본 요약은 사출 성형 및 다이캐스팅 부품의 자동화된 제조 가능성 분석에 초점을 맞춘 연구 논문에 대한 개요를 제공합니다.
1. 개요:
- 제목: 사출 성형 및 다이캐스팅 부품의 자동화된 제조 가능성 분석 (AUTOMATED MANUFACTURABILTY ANALYSIS FOR INJECTION-MOLDED AND DIE-CAST PARTS)
- 저자: 다니엘 A. 맥아담스 (Daniel A. McAdams), 라훌 A. 비드카르 (Rahul A. Bidkar)
- 발표 연도: 2003년
- 발표 학술지/학회: 2003년 ASME 국제 설계 공학 기술 컨퍼런스 및 컴퓨터 및 정보 공학 컨퍼런스 (Proceedings of the 2003 ASME International Design Engineering Technical Conferences and the Computers and Information in Engineering Conference)
- 키워드: 제조를 위한 설계 (Design for Manufacturing), 특징 인식 (Feature Recognition), 자동화된 제조 가능성 분석 (Automated Manufacturability Analysis), 사출 성형 (Injection-Molding), 다이캐스팅 (Die-Casting)
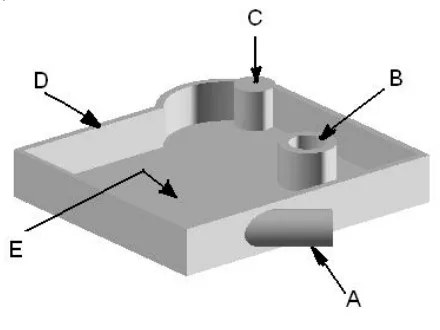
2. 연구 배경:
- 연구 주제의 사회적/학문적 맥락: 본 논문은 제품 성공을 위해 설계와 다운스트림 애플리케이션 간의 원활한 통합의 중요성을 강조합니다. 설계 단계에서 부품의 제조 가능성을 평가하는 컴퓨터 기반 도구는 설계와 제조를 연결하는 데 필수적입니다. 자동화된 제조 가능성 연구는 제조를 위한 설계 (DFM), 전산 기하학, 컴퓨터 지원 설계 (CAD) 및 특징 인식 연구를 기반으로 합니다.
- 기존 연구의 한계: 기존의 자동화된 제조 가능성 분석 연구는 주로 기계 가공 공정 (밀링, 드릴링 등)에 집중되어 있습니다. 일반적이고 중요한 제조 공정임에도 불구하고 사출 성형, 다이캐스팅, 단조 및 스탬핑과 같은 비절삭 가공 공정에 대한 연구는 눈에 띄게 부족합니다. 현재의 특징 인식 기술 또한 주로 기계 가공 응용 분야에 맞춰져 있으며, 비절삭 가공 공정에는 적용 가능성이 제한적입니다. CAD 시스템의 솔리드 모델은 고급이지만, 낮은 수준의 데이터 (점, 모서리, 면)를 저장하고 있으며, 제조 가능성 분석에 필요한 명시적인 특징 정보 (보스, 구멍, 언더컷)가 부족합니다.
- 연구의 필요성: 사출 성형 및 다이캐스팅을 위한 자동화된 제조 가능성 분석 방법 개발은 제조를 위한 설계에 대한 기본적인 기여입니다. 본 연구는 이러한 공백을 해결하기 위해 사출 성형 및 다이캐스팅 부품의 제조 가능성을 평가하는 방법을 제시하며, 이러한 공정에 맞춘 특징 인식 기술에 중점을 둡니다.
3. 연구 목적 및 연구 질문:
- 연구 목적: 사출 성형 및 다이캐스팅 부품의 자동화된 제조 가능성 평가를 위한 수학적 프레임워크 및 알고리즘을 개발하는 것입니다. 여기에는 새로운 특징 인식 방법 개발과 이러한 특정 공정에서 제조 가능성 분석을 위한 특징 인식의 주요 과제 해결이 포함됩니다.
- 주요 연구 질문:
- 컴퓨터 기반 도구를 사용하여 사출 성형 및 다이캐스팅 부품의 제조 가능성을 자동으로 평가하는 방법은 무엇인가?
- 사출 성형 및 다이캐스팅의 제조 가능성 분석에 적합한 특징 인식 방법을 개발하는 방법은 무엇인가?
- 사출 성형 및 다이캐스팅 부품의 맥락에서 파팅 면, 언더컷, 구멍 및 보스를 인식하는 과제를 해결하는 방법은 무엇인가?
- 3D 솔리드 모델의 이진 표현을 이러한 공정에서 특징 인식 및 제조 가능성 분석에 효과적으로 사용할 수 있는가?
- 연구 가설: 본 논문은 명시적인 연구 가설을 제시하지 않지만, 다음과 같은 내용을 암시합니다.
- 부품을 기본 큐브로 분해하고 개별 제조 가능성을 평가하는 수학적 프레임워크는 사출 성형 및 다이캐스팅 부품의 전체 제조 가능성을 효과적으로 평가할 수 있습니다.
- 3D 솔리드 모델의 이진 표현은 B-rep 모델의 한계를 극복하고 사출 성형 및 다이캐스팅의 DFM 분석을 위해 중요한 제조 가능성 정보를 추출하는 데 사용될 수 있습니다.
4. 연구 방법론
- 연구 설계: 본 연구는 제조 가능성 평가 알고리즘 (MEA)을 개발하고 C++ 및 Unigraphics 솔리드 모델링 소프트웨어를 사용하여 구현하는 개발 및 구현 접근 방식을 채택합니다. 알고리즘은 새로운 특징 인식 방법을 기반으로 합니다.
- 데이터 수집 방법: 본 방법은 솔리드 모델의 3D 이진 표현을 얻는 절차를 사용합니다. 여기에는 다음이 포함됩니다.
- 기본 큐브로 분해: 부품은 1 (솔리드 큐브)과 0 (보이드 큐브)의 3D 이진 배열로 분해됩니다.
- 슬라이싱: 솔리드 모델을 직교 방식으로 슬라이싱하여 3D 메시를 생성합니다.
- 부울 대수: 큐브가 솔리드 모델 내에 50% 이상 포함된 경우 솔리드로 간주하고, 그렇지 않으면 보이드로 간주하여 부울 대수를 사용하여 솔리드/보이드 큐브를 결정합니다.
- 분석 방법: 방법론의 핵심은 제조 가능성 평가 알고리즘 (MEA)입니다. MEA의 주요 측면은 다음과 같습니다.
- 솔리드 큐브의 유형 분류: 솔리드 큐브는 유형 I (부품 내부에 완전히 포함)과 유형 II (경계면에 위치)로 분류됩니다. 유형 II 큐브는 제조 가능성에 매우 중요합니다.
- 접근성 분석: MEA는 제조 가능성을 결정하기 위해 보이드 큐브의 접근성을 조사합니다. 접근 불가능한 보이드 큐브는 제조 문제를 나타냅니다.
- 언더컷 인식: 언더컷은 금형 폐쇄 방향에 수직인 접근 불가능한 유형 II 솔리드 큐브로 형성된 표면으로 식별됩니다.
- 파팅 면 결정: 파팅 면은 이진 표현에서 열을 따라 이동하고 각 열에서 가장 위에 있는 솔리드 큐브를 식별하여 찾습니다.
- 보스 및 구멍 인식: 보스와 구멍은 인접 레이어에서 유형 I 솔리드 큐브 (보스의 경우) 또는 보이드 큐브 (구멍의 경우)를 "클럽", "연결" 및 "확인"하고 경계면의 유형 II 큐브의 모양과 공간적 배열을 분석하여 인식합니다.
- 연구 대상 및 범위: 본 연구는 사출 성형 및 다이캐스팅 부품에 적용 가능한 일반적인 알고리즘 개발에 중점을 둡니다. 크랭크 케이스 커버 예시와 보스 및 구멍이 있는 간단한 부품을 사용하여 알고리즘의 기능을 시연합니다. 이진 표현에 사용된 큐브 크기는 약 70mm x 40mm x 20mm 크기의 부품에 대해 1mm x 1mm x 1mm였습니다.
5. 주요 연구 결과:
- 주요 연구 결과:
- 새로운 특징 인식 방법: 부품을 기본 큐브로 분해하고 이진 표현을 사용하는 새로운 특징 인식 방법이 개발되었습니다.
- 자동화된 제조 가능성 평가 알고리즘 (MEA): 사출 성형 및 다이캐스팅 부품의 제조 가능성을 평가하기 위한 알고리즘이 생성 및 구현되었습니다.
- 파팅 면 결정: MEA는 부품의 파팅 면을 성공적으로 결정합니다.
- 언더컷 인식: MEA는 부품의 언더컷을 식별할 수 있습니다.
- 보스 및 구멍 인식: MEA는 보스와 구멍을 인식하고 원통형과 다른 모양을 구별할 수 있습니다.
- 제조 가능성을 위한 접근성 분석: MEA는 보이드 큐브의 접근성 분석을 사용하여 전체 부품 제조 가능성을 결정합니다.
- 통계적/질적 분석 결과: 본 논문은 주로 방법론적 개발을 제시하고 예시를 통해 적용을 시연합니다. 통계 분석은 제시되지 않았습니다. 질적 결과는 예시 부품에서 특징을 성공적으로 인식함으로써 입증됩니다.
- 데이터 해석:
- 이진 표현은 제조 가능성 분석을 위해 부품의 형상을 효과적으로 캡처합니다.
- 유형 II 솔리드 큐브는 제조 가능성 문제 및 특징 경계를 식별하는 데 매우 중요합니다.
- 보이드 큐브의 접근성 분석은 성형성을 평가하는 직접적인 방법을 제공합니다.
- MEA 알고리즘은 사출 성형 및 다이캐스팅 부품에 대한 주요 특징 및 제조 가능성 측면을 인식하는 과제를 성공적으로 해결합니다.
- 그림 목록:
- Figure 1. A solid model representation of a part showing features critical to die-casting.
- Figure 2. A flow chart showing the primary steps of the Global manufacturability analysis algorithm.
- Figure 3. A detailed algorithm to determine whether a part is flat or box shaped. Step AA for the global manufacturability analysis algorithm.
- Figure 4. Summary of the applicability of existing feature recognition techniques as applied to the feature recognition needs of injection-molding and die-casting shown in part.
- Figure 5. A simple part to be molded.
- Figure 6. A candidate part decomposed into small building blocks.
- Figure 7. A simple part with a hollow boss.
- Figure 8. A block with a cylindrical boss.
- Figure 9. The sliced version of the part.
- Figure 10. Classifying solid cubes as Type I or Type II.
- Figure 11. Illustrating the accessibility analysis to find undercuts.
- Figure 12. Illustration of the recognition of undercuts.
- Figure 13. Determining the parting surface for a simple part.
- Figure 14. A simple part with boss and hole.
- Figure 15. Type classifications of solid cubes for the part.
- Figure 16. A binary representation of a layer for the part shown in Figure 15.
- Figure 17. Illustration of the connection of adjacent layers.
- Figure 18. Illustration of "manufacturing requirements".
- Figure 19 Illustration of "manufacturing requirements" in terms of binary data.
- Figure 20 Recognized hole and boss.
- Figure 21. A simple part with a hole.
- Figure 22 Recognized hole.
- Figure 23. A Graphical comparison between MEA and ASV approach.
- Figure 24. The identified parting surface and recognized features for the example.
Figure 23. A Graphical comparison between MEA and ASV approach
Figure 24. The identified parting surface and recognized features for the example.
6. 결론 및 논의:
- 주요 결과 요약: 본 연구는 사출 성형 및 다이캐스팅 부품의 자동화된 제조 가능성 분석을 위한 제조 가능성 평가 알고리즘 (MEA)을 성공적으로 개발하고 구현했습니다. MEA는 솔리드 모델의 새로운 이진 표현을 활용하고 파팅 면 결정, 언더컷, 구멍 및 보스 인식과 같이 이러한 제조 공정에 특정한 특징 인식 문제를 효과적으로 해결합니다.
- 연구의 학문적 의의: 본 연구는 자동화된 제조 가능성 분석 분야에서 사출 성형 및 다이캐스팅과 같은 비절삭 가공 공정으로 적용 범위를 확장함으로써 중요한 기여를 합니다. 성형 및 주조 공정의 물리학에서 영감을 얻은 새로운 특징 인식 프레임워크를 도입하여 주로 기계 가공에 초점을 맞춘 기존 기술과 비교하여 독특한 접근 방식을 제공합니다. 제조 가능성 평가를 위한 기본 큐브 및 이진 표현의 개념은 새로운 기여입니다.
- 실용적 의미: MEA는 설계 엔지니어가 설계 초기 단계에서 사출 성형 및 다이캐스팅 부품의 제조 가능성을 평가할 수 있는 귀중한 도구를 제공합니다. 이는 다음으로 이어질 수 있습니다.
- 설계 반복 횟수 감소 및 제품 개발 주기 단축.
- 제조 가능성 문제를 사전에 식별하고 해결하여 제조 비용 절감.
- 사출 성형 및 다이캐스팅 공정을 위한 부품 설계 개선.
- 연구의 한계:
- 특징 인식 접근 방식은 현재 금형 폐쇄 방향과 평행한 보스 및 구멍으로 제한됩니다. 각도가 있는 특징은 언더컷으로 분류됩니다.
- 현재 구현에서는 금형 폐쇄 방향을 초기에 지정해야 합니다.
- 본 논문에서는 벽, 리브 및 기타 복잡한 특징을 인식하기 위한 규칙을 공식화하는 데 추가 작업이 필요함을 인정합니다.
- MEA의 일반화 가능성 및 견고성은 더 광범위한 복잡한 사출 성형 및 다이캐스팅 부품에 대해 테스트해야 합니다.
7. 향후 후속 연구:
- 후속 연구 방향:
- 3D 이진 데이터에서 벽, 리브와 같은 복잡한 특징 및 기타 특징을 인식하기 위한 규칙을 공식화하고 확립합니다.
- 3D 이진 배열을 스캔하고 특징을 인식하여 금형 폐쇄의 선호 방향을 자동으로 결정하는 알고리즘을 개발합니다.
- 특징 인식 기능을 금형 폐쇄 방향에 대한 각도가 있는 특징을 포함하도록 확장하여 평행한 특징뿐만 아니라 더 넓은 범위의 특징을 인식하도록 합니다.
- MEA의 유효성 및 견고성을 확립하기 위해 더 광범위한 복잡한 사출 성형 및 다이캐스팅 부품에 대해 MEA를 테스트하고 검증합니다.
- 제조 가능성 분석 결과를 기반으로 부품 재설계 제안을 제공하는 "자동화된 합성" 기능을 개발하여 보다 완전한 "컴퓨터 지원 설계" 시스템으로 나아갑니다.
- 추가 탐구가 필요한 영역:
- 다양한 특징 크기 및 제조 능력에 대해 정확성과 계산 비용의 균형을 맞추기 위해 이진 표현을 위한 메시 크기 최적화.
- 설계 워크플로 내에서 원활한 제조 가능성 분석을 위해 MEA와 상용 CAD 시스템의 통합을 조사합니다.
- MEA를 단조 및 스탬핑과 같은 다른 비절삭 가공 공정에 적용하는 것을 탐구합니다.
8. 참고 문헌:
- Dastidar, P. G., A knowledge-based manufacturing advisory system for the economical design of metal stampings, PhD dissertation, University of Massachusetts Amherst, 1991.
- Dixon, J. R. and Poli, C., Engineering Design and Design for Manufacturing, Field Stone Publishers, 1995. Gadh, R., Feature mapping and feature recognition in geometric design generation, In Jami Shah, Martti Mäntylä and Dana S. Nau, editors, Advances in Feature based Manufacturing, chapter 6, pp. 107-128, Elsevier publishers, 1994.
- Gadh, R. and Prinz, F. B., Recognition of geometric forms using the differential depth filter, Computer Aided Design, Butterworth-Heinemann publishers, 24 (11), pp. 583-598, 1992.
- Gupta, S. K., Regli, W. C., Nau, D. S., and Zhang, G., A methodology for systematic generation and evaluation of alternative operation plans, In Jami Shah, Martti Mäntylä and Dana S. Nau, editors, Advances in Feature based Manufacturing, chapter 8, pp. 161-184, Elsevier publishers, 1994.
- Gupta, S. K. and Nau, D. S., A systematic approach for analyzing the manufacturability of machined parts, Computer Aided Design, 1995.
- Gupta, S. K., Regli, W. C., Das, D., and Nau, D. S., Automated Manufacturability Analysis: A Survey, Research in Engineering Design, Vol. 9, No. 3, pp. 168- 190, 1997.
- Henderson, M. R., Extraction of feature information from three-dimensional CAD data, PhD dissertation, Purdue University, 1984.
- Henderson, M. R., Srinath, G., Stage, R., Walker, K. and Regli, W., Boundary Representation-based Feature Identification, In Jami Shah, Martti Mäntylä and Dana S. Nau, editors, Advances in Feature based Manufacturing, chapter 2, pp. 15-38, Elsevier publishers, 1994.
- Joshi, S. and Chang, T. C., Graph based heuristics for recognition of machined features from a 3D solid model, Computer Aided Design, 20 (2), pp. 58-66, 1988.
- J. W. Van Vliet C. A. Van Luttervelt and H. J. J. Kals, State Of the Art report on Design for Manufacturing. In Design Engineering Technical Conference, ASME, 1999. INCLUDE PAPER NUMBER
- Kramer, T. R., Nau, D. S., Gupta, S. K., Regli, W. and Zhang, G., Development of Machining Alternatives, Based on MRSEVs, Proc. of the ASME Computers in Engineering Conference, 1993.
- Kyprianou, L., Shape classification in Computer Aided Design, PhD dissertation, Cambridge, UK, 1980.
- Lei, S. and Qamhiyah, A., Wavelet-based surface analysis for form feature extraction, Proc. of Design for Manufacturing Conf. ASME, 2000. INCLUDE PAPER NUMBER
- Mill, F.G., Naish, J.C. and Salmon, J.C., Design for machining with a simultaneous-engineering workstation, Computer Aided Design, pp. 521-527, 1994.
- Mortenson, M., Geometric modeling, Wiley, 1985.
- Poli, C., Escudero, J. and Fernandez, R., How Part Design Affects Injection Molding Tool Costs, Machine Design, 1988.
- Poli, C., Fredette, L. and Sunderland, J. E., Trimming the cost of die-castings, Machine Design, 1990.
- Poli, C., Design for Manufacturing: A Structured Approach, Butterworth Heinemann, Boston, 2001.
- Prabhakar, S., An experiment on the use of neural nets in form feature recognition, Master’s thesis, Arizona State University, 1990.
- Priest, J. W. and Sanchez, J. M., An empirical methodology for measuring producibility early in product development., International Journal of Computer Integrated Manufacturing, 4(2),pp. 114-- 120, 1991.
- Regli, W. and Nau, D. S., Building a general approach to feature recognition of material removal shape element volumes (MRSEVs), Second Symposium on Solid Modeling Foundations and CAD/CAM Applications, 1993.
- Regli, W., Gupta, S. K. and Nau, D. S., Feature recognition for manufacturability analysis, ASME Computers in Engineering Conference, pp. 93-104,1994.
- Regli, W., Geometric Algorithms for the Recognition of Features from Solid Models, Ph.D. dissertation, University of Maryland, 1995.
- Requicha, A. A. G. and Han, J., Feature recognition from CAD models, IEEE Computer Graphics, 1998.
- Sakurai, H. and Gossard, D. C., Shape Feature Recognition from 3D solid models, ASME Computers in Engineering, 1988.
- Shah, J., Mäntylä, M. and Nau, D. S., editors, Advances in Feature based Manufacturing, chapter 1, pp. 1-11, Elsevier publishers, 1994.
- Shah, J. and Mäntylä, M., Parametric and Feature-Based CAD/CAM: Concepts, techniques and applications, Wiley–Interscience Publication, 1995.
- Trucks, H. E., Designing for Economical Production, Society of Manufacturing Engineers, MI, 1987. UniGraphics Solutions Inc., V18.0 UniGraphics Help, 2001.
- Vandenbrande, J., Automatic recognition of machinable features in solid models, PhD dissertation, University of Southern California, 1990.
- Vandenbrande, J. H. and Requicha, A. A. G., Spatial reasoning for the automatic recognition of machinable features in solid models, IEEE Pattern Analysis and Machine Intelligence, vol. 15, no. 12, pp. 1269-1285, 1993.
- Woo, T., Feature recognition by volume decomposition, Proc. of Conference CAD/CAM technology in Mechanical Engineering, Cambridge, MA, 1982.
- Yong Se Kim, Volumetric feature recognition using convex decomposition, In Jami Shah, Martti Mäntylä and Dana S. Nau, editors, Advances in Feature based Manufacturing, chapter 3, pp. 39-63, Elsevier publishers, 1994. Zeid, I., CAD/CAM Theory and Practice, McGraw-Hill, 1991.
9. 저작권:
*본 자료는 다니엘 A. 맥아담스 및 라훌 A. 비드카르의 논문: 사출 성형 및 다이캐스팅 부품의 자동화된 제조 가능성 분석 (AUTOMATED MANUFACTURABILTY ANALYSIS FOR INJECTION-MOLDED AND DIE-CAST PARTS)을 기반으로 합니다.
*논문 출처: ?
본 자료는 위 논문을 기반으로 요약되었으며, 상업적 목적으로 무단 사용하는 것을 금지합니다.
Copyright © 2025 CASTMAN. All rights reserved.