본 논문 요약은 Conference Tools for Materials Science & Technology (MSE 2010)에서 발표된 논문 "Numerical determination of process parameters for fabrication of automotive component"을 기반으로 작성되었습니다.
1. 개요:
- 제목: 자동차 부품 제작을 위한 공정 변수의 수치적 결정 (Numerical determination of process parameters for fabrication of automotive component)
- 저자: 모하마드 사데기 (Mohammad Sadeghi), 자파르 마흐무디 (Jafar Mahmoudi)
- 발행 연도: 2010년
- 발행 학술지/학회: Conference Tools for Materials Science & Technology (MSE 2010)
- 키워드: 고압 다이캐스팅 (High pressures die casting), 공정 변수 (process parameters), 결함 (defect), Al 합금 (Al alloy), ProCast
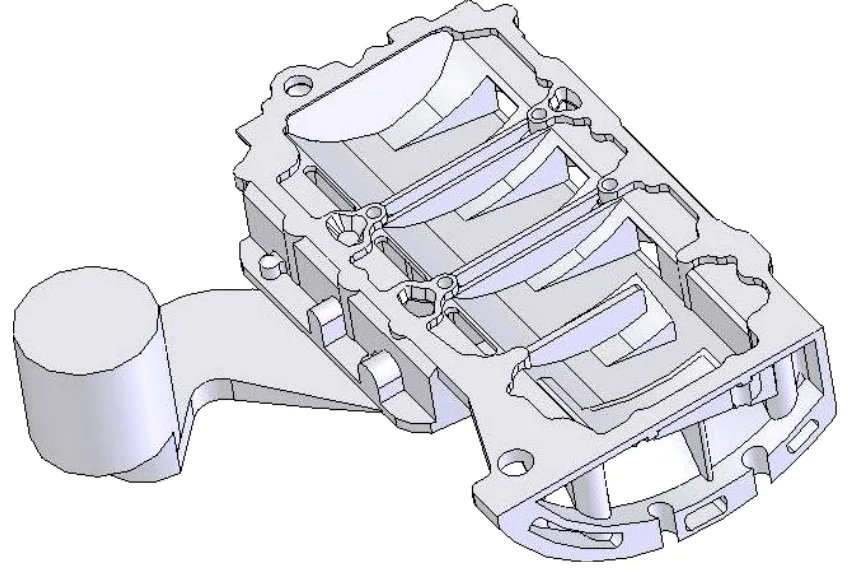
2. 연구 배경:
- 연구 주제의 사회적/학문적 맥락: 콜드 셧 (cold shut) 형성, 공기 및 가스 혼입, 개재물과 같은 주조 결함은 다이캐스팅에서 피할 수 없는 과제입니다. 전통적으로 이러한 결함 제어는 주조 엔지니어의 경험에 크게 의존해 왔습니다. 냉각 속도는 주조 결함 형성에 영향을 미치는 중요한 요인으로 인식되고 있습니다.
- 기존 연구의 한계: 기존의 게이팅 시스템 설계 및 다이캐스팅 공정 변수 최적화 방법은 종종 개인적인 지식과 시행착오에 기반합니다. 형상 및 사양에 따른 권장 사항이 존재하지만, 보다 체계적이고 최적화된 접근 방식이 필요합니다.
- 연구의 필요성: 수치 시뮬레이션은 주조 공정 중 발생하는 물리적 현상을 분석하는 강력한 도구를 제공하며, 실제 주조 공정에서 쉽게 관찰할 수 없는 유체 흐름, 열 전달 및 응고에 대한 통찰력을 제공합니다. 본 연구는 컴퓨터 시뮬레이션을 활용하여 다이캐스팅 공정 변수를 최적화하고, 스크랩을 줄이고, 에너지 소비를 최소화하며, 주조 품질을 향상시키는 것을 목표로 합니다.
3. 연구 목적 및 연구 질문:
- 연구 목적: 본 연구의 주요 목적은 고압 다이캐스팅 (HPDC) 공정에서 용융 금속의 흐름과 다이 온도가 냉각 속도 및 후속 주조 결함에 미치는 영향을 분석하는 것입니다. 본 연구는 결함을 최소화하기 위한 최적의 다이 온도를 결정하기 위해 이란 자동차 부품에 초점을 맞춥니다.
- 주요 연구 질문:
- 연구 대상 자동차 부품에서 주조 결함을 최소화하기 위한 다이캐스팅 최적 다이 온도는 무엇입니까?
- 다이 온도 변화는 다이캐스팅 공정 중 용융 금속 흐름 패턴과 냉각 속도에 어떤 영향을 미칩니까?
- 연구 가설: 본 연구는 다이 온도가 HPDC에서 주조 결함 형성에 상당한 영향을 미치는 중요한 공정 변수이며, 수치 시뮬레이션을 통해 최적의 다이 온도 범위를 효과적으로 식별할 수 있다는 가설을 암묵적으로 설정합니다.
4. 연구 방법론
- 연구 설계: 본 연구는 수치 시뮬레이션과 실험적 검증의 결합된 접근 방식을 채택합니다.
- 자료 수집 방법:
- 시뮬레이션: 유한 요소 (FE) 법 기반 ProCast 소프트웨어를 사용하여 다이캐스팅 공정을 시뮬레이션했습니다. 다른 변수를 일정하게 유지하면서 세 가지 다이 온도 (15°C, 20°C, 25°C)를 시뮬레이션했습니다. A380 알루미늄 합금에 대한 재료 속성은 소프트웨어 데이터베이스에서 가져왔습니다.
- 실험: IDRA1600 다이캐스팅 기계를 사용하여 용융 금속을 주입했습니다. 충전 시간은 스톱워치를 사용하여 측정했습니다. 응고 시간은 다른 시간에 금형을 꺼내어 결정했습니다. 다이 온도는 주입 직전에 Minolta/Land Cyclops 152 적외선 온도계를 사용하여 측정했습니다. 수축을 분석하기 위해 주조물을 횡단면으로 절단했습니다.
- 분석 방법: 시뮬레이션 결과를 실험 관찰과 비교하여 모델을 검증했습니다. 분석은 흐름 패턴, 온도 분포, 시뮬레이션에서 예측된 결함 위치, 실험 주조물에서 관찰된 결함에 초점을 맞췄습니다.
- 연구 대상 및 범위: 본 연구는 A380 알루미늄 합금으로 제작된 "Ladder frame"이라는 자동차 부품 (그림 1)에 초점을 맞췄습니다. 본 연구는 고압 다이캐스팅을 사용하여 이 특정 부품의 주조 결함에 대한 다이 온도 효과를 조사했습니다.
5. 주요 연구 결과:
- 주요 연구 결과: 본 연구는 자동차 부품 다이캐스팅에 적합한 다이 온도가 20°C에서 25°C 사이임을 발견했습니다. 15°C의 다이 온도는 적절하지 않은 것으로 나타났습니다.
- 통계적/질적 분석 결과:
- 충전 시간: 시뮬레이션에서 예측된 충전 시간은 약 0.12초로, 실험 관찰과 일치했습니다.
- 결함 예측: 15°C 다이 온도에서 시뮬레이션 결과, 최종 충전 위치에서 용융 온도가 액상선 온도 근처로 떨어져 콜드 셧 및 불량 충전으로 이어질 가능성이 있는 것으로 나타났습니다 (그림 3). 실험 결과는 15°C 다이 온도에서 이러한 영역에서 주조 결함이 관찰되어 이 예측을 검증했습니다 (그림 3, 그림 6).
- 응고 패턴: 시뮬레이션 결과, 응고는 단면이 더 얇기 때문에 부품 중앙에서 시작하여 바깥쪽으로 진행되는 것으로 나타났습니다. 이 패턴은 실험에서 주조물의 바깥쪽에서 관찰된 기공 형성 (porosity formation)과 일치했습니다 (그림 5, 그림 6).
- 자료 해석: 낮은 다이 온도 (15°C)는 용융 온도를 크게 떨어뜨려 콜드 셧 및 불완전 충전의 위험을 증가시킵니다. 더 높은 다이 온도 (20°C 및 25°C)는 용융 금속의 유동성을 더 오래 유지시켜 충전을 개선하고 결함을 줄입니다.
- 그림 목록:
- 그림 1: 시뮬레이션에 사용된 Ladder frame 부품의 형상
- 그림 2: 충전 패턴 (filling pattern)
- 그림 3: 최종 충전 위치 (final filling position)
- 그림 4: 런너에서 충전 초기 단계의 공기 혼입 위치 (entrapment of air site)
- 그림 5: 응고 패턴 (Solidification patterns)
- 그림 6: 최종 응고 위치 (final solidification positions)
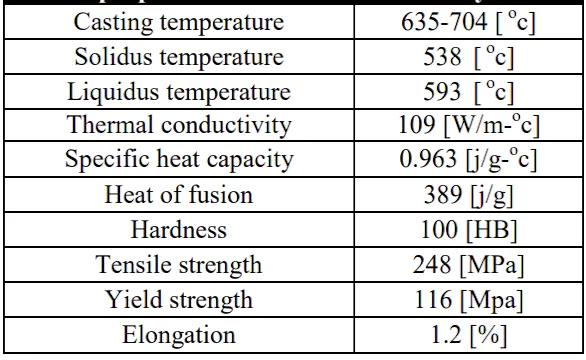
![Table 2: chemical composition of A380
aluminum alloy [wt. %]](https://castman.co.kr/wp-content/uploads/image-289-png.webp)
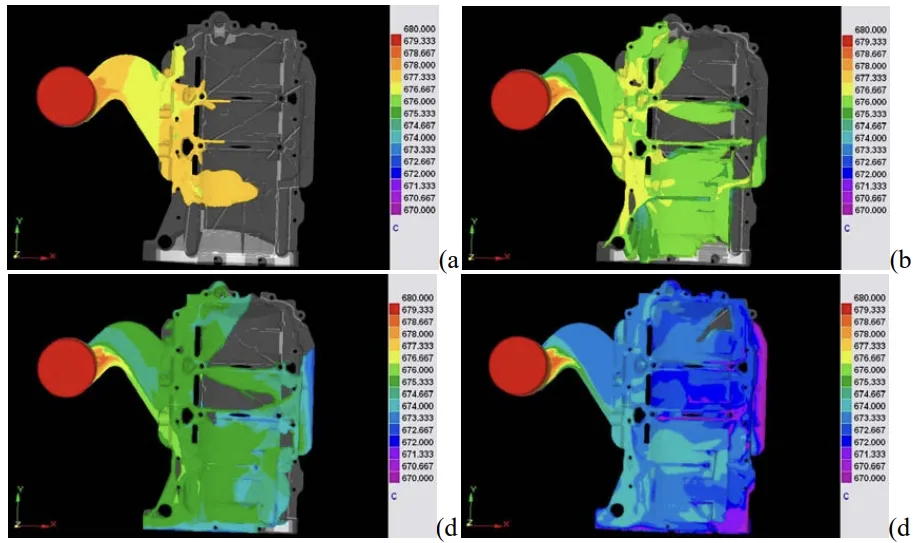
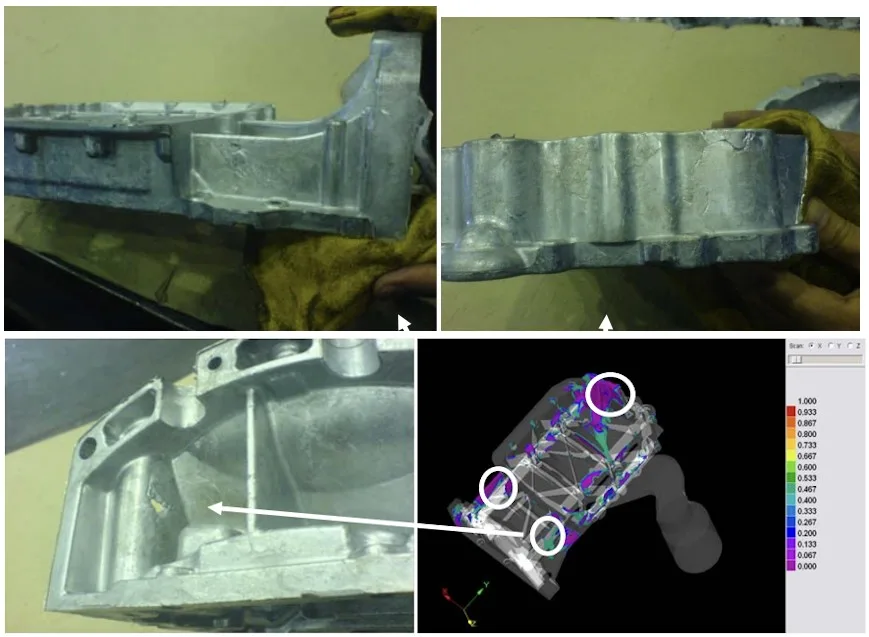
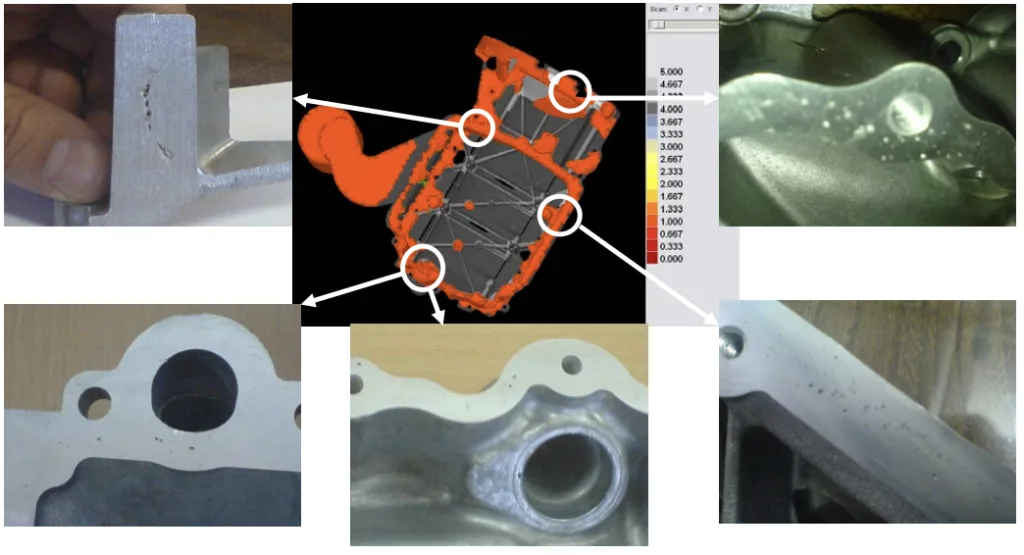
6. 결론 및 논의:
- 주요 결과 요약: 본 연구는 ProCast 소프트웨어를 사용한 수치 시뮬레이션을 성공적으로 활용하여 A380 알루미늄 합금으로 제작된 자동차 Ladder frame 부품의 고압 다이캐스팅에 대한 최적의 다이 온도를 결정했습니다. 본 연구는 이 부품에 적합한 다이 온도가 20°C에서 25°C 범위이며, 15°C는 불충분하고 주조 결함을 유발한다는 결론을 내렸습니다. 시뮬레이션 결과는 실험적 결과에 의해 검증되어 양호한 일치를 보였습니다.
- 연구의 학문적 의의: 본 연구는 수치 시뮬레이션이 다이캐스팅 공정 변수, 특히 다이 온도를 최적화하는 데 유용한 도구임을 강조합니다. 시뮬레이션이 주조 결함을 예측하고 공정 변수가 용융 금속 흐름 및 응고 거동에 미치는 영향을 이해하는 능력을 입증합니다.
- 실용적 의미: 본 연구 결과는 주조 엔지니어가 다이캐스팅 공정을 최적화하는 데 실질적인 지침을 제공합니다. 엔지니어는 시뮬레이션 도구를 사용하여 특정 부품 및 재료에 적합한 다이 온도 범위를 결정하여 주조 결함을 줄이고, 주조 품질을 개선하며, 잠재적으로 스크랩률과 에너지 소비를 낮출 수 있습니다.
- 연구의 한계: 본 연구는 단일 자동차 부품 (Ladder frame) 및 A380 알루미늄 합금으로 제한됩니다. 또한, 본 연구는 자동 몰딩 시스템 사용과 관련된 한계를 지적하며, 이는 미세 수축 (micro-shrinkage) 문제를 해결하기 위한 냉각 시스템 구현을 방해했습니다.
7. 향후 후속 연구:
- 후속 연구 방향: 향후 연구에서는 주조 부품의 품질에 대한 다른 중요한 주조 변수의 영향을 탐구해야 합니다. 이러한 변수는 다음과 같습니다.
- 용융 과열 (melt superheat)
- 주입 시간 (속도) (pouring time (velocity))
- 금형 표면 거칠기 (mould surface roughness)
- 게이팅 설계 (gating design)
- 금형 구성 (mould configuration)
시뮬레이션을 사용한 이러한 변수에 대한 추가 조사는 다이캐스팅 공정에 대한 보다 포괄적인 이해를 제공하고 품질 및 효율성 향상을 위한 추가 최적화를 가능하게 할 수 있습니다.
8. 참고 문헌:
- [1] M. Merlin, G. Timelli, F. Bonollo, G. L. Garagnania” Impact behaviour of A356 alloy for low-pressure die casting automotive wheels” J. Mater. Pro. Tech. Vol. 209 (2009), pp1060-1073.
- [2] M. Dargusch, M. Nave, P.McKinney “Porosity Reduction in a HighPressure Die Casting ThroughThe Use of Squeeze Pins” NADCA (2003), pp405-412.
- [3] J.X. Zhou, L.L. Chen, D.M. Liao, R.X. Liu: J. Mater. Pro. Tech. Vol. 192–193 (2007), pp 249-254.
- [4] Z. Sun, H. Hu, X. Chen: J. Mater. Pro. Tech. Vol. 199 (2008), pp256–264.
- [5] “FAILURES OF DIES FOR DIE-CASTING OF ALUMINIUM ALLOYS”, METABK 47(1) 51-55, 2008.
- [6] A. Kermanpur, Sh. Mahmoudi, A. Hajipour, “Numerical simulation of metal flow and solidification in the multi-cavity casting moulds of automotive components”, J. Mater. Pro. Tech. Vol. 206 (2008), pp62-68.
- [7] D. McBride, T.N. Croft, M. Cross: Computers & Fluids, Vol.37 (2008), pp170–180.
- [8] Z. Brown, C. Barnes, J. Bigelow - Contech U.S., Kalamazoo “Squeeze cast automotive applications and design considerations", 4Th International Conference High Tech Die Casting 9-10 April 2008, Montichiari, Italy.
- [9] V. Ilotte “ Die casting for chassis components" 4Th International Conference High Tech Die Casting 9-10 April 2008, Montichiari Italy.
- [10] G. Timelli, F. Grosselle, F. Voltazza, E. Della Corte “A new reference die for mechanical properties evaluation in diecasting Part 1 - Design and process optimization" 4Th International Conference High Tech Die Casting 9-10 April 2008, Montichiari Italy.
- [11] B.S. Sung, I.S. Kim “The molding analysis of automobile parts using the die-casting system” J. Mater. Pro. Tech. Vol. 201 (2008), pp635–639.
- [12] Z. GUO, S. XIONG, S.H. Cho, J.-K. Choi, “Heat Transfer between Casting and Die during High Pressure Die Casting Process of AM50 Alloy-Modeling and Experimental Results”, J. Mater. Sci. Technol. Vol.24 (2008), pp131-135.
- [13] G. Muneratti “Role, functions and heat transfer of die coating in the aluminum die casting process" 4th International Conference High Tech Die Casting 9-10 April 2008, Montichiari Italy.
- [14] P. J. Pearson, “Contact heat transfer coefficients in aluminum alloy die casting: an experimental and numerical investigation” PhD thesis, Ohio State University, 1994.
9. 저작권:
본 자료는 모하마드 사데기 (Mohammad Sadeghi), 자파르 마흐무디 (Jafar Mahmoudi)의 논문 "Numerical determination of process parameters for fabrication of automotive component"을 기반으로 합니다.
논문 출처: http://urn.kb.se/resolve?urn=urn:nbn:se:mdh:diva-22917
본 자료는 위 논문을 기반으로 요약되었으며, 상업적 목적으로 무단 사용하는 것을 금지합니다.
Copyright © 2025 CASTMAN. All rights reserved.