본 논문 요약은 ['Design and Analysis of Pressure Die Casting Die for Automobile Component'] 논문을 기반으로 작성되었으며, ['Global Journal of Researches in Engineering: A Mechanical and Mechanics Engineering']에 발표되었습니다.
1. 개요:
- 제목: 자동차 부품용 압력 다이캐스팅 금형 설계 및 해석 (Design and Analysis of Pressure Die Casting Die for Automobile Component)
- 저자: Y. Abdulfatah Abdu, T. M. Shafii, K. K. Dubey & Prof U. K. Gupta
- 발행 연도: 2016년
- 발행 저널/학회: Global Journal of Researches in Engineering: A Mechanical and Mechanics Engineering
- 키워드: 압력 다이캐스팅, 자동차 산업, 알루미늄 합금, 솔리드웍스, 3차원 유동, 프로 엔지니어 (pressure die casting, automobile industry, aluminium alloys, solid works, 3-diamensional flow, pro-engineer)
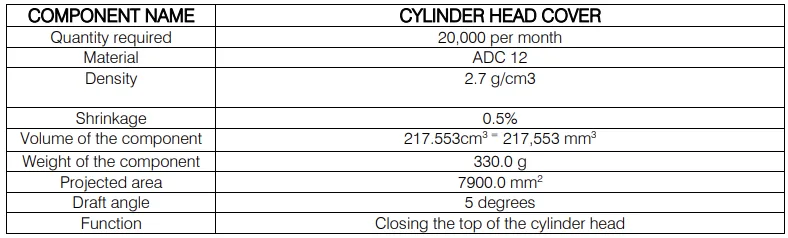
2. 연구 배경:
연구 주제 배경:
본 논문은 압력 다이캐스팅 공정 기술의 금형 설계 및 해석 방법 중 하나를 다룹니다. 압력 다이캐스팅은 정밀 공차를 유지하고, 모든 기계 가공을 줄이며, 소량 생산에 최적의 선택이 될 수 있도록 하는 공정입니다. 경량 설계와 정밀 제품을 특징으로 하는 부품은 자동차 산업의 주요 요구 사항 중 하나이며, 자동차의 연비에 직접적인 영향을 미쳐 사용자 만족도를 높입니다. 이러한 요구 사항은 알루미늄 합금, 고강도 강철 및 섬유 강화 복합재와 같은 재료를 사용하여 충족됩니다.
기존 연구 현황:
기존 연구에 따르면 다이캐스팅에는 냉간 충진, 드로스 및 알루미나 스킨과 같은 주조 결함이 흔히 발생합니다. 연구들은 런너 및 스프루 설계가 피로 강도에 미치는 영향, 다이 설계의 리드 타임 및 사이클 타임을 단축하기 위한 통합 CAD/CAM 시스템, 그리고 구상 흑연 주철로 만들어진 중요한 자동차 부품인 프론트 액슬 하우징에서 수축 및 가스 기공과 같은 결함에 대한 게이팅 시스템 설계의 영향을 탐구했습니다. 또한, 이젝터, 다이 베이스 및 게이팅 설계를 최적화하기 위한 컴퓨터 지원 다이 설계 시스템이 개발되었습니다. 불균일 냉각과 런너 및 게이팅 시스템 설계와의 상관관계도 유동 시뮬레이션을 사용하여 조사되었습니다.
연구의 필요성:
본 연구는 수축 공동, 가스 결함 및 재료 결함과 같은 압력 다이캐스팅의 결함을 최소화해야 할 필요성에 의해 시작되었습니다. 논문은 주조 공정의 모든 측면을 제어하고 낭비를 방지하기 위한 포괄적인 금형 설계 및 해석의 중요성을 강조합니다. 특히, 본 연구는 CAE (Computer Aided Engineering) 소프트웨어를 사용하여 금형을 설계하고 게이팅 시스템을 개발하여 이러한 결함을 식별하고 완화함으로써 주조 품질과 효율성을 향상시키는 것을 목표로 합니다.
3. 연구 목적 및 연구 질문:
연구 목적:
본 연구의 주요 목적은 자동차 부품용 압력 다이캐스팅 금형을 설계 및 해석하고, 주조 결함을 최소화하며 효율적인 생산을 위해 금형 설계를 최적화하는 것입니다. 이는 수축 공동, 가스 결함 및 주입 재료 결함과 같은 문제를 해결하기 위해 CAE 소프트웨어를 사용하여 금형 및 게이팅 시스템을 개발하는 것을 포함합니다.
핵심 연구 질문:
핵심 연구 목표는 다음과 같습니다:
- 주요 치수 및 충진 해석을 고려하여 자동차 부품용 압력 다이캐스팅 금형을 설계합니다.
- 주조 결함을 식별하고 최소화하기 위한 도구 및 게이팅 시스템을 개발합니다.
- 설계, 해석 및 테스트를 위해 CAE 소프트웨어 (솔리드웍스, 3차원 유동, 프로 엔지니어)를 활용합니다.
- 런너 시스템 설계, 냉각 시스템 및 공정 매개변수를 포함하여 다이캐스팅을 위한 최적의 매개변수를 결정합니다.
연구 가설:
본 논문에서는 명시적인 연구 가설을 제시하지 않지만, 다음과 같은 암묵적인 가설을 추론할 수 있습니다:
- CAE 소프트웨어로 해석된 적절하게 설계된 금형 및 게이팅 시스템은 자동차 부품의 주조 결함을 크게 줄일 것입니다.
- 최적화된 런너 및 게이팅 시스템 설계는 다이 캐비티의 완전하고 균형 잡힌 충진을 보장하여 주조 품질을 향상시킬 것입니다.
- CAE 소프트웨어 시뮬레이션은 잠재적인 주조 결함을 정확하게 예측하고 완화하는 데 도움이 되어 보다 효율적인 금형 설계 프로세스를 가능하게 합니다.
4. 연구 방법론
연구 설계:
본 연구는 CAE 소프트웨어를 활용하여 압력 다이캐스팅 공정을 시뮬레이션하고 최적화하는 설계 및 해석 방법론을 채택합니다. 설계 프로세스는 부품 식별 및 데이터 수집부터 솔리드웍스 소프트웨어를 사용한 3차원 모델링 및 2차원 도면 작성에 이르기까지 여러 단계를 포함합니다. 설계는 재료 수축률을 고려하고 런너 시스템 설계 및 충진 해석을 위해 3차원 유동 해석을 사용합니다.
자료 수집 방법:
본 연구는 주로 이론적 계산과 CAE 소프트웨어 시뮬레이션을 자료 생성 방법으로 활용합니다. 부품 상세 정보, 재료 속성 (ADC 12 알루미늄 합금) 및 80T 기계 사양은 설계 계산 및 시뮬레이션의 입력 매개변수로 사용됩니다. 본 논문에서는 실험적 자료 수집이 명시적으로 언급되지 않았습니다.
분석 방법:
분석 방법은 다음과 같습니다:
- 설계 계산: 캐비티 수, 톤수 요구량, 샷 무게, 충진 비율, 충진 시간, 건식 샷 유량, 금속 압력 및 런너 치수를 결정하기 위한 수동 계산. 이러한 계산은 확립된 다이캐스팅 원리 및 공식을 기반으로 합니다.
- 3차원 유동 시뮬레이션: "3차원 유동" 소프트웨어를 활용하여 수직 및 수평 부품 배열 모두에서 충진 공정을 시뮬레이션합니다. 이 분석은 용융 금속의 유동 거동을 시각화하고 기공과 같은 잠재적 결함을 식별하는 것을 목표로 합니다.
- P-Q² 다이어그램 분석: 게이팅 시스템 설계를 최적화하기 위해 금속 압력과 유량 간의 관계를 분석하기 위해 P-Q² 다이어그램을 사용합니다.
연구 대상 및 범위:
본 연구는 특정 자동차 부품인 ADC 12 알루미늄 합금으로 만들어진 "실린더 헤드 커버"용 압력 다이캐스팅 금형 설계에 중점을 둡니다. 범위는 게이팅 시스템 및 런너 설계, 냉각 시스템 고려 사항 및 시뮬레이션을 통한 결함 분석을 포함한 금형 설계 및 해석 측면에 국한됩니다. 설계 및 해석 작업은 하리아나 주 구르가온의 Automotive Private Limited에서 수행되었습니다.
5. 주요 연구 결과:
핵심 연구 결과:
주요 연구 결과는 최적화된 금형 설계 매개변수를 요약한 표 2 "결과 요약"에 요약되어 있습니다:
- 캐비티 수: 1
- 톤수 요구량: 80 T
- 샷 무게: 0.9kg
- 충진 비율: 0.6
- 충진 시간: 54 밀리초
- 최대 정적 압력: 838.02kgf/cm2
- 건식 샷 유량: 10,692.62 cm3/sec
- 최대 금속 압력: 131.5 kgf/cm2
- 최소 금속 압력: 51.4 kgf/cm2
- 유량: 4,834.5 cm3/sec
- 금속 압력 (P): 91.5 kgf/cm2
- 유량 (Q): 7,255.7 cm3/sec
- 게이트 면적: 69 mm2
- 게이트 길이: 23mm
- 런너 크기: L=86.7 mm2, D= 10.42mm, W= 20.84 mm
유동 시뮬레이션 분석 결과, 수평 부품 배열이 수직 배열보다 기공 결함률이 낮은 것으로 나타났습니다. 충진 패턴 시뮬레이션은 용융 알루미늄이 게이트로 들어가 0.5초 후에 캐비티를 효과적으로 채우기 시작하는 것을 보여주었습니다.
자료 해석:
설계 계산 및 시뮬레이션 결과는 실린더 헤드 커버용 압력 다이캐스팅 금형 제조를 위한 포괄적인 매개변수 세트를 제공합니다. P-Q² 다이어그램 분석 (그림 2.1) 및 유동 시뮬레이션 시각화 (그림 3.01 및 3.02)는 최적화된 설계 매개변수를 뒷받침합니다. 결과는 설계된 금형 및 게이팅 시스템이 결함을 최소화한 주조품을 생산할 수 있음을 시사합니다. 수평 부품 배열의 선택은 기공 감소로 인해 선호됩니다.
그림 목록:
- 그림 2.1: P-Q2 다이어그램
- 그림 2.1.1: 코어 인서트
- 그림 2.1.2: 캐비티 인서트
- 그림 2.1.3: 금형 캐비티 및 코어 어셈블리
- 그림 2.1.4: 조립된 금형 도구
- 그림 3.01: 부품의 수직 배열
- 그림 3.02: 부품의 수평 배열
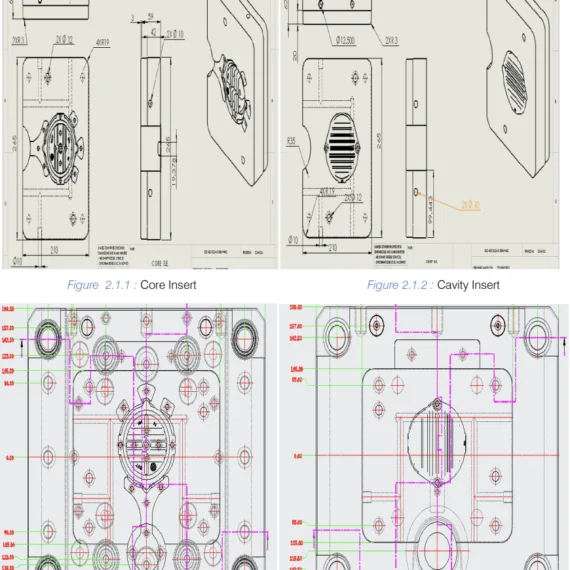
6. 결론:
주요 결과 요약:
본 연구는 CAE 소프트웨어를 사용하여 자동차 실린더 헤드 커버용 압력 다이캐스팅 금형을 성공적으로 설계하고 해석했습니다. 본 연구는 주조 결함을 최소화하기 위해 계산 및 유동 시뮬레이션을 통해 최적의 금형 설계 매개변수를 결정했습니다. 수평 부품 배열이 수직 배열에 비해 기공을 줄이는 데 더 우수한 것으로 나타났습니다. 시뮬레이션 결과는 설계된 게이팅 시스템 및 충진 공정의 효율성을 입증했습니다.
연구의 학문적 의의:
본 연구는 CAE 도구를 사용한 설계 최적화 및 결함 최소화를 위한 체계적인 접근 방식을 제시함으로써 다이캐스팅 금형 설계 분야의 지식 체계에 기여합니다. 특정 자동차 부품용 압력 다이캐스팅 금형 설계에 이론적 계산 및 시뮬레이션 기술을 적용한 실제 사례를 제공합니다. 본 연구는 기공을 완화하기 위해 금형 설계 시 부품 방향 (수직 대 수평)을 고려하는 것의 중요성을 강조합니다.
연구의 실제적 의의:
본 연구 결과는 특히 자동차 산업의 다이캐스팅 제조업체에 직접적인 실질적인 의미를 갖습니다. 최적화된 금형 설계 매개변수와 제시된 방법론은 실린더 헤드 커버용 금형 제조에 직접 적용될 수 있으며, 잠재적으로 주조 품질 향상, 결함 감소 및 생산 효율성 향상으로 이어질 수 있습니다. 설계 프로세스에서 CAE 소프트웨어를 사용하면 시행착오적인 금형 제작과 관련된 개발 시간과 비용을 크게 줄일 수 있습니다.
연구의 한계점
본 연구는 단일 자동차 부품 (실린더 헤드 커버) 및 재료 (ADC 12) 용 금형 설계 및 해석 범위로 제한됩니다. 분석은 주로 시뮬레이션에 의존하며, 금형 설계 및 주조 공정에 대한 실험적 검증은 본 논문에 제시되지 않았습니다. 또한, 최적화는 제한된 공정 매개변수 세트만 고려했습니다.
7. 향후 후속 연구:
- 후속 연구 방향
향후 연구 방향은 다음과 같습니다:- 시뮬레이션 결과를 확인하고 실제 주조 품질 및 결함률을 평가하기 위해 설계된 금형 및 주조 공정에 대한 실험적 검증.
- 보다 포괄적인 최적화를 위해 pq² 관계를 통합하여 용융 금속 온도, 사출 속도, 토출 압력, 캐비티 충진 속도 및 냉각 속도와 같은 더 넓은 범위의 공정 매개변수를 포함하도록 최적화 연구를 확장합니다.
- 이 설계 및 해석 방법론을 다른 자동차 부품 및 다양한 다이캐스팅 합금에 적용하는 것을 조사합니다.
- 추가 탐구가 필요한 영역
추가 탐구가 필요한 영역은 다음과 같습니다:- 냉각 시스템 설계와 주조 응고 및 결함 형성에 미치는 영향에 대한 상세 분석.
- 기존 설계와 비교하여 최적화된 금형 설계를 통해 달성된 결함 감소에 대한 정량적 평가.
- 압력 다이캐스팅 제조에서 CAE 기반 금형 설계 구현의 비용-편익 분석.
8. 참고 문헌:
- 1. http://www.custompartnet.com/wu/die-casting (2015년 5월 20일 접속).
- 2. Kong, L.X., She, F.H., Gao, W.M., Nahavandi, S., Hodgson, P.D. (2008). Integrated optimization system for high pressure dies casting processes. Journal of materials processing technology 201, 629-634.
- 3. Schey, A. J., Introduction to Manufacturing Processes, McGraw-Hill, Singapore, 1987.
- 4. Seo, P.K., Kim, D.U., Kang, C.G., (2006). Effects of die shape and injection conditions proposed with numerical integration design on liquid segregation and mechanical properties in semi-solid die casting process. Journal of Materials Processing Technology 176, 45–54.
- 5. Avalle, M., Belingardi, G., Cavatorta, M.P., Doglione, R., 2002. Casting defects and fatigue strength of a die cast aluminium alloy: a comparison between standard specimens and production components. International Journal of Fatigue 24, 1–9.
- 6. Yue, S., Wang, G., Yin, F., Wang, Y., Yang, J., (2003). Application of an integrated CAD/CAE/CAM system for die casting dies. Journal of Materials Processing Technology 139, 465-468.
- 7. Lin, J. C. (2002). 'Selection of the Optimal Gate Location for a Die-Casting Die with a Freeform Surface,' Int J Adv Manuf Technol, 19(4), pp.278-284.
- 8. Manjunath Swamy H. M., J. R. Nataraj, C. S. Prasad (2012) "Design Optimization of Gating System by Fluid Flow and Solidification Simulation for Front Axle Housing” International Journal of Engineering Research and Development, Vol. 4, Issue 6, pp. 83-88.
- 9. Woon, Y. K. and Lee, K. S. (2004), 'Development of a die design system for die casting,' Int J Adv Manuf Technol, Vol. 23, Issue (5-6), pp.399-411.
- B. Vijaya R., C.E., Vishal C., A. Arun K., S. M. Asif, G. Riyaz M., D. V. Raj, C. Suresh K. (2014). Analysis and Optimization of Gating System for Commutator End Bracket. Procedia Materials Science 6, 1312 – 1328.
- Abdu Y A. (2016). Implementation of Lean Manufacturing: A Case Study at ASK Automotive Private Limited (India), Int. J. Adv. Res. Sci. Technol. 5(1), 556-562.
9. 저작권:
- 본 자료는 "[Y. Abdulfatah Abdu, T. M. Shafii, K. K. Dubey & Prof U. K. Gupta]"의 논문: "[자동차 부품용 압력 다이캐스팅 금형 설계 및 해석]"을 기반으로 합니다.
- 논문 출처: https://www.researchgate.net/publication/314175819
본 자료는 상기 논문을 기반으로 요약되었으며, 상업적 목적으로 무단 사용하는 것을 금지합니다.
Copyright © 2025 CASTMAN. All rights reserved.