이 소개 자료는 "[Surface and Coatings Technology]"에 게재된 "[Application of wear-resistant PACVD coatings in aluminium diecasting: economical and ecological aspects]" 논문을 기반으로 합니다.
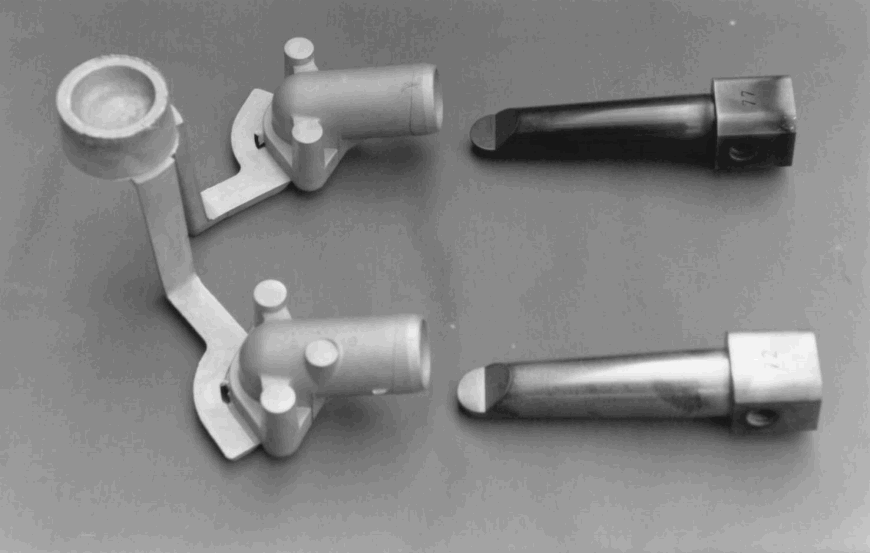
1. 개요:
- 제목: Application of wear-resistant PACVD coatings in aluminium diecasting: economical and ecological aspects (알루미늄 다이캐스팅에서 내마모성 PACVD 코팅의 적용: 경제적 및 생태학적 측면)
- 저자: C. Pfohl, A. Gebauer-Teichmann, K.-T. Rie
- 발행 연도: 1999
- 발행 학술지/학회: Surface and Coatings Technology
- 키워드: PACVD; Thin films; Aluminium die coating; Coated cores; Minimal lubrication
2. 초록:
알루미늄 정밀 부품의 주요 제조 기술 중 하나는 압력 다이캐스팅 공정입니다. 그러나 현재의 기술 수준은 많은 양의 윤활제 사용을 포함합니다. 이들의 부작용으로는 주조품의 표면 품질 저하 및 생태학적 위험이 있습니다. 내마모성 코팅의 증착은 다이캐스팅 공구의 수명을 늘리는 동시에 윤활제 사용을 최소화하는 수단을 제공합니다. 본 연구에서는 티타늄의 질화물, 탄화물, 붕화물을 조성, 구조, 경도, 접착력, 젖음성 및 알루미늄 용탕에 대한 내식성 측면에서 합성했습니다. 코팅된 코어는 윤활제 양을 줄이는 강화된 조건 하에서 다이캐스팅 실제 테스트에 노출되었습니다. 최적의 PACVD 코팅은 코팅되지 않은 공구에 비해 수명을 300배 증가시켰습니다. 원래 윤활제 양의 97% 감소를 달성할 수 있었습니다.
3. 서론:
알루미늄 압력 다이캐스팅은 정밀 부품의 근사형상(near-netshape) 생산에 자주 적용되는 제조 공정입니다. 최신 생산 기술은 여전히 상당한 양의 다이 윤활제를 필요로 합니다. 그러나 이러한 윤활제의 부작용으로는 주조 부품의 표면 품질 저하 및 주조 사이클 시간 연장이 있습니다. 작업 품질이 저하되고, 마지막으로 중요한 것은 윤활제의 생산 및 적용 중 폐기물 및 배기 가스 처리가 생태학적으로 위험하다는 것입니다. 내마모성 코팅의 증착은 주조 공정에서 윤활제 사용을 최소화하고 동시에 다이캐스팅 공구의 사용 수명을 늘리는 방법을 제공합니다. 플라즈마 보조 화학 기상 증착(PACVD)이 이 응용 분야에 가장 적합한 증착 방법으로 선택되었습니다. DC 플라즈마의 플라즈마 시스는 기판의 윤곽을 정확히 따릅니다. 따라서 PACVD는 복잡한 형상의 공구 코팅을 가능하게 합니다. 증착 온도는 다이캐스팅 공구에 일반적으로 사용되는 열간 공구강의 뜨임 온도보다 낮습니다. 증착된 코팅은 Al 다이캐스팅 공구 표면에서 발생하는 복잡한 하중을 견뎌야 합니다. 이러한 하중은 예를 들어 열 충격, 마모 마멸, 응착 마멸 및 액체 알루미늄에 의한 부식으로 구성됩니다. 많은 응용 분야에서 티타늄의 질화물, 탄화물 및 붕화물은 마모 방지용으로 성공적으로 확립되었습니다 [1]. TiN과 TiC는 정합 계면을 형성하여 특정 구배 및 다층 시스템 설계 기회를 제공합니다. 질화물은 비교적 우수한 열 안정성과 다른 재료와의 낮은 상호 작용 경향을 가지는 반면, 탄화물은 높은 경도와 금속 기판에 대한 더 나은 접착력을 나타냅니다 [2]. TiB2는 알루미늄과의 낮은 용해도로 유명하며, 이는 Al 용탕에 대한 우수한 내식성과 동의어입니다 [3].
4. 연구 요약:
연구 주제의 배경:
알루미늄 압력 다이캐스팅은 정밀 부품의 핵심 제조 공정이지만, 윤활제에 크게 의존하며 이는 표면 품질 저하, 사이클 시간 증가, 사용 및 폐기와 관련된 심각한 생태학적 문제를 야기합니다.
이전 연구 현황:
최신 다이캐스팅 생산은 상당한 윤활제 사용을 포함합니다. 티타늄의 질화물, 탄화물, 붕화물은 알려진 마모 방지 재료이지만[1, 2, 3], 실제 조건 하에서 Al 다이캐스팅에서 윤활제를 줄이고 공구 수명을 동시에 연장하기 위한 PACVD를 통한 특정 적용은 조사가 필요했습니다.
연구 목적:
본 연구는 내마모성 PACVD 코팅(특히 티타늄 질화물, 탄화물, 붕화물)이 알루미늄 다이캐스팅에서 윤활제 사용을 최소화하고 다이캐스팅 공구의 수명을 늘릴 수 있는 잠재력을 조사하여 경제적 및 생태학적 측면을 모두 다루는 것을 목표로 했습니다.
핵심 연구:
연구의 핵심은 PACVD를 사용하여 열간 공구강 기판 위에 TiN, TiC, Ti(B,N) 코팅을 합성하는 것이었습니다. 이 코팅들은 조성, 구조, 경도, 접착력, 알루미늄 합금에 대한 젖음성 및 용융 알루미늄에서의 내식성에 대해 특성화되었습니다. 이후, 최상의 코팅 성능은 윤활이 현저히 감소된 조건 하에서의 실제 다이캐스팅 현장 테스트에서 공구 수명 연장에 초점을 맞춰 평가되었습니다.
5. 연구 방법론
연구 설계:
본 연구는 PACVD를 사용하여 다이캐스팅 코어에 다양한 티타늄 기반 코팅(TiN, TiC, Ti(B,N) 및 다층)을 증착하는 실험 설계를 사용했습니다. 이후 코팅의 실험실 특성화와 강화된 조건(윤활 감소) 하의 산업 다이캐스팅 환경에서의 실제 현장 테스트가 이어졌습니다.
데이터 수집 및 분석 방법:
- 코팅 증착: 직경 400mm, 높이 1000mm 반응 챔버를 갖춘 PACVD 파일럿 플랜트. 경화된 열간 공구강 X40CrMoV5 1 (1.2344) 위에 약 500°C의 기판 온도에서 코팅 증착. 전구체: TiCl4. 공정 가스: Ar, H2, N2, CH4, BCl3. 증착 파라미터(압력: 80–250Pa, 전압: 400–700V, 펄스: 200–600µs, 퍼즈: 100–600µs) 변경.
- 코팅 특성화: 금속 조직학, XRD, SEM, EDS, WDS를 이용한 조성 및 구조 분석. Knoop 경도, 스크래치 테스트(접착력), 핀온디스크 테스트(마찰, 100Cr6 핀, FN:5N). 2×10⁻⁵ mbar에서 최대 800°C까지 Al 합금으로 젖음성 테스트. 700°C Al 용탕에서의 침지 테스트를 통한 내식성 평가.
- 다이캐스팅 현장 테스트: 인덕션 파이프 생산에 코팅된 코어 사용. Al 용탕(700°C)을 1260bar 압력으로 사출. 사이클 시간: 40초. 코어 온도 560°C와 300°C 사이에서 순환(내부 냉각 시스템). 윤활제 양 지속적으로 감소. 파손 기준: 취출 시 주조품의 찢어짐.
연구 주제 및 범위:
본 연구는 알루미늄 다이캐스팅 응용을 위한 PACVD TiN, TiC, Ti(B,N) 코팅의 합성, 특성화 및 성능 평가에 중점을 두었습니다. 범위에는 증착 파라미터의 영향 조사, 코팅 특성(기계적, 구조적, 화학적, 마찰학적, 부식, 젖음성) 특성화, 실제 다이캐스팅 시험에서 공구 수명 및 윤활제 감소에 미치는 영향 평가가 포함되었습니다.
6. 주요 결과:
주요 결과:
- TiN 코팅은 N/Ti 비율 0.95-1.06, 염소 농도 <5%, {200} 우선 배향, 두께 1-5µm, Ra 20-100nm, 최대 경도 3300HK0.005, 마찰 계수 µ=0.27-0.31을 보였습니다.
- TiC 및 Ti-C-N 다층 시스템(예: TiN/TiC, TiN/Ti(C,N)/TiC)은 최대 4µm 두께에 도달했으며, 매끄러운 표면(Ra=20-70nm)을 가졌습니다. 경도는 C/Ti 비율에 따라 달라졌으며, TiN 하부층은 접착력을 향상시켰습니다.
- 붕소 함량이 10-60at.%인 Ti(B,N) 코팅은 1.5-2µm 두께였고 매우 매끄러운 표면 구조(Ra=35nm)를 가졌습니다. 붕소 함량이 높은 유형은 비정질(경도 ~325HK0.005)이었고, 붕소 함량이 낮으면 결정질 구조(XRD로 TiN 및 TiB 피크 검출)를 가지며 경도는 최대 4400HK0.005에 달했습니다. 붕소는 확장된 TiN 격자(TiN의 4.24Å 대비 4.26Å)에 통합되었습니다.
- 젖음성 테스트 결과, 선택된 TiN, TiN/TiC, Ti(B,N) 코팅은 사용된 Al 합금에 대해 매우 높은 젖음 각도(174-177°)를 보여, 낮은 젖음성과 용탕과 코팅 간의 낮은 접착 경향을 나타냈습니다.
- 부식 테스트(700°C Al 용탕에서 6시간 침지) 결과, 코팅은 Al 용탕과 강철 기판 간의 반응을 방지하여 우수한 내식성을 보였습니다.
- 다이캐스팅 현장 테스트에서 윤활제 양은 97% 감소했으며, 냉각에 필요한 부족한 스프레이 액체 부피는 물로 대체되었습니다 (Fig. 2).
- 약 100회 주조 수명을 가진 코팅되지 않은 코어와 비교하여:
- TiN 코팅은 수명을 45배에서 130배까지 증가시켰습니다 (최대 13,001회 주조) (Fig. 3).
- TiN/Ti(C,N)/TiN 다층 코팅은 5992회 주조 후 파손되었습니다.
- 탄소 함량이 높은 TiC 코팅은 수명을 160배 증가시켰으며 (최대 15,976회 주조), 수명은 탄소 함량과 상관관계가 있었습니다 (Fig. 4).
- Ti(B,N) 코팅이 가장 유망한 결과를 보였으며, 보고된 테스트 동안 코팅되지 않은 더미 코어 수명의 300배 이상을 파손 없이 견뎌냈습니다 (Fig. 3).
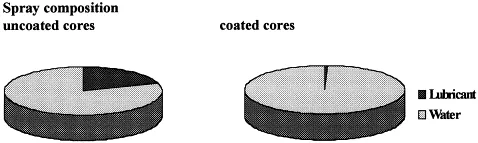
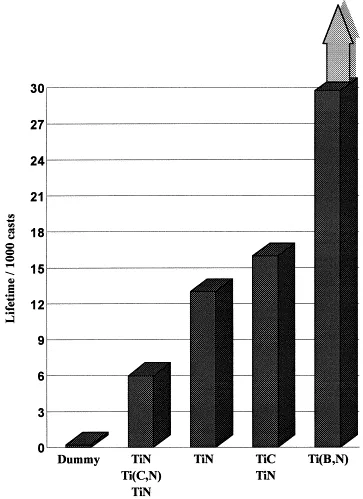
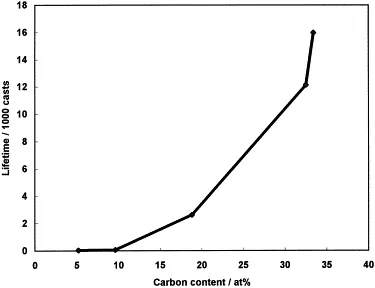
그림 이름 목록:
- Fig. 1. TiN- and Ti(B,N)-coated core with the corresponding cast.
- Fig. 2. Composition of the spray before and after study.
- Fig. 3. Maximal service life of the coating systems in diecasting field tests.
- Fig. 4. Service life of TiC coatings versus carbon content.
7. 결론:
PACVD로 증착된 기능성 코팅은 Al 다이캐스팅에서 윤활제 사용을 최소화하여 경제적 및 생태학적 이점을 모두 제공하는 중요한 기회를 제공합니다. 본 연구는 윤활제 소비량을 97% 감소시켰음을 입증했습니다. 동시에, 본 연구에서 분석된 티타늄 질화물, 탄화물, 붕화물은 동일한 까다로운 저윤활 조건 하에서 코팅되지 않은 공구에 비해 다이캐스팅 공구의 수명을 크게 증가시켰습니다. TiN 코팅은 수명을 최대 130배 증가시켰고, 다층 TiN/TiC는 160배 증가를 달성했습니다. Ti(B,N) 코팅은 특히 유망한 것으로 입증되었으며, 수행된 테스트에서 코팅되지 않은 더미 코어 수명의 300배 이상을 견뎌냈습니다.
8. 참고 문헌:
- [1] H.O. Pierson Mater. Manufact. Process., 8 (4/5) (1993), pp. 519-534
- [2] H. Holleck J. Vac. Sci. Technol. A, 4 (6) (1986), pp. 2661-2669
- [3] M. Kornmann, R. Funk Aluminium, 53 (1977), pp. 249-252
- [4] C. Pfohl, A. Gebauer-Teichmann, K.-T. Rie Matwiss. Werkstoffech., 29 (1998), pp. 51-56
- [5] K.-T. Rie, A. Gebauer, C. Pfohl, 18. Ulmer Gespräch, DGO, VDI-TZ, Ulm 1996, pp. 66–74.
- [6] N. Kikuchi, Y. Oosawa, A. Nishiyama, in: Proceedings of the Ninth International Conference on Chemical Vapour Deposition, Electrochemical Society, Pennington, 1984, pp. 728-744.
9. 저작권:
- 이 자료는 "C. Pfohl, A. Gebauer-Teichmann, K.-T. Rie"의 논문입니다. "[Application of wear-resistant PACVD coatings in aluminium diecasting: economical and ecological aspects]" 논문을 기반으로 합니다.
- 논문 출처: https://doi.org/10.1016/S0257-8972(98)00796-8
이 자료는 상기 논문을 바탕으로 요약되었으며, 상업적 목적의 무단 사용을 금합니다.
Copyright © 2025 CASTMAN. All rights reserved.