본 페이퍼 요약은 ['Ultra Large Castings to Produce Low Cost Aluminum Vehicle Structures'] 논문을 기반으로 작성되었으며, ['SAE TECHNICAL PAPER SERIES']에 발표되었습니다.
1. 개요:
- 제목: 저비용 알루미늄 차량 구조 생산을 위한 초대형 주조 (Ultra Large Castings to Produce Low Cost Aluminum Vehicle Structures)
- 저자: T. N. Meyer, M. J. Kinosz, E. M. Bradac, M. Mbaye, J. T. Burg and M. A. Klingensmith
- 발행 연도: 1999년
- 발행 저널/학회: SAE TECHNICAL PAPER SERIES, 1999년 4월 26-28일 워싱턴 D.C. 정부/산업 회의에서 발표됨.
- 키워드: 초대형 주조 (Ultra Large Castings), 알루미늄 차량 구조 (Aluminum Vehicle Structures), 저비용 (Low Cost), 다이캐스팅 (Die Casting), 금속 금형 (Metal Mold), 다중 포트 사출 (Multiport Injection), 수직 주조 공정 (Vertical Casting Process), 자동차 (Automotive), 경량화 (Lightweighting).
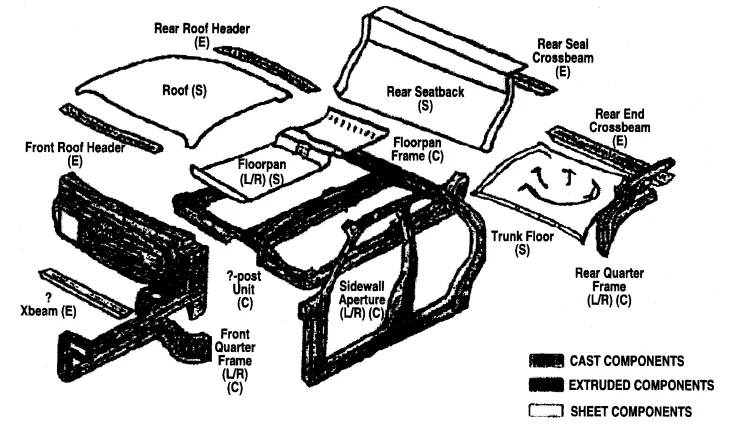
2. 연구 배경:
연구 주제 배경:
자동차 산업은 점점 더 엄격해지는 환경 배출 기준을 충족하고 연비 효율성을 향상시키기 위해 지속적으로 차량 중량 감소를 위해 노력하고 있습니다. 알루미늄은 상당한 경량화 잠재력을 제공하지만, 지상 운송 차량 (자동차, 스포츠 유틸리티 차량/경트럭/밴, 버스 및 대형 트럭) 시장에서 더 폭넓게 채택되는 데에는 강철에 비해 높은 비용이 걸림돌이 됩니다. 이 비용은 알루미늄 제품의 기본 재료 비용 (예: 판재, 압출재 또는 주조 제품)과 후속 가공 및 조립 비용 (예: 성형, 접합, 마감 작업) 모두에 기인합니다.
기존 연구 현황:
차량 플로어 팬 프레임과 같은 기존 차량 구조물 제조는 일반적으로 저항 점용접을 사용하여 여러 개의 성형된 강철 스탬핑을 조립하는 방식으로 이루어집니다. Alcoa의 기존 알루미늄 진공 다이캐스팅 (AVDC) 공정 (미국 특허 5,370,171)은 고품질 박벽 주조품을 생산할 수 있지만, 초대형 부품과 관련된 비용 및 복잡성을 해결하기 위해서는 추가적인 발전이 필요합니다. 항공우주 분야에서 활용되는 레벨 푸어 주조 공정 (level pour casting process)은 복잡한 형상에는 적합하지 않으며, 크고 얇은 벽 부품에서 러너 제거에 어려움이 있습니다.
연구의 필요성:
경량 알루미늄 구조물의 비용 장벽을 극복하고 자동차 부문에서 대량 생산 (예: 연간 100,000대)을 촉진하기 위해서는 저비용으로 초대형 박벽 부품을 생산할 수 있는 혁신적인 주조 공정이 절실히 필요합니다. 본 연구는 기존 강철 조립품과 경량 알루미늄 대안 사이의 비용 격차를 해소하는 것을 목표로 합니다.
3. 연구 목적 및 연구 질문:
연구 목적:
주요 연구 목적은 차량 구조용 초대형 박벽 알루미늄 부품 생산을 위한 새로운 주조 공정을 개발하고 시연하는 것입니다. 이 공정은 부품 수와 조립 비용을 크게 줄여 경량 운송 차량 구조물의 전체 비용을 낮추는 것을 목표로 합니다.
주요 연구 내용:
주요 연구는 저압, 핫 챔버, 다중 포트 사출 수직 주조 공정의 개발 및 구현에 중점을 둡니다. 연구에는 다음 내용도 포함됩니다.
- 크기와 기하학적 복잡성을 나타내는 시연 부품 선정.
- 경제성 및 공정 요구 사항과 호환되는 핫 챔버 사출 시스템 개발.
- 고품질 주조를 위한 구조적 및 주조 공정 요구 사항을 충족하도록 부품 설계, 금속 사출 포트 위치 및 초기 사출 조건 최적화.
- 용융 금속을 사출 시스템으로 전달하기 위한 시스템 구축.
- 모든 시스템 구성 요소 사양 결정, 제작, 설치 및 디버깅.
연구 가설:
명시적으로 가설로 진술되지는 않았지만, 연구는 다음과 같은 전제하에 진행됩니다.
- 개발된 공정을 통해 생산된 초대형 주조품은 알루미늄 차량 구조물의 비용을 실질적으로 절감할 수 있습니다.
- 저압, 핫 챔버, 다중 포트 수직 주조 공정은 이러한 크고 얇은 벽 알루미늄 부품을 제조하는 데 실행 가능하고 효율적인 방법입니다.
4. 연구 방법론
연구 설계:
본 연구는 개발 및 시연 연구 설계를 채택합니다. 여기에는 새로운 초대형 주조 시스템의 개념화, 설계, 제작 및 테스트가 포함됩니다. 크라이슬러 미니밴 리프트게이트 내부 패널을 공정 평가를 위한 시연 부품으로 선정했습니다.
자료 수집 방법:
자료 수집 방법은 다음과 같습니다.
- 컴퓨터 시뮬레이션: 구조 성능 평가를 위한 유한 요소 해석 (Finite Element Analysis, FEA) 및 공정 매개변수 및 부품 설계를 최적화하기 위한 주조 시뮬레이션 (충전 및 응고).
- 시스템 개발 및 테스트: 개발된 주조 시스템의 실제 구현 및 테스트 (부품 제작, 시스템 통합 및 공정 시운전 포함).
- 비용 분석: 초대형 주조 방식의 비용 효율성을 평가하기 위한 생산 시설 및 공정의 경제성 평가.
분석 방법:
- 유한 요소 해석 (FEA): 주조 알루미늄 내부 패널의 구조적 성능을 분석하고 기존 강철 조립품과 비교하는 데 사용됩니다.
- 주조 시뮬레이션: 가스 포집, 기공을 방지하고 방향성 응고를 보장하는 것을 목표로 사출 포트 위치, 금형 온도 제어 및 냉각 요구 사항을 포함한 주조 공정을 최적화하는 데 사용됩니다.
- 경제성 분석: 주조 알루미늄 부품의 생산 비용을 추정하고 기존 강철 조립품의 비용과 비교하기 위해 수행됩니다.
연구 대상 및 범위:
본 연구는 알루미늄 차량 구조용 초대형 주조 공정 개발에 중점을 둡니다. 범위는 특정 자동차 부품인 다임러-크라이슬러 미니밴 리프트게이트 내부 패널을 사용하여 공정을 시연하는 것으로 제한됩니다. 시스템은 플로어 팬 프레임 및 측벽 개구부 구조로 예시되는 대형 자동차 부품을 생산할 수 있도록 설계되었습니다.
5. 주요 연구 결과:
주요 연구 결과:
본 연구는 초대형 박벽 부품 생산을 위한 저압, 금속 금형, 다중 포트 사출 수직 주조 공정을 성공적으로 개발했습니다. Alcoa 기술 센터에 전용 주조 시스템을 설계 및 제작하여 길이 3m, 너비 1.7m, 높이 0.4m의 부품을 생산할 수 있게 되었습니다. 11개의 강철 부품으로 조립된 크라이슬러 미니밴 리프트게이트 내부 패널을 공정 시연을 위해 단일 알루미늄 주조 부품으로 재설계했습니다 (그림 2b). FEA는 주조 알루미늄 설계가 다임러-크라이슬러의 성능 요구 사항을 충족함을 확인했습니다. 초기 중량 감소 목표는 40%였지만, 기존 강철 부품 외피에 의해 제한된 강성 중심 설계로 인해 중량 감소는 25%에 더 가까워졌습니다. 생산 시설의 비용 분석 (그림 5) 결과, 26파운드 주조 알루미늄 부품이 33파운드 강철 조립품에 비해 7.00달러에서 14.00달러의 비용 프리미엄이 발생할 수 있는 것으로 나타났습니다.
자료 해석:
핫 챔버 금속 사출 시스템 개발과 금형 바로 아래에서 금속 품질을 유지하는 것이 주요 성과로 강조됩니다. 복잡한 형상의 리프트게이트 내부 패널의 성공적인 주조는 초대형 주조 공정의 타당성을 입증합니다. 비용 분석 (그림 6)은 비용 프리미엄이 존재하지만 중량 감소 및 부품 통합의 잠재력이 상당한 이점을 제공함을 시사합니다. 알루미늄 특화 설계 최적화를 통해 목표 중량 감소 40%를 달성하면 비용 프리미엄을 더욱 줄이고 알루미늄 구조물의 경쟁력을 높일 수 있습니다.
그림 목록:
- 그림 1. 초대형 주조의 후보 부품 (Candidate Parts for Ultra Large Castings)
- 그림 2a. 기존 강철 내부 패널 (Conventional Steel Inner Panel)
- 그림 2b. 단일 알루미늄 주조 내부 패널 (Single Aluminum Cast Inner Panel)
- 그림 3. 리프트게이트 영구 금형 (Liftgate Permanent Mold)
- 그림 4. 프레스 플래튼에 위치한 미니밴 (Minivan Located on Press Platen to Scale)
- 그림 5. 생산 시스템 레이아웃 (Production System Layout)
- 그림 6. 생산 시설 비용 분석 (Cost Breakdown for Production Facility)
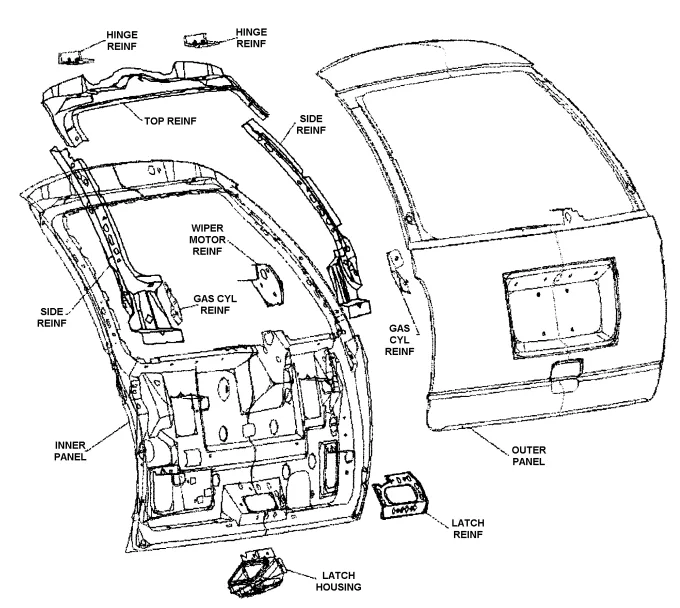
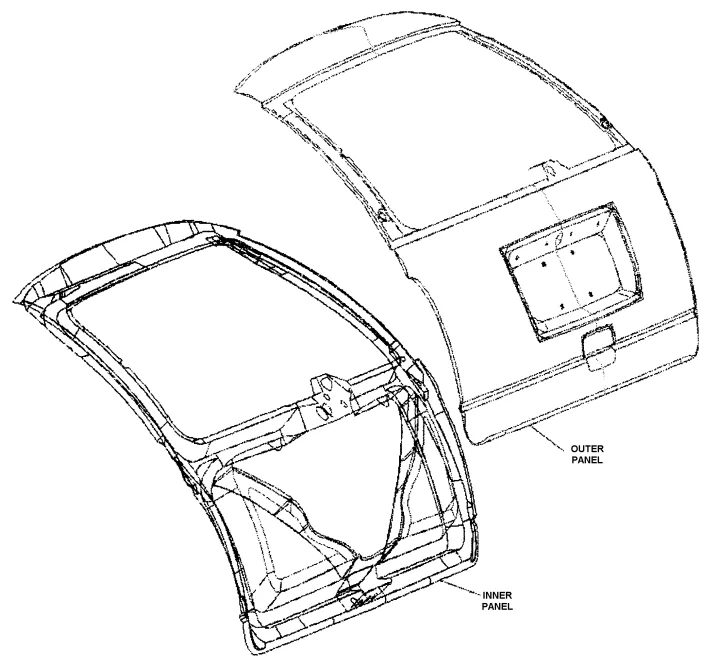
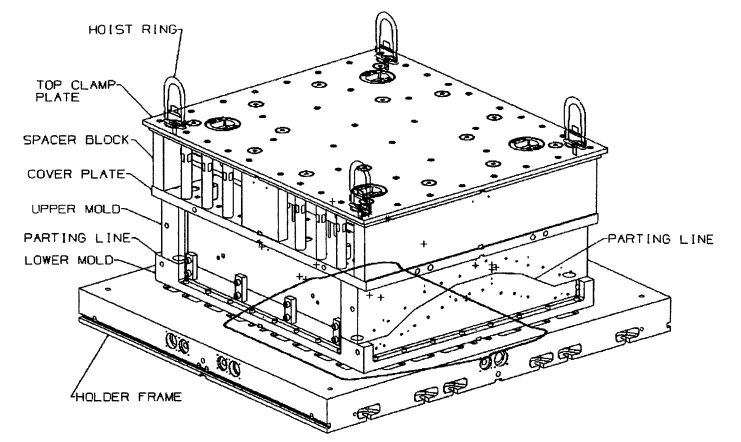
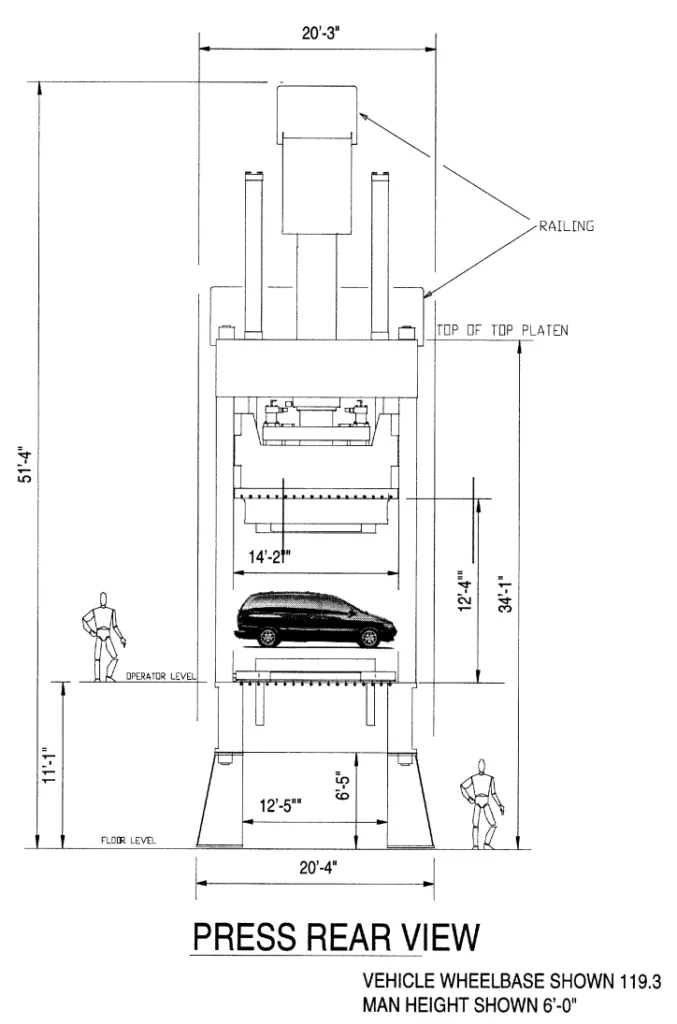
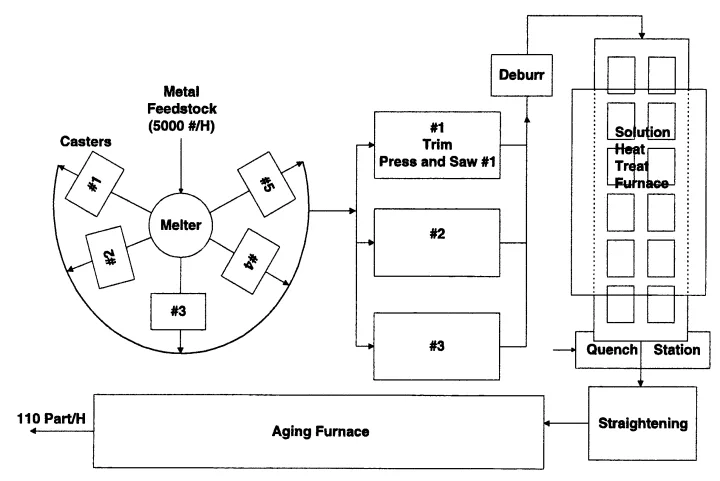
6. Conclusion:
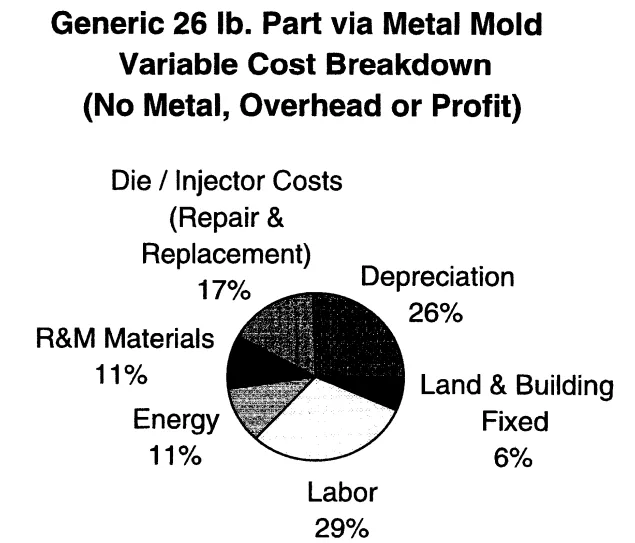
6. 결론:
주요 연구 결과 요약:
본 연구는 초대형 박벽 알루미늄 차량 구조물 생산을 위한 저압, 핫 챔버, 다중 포트 수직 주조 공정의 타당성을 성공적으로 입증했습니다. 개발된 공정 및 주조 시스템은 부품 수와 조립 작업을 줄여 경량 알루미늄 부품의 비용을 크게 절감할 수 있는 길을 제시합니다. 크라이슬러 미니밴 리프트게이트 내부 패널 시연은 복잡한 형상을 주조하고 기존 강철 조립품에 비해 중량 감소를 달성할 수 있는 능력을 보여주었습니다.
연구의 학문적 의의:
본 연구는 크고 복잡한 알루미늄 주조품 생산을 위한 새로운 접근 방식을 도입하고 검증함으로써 다이캐스팅 기술 발전에 기여합니다. 저압, 핫 챔버, 다중 포트 사출 시스템의 설계 및 구현과 자동차 경량화에 대한 응용 분야에 대한 귀중한 통찰력을 제공합니다.
실용적 의미:
본 초대형 주조 공정의 성공적인 개발은 자동차 산업에 상당한 실용적 의미를 갖습니다. 알루미늄 차량 구조물의 비용을 절감하여 강철과의 경제적 경쟁력을 높이고 연비 효율성을 개선하고 배기가스 배출을 줄이기 위한 경량화 전략의 광범위한 채택을 촉진할 수 있는 잠재적인 솔루션을 제공합니다.
연구의 한계 및 향후 연구 분야:
시연에서 달성된 중량 감소는 기존 강철 부품 외피에 의해 부과된 강성 요구 사항에 의해 제한되었습니다. 향후 연구에서는 중량 감소 잠재력을 극대화하기 위해 알루미늄에 특화된 부품 설계 최적화에 초점을 맞춰야 합니다. 추가적인 공정 최적화, 산업 규모 확장 및 시연 부품을 넘어선 더 넓은 응용 분야 탐색이 향후 연구 분야로 권장됩니다.
7. 참고 문헌:
- 미국 특허 5,370,171, 1994년 12월 06일, "다이캐스팅 공정 및 장비 (Die Casting Process and Equipment)," J. R. Fields 외, Alcoa.
8. 저작권:
- 본 자료는 "T. N. Meyer, M. J. Kinosz, E. M. Bradac, M. Mbaye, J. T. Burg and M. A. Klingensmith"의 논문: "저비용 알루미늄 차량 구조 생산을 위한 초대형 주조 (Ultra Large Castings to Produce Low Cost Aluminum Vehicle Structures)"를 기반으로 작성되었습니다.
- 논문 출처: SAE TECHNICAL PAPER SERIES 1999-01-2252
본 자료는 상기 논문을 기반으로 요약되었으며, 상업적 목적으로 무단 사용하는 것을 금지합니다.
Copyright © 2025 CASTMAN. All rights reserved.