본 논문 요약은 ['Mohsen Soori']가 발행한 ['Manufacturing Processes of Car Alloy Wheels'] 논문을 기반으로 작성되었습니다.
1. 개요:
- 제목: 자동차 합금 휠의 제조 공정 (Manufacturing Processes of Car Alloy Wheels)
- 저자: Mohsen Soori
- 발행 연도: 2022년
- 발행 저널/학술 단체: HAL open science (프리프린트)
- 키워드: 알로이 휠 (Alloy wheels), 주조 (Casting), CNC 가공 작업 (CNC machining operations), 유한 요소법 (Finite Element Method), 최적화 (Optimization)
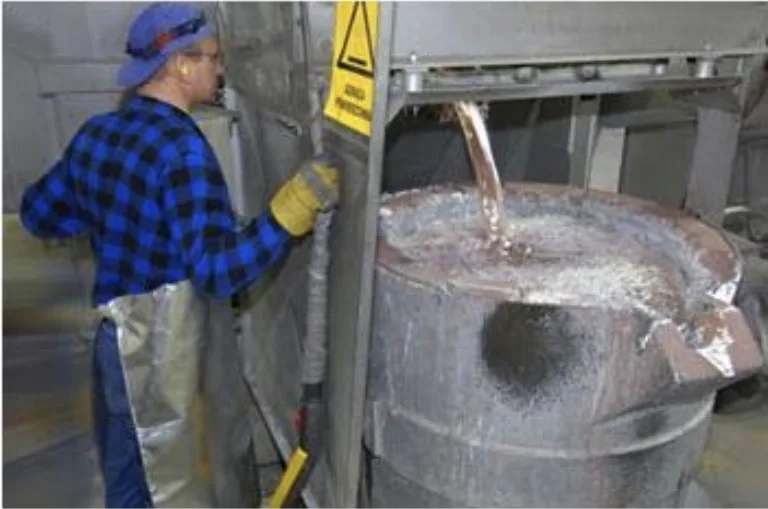
2. 초록
승용차는 연비 절감을 위해 경량 휠인 알로이 휠을 사용하고 있습니다. 알로이 휠은 일반적으로 알루미늄 및 마그네슘과 같은 가볍고 강한 합금으로 만들어지며, 이는 제동 시스템의 성능을 향상시켜 주행 안전성을 높일 수 있습니다. 알로이 휠은 주조, 가공 및 단조 공정을 통해 생산됩니다. 생산 공정은 부품 생산 효율성을 높이기 위해 분석 및 수정될 수 있습니다. 유한 요소 해석은 실제 작동 조건에서 휠의 정적 및 동적 응력을 찾는 데 사용될 수 있습니다. 터닝 머신 툴을 사용한 가공 작업 공정 또한 분석하여 수정할 수 있습니다. 최적화 공정은 생산된 알로이 휠의 강성을 높이는 데 사용될 수 있습니다. 새로운 합금 특성은 알로이 휠의 성능을 향상시키기 위해 가상 시뮬레이션을 사용하여 테스트할 수 있습니다. 생산 부품의 품질을 높이기 위해 알로이 휠 생산 공정의 저압 다이캐스팅의 열 모델을 분석합니다. 따라서 알로이 휠 제조 공정에서 더 많은 부가가치를 달성할 수 있습니다.
키워드: 알로이 휠 (Alloy wheels), 주조 (Casting), CNC 가공 작업 (CNC machining operations), 유한 요소법 (Finite Element Method), 최적화 (Optimization)
3. 연구 배경:
연구 주제 배경:
자동차 산업에서 연비 효율성을 추구함에 따라 승용차에서 알로이 휠의 채택이 증가했으며, 이는 주로 강철 휠에 비해 무게가 가볍기 때문입니다. 일반적으로 알루미늄 및 마그네슘과 같은 가볍고 견고한 재료로 구성된 이러한 알로이 휠은 연비뿐만 아니라 제동 시스템 성능을 향상시켜 주행 안전성을 개선하는 데 기여합니다. 알로이 휠 제조는 주조, 가공 및 단조 공정을 포함한 여러 주요 공정을 포함합니다.
기존 연구 현황:
알로이 휠 제조 분야의 현재 연구는 부품 생산 효율성을 극대화하기 위해 생산 공정을 분석하고 개선하는 데 중점을 두고 있습니다. 유한 요소 해석(FEA)은 작동 조건에서 휠 내부의 정적 및 동적 응력을 평가하는 데 사용됩니다. 터닝 머신 툴을 활용한 가공 작업은 최적화를 위해 분석 및 수정 대상이 됩니다. 또한 최적화 기술은 제조된 알로이 휠의 강성을 향상시키기 위해 적용됩니다. 가상 시뮬레이션은 새로운 합금 특성을 평가하고 전체 휠 성능을 개선하기 위해 활용됩니다. 저압 다이캐스팅 공정의 열 모델링 또한 생산 부품의 품질을 높이기 위해 조사됩니다.
연구의 필요성:
본 연구는 알로이 휠 제조 분야에서 지속적인 효율성 및 품질 향상 요구에 의해 필요성이 제기되었습니다. 기존 생산 방법론을 분석하고 수정함으로써 알로이 휠 제조 공정에서 성능, 안전성 및 구조적 무결성과 같은 중요한 측면을 해결하여 부가가치를 높이는 것을 목표로 합니다.
4. 연구 목적 및 연구 질문:
연구 목적:
본 연구의 주요 목적은 알로이 휠 생산 공정에 대한 포괄적인 개요를 제시하고 이러한 제조 기술을 발전시키고 최적화하는 것을 목표로 하는 최근 연구 노력을 분석하는 것입니다.
주요 연구 내용:
본 논문은 알로이 휠 생산 개발과 관련된 최근 학술 연구를 검토하며, 다음 주요 영역에 중점을 둡니다.
- 알루미늄 휠 주조 공정의 컴퓨터 시뮬레이션 (Computer Simulation of Casting Process of Aluminum Wheels)
- 저압 다이캐스트 알루미늄 합금 휠의 주조 결함 (Casting defects in low-pressure die-cast aluminum alloy wheel)
- 알루미늄 합금 휠 가공의 공정 능력 개선 (Process capability improvement for aluminum alloy wheel machining)
- 승용차 알로이 휠의 정적 응력 분석 (Analysis of Static Stress in an Alloy Wheel of the Passenger car)
- 알루미늄 합금 휠의 강성 최적화 (Optimization of Rigidity of Aluminum Alloy Wheels)
- 자동차 휠 제조를 위한 합금 특성 분석 (Analysis of Alloy properties for the Manufacture of Automotive Wheels)
- 알루미늄 합금 휠의 내부 림 압축 시험 시뮬레이션 (Simulation of Inner Rim Compression Test of Aluminum Alloy Wheels)
- 6061 알루미늄 합금 휠의 단조 공정 분석 (Analysis of the forging processes for 6061 aluminum-alloy wheels)
- A356 알루미늄 합금 휠의 저압 다이캐스트(LPDC) 공정의 3차원 열 모델 개발 (Development of a 3-D thermal model of the low-pressure die-cast (LPDC) process of A356 aluminum alloy wheels)
- 알루미늄 합금의 정밀 단조 기술 (Precision forging technology for aluminum alloy)
- 알루미늄 합금 휠의 균열 현상에 대한 유한 요소 시뮬레이션 및 실험적 검증 (Finite element simulation and experimental validation of the cracking phenomenon in aluminum alloy wheels)
- 저압 다이캐스팅 중 알루미늄 합금 자동차 휠의 기공률에 대한 냉각 공정의 영향 (Effect of Cooling Process on Porosity in the Aluminum Alloy Automotive Wheel During Low-Pressure Die Casting)
연구 가설:
공식적인 가설로 명시되지는 않았지만, 검토된 연구는 FEA, 열 모델링 및 최적화 알고리즘과 같은 고급 분석 및 시뮬레이션 기술의 적용이 주조 및 가공에서 단조 및 품질 관리에 이르기까지 다양한 단계에서 알로이 휠 제조 공정의 개선에 크게 기여할 수 있다는 전제를 암묵적으로 조사합니다.
5. 연구 방법론
연구 설계:
본 연구는 문헌 검토 설계를 채택하여 자동차 알로이 휠의 제조 공정과 관련된 기존 연구 출판물을 체계적으로 검토하고 종합합니다.
자료 수집 방법:
본 검토를 위한 자료는 알로이 휠 제조 기술에 초점을 맞춘 동료 검토 저널 논문, 학술 대회 발표 자료 및 학술 출판물에 대한 포괄적인 검색 및 분석을 통해 수집되었습니다.
분석 방법:
사용된 분석 방법은 기술적 요약입니다. 각 선정된 연구 논문을 분석하고 요약하여 주요 결과, 방법론 및 결론을 추출합니다. 그런 다음 요약을 종합하여 해당 분야의 최근 발전 및 동향에 대한 개요를 제공합니다.
연구 대상 및 범위:
연구 대상은 주조, 가공, 단조, 재료 특성, 공정 최적화 및 결함 분석을 포함한 알로이 휠 제조의 다양한 측면을 포함합니다. 범위는 알로이 휠의 생산 공정, 주로 알루미늄 합금 및 관련 제조 기술을 향상시키는 것을 목표로 하는 연구 개발 활동으로 제한됩니다.
6. 주요 연구 결과:
주요 연구 결과:
본 논문은 알로이 휠 제조의 여러 중요한 영역에 걸친 최근 연구 결과를 요약하고 종합합니다.
- 주조 공정의 컴퓨터 시뮬레이션: Hsu와 Yu [22]는 주조 시뮬레이션 소프트웨어를 활용하여 금형 온도 안정화될 때까지 알루미늄 휠 주조 공정을 반복적으로 모델링했습니다. 그들은 주조 품질을 정량화하기 위해 "수축 지수"(SI)를 도입하여 누출 테스트 결과와 잘 연관시키고 주조 매개변수의 최적화를 가능하게 했습니다.
- 저압 다이캐스트 알루미늄 합금 휠의 주조 결함: Zhang et al. [23]은 저압 다이캐스트 알루미늄 휠의 주조 관련 결함을 조사하여 휠 외관, 기밀성 및 기계적 성능에 영향을 미치는 주요 문제로 거시적 및 미시적 기공, 수반된 산화막 및 외인성 산화물 개재물을 확인했습니다.
- 알루미늄 합금 휠 가공의 공정 능력 개선: Sharma et al. [24]은 A356 알루미늄 합금 휠 가공의 공정 능력을 향상시키기 위해 DMAIC(정의-측정-분석-개선-관리) 접근 방식을 적용했습니다. Ishikawa 다이어그램과 공정 고장 모드 분석을 활용하여 공정 능력 지수(Cp, Cpk, Cpm)에서 상당한 개선을 달성했습니다.
- 승용차 알로이 휠의 정적 응력 분석: Nallusamy et al. [25]은 정적 응력 분석을 사용하여 알로이 휠의 품질과 안전성을 개선하고 A356 합금과 T6 열처리를 사용했습니다. 그들의 연구는 테스트 생산성을 향상시키기 위해 동적 코너링 피로 테스트를 최적화하는 데 중점을 두었습니다.
- 알루미늄 합금 휠의 강성 최적화: Kocaturk et al. [26]은 알루미늄 합금 휠의 강성 매개변수에 대한 최적화 절차를 제시하고 유한 요소 시뮬레이션에는 ANSYS Workbench를, 통계 분석에는 Minitab을 활용했습니다. 그들의 연구는 질량 증가를 최소화하면서 강성을 최대화하는 것을 목표로 했습니다.
- 자동차 휠 제조를 위한 합금 특성 분석: Kaba et al. [27]은 합금 특성을 분석하여 AlSi7Mg0.3 및 AlSi5Mg0.3 합금을 비교했습니다. 그들은 AlSi5Mg0.3이 더 작은 결정립을 나타내는 반면, AlSi7Mg0.3은 우수한 기계적 특성과 유동성을 제공하여 산업 응용 분야에 유리하다는 것을 발견했습니다.
- 알루미늄 합금 휠의 내부 림 압축 시험 시뮬레이션: Kara와 Daysal [28]은 ABAQUS를 사용하여 내부 림 압축 테스트에 대한 시뮬레이션을 개발하고 시뮬레이션 결과를 실험 데이터와 비교하여 휠 안전을 보장하는 데 중요한 파괴 및 파손 거동을 평가했습니다.
- 6061 알루미늄 합금 휠의 단조 공정 분석: Kim et al. [29]은 유한 요소법을 사용하여 6061 알루미늄 합금 휠의 단조 공정을 분석하고, 고온에서 금속 성형을 시뮬레이션하고 공정 조건을 최적화하기 위해 열-기계 모델과 강성 점소성(rigid visco-plasticity)을 통합했습니다.
- A356 알루미늄 합금 휠의 저압 다이캐스트(LPDC) 공정의 3차원 열 모델 개발: Zhang et al. [30]은 광범위한 온도 측정으로 검증된 ABAQUS를 사용하여 LPDC 공정에 대한 3차원 열 모델을 개발했습니다. 이 모델은 복잡한 열 흐름 경로와 핫스팟을 식별하여 생산 능력 향상을 위한 공정 최적화를 지원합니다.
- 알루미늄 합금의 정밀 단조 기술: Deng et al. [31]은 알루미늄 합금에 대한 정밀 단조 기술을 검토하여 변형 특성과 관련된 문제를 극복하고 정밀 형상을 달성하기 위해 밀폐 단조 및 등온 단조와 같은 고급 기술을 강조했습니다.
- 알루미늄 합금 휠의 균열 현상에 대한 유한 요소 시뮬레이션 및 실험적 검증: Otarawanna et al. [32]은 휠 충격 테스트 중 균열 현상을 예측하기 위해 유한 요소 해석을 사용하고 FEA 모델을 실험 결과와 비교하여 설계 시간과 비용을 절감했습니다.
- 저압 다이캐스팅 중 알루미늄 합금 자동차 휠의 기공률에 대한 냉각 공정의 영향: Sui et al. [33]은 저압 다이캐스팅에서 기공률에 대한 냉각 공정의 영향을 조사했습니다. 수치 시뮬레이션과 실험을 통해 전략적 냉각 및 단열이 중요한 영역에서 미세기공 결함을 줄일 수 있음을 입증했습니다.
제시된 데이터 분석:
검토된 연구들은 알로이 휠 제조 공정을 최적화하고 향상시키기 위해 전산 시뮬레이션 및 분석 도구에 대한 의존도가 증가하고 있음을 종합적으로 강조합니다. 주조 및 단조에서 가공 및 재료 선택에 이르기까지 유한 요소 해석, 열 모델링 및 공정 시뮬레이션은 결함 식별 및 완화, 공정 효율성 개선, 제품 품질 및 안전성 보장에 중요한 역할을 합니다. 제시된 데이터는 연구자들이 수치적 및 실험적 방법론을 모두 활용하여 알로이 휠 생산의 과제를 해결하기 위해 다각적인 접근 방식을 취하고 있음을 강조합니다.
그림 목록:
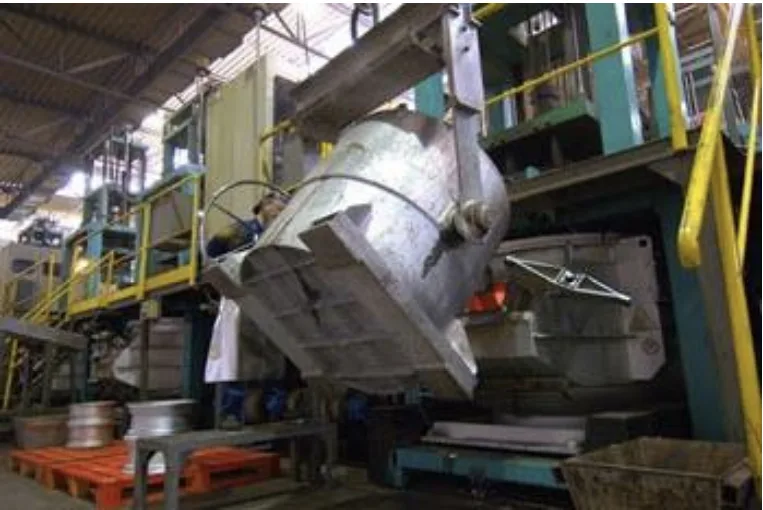
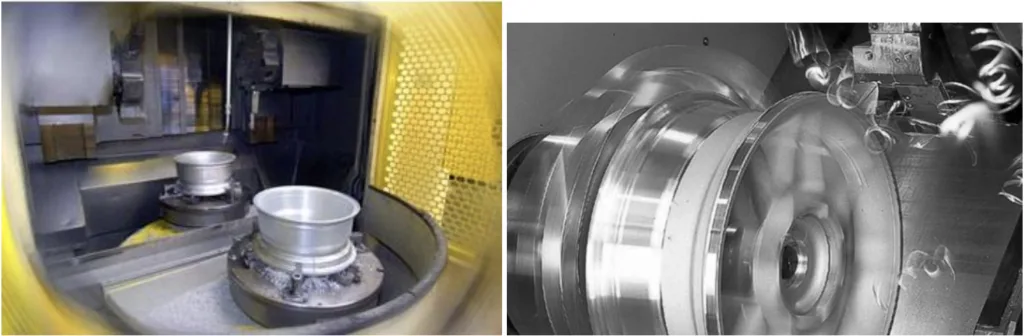
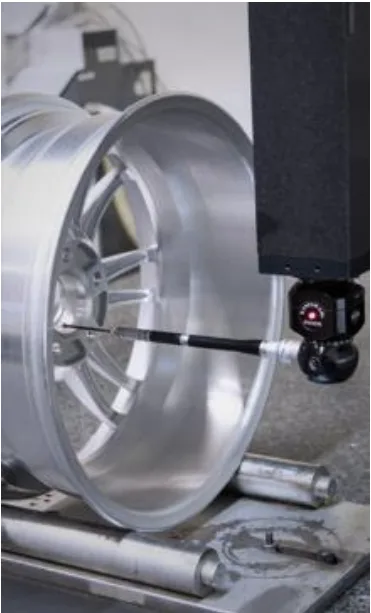
![Fig. 5. CAD models of casting molds for an aluminum disc wheel [22]](https://castman.co.kr/wp-content/uploads/image-655-png.webp)
![Fig. 6. The finite element model of an aluminum wheel and its molds [22].
Temperature distributions of mold during the casting process is shown in the figure 5.](https://castman.co.kr/wp-content/uploads/image-656-1024x377.webp)
![Fig. 7. Temperature distributions of mold during the casting process [22].](https://castman.co.kr/wp-content/uploads/image-657-png.webp)
![Fig. 8. Alloy wheel machining drawing with center hole diameter of ø50.000 (±0.050) [24].](https://castman.co.kr/wp-content/uploads/image-658-1024x551.webp)
![Fig. 12. Contour of the von Mises stress obtained from the simulation without the tire at 850 kg. Arrows mark the location where the von Mises stress is maximum (ignoring the direct impact region) [32].](https://castman.co.kr/wp-content/uploads/image-659-1024x545.webp)
![Fig. 13. Effect of the cooling and insulation process in removing the macroporosity defects in the junctions of prodcuced alloy wheels [33].](https://castman.co.kr/wp-content/uploads/image-660-1024x295.webp)
- Fig. 1. 주조 작업을 위한 용융 합금 제공 (Providing the molten alloys for the casting operation).
- Fig. 2. 휠 합금의 주조 작업 (Casting operation of wheel alloys).
- Fig. 3. 휠 합금의 가공 작업 (Machining operations of wheel alloys).
- Fig. 4. CMM을 사용한 생산된 알로이 휠의 품질 관리 (Quality control of produced alloy wheels using the CMM).
- Fig. 5. 알루미늄 디스크 휠용 주조 금형의 CAD 모델 [22] (CAD models of casting molds for an aluminum disc wheel [22]).
- Fig. 6. 알루미늄 휠 및 금형의 유한 요소 모델 [22] (The finite element model of an aluminum wheel and its molds [22]).
- Fig. 7. 주조 공정 중 금형의 온도 분포 [22] (Temperature distributions of mold during the casting process [22]).
- Fig. 8. 중심 구멍 직경 ø50.000 (±0.050)의 알로이 휠 가공 도면 [24] (Alloy wheel machining drawing with center hole diameter of ø50.000 (±0.050) [24]).
- Fig. 9. 단조 직후의 휠 구성 [29] (Wheel configuration just after forging [29]).
- Fig. 10. 휠 및 다이의 30° 단면 메쉬 (다이에 비해 미세 메쉬 크기로 차별화된 휠) [30] (30° section mesh of a wheel and die (wheel differentiated by fine mesh size compared to die) [30]).
- Fig. 11. (a) 휠 및 (b) 다이의 다이 오픈 전 온도 등고선 플롯 [30] (Contour plot of temperatures in the (a) wheel and (b) die prior to die-open [30]).
- Fig. 12. 850kg에서 타이어 없이 시뮬레이션에서 얻은 폰 미세스 응력 등고선. 화살표는 폰 미세스 응력이 최대인 위치를 표시합니다 (직접 충격 영역 무시) [32] (Contour of the von Mises stress obtained from the simulation without the tire at 850 kg. Arrows mark the location where the von Mises stress is maximum (ignoring the direct impact region) [32]).
- Fig. 13. 생산된 알로이 휠 접합부에서 거시적 기공 결함을 제거하는 냉각 및 단열 공정의 효과 [33] (Effect of the cooling and insulation process in removing the macroporosity defects in the junctions of prodcuced alloy wheels [33]).
7. 결론:
주요 연구 결과 요약:
본 연구에서는 알로이 휠의 제조 공정을 포괄적으로 검토하고 공정 최적화 및 개선을 목표로 하는 최근 연구를 강조했습니다. 연구 결과는 알로이 휠 생산 발전에 있어 컴퓨터 시뮬레이션 및 분석의 중추적인 역할을 일관되게 강조합니다. 연구 노력은 자동차 알루미늄 합금 주조의 결함 완화, 가공 효율성 개선, 정적 응력 분석을 통한 구조적 무결성 보장, 휠 강성 최적화 및 고급 합금 재료 탐색에 크게 집중되어 있습니다. 저압 다이캐스팅의 열 모델링과 단조 기술의 발전 또한 중요한 관심 영역입니다. 저압 다이캐스팅의 냉각 방법론은 생산 부품의 품질을 향상시키는 데 중요한 것으로 확인되었습니다.
연구의 학술적 의의:
본 검토는 알로이 휠 제조 분야의 현재 학술 연구 동향에 대한 귀중한 종합 정보를 제공합니다. 이는 제조 문제를 해결하고 공정 이해를 개선하기 위해 가상 시뮬레이션 및 분석 기술을 활용하는 데 학계가 집중하고 있음을 강조합니다. 본 연구는 최첨단 기술을 이해하고 이 분야에서 잠재적인 미래 연구 방향을 식별하려는 연구자에게 통합된 자료 역할을 합니다.
실용적 의미:
검토된 연구의 실용적 의미는 알로이 휠 제조 산업에 상당한 영향을 미칩니다. 본 연구는 제조업체가 생산 공정을 개선하고 제품 품질을 향상시키며 운영 효율성을 개선하기 위한 실행 가능한 통찰력과 방법론을 제공합니다. 가상 시뮬레이션 및 최적화 기술에 대한 강조는 공정 개발 및 품질 관리를 위한 비용 효율적이고 시간 절약적인 접근 방식을 제공하여 제조 결과에서 상당한 개선을 가져올 수 있습니다.
연구의 한계 및 향후 연구 분야:
검토 논문으로서 본 연구는 본질적으로 기존 출판된 연구에 의존하며 독창적인 실험적 검증을 포함하지 않는다는 한계가 있습니다. 향후 연구는 실제 제조 환경에서 요약된 기술의 산업적 구현 및 검증에 초점을 맞춰야 합니다. 새로운 최적화 알고리즘, 고급 시뮬레이션 방법론 및 알로이 휠 제조에 Industry 4.0 기술을 통합하는 것에 대한 추가 탐색도 향후 연구를 위한 권장 영역입니다.
8. 참고 문헌:
- 1. Soori M, Arezoo B, Habibi M (2017) Accuracy analysis of tool deflection error modelling in prediction of milled surfaces by a virtual machining system. International Journal of Computer Applications in Technology 55 (4):308-321
- 2. Soori M, Arezoo B, Habibi M (2014) Virtual machining considering dimensional, geometrical and tool deflection errors in three-axis CNC milling machines. Journal of Manufacturing Systems 33 (4):498-507
- 3. Soori M, Arezoo B, Habibi M (2013) Dimensional and geometrical errors of three-axis CNC milling machines in a virtual machining system. Computer-Aided Design 45 (11):1306-1313
- 4. Soori M, Arezoo B, Habibi M (2016) Tool deflection error of three-axis computer numerical control milling machines, monitoring and minimizing by a virtual machining system. Journal of Manufacturing Science and Engineering 138 (8)
- 5. Soori M, Arezoo B (2020) Virtual Machining Systems for CNC Milling and Turning Machine Tools: A Review. International Journal of Engineering and Future Technology 18 (1):56-104
- 6. Soori M, Arezoo B A Review in Machining-Induced Residual Stress.
- 7. Soori M, Arezoo B (2022) NURBS Interpolation Algorithm to Minimize Chord Error in 5-Axis CNC Milling Operations of Turbine Blades.
- 8. Soori M (2019) Virtual product development. GRIN Verlag,
- 9. Dastres R, Soori M (2021) Advances in Web-Based Decision Support Systems. International Journal of Engineering and Future Technology
- Dastres R, Soori M (2021) A Review in Recent Development of Network Threats and Security Measures. International Journal of Computer and Information Engineering 15 (1):75-81
- Dastres R, Soori M (2021) Artificial Neural Network Systems. International Journal of Imaging and Robotics (IJIR) 21 (2):13-25
- Dastres R, Soori M (2021) A Review in Advanced Digital Signal Processing Systems. International Journal of Electrical and Computer Engineering 15 (3):122-127
- Soori M, Asmael M, Solyalı D (2020) Recent Development in Friction Stir Welding Process: A Review. SAE International Journal of Materials and Manufacturing (5):18
- Soori M, Asmael M (2021) Virtual Minimization of Residual Stress and Deflection Error in Five-Axis Milling of Turbine Blades. Strojniski Vestnik/Journal of Mechanical Engineering 67 (5):235-244
- Soori M, Asmael M (2021) Cutting temperatures in milling operations of difficult-to-cut materials. Journal of New Technology and Materials 11 (1):47-56
- Soori M, Asmael M, Khan A, Farouk N (2021) Minimization of surface roughness in 5-axis milling of turbine blades. Mechanics Based Design of Structures and Machines:1-18. doi:10.1080/15397734.2021.1992779
- Soori M, Asmael M (2021) MINIMIZATION OF DEFLECTION ERROR IN FIVE AXIS MILLING OF IMPELLER BLADES. Facta Universitatis, series: Mechanical Engineering. doi:10.22190/FUME2108220695
- Soori M, Asmael M (2022) A Review of the Recent Development in Machining Parameter Optimization. Jordan Journal of Mechanical & Industrial Engineering 16 (2):205-223
- Dastres R, Soori M, Asmael M (2022) RADIO FREQUENCY IDENTIFICATION (RFID) BASED WIRELESS MANUFACTURING SYSTEMS, A REVIEW. Independent Journal of Management & Production 13 (1):258-290
- Dastres R, Soori M (2021) Advances in Web-Based Decision Support Systems. International Journal of Engineering and Future Technology 19 (1):1-15
- Dastres R, Soori M (2021) The Role of Information and Communication Technology (ICT) in Environmental Protection. International Journal of Tomography and Simulation 35 (1):24-37
- Hsu Y-L, Yu C-C (2006) Computer simulation of casting process of aluminium wheels-a case study. Proceedings of the Institution of Mechanical Engineers, Part B: Journal of Engineering Manufacture 220 (2):203-211
- Zhang B, Cockcroft S, Maijer D, Zhu J, Phillion A (2005) Casting defects in low-pressure die-cast aluminum alloy wheels. Jom 57 (11):36-43
- Sharma G, Rao PS, Babu BS (2018) Process capability improvement through DMAIC for aluminum alloy wheel machining. Journal of Industrial Engineering International 14 (2):213-226
- Nallusamy S, Prabu NM, Balakannan K, Majumdar G Analysis of Static Stress in an Alloy Wheel of the Passengercar. In: International Journal of Engineering Research in Africa, 2015. Trans Tech Publ, pp 17-25
- Kocaturk O, Elagoz FY, Kara A Optimization of Rigidity of Aluminum Alloy Wheels. In: Fracture, Fatigue and Wear, 2018. Springer, pp 814-819
- Kaba M, Donmez A, Cukur A, Kurban A, Cubuklusu H, Birol Y (2018) AlSi5Mg0. 3 Alloy for the manufacture of automotive wheels. International Journal of Metalcasting 12 (3):614-624
- Kara A, Daysal O Simulation of Inner Rim Compression Test of Aluminum Alloy Wheels. In: Key Engineering Materials, 2018. Trans Tech Publ, pp 379-384
- Kim Y, Ryou T, Choi H, Hwang B (2002) An analysis of the forging processes for 6061 aluminum-alloy wheels. Journal of Materials Processing Technology 123 (2):270-276
- Zhang B, Maijer D, Cockcroft S (2007) Development of a 3-D thermal model of the low-pressure die-cast (LPDC) process of A356 aluminum alloy wheels. Materials Science and Engineering: A 464 (1-2):295-305
- Deng L, Wang X, Jin J, Xia J (2018) Precision forging technology for aluminum alloy. Frontiers of Mechanical Engineering 13 (1):25-36
- Otarawanna S, Uttamung P, Malatip A Finite element simulation and experimental validation of the cracking phenomenon in aluminium alloy wheels during the impact test. In: AIP Conference Proceedings, 2018. vol 1. AIP Publishing LLC, p 020303
- Sui D, Cui Z, Wang R, Hao S, Han Q (2016) Effect of cooling process on porosity in the aluminum alloy automotive wheel during low-pressure die casting. International Journal of Metalcasting 10 (1):32-42
9. 저작권:
- 본 자료는 "Mohsen Soori"의 논문: "Manufacturing Processes of Car Alloy Wheels"를 기반으로 합니다.
- 논문 출처: https://hal.science/hal-03740879v1
본 자료는 상기 논문을 요약한 것으로, 상업적 목적으로 무단 사용하는 것을 금지합니다.
Copyright © 2025 CASTMAN. All rights reserved.