Acta Mechanica Slovaca에서 발행한 ["Use of Duplex PVD Coatings to Increase the Life of Moulds and Cores for die Casting of Aluminium Alloys in the Automotive Industry"] 논문 연구 내용을 소개합니다.
1. Overview:
- 제목: Use of Duplex PVD Coatings to Increase the Life of Moulds and Cores for die Casting of Aluminium Alloys in the Automotive Industry
- 저자: Janette Brezinová, Ján Viňáš, Miroslav Džupon, Dagmar Jakubeczyová, Jakub Brezina, Henrich Sailer, Ján Hašuľ, Michal Považan
- 출판 연도: 2022년
- 출판 저널/학회: Acta Mechanica Slovaca
- 키워드: PVD coatings, laser surface remelting, die casting of aluminium, tribology
![Table 1: Chemical composition of Uddeholm Dievar [15]](https://castman.co.kr/wp-content/uploads/image-1323-png.webp)
![Table 2: Mechanical properties of Uddeholm Dievar [15]](https://castman.co.kr/wp-content/uploads/image-1324-png.webp)
2. Abstracts or Introduction
본 논문은 자동차 산업 부품용 고압 알루미늄 다이캐스팅에 사용되는 금형 및 코어의 수명 연장을 목표로 한 연구 결과를 상세히 설명합니다. 연구 방법론은 Uddeholm Dievar 금형강 모재 표면에 국부 임펄스 가열을 적용하고, 세 가지 다른 가열 속도를 사용했습니다. 표면 처리 후, 구조 분석을 수행하고, Larc 기술을 통해 PVD nACRo³ 코팅을 적용했습니다.
코팅 품질 평가는 스크래치 테스트와 메르세데스 테스트를 사용하여 수행했습니다. 레이저 처리 및 nACRo³ 코팅 적용 후 표면 미세 형상은 ISO 25 178에 따라 평가했습니다. 코팅된 표면을 680 ± 20°C의 온도로 Al-Si계 합금 용융물에 120분 및 300분 동안 담갔습니다. 실험 결과 금형 표면의 저항이 크게 증가했음을 확인했습니다.
서론에서는 자동차 산업에서 알루미늄 및 플라스틱 주물의 중요성을 강조하며, 주로 다이캐스팅 및 사출 성형용 금속 금형을 사용하여 생산된다는 점을 설명합니다. 다이캐스팅 금형은 일반적으로 크롬 또는 공구강으로 만들어지며 29-48 HRC의 경도로 열처리되며, 금형 수명은 대량 생산 생산성에 큰 영향을 미치는 중요한 요소입니다.
금형 손상은 적용 분야에 따라 다양하게 나타나며, 열 피로 균열이 일반적인 파손 형태이며, 공구 표면에 미세 균열 또는 개별 균열 네트워크로 관찰됩니다. 열 피로 균열 형성은 작은 파편 형태의 표면 재료 손실로 이어집니다.
다른 손상 원인으로는 구조적 노치로 인한 인장 균열, 국부적인 합금 접착(땜납), 용융 금속 또는 플라스틱 주조에 의한 강철 침식 등이 있습니다. 플라스틱 사출 금형은 더 낮은 작동 온도에서 작동하지만, 더 까다로운 압력 사이클을 견뎌야 하므로 기계적 피로 및 과부하 파손이 발생할 수 있습니다 [1].
알루미늄 합금 주조용 금형 부품 및 코어는 고온에서 적절한 물리적, 기계적 특성을 가져야 하며, 이는 열 및 기계적 응력, 그리고 알루미늄 용융물과의 계면 상호 작용에 의해 정의됩니다. 알루미늄 용융물로 금형 캐비티를 난류 및 분산 충전하는 높은 속도, 유체역학적 압력 및 높은 표면 온도는 금형 및 코어의 수명을 단축시킬 수 있습니다.
이러한 현상은 침식, 마모, 부식 및 열 피로 메커니즘에 의해 표면 열화를 유발하며, 각각 동시에 작용합니다.
3. Research Background:
Background of the Research Topic:
알루미늄 및 플라스틱 주물은 자동차 산업에서 매우 중요하며, 주로 금속 금형을 사용하는 다이캐스팅 및 사출 성형을 통해 생산됩니다. 다이캐스팅 금형은 일반적으로 크롬 또는 공구강으로 만들어지고 29-48 HRC로 열처리되며, 수명과 생산 효율성에 영향을 미치는 상당한 문제에 직면합니다.
금형 수명은 다이캐스팅 생산성에 중요한 요소이며, 주조 또는 금형 적용 분야에 따라 다양한 유형의 금형 손상에 의해 크게 영향을 받습니다. 열 피로 균열은 일반적인 파손 모드이며, 공구 표면에 미세 균열 또는 개별 균열 네트워크로 나타나 재료 손실을 유발합니다.
추가적인 손상 원인으로는 구조적 불규칙성으로 인한 인장 균열, 솔더링(주조 합금의 국부적 접착), 강철 침식 등이 있습니다. 이러한 열화 메커니즘은 알루미늄 용융물 주입 중 높은 유체역학적 압력과 온도에 의해 악화되어 침식, 마모, 부식 및 열 피로를 유발합니다 [2].
Status of Existing Research:
현재 산업계에서는 공구 및 기계 부품의 표면 보호 및 처리에 중점을 두고 있습니다. 그러나 최종 표면 마감 방법의 발전은 뒤쳐져 있습니다. 최종 표면 처리 방법의 연구 개발은 주로 학술 기관 및 전문 연구소에 집중되어 있습니다 [6]. 향상된 특성을 달성하고 새로운 응용 분야를 가능하게 하는 진보적인 표면 마감 기술이 개발되고 있습니다.
표면 전처리는 적절한 코팅 증착을 보장하고 원하는 수명과 내구성을 달성하는 데 매우 중요합니다 [7]. 금속 압력 다이캐스팅 공구 및 금형의 마모는 주로 열 피로, 마모, 침식 및 용융 금속의 부식 작용으로 인해 발생하며, 금형 기능 표면에 표면 형태 변화 및 용융물 달라붙음을 유발합니다 [8].
Necessity of the Research:
금형 표면 열화를 완화하기 위한 잠재적인 해결책은 용융 알루미늄과 접촉하는 부품의 표면 처리를 포함합니다. 가혹한 주조 조건(열 및 화학적 작용)으로 인해 금형 표면은 손상되기 쉽고 금형 수명은 중요한 관심사입니다. 열처리된 공구의 레이저 경화 후 PVD 코팅 증착은 저항을 향상시키는 유망한 접근 방식입니다.
이 방법은 코팅 전에 더 나은 표면 접착 특성을 달성하기 위해 레이저 전처리를 활용합니다 [9]. 슬로바키아 공화국의 자동차 산업은 유럽 자동차 생산의 상당 부분을 차지하며, 전략적으로 더 가볍고 경제적이며 친환경적인 차량에 초점을 맞추고 있습니다.
강철 부품을 경금속 합금, 특히 비용 효율적인 다이캐스팅 기술 [10]을 통해 생산된 알루미늄 주물로 대체하는 것이 핵심 전략입니다.
합금 특성, 금형 설계 및 작동 매개변수를 포함한 다이캐스팅 기술 최적화는 생산 효율성 및 주조 품질에 매우 중요합니다. 금형 설계 및 기술 수명은 주조 품질 요구 사항 및 기술 매개변수 공차에 의해 제한되는 결정적인 요소입니다 [11].
4. Research Purpose and Research Questions:
Research Purpose:
주요 연구 목적은 자동차 산업용 알루미늄 합금의 고압 다이캐스팅에 사용되는 금형 및 코어의 서비스 수명을 늘리는 것입니다. 이는 레이저 표면 재용융 기술과 함께 듀플렉스 PVD 코팅을 적용하여 달성합니다.
Key Research:
핵심 연구는 레이저 처리된 Uddeholm Dievar 강철 표면에 듀플렉스 PVD 코팅, 특히 AIXN³ 및 nACRo³의 효과를 평가하는 데 중점을 둡니다. 이 연구는 열 피로, 침식 및 마모와 같이 알루미늄 다이캐스팅에서 널리 퍼진 열화 메커니즘에 대한 금형 표면 저항 향상을 조사합니다. 또한 적용된 코팅의 접착력 및 미세 형상과 모의 다이캐스팅 조건에서의 성능을 특성화하는 것을 목표로 합니다.
5. Research Methodology
Research Design:
본 연구는 국부 집중 레이저 가열을 사용한 Uddeholm Dievar 강철 시편의 표면 처리와 Larc 기술을 사용한 듀플렉스 PVD 코팅(AIXN³ 및 nACRo³) 증착을 포함하는 실험 설계를 채택했습니다. 레이저 처리를 하지 않은 대조군 시편도 준비했습니다. 처리 및 코팅된 시편은 코팅 품질 및 표면 특성을 평가하기 위해 다양한 평가 방법을 거쳤습니다. 이러한 방법에는 스크래치 테스트, 메르세데스 테스트, ISO 25 178에 따른 표면 미세 형상 분석, 다이캐스팅 조건을 모의 실험하기 위한 용융 Al-Si 합금 침지 등이 포함됩니다.
Data Collection Method:
데이터는 다음과 같은 여러 실험 기술을 통해 수집되었습니다.
- 스크래치 테스트 및 메르세데스 테스트: 코팅의 접착-응집 거동을 평가합니다. 메르세데스 테스트는 1500 N 하중의 로크웰 압입자를 사용하여 DIN EN ISO 18265에 따라 평가하고 접착 번호 HF1에서 HF6까지 사용하여 분류했습니다 [19].
- 표면 미세 형상 분석: ISO 25 178 표준에 따라 평가하여 레이저 처리 및 코팅 후 표면 거칠기 및 지형 매개변수를 정량화했습니다.
- 침지 테스트: 시편을 680 ± 20°C의 Al-Si 합금 용융물에 120분 및 300분 동안 담가 용융 금속 공격에 대한 코팅 저항을 평가했습니다.
- 현미경(광학 및 SEM): 표면 결함, 코팅 단면 및 압입 형태의 육안 검사에 사용되었습니다.
- EDX 미세 분석: 국부적인 화학 조성을 결정합니다.
- 미세 경도 테스트: 코팅 및 모재 전체의 경도 프로파일을 평가합니다.
- 모세관 테스트: 마모된 금형 인서트의 표면 및 표면하 결함을 식별합니다.
Analysis Method:
- 정성적 분석: 표면 결함, 균열 전파 및 코팅 무결성에 대한 육안 검사 및 현미경 검사. HF 척도를 기준으로 한 메르세데스 테스트 압흔 평가.
- 정량적 분석: 스크래치 테스트 임계 하중 측정, ISO 25 178 분석에서 얻은 표면 거칠기 매개변수(Sa, Sq, Ssk, Sku, Sp, Sv, Sz) 및 미세 경도 값. 다양한 처리 조건 비교를 위한 표면 매개변수 데이터의 통계 분석.
- 비교 분석: AIXN³ 및 nACRo³ 코팅 간의 결과와 레이저 처리 및 비 레이저 처리 시편 간의 결과를 비교하여 복합 표면 처리 접근 방식의 효과를 결정합니다.
Research Subjects and Scope:
연구 대상은 다이캐스팅 금형 및 코어에 일반적으로 사용되는 크롬-몰리브덴 공구강인 Uddeholm Dievar 강철 시편입니다. 연구 범위는 자동차 산업의 알루미늄 다이캐스팅 응용 분야에서의 성능에 초점을 맞춰 이러한 강철 시편에 적용된 듀플렉스 PVD 코팅(AIXN³ 및 nACRo³)을 조사하는 것으로 제한됩니다. 이 연구는 코팅 접착력 및 성능을 향상시키기 위한 전처리로서 레이저 표면 재용융의 효과를 구체적으로 조사합니다.
6. Main Research Results:
Key Research Results:
- 금형 표면 저항 증가: 실험 결과 레이저 표면 재용융 및 듀플렉스 PVD 코팅(AIXN³ 및 nACRo³) 적용 후 금형 표면의 저항이 크게 증가한 것으로 확인되었습니다.
- 우수한 코팅 접착력: 스크래치 테스트 및 메르세데스 테스트에서 확인된 바와 같이 AIXN³ 및 nACRo³ 코팅 모두 만족스러운 접착력을 나타냈습니다. 접착력은 메르세데스 테스트에서 HF 1-2로 분류되었으며, 이는 압흔 주변에 최소한의 균열이 있는 양호에서 만족스러운 접착력을 나타냅니다.
- 표면 미세 형상: ISO 25 178에 따라 평가된 표면 미세 형상 매개변수는 레이저 표면 전처리 및 연삭이 연삭 표면에 비해 듀플렉스 PVD 코팅의 표면 매개변수에 큰 영향을 미치지 않는 것으로 나타났습니다.
- 경도 향상: 미세 경도 측정 결과 레이저 처리된 모재의 코팅 영역에서 모재 재료에 비해 18.6 - 25% HV0.025의 경도 증가가 나타났습니다.
- 용융 알루미늄에 대한 저항: 680 ± 20°C의 용융 Al-Si 합금에 침지 후 코팅은 조밀하고 손상되지 않은 상태로 유지되었으며, 모재와 용융물 사이에 장벽을 형성하여 고온 부식에 대한 저항을 입증했습니다.
- 레이저 경화 매개변수: 레이저 표면 경화는 400W 레이저와 3mm 빔 직경을 사용하여 20mm/s, 30mm/s, 40mm/s 및 60mm/s의 스캔 속도에서 각각 160μm, 90μm, 80μm 및 75μm의 가열 깊이를 달성했습니다.
Analysis of presented data:
- 경도 프로파일 (Figure 10): Figure 10은 nACRo³ 및 AIXN³ 코팅 모두에 대한 표면에서 모재 방향으로의 경도 프로파일 HV0.025를 보여줍니다. 두 코팅 모두 표면에서 더 높은 경도 값을 나타내며, 모재 방향으로 감소하여 모재 경도(W300)에 접근하는 것을 보여줍니다. nACRo 코팅된 시편에 대한 0.025 HVm 압흔은 레이저 영역과 W300 모재의 계면에 표시됩니다.
- 표면 매개변수 (Table 4): Table 4는 ISO 25 178에 따른 PVD 코팅의 표면 매개변수를 나타냅니다. PVD 코팅 듀플렉스 nACRo³, PVD 코팅 듀플렉스 AIXN³, 레이저 처리된 표면의 PVD 코팅 듀플렉스 nACRo³ 및 레이저 처리된 표면의 PVD 코팅 듀플렉스 AIXN³에 대한 Sq, Ssk, Sku, Sp, Sv, Sz 및 Sa 값을 비교합니다. 데이터는 레이저 전처리가 표면 미세 형상 매개변수를 크게 변경하지 않았음을 나타냅니다.
- 메르세데스 테스트 (Figure 12 & 13): Figure 12와 Figure 13은 각각 AIXN³ 및 nACRo³ 코팅에 대한 메르세데스 테스트에서 얻은 압흔 형태를 보여줍니다. 이미지는 고립된 방사형 균열만 나타내어 우수한 코팅 품질과 접착력을 확인하며, HF 1-2 접착 등급에 해당합니다.
Figure Name List:
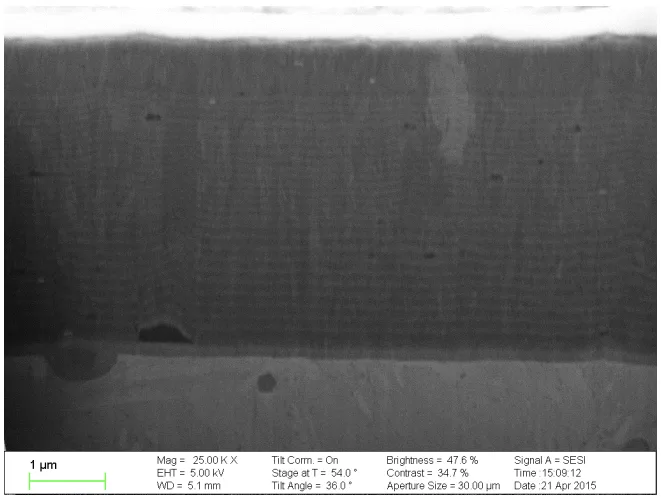
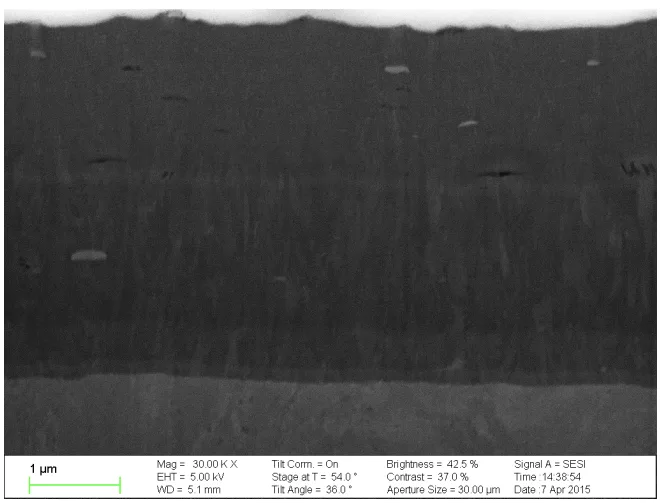
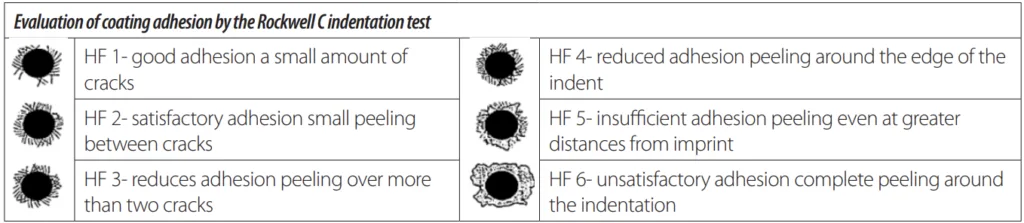
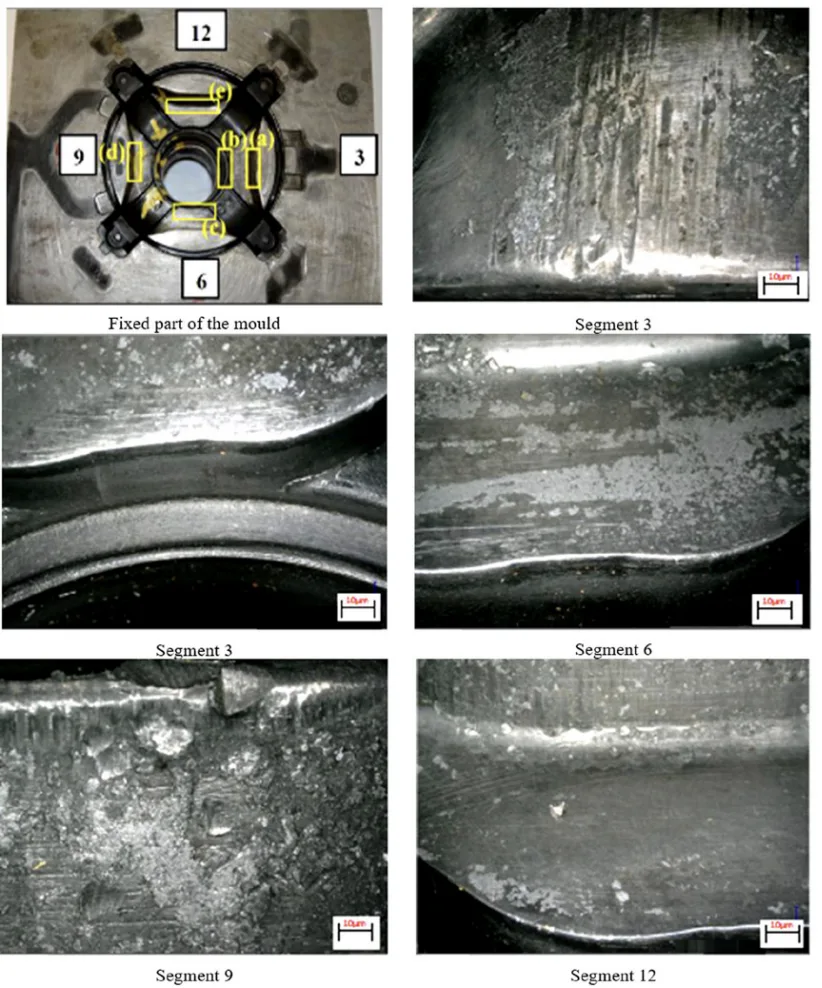
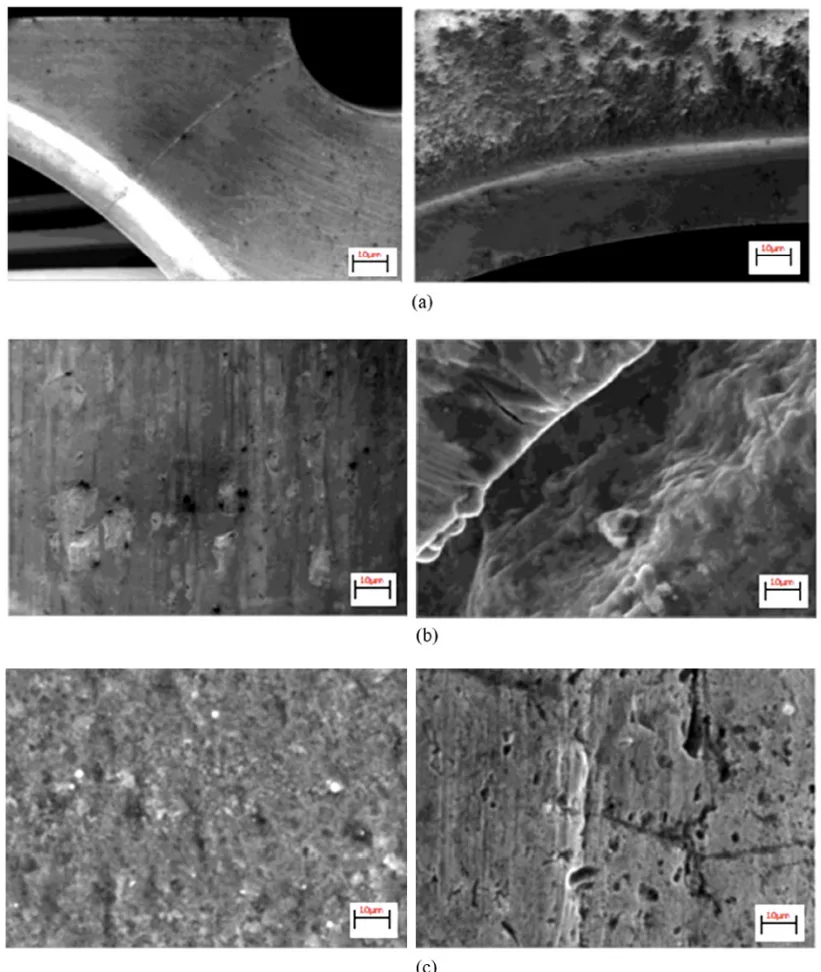
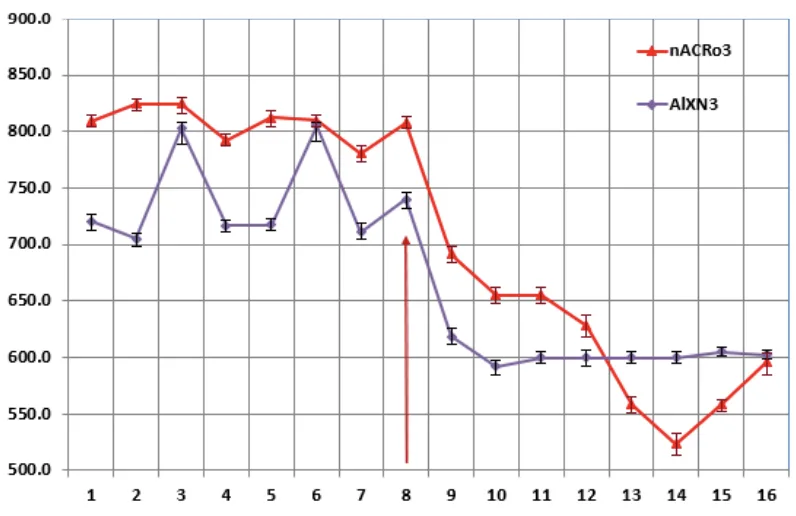
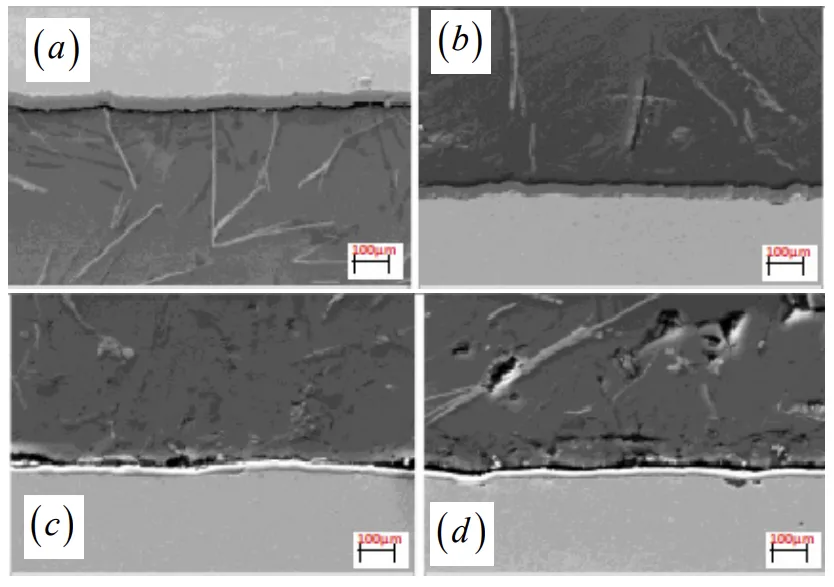
- Figure 1: FIB (Focused Ion Beam) 장치에서 제작된 AIXN³ 코팅의 단면
- Figure 2: FIB 장치에서 수행된 nACRo³ 코팅의 단면
- Figure 3: 마모된 금형 부품 - 금형 인서트의 솔리드 절반
- Figure 4: 모세관 테스트 후 성형된 금형 부품
- Figure 5: 금형 하단의 균열 모양
- Figure 6: 마모된 형태의 세부 사항; a) 이젝터 및 코어 캐비티 주변의 균열 b) 성형 부품 표면의 분리 수단 c) 가동 코어와 성형 부품의 접촉
- Figure 7: 레이저 표면 경화
- Figure 8: 레이저 처리 및 코팅 증착 후 대조군 시편 및 시편의 PVD 코팅 표면
- Figure 9: nACRo 코팅된 시편에 대한 압흔
- Figure 10: 표면에서 모재 방향으로의 경도 테스트 HV0.025
- Figure 11: 스크래치 테스트 시스템 o PVD 코팅 - 레이저 열처리된 모재; a) PVD 코팅 듀플렉스 AIXN³; b) PVD 코팅 듀플렉스 nACRo³; c) 레이저 처리된 표면의 PVD 코팅 듀플렉스 AIXN³; d) 레이저 처리된 표면의 PVD 코팅 듀플렉스 nACRo3
- Figure 12: AIXN3 코팅 (X = Cr)의 압흔 형태
- Figure 13: nACR03, LM 코팅의 압흔 형태
- Figure 14: Al 용융물에 노출 후 레이저 처리 및 연삭된 표면의 PVD 코팅 듀플렉스; a) 듀플렉스 AIXN³/120분/680+/-20°C/Al-Si; b) 듀플렉스 AIXN³/300분/680 +/-20°C/Al-Si; c) 듀플렉스 nACRo³/120분/680+/-20°C/Al-Si; d) 듀플렉스 nACRo³/300분/680+/-20°C/Al-Si
7. Conclusion:
Summary of Key Findings:
본 연구는 국부 레이저 표면 재용융과 듀플렉스 PVD 코팅(AIXN³ 및 nACRo³)을 결합한 다이캐스팅 금형 및 코어용 혁신적인 표면 처리 방법을 성공적으로 입증했습니다. 이 접근 방식은 알루미늄 다이캐스팅 환경에서 열화에 대한 금형 표면의 저항을 크게 증가시켰습니다. 적용된 PVD 코팅은 고품질과 강력한 접착력을 나타내어 용융 알루미늄 및 고온 부식에 대한 효과적인 장벽 역할을 했습니다. 표면 미세 형상은 레이저 전처리 및 연삭에 의해 크게 변경되지 않았습니다.
Academic Significance of the Study:
본 연구는 다이캐스팅 금형의 열화 메커니즘에 대한 기본적인 이해에 기여하고 고급 표면 엔지니어링 기술을 통해 금형 수명을 연장하기 위한 검증된 방법론을 제공합니다. 이 연구는 가혹한 다이캐스팅 조건에서 공구강의 성능을 향상시키는 데 있어 레이저 표면 재용융과 듀플렉스 PVD 코팅의 시너지 효과를 강조합니다.
Practical Implications:
본 연구 결과는 자동차 및 다이캐스팅 산업에 중요한 실질적인 의미를 갖습니다. 개발된 표면 처리 방법은 다이캐스팅 금형 및 코어의 서비스 수명을 연장하는 실행 가능한 솔루션을 제공하여 공구 비용 절감, 생산 효율성 향상 및 주조 품질 개선으로 이어집니다. 이는 자동차 부문에서 경량 알루미늄 부품 생산에 특히 관련이 있으며, 보다 경제적이고 친환경적인 차량 개발에 기여합니다.
Limitations of the Study and Areas for Future Research:
본 연구는 실험실 규모의 실험과 모의 다이캐스팅 조건에 초점을 맞추었습니다. 향후 연구는 다음 영역에 초점을 맞춰야 합니다.
- 산업 규모 검증: 개발된 표면 처리 방법을 실제 생산 환경에서 성능과 확장성을 평가하기 위해 산업 다이캐스팅 작업에서 테스트합니다.
- 장기 성능 평가: 연속 다이캐스팅 사이클에서 처리된 금형 및 코어의 수명 연장을 평가하기 위해 장기 내구성 테스트를 수행합니다.
- 레이저 및 코팅 매개변수 최적화: 코팅 성능과 효율성을 극대화하기 위해 레이저 표면 재용융 및 PVD 코팅 매개변수를 추가로 최적화합니다.
- 경제성 분석: 기존 금형 유지 보수 및 교체 전략과 비교하여 제안된 표면 처리 방법의 비용 효율성을 정량화하기 위해 포괄적인 경제성 분석을 수행합니다.
- 다른 코팅 재료 조사: 금형 표면 특성 및 특정 열화 메커니즘에 대한 저항성을 더욱 향상시키기 위해 다른 고급 PVD 코팅 재료 및 조성을 탐색합니다.
8. References:
- [1] Changrong Chen et al.: Energy based approach to thermal fatigue life of tool steels for die casting dies. In: International Journal of Fatigue Volume 92, Part 1, November 2016, Pages 166-178.
- [2] J. Lin et al.: Design methodology for optimized die coatings: The case for aluminium pressure die-casting In: Surface and Coatings Technology 201 (2006) pp. 2930-2941.
- [3] K. Domkin, J.H. Hattel, J. Thorborg, Modeling of high temperature- and diffusion-controlled die soldering in aluminium high pressure die casting, J. Mater. Process. Technol. 209 (8) (2009) 4051-4061.
- [4] Sundqvist M., Hogmark S.: Effects of liquid aluminium on hot-work tool steel Tribol. Int. 26 (1993) in International Journal of Fatigue p. 129.
- [5] H. Zhu, J. Guo, J. Jia, Experimental study and theoretical analysis on die soldering in aluminium die casting, J. Mater. Process. Technol. 123 (2) (2002) 229-235.
- [6] Z.W. Chen, M.Z. Jahedi, Die erosion and its effect on soldering formation in high pressure die casting of aluminium alloys, Mater. Des. 20 (6) (1999) 303-309.
- [7] K. Venkatesan, R. Shivpuri, Experimental and numerical investigation of the effect of process parameters on the erosive wear of die casting dies, J. Mater. Eng. Perform. 4 (2) (1995) 166-174. R. Markežič et al. Engineering Failure Analysis 95 (2019) 171-180179.
- [8] A Mohammed, M.B. Marshall, R. Lewis, Development of a method for assessing erosive wear damage on dies used in aluminium casting, Wear 332-333 (2015)1215-1224.
- [9] LF. Hou, Y.H. Wei, Y.G. Li, B.S. Liu, H.Y. Du, C.L. Guo, Erosion process analysis of die-casting inserts for magnesium alloy components, Eng. Fail. Anal. 33 (2013)457-564.
- [10] D.W.C. Baker, K.H. Jolliffe, D. Pearson, The resistance of materials to impact erosion damage, Philos. Trans. R. Soc. A Math. Phys. Eng. Sci. 260 (1110) (1966) 193-203.
- [11] A. Persson, S. Hogmark, J. Bergström, Temperature profiles and conditions for thermal fatigue cracking in brass die casting dies, J. Mater. Process. Technol. 152(2) (2004) 228-236.
- [12] C. Rosbrook, Analysis of Thermal Fatigue and Heat Checking in Die-Casting Dies: A Finite Element Approach, PhD thesis Ohio State University, 1992.
- [13] F. Medjedoub, G. Dour, S. Le Roux, P. Lamesle, M. Salem, P. Hairy, F. Rézaï-Aria, Experimental conditions and environment effects on thermal fatigue damage accumulation and life of die-casting steel X38CrMoV5 (AISI H11), Int. J. Microstruct. Mater. Propert. 3 (2-3) (2008).
- [14] P. Hansson, "Modern prehardened tool steels in die-casting applications," Materials and Manufacturing Processes, vol. 24, no. 7-8, pp. 824-827, 2009.
- [15] Uddeholm, "Dievar," 2014, (18.10.2021) internet: http://www.uddeholm.com
- [16] D. Klobčar, J. Tušek, B. Taljat, Thermal fatigue of materials for die-casting tooling, Mater. Sci. Eng. A 472 (1) (2008) 198-207.
- [17] D. Schwam, J. F. Wallace, and S. Birceanu, "Die Materials for Critical Applications and Increased Production Rates," Case Western Reserve University, 2002.
- [18] Methodical measurement and evaluation of adhesive cohesive behavior of thin film - substrate systems, 2005, (19.10.2021) internet: https://www.opi.zcu.cz/adheze.html
- [19] J. Tkáčová, E. Zdravecká, E. Evin, M. Tomáš, D. Jakubéczyová: Koroze a ochrana materiálu 63(4) 159-166 (2019).
- [20] D. Klobčar, et al.: Thermo fatigue cracking of die casting dies. In: Engineering Faliure Analysis Volume 20, March 2012, pp. 43-53.
- [21] D. Jakubéczyová, M. Džupon: Effect of the roughness on the adhesive properties of nanocomposite PVD coatings. In Vrstvy a povlaky 2016: 15. ročník konferencie. Rožnov pod Radhoštěm, 17.-18.10.2016. - Plzeň: Západočeská univerzita, 2016, p. . 49-55.(Layers and coatings 2016)
9. Copyright:
- 본 자료는 "Janette Brezinová et al."의 논문: "Use of Duplex PVD Coatings to Increase the Life of Moulds and Cores for die Casting of Aluminium Alloys in the Automotive Industry"를 기반으로 합니다.
- 논문 출처: https://doi.org/10.21496/ams.2022.003
본 자료는 위 논문을 소개하기 위해 제작되었으며, 상업적 목적의 무단 사용을 금지합니다.
Copyright © 2025 CASTMAN. All rights reserved.