본 논문 요약은 ['ResearchGate' 발행의 'A Design and Analysis Method for Automotive and Aerospace Composite Structures including Manufacturing Variations'] 논문을 기반으로 작성되었습니다.
1. 개요:
- 제목: 자동차 및 항공우주 복합재 구조의 제조 변동을 포함한 설계 및 해석 방법 (A Design and Analysis Method for Automotive and Aerospace Composite Structures including Manufacturing Variations)
- 저자: Dirk Lukaszewicz, Simon Hesse, Lavinia Graff, Stefan Kerscher, Lyle Deobald, Chul Y Park, Nihar Desai
- 발행 연도: 2014년 9월
- 발행 저널/학회: 컨퍼런스 논문, ResearchGate
- 키워드: 제조 변동 (Manufacturing variations), 복합재 구조 (composite structures), 자동차 (automotive), 항공우주 (aerospace), 설계 방법 (design method), 해석 방법 (analysis method)
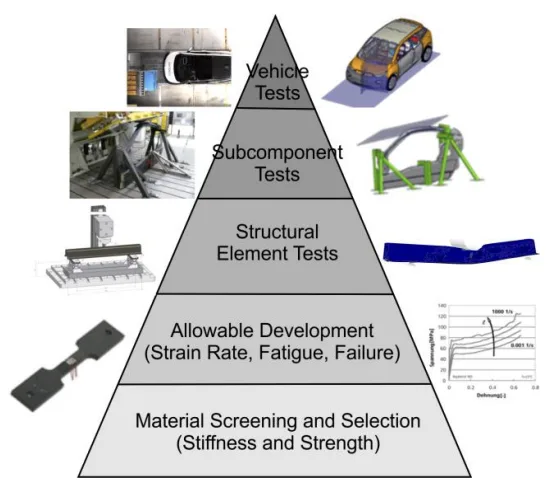
2. 초록
본 논문은 복합재 자동차 구조 및 하위 시스템의 설계 단계에서 제조 및 형상 유도 변동 (MV, Manufacturing and geometry-induced variations)의 잠재적 상호 작용을 모델링하기 위한 접근 방식을 제시합니다. 먼저, 제조 변동 처리에 중점을 두고 일반적인 설계 프로세스를 논의합니다. 이러한 변동의 영향은 고급 복합재 자동차 측면 프레임을 사용하여 시연됩니다. 자동차 측면 프레임의 충돌 안전성 시연에 적용되는 일반적인 방법은 일반적인 항공우주 구조의 강도 예측으로 확장될 수 있습니다. 평면 외 파형 (out-of-plane waviness)과 같은 실제 제조 변동은 부품 내 위치와 함께 파괴 테스트를 통해 기록된 다음 Abaqus Explicit [1]에 설정된 FE (Finite Element) 모델에 도입되었습니다. 가변 영역은 넉다운 계수 (knockdown factors)와 연관되었으며, 그 중 일부는 보완 논문 [2]에서 파생되었습니다. 서로 다른 MV 맵을 가진 두 개의 FE 모델이 실험 결과에 대해 검증되었습니다.
다중 MV 특성 수준은 확률적으로 동시에 변경되었으며 임팩터 침입에 미치는 영향이 기록되었습니다. 이로부터 반응 표면 모델 (RSM, Response Surface Model)이 생성되었습니다. 모든 넉다운 계수를 분리하고 MV의 영향을 개별적으로 평가할 수 있는 새로운 최적화 방법도 사용되었습니다. 그 결과는 각 MV에 대한 최대 허용 특성입니다. 이 방법론은 스크랩률 감소, 고가의 자격 시험 프로그램 감소, 알 수 없는 제조 변동을 설명하기 위한 과도한 안전 계수 사용 제거를 통해 부품 중량 감소를 가능하게 하므로 고용량 복합재 제조 및 설계에 상당한 이점을 제공합니다.
3. 연구 배경:
연구 주제 배경:
복합재 설계 및 제조는 부품 생산 과정에서 필연적으로 제조 변동 (MV, Manufacturing Variations)을 수반합니다. 이러한 MV는 부품 형상, 레이업 순서 및 공정 조건에 따라 달라지며, 강성이나 강도와 같은 복합재 구조물의 기계적 특성에 상당한 영향을 미칠 수 있습니다. 평판 시편에서 얻은 기계적 물성과 달리, 실제 부품은 MV를 나타내어 보수적이지 못한 설계 허용치를 초래할 수 있습니다.
기존 연구 현황:
현재 항공우주 산업에서는 MV를 고려하기 위해 설계 프로세스에 여러 요소를 통합하여 견고성을 확보합니다. 주요 요소는 넉다운 계수 (knockdown factors)를 공칭 재료 물성에 적용하여 유도된 허용치 (allowables)의 사용입니다. "빌딩 블록 접근 방식 (Building Block Approach)"에 기반한 이 방법은 광범위한 테스트와 비파괴 검사 (NDI, Non-Destructive Inspection)에 의존합니다. 그러나 대량 생산 자동차 제조 환경에서는 NDI가 시간과 비용 제약으로 인해 비실용적인 경우가 많습니다. 기존 방법은 MV를 고려하기 위해 구조 강도를 전반적으로 감소시키는 방법을 사용하는데, 이는 지나치게 보수적일 수 있습니다.
연구의 필요성:
항공우주 산업의 접근 방식은 효과적이지만, 생산량과 비용 고려 사항으로 인해 대량 생산 자동차 복합재 제조에 직접적으로 적용하기 어렵습니다. 제품 개발 과정에서 MV를 고려하여 설계 및 제조 프로세스 모두에 정보를 제공하는 방법론이 필요합니다. 여기에는 중요한 MV를 식별하고, 다이캐스팅 알루미늄 부품 설계에서 다공성을 명시적으로 고려하는 접근 방식과 유사하게, MV의 영향을 완화하기 위해 제조 프로세스를 최적화하는 것이 포함됩니다.
4. 연구 목적 및 연구 질문:
연구 목적:
본 연구의 주요 목적은 복합재 자동차 및 항공우주 구조물의 설계 단계에서 제조 변동 (MV, Manufacturing Variations)을 명시적으로 통합하는 설계 및 해석 방법론을 개발하고 시연하는 것입니다. 이 방법론은 구조적 성능을 유지하면서 제조 공정을 최적화하고 지나치게 보수적인 안전 계수에 대한 의존도를 줄이기 위해 MV에 대한 허용 한계를 정의하는 것을 목표로 합니다.
핵심 연구 질문:
- 설계 단계에서 제조 및 형상 유도 변동의 상호 작용을 모델링하는 방법은 무엇인가?
- 고급 복합재 자동차 측면 프레임을 사용하여 MV의 영향을 시연하고, 항공우주 구조로 방법론을 확장하는 방법은 무엇인가?
- 평면 외 파형 (out-of-plane waviness)과 같은 실제 MV를 기록하고 FE (Finite Element) 모델에 통합하는 방법은 무엇인가?
- 넉다운 계수 (knockdown factors)를 분리하고 개별 MV의 영향을 평가하기 위해 반응 표면 모델 (RSM, Response Surface Model)과 새로운 최적화 기술을 활용하는 방법은 무엇인가?
- 설계 및 제조 공정 최적화를 안내하기 위해 각 MV에 대한 최대 허용 특성을 정의하는 방법은 무엇인가?
연구 가설:
본 연구는 다음과 같은 가설을 내포하고 있습니다:
- FE (Finite Element) 시뮬레이션에서 MV를 명시적으로 모델링하면 전반적인 넉다운 계수 (knockdown factors)를 사용하는 것보다 복합재 구조 성능을 더 정확하게 예측할 수 있을 것이다.
- 특정 MV가 구조 성능에 미치는 영향을 기반으로 제조 공정을 최적화하면 스크랩률 감소, 자격 비용 절감 및 부품 중량 감소로 이어질 수 있을 것이다.
- RSM (Response Surface Model) 및 분리된 넉다운 계수 (knockdown factors)에 기반한 방법론은 복합재 구조에서 MV에 대한 허용 한계를 효과적으로 정의할 수 있을 것이다.
5. 연구 방법론
연구 설계:
본 연구는 실험적 테스트와 수치 시뮬레이션을 결합한 접근 방식을 채택합니다. 복합재 자동차 측면 프레임의 사례 연구를 사용하여 방법론을 시연합니다. 설계는 복합재 차량에 맞게 조정된 "빌딩 블록 접근 방식 (Building Block Approach)"을 사용하여 반복됩니다.
자료 수집 방법:
- 파괴 시험 (Destructive Testing): 평면 외 파형 (out-of-plane waviness)과 같은 실제 제조 변동 (MV, Manufacturing Variations)은 제조된 복합재 측면 프레임의 파괴 시험을 통해 기록되었습니다.
- 육안 검사 (Visual Inspection): MV 특성은 격자 투영법을 사용하여 제조된 부품의 각 층에 대해 육안으로 검사하고 기록했습니다. 품질 검사 직원이 결함을 분류하고 특성화했습니다.
- 실험적 검증 (Experimental Validation): 서로 다른 MV 맵을 가진 두 개의 FE (Finite Element) 모델이 실제 충돌 테스트의 실험 결과에 대해 검증되었습니다.
분석 방법:
- 유한 요소 (FE, Finite Element) 모델링: FE 모델은 Abaqus Explicit에서 개발되어 동적 충격 하에서 복합재 측면 프레임의 구조적 거동을 시뮬레이션하고 기록된 MV 맵을 통합했습니다.
- 반응 표면 모델 (RSM, Response Surface Model): RSM은 확률적으로 변화된 MV 특성이 구조적 성능 (임팩터 침입)에 미치는 영향을 분석하기 위해 몬테카를로 시뮬레이션 (Monte Carlo simulations)을 기반으로 생성되었습니다.
- 몬테카를로 시뮬레이션 (Monte Carlo Simulation): 몬테카를로 샘플링 (Monte Carlo sampling)은 MV 특성이 구조적 성능에 미치는 영향을 평가하기 위해 FE 모델에서 MV 특성을 변경하는 데 사용되었습니다.
- 최적화 알고리즘 (Optimization Algorithm): 새로운 최적화 알고리즘은 넉다운 계수 (knockdown factors)를 분리하고 각 MV에 대한 최대 허용 특성을 결정하는 데 사용되었습니다.
연구 대상 및 범위:
본 연구는 자동차 및 항공우주 응용 분야의 복합재 구조에 중점을 두며, 특히 자동차 측면 프레임을 사례 연구로 사용합니다. 범위에는 평면 내 및 평면 외 파형 (in-plane and out-of-plane waviness), 종방향 및 횡방향 폴딩 (longitudinal and transverse folding)과 같은 제조 변동이 포함됩니다. 본 연구는 고려된 MV 유형과 자동차 측면 프레임의 특정 형상으로 제한됩니다.
6. 주요 연구 결과:
핵심 연구 결과:
- 측정된 제조 변동 (MV, Manufacturing Variations)을 복합재 구조의 FE (Finite Element) 모델에 통합하기 위한 방법론이 개발 및 검증되었습니다.
- MV 맵을 통합한 FE 모델은 동적 충격 테스트에 대한 실험 결과와 양호한 상관관계를 보였습니다.
- 다양한 MV 특성이 구조적 성능 (임팩터 침입)에 미치는 영향을 정량화하기 위해 반응 표면 모델 (RSM, Response Surface Model)이 생성되었습니다.
- 넉다운 계수 (knockdown factors)를 분리하는 새로운 최적화 접근 방식을 사용하여 각 MV 유형에 대한 최대 허용 특성이 결정되었습니다.
- 본 연구는 특정 MV 조합이 충격 중 최대 침입 감소로 이어질 수 있음을 입증했으며, 이는 잠재적으로 강성 증가 또는 변경된 파괴 모드 때문일 수 있습니다.
제시된 데이터 분석:
- 표 1: 변화된 MV 및 특성 범위 (Table 1: Varied MVs and characteristic range): 이 표는 고려된 제조 변동 유형 (평면 외 파형, 평면 내 파형, 종방향 폴딩, 횡방향 폴딩)과 특성 크기 범위 (1-6)를 나열합니다.
- 그림 3: 임팩터 및 지지대가 있는 FE 모델 이미지, 매핑된 MV도 표시 (Figure 3: Image of the FE-model with Impactor and supports, mapped MVs are also shown): 이 그림은 임팩터, 지지대 및 복합재 측면 프레임에 매핑된 제조 변동을 포함한 FE 모델 설정을 시각적으로 나타냅니다.
- 그림 4: 기준선 FE 시뮬레이션과 MV 맵 A 및 B에 대한 하중-변위 곡선 비교 (Figure 4: Comparison of load-displacement curves for the baseline FE Simulation and MV map A and B): 이 그림은 FE 시뮬레이션의 하중-변위 곡선을 비교합니다. MV가 없는 기준선 시뮬레이션과 두 개의 서로 다른 MV 맵 (A 및 B)을 통합한 시뮬레이션입니다. MV가 구조적 반응에 미치는 영향을 보여줍니다.
- 표 2: 3점 굽힘 동적 충격 테스트의 변동성 (Table 2: Variability of 3-point-bending dynamic impact tests): 이 표는 공칭상 동일한 시편에 대한 변동성 테스트 결과를 제시하며, 최대 침입 및 평균 침입과 표준 편차를 보여줍니다. 이 데이터는 MV로 인한 허용 가능한 변화를 정의하는 데 사용됩니다.
- 표 3: 몬테카를로 시뮬레이션 결과 및 임계 제한을 초과하는 설계 수 (Table 3: Monte Carlo Simulation Results and No of designs above the critical limit): 이 표는 반복에 따른 몬테카를로 시뮬레이션 결과를 요약하여 RSM의 R² 값, 이상치 설계 수 및 이상치 비율을 보여줍니다. RSM의 수렴 및 품질을 나타냅니다.
- 표 4: MV 특성에 대한 회랑 제한 (Table 4: Corridor Limits on MV Characteristics): 이 표는 최적화 프로세스의 여러 반복에 걸쳐 각 MV 유형 (평면 외 파형, 평면 내 파형, 종방향 폴딩, 횡방향 폴딩)에 대한 회랑 제한 (최대 허용 MV 특성)을 보여줍니다. 허용 한계가 어떻게 개선되는지 보여줍니다.
그림 목록:
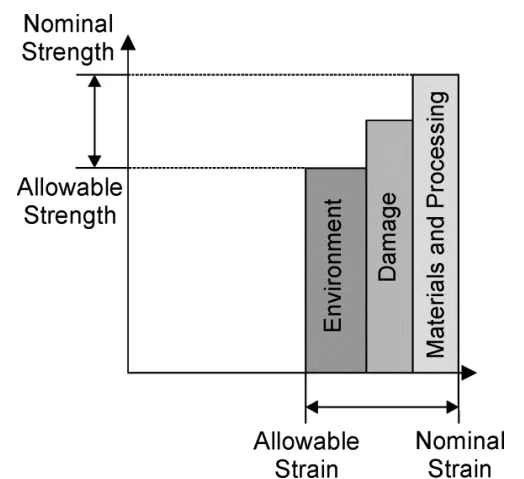
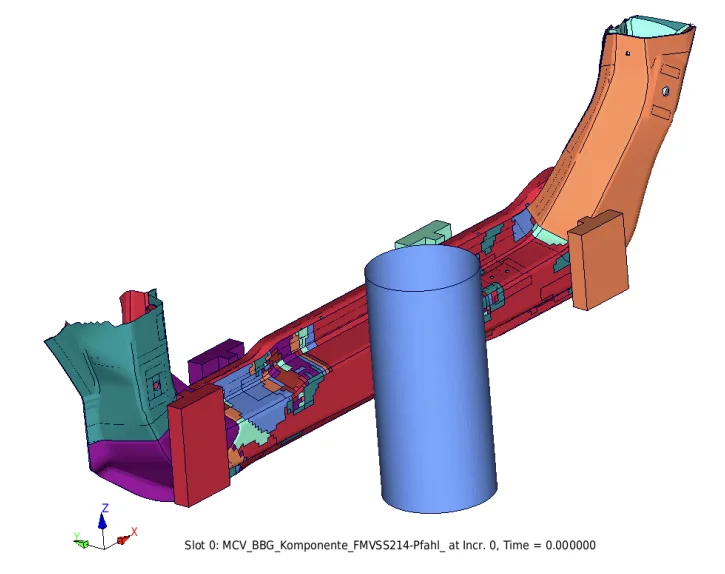
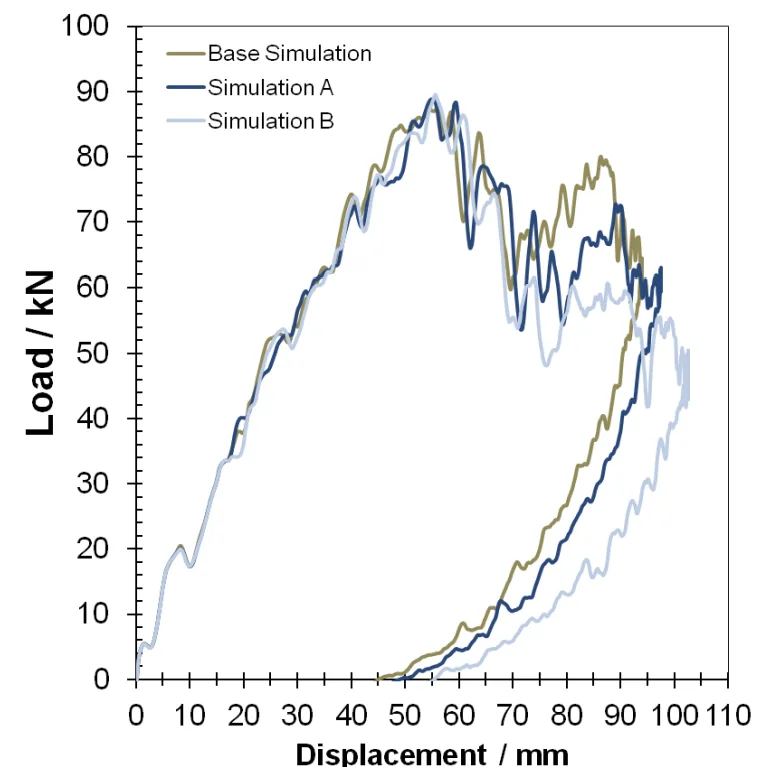
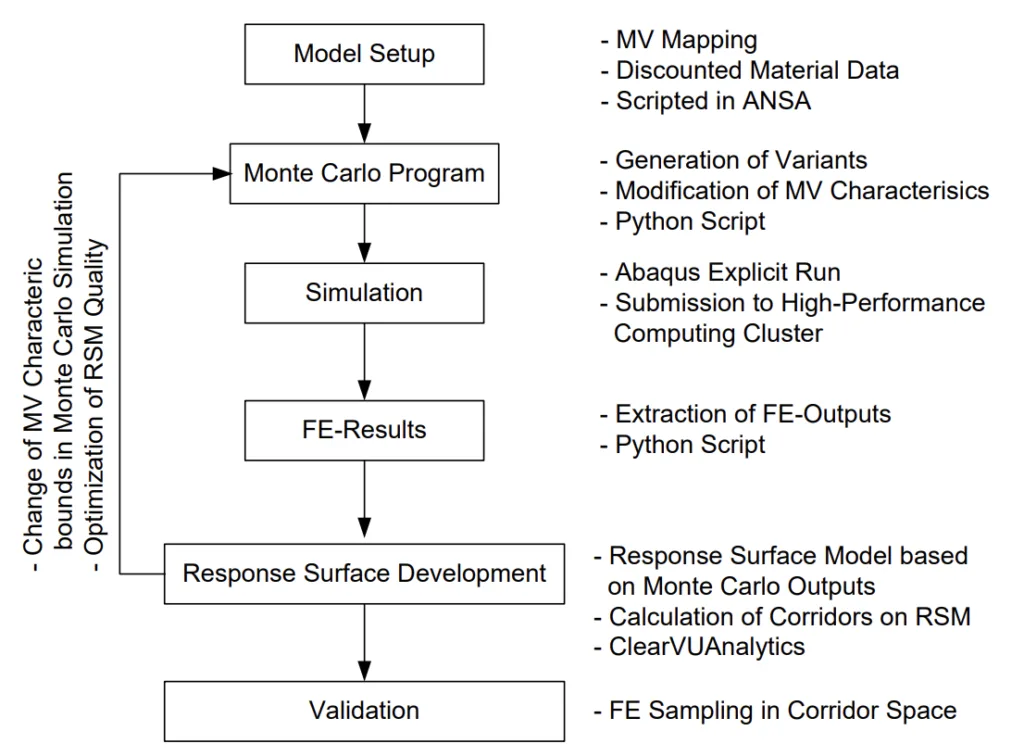
- 그림 1: 복합재료의 공칭 값 및 파생된 설계 허용치 정의 (Figure 1: Definition of nominal values for a composite material and derived design allowables).
- 그림 2: 복합재 차량에 대한 빌딩 블록 접근 방식 (Figure 2: Building Block approach for a composite vehicle).
- 그림 3: 임팩터 및 지지대가 있는 FE 모델 이미지, 매핑된 MV도 표시 (Figure 3: Image of the FE-model with Impactor and supports, mapped MVs are also shown).
- 그림 4: 기준선 FE 시뮬레이션과 MV 맵 A 및 B에 대한 하중-변위 곡선 비교 (Figure 4: Comparison of load-displacement curves for the baseline FE Simulation and MV map A and B)
- 그림 5: MV 회랑 및 최대 허용 특성에 대한 시뮬레이션 워크플로 (Figure 5: Simulation Workflow for the MV corridors and the maximum allowable characteristic).
7. 결론:
주요 연구 결과 요약:
본 연구는 제조 변동 (MV, Manufacturing Variations)을 명시적으로 고려하는 복합재 구조 설계 방법론을 성공적으로 개발하고 검증했습니다. 측정된 MV를 FE (Finite Element) 모델에 통합하고 RSM (Response Surface Model) 및 새로운 최적화 기술을 사용하여 구조적 무결성을 유지하면서 MV에 대한 허용 한계를 정의했습니다. 이 방법론은 자동차 복합재 측면 프레임에 대해 시연되었으며, 시뮬레이션과 실험 결과 간에 양호한 상관관계를 보였습니다.
연구의 학문적 의의:
본 연구는 제조 가변성을 설계 프로세스에 직접 통합하는 강력한 방법론을 제공함으로써 복합재 구조 설계 분야에 기여합니다. 전반적인 넉다운 계수 (knockdown factors)에 의존하는 기존 접근 방식에서 벗어나 MV가 존재하는 경우 구조적 성능을 예측하는 더 정교하고 정확한 방법을 제공합니다. RSM (Response Surface Model) 및 분리된 넉다운 계수 (knockdown factors)의 사용은 제조 불확실성이 있는 복합재 구조의 분석 및 최적화에 있어 진전을 나타냅니다.
실용적 의미:
개발된 방법론은 특히 자동차 및 항공우주 산업에서 대량 생산 복합재 제조에 상당한 실용적 의미를 갖습니다. MV를 명시적으로 고려하여 복합재 부품을 설계할 수 있도록 함으로써 다음과 같은 결과를 얻을 수 있습니다:
- 최적화된 제조 공정을 통한 스크랩률 감소.
- 광범위한 물리적 테스트의 필요성을 줄여 자격 비용 절감.
- 과도한 안전 계수 사용을 최소화하여 부품 중량 감소.
- 제조와 설계 간의 개선된 연결, 동시 최적화 촉진.
연구의 한계 및 향후 연구 분야:
본 연구는 특정 유형의 제조 변동과 특정 자동차 부품으로 제한됩니다. 향후 연구에서는 다음을 수행해야 합니다:
- 더 광범위한 MV 유형 및 복합재료를 포함하도록 방법론 확장.
- 항공우주 구조를 포함하여 다양한 구조 형상 및 하중 조건에 방법론 적용.
- 다양한 MV 유형의 상호 작용 및 결합 효과가 구조적 성능에 미치는 영향에 대한 추가 조사.
- 식별된 중요한 MV 및 허용 한계를 기반으로 제조 공정 최적화 탐색.
- 방법론을 더욱 개선하기 위해 결과에서 관찰된 수치적 노이즈 및 도메인 분해 효과 조사.
8. 참고 문헌:
- [1] Dassault Simulia. Abaqus 6.11-2A; 2013.
- [2] Deobald L, Park C, Desai N, et al. Simulation of Composite Manufacturing Variations to Determine Stiffness and Strength Reductions in Automotive and Aerospace Structure. ACS 29th Technical Conferences. San Diego 2014.
- [3] Potter K. In: (unpublished), 2013.
- [4] Huang H, Talreja R. Effects of void geometry on elastic properties of unidirectional fiber reinforced composites. Comp Sci Tech. 2005;65(13):1964-81.
- [5] Feraboli P. Composite Materials Strength Determination Within the Current Certification Methodology for Aircraft Structures. 2009;46(4):1365-74.
- [6] Graff L. Stochastic Algorithm for the identification of solution spaces in high-dimensional design spaces [PhD Thesis]: University of Basel, 2013.
- [7] Baxter B. The interpolation theory of radial basis functions [PhD Thesis]: Cambridge University, 1992.
- [8] Piret C. Analytical and numerical advances in radial basis functions [PhD Thesis]: University of Colorado, 2007.
- [9] Zimmermann M, von Hoessle J. Computing solution spaces for robust design. Int J Num Methods Eng. 2013;94(3):290-307.
- [10] Lukaszewicz D. Automotive Composite Design Process. FISITA World Automotive Congress. Maastricht, The Netherlands, 2014.
- [11] Beta CAE. ANSA; 2014.
- [12] Divis. ClearVU Analytics; 2014.
9. 저작권:
- 본 자료는 "[Dirk Lukaszewicz 외 다수]"의 논문: "[자동차 및 항공우주 복합재 구조의 제조 변동을 포함한 설계 및 해석 방법 (A Design and Analysis Method for Automotive and Aerospace Composite Structures including Manufacturing Variations)]"을 기반으로 합니다.
- 논문 출처: https://www.researchgate.net/publication/268925382
본 자료는 상기 논문을 요약한 것이며, 상업적 목적으로 무단 사용하는 것을 금지합니다.
Copyright © 2025 CASTMAN. All rights reserved.