본 문서는 "Defect reduction using Lean Six Sigma and DMAIC" 연구 논문을 요약하여 다이캐스팅 산업에 대한 방법론, 연구 결과 및 시사점에 대한 자세한 개요를 제공합니다.
1. 개요: Overview
- 제목: Title: Lean Six Sigma 및 DMAIC을 활용한 결함 감소
- 저자: Authors: Condé, G.C.P., Oprime, P.C., Pimenta, M.L., Sordan, J.L., Bueno, C.R.
- 발행 연도: Year: 2022년 8월
- 발행 학술지/학회: Journal/Conference: 포르투갈 미뇨 대학교 제5회 ICQEM 컨퍼런스 회의록, 2022년
- Keywords:
- 결함 감소
- Lean Six Sigma
- DMAIC
2. 연구 배경: Research Background
- 연구 주제의 사회적/학문적 맥락: Social/Academic Context of the Research Topic:
- 경쟁 압력으로 인해 기업은 낭비를 제거하고 제품 품질을 개선하기 위한 솔루션을 모색하게 됩니다.
- Lean Six Sigma (LSS)는 비즈니스 혁신을 위한 가장 효과적인 접근 방식 중 하나로 간주됩니다.
- 자동차 부품 산업은 높은 폐기물 발생률과 불필요한 운영으로 인해 심각한 효율성 문제를 안고 있습니다.
- 자동차 부문에서 LSS 및 DMAIC 적용 사례가 일부 존재함에도 불구하고, 문헌에 따르면 이러한 방법론은 자동차 부품 제조업체에서 여전히 제대로 적용되지 않고 있습니다.
- 기존 연구의 한계점: Limitations of Existing Research:
- LSS 및 DMAIC 문헌에는 실제 적용 사례에 대한 많은 설명이 있지만, 자동차 부품 제조 환경 내에서 구조화된 개선 활동에 사용된 전체 프로세스에 대한 자세한 설명이 필요합니다.
- 연구의 필요성: Necessity of Research:
- Lean Six Sigma 및 DMAIC 방법론이 자동차 부품 제조업체의 결함 감소에 적용된 경험적 사례 연구를 제시합니다.
- 자동차 부품 제조에서 결함 감소를 위해 유사한 개선 방법론을 사용하려는 사람들에게 참고 자료를 제공합니다.
3. 연구 목적 및 연구 질문: Research Objectives and Research Questions
- 연구 목적: Research Objective:
- Lean Six Sigma 및 DMAIC 방법론을 사용하여 자동차 부품 제조업체의 결함 감소에 대한 경험적 사례 연구를 제시합니다.
- 구조화된 개선 활동에 사용된 전체 프로세스를 자세히 설명합니다.
- 핵심 연구 질문: Core Research Questions:
- Lean Six Sigma 및 DMAIC 방법론은 자동차 부품 제조 회사의 다이캐스팅 및 가공 공정에서 결함을 줄이기 위해 어떻게 효과적으로 적용될 수 있습니까?
- 이러한 공정에서 결함률에 영향을 미치는 주요 변수는 무엇입니까?
- 결함 발생률을 지속적으로 줄이고 시그마 수준을 개선하기 위해 어떤 솔루션을 구현할 수 있습니까?
- 연구 가설: Research Hypothesis:
- Lean Six Sigma 프레임워크 내에서 DMAIC 방법론을 적용하면 자동차 부품 제조의 다이캐스팅 및 가공 공정에서 결함이 유의미하고 지속적으로 감소할 수 있습니다.
4. 연구 방법론: Research Methodology
- 연구 설계: Research Design:
- 경험적 단일 종단 사례 연구.
- DMAIC 방법론(Define, Measure, Analyse, Improve, Control)을 따랐습니다.
- 데이터 수집 방법: Data Collection Methods:
- DMAIC 단계 순서에 따라 반구조화된 인터뷰를 실시했습니다.
- 문서 분석.
- 직접 현장 관찰.
- 분석 방법: Analysis Methods:
- Minitab을 사용한 통계 분석.
- 실험 설계 (요인 실험).
- 가설 검정.
- 원인-결과 매트릭스.
- 측정 시스템 분석 (MSA).
- 공정 능력 분석.
- 연구 대상 및 범위: Research Subject and Scope:
- 브라질에 위치한 주요 자동차 제조업체에 다이캐스팅 및 가공 알루미늄 자동차 부품을 생산하는 제조 회사.
- 본 연구는 특정 자동차 부품인 리어 뷰 하우징 지지대 (RHS)의 다이캐스팅 및 가공 공정에서 결함 감소에 초점을 맞추었습니다.
5. 주요 연구 결과: Key Research Findings
- 핵심 연구 결과: Core Research Findings:
- 분석 결과 다이캐스팅 및 가공 단계에서 주요 결함이 지적되었습니다.
- 다이캐스팅: "금형 온도, 금속 온도 및 2단 사출 속도가 불량 다이캐스팅 부품의 양에 영향을 미쳤습니다."
- 가공: "반면에 가공 공정에서 결함 발생률은 고정 방법에 영향을 받았습니다."
- "구현된 솔루션은 만성적으로 높은 수준에서 허용 가능한 수준으로 결함 발생률을 감소시켰습니다."
- "시그마 수준은 3.4σ에서 4σ로 지속적으로 상승했습니다."
- 통계적/정성적 분석 결과: Statistical/Qualitative Analysis Results:
- Define 단계: "다이캐스팅 부품의 불량률에 대한 p-차트 (그림 1)와 가공 부품의 불량률에 대한 p-차트 (그림 2)가 작성되었습니다." 이러한 차트는 특수 원인과 높은 결함률을 가진 공정을 보여주었습니다. 기준 시그마 수준은 "3.4 시그마"로 계산되었습니다.
- Measure 단계: "프로젝트 팀은 SIPOC (공급업체, 투입물, 공정, 산출물, 고객) 매트릭스 (그림 3)를 준비했습니다." 상세 변수 분석을 통해 결함률에 영향을 미치는 30개의 가능한 변수를 확인했습니다 (표 3). "원인-결과 매트릭스"는 7개의 주요 변수에 우선 순위를 부여했습니다 (표 4 및 5). "측정 시스템 분석 (MSA)"은 허용 가능한 측정 시스템을 확인했습니다 ("표 7에서 모든 카파 값이 0.7 이상").
- Analyse 단계: "이시카와 다이어그램" (그림 7 및 그림 8)은 근본 원인 분석에 사용되었습니다. "일련의 요인 실험" (그림 9, 10, 13, 14)은 중요한 변수를 확인했습니다.
- 다이캐스팅: 금형 온도 (x1), 금속 온도 (x2) 및 2단 사출 속도 (x3). 최적 조합은 그림 12에서 찾았습니다: "금형 온도 수준 = 220°C, 금속 온도 수준 = 700°C, 사출 속도 (2단계) 수준 = 초당 3미터".
- 가공: 고정 방법 (x5). 최적 방법은 그림 16에서 찾았습니다: "유형 II (대안) 고정 방법 - x5, 이름은 “Torres”".
- Improve 단계: "의사 결정 매트릭스" (표 10)는 "열유 사용, 새로운 가공 고정 방법, 주조 부품 유지 보수 개선, 대안 공구 홀더 유형"의 4가지 솔루션을 구현하기 위해 순위를 매기고 선택했습니다.
- Control 단계: "가설 검정" (그림 18 및 그림 19)은 다이캐스팅 및 가공 공정 모두에서 결함률이 유의미하게 감소했음을 확인했습니다 ("P-값 = 0.000"). "공정 능력 분석" (그림 21 및 그림 22)은 "4σ" 시그마 수준 (그림 20)에 도달하여 개선되고 지속적인 공정 성능을 보여주었습니다.
- 데이터 해석: Data Interpretation:
- 통계 분석 및 실험 결과는 DMAIC 방법론이 결함의 근본 원인을 식별하고 해결하는 데 효과적임을 입증했습니다.
- 최적화된 매개변수와 구현된 솔루션은 결함률의 유의미하고 지속적인 감소와 공정 시그마 수준 개선으로 이어졌습니다.
- Figure Name List:
- 그림 1 - 다이캐스팅 부품의 불량률에 대한 p-차트.
- 그림 2 - 가공 부품의 불량률에 대한 p-차트.
- 그림 3 - SIPOC / 다이캐스팅 및 가공 하우징 지지대 제조 공정.
- 그림 4 - 부품 영역.
- 그림 5 - 개선 전 최종 공정 수율 계산.
- 그림 6 - 파레토 차트 - 부품 불량의 주요 원인.
- 그림 7 - 선택된 변수 x1 (금형 온도)에 대한 근본 원인 분석.
- 그림 8 - 선택된 변수 x7 (절삭 공구 유형 - 나사산)에 대한 근본 원인 분석.
- 그림 9 - 1차 실험 실행 효과에 대한 파레토 차트 - 다이캐스팅.
- 그림 10 - 2차 실험 실행 효과에 대한 파레토 차트 - 다이캐스팅.
- 그림 11 - 2차 실험 실행 상호 작용 - 다이캐스팅.
- 그림 12 - 2차 실험 실행 중 발견된 최적 변수 조합 - 다이캐스팅.
- 그림 13 - 1차 실험 실행 효과에 대한 파레토 차트 - 가공.
- 그림 14 - 2차 실험 실행 효과에 대한 파레토 차트 - 가공.
- 그림 15 - 2차 실험 실행 상호 작용 - 가공.
- 그림 16 - 2차 실험 실행 중 발견된 최적 변수 조합 - 다이캐스팅.
- 그림 17 - 프로젝트 팀 회의.
- 그림 18 - 다이캐스팅 개선에 대한 가설 검정.
- 그림 19 - 가공 개선에 대한 가설 검정.
- 그림 20 - 개선된 공정의 최종 공정 수율 계산.
- 그림 21 - 주기적 공정 능력 분석 - 다이캐스팅 공정.
- 그림 22 - 주기적 공정 능력 분석 - 가공 공정.
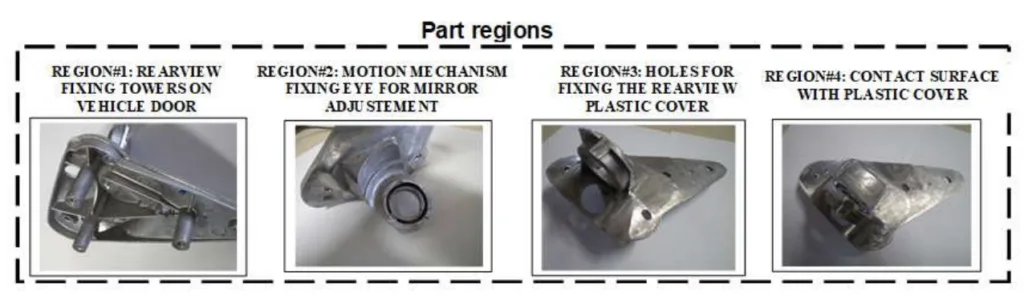
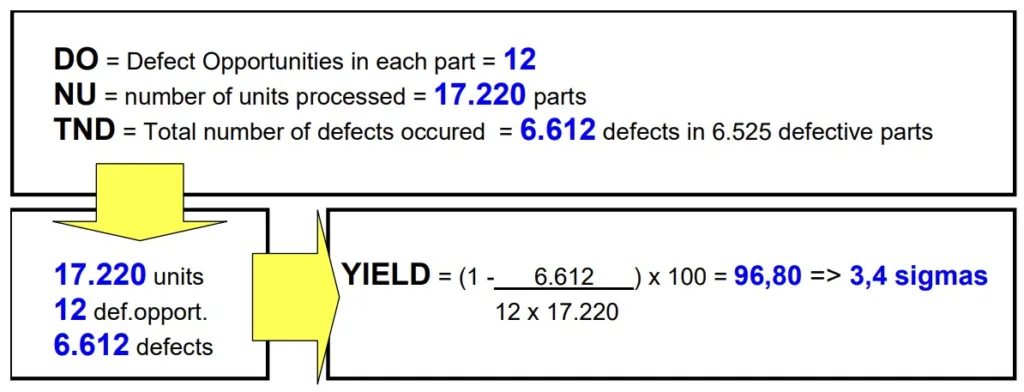
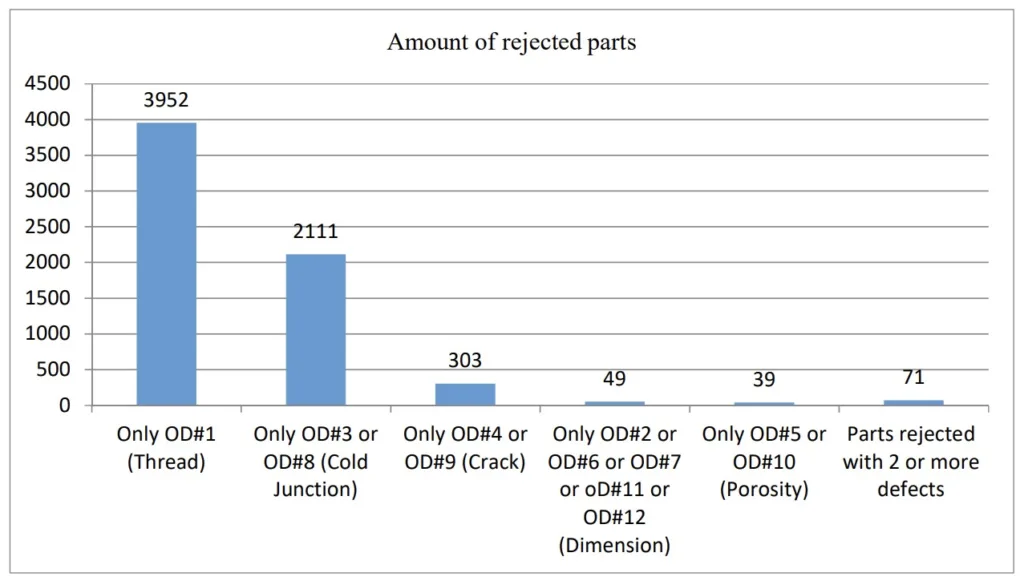
6. 결론 및 논의: Conclusion and Discussion
- 주요 결과 요약: Summary of Main Results:
- 프로젝트는 DMAIC 방법론을 성공적으로 적용하여 다이캐스팅 및 가공 공정에서 결함을 줄였습니다.
- 결함에 영향을 미치는 주요 변수를 식별하고 최적화했습니다.
- 구현된 솔루션은 시그마 수준을 "3.4σ에서 4σ"로 지속적으로 증가시켰습니다.
- "다이캐스팅 공정에서 7% 미만" 및 "가공 공정에서 1% 미만"으로 불량률을 줄이는 프로젝트 목표를 달성했습니다.
- 연구의 학술적 의의: Academic Significance of the Research:
- 자동차 부품 제조에서 Lean Six Sigma 및 DMAIC의 효과적인 적용을 입증하는 상세한 경험적 사례 연구를 제공합니다.
- 특정 도구 및 기술의 사용을 포함하여 DMAIC 구현의 단계별 프로세스를 설명하여 문헌에 기여합니다.
- 실무적 시사점: Practical Implications:
- 본 논문은 동일한 유형의 개선 방법론을 사용하려는 사람들에게 활용될 수 있습니다.
- 본 연구는 결함 감소를 위해 Lean Six Sigma 프로젝트를 구현하려는 자동차 부품 산업의 관리자 및 엔지니어에게 참고 자료로 사용될 수 있습니다.
- 상세한 방법론과 식별된 주요 변수는 유사한 개선 이니셔티브에 대한 실질적인 지침을 제공합니다.
- 성공적인 사례 연구는 DMAIC가 제조 공정에서 유의미하고 지속적인 개선을 달성할 수 있는 잠재력을 입증합니다.
- 연구의 한계점: Limitations of the Research:
- "본 연구는 단일 사례 연구로 제한되며, 결과를 다른 유형의 산업으로 일반화할 의도는 없습니다."
7. 향후 후속 연구: Future Research
- 후속 연구 방향: Directions for Future Research:
- 향후 연구에서는 이러한 연구 결과의 일반화 가능성을 다른 유형의 산업 및 제조 공정으로 확장하여 탐구할 수 있습니다.
- 결함 감소 외에 자동차 부품 제조의 다른 영역에서 LSS 및 DMAIC의 적용을 조사하는 것이 유익할 수 있습니다.
- 추가 탐구가 필요한 영역: Areas for Further Exploration:
- 달성된 개선 사항의 장기적인 지속 가능성과 이에 영향을 미치는 요인을 탐구합니다.
- 자동차 부품 제조에서 LSS 및 DMAIC 구현의 성공에 대한 조직 문화 및 직원 참여의 영향을 조사합니다.
8. 참고문헌: References
- Antony, J. (2015), “Challenges in the deployment of LSS in the higher education sector: Viewpoints from leading academics and practitioners”, International Journal of Productivity and Performance Management.
- Antony, J., Antony, F. J., Kumar, M. and Cho, B. R. (2007). “Six sigma in service organisations: Benefits, challenges and difficulties, common myths, empirical observations and success factors", International journal of quality & reliability management, Vol. 24 No. 3, pp. 294-311.
- Bass, I., and Lawton, B. (2009). Lean six sigma using SigmaXL and Minitab. McGraw Hill Professional.
- Bayou, M. E. and De Korvin, A. (2008). “Measuring the leanness of manufacturing systems—a case study of Ford Motor Company and General Motors”, Journal of Engineering and Technology Management, Vol. 25 No 4, pp. 287-304.
- Chaurasia, B., Garg, D., & Agarwal, A. (2019), “Lean Six Sigma approach: a strategy to enhance performance of first through time and scrap reduction in an automotive industry”, International Journal of Business Excellence, Vol. 17, No. 1, pp. 42-57.
- Costa, L. B. M., Godinho Filho, M., Fredendall, L. D. and Ganga, G. M. D. (2021), “Lean six sigma in the food industry: Construct development and measurement validation”, International Journal of Production Economics, Vol. 231, pp. 107843.
- Chua, R. C. H. and DeFeo, J. A. (2006), Juran's quality planning and analysis: For enterprise quality. Tata McGraw-Hill Education.
- Daniyan, I., Adeodu, A., Mpofu, K., Maladzhi, R. and Katumba, M. G. K. Κ. (2022), “Application of lean Six Sigma methodology using DMAIC approach for the improvement of bogie assembly process in the railcar industry”, Heliyon, e09043.
- Doolen, T. L. and Hacker, M. E. (2005), “A review of lean assessment in organizations: an exploratory study of lean practices by electronics manufacturers”, Journal of Manufacturing systems, Vol. 24 No. 1, pp. 55-67.
- George, M. L., Maxey, J., Rowlands, D. T., & Upton, M. (2004). Lean six sigma pocket toolbook. McGraw-Hill Professional Publishing.
- Gupta, S., Modgil, S. and Gunasekaran, A. (2020), “Big data in lean six sigma: a review and further research directions”, International Journal of Production Research, Vol. 58 No. 3, pp. 947-969.
- International Organization for Standardization. ISO 13.053-1: Quantitative methods in process improvement – Six Sigma Part 1: DMAIC methodology. Genebra: ISO, 2011.
- Kahraman, C., and Büyüközkan, G. (2008), “A Combined Fuzzy AHP and Fuzzy Goal Programming Approach for Effective Six-Sigma Project Selection”, Journal of Multiple-Valued Logic & Soft Computing, Vol. 14 No. 6.
- Karlsson, C. and Åhlström, P. (1996). “Assessing changes towards lean production", International Journal of Operations & Production Management.
- Kwak, Y. H., and F. T. Anbari. (2006), “Benefits, Obstacles, and Future of Six Sigma Approach”, Technovation, Vol. 26 No. 5–6, pp. 708–715.
- Mancilla-Escobar, J., Maccasi-Jaurequi, I., Raymundo-Ibañez, C. and Perez, M. (2020, March). Layout Lean model of production management based on change management to improve efficiency in the production of packaging in auto parts sector SMEs. In IOP Conference Series: Materials Science and Engineering (Vol. 796, No. 1, p. 012014). IOP Publishing.
- McLachlin, R. (1997), “Management initiatives and just-in-time manufacturing”, Journal of Operations management, Vol. 15 No. 4, pp. 271-292.
- Mishra, Y., Sharma, M. K., Yadav, V., Meena, M. L. and Dangayach, G. S. (2021), “Lean Six Sigma implementation in an Indian manufacturing organisation: a case study”, International Journal of Six Sigma and Competitive Advantage, Vol. 13 No. 1-3, pp. 76-100.
- Panizzolo, R. (1998), “Applying the lessons learned from 27 lean manufacturers.: The relevance of relationships management”, International journal of production economics, Vol. 55 No. 3, pp. 223-240.
- Pinheiro, T. H., Scheller, A. C., & Miguel, P. A. C. (2013), “Integração do seis sigma com o lean production: uma análise por meio de múltiplos casos”, Revista Produção Online, Vol. 13 No. 4, pp. 1297-1324.
- PMBOK, G. (2008). Um guia do conjunto de conhecimentos em gerenciamento de projetos (guia pmbok®). Project Management Institute, Inc. EUA.
- Salah, S., Rahim, A. and Carretero, J. A. (2010), “The integration of Six Sigma and lean management", International Journal of Lean Six Sigma.
- Schroeder, R. G., Linderman, K., Liedtke C. and Choo, A.S. (2009), “Six Sigma: Definition and Underlying Theory.” Quality Control and Applied Statistics, Vol. 54 No. 5: pp. 441–445.
- Shah, R. and Ward, P. T. (2003), “Lean manufacturing: context, practice bundles, and performance", Journal of operations management, Vol. 21 No. 2, pp. 129-149.
- Shokri, A. (2019), “Reducing the scrap rate in manufacturing SMEs through lean six sigma methodology: An action research”, IEEE Engineering Management Review, Vol. 47 No. 3, pp. 104-117.
- Snee, R. D. (2004), “Six-Sigma: The Evolution of 100 Years of Business”, International Journal of Six Sigma and Competitive Advantage, Vol. 1 No. 1: pp. 4-20.
9. 저작권: Copyright
- 본 자료는 [Giovanni Condé, Pedro Carlos Oprime, Pimenta, M.L., Sordan, J.L., Bueno, C.R.]의 논문: [Defect reduction using Lean Six Sigma and DMAIC]을 기반으로 작성되었습니다.
- 논문 출처: https://www.researchgate.net/publication/362389760
본 자료는 위 논문을 바탕으로 요약 작성되었으며, 상업적 목적으로 무단 사용이 금지됩니다.
Copyright © 2025 CASTMAN. All rights reserved.