본 페이퍼 요약은 [Advanced metals for aerospace and automotive use] ([출판사: Materials Science and Engineering A])에 게재된 논문을 기반으로 작성되었습니다.
1. 개요:
- 제목: Advanced metals for aerospace and automotive use
- 저자: F. H. Froes
- 출판 연도: 1994년
- 출판 저널/학회: Materials Science and Engineering A
- 키워드: 경량 금속, 항공우주, 자동차, 알루미늄, 마그네슘, 티타늄, 티타늄 알루미나이드, 합금 설계, 제조 공정, 금속 매트릭스 복합재료, 용접 접합
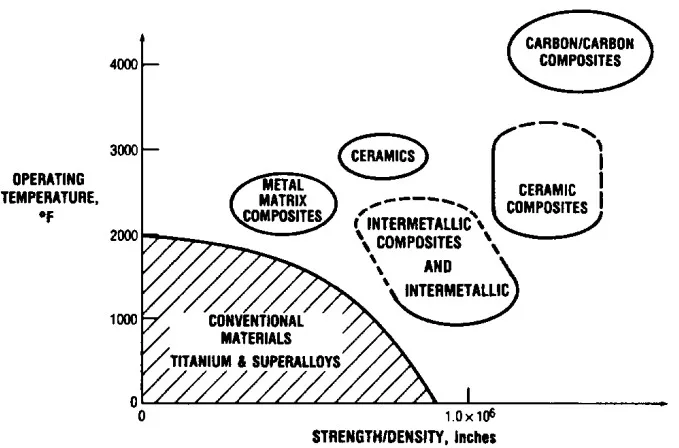
2. 연구 배경:
- 연구 주제의 사회적/학문적 맥락:
- 항공우주 및 자동차 산업에서는 성능 향상을 위해 기존 재료보다 향상된 특성을 가진 재료가 요구되고 있습니다. 특히 자동차 산업에서는 차체 경량화와 파워트레인 효율 향상이 중요한 과제입니다.
- 기존의 미세 구조-물성 관계 연구 중심의 접근 방식에서 벗어나, 새로운 합성 및 가공 방법을 통해 재료 특성을 향상시키는 연구의 필요성이 대두되었습니다.
- 기존 연구의 한계:
- 전통적인 재료 개발 방식은 미세 구조 제어에 집중되어 왔지만, 재료의 근본적인 성능 향상에는 한계가 있었습니다.
- 기존 경량 금속 재료는 강도, 내열성, 연성, 파괴 인성 등의 특성을 동시에 만족시키기 어려웠습니다.
- 연구의 필요성:
- 항공우주 및 자동차 산업의 요구 사항을 충족시키기 위해 밀도와 비용을 최소화하면서 강도, 내열성, 연성, "forgiveness"(파괴 인성, 피로 균열 성장 속도 등)과 같은 특성을 극대화하는 새로운 재료 개발이 필요합니다.
- 특히 알루미늄, 마그네슘, 티타늄 및 티타늄 알루미나이드와 같은 경량 금속은 밀도가 낮아 항공우주 및 자동차 응용 분야에 매우 매력적인 소재입니다.
3. 연구 목적 및 연구 질문:
- 연구 목적:
- 항공우주 및 자동차 응용 분야에 적합한 고급 금속 재료의 개발 동향과 합성 및 가공 기술을 조사하고, 경량 금속의 물리적, 기계적 특성을 향상시키는 다양한 방법을 제시하는 것을 목표로 합니다.
- 핵심 연구 질문:
- 항공우주 및 자동차 산업에서 요구하는 재료 특성은 무엇인가?
- 경량 금속(알루미늄, 마그네슘, 티타늄, 티타늄 알루미나이드)의 특성을 향상시키기 위한 합성 및 가공 방법은 무엇인가?
- 고급 금속 재료의 실제 응용 사례는 무엇이며, 향후 연구 방향은 어떠한가?
- 연구 가설:
- 새로운 합성 및 가공 기술을 적용하면 기존 재료의 한계를 극복하고 항공우주 및 자동차 산업의 요구 사항을 충족하는 고급 경량 금속 재료를 개발할 수 있을 것이다.
4. 연구 방법론
- 연구 설계:
- 문헌 연구 및 기술 동향 분석: 항공우주 및 자동차 분야의 고급 금속 재료 관련 연구 논문, 기술 보고서, 특허 등을 조사하고 분석합니다.
- 기술 검토 및 분류: 다양한 경량 금속 재료의 합성 및 가공 기술을 검토하고, 각 기술의 특징, 장단점, 적용 분야 등을 분류합니다.
- 사례 연구 분석: 고급 금속 재료의 항공우주 및 자동차 부품 적용 사례를 분석하여 기술의 실용성을 평가합니다.
- 데이터 수집 방법:
- 학술 데이터베이스 검색 (Materials Science & Engineering A, Elsevier ScienceDirect 등)
- 기술 보고서 및 산업 자료 조사
- 특허 정보 검색
- 분석 방법:
- 기술 동향 분석: 고급 금속 재료 개발 및 응용 분야의 기술 발전 추세를 분석합니다.
- 비교 분석: 다양한 합성 및 가공 기술의 특성 및 성능을 비교 분석합니다.
- 사례 분석: 실제 응용 사례를 통해 고급 금속 재료의 기술적 및 경제적 효과를 분석합니다.
- 연구 대상 및 범위:
- 주요 연구 대상 재료: 알루미늄, 마그네슘, 티타늄, 티타늄 알루미나이드 기반 경량 금속 및 이들의 복합재료
- 주요 연구 범위 기술: 잉곳 및 주조, 급속 응고, 기계적 합금화, 나노 구조 재료 제조 및 활용, 용사 코팅, 증착 공정, 열화학적 처리, 금속 매트릭스 복합재료, 용융 접합
5. 주요 연구 결과:
- 주요 연구 결과:
- 항공우주 및 자동차 산업에서 고성능 재료에 대한 요구가 증가하고 있으며, 특히 경량 금속 재료의 중요성이 강조되고 있습니다.
- 기존의 미세 구조 제어 방식에서 벗어나 새로운 합성 및 가공 기술을 통해 재료 특성을 획기적으로 향상시킬 수 있습니다.
- 다양한 고급 금속 재료 합성 및 가공 기술 (잉곳 및 주조, 급속 응고, 기계적 합금화, 나노 구조 재료, 용사 코팅, 증착 공정, 열화학적 처리, 금속 매트릭스 복합재료, 용융 접합)의 개발 동향과 특징을 상세히 분석하였습니다.
- 각 기술별로 알루미늄, 마그네슘, 티타늄, 티타늄 알루미나이드 등 경량 금속 재료에 적용된 사례와 성능 향상 효과를 제시하였습니다.
- 금속 매트릭스 복합재료는 강성, 강도, 내크리프성을 향상시키는 효과적인 방법이며, 다양한 강화재와 제조 공정을 통해 특성을 최적화할 수 있습니다.
- 용융 접합 기술은 고급 금속 재료를 항공기 및 엔진 구조체에 통합하는 데 필수적이며, 재료의 특성을 유지하거나 향상시키는 접합 기술 개발이 중요합니다.
- 통계적/정성적 분석 결과:
- 표 1: 무게 절감에 따른 달러 가치 (산업별)
- 자동차: $3/파운드 절감
- 상업 항공우주: $300/파운드 절감
- 군용 항공우주: $3000/파운드 절감
- 우주: $30000/파운드 절감
- 표 3: Ti₃Al 유형 티타늄 알루미나이드의 일반적인 특성
- 합금 종류에 따라 UTS, YS, EL(%), Kic, 크리프 파단 시간 등의 물성치가 다름.
- 표 5: 315°C 고온에서 PM/RS 알루미늄 합금의 인장 특성
- Al-Fe-Ce, Al-Fe-Mo, Al-Fe-V-Si, Al-Cr-Zr-Mn 합금의 UTS, YS, El(%) 값 제시.
- 표 6: 기계적 합금화된 알루미늄 합금의 상온 기계적 특성
- MA 및 기존 IM 방식 Al-Li-Mg-O-C, 7075-T73 합금의 UTS, YS, El(%), KIC, 밀도 비교.
- 표 7: 압출재의 일반적인 종방향 특성
- 6061-T6, 6061-T6 (20% SiC), 6061-T6 재료의 UTS, YS, El(%), E 값 제시.
- 표 8: 강화된 ZK60A (Mg-5.5Zn-0.5Zr) 압출재의 기계적 특성
- SiCp, SiCw, B₄Cp 강화재 함량에 따른 UTS, YS, El(%), E 값 비교.
- 표 9: 티타늄 금속 매트릭스 복합재료의 기계적 특성
- Ti-6Al-4V, SCS-6(SiC)/Ti-6Al-4V 복합재료의 UTS(L, T), E(L) 값 비교.
- 데이터 해석:
- 무게 절감은 산업 분야에 따라 경제적 가치가 크게 다르며, 특히 항공우주 분야에서 무게 절감의 중요성이 매우 높습니다.
- 다양한 고급 금속 재료 및 제조 공정을 통해 기존 재료의 성능 한계를 극복하고, 특정 응용 분야에 최적화된 맞춤형 재료 개발이 가능합니다.
- 금속 매트릭스 복합재료는 고강도, 고강성, 내열성이 요구되는 부품에 효과적으로 적용될 수 있습니다.
- 그림 목록:
- Fig. 1. 기본 재료와 엔지니어링 재료의 향상된 추세 밴드 특성 비교.
- Fig. 2. 물성 향상이 구조적 무게에 미치는 영향 (Lockheed 제공).
- Fig. 3. 다양한 재료 등급의 온도 성능 (NASA Lewis 제공).
- Fig. 4. 미래 전투기 전투 영역.
- Fig. 5. 전투기 구조적 무게 감소 추세, 신소재 및 개선된 재료의 중요성 강조.
- Fig. 6. 항공기 종류에 따른 기체 제작 비용 변화.
- Fig. 7. 대형 티타늄 엔진 부품 주조품, HIP 밀도화 (Precision Castparts Corporation 제공).
- Fig. 8. 단조 RS 알루미늄 합금 랜딩 기어 휠 (Allied Signal 제공).
- Fig. 9. MA 알루미늄 합금 플랩 트랙 캡 (INCOmap 제공).
- Fig. 10. PM/등온 단조 방식으로 제작된 Ti-48 at.% Al 베인 (VILS 제공).
- Fig. 11. GE T700 엔진 압축기 케이스, 주조 TiAl로 제작.
- Fig. 12. 티타늄 알루미나이드 복합재 링으로 기존 디스크-스페이서 어셈블리 대체 시 무게 절감 효과.
- Fig. 13. 미국 정부의 연비 규제 요구 사항.
- Fig. 14. 밸브 부품 비용과 엔진 응용 범위 간의 가상 관계.
- Fig. 15. 연료 효율 및 배출에 영향을 미치는 피스톤 어셈블리의 주요 왕복 및 회전 질량 부품.
- Fig. 16. PREP 분말로 핫 등방 압착 성형된 TiAl 피스톤 헤드 (VILS 제공).
- Fig. 17. 블렌디드 엘리멘탈 PM 티타늄 커넥팅 로드.
- Fig. 18. 다양한 질량의 밸브에 대한 속도 함수로서의 엔진 마력 출력.
- Fig. 19. 상부 날개 스킨 플레이트 합금/템퍼 연대기.
- Fig. 20. 전자빔 (좌) 및 플라즈마 (우) 냉각로.
- Fig. 21. 티타늄 합금의 고온 강도 및 크리프 특성.
- Fig. 22. (a) 알루미늄 재료의 내마모성. (b) 내마모성 시험 장치의 개략도.
- Fig. 23. 기계적 합금화 공정의 개략도.
- Fig. 24. Ti₃Al+2Er 분말 압축체의 미세 구조 비교: (a) RS, 850°C 핫 등방 압착; (b) MA, 1000°C 핫 등방 압착.
- Fig. 25. 등축 나노 구조 재료의 개략도: 검은색 원은 결정립 내 원자, 흰색 원은 결정립계 원자 (H. Gleiter 제공).
- Fig. 26. 비정질 MA 분말로 제작된 HIP 처리된 Ti-55at.%Al의 나노 구조 결정립.
- Fig. 27. 용사 코팅된 Al-7075 재료의 향상된 파괴 인성.
- Fig. 28. 불연속 강화 알루미늄 재료의 인성에 영향을 미치는 요인 개략도.
- Fig. 29. 다양한 불연속 강화 알루미늄 재료의 인성-항복 강도 관계, 광범위한 조합 입증.
- Fig. 30. CermeTi 재료의 미세 구조.
- Fig. 31. CermeTi 재료: (좌) 듀얼 경도 기어 CermeTi/모놀리식 PM Ti-6Al-4V, (우) 7겹 방탄 플레이트, CermeTi 및 모놀리식 PM Ti-6Al-4V 교대층으로 구성 (Dynamet 제공).
- Fig. 32. Al-8Fe-2Mo 시트의 전자빔 용접부의 광학 (상) 및 SEM (하) 현미경 사진. 화살표는 용융 경계를 나타냄.
- Fig. 33. 전자빔 용접된 감마 티타늄 알루미나이드의 고상 균열.
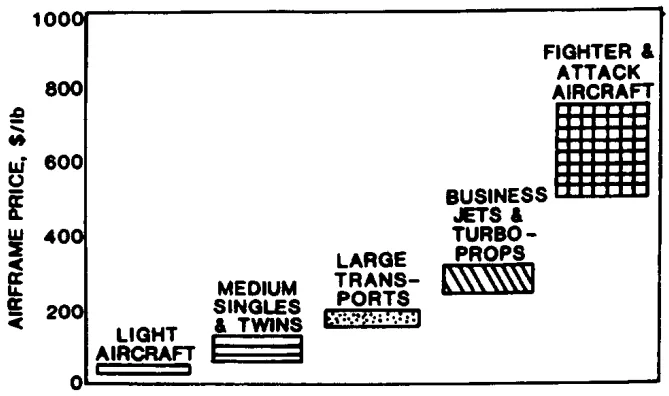
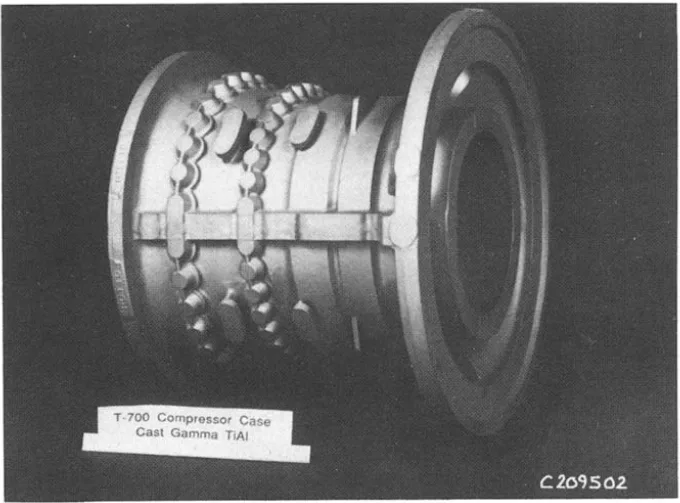
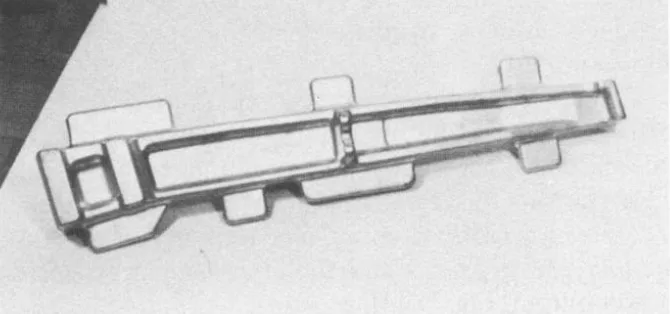

6. 결론 및 논의:
- 주요 결과 요약:
- 항공우주 및 자동차 시스템의 성능 향상은 고성능 경량 재료를 통해 달성할 수 있으며, 알루미늄, 마그네슘, 티타늄, 티타늄 알루미나이드 기반 경량 재료의 생산은 혁신적인 합성 기술을 필요로 합니다.
- 잉곳 주조, 급속 응고, 기계적 합금화, 나노 구조 재료, 용사 코팅, 증착 공정, 열화학적 처리, 금속 매트릭스 복합재료, 용융 접합 등 다양한 합성 방법이 검토되었으며, 각 기술은 특정 재료 및 응용 분야에 적합한 특성을 제공합니다.
- 금속 매트릭스 복합재료는 강성, 강도, 내크리프성 향상에 효과적이며, 용융 접합 기술은 고급 금속 재료를 구조체에 통합하는 데 필수적입니다.
- 연구의 학문적 의의:
- 본 연구는 항공우주 및 자동차 분야의 고급 금속 재료 개발 동향을 종합적으로 분석하고, 다양한 합성 및 가공 기술의 특징과 응용 가능성을 제시함으로써 재료 과학 및 공학 분야의 학문적 발전에 기여합니다.
- 특히 경량 금속 재료의 성능 향상을 위한 새로운 접근 방식과 기술적 해결책을 제시하여 향후 관련 연구 방향 설정에 중요한 참고 자료를 제공합니다.
- 연구의 실제적 의미:
- 본 연구 결과는 항공우주 및 자동차 산업에서 고성능 경량 부품 개발에 활용될 수 있으며, 연비 향상, 배기가스 감소, 안전성 향상 등 사회적 편익 증진에 기여할 수 있습니다.
- 다양한 고급 금속 재료 및 제조 공정에 대한 정보를 제공하여 산업계의 재료 선택 및 공정 개발 의사 결정에 도움을 줄 수 있습니다.
- 연구의 한계:
- 본 연구는 1994년 발표된 논문을 기반으로 작성되었으므로, 이후 개발된 최신 기술 및 재료 동향을 반영하지 못할 수 있습니다.
- 특정 기술 및 재료에 대한 심층적인 분석보다는 전반적인 기술 동향 및 개요를 중심으로 논의가 진행되었습니다.
7. 향후 후속 연구:
- 후속 연구 방향:
- 본 연구에서 다룬 고급 금속 재료의 최신 기술 동향 및 응용 사례에 대한 추가 연구가 필요합니다.
- 각 합성 및 가공 기술의 경제성, 생산성, 환경 영향 등을 평가하고, 실제 산업 적용 가능성을 높이는 연구가 필요합니다.
- 금속 매트릭스 복합재료의 계면 제어, 강화재 분산 최적화, 새로운 복합재료 설계 등에 대한 심층적인 연구가 요구됩니다.
- 용융 접합 기술의 접합부 특성 향상, 이종 재료 접합 기술 개발, 비파괴 검사 기술 개발 등에 대한 연구가 필요합니다.
- 추가 탐색 필요 영역:
- 나노 기술을 활용한 경량 금속 재료의 성능 향상 연구
- 3D 프린팅 등 적층 제조 기술을 이용한 고급 금속 부품 제조 연구
- 인공지능 및 빅데이터 기반 재료 설계 및 공정 최적화 연구
8. 참고 문헌:
- [1] F.H. Froes, P. Tsakiropoulos, C. Suryanarayana and W. Baeslack, in N.J. Kim (ed.), Light Materials for Transportation Systems, CAAM, Postech, Pohang, Korea, 1993, p. 27.
- [2] F.H. Froes, Mater. Design, 10(3) (1989) 186.
- [3] J.E. Allison and G.S. Cole, JOM, 45(1) (1993) 19.
- [4] W.F. Jandeska, Jr., in F.H. Froes (ed.), P/M in Aerospace, Defense and Demanding Applications - 1993, Metal Powder Industries Federation, Princeton, NJ, p. 45.
- [5] F.H. Froes and C. Suryanarayana, Titanium Aluminides, in V.K. Sikka and N. Stoloff (eds.), Physical Metallurgy and Processing of Intermetallic Compounds, Van Nostrand Reinhold, New York, NY, in press, 1994.
- [6] F.H. Froes, in F.H. Froes and R.A. Cull (eds.), Space Age Metals Technology, SAMPE, Covina, CA, 1988, p. 1.
- [7] F.H. Froes, Light Metal Age, 50(3-4) (1992) 66.
- [8] F.H. Froes, D. Eylon and H.B. Bomberger, Titanium Technology: Present Status and Future Trends, 1985, Titanium Development Association, Denver, CO.
- [9] F.H. Froes and W. Baeslack, in J.C. Danko and E.E. Nolting (eds.), Advanced Metals for Aerospace Component Fabrication, American Welding Society-High Energy Electron Beam Welding and Materials Processing Workshop, Boston, MA, Sept. 21-23, 1992, American Welding Society, Miami, FL, 1993, p. 219.
- [10] F.H. Froes and C. Suryanarayana, in A. Bose, R. German and A. Lawley (eds.), Powder Processing of Titanium Alloys, Book Series on Reviews in Particulate Materials, Metal Powder Industries Federation, Princeton, NJ, 1993, Vol. 1, p. 223.
- [11] J. Staley, Alcoa Research Center, Pittsburgh, PA, 1993
- [12] A. Mortenson, Fabrication of Particulate Reinforced Metal Composites, ASM Int., Materials Park, OH, 1990, p. 217.
9. 저작권:
- 본 자료는 "[F. H. Froes]"의 논문: "[Advanced metals for aerospace and automotive use]"을 기반으로 작성되었습니다.
- 논문 출처: https://doi.org/10.1016/0921-5093(93)01104-H
본 자료는 위 논문을 기반으로 요약되었으며, 상업적 목적으로 무단 사용하는 것을 금지합니다.
Copyright © 2025 CASTMAN. All rights reserved.