본 논문 요약은 ['Int J Adv Manuf Technol']에 발표된 ['Development of a die design system for die casting'] 논문을 기반으로 작성되었습니다.
1. 개요:
- 제목: 다이캐스팅 금형 설계 시스템 개발 (Development of a die design system for die casting)
- 저자: Y. K. Woon, K. S. Lee
- 발행 연도: 2004년
- 발행 학술지/학회: Int J Adv Manuf Technol (International Journal of Advanced Manufacturing Technology, 국제 첨단 제조 기술 저널)
- 키워드: 다이캐스팅 (Die casting), 금형 설계 시스템 (Die design system), 피처 기반 (Feature-based), 구속 조건 기반 (Constraint-based), 파라메트릭 설계 (Parametric design), B-rep 모델 (B-rep model)
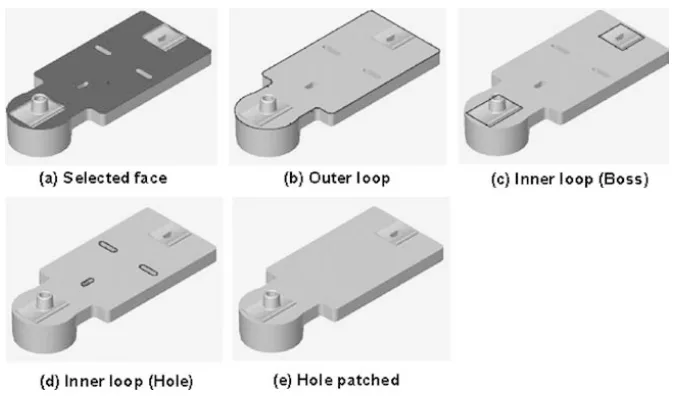
2. 연구 배경:
연구 주제 배경:
다이캐스팅 공정은 정밀한 치수와 선명한 형태의 금속 부품을 제조하는 주요 방법 중 하나입니다. 다이캐스팅 금형 설계는 여러 단계를 거치는 과정으로, 본질적으로 많은 시간이 소요됩니다. 초기 금형 설계가 만족스러운 수준에 도달하기까지 복잡성으로 인해 반복적인 수정이 필요하며, 이는 설계 주기를 더욱 연장시킵니다.
기존 연구 현황:
기존 연구는 개별 금형 요소의 자동 또는 반자동 설계, 특히 게이팅 시스템에 초점을 맞추어 진행되었습니다. P-Q² 기법과 피처 기반 파라메트릭 설계를 활용한 게이팅 시스템 프로토타입 설계, 그리고 압력 다이캐스팅용 게이팅 및 러너 시스템 설계를 전문으로 하는 DiEdiFice와 같은 상용 애플리케이션이 그 예입니다. 그러나 DiEdiFice는 이젝터 및 코어 캐비티 인서트 생성까지는 지원하지 않습니다. AutoCAD 기반과 같은 기존의 완전한 금형 설계 시스템은 단순 형상 및 언더컷이 없는 단일 인상 금형에만 적용이 제한됩니다. 시뮬레이션 분석을 사용하여 금형 형상 및 공정 매개변수 최적화를 위한 통합 CAD/CAE 시스템 연구도 진행되었습니다. IMOLD와 같은 특수 소프트웨어 패키지는 반자동 사출 금형 설계를 위해 존재하지만, 다이캐스팅 게이팅 시스템의 복잡성 증가로 인해 다이캐스팅 설계에는 직접적으로 적용하기 어렵습니다.
연구의 필요성:
다이캐스팅 산업은 다양한 금형 설계 단계를 통합하고 설계 편집을 용이하게 하는 애플리케이션 소프트웨어로부터 큰 혜택을 얻을 수 있습니다. 3D CAD가 금형 설계에 점점 더 많이 채택됨에 따라 시각화를 향상시키고 설계 수정 작업을 간소화하는 시스템의 필요성이 강조됩니다. 따라서 금형 설계 시간을 단축하는 컴퓨터 지원 금형 설계 시스템 개발이 매우 중요합니다.
3. 연구 목적 및 연구 질문:
연구 목적:
본 연구의 실질적인 목표는 두 가지입니다.
(1) 다양한 금형 설계 단계를 통합하는 시스템 개발.
(2) 금형 설계 과정 중 및 이후에 다이캐스팅 설계 편집을 용이하게 하는 것.
핵심 연구:
본 연구는 사용자 친화적인 다이캐스팅 금형용 컴퓨터 지원 설계 시스템을 만드는 데 중점을 둡니다. 이 시스템은 숙련된 설계자와 초보 설계자 모두 제품 부품 모델로부터 효율적으로 금형을 설계할 수 있도록 하는 것을 목표로 합니다.
연구 가설:
피처 기반 및 구속 조건 기반 모델링, 파라메트릭 설계, B-rep 모델로부터의 기하학적/위상 정보 추출 기술을 통합한 금형 설계 시스템은 다이캐스팅 금형 설계 프로세스의 자동화 및 효율성, 품질, 비용 효율성을 향상시킬 수 있다는 가설을 설정합니다.
4. 연구 방법론
연구 설계:
본 연구는 다음 접근 방식을 결합합니다.
(1) 피처 기반 및 구속 조건 기반 모델링 (Feature-based and constraint-based modelling).
(2) 파라메트릭 설계 (Parametric design).
(3) B-rep (Boundary Representation, 경계 표현) 모델로부터의 기하학적 및 위상 정보 추출 기술 (Geometric and topological information extraction technique).
자료 수집 방법:
본 논문에서는 전통적인 의미의 경험적 데이터 수집과 같은 특정 자료 수집 방법을 명시적으로 자세히 설명하지 않습니다. 그러나 프로토타입 시스템의 개발 및 검증에는 시스템 성능, 사용자 상호 작용 및 설계 결과와 관련된 데이터가 암묵적으로 포함되지만, 이러한 데이터는 논문 내에서 공식적인 데이터 세트로 제시되지는 않습니다. 푸시 버튼 하우징의 사례 연구는 시스템의 기능을 보여주는 데모 데이터의 형태를 제공합니다.
분석 방법:
본 논문은 금형 설계 시스템의 개발 및 기능 시연에 중점을 둡니다. 분석은 주로 질적이며, 설계 단계 통합, 설계 편집 용이성, 금형 설계 작업 자동화에 대한 시스템의 능력을 평가합니다. 사례 연구는 시스템의 실제 적용 및 워크플로우의 실례를 제공합니다. 설계 시간 단축 또는 품질 향상과 같은 정량적 성능 지표는 본 논문에서 명시적으로 측정하거나 분석하지 않습니다.
연구 대상 및 범위:
본 연구는 일반적인 다이캐스팅 금형 설계에 적용 가능한 프로토타입 금형 설계 시스템 개발에 초점을 맞춥니다. 시스템의 범위는 캐비티 인서트, 코어 슬라이드, 금형 베이스, 게이팅 시스템, 이젝터 시스템 및 표준 부품을 갖춘 금형 설계를 포함합니다. 시스템은 SolidWorks 2001 플랫폼에서 Visual C++를 사용하여 구현되었습니다. 사례 연구는 푸시 버튼 하우징 금형 설계에 대한 시스템의 적용을 보여줍니다.
5. 주요 연구 결과:
핵심 연구 결과:
- 7개의 개별 모듈로 구성된 다이캐스팅용 프로토타입 컴퓨터 지원 금형 설계 시스템이 개발되었습니다.
- 이 시스템은 주조 설계부터 이젝터 시스템 설계까지 다양한 금형 설계 단계를 단일 환경 내에 통합합니다.
- 시스템은 피처 기반 및 구속 조건 기반 모델링, 파라메트릭 설계 및 B-rep 모델 정보 추출을 통합합니다.
- 시스템에는 슬라이드, 게이팅 요소 및 이젝터 핀과 같은 구성 요소에 대한 사용자 정의 다이캐스팅 피처 라이브러리가 포함되어 있습니다.
- 파팅 표면 생성을 위한 "홀 패칭 (hole patching)"과 같은 작업 알고리즘이 기하학적 및 위상 정보를 사용하여 구현되었습니다.
- 시스템 아키텍처는 모듈식으로, 프로젝트 관리, 캐비티 인서트 빌더, 금형 베이스 설계, 게이팅 시스템 구성, 이젝터 시스템 구성, 코어 슬라이드 설계 및 표준 부품 통합을 허용합니다.
- 사례 연구를 통해 캐비티 인서트, 코어 슬라이드, 게이팅 및 러너 시스템, 금형 베이스 및 이젝터 시스템을 포함한 푸시 버튼 하우징용 2-캐비티 금형을 설계하는 시스템의 능력을 입증했습니다.
데이터 해석:
개발된 프로토타입 시스템은 다양한 다이캐스팅 금형 설계 단계를 응집력 있는 CAD 환경으로 통합하는 것이 가능하다는 것을 보여줍니다. 피처 기반 및 구속 조건 기반 접근 방식은 파라메트릭 설계와 결합되어 효율적이고 유연한 금형 설계 및 수정이 가능합니다. 모듈식 아키텍처와 사용자 정의 피처 라이브러리는 시스템의 사용 편의성과 다양한 금형 설계 요구 사항에 대한 적응성을 향상시킵니다. 사례 연구는 복잡한 다이캐스팅 금형 설계에 대한 시스템의 실제 적용을 보여줍니다.
그림 목록:
- Fig. 1 다이캐스팅 금형 설계 시스템의 순서도 (Flowchart of the die design system for die casting)
- Fig. 2 위상 구속 조건의 예 - 탑 플레이트의 상면과 리더 핀의 상면 정렬 (Example of a topological constraint—top face of leader pin align with top face of top plate)
- Fig. 3a-e 그래픽 삽화: "홀 패칭 (hole patching)" 알고리즘 (Graphical illustration: "hole patching" algorithm)
- Fig. 4 시스템 아키텍처 및 메뉴 옵션 (System architecture and menu options)
- Fig. 5 프로젝트 관리자 모듈 및 새 프로젝트 인터페이스 (Project manager module and the new project interface)
- Fig. 6a,b 캐비티 인서트 빌더 모듈. a 볼스터 빌더 인터페이스. b 볼스터 브레이커 인터페이스 (Cavity insert builder module. a Bolster builder interface. b Bolster breaker interface)
- Fig. 7a,b 게이팅 시스템 설계자 모듈. a 게이트 인터페이스. b 오버플로우 인터페이스 (Gating system designer module. a Gates interface. b Overflows interface)
- Fig. 8a,b 금형 베이스 설계자 모듈. a 로드 N 구성 인터페이스. b 두께 인터페이스 (Die base designer module. a Load N configure interface. b Thickness interface)
- Fig. 9 a 슬라이드 코어 설계자 모듈: 헤드 설계 인터페이스. b 표준 부품 인터페이스 (Slide core designer module: head design interface. b Standard component interface)
- Fig. 10 푸시 버튼 하우징 (Push-button housing)
- Fig. 11a-c 캐비티 인서트 빌더: a 파팅 면 생성기 인터페이스. b 커버 캐비티 인서트. c 이젝터 캐비티 인서트 (Cavity insert builder: a Parting face generator interface. b Cover cavity insert. c Ejector cavity insert)
- Fig. 12 a 언더컷 형상. b 코어 슬라이드 헤드 (Undercut feature. b Core slide head)
- Fig. 13a,b 코어 슬라이드 설계자: a 바디 설계 인터페이스. b 코어 슬라이드 메커니즘이 있는 캐비티 인서트 (Core slide designer: a Body design interface. b Cavity inserts with core slides mechanism)
- Fig. 14 2-캐비티 레이아웃, 캐비티 간 거리 500mm (2-cavity layout with 500 mm distance between cavity inserts)
- Fig. 15 a 게이팅 시스템 - 비스킷; 게이트; 러너; 오버플로우. b 확대된 캐비티 인서트 뷰 (Gating system-biscuit; gate; runner; overflow. b Enlarged view of cavity insert)
- Fig. 16 DME 금형 베이스 D 시리즈 (DME Die base D series)
- Fig. 17 a 일반적인 이젝터 핀. b 강화된 이젝터 핀 (Typical ejector pin. b Reinforced ejector pin)
- Fig. 18 a 이젝터 시스템 구성자 인터페이스. b 2가지 유형의 10개 이젝터 핀이 있는 캐비티 인서트 (Ejector system constructor interface. b Cavity insert with the 10 ejector pins of two different types)
- Fig. 19 제안된 시스템을 사용한 푸시 버튼 케이스 다이캐스팅 금형 설계 (Die design for die casting of the push button casing using the proposed system)
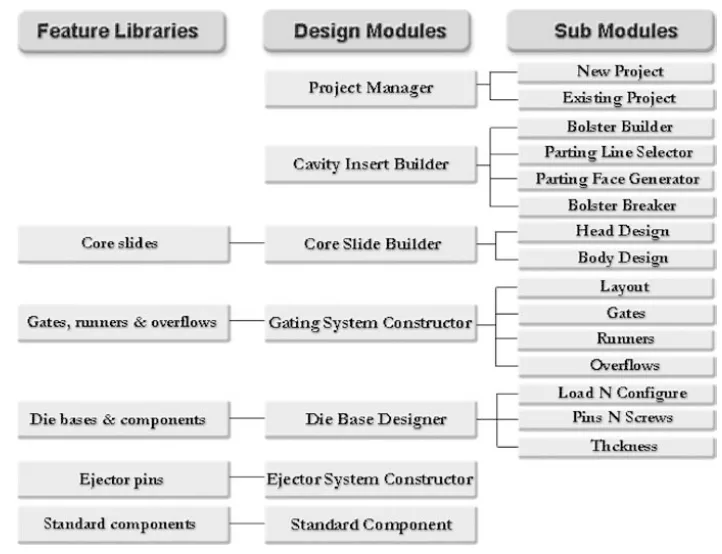

6. 결론:
주요 결과 요약:
본 연구는 다이캐스팅용 프로토타입 컴퓨터 지원 금형 설계 시스템을 성공적으로 개발했습니다. 이 시스템은 피처 기반 및 구속 조건 기반 모델링, 파라메트릭 설계 및 B-rep 모델 정보를 통합하여 금형 설계 프로세스를 자동화하고 간소화합니다. 초기 프로젝트 설정부터 이젝터 시스템 설계까지 금형 설계의 모든 중요한 단계를 포괄하는 모듈과 사용자 정의 가능한 피처 라이브러리가 포함되어 있습니다. 사례 연구를 통해 복잡한 다이캐스팅 금형 설계에 대한 시스템의 실제 적용을 입증했습니다.
연구의 학문적 의의:
본 연구는 다단계 설계를 통합하고 고급 CAD 기술을 활용하는 포괄적인 시스템을 제시함으로써 컴퓨터 지원 금형 설계 분야에 기여합니다. 피처 기반 및 구속 조건 기반 모델링의 적용과 기하학적 및 위상 정보 추출은 복잡한 금형 설계 작업을 자동화하기 위한 강력한 프레임워크를 제공합니다. 모듈식 아키텍처와 사용자 정의 가능한 피처 라이브러리는 다이캐스팅 금형 설계를 위한 유연하고 적응 가능한 플랫폼을 제공합니다.
실용적 의미:
개발된 금형 설계 시스템은 다이캐스팅 산업에 상당한 실용적 의미를 갖습니다. 설계 단계를 통합하고 설계 수정 작업을 용이하게 함으로써 시스템은 금형 설계 리드 타임을 크게 단축하고 설계 품질을 향상시키며 설계 비용을 절감할 수 있는 잠재력을 가지고 있습니다. 사용자 친화적인 인터페이스와 모듈식 설계는 시스템을 숙련된 금형 설계자와 초보 금형 설계자 모두가 접근할 수 있도록 하여 금형 설계 워크플로우의 생산성과 효율성을 향상시킵니다.
연구의 한계점
프로토타입 시스템에 포함된 피처 라이브러리는 포괄적이지 않으며, 더 넓은 범위의 다이캐스팅 부품 및 설계 시나리오를 포괄하기 위해 추가 확장이 필요합니다. 또한 현재 시스템에는 다이캐스팅 금형 설계의 중요한 측면인 냉각 시스템 설계 모듈이 통합되어 있지 않습니다. 시스템 성능은 단일 사례 연구를 통해 입증되었으며, 시스템의 견고성과 일반적인 적용 가능성을 완전히 평가하려면 다양하고 복잡한 금형 설계를 통한 추가 검증이 필요합니다. 설계 시간 단축 및 품질 향상에 대한 정량적 지표는 공식적으로 평가되지 않았습니다.
7. 향후 후속 연구:
- 후속 연구 방향
향후 연구 방향은 다음과 같습니다.- 더 넓은 범위의 다이캐스팅 부품 및 설계 변형을 포괄하도록 피처 라이브러리 확장.
- 냉각 시스템 설계 모듈을 개발하여 시스템에 통합.
- 캐비티 충전 시간 분석, 벤팅 분석 및 게이팅 시스템 최적화를 위한 계산 능력을 시스템에 강화.
- 설계 시간 단축, 품질 향상 및 시스템 견고성을 정량화하기 위해 다양하고 복잡한 금형 설계를 사용하여 포괄적인 성능 평가 수행.
- 추가 탐구가 필요한 영역
다음과 같은 영역에서 추가 탐구가 필요합니다.- 공정 시뮬레이션 및 설계 최적화를 위한 CAE 분석 도구를 시스템 내에 통합.
- 특히 복잡한 형상에 대한 자동 파팅 라인 및 파팅 표면 생성을 위한 보다 진보된 알고리즘 개발.
- 금형 설계 프로세스를 더욱 자동화하고 최적화하기 위한 지식 기반 엔지니어링 원칙 및 설계 규칙 통합.
- 사용자 경험 및 시스템 적응성을 개선하기 위한 사용자 인터페이스 개선 및 사용자 정의 옵션 개발.
8. 참고 문헌:
- [1] Wu SH, Lee KS, Fuh JY (2002) Feature-based parametric design of a gating system for a die-casting die. Int J Adv Manuf Technol 19:821-829
- [2] http://www.diedifice.com
- [3] Choi JC, Kwon TH, Park JH, Kim JH, Kim CH (2002) A study on development of a die design system for die-casting. Int J Adv Manuf Technol 20:1-8
- [4] Zhang WS, Xiong SM, Liu BC (1997) Study on a CAD/CAE system of die casting. J Mater Process Tech 63:707-711
- [5] Lee KS, Fuh JYH, Zhang YF, Nee AYC, Li Z (1997) IMOLD: An intelligent plastic injection mold design and assembly system. In: Proceedings of the 4th international conference on die and mold technology, 4-16 June 1997, Kuala Lumpur, Malaysia, pp 30-37
- [6] Shimizu S, Numao M (1997) Constraint-based design for 3D shapes. Artif Intell 91:51-69
- [7] Roller D (1991) An approach to computer-aided parametric design. Comput Aided Des 23(5):385-391
- [8] Anderl R (1994) Parametrics for product modelling. J. Hoschek and Teubner, Stuttgart
- [9] Herman EA (1996) Gating die casting dies. North American Die Casting Association
- [10] Chen YM, Wei CL (1997) Computer-aided feature-based design for net shape manufacturing. Comput Integr Manuf Syst 10(2):147-164
- [11] Hoffmann CM, Joan-Arinyo R (1998) On user-defined features. Comput Aided Des 30(5):321-332
9. 저작권:
- 본 자료는 "Y. K. Woon, K. S. Lee"의 논문: "Development of a die design system for die casting"을 기반으로 합니다.
- 논문 출처: DOI 10.1007/s00170-003-1754-3
본 자료는 위 논문을 기반으로 요약되었으며, 상업적 목적으로 무단 사용하는 것을 금지합니다.
Copyright © 2025 CASTMAN. All rights reserved.