본 문서는 2007년 9월 Journal of Computing and Information Science in Engineering에 게재된 "자동화된 파팅 방향 및 파팅 라인 결정을 위한 다이캐스팅 특징 인식"이라는 제목의 연구 논문을 요약합니다. 이 논문은 전통적으로 전문가의 직관과 시간 소모적인 수동 절차에 의존했던 다이캐스팅에서 파팅 방향 및 파팅 라인 결정을 자동화하는 중요한 과제를 다룹니다.
1. 개요:
- 제목: 자동화된 파팅 방향 및 파팅 라인 결정을 위한 다이캐스팅 특징 인식 (Die-Casting Feature Recognition for Automated Parting Direction and Parting Line Determination)
- 저자: 자틴더 마단 (Jatinder Madan), P.V.M. 라오 (P.V.M. Rao), T.K. 쿤드라 (T.K. Kundra)
- 발행 연도: 2007년 9월
- 발행 저널/학회: Journal of Computing and Information Science in Engineering
- 키워드: 다이캐스팅 (die casting), 특징 인식 (feature recognition), 인출 방향 (withdrawal direction), 파팅 방향 (parting direction), 파팅 라인 (parting line), 제조를 위한 설계 (design for manufacture)
2. 연구 배경:
- 연구 주제의 사회적/학문적 맥락: 다이캐스팅은 중요한 정미 성형 제조 공정으로 강조됩니다. 다른 정미 성형 공정과 마찬가지로 다이캐스팅은 주로 코어와 캐비티라는 두 개의 금형 반쪽을 활용합니다 (그림 1 참조). 논문은 특히 제품 설계 단계에서 부품 설계의 복잡성이 증가함에 따라 금형 설계와 부품의 전반적인 제조 가능성이 상당히 어려워진다고 강조합니다. 주요 문제점은 부품 설계자가 다이캐스팅 공정의 복잡성, 특히 파팅 방향 및 파팅 라인 결정과 관련된 문제에 대한 포괄적인 지식이 부족한 경우가 많다는 것입니다. 현재 산업 관행은 부품 설계자와 제조 전문가 간의 반복적인 순환을 통해 설계 제조 가능성을 확보하는 특징을 보입니다.
- 기존 연구의 한계: 논문은 연구자들이 파팅 방향 및 라인 선택에 대한 지침을 제시했지만, 자동화 부족으로 인해 부품 형상 및 모양과 관련된 광범위한 데이터 처리가 필요하다고 지적합니다. 이러한 수동 구현은 시간이 많이 걸리고 다이캐스팅 전문가의 상당한 노력이 필요합니다. 이전의 특징 인식 연구는 주로 절삭 가공 및 판금 성형에 집중되어 왔으며, 다이캐스팅과는 구별되는 특징 정의를 가지고 있습니다. 기존의 다이캐스팅 특징 인식 및 파팅 방향 결정 방법은 다음과 같은 여러 측면에서 제한적입니다.
- 상당한 수동 입력 및 계산 노력이 필요한 경우가 많습니다.
- 일부 방법은 특정 유형의 표면 (예: 평면 표면, 다면체 부품)으로 제한됩니다.
- 국소 가시성에 기반한 접근 방식은 산업 관행을 정확하게 반영하지 못할 수 있습니다.
- 기존의 특징 인식 기술은 복잡하고 중첩되며 상호 작용하는 특징을 처리하는 데 어려움을 겪을 수 있습니다.
- 일부 방법은 미리 정의된 특징 라이브러리에 의존하여 새로운 설계에 대한 적응성을 제한합니다.
- 연구의 필요성: 본 연구는 설계 프로세스 효율성을 높이고 설계-제조 통합을 가능하게 하는 중요한 도구로서 자동화된 제조 가능성 분석의 필요성을 강조합니다. 또한 공정 계획의 자동화 증가는 제조에서 더 높은 효율성과 생산성을 달성하는 데 필수적입니다. 다이캐스팅 특징, 파팅 방향, 파팅 라인, 사이드 코어 및 캐비티 수의 자동 결정은 공정 계획에 중요한 입력 요소이며, 생산 시간, 부품 비용 및 전반적인 수익성에 직접적인 영향을 미칩니다. 논문은 특히 자동화된 다이캐스팅 특징 인식 및 파팅 방향 및 파팅 라인의 자동 선택과 같은 공정 계획 자동화에 대한 관심이 제한적이라고 구체적으로 지적합니다. 따라서 파팅 방향 및 파팅 라인 결정을 위한 자동화된 접근 방식은 다이캐스팅 설계-제조 통합 및 자동화된 DFM (Design for Manufacture, 제조를 위한 설계) 분석에 매우 중요합니다. 제안된 시스템은 STEP 파일에서 직접 제품 데이터를 활용하고 자동화된 파팅 방향 및 파팅 라인 결정을 위해 다이캐스팅 특징을 식별함으로써 이러한 요구 사항을 해결하는 것을 목표로 합니다.
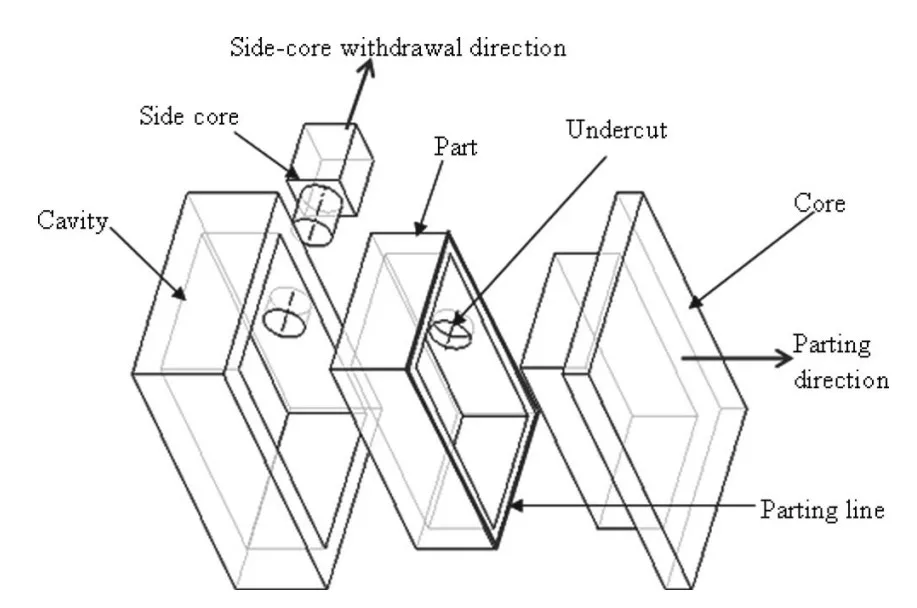
3. 연구 목적 및 연구 질문:
- 연구 목적: 주요 연구 목적은 다음과 같은 포괄적인 자동화 시스템을 개발하는 것입니다.
- 다이캐스팅 특징 인식: STEP 파일로 표현된 부품 CAD 모델에서 다이캐스팅 특징 (돌출 및 함몰)을 자동으로 식별하고 분류합니다.
- 자동화된 파팅 방향 결정: 인식된 특징 및 공정 제약 조건을 기반으로 다이캐스트 부품에 대한 최적의 파팅 방향을 자동으로 결정합니다.
- 자동화된 파팅 라인 결정: 선택된 파팅 방향을 기반으로 공정 제약 조건 및 우선 순위를 고려하여 파팅 라인을 자동으로 결정합니다.
- 주요 연구 질문: 본 연구는 다음과 같은 주요 질문에 답하고자 합니다.
- 미리 정의된 특징 라이브러리에 의존하지 않고 STEP 파일 데이터에서 복잡하고 중첩되며 상호 작용하는 특징을 포함한 다이캐스팅 특징을 어떻게 자동으로 인식할 수 있을까요?
- 산업 관행에 맞춰 다이캐스팅 특징에 대한 인출 방향을 결정하기 위해 자동화 시스템에서 전역 가시성을 효과적으로 활용하려면 어떻게 해야 할까요?
- 선택된 파팅 방향을 기반으로 파팅 라인을 결정하기 위해 공정 제약 조건 및 우선 순위를 자동화 시스템에 통합하려면 어떻게 해야 할까요?
- 포괄성, 정확성 및 복잡한 산업 다이캐스트 부품에 대한 적용 가능성 측면에서 기존 접근 방식의 한계를 극복하는 자동화 시스템을 개발할 수 있을까요?
- 연구 가설: 핵심 연구 가설은 STEP 파일 입력, 기하학적 추론, 전역 가시성 분석 및 공정 제약 조건 고려 사항을 활용하는 새롭게 개발된 자동화 시스템이 다이캐스트 부품에 대한 파팅 방향 및 파팅 라인 결정을 효과적이고 포괄적으로 자동화할 수 있다는 것입니다. 이 시스템은 기존의 자동화된 접근 방식의 한계를 극복하고 다이캐스팅 산업의 전문가 결정과 일치하는 결과를 제공할 것으로 가설화됩니다.
4. 연구 방법론:
- 연구 설계: 본 연구는 개발 및 검증 연구 설계를 채택합니다. 다이캐스팅 특징 인식 및 파팅 방향/라인 결정을 위한 새로운 자동화 시스템 개발에 중점을 둡니다. 그런 다음 시스템의 성능과 결과를 전문가 지식 및 산업 관행과 비교하여 검증합니다.
- 데이터 수집 방법: 시스템은 부품 CAD 모델의 STEP 파일 (특히 AP 203/214)을 주요 입력 데이터 소스로 활용합니다. STEP 파일은 중립 표준이므로 다양한 CAD 플랫폼에서 더 넓은 적용 가능성을 보장합니다. 시스템은 면-모서리 및 모서리-정점 관계를 포함하여 이러한 STEP 파일에서 직접 기하학적 데이터를 추출합니다.
- 분석 방법: 방법론의 핵심은 기하학적 추론과 규칙 기반 시스템에 기반합니다.
- 특징 인식: 기하학적 추론은 돌출 또는 함몰 영역으로 정의되는 다이캐스팅 특징을 식별하는 데 적용됩니다. 시스템은 이러한 특징을 인출 방향 (단일, 이중 또는 다중)에 따라 분류합니다. 중첩되고 상호 작용하는 특징을 인식하기 위한 규칙을 통합하고 인출 방향 계획을 위해 전역 가시성을 사용합니다.
- 파팅 방향 및 파팅 라인 결정: 파팅 라인 결정은 공정 제약 조건 및 우선 순위를 고려하여 선택된 후보 파팅 방향을 기반으로 합니다. 파팅 방향 및 파팅 라인에 대한 평가 기준은 중요한 다이캐스팅 특정 요소를 고려합니다.
- 검증: 시스템 결과는 다이캐스팅 산업 전문가의 의견과 비교하여 검증됩니다. 시스템은 산업 부품에 대해 테스트되며, 전문가 해석과의 출력 일관성을 평가합니다.
- 연구 대상 및 범위: 본 연구는 다이캐스트 부품에 초점을 맞추고 특히 돌출 및 함몰 특징의 인식 및 분석을 목표로 합니다. 범위는 다음을 포함합니다.
- 특징 유형: 내부 및 외부 언더컷으로 분류되는 돌출 및 함몰 특징.
- 인출 방향: 특징은 단일, 이중 또는 다중 인출 방향을 갖는 것에 따라 분류됩니다.
- 부품 형상: 시스템은 중첩되고 상호 작용하는 특징을 포함하여 복잡한 부품 형상을 처리하도록 설계되었습니다.
- 공정 고려 사항: 방법론은 파팅 방향 및 파팅 라인 결정에 다이캐스팅 공정 제약 조건을 통합합니다.
- 소프트웨어 구현: 연구에는 STEP 파일 입력부터 파팅 방향 및 파팅 라인 출력까지 전체 프로세스를 자동화하는 소프트웨어 시스템 개발이 포함됩니다.
5. 주요 연구 결과:
- 주요 연구 결과: 본 연구의 주요 결과는 다이캐스팅 특징 인식 및 자동화된 파팅 방향 및 파팅 라인 결정을 위한 기능적인 자동화 시스템 개발입니다. 시스템은 성공적으로 다음을 수행합니다.
- 다이캐스팅 특징 식별: STEP 파일 입력에서 돌출 및 함몰을 포함한 다이캐스팅 특징을 정확하게 인식합니다.
- 인출 방향별 특징 분류: 특징을 단일, 이중 또는 다중 인출 방향을 기반으로 한 범주로 효과적으로 분류합니다.
- 기하학적 추론 및 전역 가시성 활용: 시스템은 특징 인식을 위해 기하학적 추론을 사용하고 산업 관행에 맞춰 인출 방향 계획을 위해 전역 가시성을 활용합니다.
- 공정 제약 조건을 고려한 파팅 라인 결정: 공정 제약 조건 및 우선 순위를 통합하여 선택된 파팅 방향을 기반으로 파팅 라인을 결정합니다.
- 기존 시스템의 한계 극복: 시스템은 이전의 자동화된 접근 방식에서 발견된 한계를 극복하고 더 포괄적인 것으로 제시됩니다.
- 통계적/질적 분석 결과: 논문은 시스템 결과를 다이캐스팅 산업 전문가의 의견과 비교하여 검증하는 것을 강조합니다. 제공된 텍스트를 기반으로 한 이 요약에서는 특정 통계 분석이 자세히 설명되어 있지 않지만, 전문가에 의한 질적 검증은 결과의 핵심 측면입니다. 논문은 시스템을 세 가지 산업 부품에 적용한 예시를 제시합니다.
- 자동차 다이캐스트 부품 (그림 12): 특징 인식 및 인출 방향 결과는 표 1에 나와 있습니다. 특징 연결 결과는 표 2에 있습니다. 파팅 방향 평가 결과는 표 3에 있습니다. 최적의 파팅 방향은 "A"로 결정되었습니다.
- 소켓 하우징 (그림 13(a)): 중첩된 특징과 외부 오목 모서리를 사용하는 특징을 포함하여 13개의 특징이 식별되었습니다. 최적의 파팅 방향은 "Y"입니다 (표 4).
- 카운터웨이트 (그림 13(b)): 특징 인식 결과가 표시됩니다. 최적의 파팅 방향은 "Y"입니다 (표 4).
- 데이터 해석: 결과는 개발된 시스템이 다이캐스팅 특징 인식, 파팅 방향 및 파팅 라인 결정의 복잡한 작업을 효과적으로 자동화한다는 것을 보여줍니다. 다양한 특징 유형을 식별하고, 전역 가시성을 고려하고, 공정 제약 조건을 통합하는 시스템의 능력은 숙련된 다이캐스팅 전문가의 결정과 일치하는 결과를 가져옵니다. 이는 시스템이 이전의 자동화된 방법의 한계를 성공적으로 해결하고 다이캐스팅 설계 및 제조를 위한 실용적인 도구를 제공함을 시사합니다.
- 그림 목록:
- 그림 1 다이캐스팅 공정
- 그림 2 용어
- (a) V-맵 (V-Map)
- (b) 볼록 모서리 (Convex edge)
- (c) 오목 모서리 (Concave edge)
- (d) 전역 가시성 (접근성) (Global visibility (accessibility))
- (e) 국소 가시성 (Local Visibility)
- 그림 3 단일 인출 방향을 갖는 고립된 함몰 특징 (Isolated depression features with single withdrawal direction)
- 그림 4 고유한 인출 방향을 갖는 중첩된 함몰 (Nested depressions with unique withdrawal direction)
- (a) 중첩된 원통형 구멍 (Nested cylindrical holes)
- (b) 중첩된 각기둥 및 원통형 함몰 (Nested prismatic and cylindrical depressions)
- 그림 5 관통 구멍 및 함몰 (Through holes and depressions)
- (a) 관통 원통형 구멍 (Through cylindrical hole)
- (b) 관통 각기둥 함몰 (Through prismatic depression)
- 그림 6 고립된 돌출의 인출 방향 (Withdrawal directions of isolated protrusions)
- (a) 원통형 돌출 (Cylindrical protrusion)
- (b) 원뿔형 돌출 (Conical protrusion)
- (c) 구형 돌출 (Spherical protrusion)
- 그림 7 단순화된 트레이 모델 (Simplified model of a tray)
- 그림 8 일반 함몰 및 돌출 (Generic depression and protrusion)
- (a) 일반 함몰 (Generic depression)
- (b) 일반 돌출 (Generic protrusion)
- 그림 9 외부 언더컷 (Outside undercuts)
- 그림 10 상호 작용하는 언더컷 (Interacting undercuts)
- (a) 상호 작용하는 오목 모서리 및 원통형 돌출 (Interacting concave edges and cylindrical protrusion)
- (b) 상호 작용하는 오목 모서리 및 원통형 함몰 (Interacting concave edges and cylindrical depression)
- 그림 11 파팅 라인 식별 (Parting line identification)
- (a) PLR 및 PLS (PLR and PLS)
- (b) 선택된 파팅 라인 (Selected parting line)
- 그림 12 자동차 다이캐스트 부품 [50] (An automotive die-cast part [50])
- 그림 13 특징 인식 결과 (Feature recognition results)
- (a) 소켓 하우징 (Socket Housing)
- (b) 카운터웨이트 (Counterweight)
- 그림 14 파팅 라인 식별 결과 (Parting line identification results)
- (a) 소켓 하우징 (Socket Housing)
- (b) 카운터웨이트 (Counterweight)
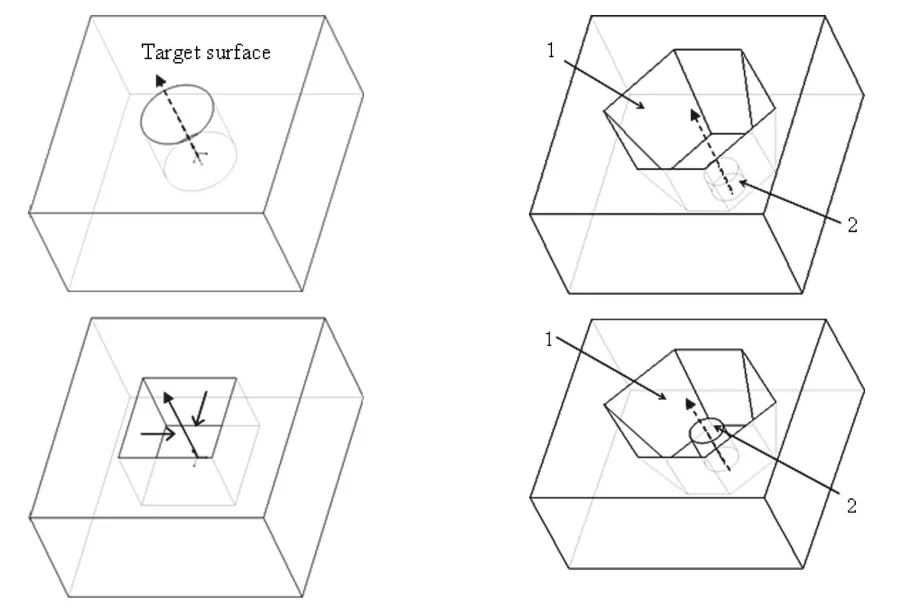
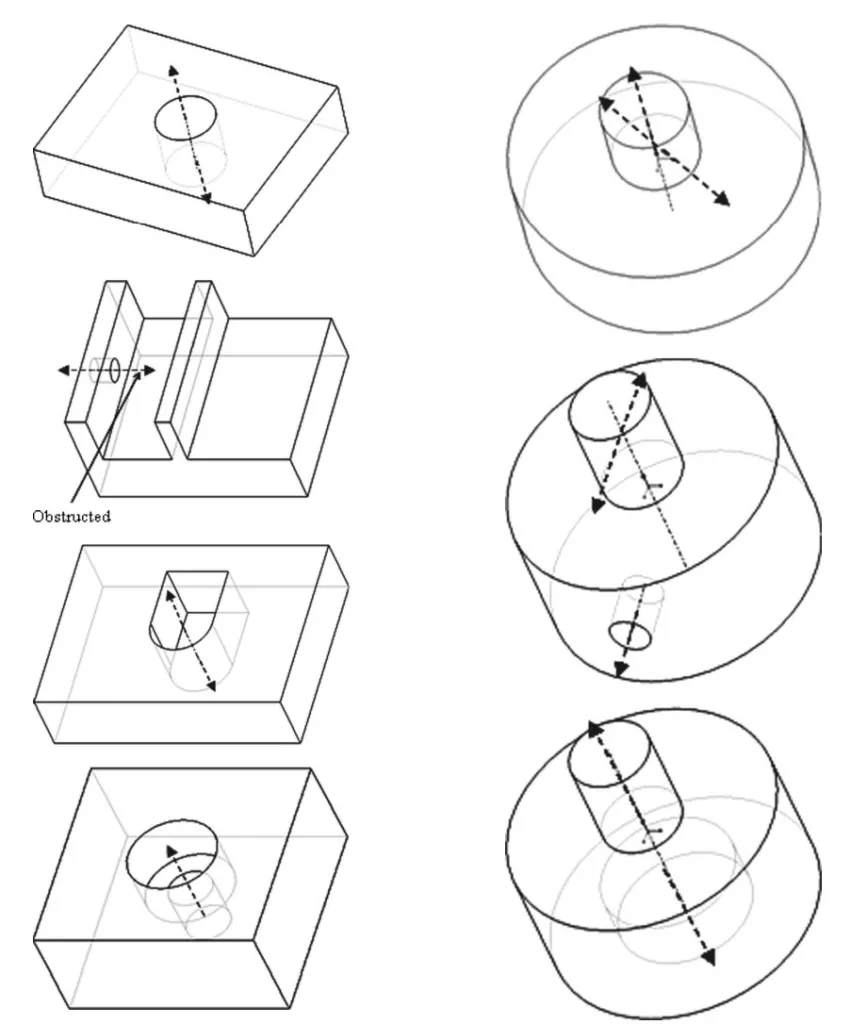
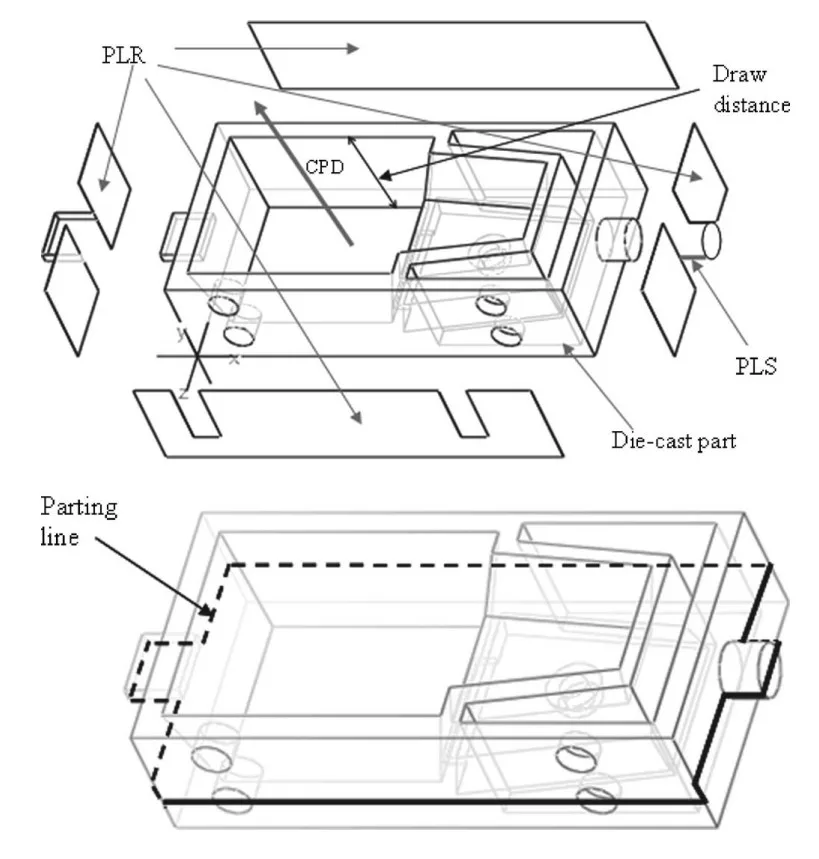
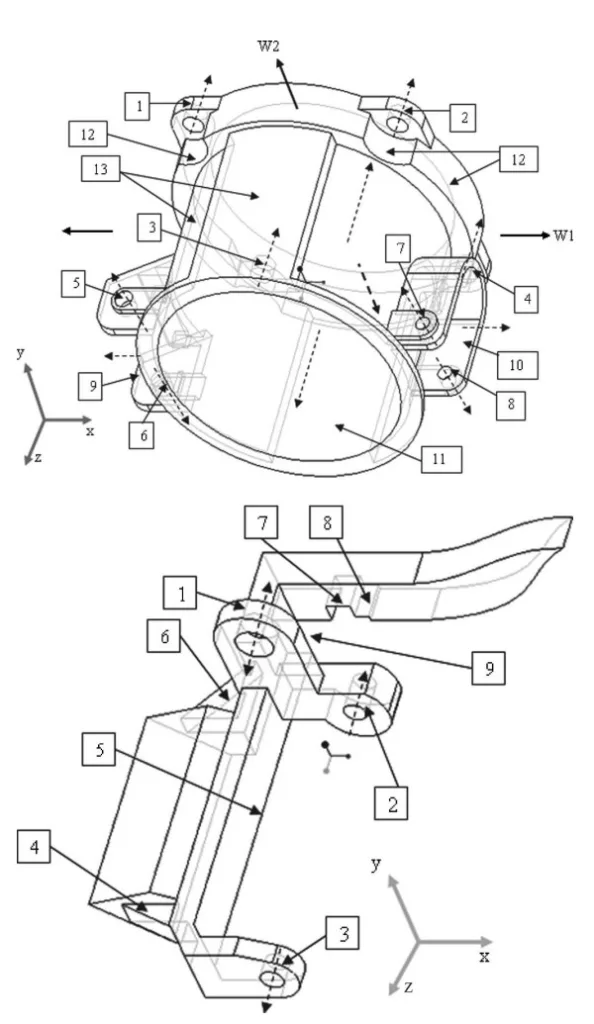
6. 결론 및 논의:
- 주요 결과 요약: 본 연구는 다이캐스팅 특징 인식, 파팅 방향 및 파팅 라인 결정을 위한 자동화 시스템을 성공적으로 개발하고 검증했습니다. 이 시스템은 이전 연구의 한계를 효과적으로 해결하여 보다 포괄적이고 실용적인 접근 방식을 제공합니다. 다이캐스팅 특징을 정확하게 식별하고, 최적의 파팅 방향 및 라인을 결정하며, 그 결과는 다이캐스팅 산업의 전문가 판단과 일치합니다.
- 연구의 학문적 의의: 본 연구는 컴퓨터 지원 설계 및 제조 분야, 특히 다이캐스팅 영역에서 중요한 학문적 기여를 합니다. 개발된 시스템은 중요한 설계 및 공정 계획 작업의 자동화를 발전시킵니다. 적응성과 범위를 향상시키는 미리 정의된 라이브러리에 의존하지 않는 일반적인 특징 인식에 대한 새로운 방법론을 소개합니다. 전역 가시성 사용과 파팅 방향 및 라인 결정에 공정 제약 조건을 통합하는 것은 이전 접근 방식에 비해 상당한 개선을 나타냅니다.
- 실용적 의미: 본 연구의 실용적 의미는 다이캐스팅 산업의 부품 설계자와 공정 계획가 모두에게 상당합니다. 자동화된 시스템은 다음과 같은 여러 가지 주요 이점을 제공합니다.
- 시간 절약: 시간 소모적인 수동 프로세스를 자동화하여 파팅 방향 및 파팅 라인 결정에 필요한 시간을 크게 줄입니다.
- 효율성 향상: 설계 프로세스 및 공정 계획 활동의 효율성을 향상시킵니다.
- 비용 절감: 금형 설계 및 공정 계획을 최적화하여 생산 시간과 부품 비용을 절감하는 데 기여합니다.
- 설계-제조 통합: 설계 및 제조 단계 간의 더 나은 통합을 촉진합니다.
- 자동화된 DFM 분석: 자동화된 DFM (Design for Manufacture, 제조를 위한 설계) 분석을 가능하게 하여 제조 가능성 문제를 조기에 식별하고 해결할 수 있습니다.
- 더 넓은 적용 가능성: STEP 파일을 입력으로 사용하면 다양한 CAD 플랫폼에서 더 넓은 적용 가능성을 보장합니다.
- 연구의 한계: 논문은 현재 연구의 특정 한계를 인정합니다.
- 금형 유형 가정: 시스템은 부품이 사이드 코어를 사용하여 잠재적으로 2피스 금형을 사용하여 성형 가능하다고 가정합니다. 스플릿 코어가 필요한 시나리오는 명시적으로 다루지 않습니다.
- 자유 곡면: 현재 시스템은 자유 곡면을 가진 부품을 직접 처리하지 않습니다. 그러나 저자는 자유 곡면에 대한 가시성 및 금형 접근성 연구를 통합하면 시스템의 적용 가능성을 확장할 수 있다고 제안합니다.
- 내부 스플릿 코어: 시스템은 다이캐스팅에서 작동이 거의 불가능한 것으로 간주되므로 내부 스플릿 코어를 고려하지 않습니다.
7. 향후 후속 연구:
- 후속 연구 방향: 저자는 개발된 시스템의 기능을 더욱 향상시키고 확장하기 위해 여러 가지 향후 연구 방향을 제안합니다.
- 스플릿 코어 처리: 스플릿 코어가 필요할 수 있는 다이캐스팅 시나리오를 수용하도록 시스템을 확장합니다 (다이캐스팅에서 덜 일반적이고 복잡하지만).
- 자유 곡면 통합: 자유 곡면 처리를 위한 기술을 통합하고 잠재적으로 이러한 표면에 대한 가시성 및 금형 접근성에 대한 기존 연구를 활용합니다.
- 공정 계획 시스템과의 통합: 보다 포괄적인 자동화된 다이캐스팅 공정 계획 환경을 만들기 위해 광범위한 컴퓨터 지원 공정 계획 (CAPP) 시스템과의 인터페이스 및 통합을 개발합니다.
- DFM 시스템과의 통합: 다이캐스트 부품의 제조 가능성 평가를 더욱 자동화하기 위해 DFM (Design for Manufacture, 제조를 위한 설계) 시스템과 시스템을 통합합니다.
- 추가 탐구가 필요한 영역: 다음과 같은 영역에서 추가 탐구가 권장됩니다.
- 복잡한 부품 형상: 훨씬 더 광범위한 복잡한 산업 부품 형상에 대한 시스템 성능을 테스트하고 개선합니다.
- 공정 제약 조건 개선: 시스템의 의사 결정 프로세스에 보다 상세하고 미묘한 다이캐스팅 공정 제약 조건을 추가로 조사하고 통합합니다.
- 평가 기준 개선: 진화하는 산업 모범 사례 및 다이캐스팅의 기술 발전을 더 잘 반영하기 위해 파팅 방향 및 파팅 라인 선택에 사용되는 평가 기준을 지속적으로 개선합니다.
8. 참고 문헌:
- [1] Gupta, S. K., Das, D., Regli, W. C., and Nau, D. S., 1997, "Automated Manufacturability Analysis: A Survey," Res. Eng. Des., 9(3), pp. 168-190.
- [2] Chen, L. L., Chou, S. Y., and Woo, T. C., 1993, "Parting Directions for Mould and Die Design," Comput.-Aided Des., 25, pp. 762-768.
- [3] Gan, G. H., Woo, T. C., and Tang, K., 1994, "Spherical Maps: Their Construction, Properties and Approximation," ASME J. Mech. Des., 116, pp. 357-363.
- [4] Elber, G., and Cohen, E., 1995, "Arbitrarily Precise Computation of Gauss Maps and Visibility Sets for Freeform Surface," Transactions of ACM Solid Modeling '95, Salt Lake City, UT.
- [5] Corney, J., Hayes, C., Sundararajan, V., and Wright, P., 2005, "The CAD/CAM Interface: A 25 Years Retrospective," ASME J. Comput. Inf. Sci. Eng., 5, pp. 188-191.
- [6] Gao, S., and Shah, J. J., 1998, "Automatic Recognition of Machining Features Based on Minimal Condition Subgraph," Comput.-Aided Des., 30(9), pp. 727-739.
- [7] Nnaji, B. O., Kang, T.-S., Yeh, S., and Chen, J.-P., 1991, "Feature Reasoning for Sheet Metal Components," Int. J. Prod. Res., 29(9), pp. 1867-1896.
- [8] Gavankar, P., and Henderson, M. R., 1990, "Graph Based Extraction of Protrusions and Depression From Boundary Representation," Comput.-Aided Des., 22(7), pp. 442-450.
- [9] Floriani, L. D., 1989, "Feature Extraction From Boundary Models of Three-Dimensional Objects," IEEE Trans. Pattern Anal. Mach. Intell., 2(8), pp. 785-798.
- [10] Lockett, H. L., and Guenov, M. D., 2005, "Graph-Based Feature Recognition for Injection Moulding Based on a Mid-Surface Approach," Comput.-Aided Des., 37, pp. 251-262.
- [11] McAdams, D. A., and Bidkar, R. A., 2003, "Automated Manufacturability Analysis for Injection Moulding and Die Cast Parts," Proceedings of DETC 2003/DFM-48154, Chicago, IL.
- [12] Fu, M. W., Fuh, J. Y. H., and Nee, A. Y. C., 1999, "Undercut Feature Recognition in an Injection Mold Design System," Comput.-Aided Des., 31, pp. 777-790.
- [13] Ye, X. G., Fuh, J. Y. H., and Lee, K. S., 2001, "A Hybrid Method for Recognition of Undercut Features From Molded Parts," Comput.-Aided Des., 33, pp. 1023-1034.
- [14] Ye, X. G., Fuh, J. Y. H., and Lee, K. S., 2004, "Automatic Undercut Feature Recognition for Side Core Design of Injection Molds," J. Mech. Des., 126, pp. 519-526.
- [15] Chung, K., Lee, K., and Kim, T., 2002, "Recognition of Pass Features for Automatic Parting Surface Generation in Injection Moulds," Proc. Inst. Mech. Eng., Part B, 216, pp. 783-796.
- [16] Lim, T., Corney, J., and Clark, D. E. R., 2001, "Laminae-Based Feature Recognition," IEEE Trans. Pattern Anal. Mach. Intell., 23(9), pp. 1043-1048.
- [17] Bralla, J. G., 1999, Design for Manufacturability Handbook, McGraw Hill, New York.
- [18] ASM, 1970, Metals Handbook, Forging and Casting, Vol. 5, American Society of Metals, Metals Park, OH.
- [19] Pye, R. G. W., 1978, Injection Mould Design: A Design Manual for the Thermoplastic Industry, The Plastic and Rubber Institute, London.
- [20] Ravi, B., and Srinivasan, M. N., 1990, "Decision Criteria for Computer Aided Parting Surface Design," Comput.-Aided Des., 22, pp. 11-18.
- [21] Madan, J., Rao, P. V. M., and Kundra, T. K., 2006, "Optimal Parting Direction Selection for Die-Casting," paper communicated to International Journal of Manufacturing Technology and Management.
- [22] Chen, Y., H., 1997, "Determining Parting Direction Based on Minimum Bounding Box and Fuzzy Logic," Int. J. Mach. Tools Manuf., 37(9), pp. 1189-1199.
- [23] Chen, Y. H., Wang, Y. Z., and Leung, T. M., 2000, "An Investigation of Parting Direction Based on Dexel Model and Fuzzy Decision Making," Int. J. Prod. Res., 38(6), pp. 1357-1375.
- [24] Chen, L. L., and Chou, S. Y., 1995, "Partial Visibility for Selecting a Parting Direction in Mould and Die Design," J. Manuf. Syst., 14(5), pp. 319-330.
- [25] Mochizuki, T., and Yuhara, N., 1992, "Methods of Extracting Potential Undercut and Determining Optimal Withdrawal Direction for Mold Designing," Int. J. Jpn. Soc. Precis. Eng., 26, pp. 68-73.
- [26] Yin, Z. P., Ding, H., and Xiong, Y. L., 2000, "Moldability Analysis for Near-Net-Shaped Manufactured Parts Using Freedom Cones," Int. J. Adv. Manuf. Technol., 16, pp. 169–175.
- [27] Yin, Z. P., Ding, H., and Xiong, Y. L., 2001, "Virtual Prototyping of Mold Design: Mouldablity Analysis for Near Net Shape Manufactured Parts by Feature Recognition and Geometric Reasoning," Comput.-Aided Des., 33, pp. 137-154.
- [28] Kurth, G. R., and Gadh, R., 1997, "Virtual Prototyping of Die-Design: Determination of Die-Open Directions for Near-Net-Shape Manufactured Parts With Extruded or Rotational Features," Comput.-Integr. Manuf. Syst., 10(1), pp. 69-81.
- [29] Fu, M. W., Fuh, J. Y. H., and Nee, A. Y. C., 1999, "Generation of Optimal Parting Direction Based on Undercut Features in Injection Molded Parts," IIE Trans., 31, pp. 947-955.
- [30] Khardekar, R., Burton, G., and McMains, S., 2006, "Finding Feasible Mold Parting Directions Using Graphics Hardware," Comput.-Aided Des., 38(4), pp. 327-341.
- [31] Lu, H. Y., and Lee, W. B., 2000, "Detection of Interference Elements and Release Directions in Die-Cast and Injection Molded Components," Proc. Inst. Mech. Eng., Part B, 214, pp. 431-441.
- [32] Huang, J., Gupta, S. K., and Stoppel, K., 2003, "Generating Sacrificial Multi-Piece Molds Using Accessibility Driven Spatial Partitioning," Comput.-Aided Des., 35(13), pp. 1147-1160.
- [33] Banerjee, A. G., and Gupta, S. K., 2006, "A Step Towards Automated Design of Side Actions in Injection Molding of Complex Parts," Geometric Modeling and Processing Conference, Pittsburgh, PA.
- [34] Tan, S. T., Yuen, M. F., Sze, W. S., and Kwong, K. W., 1990, "Parting Lines and Parting Surfaces of Injection Molded Parts," Proc. Inst. Mech. Eng., Part B, 204, pp. 211-219.
- [35] Wong, T., Tan, S. T., and Sze, W. S., 1998, "Parting Line Formation by Slicing a 3D CAD Model," Eng. Comput., 14, pp. 330-343.
- [36] Weinstein, M., and Manoochehri, S., 1997, "Optimum Parting Line Design of Molded and Cast Parts for Manufacturability," J. Manuf. Syst., 16, pp. 1-12.
- [37] Nee, A. Y. C., Fu, M. W., Fuh, J. Y. H., Lee, K. S., and Zhang, Y. F., 1998, "Automatic Determination of 3-D Parting Lines and Surfaces in Plastic Injection Mold Design," CIRP Ann., 47(1), pp. 95-98.
- [38] Fu, M. W., Nee, A. Y. C., and Fuh, J. Y. H., 2002, "The Application of Surface Visibility and Moldability to Parting Line Generation," Comput.-Aided Des., 34, pp. 469-480.
- [39] Nainy-Nejad, M., and Creese, R. C., 1999, "Computer Generation and Optimization of Parting Directions, Parting Lines and Core Cavities," One Hundred Third Annual Meeting of the American Foundrymen's Society, Rosemont, IL, September.
- [40] Penny, F. D., 1953, A Handbook of Die Casting, Ministry of Supply, York House, London.
- [41] Boothroyd, G., Dewhurst, P., and Knight, W., 1994, Product Design for Manufacture and Assembly, Marcel Dekker Inc, New York.
- [42] Elber, G., Chen, X., and Cohen, E., 2005, "Mold Accessibility via Gauss Map Analysis," ASME J. Comput. Inf. Sci. Eng., 5, pp. 79-85.
- [43] Pratt, M. J., and Wilson, P. R., 1985, "Requirements for Support of Form Features in a Solid Modelling System," Computer Aided Manufacturing International (CAMI), Paper No. R-85-ASPP-01.
- [44] Shah, J., and Rogers, M., 1988, "Functional Requirements and Conceptual Design of Feature Based Modeling System," Journal of Computer Aided Engineering, 5(1), pp. 9-15.
- [45] Shah, J. J., Anderson, D., Kim, Y. S., and Joshi, S., 2001 "A Discourse on Geometric Feature Recognition From CAD Models," ASME J. Comput. Inf. Sci. Eng., 1, pp. 41-51.
- [46] Dhaliwal, S., Gupta, S. K., and Huang, J., 2000, "Computing Exact Global Accessibility Cones for Polyhedral Objects," ASME Design for Manufacturability Conference, Baltimore, MD, September.
- [47] Dhaliwal, S., Gupta, S. K., Huang, J., and Priyadarshi, A., 2003, "Algorithm for Computing Global Accessibility Cones," ASME J. Comput. Inf. Sci. Eng., 3, 200-209.
- [48] Priyadarshi, A., and Gupta, S. K., 2004, "Geometric Algorithms for Automated Design of Multi-piece Permanent Molds," Comput.-Aided Des., 36(3), pp. 241-260.
- [49] Pahl, G., and Beitz, W., 1996, Engineering Design, Springer Verlag, London.
- [50] NADCA, 2007, Website of North American Die Casting Association, Rosemont, Illinois, http://www.diecasting.org/information/dc_shape. htm (accessed on Jan. 2, 2007).
- [51] Madan, J., Rao, P. V. M., and Kundra, T. K., 2006, "System for Early Cost Estimation of Die-Cast Parts," Int. J. Prod. Res., accepted for publication.
- [52] Zhao, Z., and Shah, J. J., 2005, "Domain Independent Shell for Dfm and Its Application to Sheet Metal Forming and Injection Molding," Comput.-Aided Des., 37, pp. 881-898.
9. 저작권:
- 본 자료는 자틴더 마단, P.V.M. 라오, T.K. 쿤드라의 논문: "자동화된 파팅 방향 및 파팅 라인 결정을 위한 다이캐스팅 특징 인식"을 기반으로 합니다.
- 논문 출처: DOI: 10.1115/1.2768369
본 자료는 상기 논문을 기반으로 요약되었으며, 상업적 목적으로 무단 사용하는 것을 금지합니다.
Copyright © 2025 CASTMAN. All rights reserved.