VSM과 시뮬레이션: 다이캐스팅 공정의 숨겨진 40% 낭비를 제거하고 생산성을 극대화하는 방법
이 기술 브리프는 Pradip Gunaki와 S.N. Teli가 작성하여 2015년 JETIR(Journal of Emerging Technologies and Innovative Research)에 발표한 학술 논문 "[Productivity Improvement by Value Stream Mapping in Die Casting Industry]"를 기반으로 합니다. HPDC 전문가를 위해 CASTMAN의 전문가들이 요약하고 분석했습니다.
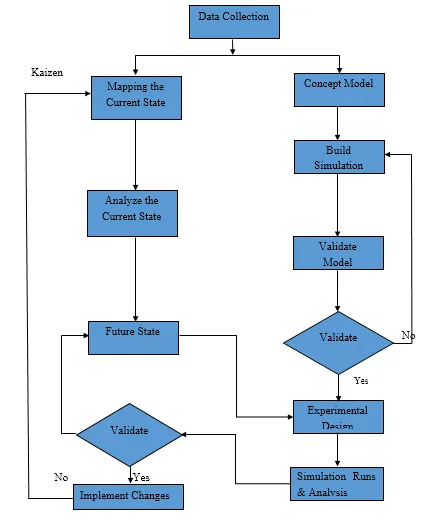
키워드
- 주요 키워드: 다이캐스팅 생산성 향상
- 보조 키워드: 가치 흐름 지도(Value Stream Mapping, VSM), 사이클 타임 감소, 린 제조, 공정 개선, 아레나 시뮬레이션, 비부가 가치 활동
Executive Summary
- 도전 과제: 다이캐스팅 생산 공정 내 비부가 가치 활동으로 인해 사이클 타임이 증가하여 고객 수요를 충족시키지 못하는 문제에 직면했습니다.
- 해결 방법: 가치 흐름 지도(VSM)를 사용하여 현재 공정 상태를 시각화하고, 아레나(Arena) 시뮬레이션 소프트웨어를 통해 낭비 요소를 정량적으로 분석했습니다.
- 핵심 성과: 전체 공정 시간의 39.96%를 차지하는 비부가 가치 활동(대기, 불필요한 운송 등)을 식별하고, 이를 24.57%까지 줄이는 개선안을 도출했습니다.
- 결론: 린(Lean) 원칙을 적용하여 전체 사이클 타임을 6.146% 단축하고, 생산성을 실질적으로 향상시킬 수 있음을 입증했습니다.
도전 과제: 왜 이 연구가 HPDC 전문가에게 중요한가?
글로벌 시장의 경쟁이 심화됨에 따라 다이캐스팅 제조업체는 유연성, 경쟁력, 고품질을 동시에 확보해야 하는 압박에 직면해 있습니다. 특히 고객의 요구가 다양해지고 맞춤형 주문이 증가하면서, 생산 시스템의 효율성은 기업의 생존과 직결됩니다. 본 논문에서 다루는 XYZ 회사는 증가하는 사이클 타임으로 인해 원하는 생산량을 맞추지 못하고 고객의 요구에 신속하게 대응하지 못하는 전형적인 문제를 겪고 있었습니다. 이는 생산 흐름 속에 숨어 있는 '낭비', 즉 가치를 더하지 않는 활동들 때문입니다. 많은 현장 엔지니어와 관리자들이 공정 비효율성으로 고민하지만, 문제의 정확한 원인과 규모를 파악하는 것은 늘 어려운 과제입니다. 이 연구는 바로 이 문제를 해결하기 위한 체계적인 접근법을 제시합니다.
해결 방법: 방법론 분석
연구팀은 이 문제를 해결하기 위해 강력한 린 제조 도구인 가치 흐름 지도(Value Stream Mapping, VSM)를 핵심 방법론으로 채택했습니다. VSM은 원자재 투입부터 최종 제품 인도까지의 모든 과정을 시각화하여 가치를 창출하는 활동과 그렇지 않은 활동을 명확히 구분하는 기법입니다.
연구팀은 먼저 현장 방문, 작업자 인터뷰, 모션 스터디 등을 통해 데이터를 수집하여 현재 생산 라인의 문제점을 담은 '현재 상태 지도(Current State Map)'를 작성했습니다. 이후, 아레나(Arena) 시뮬레이션 소프트웨어를 활용하여 현재 상태 모델을 구축하고, 각 공정 단계의 사이클 타임, 대기 시간, 가치 부가 시간(Value Added Time)과 비부가 가치 시간(Non-Value Added Time)을 정량적으로 분석했습니다. 이 분석을 통해 얻은 통찰력을 바탕으로 카이젠(Kaizen)과 5S 같은 린 기법을 적용한 '미래 상태 지도(Future State Map)'를 설계하고, 개선된 공정의 효과를 시뮬레이션을 통해 검증했습니다.
핵심 성과: 주요 발견 및 데이터
이 연구는 VSM과 시뮬레이션의 결합이 어떻게 실질적인 생산성 향상으로 이어지는지를 명확한 데이터로 보여줍니다.
- 낭비의 정량화: 현재 상태 분석 결과, 총 생산 시간(65.08분/개) 중 39.96%가 대기, 불필요한 운반 등 가치를 창출하지 않는 비부가 가치 활동에 소요되고 있었습니다. 이는 생산성의 발목을 잡는 핵심 원인이었습니다 (논문의
Corrective Action for Improvement
섹션 참조). - 사이클 타임 분석: 현재 상태 지도(Figure 6)와 시뮬레이션 결과(Figure 10)에 따르면, 각 공정 단계별 시간과 전체 리드 타임이 상세히 측정되었습니다. 예를 들어, 총 가치 부가 시간은 부품당 39.08분이었지만, 총 생산 시간은 65.08분으로 상당한 시간 격차가 존재했습니다.
- 개선을 통한 성과: 카이젠 철학을 바탕으로 작업 환경 개선(5S) 및 공정 흐름 최적화를 제안하고, 이를 미래 상태 지도(Figure 15)에 반영했습니다. 시뮬레이션 결과, 비부가 가치 활동의 비율이 24.57%로 크게 감소했으며, 총 사이클 타임은 61.08분으로 6.146% 단축되었습니다.
- 결과 비교: Figure 16은 개선 전(Current State)과 후(Future State)의 총 사이클 타임 및 비부가 가치 활동을 시각적으로 비교하여 개선 효과를 명확하게 보여줍니다.
귀사의 HPDC 운영을 위한 실질적인 시사점
이 연구 결과는 단순한 학술적 성과를 넘어, 실제 다이캐스팅 현장에 즉시 적용할 수 있는 중요한 통찰을 제공합니다.
- 공정 엔지니어: VSM을 도입하면 막연하게 느껴졌던 공정 내 병목 현상과 낭비 요소를 시각적으로 식별할 수 있습니다. 논문에서처럼 대기 시간, 불필요한 자재 이동 경로 등을 데이터 기반으로 파악하고 제거함으로써 전체 처리량을 높이고 리드 타임을 단축할 수 있습니다.
- 품질 관리: 논문에서 제안된 카이젠 활동의 일환인 5S(정리, 정돈, 청소, 청결, 습관화)는 단순히 작업장을 깨끗하게 만드는 것을 넘어, 표준화된 작업 환경을 구축하여 작업자의 실수를 줄이고 제품 품질의 일관성을 높이는 데 직접적으로 기여합니다.
- 생산 관리자: 이 연구는 개별 장비의 성능 개선만으로는 전체 생산성 향상에 한계가 있음을 보여줍니다. 공정 전체의 '흐름'을 최적화하는 것이 핵심입니다. 시뮬레이션 도구를 활용하면, 실제 라인을 멈추지 않고도 다양한 개선 시나리오의 효과를 사전에 예측하고 최적의 투자 결정을 내릴 수 있습니다.
논문 상세 정보
Productivity Improvement by Value Stream Mapping in Die Casting Industry
1. 개요:
- 제목: Productivity Improvement by Value Stream Mapping in Die Casting Industry
- 저자: Pradip Gunaki, S.N. Teli
- 발행 연도: 2015
- 학술지/학회: Journal of Emerging Technologies and Innovative Research (JETIR)
- 키워드: Value Stream, Current Stream Mapping, Future State Mapping, Takt time, Cycle Time, Lean Manufacturing, Simulation.
2. 초록 (Abstract):
가치 흐름 지도(Value Stream Mapping)는 제조, 생산 및 비즈니스 프로세스에서 비부가 가치 단계를 식별하고 제거하거나 간소화하여 낭비를 찾아내는 것으로 명성이 높습니다. 공정을 보여주는 흐름도를 그려 작업의 현재 상태를 반영합니다. 비부가 가치 활동은 각 단계와 단계 사이에서 시간과 자원의 낭비로 식별됩니다. 이 프로세스는 시뮬레이션 소프트웨어의 도움을 받아 분석되어, 필요한 최소한의 조치로 대폭 줄이고 단순화할 기회를 찾습니다. 낭비를 줄임으로써 전체 프로세스에서 가치 부가 시간의 비율이 높아지고 프로세스 처리 속도가 증가합니다. 이는 재설계된 프로세스를 더 효과적(올바른 일이 수행됨)이고 더 효율적(더 적은 자원 필요)으로 만듭니다. 이 논문은 아레나(Arena) 시뮬레이션 소프트웨어의 도움으로 다이캐스팅 산업에서 비부가 가치 활동을 제거하기 위한 수정 방법에 대해 설명합니다. 재설계된 프로세스는 공정 단계와 정보 흐름이 재설계, 단순화되고 비용이 절감되며 생산성이 증가된 미래 상태로 순서도에 그려집니다.
3. 서론 (Introduction):
가치 흐름은 고객을 위해 가치를 창출하는 프로세스/활동의 종단 간 집합입니다. 이는 제품을 주요 흐름을 통해 가져오는 데 현재 필요한 모든 활동(가치 부가 및 비부가 가치 모두)을 포함합니다. VSM은 내부 커뮤니케이션과 더 넓은 린 커뮤니티와 기술 및 결과를 공유하기 위한 커뮤니케이션 도구로 사용될 수 있습니다. 글로벌 시장에서의 경쟁 심화는 제조업체들이 더 많은 유연성, 경쟁력, 고품질 제품을 제공하고 생산 비용 절감을 보장하는 생산 시스템과 프로세스를 개발하도록 강요하고 있습니다. 동시에, 대량 생산의 시대가 끝났기 때문에 제조업체는 제품 다양성과 고객 가치에 더 많은 주의를 기울여야 합니다.
4. 연구 요약:
연구 주제의 배경:
다이캐스팅 산업은 고객의 요구를 충족시키기 위해 높은 생산성과 유연성을 유지해야 하는 압박에 직면해 있습니다. 공정 내 비효율성과 낭비는 사이클 타임을 증가시켜 생산 목표 달성을 저해하는 주요 원인이 됩니다.
이전 연구 현황:
Hugh L. McManus와 Richard L. Millard는 제품 개발(PD) 분야에서 가치 흐름 분석 및 지도(VSA/M) 개념을 탐구했습니다. Mahmoud Al-Odeh 등은 VSM이 가치를 향상시키고 낭비를 제거하며 흐름을 개선할 기회를 지속적으로 식별할 수 있다고 제안했습니다. 이들은 VSM을 구현하는 네 단계를 따랐습니다.
연구의 목적:
본 연구의 주된 목적은 다이캐스팅 산업에서 VSM이라는 시각화 도구를 사용하여 비부가 가치 활동을 찾아내고, 린 기법과 시뮬레이션 소프트웨어를 통해 이러한 활동을 제거하여 생산성을 향상시키는 것입니다. 구체적으로는 사이클 타임을 단축하고 고객 수요에 효과적으로 대응하는 것을 목표로 합니다.
핵심 연구:
연구는 XYZ라는 알루미늄 다이캐스팅 회사를 사례로 진행되었습니다. VSM 방법론에 따라 파운드리 공정을 핵심 개선 대상으로 선정했습니다. 현재 공정의 정보 흐름과 자재 흐름을 분석하여 '현재 상태 지도'를 작성하고, 아레나 시뮬레이션을 통해 공정 데이터를 정량화했습니다. 분석 결과를 바탕으로 카이젠(Kaizen)과 5S를 포함한 개선안을 도출하고, 이를 반영한 '미래 상태 지도'를 설계하여 시뮬레이션으로 그 효과를 검증했습니다.
5. 연구 방법론
연구 설계:
본 연구는 특정 다이캐스팅 회사를 대상으로 한 사례 연구(Case Study)로 설계되었습니다. VSM 방법론을 적용하여 '현재 상태 분석 → 문제점 식별 → 개선안 도출(미래 상태 설계) → 효과 검증'의 단계적 접근법을 따랐습니다.
데이터 수집 및 분석 방법:
데이터는 현장 방문(Site Visits), 구조화된 인터뷰(Structured Interviews), 문서 검토 등을 통해 수집되었습니다. 수집된 데이터는 VSM을 사용하여 시각화되었으며, 아레나(Arena) 시뮬레이션 소프트웨어를 사용하여 공정의 동적 행태를 모델링하고 사이클 타임, 대기 시간, 자원 활용률 등을 정량적으로 분석했습니다.
연구 주제 및 범위:
연구는 알루미늄 다이캐스팅을 생산하는 XYZ 회사의 파운드리 공장에 초점을 맞췄습니다. 연구 범위는 원자재 투입부터 금형 준비, 주입, 녹아웃, 쇼트 블라스팅, 페틀링, 검사 및 출하에 이르는 전체 생산 흐름을 포함합니다.
6. 주요 결과:
주요 결과:
- 현재 상태: 총 사이클 타임은 부품당 65.08분이며, 이 중 39.96%가 비부가 가치 활동에 해당했습니다. 고객 수요(월 430개) 대비 생산량(월 364개)이 부족한 상태였습니다.
- 개선 활동: 카이젠(Kaizen) 철학을 도입하여 작업 흐름을 개선하고 5S 활동을 통해 작업 환경을 최적화했습니다.
- 미래 상태: 개선 결과, 비부가 가치 활동이 24.57%로 감소했으며, 총 사이클 타임은 부품당 61.08분으로 6.146% 단축되었습니다. 이를 통해 생산성이 향상되어 고객 수요에 더 효과적으로 대응할 수 있게 되었습니다.
Figure Name List:
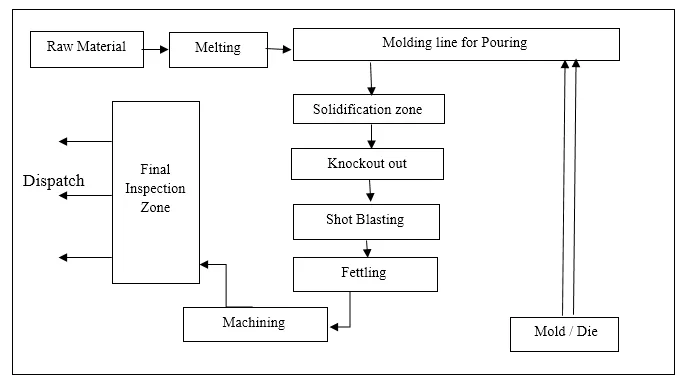
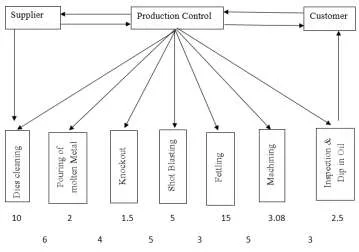
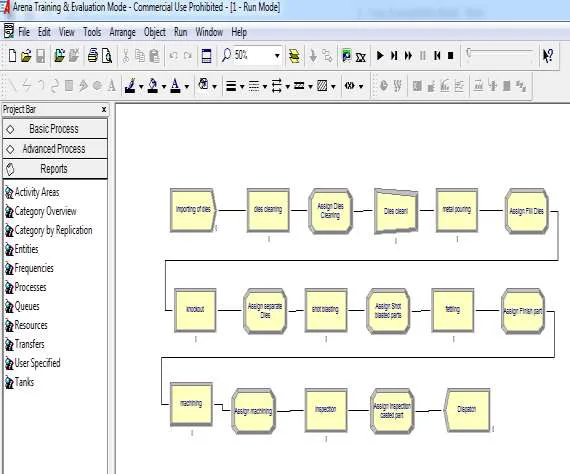
- Figure 1. Value Stream Mapping Methodology
- Figure 2. Integration of Value Stream Mapping with Simulation
- Figure 3 Site Visits
- Figure 4. Structured Interviews
- Figure 5 Current Foundry Production Lay out
- Figure 6. Current State Map
- Figure 7. Arena Simulation Model for Current State Map
- Figure 8. Key Performance Indicator
- Figure 9 Category Overview of Queue
- Figure 10 Category Review of Time Entity
- Figure 11 Kaizen Umbrella
- Figure 12 Arena Simulation Model
- Figure 13. Category Review of non-value added activities
- Figure 14. Category Overview of Product Entity
- Figure 15 Future State Map
- Figure 16 Comparison between Current & Future State Map
7. 결론 (Conclusion):
가치 흐름 지도 도구는 세계적 수준의 제조 도구로서 어떤 종류의 분야에서든 효과적으로 사용될 수 있습니다. 분석된 연구는 다이캐스팅 산업의 사례 연구입니다. 주요 목표는 가치 흐름에서 낭비를 제거하는 것입니다. 이 연구에서는 가치 흐름 분석 도구를 사용하여 비부가 가치 활동을 식별합니다. 현재 상태 지도는 현재 상태를 평가하기 위해 그려집니다. 낭비 제거 기술이 제시되고 미래 상태 지도 또한 개선을 위해 선호됩니다. 연구 결과는 가치 흐름에서 비부가 가치 활동의 15% 낭비 감소를 보여주며, 따라서 총 사이클 타임이 6.146% 감소합니다. VSM과 시뮬레이션 소프트웨어의 통합은 시스템을 적절하게 분석하는 데 도움이 될 것입니다. 가치 흐름 지도는 생산성을 향상시킬 기회를 찾는 데 사용되는 시각화 도구입니다.
8. 참고 문헌 (References):
- [List the references exactly as cited in the paper, Do not translate and omit.]
1) R.M. Belokar, Sandeep Singh Kharb, Vikas Kumar “An Application of Value Stream Mapping In Automobile Industry: A Case Study", International Journal of Innovative Technology and Exploring Engineering (IJITEE) ISSN: 2278-3075, Vol.-1(2), pp.231-236, (2012).
2) Muhammad Abdus Samad et.Al, “Value Stream Mapping To Reduce Manufacturing Lead Time In A Semi-Automated Factory", Asian Transactions On Engineering, Vol.2 Issue 06, pp. 22-28, (2013).
3) Danijela Gracanina & BorutBuchmeister, BojanLalic “Using Cost-Time Profile for Value Stream Optimization”, Procedia Engineering 69 (2014), p. 1225 – 1231.
4) Rahani AR, Muhammad al-Ashraf “Production Flow Analysis through Value Stream Mapping: A Lean Manufacturing Process Case Study”, Procedia Engineering, Vol.41, pp.1727 – 1734, (2012).
5) Mahmoud Al-Odeh et.al, “Value Stream Mapping: Recreating an Industrial Environment in an Educational Setting", Proceedings of The (2014) IAJC/ISAM Joint International Conference ISBN, p.978-1-60643-379-9.
6) Palak P. Sheth1 et.Al, “Value Stream Mapping: A Case Study of Automotive Industry”, Ijret (2014), p.2321-7308.
7) Rehab M. Ali et.al “Dynamic Lean Assessment for Takt Time Implementation”, Procedia CRIP 17 (2014), p.577-581.
8) G. M. Gohane, A. S. Bonde & C.S. Sable," Improvement of Productivity Using Value Stream Mapping", IJSRD - International Jour nal for Scientifi c Research & Development| Vol. 2(8), ISSN (online): 2321-0613, pp.1-5, (2015).
9) G. Sahitya Reddy, Harsha Lingareddy & K.Jagadeeshwar, "Value Stream Mapping In A Manufacturing Industry", International Journal of Advanced Engineering Technology E-ISSN 0976-3945, Vol.4(2), pp.20-23,(2013).
10) Binu Bose V & K N Anilkumar, “Reducing rejection rate of castings using Simulation Model”, Proceedings of International Conference on Energy and Environment, International Journal of Innovative Research in Science, Engineering and Technology, Vol. 2(1), pp.589-597,(2013).
11) Petter Solding & Per Gullandar, “Concepts for Simulation Based Value Stream Mapping", Proceedings of the 2009 Winter Simulation Conference, pp.2231-2237, (2009).
12) Wei Xia & Jiwen Sun, “Simulation guided value stream mapping and lean improvement: A case study of a tubular machining facility", Journal of Industrial Engineering and Management, JIEM,pp.456-476, (2013).
13) Abu Md. Saifuddoha, Md. Ahasan Habib2, Sohana Yasmin Sumi, Md. Jennurine, Md. Saiful Islam, “Minimization Of Waste By Applying Value Stream Mapping In The Supply Chain Of Cement Industry”, IOSR Journal of Business and Management (IOSR-JBM), ISSN: 2319-7668, Volume 9, Issue 3,pp.79-84,(2013).
14) S. Santhosh kumar, M. Pradeep kumar, “Cycle Time Reduction of truck body assembly in an automobile industry by lean principles", Procedia Materials science, Vol.5, pp.1853-1862, (2014).
15) Schönemann, M. et.al “Integrating product characteristics into extended value stream modeling”, Procedia CIRP (2014) p.368 – 373.
전문가 Q&A: 가장 궁금한 질문에 대한 답변
(참고: 답변은 반드시 논문의 특정 출처를 인용합니다. 예: "[논문 제목], 방법론 섹션" 또는 "Figure 4에서 볼 수 있듯이".)
Q1: 이 연구에서 생산성 저하의 가장 큰 원인으로 지목된 것은 무엇입니까?
A1: 연구에서는 총 생산 시간의 39.96%를 차지하는 '비부가 가치 활동(Non-Value Added Activities)'이 가장 큰 원인이라고 결론 내렸습니다. 이는 대기 시간, 불필요한 운송, 과잉 생산 등을 포함하며, 논문의 Corrective Action for Improvement
섹션에서 상세히 설명하고 있습니다.
Q2: 이 접근법이 단순히 개별 장비의 속도를 높이는 것과 어떻게 다른가요?
A2: VSM은 개별 공정이 아닌, 원자재부터 완제품까지 이어지는 '전체 흐름(stream)'을 분석합니다. 논문의 Introduction
섹션에서 설명하듯이, VSM은 공정과 공정 '사이'에 발생하는 대기 시간이나 운송 시간 같은 숨겨진 낭비를 찾아내는 데 중점을 둡니다. 이는 개별 장비의 효율만으로는 파악하기 어려운 시스템 전체의 비효율을 개선하는 접근법입니다.
Q3: 이 연구 결과는 모든 다이캐스팅 공정에 적용될 수 있나요?
A3: 본 연구는 Implementation of VSM in Die Casting Industry
섹션에 명시된 바와 같이 특정 알루미늄 다이캐스팅 회사의 사례 연구입니다. 하지만 VSM과 린 제조의 원칙은 보편적이므로, 논문의 Conclusion
에서 언급하듯이 다른 종류의 다이캐스팅 공장이나 제조업 분야에서도 효과적으로 적용될 수 있습니다.
Q4: 연구원들이 결론에 도달하기 위해 사용한 구체적인 분석 도구는 무엇이었나요?
A4: 연구원들은 두 가지 핵심 도구를 사용했습니다. 첫째, 공정을 시각화하고 낭비를 식별하기 위해 '가치 흐름 지도(VSM)'를 사용했습니다. 둘째, Arena Simulation Modeling
섹션에서 설명하듯이, '아레나(Arena) 시뮬레이션 소프트웨어'를 사용하여 현재 및 미래 상태의 공정을 정량적으로 분석하고 개선 효과를 예측했습니다.
Q5: 논문에서 제안된 구체적인 해결책은 무엇이었습니까?
A5: 논문은 Corrective Action for Improvement
섹션과 Figure 11에서 보여주듯이, '카이젠(Kaizen)' 철학의 도입을 핵심 해결책으로 제시했습니다. 여기에는 작업 흐름의 지속적인 개선과 함께 작업 환경을 체계적으로 관리하는 5S 활동이 포함되어 식별된 낭비를 제거하고 효율성을 높였습니다.
Q6: 이 논문이 제시하는 최종적이고 측정 가능한 개선 효과는 무엇입니까?
A6: 논문의 Results & Discussion
섹션과 Figure 16의 비교 차트에서 명확히 보여주듯이, 제안된 개선안을 통해 총 사이클 타임이 6.146% 감소했으며, 비부가 가치 활동의 비율은 39.96%에서 24.57%로 크게 줄었습니다.
결론 및 다음 단계
이 연구는 다이캐스팅 공정의 생산성을 향상시키기 위한 가치 있는 로드맵을 제공합니다. VSM과 시뮬레이션의 결합은 품질을 개선하고, 결함을 줄이며, 생산을 최적화하기 위한 명확하고 데이터 기반의 경로를 제시합니다.
CASTMAN은 최신 산업 연구를 적용하여 고객의 가장 어려운 다이캐스팅 문제를 해결하는 데 전념하고 있습니다. 이 논문에서 논의된 문제가 귀사의 운영 목표와 관련이 있다면, 저희 엔지니어링 팀에 연락하여 이러한 고급 원칙을 귀사의 부품에 구현하는 방법을 논의해 보십시오.
References
- 1) R.M. Belokar, Sandeep Singh Kharb, Vikas Kumar “An Application of Value Stream Mapping In Automobile Industry: A Case Study", International Journal of Innovative Technology and Exploring Engineering (IJITEE) ISSN: 2278-3075, Vol.- 1(2), pp.231-236, (2012).
- 2) Muhammad Abdus Samad et.Al, “Value Stream Mapping To Reduce Manufacturing Lead Time In A Semi-Automated Factory", Asian Transactions On Engineering, Vol.2 Issue 06, pp. 22-28, (2013).
- 3) Danijela Gracanina & BorutBuchmeister, BojanLalic “Using Cost-Time Profile for Value Stream Optimization”, Procedia Engineering 69 (2014), p. 1225 – 1231.
- 4) Rahani AR, Muhammad al-Ashraf “Production Flow Analysis through Value Stream Mapping: A Lean Manufacturing Process Case Study”, Procedia Engineering, Vol.41, pp.1727 – 1734, (2012).
- 5) Mahmoud Al-Odeh et.al, “Value Stream Mapping: Recreating an Industrial Environment in an Educational Setting", Proceedings of The (2014) IAJC/ISAM Joint International Conference ISBN, p.978-1-60643-379-9.
- 6) Palak P. Sheth1 et.Al, “Value Stream Mapping: A Case Study of Automotive Industry”, Ijret (2014), p.2321-7308.
- 7) Rehab M. Ali et.al “Dynamic Lean Assessment for Takt Time Implementation”, Procedia CRIP 17 (2014), p.577-581.
- 8) G. M. Gohane, A. S. Bonde & C.S. Sable," Improvement of Productivity Using Value Stream Mapping", IJSRD - International Jour nal for Scientifi c Research & Development| Vol. 2(8), ISSN (online): 2321-0613, pp.1-5, (2015).
- 9) G. Sahitya Reddy, Harsha Lingareddy & K.Jagadeeshwar, "Value Stream Mapping In A Manufacturing Industry", International Journal of Advanced Engineering Technology E-ISSN 0976-3945, Vol.4(2), pp.20-23,(2013).
- 10) Binu Bose V & K N Anilkumar, “Reducing rejection rate of castings using Simulation Model”, Proceedings of International Conference on Energy and Environment, International Journal of Innovative Research in Science, Engineering and Technology, Vol. 2(1), pp.589-597,(2013).
- 11) Petter Solding & Per Gullandar, “Concepts for Simulation Based Value Stream Mapping", Proceedings of the 2009 Winter Simulation Conference, pp.2231-2237, (2009).
- 12) Wei Xia & Jiwen Sun, “Simulation guided value stream mapping and lean improvement: A case study of a tubular machining facility", Journal of Industrial Engineering and Management, JIEM,pp.456-476, (2013).
- 13) Abu Md. Saifuddoha, Md. Ahasan Habib2, Sohana Yasmin Sumi, Md. Jennurine, Md. Saiful Islam, “Minimization Of Waste By Applying Value Stream Mapping In The Supply Chain Of Cement Industry”, IOSR Journal of Business and Management (IOSR-JBM), ISSN: 2319-7668, Volume 9, Issue 3,pp.79-84,(2013).
- 14) S. Santhosh kumar, M. Pradeep kumar, “Cycle Time Reduction of truck body assembly in an automobile industry by lean principles", Procedia Materials science, Vol.5, pp.1853-1862, (2014).
- 15) Schönemann, M. et.al “Integrating product characteristics into extended value stream modeling”, Procedia CIRP (2014) p.368 – 373.
Copyright
- This material is an analysis of the paper "Productivity Improvement by Value Stream Mapping in Die Casting Industry" by Pradip Gunaki and S.N. Teli.
- Source of the paper: https://www.researchgate.net/publication/317427739ProductivityImprovementbyValueStreamMappinginDieCastingIndustry
- This material is for informational purposes only. Unauthorized commercial use is prohibited.
- Copyright © 2025 CASTMAN. All rights reserved.