 알루미늄 합금 시편 표면의 광학 현미경 사진: (a) 수령된 시편 및 (b), (c) 및 (d) 결정립 크기가 각각 40, 130 및 290 µm인 시편 [48].
- 그림 38: SCC를 설명하기 위해 지금까지 개발된 일부 이론 개략도: a) 양극 용해; b) 수소 유기 균열 및 c) 수동 피막 파괴 [2].
- 그림 39: SCC에 대한 다양한 감수성을 생성하기 위해 처리 후 5356-H12 합금의 미세 구조. a) 냉간 압연 20%; 내성이 높음. b) 냉간 압연 20%, 100°C에서 1년 가열; 감수성이 높음. c) 냉간 압연 20%, 150°C에서 1회 가열; 약간의 감수성. d) 냉간 압연 20%, 205°C에서 1회 가열; 내성이 높음 [2].
- 그림 40: Al–Zn–Mg–Cu–Zr 및 Al–Zn–Mg–Cu–Zr–Er–Cr 합금 [45]의 3.5 wt% NaCl 용액에서 균열 전파 속도(v) 대 균열 선단 응력 확대 계수(KI).
- 그림 41: 다양한 화학 용액 [2]에 의한 1100-H14 합금의 부식에 대한 pH 영향.
- 그림 42: 황산 [2]에서 1100 알루미늄 합금의 부식에 대한 온도 영향.
- 그림 43: 압출 AA6060 알루미늄 합금 [38] 조각에 대한 양극 산화 피막의 SEM 이미지.
- 그림 44: UNIFONT-90 자가 경화 알루미늄 합금 [70]으로 제작된 자동차 도어 패널.
- 그림 45: UNIFONT-90 자가 경화 알루미늄 합금 [70]으로 제작된 로봇 섀시.
- 그림 46: UNIFONT-94 자가 경화 알루미늄 합금 [70]으로 제작된 진동 댐퍼 지지대.
- 그림 47: UNIFONT-94 자가 경화 알루미늄 합금 [70]으로 제작된 비행기 좌석 테이블 지지대.
- 그림 48: Teksid에서 생산한 너클 부품 (Teksid Aluminum 제공).
- 그림 49: 너클 부품 [71].
- 그림 50: 그림 48의 너클 부품에 사용된 열처리 비용 요소 및 400,000개 너클 부품에 사용된 열처리 연간 생산 비용.
- 그림 51: AlZn10Si8Mg 자가 경화 알루미늄 합금의 미세 구조: a) 주조 상태(100배); b) 7일간의 자연 시효 경화 후(100배); c) 주조 상태(500배); d) 7일간의 자연 시효 경화 후(500배).
- 그림 52: 알루미늄-아연 상 다이어그램 [72].
- 그림 53: 주조 상태에서 AlZn10Si8Mg 자가 경화 알루미늄 합금의 SEM 현미경 사진 및 EDS 분석 결과.
- 그림 54: 7일간의 자연 시효 경화 후 AlZn10Si8Mg 자가 경화 알루미늄 합금의 SEM 현미경 사진 및 EDS 분석 결과.
- 그림 55: Mn 함량이 다른 Al-Si-Fe 시스템의 부분 상 다이어그램: a) 0 wt%; b) 0.1 wt%; c) 0.2 wt% 및 d) 0.3 wt% [73].
- 그림 56: AlZn10Si8Mg 자가 경화 합금의 X선 회절도.
- 그림 57: 인장 시험 결과: a) 극한 인장 강도; b) 항복 강도; c) 파단 연신율(A%).
- 그림 58: 브리넬 경도 시험 결과.
- 그림 59: 염수 분무 부식 시험 중 배치 내부의 시편 위치.
- 그림 60: 염수 분무 부식 시험 후 조사된 시편 사진.
- 그림 61: 염수 분무 부식 시험을 거친 시편 사진 및 EDS 분석으로 얻은 변질된 층의 조성.
- 그림 62: 단계별 주조 형상: a) 일반적인 뷰; b) 측면 뷰를 사용한 분석에 사용된 형상; c) 열전대로 측정한 평균 냉각 속도.
- 그림 63: 냉각 속도 함수로서 AlZn10Si8Mg 자가 경화 알루미늄 합금의 OM 현미경 사진 및 SDAS 값 [µm].
- 그림 64: 냉각 속도 함수로서 AlZn10Si8Mg1 자가 경화 알루미늄 합금의 OM 현미경 사진 및 SDAS 값 [µm].
- 그림 65: 냉각 속도 함수로서 AlZn10Si8Mg3 자가 경화 알루미늄 합금의 OM 현미경 사진 및 SDAS 값 [µm].
- 그림 66: 고려된 모든 합금에 대해 영역 C의 미세 구조를 비교하는 OM 현미경 사진.
- 그림 67: 냉각 속도가 다른 AlZn10Si8Mg 자가 경화 합금의 OM 현미경 사진: a) 시편 D (3 °C/s), b) 시편 C (6°C/s), c) 시편 B (8°C/s) 및 d) 시편 A (14°C/s) (500배).
- 그림 68: 냉각 속도가 다른 AlZn10Si8Mg1 자가 경화 합금의 OM 현미경 사진: a) 시편 D (3 °C/s), b) 시편 C (6°C/s), c) 시편 B (8°C/s) 및 d) 시편 A (14°C/s) (500배).
- 그림 69: 냉각 속도가 다른 AlZn10Si8Mg3 자가 경화 합금의 OM 현미경 사진: a) 시편 D (3 °C/s), b) 시편 C (6°C/s), c) 시편 B (8°C/s) 및 d) 시편 A (14°C/s) (500배).
- 그림 70: Mg wt% 및 냉각 속도가 다른 실리콘 입자의 역 면적.
- 그림 71: Mg wt% 및 냉각 속도가 다른 공정 실리콘 입자의 원형도.
- 그림 72: Mg wt% 및 냉각 속도가 다른 실리콘 입자의 등가 직경.
- 그림 73: 합금의 SDAS 값.
- 그림 74: a) 영역 B 및 영역 D에서 추출한 AlZn10Si8Mg, AlZn10Si8Mg1 및 AlZn10Si8Mg3 합금 시편의 미세 구조를 보여주는 OM 현미경 사진 및 b) EDS 분석 결과.
- 그림 75: 연구된 합금의 X선 스펙트럼.
- 그림 76: Scherrer 공식에 따라 계산된 a) Mg2Si 및 b) MgZn2 경화 석출물의 크기.
- 그림 77: 조사된 합금의 굽힘 강도: a) 7일간의 자연 시효 경화 후 및 b) 10개월간의 자연 시효 경화 후.
- 그림 78: 조사된 합금의 굽힘 변형률: a) 7일간의 자연 시효 경화 후 및 b) 10개월간의 자연 시효 경화 후.
- 그림 79: 샤르피 시험 결과: a) 7일간의 자연 시효 경화 후 및 b) 10개월간의 자연 시효 경화 후.
- 그림 80: 비커스 경도 값: a) 7일간의 자연 시효 경화 후 및 b) 10개월간의 자연 시효 경화 후.
- 그림 81: 파단면의 SEM 현미경 사진.
- 그림 82: 파단면의 일부 세부 사항을 보여주는 SEM 이미지: a) 수축 기공 및 b) 산화물 입자.
- 그림 83: 염수 분무 부식 시험 후 조사된 시편.
- 그림 84: EDS 분석으로 얻은 AlZn10Si8Mg 시편의 외부 표면에서 개별화된 변질된 층의 화학 조성.
- 그림 85: 샤르피 충격 시험 결과: a) 염수 분무 부식 시험 전 및 b) 염수 분무 부식 시험 후.
- 그림 86: 광학 미세 구조 a), b) 및 SEM 미세 구조와 EDS 분석 결과 c)는 공정 Al 매트릭스에 대해 국부적인 음극으로 작용하는 Si 입자를 보여주는 부식된 시편의 횡단면.
- 그림 87: SEM 미세 구조 및 EDS 분석 결과는 공정 Al 매트릭스에 대해 국부적인 음극으로 작용하는 Fe 금속간 화합물을 보여주는 부식된 시편의 횡단면.
- 그림 88: Al–Fe–Si–Mg 화합물의 SEM 이미지 a) 및 FESEM 이미지 b).
- 그림 89: a) 중량 손실 및 b) 입계 부식 시험 후 측정한 침투 깊이.
- 그림 90: 입계 부식 시험을 거친 시편의 외부 표면에서 수행된 분석의 EDS 결과.
- 그림 91: 3점 굽힘 시험, 굽힘 강도 결과: a) 입계 부식 시험 전 및 b) 입계 부식 시험 후.
- 그림 92: 3점 굽힘 시험, 굽힘 변형률 결과: a) 입계 부식 시험 전 및 b) 입계 부식 시험 후.
- 그림 93: 샤르피 시험 결과: a) 입계 부식 시험 전 및 b) 입계 부식 시험 후.
- 그림 94: 피로 시험 결과: a) S-N 곡선 및 b) 계단식 방법으로 얻은 생존 확률.
- 그림 95: 균열 시작 부위로 작용한 수축 기공을 보여주는 SEM 현미경 사진.
- 그림 96: 수축 기공 발달 및 EDS 분석 결과의 원인 중 하나인 Fe-Mn 금속간 화합물을 보여주는 SEM 현미경 사진.
7. 결론:
주요 연구 결과 요약:
본 박사 학위 논문은 자가 경화 Al-Zn-Si-Mg 합금이 자동차 부품 생산, 특히 너클 서스펜션과 같은 부품에 T6 열처리된 A356 합금을 대체할 수 있는 실행 가능한 대안임을 결론지었습니다. "획득한 기계적 특성은 T6 열처리된 A356 (AlSi7Mg0.3) 알루미늄 합금의 기계적 특성과 완벽하게 유사하며 너클 부품에 대한 특성 요구 사항을 충족합니다." 특히 약 14°C/s의 냉각 속도로 주조된 AlZn10Si8Mg1 합금은 기계적 특성, 내식성 및 피로 한계의 유망한 균형을 보여주었으며, 이는 "T6 열처리 및 영구 금형 주조 기술 [3]을 거친 A356 (AlSi7Mg0.3) 합금의 피로 한계 값과 유사합니다." Mg 함량이 최대 3wt% (AlZn10Si8Mg3)까지 증가하면 입계 부식 저항성이 더욱 향상되어 연구된 합금 중 내식성이 가장 우수했습니다. 그러나 Mg 함량이 높을수록 연성 및 충격 저항성에 부정적인 영향을 미칠 수 있습니다. 이러한 합금의 중요한 장점은 열처리 생략으로, 잠재적인 비용 및 에너지 절감 효과를 가져올 수 있다는 것입니다.
연구의 학문적 의의:
본 연구는 자가 경화 알루미늄 합금에 대한 학문적 이해에 기여하며, Mg 함량 및 냉각 속도가 미세 구조, 기계적 거동 및 부식 특성에 미치는 영향에 대한 자세한 통찰력을 제공합니다. 본 연구는 이러한 합금의 석출 메커니즘과 관찰된 특성과의 상관 관계를 설명합니다. 연구 결과는 일반적으로 자가 경화 알루미늄 합금에 대한 합금 설계 및 최적화 전략에 유용합니다.
실용적 의미:
본 연구의 실용적 의미는 자동차 산업에 매우 중요합니다. 본 연구는 너클 서스펜션과 같은 자동차 부품에서 자가 경화 Al-Zn-Si-Mg 합금, 특히 AlZn10Si8Mg1을 열처리된 A356 합금의 직접적인 대체재로 사용할 수 있음을 입증합니다. 이러한 대체는 열처리 공정을 생략함으로써 상당한 "열처리 설비 실현 없이 실현된 비용 절감 [€] 2,170,000" 및 에너지 소비 감소 가능성을 제공합니다. 유사한 피로 한계는 이러한 합금의 실제 적용 가능성을 더욱 뒷받침합니다.
연구의 한계 및 향후 연구 분야:
확인된 주요 한계는 AlZn10Si8Mg 합금의 "파단 연신율(A%)"이며, 이는 "너클 서스펜션 부품에 대한 요구 사항을 충족하지 못합니다." 이러한 한계를 해결하고 이러한 합금의 연성을 개선하기 위한 추가 연구가 권장됩니다. 논문은 또한 다음과 같은 향후 연구 방향을 제시합니다.
- "자동차 산업에서 요구하는 표준에 도달하기 위해 파단 연신율 값을 높이는 것"
- "또한 가장 유망한 합금의 피로 저항성은 고온에서 평가될 것입니다."
- 자동차 응용 분야를 위한 자가 경화 알루미늄 합금의 전반적인 성능을 향상시키기 위한 합금 조성 및 가공 매개변수의 추가 최적화.
8. 참고 문헌:
- [1] Atlante metallografico delle leghe di alluminio da fonderia, Ettore di Russo, Edimet.
- [2] Corrosion of aluminum and aluminum alloys, edited by J.R.Davis, The materials information society.
- [3] ASM handbook, volume 2 edited by Joseph R. Davis.
- [4]E.A. Starke Jr.; Aluminum alloys: Alloy, Heat Treatment, and Temper Designation; Encyclopedia of Materials: Science and Technology (Second Edition), 2001, Pages 106-107.
- [5] H.A. Elhadari, H.A. Patel, D.L. Chena,W. Kasprzak; Tensile and fatigue properties of a cast aluminum alloy with Ti, Zr and V additions; Materials Science and Engineering A 528 (2011) 8128–8138.
- [6] R. S. Rana, Rajesh Purohit, and S Das; Reviews on the Influences of Alloying elements on the Microstructure and Mechanical Properties of Aluminum; International Journal of Scientific and Research Publications, Volume 2, Issue 6, June 2012 .
- [7] G.Timelli, E.Fiorese, Metodi di neutralizzazione del Fe in leghe Al-Si da fonderia, La Metallurgia Italiana n.3 Marzo (2011) 9-23.
- [8] GUO Hong-min, YANG Xiang-jie; Preparation of semi-solid slurry containing fine and globular particles for wrought aluminum alloy 2024; Trans. Nonferrous Met. SOC. China 17(2007) 799-804.
- [9] D.G. Eskin, Suyitno, L. Katgerman; Mechanical properties in the semi-solid state and hot tearing of aluminium alloys; Progress in Materials Science 49 (2004) 629–711.
- [10] Emma Sjölander, Salem Seifeddine; The heat treatment of Al–Si–Cu–Mg casting alloys; Journal of Materials Processing Technology 210 (2010) 1249–1259.
- [11] M.F. Ibrahim, A.M. Samuel, F.H. Samuel, A preliminary study on optimizing the heat treatment of high strength Al-Cu-Mg-Zn alloys, Materials and Design 57 (2014) 342–350.
- [12] Higgins R.A., Engineering metallurgy, Second Edition, ELBS, ISBN 034018468X, (1986).
- [13] J.S. Robinson, D.A. Tanner, C.E. Truman, A.M. Paradowska, R.C.Wimpory; The influence of quench sensitivity on residual stresses in the aluminium alloys 7010 and 7075; Materials Characterization 65 (2012) 73 – 8 5.
- [14] Jasim M. Salman, Shaymaa Abbas Abd Alsada and Khadim F. Al-Sultani; Improvement Properties of 7075-T6 Aluminum Alloy by Quenching in 30% Polyethylene Glycol and Addition 0.1%B; Research Journal of Material Sciences Vol. 1(6), 12-17, July (2013).
- [15] Diana A. Lados, Diran Apelian, Libo Wang; Minimization of residual stress in heat-treated Al–Si–Mg cast alloys using uphill quenching: Mechanisms and effects on static and dynamic properties; Materials Science and Engineering A 527 (2010) 3159–3165.
- [16] William D. Callister, Jr.; Fundamentals of Materials Science and Engineering; Fifth edition.
- [17] D.L. Cocks, A proposed simple qualitative classification for die-casting defects, Proc. Die-Casting Conference, Montreaux (1996), p. 19/1.
- [18] J. Campbell, R.A. Harding, Casting Technology, in TALAT 2.0 cd-rom, EEA, Brussels (2000).
- [19] Manuale della difettologia nei getti pressocolati, E.Gariboldi – F.Bonollo – P.Parona, Associazione Italiana di Metallurgia.
- [20] S.B. Ghanti, E.A.Druschitz, A.P. Druschitz, J.A.Griffin; The effects of soilidification underpressure on the porosity and mechanical properties of A206-T6 cast aluminum alloy; Paper 11-048 page 1-8 AFS proceedings 2011 America Foundry Society Schaumburg, IL USA.
- [21] H.R. Ammar, A.M. Samuel, F.H. Samuel; Porosity and the fatigue behavior of hypoeutectic and hypereutectic aluminum–silicon casting alloys; International Journal of Fatigue 30 (2008) 1024–1035.
- [22] Bita Ghaffari, George Mozurkewich, Larry A. Godlewski, JacobW. Zindel; Ultrasonic characterization of shrinkage microporosity in aluminum castings; Ultrasonics 41 (2004) 699–707.
- [23] C. Tian, J. Law, J. van der Touw, M. Murray, J.-Y. Yao, D. Graham, D. St. John; Effect of melt cleanliness on the formation of porosity defects in automotive aluminium high pressure die castings; Journal of Materials Processing Technology 122 (2002) 82–93.
- [24] O. Majidi, S.G. Shabestari, M.R. Aboutalebi; Study of fluxing temperature in molten aluminum refining process; Journal of Materials Processing Technology 182 (2007) 450–455.
- [25] Yun Wang, Hu-Tian Li, Zhongyun Fan; Oxidation of Aluminium Alloy Melts and Inoculation by Oxide Particles; Trans Indian Inst Met DOI 10.1007/s12666-012-0194-x.
- [26] J.Campbell, Castings, Butterworth, Oxford, 1991.
- [27] D.Dispinar, J.Campbell, International Journal of cast metal research 17,2004, 280-286.
- [28] Salem Seifeddine, Torsten Sjögren and Ingvar L Svensson; Variations in microstructure and mechanical properties of cast aluminum EN AC 43100 alloy; Metallurgical Science and Technology 12-22.
- [29] J. Hirsch, T. Al-Samman; Superior light metals by texture engineering: Optimized aluminum and magnesium alloys for automotive applications; Acta Materialia 61 (2013) 818–843.
- [30] European Aluminium Association.
- [31] Ju¨rgen Hirsch; Aluminium in Innovative Light-Weight Car Design; Materials Transactions, Vol. 52, No. 5 (2011) pp. 818 to 824.
- [32] Jürgen HIRSCH; Recent development in aluminium for automotive applications; Trans. Nonferrous Met. Soc. China 24(2014) 1995−2002.
- [33]J.Hirsch; Aluminium in innovative light-weight car design; Proc Innovative Development for Lightweight Vehicle Structures; Wolfsburg, Germany: VW, 2009: 101.
- [34] SLC Super Light Car Project [EB/OL]. http://www.superlightcar.com.
- [35] K. Shimizu, R.C. Furneaux, G.E. Thompson, G.C. Wood, A. Gotoh and K. Kobayashi; On the nature of “easy paths” for the diffusion of oxygen in thermal oxide films on aluminium; Oxidation of Metals vol.35, Nos.5/6 pp.427-439, 1991.
- [36] J.R. Davis; Corrosion of aluminum and aluminum alloys; Edited by J.R.Davis ASM International.
- [37] N. L. Sukiman, X. Zhou, N. Birbilis, A.E. Hughes, J. M. C. Mol, S. J. Garcia, X. Zhou and G. E. Thompson; Aluminium Alloys - New Trends in Fabrication and Applications; Edited by Zaki Ahmad, Intech.
- [38] G. M. Scamans, N. Birbilis, R. G. Buchheit; Corrosion of Aluminum and its Alloys; 2010 Elsevier B.V..
- [39] M.G. Alvarez, J.R. Galvele; Pitting Corrosion; Shreir's Corrosion Volume 2, 2010, Pages 772-800.
- [40] M.A. Pech-Canul, M.I. Pech-Canul, P. Bartolo-Pérez, M. Echeverría; The role of silicon alloying addition on the pitting corrosion resistanceof an Al-12 wt.%Si alloy; Electrochimica Acta 140 (2014) 258–265.
- [41] S. Jain; Corrosion and protection of heterogeneous cast Al–Si (356) and Al–Si–Cu–Fe (380) alloys by chromate and cerium inhibitors; The Ohio State University, Ohio, USA, 2006.
- [42] K. Nisancioglu; Electrochemical behavior of aluminum-base intermetallics containing iron; J. Electrochem. Soc. 137 (1990) 69–77.
- [43] K.A. Yasakau, M.L. Zheludkevich, S.V. Lamaka, M.G.S. Ferreira; Role of intermetallic phases in localized corrosion of AA5083; Electrochim. Acta 52 (2007) 7651–7659.
- [44] R. Arrabal, B. Mingo, A. Pardo, M. Mohedano, E. Matykina, I. Rodriguez; Pitting corrosion of rheocast A356 aluminium alloy in 3.5 wt.% NaCl solution; Corrosion Science 73 (2013) 342–355.
- [45] H.C. Fang, H. Chao, K.H. Chen; Effect of recrystallization on intergranular fracture and corrosion of Al–Zn–Mg–Cu–Zr alloy; Journal of Alloys and Compounds 622 (2015) 166–173.
- [46] Fengxuan Song, Xinming Zhang, Shengdan Liu, Qi Tan, Dongfeng Li; The effect of quench rate and overageing temper on the corrosion behaviour of AA7050; Corrosion Science xxx (2013).
- [47] Lanping Huang, Kanghua Chen, Song Li; Influence of grain-boundary pre-precipitation and corrosion characteristics of inter-granular phases on corrosion behaviors of an Al–Zn–Mg–Cu alloy; Materials Science and Engineering B 177 (2012) 862– 868.
- [48] Amjad Saleh El-Amoush; Intergranular corrosion behavior of the 7075-T6 aluminum alloy under different annealing conditions; Materials Chemistry and Physics 126 (2011) 607-613.
- [49] W.J. Liang, P.A. Rometsch, L.F. Cao, N. Birbilis; General aspects related to the corrosion of 6xxx series aluminium alloys:Exploring the influence of Mg/Si ratio and Cu; Corrosion Science 76 (2013) 119–128.
- [50] Starink M.J., Li X M.; A model for electrical conductivity of peak-aged and overaged Al−Zn−Mg−Cu alloys; [J]. Metallurgical and Materials Transactions A, 2003, 34(4): 899−911.
- [51] Chen Song-yi, Chwn Kang-hua, Peng Guo-sheng, Liang Xin, Chen Xue-hai; Effect of quenching rate on microstructure and stress corrosion cracking of 7085 aluminum alloy; [J]. Transactions of Nonferrous Metals Society of China, 2012, 22(1): 47−52.
- [52] Knight S. P., Birbilis N., Muddle B. C., Trueman A. R., Lynch S. P.; Correlations between intergranular stress corrosion cracking, grain-boundary microchemistry, and grain-boundary electrochemistry for Al−Zn−Mg−Cu alloys; [J]. Corrosion Science, 2010, 52(12): 4073−4080.
- [53] Andreatta F., Terryn H., de Wit J. H. W.; Effect of solution heat treatment on galvanic coupling between intermetallics and matrix in AA7075-T6; [J]. Corrosion Science, 2003, 45(8): 1733−1746.
- [54] Zhang Ping, Li Qi, Zhao Jun-jun, Zeng Qing-qiang.; Analysis of secondary phases and measurement of volta potential of 7A52aluminum alloy; [J]. The Chinese Journal of Nonferrous Metals, 2011, 21(6): 1252−1257.
- [55] Venugopal A., Panda R., Manwatkar S., Sreekumar K., Rama Krishna L., Sundararajan G.; Effect of micro arc oxidation treatment on localized corrosion behaviour of AA7075 aluminum alloy in 3.5% NaCl solution; [J]. Transactions of Nonferrous Metals Society of China, 2012, 22(3): 700−710.
- [56] Huan She, Wei Chu, Da Shu, Jun Wang, Bao-de Sun; Effects of silicon content on microstructure and stress corrosion cracking resistance of 7050 aluminum alloy; Trans. Nonferrous Met. Soc. China 24(2014) 2307−2313.
- [57] S. Geng, S. Joshi, W. Pinc, W.G. Fahrenholtz, M.J. O’Keefe, T.J. O’Keefe, P. Yu; Influence of processing parameters on cerium based conversion coatings; in: Proc. Tri-Service Corrosion Conference, Denver, CO, NACE International, 2007,p. 10.
- [58] B. Valdez, S. Kiyota, M. Stoytcheva, R. Zlatev, J.M. Bastidas; Cerium-based conversion coatings to improve the corrosion resistance of aluminium alloy 6061-T6; Corrosion Science 87 (2014) 141–149.
- [59] Peter Plagemann, Joerg Weise, Anja Zockoll; Zinc–magnesium-pigment rich coatings for corrosion protection of aluminum alloys; Progress in Organic Coatings 76 (2013) 616– 625.
- [60] Du Nan, Wang Shuai-xing, Zhao Qing, Shao Zhi-song; Effects of boric acid on microstructure and corrosion resistance of boric/sulfuric acid anodic film on 7050 aluminum alloy; Trans. Nonferrous Met. Soc. China 22(2012) 1655-1660.
- [61] J. Singh-Beemat, J.O. Iroh; Effect of clay on the corrosion inhibition and dynamic mechanical properties of epoxy ester–polyurea–polysiloxane hybrid coatings; Polym. Eng. Sci. (2012).
- [62] J. Singh-Beemat, J.O. Iroh; Characterization of corrosion resistant clay/epoxy ester composite coatings and thin films; Progress in Organic Coatings 74 (2012) 173–180.
- [63] Jaspreet Singh-Beemat, Jude O. Iroh, Linqian Feng; Mechanism of corrosion protection of aluminum alloy substrate byhybrid polymer nanocomposite coatings; Progress in Organic Coatings 76 (2013) 1576– 1580.
- [64] E. Tillová, E. Ďuriníková, M. Chalupová; Structural analysis of secondary AlZn10Si8Mg cast alloy; Acta Metallurgica Slovaca, Vol. 17, 2011, No. 1, p. 4-10.
- [65] E. Tillová, E. Ďuriníková, M. Chalupová; Characterization of phases in secondary AlZn10Si8Mg cast alloy; Materials Engineering - Materiálové inžinierstvo 18 (2011) 1-7.
- [66] http://www.dietermann-guss.de/_pdf-Dateien/IN%20FORM_01_12%20eng.pdf.
- [67] M.Rosso, I.Peter, C.Castella , R.Molina; Investigation on AlZn10Si8Mg alloys for automotive application; Metallurgical Science and Technology Vol. 31-1 - Ed. 2013.
- [68] M.Rosso, I.Peter, C.Castella , R.Molina; Properties of AlZn10Si8Mg Alloys for High Performances Application; Light metals 2014 p.213-218.
- [69] I.Peter, M.Rosso, C.Castella, R.Molina; Self-hardening alloys for automotive application; Materials Science Forum Vols. 794-796 (2014) pp 1221-1226.
- [70] http://www.rheinfelden-alloys.eu/.
- [71] C. Y. Song, J. Lee; Reliability-based design optimization of knuckle component using conservative method of moving least squares meta-models; Probabilistic Engineering Mechanics 26 (2011) 364–379.
- [72] J. L. Murray; The Al-Zn (Aluminum-Zinc) System; Bulletin of Alloy Phase Diagrams Vol. 4 No. 1 1983.
- [73] G.Timelli, E.Fiorese; Metodi di neutralizzazione del Fe in leghe Al-Si da fonderia; La Metallurgia Italiana n.3 Marzo 2011 9-23.
- [74] C. Mascré, Fonderie, 108 (1955), 4330-4334.
- [75] R. Arrabal, B. Mingo, A. Pardo, M. Mohedano, E. Matykina, I. Rodriguez, Pitting corrosion of rheocast A356 aluminium alloy in 3.5 wt.% NaCl solution, Corrosion Science 73 (2013) 342–355.
- [76] Kiryl A. Yasakau, Mikhail L. Zheludkevich ,Sviatlana V. Lamaka, Mario G.S. Ferreira; Role of intermetallic phases in localized corrosion of AA5083; Electrochimica Acta 52 (2007) 7651–7659.
- [77] V.A. Hosseini, S.G. Shabestari, R. Gholizadeh; Study on the effect of cooling rate on the solidification parameters, microstructure, and mechanical properties of LM13 alloy using cooling curve thermal analysis tecjnique; Materials and Design 50 (2013) 7–14.
- [78] Deepak Singla1, S.R. Mediratta; Evaluation of mechanical properties of Al 7075-fly ash composite material; International Journal of Innovative Research in Science, Engineering and Technology Vol. 2, Issue 4, April 201.
- [79] Determination of resistance to IGC of solution heat-treatable aluminium alloys, Standard BS11846:1995, Brithish Standards Institution (1995).
9. 저작권:
- 본 자료는 "Christian Castella"의 논문: "Self hardening aluminum alloys for automotive applications"을 기반으로 합니다.
- 논문 출처: [DOI URL]
본 자료는 상기 논문을 요약한 것으로, 상업적 목적으로 무단 사용하는 것을 금지합니다.
Copyright © 2025 CASTMAN. All rights reserved.