본 논문 요약은 ['Optimization of Die casting process based on Taguchi approach']에 기초하여 작성되었으며, 발행처는 ['Elsevier']입니다.
1. 개요:
- 제목: Taguchi 방법을 기반으로 한 다이캐스팅 공정 최적화 (Optimization of Die casting process based on Taguchi approach)
- 저자: K.Ch. Apparao 및 Anil Kumar Birru
- 발행 연도: 2017년
- 발행 학술지/학회: Materials Today: Proceedings 4 (2017) 1852–1859, 제5회 국제 재료 가공 및 특성 분석 컨퍼런스 (ICMPC 2016)
- 키워드: 최적화, 다구치 방법, 다이캐스팅 (optimization, Taguchi method, Die casting)
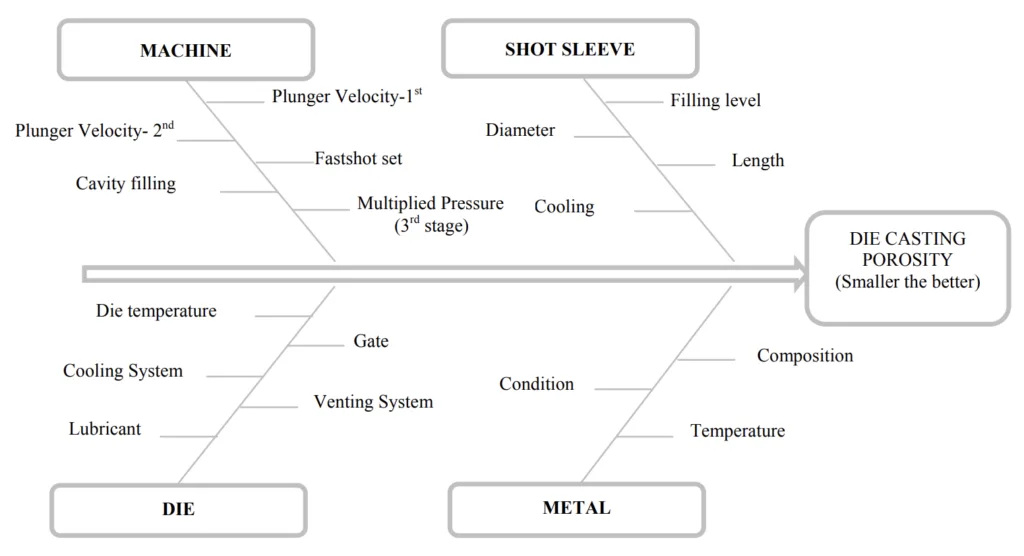
2. 초록 또는 서론
경량성과 우수한 성형성으로 인해 알루미늄 다이캐스팅은 특히 자동차 산업에서 중요한 역할을 합니다. 알루미늄 다이캐스팅에서 기공은 가장 흔하게 발생하는 결함 중 하나이며, 이는 고강도 응용 분야에서 다이캐스트 부품의 사용을 제한합니다. 본 연구에서는 Al-Si8Cu3Fe (EN AC-46500) 알루미늄 합금 다이캐스팅의 품질과 효율성을 높이기 위해 기공 형성을 줄이는 다이캐스팅 매개변수의 최적 설정을 얻기 위해 다구치 방법의 사용을 개념화했습니다. 선택된 매개변수가 기공 형성에 미치는 영향과 이후 다구치 방법을 사용하여 매개변수의 최적 설정을 달성했습니다. 최종 결과는 최적화된 매개변수가 Al-Si8Cu3Fe 알루미늄 합금 다이캐스팅의 기공 형성에 상당한 영향을 미친다는 것을 나타냅니다.
3. 연구 배경:
연구 주제 배경:
오늘날 많은 산업 분야, 특히 자동차 산업에서는 경량 재료를 개발해야 합니다. 따라서 전 세계적으로 알루미늄 합금 생산이 증가했으며 알루미늄 소비량은 1차 금속의 기존 생산 능력을 초과하고 있습니다. 알루미늄은 항공 우주, 방위 및 자동차 응용 분야 등과 같은 엔지니어링 부품의 다이캐스팅 분야에서 여전히 가장 널리 가공되는 금속입니다 [1-2]. 다이캐스팅(DC)은 다른 공정으로는 얻을 수 없는 부품을 생산하는 데 사용되는 가장 전문화된 제조 공정 중 하나입니다. 이 공정의 장점으로는 금형 적합성, 유리한 기계적 특성 및 저비용이 있습니다. 알루미늄 다이캐스팅 공정에는 효과적으로 결정되고 조정될 때 다이캐스트 부품의 품질을 향상시키는 많은 매개변수가 존재합니다. 이러한 주조에서 내부 기공은 가장 흔한 결함입니다. 이 결함의 주요 원인은 다이캐스팅 공정의 처음 두 충전 단계 동안 액체 금속에 갇힌 공기입니다 [3-6]. 압력 다이캐스팅의 기공은 항상 문제였으며, 상당한 연구, 설계 및 개발에도 불구하고 산업계에서 요구하는 주물의 복잡성이 증가함에 따라 기공을 완전히 제거하는 것은 사실상 불가능해졌습니다. 그러나 주조 매개변수 최적화 기술은 기공을 중요하지 않은 영역으로 제한할 수 있습니다. 알루미늄 합금의 기공 형성은 주물의 기계적 특성을 저하시킬 뿐만 아니라 알루미늄 주물의 가공성 및 표면 특성에도 부정적인 영향을 미치기 때문에 매우 중요합니다. 다이캐스팅 공정에 다구치 기법을 적용하면 기공 형성을 상당히 줄일 수 있습니다.
기존 연구 현황:
압력 다이캐스팅에서의 기공은 오랫동안 문제로 여겨져 왔습니다. 상당한 연구, 설계 및 개발 노력에도 불구하고 산업계에서 요구하는 주조 설계의 복잡성이 증가함에 따라 기공을 완전히 제거하는 것은 사실상 불가능합니다. 그러나 주조 매개변수 최적화 기술은 기공을 중요하지 않은 영역으로 제한할 수 있습니다.
연구의 필요성:
다이캐스팅 매개변수를 최적화하기 위한 기존의 시행착오 방법은 시간이 많이 걸리고 비용이 많이 듭니다. 다구치 기법은 기공 형성을 최소화하기 위해 공정 매개변수를 체계적으로 최적화함으로써 다이캐스팅의 지속적이고 신속한 품질 개선을 위한 보다 효율적인 접근 방식을 제공하며, 이는 알루미늄 다이캐스팅의 기계적 및 표면 특성을 향상시키는 데 매우 중요합니다.
4. 연구 목적 및 연구 질문:
연구 목적:
본 연구의 주요 목적은 주조 품질을 향상시키기 위해 압력 다이캐스팅에서 공정 매개변수가 기공 형성에 미치는 역할을 조사하는 것입니다.
핵심 연구:
본 연구는 다구치 방법을 사용하여 Al-Si8Cu3Fe 알루미늄 합금 다이캐스팅에서 기공 형성을 최소화하기 위한 다이캐스팅 매개변수의 최적 설정을 식별하는 것을 목표로 합니다.
연구 가설:
본 논문에서는 연구 가설을 명시적으로 언급하지 않습니다. 그러나 암묵적으로 본 연구는 다구치 방법을 적용하여 다이캐스팅 매개변수(주입 온도, 충전 시간, 금형 온도 및 사출 압력)를 최적화함으로써 Al-Si8Cu3Fe 알루미늄 합금 다이캐스팅의 기공을 크게 줄일 수 있다는 가정하에 진행됩니다.
5. 연구 방법
연구 설계:
본 연구에서는 통계적 실험 설계 기법인 다구치 방법을 활용하여 다이캐스팅 공정 매개변수를 최적화했습니다. 4개의 선택된 매개변수 각각에 대해 3가지 수준의 L9 직교 배열을 사용하여 실험을 수행하고 이러한 매개변수가 기공에 미치는 영향을 분석했습니다. 목표로 하는 품질 특성은 "더 작을수록 더 좋은" 주조 기공이었습니다.
자료 수집 방법:
실험은 Technocrats 모델 TDC-120 고압 다이캐스팅 기계에서 수행되었습니다. 시험 샘플은 크기가 100mm x 100mm x 20mm인 Al-Si8Cu3Fe 알루미늄 합금 정사각형 판이었습니다. L9 직교 배열에 의해 정의된 9가지 시험 조건 각각에 대해 무작위화 기법을 사용하여 3개의 주물을 제작했습니다. 주조 밀도는 실험적 밀도 장치를 사용하여 측정하고, 기공도는 다음 방정식 (1)을 사용하여 계산했습니다.
기공률 (%) =(Po-Ps) × 100 (1)
여기서 ps는 측정된 주조 밀도이고 po는 기공이 없는 완전 조밀 주조의 밀도(2.79 g/cm³)입니다.
분석 방법:
신호 대 잡음비(S/N비)를 사용하여 기공 변동성을 분석했으며, 목표는 이를 최소화하는 것("더 작을수록 더 좋은" 특성)이었습니다. S/N비는 방정식 (2)를 사용하여 계산했습니다.
S/N비 (n) = − 10 log (∑(1/yᵢ²)/n) (2)
분산 분석(ANOVA)을 수행하여 주조 기공에 대한 각 매개변수의 통계적 유의성과 기여율을 결정했습니다.
연구 대상 및 범위:
본 연구는 Al-Si8Cu3Fe (EN AC-46500) 알루미늄 합금의 다이캐스팅 공정 최적화에 초점을 맞추었습니다. 조사된 공정 매개변수는 다음과 같습니다.
- 주입 온도 (요인 A)
- 충전 시간 (요인 B)
- 금형 온도 (요인 C)
- 사출 압력 (요인 D)
이러한 매개변수의 범위와 수준은 표 1에 자세히 나와 있습니다.
표 1 범위 및 3가지 수준의 값을 갖는 공정 매개변수
매개변수 대상 | 공정 매개변수 | 범위 | 수준 1 | 수준 2 | 수준 3 |
---|---|---|---|---|---|
A | 주입 온도 (°C) | 650-750 | 650 | 700 | 750 |
B | 충전 시간 (ms) | 40-130 | 40 | 85 | 130 |
C | 금형 온도 (°C) | 180-260 | 180 | 220 | 260 |
D | 사출 압력 (bar) | 120 - 240 | 120 | 180 | 240 |
6. 주요 연구 결과:
주요 연구 결과:
분석 결과 사출 압력(매개변수 D)과 주입 온도(매개변수 A)가 주조 기공에 가장 큰 영향을 미치는 매개변수임을 확인했습니다. 기공을 최소화하기 위한 최적 수준은 다음과 같이 확인되었습니다.
- 주입 온도: 수준 3 (750°C)
- 충전 시간: 수준 3 (130 ms)
- 금형 온도: 수준 1 (180°C)
- 사출 압력: 수준 3 (240 bar)
ANOVA 분석 결과 사출 압력이 주조 기공 변동에 약 46.931% 기여하고 주입 온도가 43.606% 기여하는 것으로 나타났습니다. 충전 시간과 금형 온도는 각각 4.733%와 4.730%로 기여도가 더 작았습니다.
제시된 데이터 분석:
그림 1 원인-결과 다이어그램은 다이캐스팅 기공에 영향을 미칠 수 있는 주조 공정 매개변수를 보여줍니다. 주입 온도, 충전 시간, 금형 온도 및 사출 압력이 실험 설계를 위한 중요한 매개변수로 확인되었습니다.
그림 2 표 1에 제시된 매개변수 값에서 Al-Si8Cu3Fe 알루미늄 합금 주물의 평균 주조 기공률 및 그림 3 표 1에 제시된 매개변수 값에서 Al-Si8Cu3Fe 알루미늄 합금 주물의 평균 S/N비는 각 매개변수의 수준 변화가 기공률 및 S/N비에 미치는 영향을 시각적으로 나타냅니다. 이러한 그림은 표 4 수준별 평균 주조 밀도 값과 주요 효과 및 표 5 수준별 평균 S/N비 값과 주요 효과와 함께 기공률이 주입 온도, 충전 시간 및 사출 압력의 수준이 높을수록 감소하는 경향을 보이며, 금형 온도가 가장 낮은 수준에서 최소화됨을 보여줍니다.
표 6 다이캐스팅 밀도 ANOVA 및 표 7 다이캐스팅 밀도 S/N비 ANOVA는 주조 기공 변동에 대한 각 매개변수의 기여도를 정량화합니다. 이러한 표는 사출 압력과 주입 온도가 가장 영향력 있는 매개변수임을 확인합니다.
그림 목록:
- Fig. 1 원인-결과 다이어그램 (Cause and effect diagram)
- Fig. 2 표 1에 제시된 매개변수 값에서 Al-Si8Cu3Fe 알루미늄 합금 주물의 평균 주조 기공률 (Average values of casting porosity for Al-Si8Cu3Fe aluminium alloy castings under the parameter values given in Table 1)
- Fig.3 표 1에 제시된 매개변수 값에서 Al-Si8Cu3Fe 알루미늄 합금 주물의 평균 S/N비 (Average values of the S/N rations forAl-Si8Cu3Fe aluminium alloy castings under the parameter values given in Table 1)
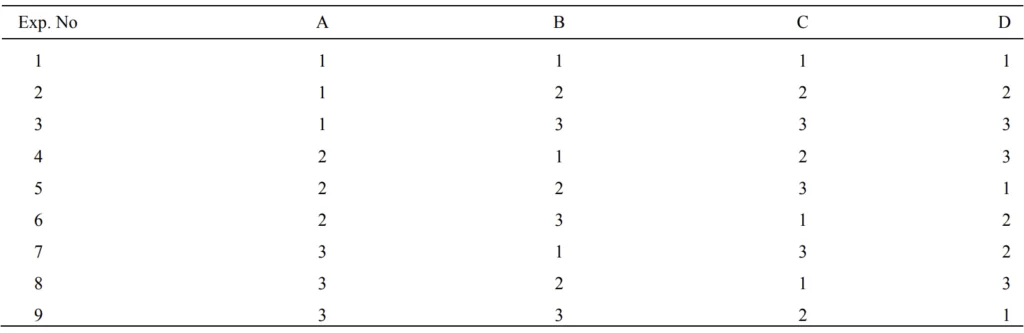
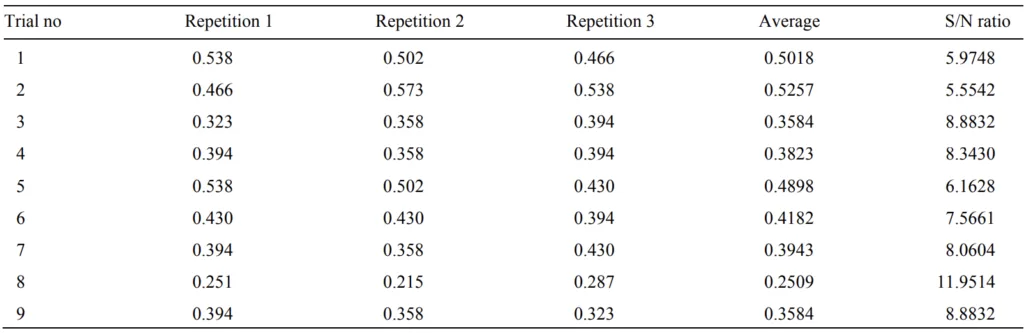

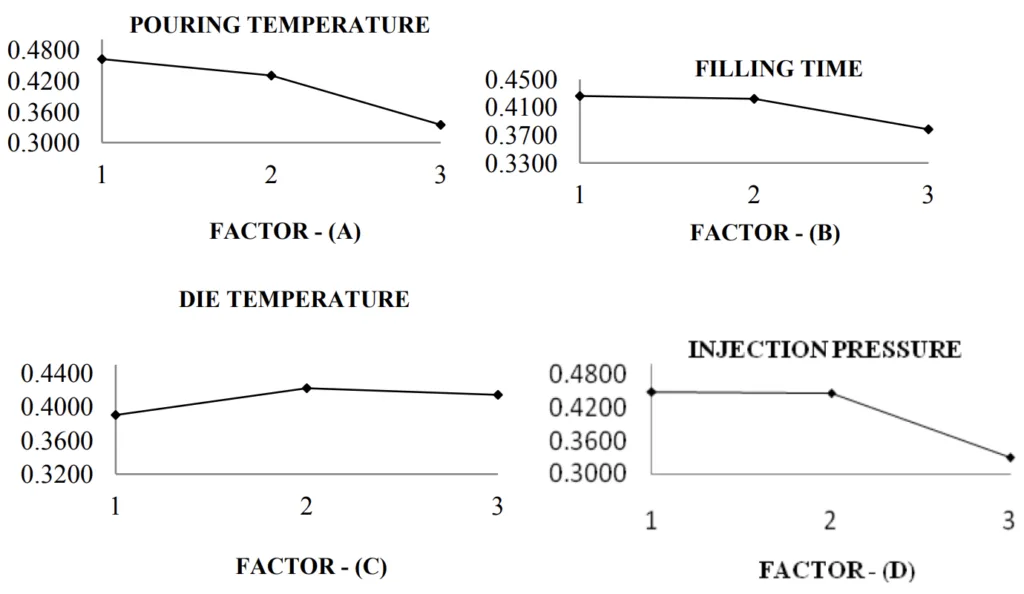
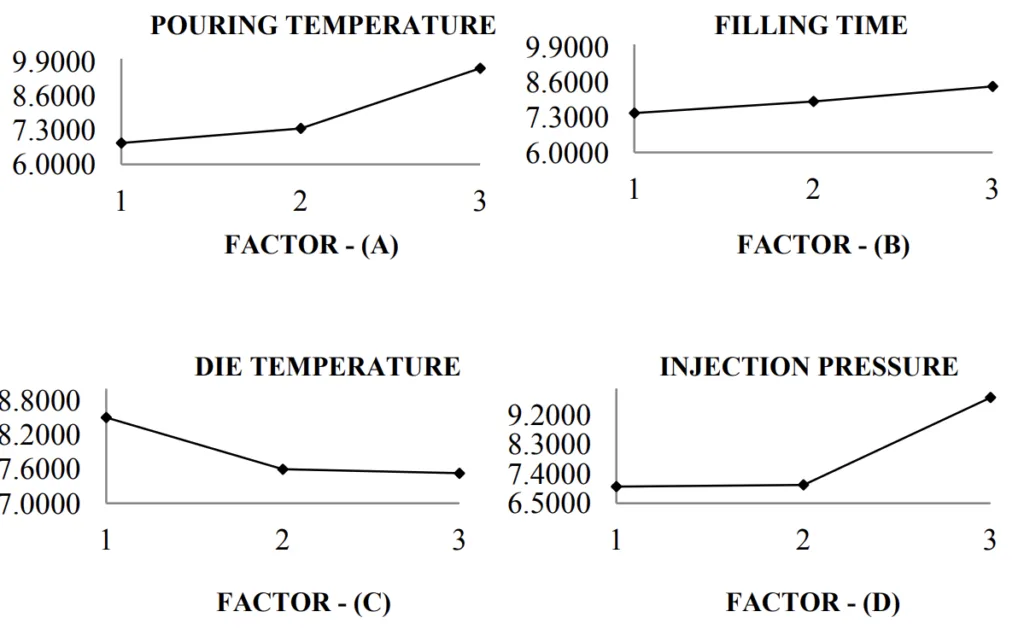
7. 결론:
주요 연구 결과 요약:
본 연구에서는 다이캐스팅 공정 매개변수의 변화가 Al-Si8Cu3Fe 알루미늄 합금 다이캐스팅의 기공 형성에 상당한 영향을 미친다는 것을 결정적으로 입증했습니다. 주입 온도, 충전 시간, 금형 온도 및 사출 압력이 기공에 영향을 미치는 주요 매개변수로 확인되었습니다. 다구치 방법을 사용하여 기공을 최소화하기 위한 최적 매개변수 수준은 주입 온도 750°C, 충전 시간 130ms, 금형 온도 180°C, 사출 압력 240bar로 결정되었습니다.
연구의 학문적 의의:
본 연구는 다구치 방법을 사용하여 기공을 최소화하기 위한 다이캐스팅 매개변수를 최적화하는 체계적인 접근 방식을 제공합니다. 통계적 실험 설계가 다이캐스팅 품질 향상에 효과적임을 강조하고 Al-Si8Cu3Fe 알루미늄 합금의 기공 형성에 대한 개별 공정 매개변수의 영향에 대한 귀중한 통찰력을 제공합니다.
실용적 의미:
본 연구 결과는 다이캐스팅 산업계가 Al-Si8Cu3Fe 알루미늄 합금에 대한 공정 매개변수를 최적화하여 특히 기공을 줄이고 주조 품질을 향상시키는 데 실질적인 지침을 제공합니다. 제조업체는 확인된 최적 설정을 구현함으로써 다이캐스트 부품의 기계적 특성과 표면 마감을 개선하여 특히 중요한 응용 분야에서 더 높은 품질의 부품을 생산할 수 있습니다.
연구의 한계 및 향후 연구 분야:
본 논문에서는 연구의 한계나 향후 연구 분야를 명시적으로 언급하지 않았습니다. 그러나 본 연구는 특정 합금(Al-Si8Cu3Fe)과 조사된 매개변수 범위로 제한된다고 추론할 수 있습니다. 향후 연구에서는 다음 사항을 탐구할 수 있습니다.
- 이러한 최적 매개변수의 다른 알루미늄 합금 및 다이캐스팅 기계 유형에 대한 적용 가능성.
- 본 연구에서 고려하지 않은 다른 공정 매개변수 조사.
- 매개변수 간의 상호 작용 효과를 보다 자세히 탐구.
- 확장성 및 견고성을 위해 산업 생산 환경에서 이러한 결과의 유효성 검증.
8. 참고 문헌:
- [1] Anuj Dixit, Koushik Kumar, Journal of Materials Today: Proceedings,2, (2015), pp 2359 – 2366.
- [2] Shashi Prakash Dwivedi, S. Sharma, R. K. Mishra., Journal of Advanced Materials Manufacturing &Characterization, 14 (2014), pp 81-82.
- [3] Dahle, A. K., Arnberg, L., Apelian, D., AFS Trans., 1997, 160, 963-969.
- [4] Emadi, D., Gruzleski. Effects of casting and melt variables on porosity in directionally solidified Al-Si alloys. AFS Trans., 1994, 95, 307-312.
- [5] Klein, F. and Wimmer, P. In NADCA International Die Casting Congress, Indianapolis, 2-5 October 1995, paper T95-035, pp. 101-111.
- [6] Chiesa, F., Fuoco, R. and Gruzleski, J. E.. Int. J. Cast Metals, 1995, 7(2), 113-122.
- [7] Ross, P. J. Taguchi Techniques for Quality Engineering, 1988 (McGraw-Hill, New York).
- [8] Logothetis, N. Total Quality Control, 1992 [Prentice-Hall International (UK) Limited].
- [9] Taguchi, G. Introduction to Quality Engineering, 1986 (Asian Productivity Organization, UNIPUB, White Plains, New York).
- [10] Phadke, S. M. Quality Engineering Using Robust Design, 1989 (Prentice-Hall, Englewood Clis, New Jersey).
- [11] Johnston, R. E. Design of experiments: Taguchi in the foundry. AFS Trans., 1989, 82, 415-418.
- [12] Johnston, R. E. Statistical methods in foundry experiments, AFS Trans. 72(1964) 17-18.
- [13] Makhlouf, M., Wang, L., Apelian, D. and Yang, L.Thermal conductivity of Al die casting alloys, AFS Trans., 1999, 12, 501-505.
- [14] D.M.Byrne, S. Taguchi, The Taguchi Approach to parameter Design, Quality progress, December 1987, pp. 19-26
- [15] Roy, R. K. Design of Experiments Using the Taguchi Approach: 16 Steps to Product and Process Improvement, 2001 (J. Wiley, New York).
- [16] Taguchi, G. and Konishi, S. Orthogonal Arrays and Linear Graphs, 1987 (American Supplier Institute, Dearborn, Michigan).
참고: 참고 문헌 목록은 원본 논문에 따라 영어로 작성되었습니다.
9. 저작권:
- 본 자료는 "[K.Ch. Apparao 및 Anil Kumar Birru]"의 논문: "[Optimization of Die casting process based on Taguchi approach]"을 기반으로 합니다.
- 논문 출처: DOI URL
본 자료는 상기 논문을 요약한 것으로, 상업적 목적으로 무단 사용하는 것을 금지합니다.
Copyright © 2025 CASTMAN. All rights reserved.