본 페이지는 2022년 Defect and Diffusion Forum에 게재된 연구 논문 "성형 및 다이캐스팅 금속 부품의 인터로킹을 위한 구조화된 냉간 압연에서 표면 형상 최적화(Optimization of the Surface Geometry in Structured Cold Rolling for Interlocking of Formed and Die-Cast Metal Components)"를 요약한 것입니다.
1. 개요:
- 제목: 성형 및 다이캐스팅 금속 부품의 인터로킹을 위한 구조화된 냉간 압연에서 표면 형상 최적화
- 저자: 아론 링겔(Aron Ringel) 및 요하네스 로마(Johannes Lohmar)
- 발행 연도: 2022년
- 발행 저널/학회: Defect and Diffusion Forum
- 키워드: 인터로킹(interlocking), 다중 재료 부품(multi-material components), 구조화된 냉간 압연(structured cold rolling), FE-모델링(FE-modelling)
2. 연구 배경:
- 연구 주제의 사회적/학문적 맥락:
최근 경량 설계는 특히 자동차 산업에서 점점 더 중요해지고 있습니다. 다중 재료 부품은 성능과 안전성을 유지하면서 무게를 줄이는 핵심 전략입니다. 강철과 알루미늄과 같은 재료를 결합하면 장점이 있지만, 잠재적인 화학 반응으로 인해 접합에 어려움이 있으며, 이는 전형적인 융합 용접이 기계적 성질이 좋지 않은 금속간 화합물 형성으로 인해 적합하지 않게 만듭니다. 액체 금속을 고체 금속에 접합하는 하이브리드(또는 복합) 주조는 실행 가능한 해결책으로 떠오르고 있습니다. 판금의 경우, 다중 패스 압연을 통해 언더컷이 있는 표면 구조를 만드는 것이 인터로킹 조인트를 형성하는 데 효과적인 것으로 입증되었습니다. 그러나 이러한 언더컷으로 조인트 강도를 극대화하는 최적의 표면 구조는 여전히 미해결 문제입니다. - 기존 연구의 한계:
다중 패스 압연으로 생성된 언더컷이 있는 표면 구조가 인터로킹 조인트에 사용되지만, "조인트를 지지하는 이러한 언더컷에 대한 최적의 표면 구조는 여전히 알려지지 않았습니다." 기존 연구에서는 또한 "내부 노치가 균열 시작에 취약하고 이후 부품 파손으로 이어질 수 있다"고 지적합니다. - 연구의 필요성:
이러한 한계를 해결하기 위해, 본 연구는 "언더컷과 내부 노치의 형성 메커니즘을 이해하여 내부 노치 형성을 피하면서 언더컷을 극대화하는 최적점을 도출"하는 것이 필요합니다. 이러한 이해는 "표면 구조 형상과 달성 가능한 부품 강도 사이의 관계에 대한 건전한 이해를 확립"하는 데 매우 중요합니다.
3. 연구 목적 및 연구 질문:
- 연구 목적:
주요 연구 목적은 "채널 깊이, 언더컷 및 내부 노치에 대한 표면 구조를 분석하고 최종적으로 조인트 강도를 극대화"하는 것입니다. 추가적인 목표는 "언더컷과 내부 노치의 형성 메커니즘을 이해하여 내부 노치 형성을 피하면서 언더컷을 극대화하는 최적점을 도출"하는 것입니다. - 주요 연구 질문:
본 연구는 구조화된 냉간 압연에서 표면 형상 최적화 문제를 해결하고자 합니다. 특히, 다음을 결정하는 것을 목표로 합니다.- 내부 노치 형성을 방지하면서 언더컷 폭을 최대화하는 표면 형상은 무엇인가?
- 내부 노치 없이 언더컷 폭이 넓은 표면 구조를 생성하는 최적의 공정 조건은 무엇인가?
- 연구 가설:
본 연구는 "조인트 강도는 언더컷 형상에 의해 결정적으로 결정된다"는 가설 하에 진행됩니다. 또한 "재료 변위에 의해 형성된 언더컷은 평탄 압연 패스에서 높이 감소와 함께 증가"하지만, "특정 양의 재료 변위 후 채널 측면 가장자리가 채널 바닥 위로 접혀 내부 노치를 형성하기 시작한다"는 관찰에 기반합니다.
4. 연구 방법론:
- 연구 설계:
본 연구는 "실험 및 수치 연구를 결합한" 방법을 사용합니다. 이러한 접근 방식은 표면 구조를 분석하기 위해 "실험 및 수치 연구를 배치"하는 것을 통합합니다. - 자료 수집 방법:
실험 데이터는 "Dreistern GmbH & Co. KG사의 롤 성형기 P3.160"을 사용하여 수집되었습니다. 다양한 표면 구조를 가진 강철 샘플은 "워터젯으로 단면 준비를 위해 절단"되었습니다. 내부 노치는 "3% Nital 에칭을 사용하여 가시화"되었습니다. 결과 구조는 "Keyence VHX-1000D 디지털 현미경"을 사용하여 측정되었습니다. - 분석 방법:
수치 해석은 Abaqus 소프트웨어를 사용하여 "2D 명시적 FE-모델" 시뮬레이션을 통해 수행되었습니다. "언더컷 폭 및 내부 노치 길이에 대한 결과 평가는 파이썬 스크립트를 통해 자동화"되었습니다. 실험 결과는 표면 구조를 측정하고 이를 공정 변수와 상관시켜 분석했습니다. - 연구 대상 및 범위:
본 연구는 "DC04 타입의 2.0mm 두께 강판"에 초점을 맞추었습니다. 표면은 "최대 0.5mm 깊이의 채널로 구조화된 다음 다양한 높이 감소로 평탄화"되었습니다. 실험에는 폭 160mm, 길이 245mm의 강판이 사용되었습니다. 시뮬레이션은 "채널과 립의 절반 높이와 폭을 포함하는" 2D 평면 변형 모델로 단순화되었습니다.
5. 주요 연구 결과:
- 주요 연구 결과:
본 연구는 표면 형상 최적화에 대한 시뮬레이션 및 실험 결과를 모두 도출했습니다.- 시뮬레이션 결과: "2D 명시적 FE-모델의 결과는 내부 노치 없이 언더컷 폭이 넓은 표면 구조에 대한 최적의 공정 조건이 14% 높이 감소에서 존재함을 시사합니다."
- 실험 결과: "그러나 실험에서 내부 노치는 주어진 실험 설정에 대해 약 20 µm 폭의 언더컷으로 약 8% 높이 감소에서 형성되기 시작했습니다. 대조적으로, 최대 약 50 µm의 언더컷은 26% 높이 감소에서 형성되지만, 약 60 µm 길이의 내부 노치도 유발합니다."
- 실험에서 "노치 없는 언더컷은 약 25 µm 폭에 불과"합니다.
- 통계적/정성적 분석 결과:
- 그림 3: "ɛh,1 = 12.08% 및 ɛh,2 = 28.18% 조건의 2D 평면 변형 시뮬레이션 예시"는 공정 중 재료 흐름과 응력 분포를 보여주며, 채널 및 잠재적인 내부 노치 형성을 보여줍니다. 주어진 변형률 값에 대해 "0.498 mm" 채널 깊이, "0.142 mm" 언더컷 폭 및 "0.358 mm" 내부 노치 길이를 보여줍니다.
- 그림 4: "언더컷 및 내부 노치가 있는 채널 단면, (ɛh,₁ = 18% 및 ɛh,2 = 33%)"는 실험 샘플의 현미경 이미지를 제시하여 "언더컷 폭" 및 "내부 노치 길이"를 시각화합니다. 스케일 바는 "50.00 μm"를 나타냅니다.
- 그림 5: "시뮬레이션 및 실험의 형상 매개변수"는 "채널 압연(1차)" 및 "평탄화(2차)"에 대한 시뮬레이션 및 실험 결과를 그래프로 비교합니다. "채널 깊이 [mm]" 및 "언더컷 폭 [mm]"과 "내부 노치 길이 [mm]"를 각각 "높이 감소 [%], 식 (1)" 및 "높이 감소 [%], 식 (2)"에 대해 플롯합니다. 시뮬레이션은 언더컷이 약 7% 높이 감소에서 시작하여 14% 높이 감소에서 최대 약 60 µm에 도달하는 것으로 예측합니다. 실험은 최대 언더컷 폭이 약 50 µm이고 약 26% 높이 감소에서 발생하며, 내부 노치는 약 8% 높이 감소에서 나타나는 것을 보여줍니다.
- 데이터 해석:
시뮬레이션 결과는 내부 노치 없이 언더컷 폭을 최대화하기 위한 최적의 높이 감소가 14%임을 나타냅니다. 그러나 실험 결과는 내부 노치가 더 일찍 나타나고 최대 언더컷 폭이 더 높은 높이 감소(26%)에서 달성되지만 내부 노치가 동반됨을 보여줍니다. "채널 압연 패스의 경우, 평면 변형 시뮬레이션은 실험 결과에 비해 채널 깊이를 과대평가합니다." 이러한 불일치는 실험에서 관찰되는 "채널 압연 중의 종방향 재료 흐름이 샘플의 변형되지 않은 측면에 의해 완전히 억제되지 않기 때문"이며, 이는 2D 평면 변형 시뮬레이션에서 제약됩니다. "평면 변형 제한으로 인해 시뮬레이션 라인의 기울기는 높이 감소 백분율당 약 0.04 mm입니다. 종방향 재료 흐름으로 인해 실험 기울기는 65%에 불과합니다." - 그림 목록:
- 그림 1: 공정 개요 (Senge et al., [12] 제안)
- 그림 2: 2D 시뮬레이션 어셈블리
- 그림 3: ɛh,1 = 12.08% 및 ɛh,2 = 28.18% 조건의 2D 평면 변형 시뮬레이션 예시
- 그림 4: 언더컷 및 내부 노치가 있는 채널 단면, (ɛh,₁ = 18% 및 ɛh,2 = 33%)
- 그림 5: 시뮬레이션 및 실험의 형상 매개변수
- 그림 6: DC04의 유동 곡선
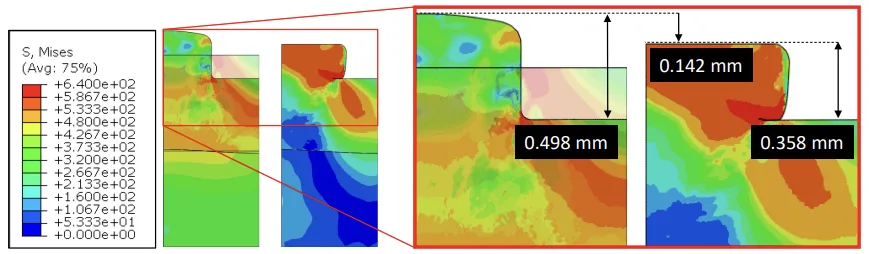
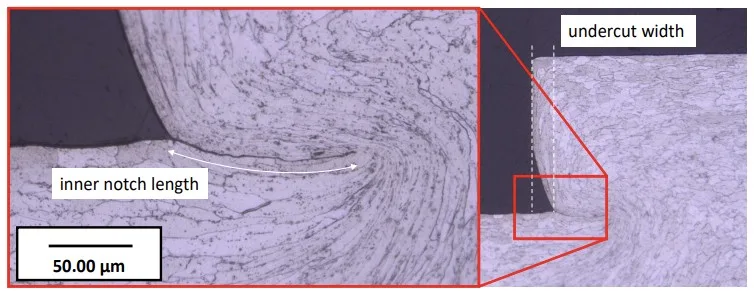
6. 결론 및 논의:
- 주요 결과 요약:
"본 연구에서는 노치 없는 언더컷을 위한 DC04 강판의 표면 구조 형상을 최대화하기 위해 시뮬레이션과 실험을 수행했습니다." 시뮬레이션은 노치 없는 언더컷에 대해 "2mm DC04 및 선택된 롤러 형상에 대해 약 14% 높이 감소에서 최적점"을 제시합니다. 실험에서는 26% 높이 감소에서 "최대 50 µm 폭의 언더컷"을 달성했지만, 이는 "약 60 µm의 내부 노치"를 동반했습니다. 실험 설정에서 "노치 없는 언더컷은 약 25 µm 폭에 불과"하며 내부 노치가 회피되는 더 낮은 높이 감소에서 발생했습니다. "이러한 거동은 현재 시뮬레이션에서 재현되지 않습니다." - 연구의 학문적 의의:
본 연구는 구조화된 냉간 압연에서 "언더컷 및 내부 노치의 형성 메커니즘"에 대한 이해에 기여합니다. 재료 흐름의 복잡성과 2D 시뮬레이션을 사용하여 이러한 공정에서 표면 형상을 정확하게 예측하는 데 따르는 어려움을 강조합니다. - 실용적 의미:
본 연구 결과는 특히 자동차 산업에서 "다중 재료 부품의 인터로킹 조인트"를 위한 판금의 표면 형상을 최적화하는 데 유용한 통찰력을 제공합니다. 본 연구는 내부 노치 없이 최대 언더컷 폭을 달성하려면 냉간 압연 공정에서 높이 감소를 신중하게 제어해야 함을 시사합니다. - 연구의 한계:
"정확도를 높이고 효능을 유지하는 한 가지 방법은 2D 평면 변형 모델에 운동학적 경계 조건을 추가하는 것입니다." "2D 평면 변형 모델은" 특히 실험에서 관찰되는 종방향 흐름과 같은 재료 흐름을 완전히 포착하는 데 "한계가 있습니다". "시뮬레이션은 내부 노치 형성에 대한 실험 결과를 완전히 재현하지 못합니다."
7. 향후 후속 연구:
- 후속 연구 방향:
저자들은 결과의 정확성과 적용 가능성을 개선하기 위해 다음과 같은 여러 가지 향후 연구 방향을 제시합니다.- "정확도를 높이고 효능을 유지하는 한 가지 방법은 2D 평면 변형 모델에 운동학적 경계 조건을 추가하는 것입니다."
- "또는, 측면에 변형되지 않은 강판을 포함하는 계산 비용이 많이 드는 3D 모델은 운동학적 및 응력 상태를 정확하게 설명하고 마찰 효과 조사를 허용할 것입니다."
- "높은 정확도를 위해서는 사용된 유동 곡선 외삽법도 중요한 역할을 하는 것으로 보입니다."
- "또한, 채널 압연 패스에서 롤러 형상의 영향도 조사해야 합니다. 구조화된 롤러의 립 가장자리에 더 큰 필렛 반지름을 사용하면 평탄화 패스에서 내부 노치 형성이 지연될 수 있기 때문입니다."
- "게다가, 언더컷 폭은 채널 압연 패스에서 더 넓은 립으로 증가할 수 있습니다."
- 추가 탐구가 필요한 영역:
다음 영역에 대한 추가 탐구가 필요합니다.- "롤러 형상의 영향"
- "마찰 효과"
- "더 나은 정확도를 위한 3D 모델링"
- "향후 연구에서는 시뮬레이션 정확도를 실용적인 관점에서 평가하기 위해 롤 압연/다이캐스팅 복합 부품을 사용하여 이러한 구조 형상의 조인트 강도에 대한 영향을 테스트할 것입니다."
8. 참고 문헌:
- [1] H.E. Friedrich, Leichtbau in der Fahrzeugtechnik, Springer Fachmedien, Wiesbaden, 2017.
- [2] B. Klein, T. Gänsicke, Leichtbau-Konstruktion, Springer Fachmedien, Wiesbaden, 2019.
- [3] W. Cai, G. Daehn, A. Vivek, J. Li, H. Khan, R.S. Mishra, M. Komarasamy, A State-of-the-Art Review on Solid-State Metal Joining, J. Manuf. Sci. Eng. 141 (3) (2019).
- [4] M. Rübner, M. Günzl, C. Körner, R.F. Singer, Aluminium-aluminium compound fabrication by high pressure die casting, Mater. Sci. Eng. A 528 (22-23), (2011) 7024–7029.
- [5] A. Bührig-Polaczek, T. Röth, E. Baumeister, N. Nowack, T. Süßmann, Hybride Leichtbaustrukturen in Stahlblech-Leichtmetall Verbundguss, FH Aachen (2006).
- [6] S. Senge, J. Brachmann, G. Hirt, A. Bührig-Polaczek, Evaluation of interlocking bond strength between structured 1.0338 steel sheets and high pressure die cast AlMg5Si2, in ESAFORM, (2018) p. 40019.
- [7] X. Fang, Evaluation of Coating Systems for Steel Aluminum Hybrid Casting; Mater. Sci. Eng. A 7 (2) (2017).
- [8] S. Ucsnik, R. Gradinger, A. Becirovic, A. Waldhör, Enhanced Performance of Steel-Aluminium Cast Nodes through Cold Metal, Transfer. Mater. Sci. Forum 765, (2013) 736–740.
- [9] N. Pasligh, Hybride formschlüssige Strukturverbindungen in Leichtbaustrukturen aus Stahlblech und Aluminiumdruckguss, Dissertation, Gießerei-Institut, Aachen (2011).
- [10]D. Joop, S. Heupel, C. Schnatterer, D. Zander, A. Bührig-Polaczek, Evaluation of Corrosion Mechanisms of Hybrid Light Metal Structures by High Pressure Die Casting, Mater. Sci. Forum 825-826, (2015) 441-448.
- [11]J. Jakumeit, H. Behnken, R. Laqua, J. Eiken, J. Brachmann, Multi-scale simulation of hybrid light metal structures produced by high pressure die casting; IOP Conf. Ser.: Mater. Sci. Eng. 861, (2020) p. 12035.
- [12] S. Senge, J. Brachmann, G. Hirt, A. Bührig-Polaczek, Interlocking Multi-Material Components made of Structured Steel Sheets and High-Pressure Die Cast Aluminium, in ESAFORM, (2017) p. 190007.
- [13]S. Senge, Walztechnische Herstellung von Oberflächenstrukturen für formschlüssige Verbindungen, Dissertation, Verlagshaus Mainz GmbH, Aachen (2020).
- [14] Y. Iino, Local Fatigue Damage Accumulation around Notch Attending Crack Initiation, Metall. Mater. Trans. A (26A), (1995) p. 1419.
- [15] A. Tieu, Y. Liu, Friction variation in the cold-rolling process, Tribol. Int. 37 (2), (2004) p. 177.
- [16] T. Clausmeyer, A. Schowtjak, S. Wang, R. Gitschel, O. Hering, P. Pavliuchenko, J. Lohmar, R. Ostwald, G. Hirt, A.E. Tekkaya, Prediction of Ductile Damage in the Process Chain of Caliber Rolling and Forward Rod Extrusion, Procedia Manuf. 47 (1), (2020) p. 649–655.
9. 저작권:
- 본 자료는 아론 링겔(Aron Ringel) 및 요하네스 로마(Johannes Lohmar)의 논문: "성형 및 다이캐스팅 금속 부품의 인터로킹을 위한 구조화된 냉간 압연에서 표면 형상 최적화"를 기반으로 합니다.
- 논문 출처: doi:10.4028/p-z54p05
본 자료는 상기 논문을 기반으로 요약되었으며, 상업적 목적으로 무단 사용하는 것을 금지합니다.
저작권 © 2025 CASTMAN. All rights reserved.