본 문서는 "A356 알루미늄 휠의 저압 다이캐스팅 공정의 컴퓨터 지원 설계" 연구 논문을 요약한 것입니다.
1. 개요:
- 제목: Compute-Aided Design of Low Pressure Die-Casting Process of A356 Aluminum Wheels (A356 알루미늄 휠의 저압 다이캐스팅 공정의 컴퓨터 지원 설계)
- 저자: Pei-Hsing Huang, Wei-Jen Wu, Chung-Han Shieh
- 발행 연도: 2017년 4월
- 발행 학술지/학회: Applied Mechanics and Materials
- Keywords:
- 저압 다이캐스팅 (low pressure die-casting)
- A356 알루미늄 (A356 aluminum)
- Anycasting (Anycasting)
- 수축 결함 (shrinkage defect)
- 금형 유동 해석 (mold flow analyses)
2. 연구 배경:
- 연구 주제의 사회적/학문적 맥락:
- 자동차 산업은 경량, 고강도, 내충격성 차량 설계 개발에 박차를 가하고 있습니다.
- 저압 다이캐스팅은 휠 생산에 널리 사용됩니다.
- 다이캐스팅 중 발생하는 결함은 휠 프레임 변형 및 크리프 손상을 유발하여 교통 안전에 영향을 미칠 수 있습니다.
- 고품질 다이캐스팅 휠 프레임 제품 확보가 중요한 과제가 되었습니다.
- 기존 연구의 한계점:
- 기존 연구에서는 복잡한 형상과 고속 충전으로 인해 알루미늄 휠의 저압 다이캐스팅에서 발생하는 결함 문제를 인지하고 있었습니다.
- 이전 연구들은 수치 시뮬레이션을 사용하여 결함을 예측하고 매개변수를 최적화했지만, 결함을 효과적으로 제거하기 위한 추가적인 개선이 필요합니다.
- 연구의 필요성:
- A356 알루미늄 휠의 저압 다이캐스팅 공정에서 금형 유동, 온도장 및 응고 과정을 이해하기 위해.
- 최적화된 주조 매개변수와 유로 및 오버플로우 설계 설계를 통해 휠 제품에서 발생하는 결함을 줄이기 위해.
- 수축 공동 및 기공 결함을 제거하기 위해 결함 위치 및 분포를 예측하기 위해.
3. 연구 목적 및 연구 질문:
- 연구 목적:
- Anycasting 소프트웨어를 사용하여 A356 알루미늄 휠의 저압 다이캐스팅 공정을 설계하고 시뮬레이션합니다.
- 공정 매개변수 및 오버플로우 탱크 구성을 최적화하여 결함 형성을 예측하고 결함 감소 전략을 개선합니다.
- 핵심 연구 질문:
- Anycasting 소프트웨어 및 오버플로우 탱크 최적화를 통해 저압 다이캐스팅 공정의 컴퓨터 지원 설계 및 시뮬레이션이 A356 알루미늄 휠의 수축 및 기공 결함을 효과적으로 줄이는 방법은 무엇입니까?
- 연구 가설:
- 오버플로우 탱크를 설정하면 다이캐스팅의 수축 공동 및 기공 형성을 효과적으로 방지하고 다이캐스팅 휠 제품의 품질과 생산성을 크게 향상시킬 수 있습니다.
4. 연구 방법론:
- 연구 설계:
- 수치 시뮬레이션 기술을 사용한 시뮬레이션 기반 연구.
- 데이터 수집 방법:
- Anycasting 소프트웨어 패키지에서 생성된 시뮬레이션 데이터.
- 분석 방법:
- 유한 차분법 (FDM)을 사용하는 Anycasting 수치 시뮬레이션 분석.
- 결함 위치 및 분포를 예측하기 위한 잔류 용융 모듈러스 (RMM) 분석.
- 금형 유동, 온도장 및 응고 과정의 시뮬레이션.
- 공정 매개변수 및 오버플로우 탱크 구성 설계 분석.
- 연구 대상 및 범위:
- A356 알루미늄 휠의 저압 다이캐스팅 공정.
- 다양한 오버플로우 탱크 구성을 갖춘 리프트 휠, 휠 및 오버플로우 탱크에 대한 시뮬레이션 분석.
- 재료: 금형용 SKD61 다이강 및 휠 주조용 A356 알루미늄.
5. 주요 연구 결과:
- 핵심 연구 결과:
- 오버플로우 탱크를 설정하면 A356 알루미늄 다이캐스팅에서 수축 공동 및 기공 형성을 효과적으로 방지합니다.
- 오버플로우 탱크를 사용하면 다이캐스팅 휠 제품의 품질과 생산성이 크게 향상됩니다.
- Anycasting 소프트웨어를 사용한 수치 시뮬레이션은 저압 다이캐스팅에서 결함의 형성과 분포를 효과적으로 예측할 수 있습니다.
- 통계적/정성적 분석 결과:
- 잔류 용융 모듈러스 (RMM) 분석을 사용하여 결함 확률 분포를 예측했습니다.
- 시뮬레이션 결과 초기 접근 방식에서 오버플로우 탱크가 없을 때 결함이 주로 림 하단과 휠 중앙에 집중되어 있음을 보여주었습니다.
- 오버플로우 탱크를 추가하면 결함의 원인이 되는 독립적인 잔류 용융물을 효과적으로 배출할 수 있었습니다.
- 데이터 해석:
- 테이퍼 개방 리프트 튜브 (70° 테이퍼 각도, 706.5mm² 물 유입 단면적)를 사용한 초기 접근 방식은 독립적인 잔류 용융으로 인해 림 하단과 휠 중앙에 결함이 집중되었습니다.
- 오버플로우 탱크를 추가하면 독립적인 잔류 용융물의 배출이 용이해져 수축 및 기공이 휠 본체에서 멀리 떨어진 오버플로우 탱크로 이동했습니다.
- Figure Name List:
- Fig. 1: (a) 휠 및 리프트 튜브 조립체의 3D 모델 (b) 물리적 모델의 메쉬 생성 후 결과.
- Fig. 2: 저압 다이캐스팅 금형 충전 다이어그램.
- Fig. 3: (a) 외부 뷰 및 (b) 테이퍼 개방 리프트 튜브의 초기 접근 방식의 잔류 용융 모듈러스 분석을 통한 결함 확률 분포의 컷어웨이 뷰.
- Fig. 4: (a) 초기 접근 방식 (b) 오버플로우 탱크 추가를 통한 개선 접근 방식의 응고 순서 다이어그램.
- Fig. 5: (a) 외부 뷰, (b) 전면 뷰 및 (c) 오버플로우 탱크 추가를 통한 개선 접근 방식의 잔류 용융 모듈러스 분석을 통한 결함 확률 분포의 후면 뷰.

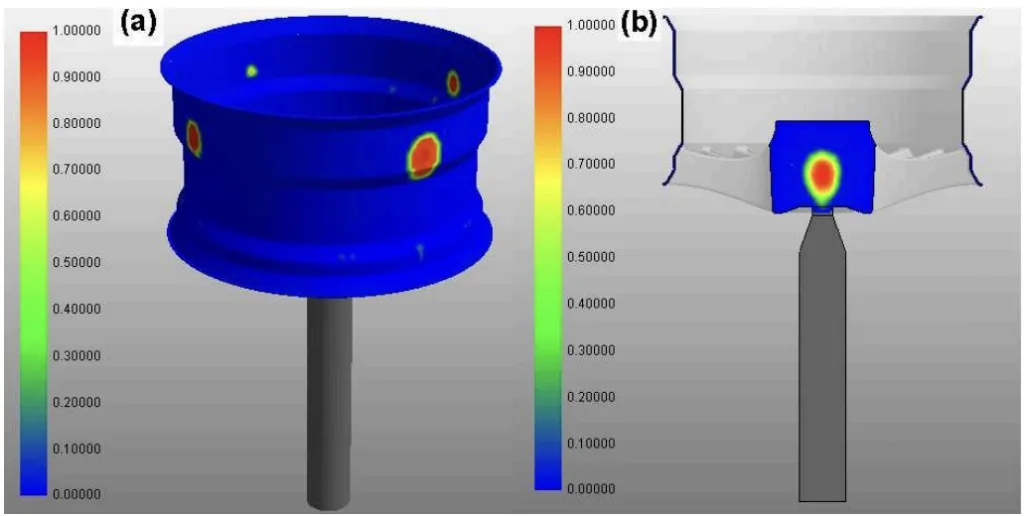


6. 결론 및 논의:
- 주요 결과 요약:
- 본 연구에서는 A356 알루미늄 휠의 저압 다이캐스팅 공정에 오버플로우 탱크를 추가하면 수축 및 기공 결함이 효과적으로 감소하는 것을 입증했습니다.
- Anycasting 소프트웨어 및 RMM 분석을 사용한 수치 시뮬레이션은 결함 형성 및 분포를 정확하게 예측했습니다.
- 오버플로우 탱크 설계는 가스 배출을 용이하게 하고 수축 및 기공이 오버플로우 탱크로 이동하도록 하여 휠 림 및 중앙의 결함을 제거했습니다.
- 연구의 학술적 의의:
- 본 연구는 컴퓨터 지원 설계 및 수치 시뮬레이션, 특히 Anycasting 소프트웨어 및 RMM 분석이 저압 다이캐스팅 공정 최적화에 유용함을 입증합니다.
- 독립적인 잔류 용융과 관련된 결함 형성 메커니즘과 이러한 결함을 완화하는 오버플로우 탱크의 효과에 대한 자세한 이해를 제공합니다.
- 본 연구는 경량 자동차 부품의 다이캐스팅 공정 최적화에 대한 지식 체계에 기여합니다.
- 실무적 시사점:
- 본 연구 결과는 다이캐스팅 엔지니어가 알루미늄 휠 제조의 품질과 생산성을 향상시키는 데 실질적인 지침을 제공합니다.
- 시뮬레이션 분석을 기반으로 한 오버플로우 탱크 설계를 구현하면 결함, 불량률 및 제조 비용을 크게 줄일 수 있습니다.
- 본 연구는 다이캐스팅 공정 설계 단계에서 금형 유동, 온도장 및 응고를 고려하는 것의 중요성을 강조합니다.
- 연구의 한계점:
- 논문에서는 연구의 한계점에 대해 명시적으로 논의하지 않습니다.
7. 향후 후속 연구:
- 후속 연구 방향:
- 향후 연구에서는 다양한 휠 형상 및 주조 매개변수에 대한 크기, 모양 및 배치 측면에서 오버플로우 탱크 설계 최적화를 탐구할 수 있습니다.
- 오버플로우 탱크 설계와 함께 다양한 공정 매개변수 (예: 주조 온도, 압력 프로파일, 냉각 속도)의 영향을 조사하는 것이 유익할 수 있습니다.
- 물리적 다이캐스팅 시험을 통한 시뮬레이션 결과의 실험적 검증은 연구 결과를 더욱 강화할 것입니다.
- 추가 탐구가 필요한 영역:
- 이 방법론을 다른 알루미늄 합금 및 다이캐스팅 공정에 적용하는 것을 탐구합니다.
- 더욱 정확한 결함 예측을 위해 고급 시뮬레이션 기술 및 재료 모델을 사용하는 것을 조사합니다.
- 오버플로우 탱크 설계가 다이캐스팅된 알루미늄 휠의 기계적 특성 및 피로 수명에 미치는 영향을 연구합니다.
8. 참고문헌:
- [1] P. H. Huang, S. C. Hung, C. J. Lin, Optimal pouring system design for investment casting of cladding thin-plate heater using metallic mold flow analyses, Appl. Mech. Mater. 627 (2014) 46-49 doi:10.4028/www.scientific.net/AMM.627.46
- [2] P. H. Huang, B. T. Wang, Y. T. Chen, An effective method for separating casting components from the runner system using vibration-induced fatigue damage, Int. J. Adv. Manuf. Technol. 74(9) (2014) 1275-1282 doi:10.1007/s00170-014-6077-z
- [3] J. L. Chen, Automotive aluminum wheels low pressure casting process overview, Theor. Urban Construct. 13 (2014).
- [4] Z. J. Wang, Y. Zhao, H. W. Song, X. D. Xu, R. J. You, Numerical Simulation of Low Pressure Casting Large Size Aluminum Alloy Wheel and its Process Optimization, Comput. Appl. Technol. 34(3) (2014) doi:1001-2249(2014)0.-0256-04
- [5] P. H. Huang, M. J. Guo, A study on the investment casting of 17-4PH stainless steel helical impeller of centrifugal pump, Mater. Res. Innov. 19(sup9) (2015) 77-81. doi:10.1179/1432891715Z.0000000001924
- [6] P. H. Huang, C. J. Lin, Computer-aided modeling and experimental verification of optimal gating system design for investment casting of precision rotor, Int. J. Adv. Manuf. Technol. 79(5) (2015) 997-1006.
- [7] J. K. Kuo, P. H. Huang, M. J. Guo, Removal of CrMo alloy steel components from investment casting gating system using vibration-excited fatigue failure, Int. J. Adv. Manuf. Technol. In press (2016) doi:10.1007/s00170-016-9079-1
- [8] G. F. Mi, X. Y. Liu, K. F. Wang, J. T. Niu, Numerical simulation of low pressure die-casting aluminum wheel, China Foundry, 48(1) (2009) 48-52.
- [9] X. F. Huang, Z. Y. Tian, K. Zhu, X. J. Cao, R. Xie, Study and Application of Die-Casting Aluminum Alloy and Die-Casting Technology, Cast. Forg. Weld. 37(17) (2008) doi:1001-3814(2008)17-0137-05
- [10] Y. J. Zhang, Study of Performance of Automobile Wheel of A356 AL-alloy by Low Pressure Casting, Foundry Technol. 35(2) (2014).
9. Copyright:
- 본 자료는 Pei-Hsing Huang의 논문: Compute-Aided Design of Low Pressure Die-Casting Process of A356 Aluminum Wheels을 기반으로 작성되었습니다.
- 논문 출처: doi:10.4028/www.scientific.net/AMM.864.173
본 자료는 위 논문을 바탕으로 요약 작성되었으며, 상업적 목적으로 무단 사용이 금지됩니다.
Copyright © 2025 CASTMAN. All rights reserved.