본 논문 요약은 ['POLITECNICO DI TORINO']에서 발행한 ['LIGHTWEIGHT DESIGN OF VEHICLE SIDE DOOR'] 논문을 기반으로 작성되었습니다.
1. 개요:
- 제목: LIGHTWEIGHT DESIGN OF VEHICLE SIDE DOOR (차량 측면 도어 경량 설계)
- 저자: JINDONG JI
- 발행 연도: 2015년 2월
- 발행 학술지/학회: POLITECNICO DI TORINO, DOCTORATE SCHOOL, Ph.D in Mechanics (박사 학위 논문)
- 키워드: Vehicle side door (차량 측면 도어), Lightweight design (경량 설계), Composite material (복합 재료), Crashworthiness (충돌 안전성), Finite element analysis (유한 요소 해석), NVH, Static analysis (정적 해석)
![Figure 1.1-1 Passenger cars registrations by member state [1]](https://castman.co.kr/wp-content/uploads/image-741-png.webp)
2. 초록 또는 서론
본 논문은 Green House Gas (GHG) 배출에 대한 환경적 우려 증가와 차량 안전에 대한 정부 규제 강화로 인해 자동차 산업이 더 가볍고 안전한 차량을 만들기 위한 새로운 기술을 채택해야 할 필요성을 다룹니다. 경량 설계는 연비 향상과 차량 배출 감소를 위한 효과적인 전략으로 제시됩니다. 본 연구는 전통적으로 강철로 제작되는 복잡한 시스템인 차량 측면 도어 하부 구조에 초점을 맞추고 안전 및 성능 저하 없이 중량 감소를 달성하기 위한 복합 재료의 잠재력을 탐구합니다. 본 연구에서는 Toyota Yaris 2010 모델을 위한 여러 복합 측면 도어 구조를 개발 및 평가하고 정적 설계 요구 사항, NVH 설계 기준 및 충돌 안전성을 고려합니다. ABAQUS 및 LS-DYNA 수치 시뮬레이션 도구를 사용하여 복합 재료 설계의 성능을 기준 솔루션 역할을 하는 원래 강철 도어 구조와 비교 평가합니다. 본 논문은 복합 재료 특성 분석, 유한 요소 모델 시뮬레이션, 정적 및 모달 해석, 충돌 안전성 평가를 포괄적으로 다루어 복합 재료를 사용한 차량 측면 도어의 경량 설계에 대한 종합적인 연구를 제공합니다.
3. 연구 배경:
연구 주제 배경:
GHG 배출에 대한 환경적 우려 증가와 차량 안전에 대한 정부 규제 강화는 자동차 제조업체가 새로운 기술을 모색하도록 압력을 가하고 있습니다. 경량 설계는 연비 향상과 차량 배출 감소를 위해 점점 더 중요해지고 있습니다. 그러나 차량 중량 감소 기술은 고객의 편안함과 차량 안전을 저해해서는 안 됩니다.
기존 연구 현황:
자동차 연구 및 설계 부서는 고강도 강철, 알루미늄, 마그네슘 및 복합재와 같은 첨단 재료를 적극적으로 탐색하여 기존 재료를 대체하고 있습니다. 복합재는 더 높은 강도, 더 낮은 무게, 더 나은 내식성과 같은 장점을 제공합니다. 그러나 생산 비용, 생산량, 설계 방법론, 접합 기술 및 재활용 문제 등 복합재의 광범위한 채택에는 여전히 어려움이 남아 있습니다. 차량 안전은 자동차에 경량 재료를 적용할 때 여전히 중요한 고려 사항입니다.
연구의 필요성:
본 연구는 안전 기준을 유지하면서 경량 차량 설계의 과제를 해결해야 할 필요성에 의해 동기가 부여되었습니다. 차량 측면 도어 하부 구조는 구조적 복잡성과 기능적 중요성으로 인해 연구 대상으로 선정되었습니다. 기존의 강철 도어 구조는 무겁고, 이 부품에 대한 복합재 대안을 탐색하는 것은 전체 차량 중량 감소와 성능 향상을 달성하는 데 필수적입니다.
4. 연구 목적 및 연구 질문:
연구 목적:
주요 연구 목적은 차량용 복합 측면 도어 구조를 개발 및 평가하여 경량 설계를 달성하면서 정적, NVH 및 충돌 안전성 요구 사항을 충족하는 것입니다. 본 논문은 기존 강철을 대체하여 차량 측면 도어 설계에 복합 재료를 사용하는 것의 타당성과 이점을 입증하고자 합니다.
핵심 연구:
핵심 연구는 다음 사항에 중점을 둡니다.
- Toyota Yaris 2010 모델용 복합 측면 도어 구조 여러 개 개발.
- ABAQUS 및 LS-DYNA 수치 해석 도구를 사용하여 이러한 복합 구조의 성능 시뮬레이션 및 분석.
- 정적 거동, NVH 특성 및 충돌 안전성 측면에서 복합 도어 솔루션의 성능을 원래 Yaris 강철 도어 구조와 비교.
- 차량 측면 도어용 혁신적인 복합 보강 패널 설계 연구.
연구 가설:
본 연구에서는 복합 측면 도어 구조가 기존 강철 도어에 비해 상당한 중량 감소를 달성하면서 강성, NVH 및 충돌 안전성 측면에서 구조적 성능을 유지하거나 향상시킬 수 있다고 가정합니다. 또한 혁신적인 복합 보강 패널 설계가 기존 강철 충격 빔 및 보강재를 효과적으로 대체하여 복합 측면 도어의 전체적인 성능을 향상시킬 수 있다고 가정합니다.
5. 연구 방법론
연구 설계:
본 연구에서는 복합 측면 도어 구조를 설계하고 평가하기 위해 수치 시뮬레이션 기반 접근 방식을 사용합니다. 기존 강철 및 복합 도어 설계의 유한 요소(FE) 모델을 개발하고 다양한 하중 조건에서 분석합니다.
자료 수집 방법:
자료는 ABAQUS 및 LS-DYNA 소프트웨어를 사용한 수치 시뮬레이션을 통해 수집됩니다. 강철 및 다양한 복합 재료(CFRP, GFRP, GMT, GMT-UD, GMT-TEX, SIMS)의 재료 속성이 FE 모델의 입력 매개변수로 사용됩니다. 시뮬레이션 결과에는 응력 분포, 변위, 침입 측정 및 충돌 시뮬레이션에서 더미의 생체 역학적 반응이 포함됩니다.
분석 방법:
- 정적 해석: 수직, 수평, 측면 강성 및 처짐 하중 사례에서 복합 도어 설계의 구조적 강성 및 강도를 평가하기 위해 선형 및 비선형 정적 해석을 수행합니다. NVH 특성을 평가하기 위해 모달 해석을 수행합니다.
- 동적 해석: 충돌 안전성 평가를 위해 명시적 동적 해석을 사용하여 FMVSS214 규정에 따른 측면 충돌 시나리오를 시뮬레이션합니다. Head Injury Criteria (HIC), 늑골 편향, 복부 힘 및 치골 결합력을 포함한 생체 역학적 반응을 분석하여 탑승자 안전을 평가합니다.
- 비교 분석: 복합 도어 솔루션의 성능을 정적, NVH 및 충돌 안전성 기준에 대한 시뮬레이션 결과를 기반으로 원래 Yaris 강철 도어 구조(기준 솔루션)와 비교합니다.
연구 대상 및 범위:
연구 대상은 차량 측면 도어 구조이며, 특히 Toyota Yaris 2010 모델을 대상으로 합니다. 범위는 다음을 포함합니다.
- CFRP, GFRP, GMT, GMT-UD, GMT-TEX 및 SIMS 재료를 사용한 복합 측면 도어 구조의 설계 및 분석.
- 정적, 모달 및 충돌 안전성 성능의 수치 시뮬레이션.
- 측면 충돌 시나리오에서 침입 변위 및 생체 역학적 반응 평가.
- 기준 강철 도어 구조와의 비교.
6. 주요 연구 결과:
핵심 연구 결과:
- 정적 및 모달 해석: 복합 도어 구조, 특히 복합 프레임이 있는 구조는 수직 및 수평 하중 사례에서 강철 기준 도어와 비슷하거나 약간 더 높은 강성을 나타냈습니다. 모달 해석 결과 복합 도어 구조가 더 높은 고유 진동수를 나타내 NVH 성능이 향상되었음을 보여주었습니다.
- 충돌 안전성 평가: 복합 도어 솔루션은 측면 충돌 시뮬레이션에서 강철 도어에 비해 침입 변위가 감소했습니다. 에너지 흡수 용량은 복합 도어에서 훨씬 높았습니다(약 20% 증가). 늑골 편향, 복부 힘 및 치골 결합력을 포함한 생체 역학적 반응은 복합 도어 설계에 대한 FMVSS214 규제 제한 내에 있어 탑승자 보호가 만족스러운 수준임을 나타냅니다.
- 혁신적인 복합 패널: 혁신적인 복합 보강 패널 설계가 개발 및 평가되었으며, 기존 강철 충격 빔 및 보강재를 대체하여 충돌 안전성을 유지하면서 중량을 더욱 줄일 수 있는 잠재력을 보여주었습니다.
- 중량 감소: 복합재로 재료를 대체한 결과 상당한 중량 감소가 있었으며, 강철 도어에 비해 최종 중량 감소율은 다양한 복합 솔루션에 대해 32%에서 38% 사이였습니다.
제시된 데이터 분석:
논문 전체, 특히 6장과 7장에 제시된 그림과 표의 데이터는 주요 연구 결과를 뒷받침합니다. 그림 6.1-4, 6.1-8 및 6.1-11은 정적 하중 하에서 변위 분포를 보여주며 복합 도어의 변위 감소를 나타냅니다. 표 6.1-1, 6.1-3 및 6.1-5는 응력과 변위를 정량화하여 비슷하거나 향상된 정적 성능을 확인합니다. 그림 7.1-3은 충돌 시뮬레이션에서 침입 변위 이력을 보여주며 복합 도어의 침입 감소를 나타냅니다. 그림 7.2-5, 7.2-8, 7.2-9 및 7.2-10은 생체 역학적 반응을 제시하여 복합 도어가 안전 규제 제한을 충족함을 보여줍니다. 표 7.3-1은 중량 감소 데이터를 요약하여 복합 솔루션의 경량화 잠재력을 강조합니다.
그림 목록:
![Figure 1.1-2 Passenger cars registrations by vehicle brand [1]](https://castman.co.kr/wp-content/uploads/image-742-png.webp)
![Figure 1.2-1 Average fuel consumption in the EU by vehicle manufacture [1]](https://castman.co.kr/wp-content/uploads/image-743-png.webp)
![Figure 1.2-2 Passenger cars 𝑪𝑶𝟐 emissions by member state [1]](https://castman.co.kr/wp-content/uploads/image-744-png.webp)
![Figure 1.2-3 Passenger cars 𝑪𝑶𝟐 emissions by vehicle segment [1]](https://castman.co.kr/wp-content/uploads/image-745-1024x368.webp)
![Figure 2.1-1 Representative vehicle energy flows in an urban driving cycle [1]](https://castman.co.kr/wp-content/uploads/image-746-1024x414.webp)
![Figure 2.1-2 Energy flow within an automotive vehicle [2]](https://castman.co.kr/wp-content/uploads/image-747-png.webp)
![Figure 2.1-3 Future propulsion system pathways [1]](https://castman.co.kr/wp-content/uploads/image-748-png.webp)
![Figure 2.2-2 Different segment vehicle mass change [6]](https://castman.co.kr/wp-content/uploads/image-749-png.webp)
![Figure 2.2-4 Vehicle weight composition by mass ratio [8]](https://castman.co.kr/wp-content/uploads/image-750-png.webp)
![Figure 2.2-5 1975 and 2007 average vehicle mass breakdown by material [9]](https://castman.co.kr/wp-content/uploads/image-751-1024x427.webp)
![Figure 2.2-11 Vehicle material compositions by percent mass [15]](https://castman.co.kr/wp-content/uploads/image-752-png.webp)
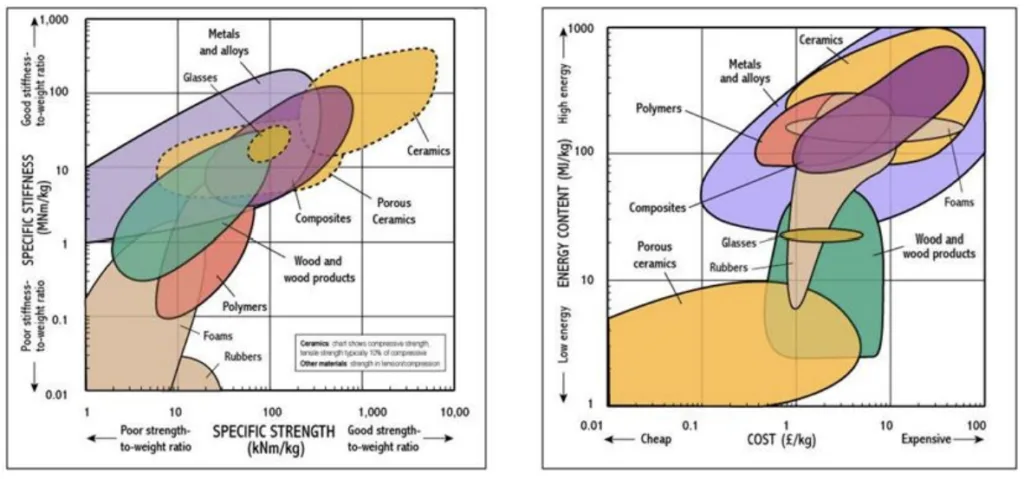
![Figure 2.2-15 Configure of BMW i3 [19]](https://castman.co.kr/wp-content/uploads/image-754-1024x281.webp)
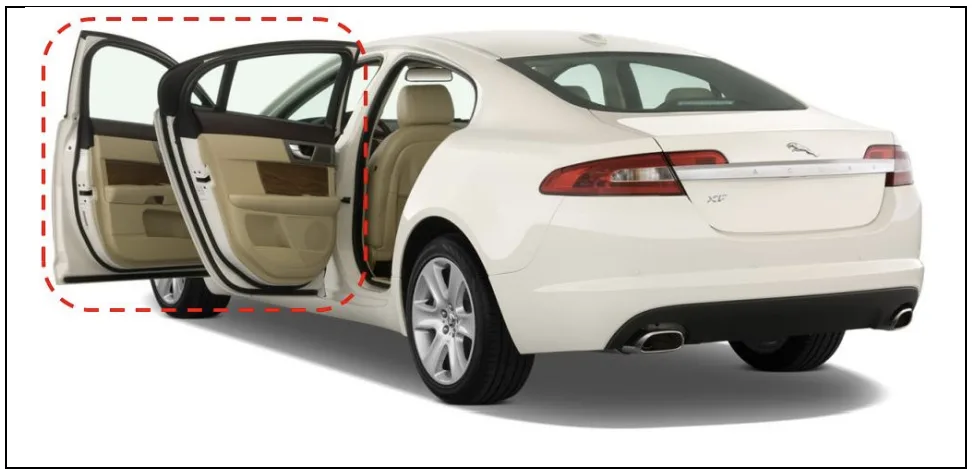
![Figure 3.1-4 Side door components of Toyota Yaris 2010 model [3]](https://castman.co.kr/wp-content/uploads/image-756-png.webp)
![Figure 3.2-2 Active safety and passive safety in automotive engineering [12]](https://castman.co.kr/wp-content/uploads/image-757-1024x667.webp)
![Figure 3.2-3 Different zones in vehicle crash impact [13]](https://castman.co.kr/wp-content/uploads/image-758-png.webp)
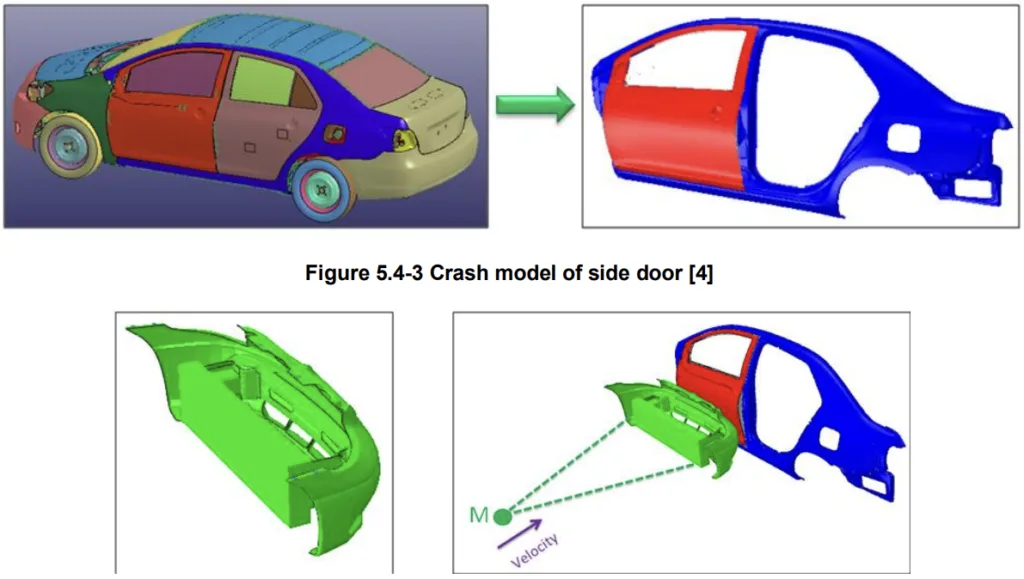
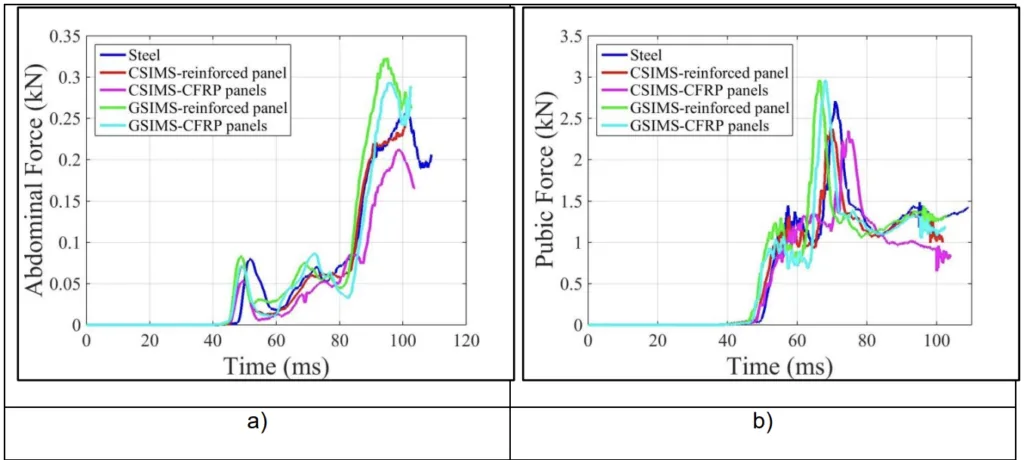
- 그림 1.1-1 회원국별 승용차 등록 [1]
- 그림 1.1-2 차량 브랜드별 승용차 등록 [1]
- 그림 1.2-1 EU의 차량 제조업체별 평균 연료 소비량 [1]
- 그림 1.2-2 회원국별 승용차 CO2 배출량 [1]
- 그림 2.1-1 도시 주행 사이클에서 대표적인 차량 에너지 흐름 [1]
- 그림 2.1-2 자동차 차량 내 에너지 흐름 [2]
- 그림 2.1-3 미래 추진 시스템 경로 [1]
- 그림 2.1-4 미국 모델 연도 2005의 연석 중량 및 연료 소비량 [1]
- 그림 2.2-1 총 차량 중량 추세 [5]
- 그림 2.2-2 다른 세그먼트 차량 질량 변화 [6]
- 그림 2.2-3 EU 회원국별 차량 중량 변화 [7]
- 그림 2.2-4 질량비에 따른 차량 중량 구성 [8]
- 그림 2.2-5 1975년 및 2007년 평균 차량 질량 재료별 분류 [9]
- 그림 2.2-6 승용차의 다른 부품의 인장 강도 요구 사항 및 HSS 적용 범위 [10]
- 그림 2.2-7 서유럽에서 자동차당 평균 알루미늄 사용량 [11]
- 그림 2.2-8 유럽 자동차의 상대적 및 절대적 알루미늄 사용량 [11]
- 그림 2.2-9 알루미늄 집약적 차량
- 그림 2.2-10 다양한 분야의 복합재 응용 분야
- 그림 2.2-11 질량 백분율별 차량 재료 구성 [15]
- 그림 2.2-12 재료의 기계적 성능 비교를 위한 Ashby 맵
- 그림 2.2-13 재료의 강도 및 비용 비교를 위한 Ashby 맵
- 그림 2.2-14 탄소 섬유로 보강된 차량
- 그림 2.2-15 BMW i3 구성 [19]
- 그림 3.1-1 기존 자동차 측면 도어
- 그림 3.1-2 다양한 유형의 차량 측면 도어 [1]
- 그림 3.1-3 세 가지 다른 도어 아키텍처 [2]
- 그림 3.1-4 Toyota Yaris 2010 모델의 측면 도어 부품 [3]
- 그림 3.1-5 2010년 실제 Toyota Yaris 승용차 및 FE 모델
- 그림 3.2-1 EU의 사고, 사망자 및 부상자 발생 추이 [11]
- 그림 3.2-2 자동차 공학의 능동 안전 및 수동 안전 [12]
- 그림 3.2-3 차량 충돌 영향의 다른 영역 [13]
- 그림 3.2-4 차량 충돌 기준
- 그림 3.3-1 규정 FMVSS 214. [14]
- 그림 3.3-2 이동식 변형 가능 장벽(MM)의 치수 [14].
- 그림 3.3-3 측면 충돌 테스트에 사용된 더미 제품군 및 다양한 더미
- 그림 3.3-4 FMVSS 표준의 등급 시스템
- 그림 4.1-1 매트릭스 재료를 기반으로 한 복합재 분류 [1]
- 그림 4.1-2 구조적 속성을 기반으로 한 복합재 분류 [2]
- 그림 4.1-3 매트릭스 재료 요약 [2]
- 그림 4.1-4 직조 유형: 평직, 능직 및 새틴 직조 [11]
- 그림 4.2-1 충돌 후 차량 변형
- 그림 4.2-2 a) GMT 구조, b) GMT-UD 구조, c) GMT-TEX 구조
- 그림 4.2-3 a) CSIMS 스태킹, b) GSIMS 스태킹
- 그림 4.2-4 Yaris 도어 외부 패널, 내부 패널 및 충격 빔 재료의 속성. [16]
- 그림 5.3-1 Yaris 도어의 단순화된 FE 모델 [4]
- 그림 5.3-2 기존 도어 모델을 얻기 위한 추출 프로세스 [4]
- 그림 5.3-3 복합 빔
- 그림 5.3-4 평면 및 곡선 모델의 복합 빔 분포
- 그림 5.3-5 복합 도어 모델의 조인트 모양 및 위치
- 그림 5.3-6 측면 전방 도어의 세 가지 FE 모델
- 그림 5.4-1 Yaris 측면 도어 모델 [4]
- 그림 5.4-2 고려된 부품: 외부 패널, 내부 패널 및 충격 빔
- 그림 5.4-3 측면 도어의 충돌 모델 [4]
- 그림 5.4-4 측면 충돌 시뮬레이션: 변형 가능 범퍼 및 측면 도어 구조
- 그림 5.5-1 시뮬레이션 모델, a) 규정 FMVSS 214, b) Yaris 모델, c) 이동식 변형 가능 장벽(MDB), d) EURO-SID 2 더미
- 그림 5.6-1 a) 단순화된 전체 알루미늄 보강재(STAR) 패널을 포함한 개략적인 알루미늄 도어 구조; b) 내부, 외부 및 STAR 패널을 보여주는 수직 도어 섹션; c) STAR 패널 주름 형상. [9]
- 그림 5.6-2 a) Yaris STAR 패널; b) Yaris의 원래 도어 모델; c) Yaris의 혁신적인 도어 모델
- 그림 5.6-3 a) 교체할 수 있는 부품; b) 복합재로 만든 혁신적인 부품; c) 4개의 연결 영역
- 그림 5.7-1 ABAQUS의 복합 재료 모델
- 그림 5.7-2 LS-DYNA의 복합 재료 모델
- 그림 6.1-1 차량 측면 도어의 세 가지 FE 모드
- 그림 6.1-2 - 수직 하중 사례 및 복합 모델의 힌지 위치에 적용된 힘.
- 그림 6.1-3 하중 사례 1에 대한 세 가지 모델의 Von Mises 응력 분포.
- 그림 6.1-4 하중 사례 1에 대한 수직 변위 분포.
- 그림 6.1-5 하중 사례 1에 대한 수직 변위 및 반력.
- 그림 6.1-6 – 수평 하중 사례.
- 그림 6.1-7 - 수평 하중 하에서 세 가지 모델의 Von Mises 응력.
- 그림 6.1-8 - 수평 하중에 대한 세 가지 모델의 수평 변위.
- 그림 6.1-9- 하중 사례 2에 대한 수평 변위 및 반력.
- 그림 6.1-10- 준정적 침입 시뮬레이션 모델
- 그림 6.1-11- 하중 사례 3에 대한 세 가지 모델의 압출 방향 변위.
- 그림 6.1-12- 준정적 침입 시뮬레이션의 변위 및 반력.
- 그림 6.2-1 Yaris의 측면 도어 구조 모델
- 그림 6.2-2 동일 강성 기준
- 그림 6.2-3 측면 강성 및 처짐 하중 사례.
- 그림 6.2-4 다양한 하중 사례에 대한 하중-변위 다이어그램
- 그림 6.2-5 처짐 사례에서 세 가지 모델에 대한 하중-변위 다이어그램
- 그림 6.3-1 1차 및 2차 모드에 대한 모달 형상.
- 그림 6.3-2 주파수 변화 이론
- 그림 7.1-1 Yaris 측면 도어 구조 모델.
- 그림 7.1-2 충돌 안전성 평가를 위한 충돌 모델.
- 그림 7.1-3 세 가지 모델의 침입 변위 이력
- 그림 7.1-4 세 가지 모델의 반력 이력
- 그림 7.1-5 측면 도어 구조에 의해 흡수된 에너지
- 그림 7.1-6 CFRP_Panel&Beam 모델의 운동 에너지 및 내부 에너지.
- 그림 7.2-1 측면 충돌 모델: a) Toyota Yaris 2010, b) 이동식 변형 가능 장벽, c) 측면 충돌 규정 FMVSS214, d) ES-2 더미.
- 그림 7.2-2 Yaris 도어에서 고려된 부품: a) 외부 패널, b) 내부 패널, c) 보강 충격 빔.
- 그림 7.2-3 측면 충돌 영향 중 더미의 움직임
- 그림 7.2-4 내부 패널의 침입 변위 조사를 위한 9개의 중요 지점.
- 그림 7.2-5 측면 도어 내부 패널의 9개 중요 지점의 침입 변위
- 그림 7.2-6 반력 및 머리 가속도
- 그림 7.2-7 a) 루프 레일과의 더미 머리 충격, b) 루프 레일 주변의 폼, c) 측면 에어백.
- 그림 7.2-8 늑골 편향, a) 상부 늑골, b) 중간 늑골, c) 하부 늑골.
- 그림 7.2-9 복부 힘.
- 그림 7.2-10 치골 결합력.
- 그림 7.3-1 외부 패널, 보강 패널 및 내부 패널.
- 그림 7.3-2 탑승자 칸의 침입 변위
- 그림 7.3-3 늑골 편향
- 그림 7.3-4 복부 합력
- 그림 7.3-5 치골 결합력
- 그림 7.3-6 침입 변위
- 그림 7.3-7 늑골 편향 a) 상부 늑골, b) 중간 늑골, c) 하부 늑골
- 그림 7.3-8 a) 복부 힘, b) 치골 결합력
- 그림 7.3-9 침입 변위
- 그림 7.3-10 늑골 편향 a) 상부 늑골, b) 중간 늑골, c) 하부 늑골
- 그림 7.3-11 a) 복부 힘, b) 치골 결합력
- 그림 7.3-12 침입 변위
- 그림 7.3-13 늑골 편향 a) 상부 늑골, b) 중간 늑골, c) 하부 늑골
- 그림 7.3-14 a) 복부 힘, b) 치골 결합력
7. 결론:
주요 결과 요약:
본 연구는 복합 재료가 차량 측면 도어 구조에 강철을 대체할 수 있는 실행 가능한 대안을 제공하여 상당한 경량화를 달성하고 구조적 및 안전 성능을 유지하거나 향상시킨다는 결론을 내립니다. 복합 도어 솔루션은 비슷한 수준의 정적 강성, 향상된 NVH 특성 및 침입 감소 및 에너지 흡수 측면에서 우수한 충돌 안전성을 입증했습니다. 충돌 시뮬레이션의 생체 역학적 반응은 FMVSS214 규제 제한 내에 있어 적절한 탑승자 보호를 나타냅니다. 혁신적인 복합 보강 패널 설계는 경량화 잠재력을 더욱 향상시킵니다.
연구의 학문적 의의:
본 연구는 차량 측면 도어 설계에 복합 재료를 적용하는 것에 대한 포괄적인 연구를 제공함으로써 학문 분야에 기여합니다. 복합 구조의 정적, NVH 및 충돌 안전성 성능을 평가하기 위한 상세한 수치 시뮬레이션 방법론을 제공합니다. 또한 본 연구는 자동차 구조 응용 분야에서 복합 재료 거동에 대한 이해를 넓히고 경량 차량 설계 및 안전에 대한 향후 연구를 위한 귀중한 데이터를 제공합니다.
실용적 의미:
본 연구 결과는 자동차 산업에 중요한 실용적 의미를 갖습니다. 경량 복합 측면 도어의 실현 가능성을 입증함으로써 차량 중량 감소, 연비 향상 및 배출 감소를 위한 경로를 제공하여 전 세계 환경 규제 및 소비자 요구에 부합합니다. 본 연구는 자동차 엔지니어가 차량 생산에 복합 측면 도어 구조를 개발하고 구현하는 데 활용할 수 있는 설계 지침과 검증된 수치 모델을 제공합니다.
연구의 한계 및 향후 연구 분야:
본 연구에서는 측면 에어백과 충돌 시뮬레이션에서 폼 및 안전 벨트 시스템에 대한 상세한 모델링을 제외한 점을 포함하여 머리 가속도 결과에 영향을 미칠 수 있는 한계를 인정합니다. 향후 연구 분야는 다음과 같습니다.
- 프로토타입 복합 측면 도어의 물리적 테스트를 통한 수치 시뮬레이션 결과의 실험적 검증.
- 향상된 성능과 비용 효율성을 위한 복합 재료 선택 및 레이업 구성 최적화.
- 복합재-알루미늄 하이브리드 도어 구조의 접합 기술 연구.
- 보다 정확한 충돌 안전성 예측을 위해 상세 에어백 및 구속 시스템을 통합하도록 FE 모델을 추가로 개선.
- 복합 측면 도어의 대량 생산을 위한 제조 공정 및 확장성 탐색.
8. 참고 문헌:
- [1]. The International Council on Clean Transportation, ―European Vehicle Market Statics, Pocketbook 2013‖.
- [2]. The Organization for Economic Co-operation and Development (OECD), ―Strategies to Reduce Greenhouse Gas Emissions from Road Transport: Analytical Methods‖, 2002.
- [3]. European Environment Agency, ―Monitoring CO2 emissions from new passenger cars in the EU: summary of data for 2012‖.
- [4]. David C., Sean B., Emily W. and Martin W., ―Trends in NOx and NO2 emissions and ambient measurements in the UK‖, 2011.
- [5]. TNO Science and Industry, ―Review and analysis of the reduction potential and cost of technological and other measures to reduce CO2-emisssions from passenger cars‖, 2006.
- [6]. www.autosteel.org.
- [7]. Nicholas L., ―Review of technical literature and trends related to automobile mass-reduction technology‖, report for California Air Resources Board, May 2010.
- [8]. The International Council on Clean Transportation, ―European Vehicle Market Statics, Pocketbook 2013‖.
- [9]. Stodolsky F., A. Vyas, et al. (1995), ―Life-Cycle Energy Savings Potential from Aluminum-Intensive Vehicles‖, Conference Paper, 1995 Total Life Cycle Conference&Exposition. October 16-19, 1995, Vienna, Austria.
- [10]. Abraham, A. Ducker Worldwide. (2011, May). ―Future Growth of AHSS [PowerPoint presentation at Great Designs in Steel Seminar]‖.
- [11]. J. Galan, L. Samek, P. Verleysen, K. Verbeken and Y.Houbaert, ―Advanced high strength steels for automotive industry‖, Revista de Metalurgia, 48 (2), ISSN: 0034-8570.
- [12]. J.Hirsch, ―Automotive Trends in Aluminum- The European Perspective‖, Materials Forum Volume 28, 2004.
- [13]. Ducker Worldwide, ―The Past, Present and Future of Aluminum in North American Light Vehicles‖, October 16, 2012.
- [14]. McWilliams A., ―Advanced Materials, Lightweight Materials in Transportation‖, report, Report Code: AVM056A, 2007.
- [15]. Ghassemieh E., ―Materials in Automotive Application, State of the Art and Prospects, New Trends and Developments in Automotive Industry‖, InTech, Marcello Chiaberge, ISBN: 978-953-307-999-8, 2011.
- [16]. http://wardsauto.com/subscriptions/facts-figures.
- [17]. Taub A., Krajewski P., Luo A. and Owens J., ―The Evolution of Technology for Materials Processing over the Last 50 Years: The Automotive Example ‖, JOM, February.
- [18]. Marc R., Deena P. and Tom W., ―Vehicle Design and the Physics of Traffic Safety‖, Physics Today, January 2006.
- [19]. http://www.bmw.com/
- [20]. http://www.euroncap.com/tests/fiat_500_2007/298.aspx.
- [21]. European Aluminum Association, ―The Aluminum Automotive MANUAL-Hang on parts‖, 2013.
- [22]. Daniel E.Whitney, MIT Engineering System Division and Cambridge MA, ―Design and Manufacturing of Car Doors: Report on Visits Made to US, European and Japanese Car Manufacturers in 2007‖, March 2008.
- [23]. National Crash Analysis Center, http://www.ncac.gwu.edu/
- [24]. World Health Organization, ―Global Status Report on Road Safety‖, 2013.
- [25]. Volvo Trucks, ―European Accident Research and Safety Report 2013‖.
- [26]. National Highway Traffic Safety Administration, ―An Analysis of Recent Improvements to Vehicle Safety‖, DOT HS 811 572, June 2012.
- [27]. EVALUE Project, ―Testing and evaluation methods for active vehicle safety‖, http://www.evalue-project.eu/.
- [28]. Final report of ELVA Project, ―Societal scenarios and available technologies for electric vehicle architectures in 2020‖, Grant Agreement Number 265898.
- [29]. Nat’l Highway Traffic Safety Admin., DOT §571.214, Dec. 13, 1979.
- [30]. Juan M. A. G, PhD thesis, ―A study to improve the crash compatibility between cars in side impact‖, Marzo 2008.
- [31]. Samaha RR, Elliott DS, ―NHTSA side impact research: motivation for upgraded test procedures‖, 18th International Technical Conference on the Enhanced Safety of Vehicles, Nagoya, Japan, 2003.
- [32]. Kathleen D. K., Carol A. C. F., Kristen N., Lawrence W. S. and Jonathan D. R., ―Abdominal injury in motor-vehicle crashes‖, UMTRI-2008-40, Nov. 2008.
- [33]. Peter S., Uli F., Sebastian S., Markus P., Arno E., DYNAmore GmbH, MAGNA STEYR, ―Comparison of ES-2re with ES-2 and USSID Dummy‖ , DYNAmore GmbH, 2014.
- [34]. Aimar A., Molina G. and Volpenge M., ―The magnesium door project‖, proc. of Int. Conf. Florence ATA 2003, Florence (1), paper 03A1039.
- [35]. Seong S. C, Dai G. L and Kwang S. J., ―Composite side-door impact beams for passenger cars.‖ Composite Structures Vol. 38, No. 1-4, 1997, pp. 229-239.
- [36]. Patberg L., Philipps M. and Dittmann R., ―Fiber-reinforced composites in the car side structure‖, Proc Instn Mech Engrs, 1999, Vol.213 part D, pp. 417-423.
- [37]. Belingardi G., ―Recent advances in joining technology for car body applications‖, proc. Int. Conf. MVM 2006 (Motor Vehicle and Motors), Kragujevac (Serbia), 4-6 October 2006.
- [38]. Banea M. D. and Da Silva L. F., ―Adhesively bonded joints in composite materials: an overview‖, Proc Instn Mech Engrs, 2009, Vol.223 part L, pp.1-18.
- [39]. http://www.slideshare.net/BKLR/polymer-matrix-composites.
- [40]. Giovanni B. , presentation of course ―Progettazione di strutture meccaniche in materiale composito‖, Politecnico di Torino, 2014.
- [41]. Frederick T. W., James C. W. and Hong Li, PPG Industries, Inc, ―Glass Fibers‖, ASM Handbook, Vol. 21: Composites (#06781G), 2001.
- [42]. Paul J. W., Zoltek Corporation, ―Carbon Fibers‖, ASM Handbook, Vol.21: Composites, 2001.
- [43]. http://www.angelfire.com/ma/ameyavaidya/b_fiber.htm#boron
- [44]. Reashad B. K. and Nasrin F., ―Kevlar-The Super Tough Fiber‖, International Journal of Textile Science 2012, pp78-83.
- [45]. David Roylance, ―Introduction to composite materials‖, March 24, 2000.
- [46]. Curt A., ―NM EPOXY HANDBOOK‖, third edition,2004.
- [47]. http://www.netcomposites.com/guide/polyester-resins/8
- [48]. Ermias G. Korico., ―Implementation of Composites and Plastics Materials for Vehicle Lightweight‖, PhD thesis,2012.
- [49]. MIL-HDBK-17-5, ―Composite Materials Handbook‖, 17 June, 2002.
- [50]. http://composite.about.com/library/data/blc-cfs003ltm25-rtd.htm
- [51]. Giovanni B. and Brunetto M., ―Recent research results in composite materials and adhesive applications for vehicle lightweight‖, Int. Cong. Motor Vechiles&Motors 2014,October 9th-10th.
- [52]. Patent US2002/0064640A1, ―Thin composite laminate and use thereof in making sports articles, especially boots‖.
- [53]. P. Nieri, I. Montanari, A. Terenzi, L. Torre and J. M. Kenny, ―A novel composite configuration for low-cost panels with improved toughness‖, 29th International Conference and Forum- SECO 08, March 31st–April 2nd.
- [54]. http://www.ncac.gwu.edu/
- [55]. Giovanni B., Alem T. Beyene and Ermias G. Korico., ―Geometrical optimization of bumper beam profile made of pultruded composite by numerical simulation‖, Composite Structures, 2013.
9. 저작권:
- 본 자료는 "JINDONG JI"의 논문: "LIGHTWEIGHT DESIGN OF VEHICLE SIDE DOOR"을 기반으로 합니다.
- 논문 출처: [DOI URL]
본 자료는 상기 논문을 요약한 것으로, 상업적 목적으로 무단 사용하는 것을 금지합니다.
Copyright © 2025 CASTMAN. All rights reserved.