본 논문 요약은 "[Causes of Casting Defects with Remedies]" 논문을 기반으로 작성되었으며, "[International Journal of Engineering Research & Technology]"에서 발표되었습니다.
1. 개요:
- 제목: 주조 결함의 원인과 해결책 (Causes of Casting Defects with Remedies)
- 저자: Rahul T Patil, Veena S Metri, Shubhangi S Tambore
- 발행 연도: 2015년 11월
- 발행 저널/학회: International Journal of Engineering Research & Technology (IJERT), Vol. 4 Issue 11
- 키워드: 다이 캐스팅 (Die Casting); 주조 결함 (Defects in Casting); 주조 결함의 원인 및 해결책 (Causes and Remedies for Casting Defects)
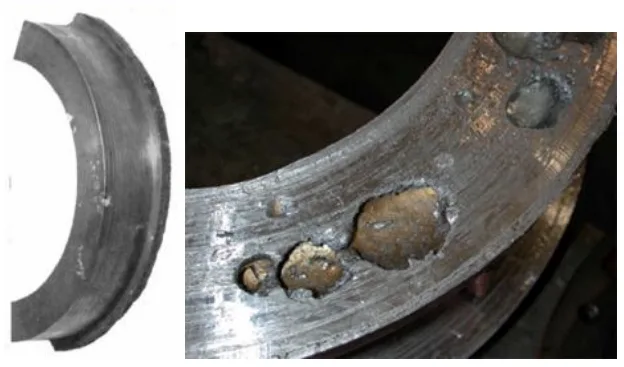
2. 연구 배경:
- 연구 주제의 사회적/학문적 맥락: 다이 캐스팅은 기하학적으로 복잡한 부품을 경제적이고 효율적으로 생산할 수 있는 공정으로 강조됩니다. 그러나 주조 결함의 발생은 이 공정에서 인지되는 과제입니다. 다이 캐스팅 응용 분야에서 품질과 효율성을 유지하려면 이러한 결함을 식별하고 해결하는 것이 중요합니다.
- 기존 연구의 한계: 본 논문은 기존 연구의 한계를 명시적으로 언급하지 않지만, 특히 알루미늄 합금 다이 캐스팅 내에서 주조 결함, 원인 및 해결책을 분류하고 설명하는 통합된 자료의 필요성을 암시합니다.
- 연구의 필요성: 본 연구는 알루미늄 다이 캐스팅의 주조 결함에 대한 체계적인 이해를 제공하기 위해 필요합니다. 결함을 근본 원인에 따라 분류하고 해결책을 자세히 설명함으로써, 본 논문은 주조 공급업체와 고객이 결함을 식별, 분석 및 수정하는 데 도움을 주어 궁극적으로 주조 품질을 개선하고 불량률을 줄이는 것을 목표로 합니다.
3. 연구 목적 및 연구 질문:
- 연구 목적: 본 논문의 주요 목적은 알루미늄 합금 다이 캐스팅에서 발생하는 다양한 결함을 식별하고 이러한 결함의 근본 원인과 함께 해결책을 제시하는 것입니다.
- 주요 연구 질문: 본 논문은 다음과 같은 연구 질문을 암묵적으로 다룹니다.
- 알루미늄 합금 다이 캐스팅에서 흔히 관찰되는 결함은 무엇입니까?
- 이러한 결함의 근본 원인은 무엇입니까?
- 이러한 결함을 완화하거나 제거하기 위한 효과적인 해결책은 무엇입니까?
- 연구 가설: 본 논문은 연구 가설을 명시적으로 제시하지 않지만, 결함을 원인별로 분류하고 해당 해결책을 제공하는 것이 다이 캐스팅 산업에 유익할 것이라는 암묵적인 가설 하에 진행됩니다.
4. 연구 방법론
- 연구 설계: 본 논문은 검토 및 분류 연구입니다. 특히 알루미늄 다이 캐스팅에 초점을 맞춰 주조 결함, 원인 및 해결책에 대한 기존 지식을 수집하고 분류합니다.
- 자료 수집 방법: 본 연구는 다이 캐스팅 결함과 관련된 기존 문헌 및 산업 지식 검토를 기반으로 합니다. 논문은 핸드북, 학회 회의록 및 저널 논문을 정보 소스로 참조합니다.
- 분석 방법: 본 논문은 질적 분석 방법을 사용하여 주조 결함을 원인 (야금학적 결함, 열 관련 결함, 기계적 유발 결함)에 따라 분류합니다. 각 결함 유형에 대해 논문은 원인을 설명하고 확립된 다이 캐스팅 원칙 및 모범 사례를 기반으로 해결책을 제시합니다.
- 연구 대상 및 범위: 본 논문의 범위는 알루미늄 다이 캐스팅의 주조 결함으로 제한됩니다. 논의된 결함은 발생 원인에 따라 분류되며, 각 범주 내에서 표면 및 내부 결함 모두 고려됩니다.
5. 주요 연구 결과:
- 주요 연구 결과: 본 논문은 알루미늄 다이 캐스팅의 주조 결함을 원인에 따라 야금학적 결함, 열 관련 결함, 기계적 유발 결함의 세 가지 주요 범주로 분류합니다. 각 범주 내에서 특정 결함 유형이 식별되고, 그 원인과 해결책이 함께 제시됩니다.
- 통계적/질적 분석 결과: 본 논문은 주로 질적 연구이며 통계 분석을 제시하지 않습니다. 결과는 결함, 원인 및 해결책에 대한 구조화된 분류 및 설명으로 제시됩니다.
- 자료 해석: 본 논문은 확립된 야금학적 및 제조 원칙에 따라 주조 결함을 해석합니다. 원인은 공정 변수, 재료 특성 및 설계 요인 측면에서 설명됩니다. 해결책은 이러한 식별된 원인을 수정하는 것을 기반으로 제안됩니다.
- 그림 목록:
- Fig 3.1 Gas porosity (가스 기공)
- Fig 3.2 Shrinkage Porosity (수축 기공)
- Fig 3.3 Sinks (수축)
- Fig 3.4 Blister (블리스터)
- Fig 3.5 Soldering (솔더링)
- Fig 3.6 Segregation (편석)
- Fig 3.7 Inclusion (개재물)
- Fig 3.8 Dross (드로스)
- Fig 4.1 Crack (균열)
- Fig 5.1 Hot tears (고온 균열)
- Fig 5.2 Hot tears in part (부품의 고온 균열)
- Fig 6.1 cold shut in part (부품의 냉간 겹침)
- Fig 7.1 Misrun in part (부품의 미충진)
- Fig 8.1 Thermal defect (열적 결함)
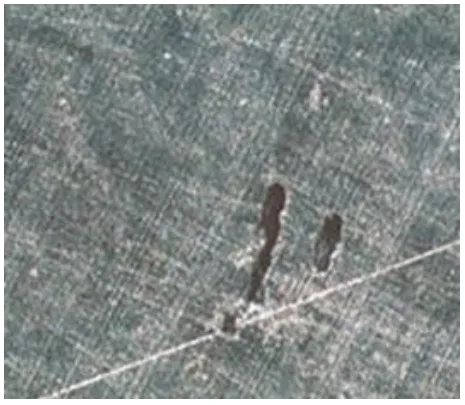
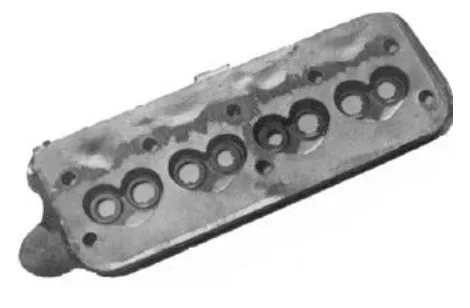
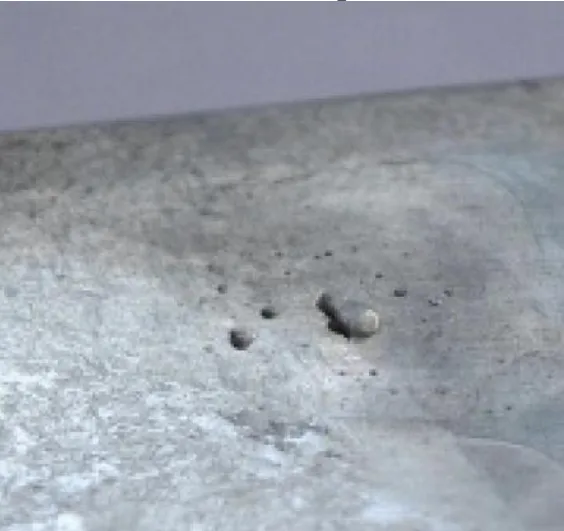
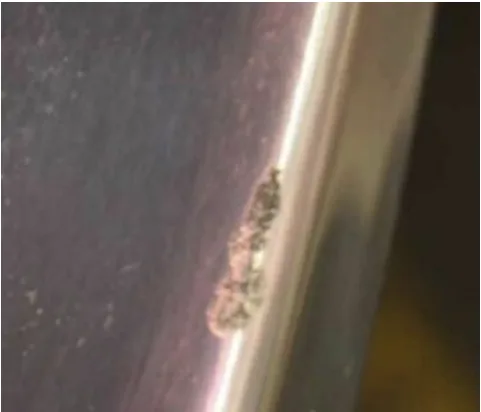
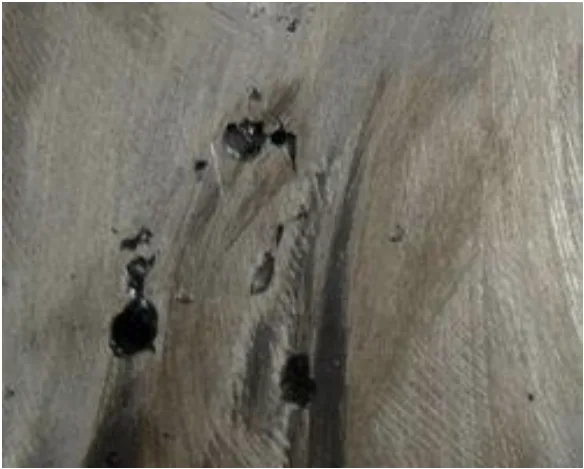
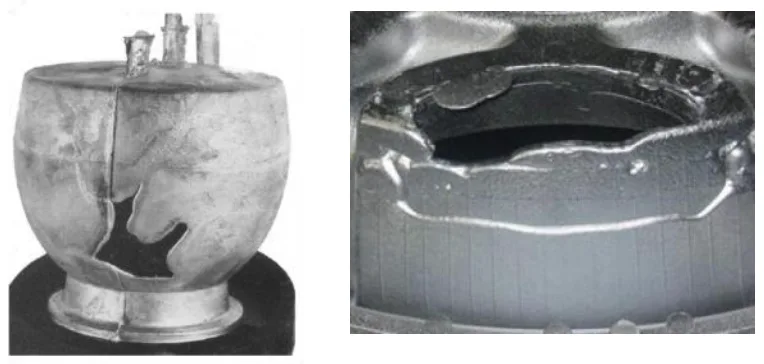
6. 결론 및 논의:
- 주요 결과 요약: 본 논문은 알루미늄 다이 캐스팅의 다양한 주조 결함을 성공적으로 분류하고 설명하며, 원인별로 분류하고 각 결함에 대한 자세한 원인과 해결책을 제공합니다. 분류에는 야금학적 결함 (Porosity, Sinks, Inclusion, Dross, Soldering), 열 관련 결함 (Hot tears, Cold shut, Thermal fatigue) 및 기계적 유발 결함 (Surface marks, bending, undercuts)이 포함됩니다.
- 연구의 학문적 의의: 본 논문은 주조 결함에 대한 가치 있는 핸드북 수준의 요약을 제공하여 다양한 출처의 정보를 구조화되고 쉽게 접근할 수 있는 형식으로 통합합니다. 이러한 분류 접근 방식은 다이 캐스팅 분야의 연구자 및 실무자에게 유용한 참고 자료가 될 수 있습니다.
- 실용적 의미: 각 결함 유형에 대한 자세한 원인 및 해결책 설명은 주조 산업의 품질 관리 부서에 실질적인 지침을 제공합니다. 다이 캐스터는 이 정보를 활용하여 결함 분석 프로세스를 개선하고, 공정 변수를 최적화하고, 생산성과 주조 수율을 향상시키기 위한 효과적인 해결책을 구현할 수 있습니다. 본 논문은 주조 불량률을 최소화하는 것은 결함의 근본 원인을 이해하고 해결하는 데 달려 있다고 강조합니다.
- 연구의 한계: 본 논문은 검토 및 분류 연구이며 제안된 해결책에 대한 경험적 테스트 또는 검증을 포함하지 않습니다. 해결책의 효과는 일반적인 다이 캐스팅 원칙 및 산업 모범 사례를 기반으로 하며, 특정 사례 연구 또는 실험적 연구를 통해 추가 검증이 필요할 수 있습니다.
7. 향후 후속 연구:
- 후속 연구 방향: 향후 연구는 다음 사항에 초점을 맞출 수 있습니다.
- 산업 환경에서 설계된 실험 및 사례 연구를 통한 제안된 해결책의 경험적 검증.
- 결함 감소에 대한 다양한 해결책의 효과에 대한 정량적 분석.
- 다이 캐스팅 공정에서 실시간 결함 감지 및 분석을 위한 고급 진단 도구 및 기술 개발.
- 수축 기공 해결책의 맥락에서 간략하게 언급된 바와 같이, 주조 결함을 예측하고 예방하기 위한 시뮬레이션 소프트웨어의 적용 조사.
- 추가 탐구가 필요한 영역: 결함 발생을 최소화하기 위한 공정 변수 및 합금 조성 최적화, 그리고 다이 캐스팅을 위한 보다 강력하고 자동화된 품질 관리 시스템 개발 분야에 대한 추가 탐구가 필요합니다.
8. 참고 문헌:
- [1] D.L cocks. “A proposed simple qualitative classification for die-casting"; 'Proc Die-casting Conference, Montreaux(1996)
- [2] ASM Handbook: Volume 15: Casting edition 9",2008,pp629-620.
- [3] J. Campbell, R.A hardening. "Casting technology", in TAIAT 2.0ncd-rom, EAA, Brussels, 2000
- [4] John Gilbert Kaunfman, Elwin L. Rooy," Aluminum alloy casting: Properties, Processes, and application", ASM international,pp47-54
- [5] R.Monroe," porosity in casting", AFS Transcation,2005,pp1-29.
- [6] Defect formation in cast iron LennartElmquist School of Engineering Jönköping University, SwedenTammerfors, Finland, November 8, 2012.
- [7] Analysis of Casting Defects and Identification of emedial Measures - A Diagnostic Study Dr D.N. Shivappal, Mr Rohit2, Mr. Abhijit Bhattacharya3 International Journal of Engineering Inventions ISSN: 2278-7461, www.ijeijournal.com Volume 1, Issue 6 (October2012) PP: 01-05
- [8] Casting Defect Analysis using Design of Experiments (DoE) and Computer Aided Casting Simulation Technique Uday A. Dabade* and Rahul C. Bhedasgaonkar,(2013) [5]. Reduction of defects in grey cast iron castings by six sigma approach Raguramsingh.M#1, SyathAbuthakeer.S*2 #ME Lean Manufacturing, PSG.
- [9] W.G WAlkington, “Gas Porosity: A guid t corrective the problem, North America die casting association, "1997.
9. 저작권:
*본 자료는 "Rahul T Patil, Veena S Metri, Shubhangi S Tambore"의 논문: "Causes of Casting Defects with Remedies"를 기반으로 합니다.
*논문 출처: www.ijert.org
본 자료는 상기 논문을 기반으로 요약되었으며, 상업적 목적으로 무단 사용하는 것을 금지합니다.
Copyright © 2025 CASTMAN. All rights reserved.