본 기사에서는 [ARPN Journal of Engineering and Applied Sciences]에서 발행한 논문 [Corrective and preventive actions of motor cycle cylinder component leak problem on casting process]을 소개합니다.
1. 개요:
- 제목: 모터사이클 실린더 부품 누설 문제의 주조 공정 개선 및 예방 조치
- 저자: 라흐마트 누르차효 (Rahmat Nurcahyo), 파투르 로흐만 파우지 (Fathur Rohman Fauzi)
- 발행 연도: 2016년 1월
- 발행 학술지/학회: ARPN Journal of Engineering and Applied Sciences
- 키워드: PDCA, TQM, 개선 조치, 다이캐스팅
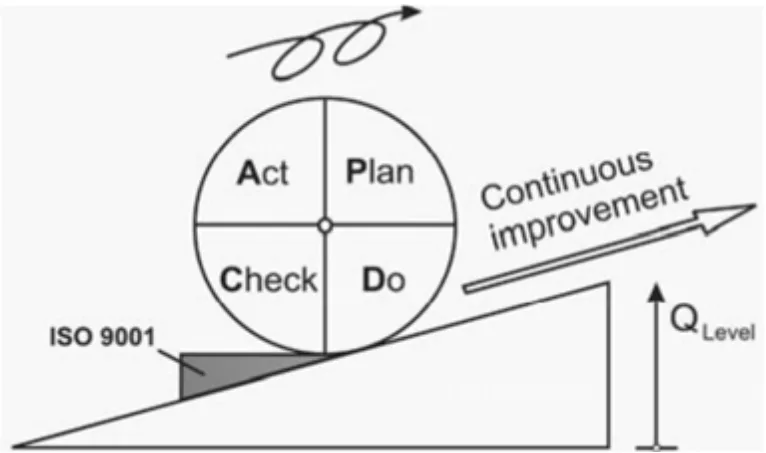
2. 초록 또는 서론
산업 현장에서 불량 제품은 생산 공정에서 바람직하지 않은 품질 편차입니다. 모터사이클 실린더 부품의 주조 공정에서 불량 제품 문제는 4.47%의 비율로 주요 문제 중 하나입니다. 본 연구는 목표 불량률 3.6%를 달성하기 위해 문제점을 개선하는 것을 목표로 합니다. 문제 분석 및 개선 조치 개발을 위해 품질 보조 도구인 7가지 도구를 포함한 Plan Do Check Action (PDCA) 방법론이 사용되었습니다.
분석 결과 문제의 원인은 실린더 부품의 언더컷 및 기공으로 나타났습니다. 재료, 기계 및 검사와 관련된 개선 조치가 취해졌습니다. 개선 조치 결과 불량률은 3.17%로 감소했습니다. 예방 조치는 향후 재발 방지를 위해 부적합 제품의 잠재적 원인을 줄이기 위해 수행되었습니다.
3. 연구 배경:
연구 주제 배경:
오늘날 모터사이클 산업은 거대한 산업으로 자리 잡았으며 제품 품질에 높은 기준을 적용하고 있습니다. Feigenbaum (1991)에 따르면 품질은 마케팅, 엔지니어링, 제조, 유지 보수에 이르기까지 고객의 기대를 충족시키기 위해 제품과 서비스가 사용되는 전반적인 제품 및 서비스 특성의 조합입니다. 한편, ANSI/ASQC 표준 (1978)의 정의에 따르면 품질은 주어진 만족 필요성을 보장할 수 있는 제품 또는 서비스의 총체적인 특징 및 특성입니다. Crosby는 총체적 품질 경영 (TQM)이 고객 만족도 향상, 모든 관리자 및 직원의 참여 우선 순위 부여, 양적 방법 사용을 위한 경영 시스템 전략 및 통합이라고 주장했습니다 (Bhat dan Cozzolino, 1993). ISO 9001: 2008에 따르면 품질 경영 시스템의 채택은 조직의 전략적 결정으로 바람직합니다. 조직의 품질 경영 시스템의 설계 및 구현은 조직 환경, 다양한 필요성, 주요 목표, 사용 가능한 제품, 적용된 공정, 조직 규모 및 구조에 의해 영향을 받습니다.
기존 연구 현황:
조직은 품질 정책, 품질 목표, 감사 결과, 데이터 분석, 개선 및 예방 조치, 경영진 고려 사항을 사용하여 품질 경영 시스템의 효과성을 지속적으로 개선해야 합니다. 조직은 재발 방지를 위해 부적합 원인을 줄이기 위한 개선 조치를 취해야 합니다. 예방 조치는 발생할 수 있는 문제의 예방에 정확해야 합니다. PDCA 사이클은 지속적인 개선을 창출하는 데 사용되는 방법이며 작업 프로세스 또는 프로그램 실행에 효과적으로 사용됩니다. PDCA 사이클은 임시 및 영구적 개선과 같은 두 가지 유형의 개선을 수행할 수 있습니다. 7가지 도구 (7가지 품질 보조 도구)는 일본에서 유래된 용어이며 품질 서클 및 지속적인 개선과 분리될 수 없습니다. 7가지 도구는 파레토 다이어그램, 특성 요인도, 체크 시트, 히스토그램, 산점도, 순서도, 관리도입니다.
연구의 필요성:
불량 제품은 생산 공정에서 바람직하지 않은 품질 편차이며 산업 현장에서 주요 문제 중 하나입니다. 모터사이클 실린더 부품의 주조 공정은 4.47%의 불량률로 회사 목표인 3.6%를 초과하는 불량 제품 문제를 가지고 있습니다. 따라서 목표를 달성하기 위해 불량률을 줄이기 위한 개선 및 예방 조치가 필요합니다.
4. 연구 목적 및 연구 질문:
연구 목적:
본 연구의 주요 목적은 다이캐스팅 공정에서 모터사이클 실린더 부품의 불량률을 줄여 회사 목표인 3.6% 이하로 달성하는 것입니다.
핵심 연구:
본 연구는 다이캐스팅으로 생산된 모터사이클 실린더 부품의 누설 문제 원인을 분석하고 PDCA 방법론과 7가지 도구를 사용하여 불량률을 줄이기 위한 개선 및 예방 조치를 구현하는 데 중점을 둡니다.
연구 가설:
본 논문에서는 연구 가설을 명시적으로 언급하지 않았습니다. 그러나 PDCA 및 7가지 도구를 적용하고, 결함의 근본 원인 (언더컷 및 기공)을 식별하고, 개선 및 예방 조치를 구현함으로써 불량률을 4.47%에서 목표인 3.6% 이하로 줄일 수 있다는 가설을 암묵적으로 제시합니다.
5. 연구 방법론
연구 설계:
본 연구는 PDCA 방법론과 7가지 도구를 사용하여 모터사이클 실린더 부품 누설 문제의 주조 공정의 불량 문제를 분석합니다. 연구 방법론 단계는 문제 정의, 연구 목표 결정, 문헌 고찰, 연구 범위 설정, 데이터 수집 및 계산, 데이터 분석, 개선 조치 개발, 예방 조치 개발, 연구 결과 결론 도출입니다.
데이터 수집 방법:
예비 데이터는 다이캐스팅 섹션에서 10개월 동안 발생한 실린더 부품 불량 데이터이며, 생산 공정 생산 시스템 데이터베이스에서 수집되었습니다. 연구와 동일한 해에 A 생산 공정 생산 시스템에서 10개월 동안의 실린더 부품 다이캐스팅 불량 공정 데이터는 표 1에 나와 있습니다.
분석 방법:
데이터 집계는 주요 불량 실린더 부품 유형을 결정하기 위해 처리되었습니다. 데이터 분석은 PDCA 방법론과 품질 보조 도구인 7가지 도구를 사용하여 주요 불량 제품 유형의 모든 원인 요인, 즉 실린더 부품의 누설 문제를 분석하기 위해 수행되었습니다. 5 Why 분석은 PICA-PA 설명의 분석 프로세스 일부로 언급됩니다. 파레토 다이어그램은 개선 조치에서 우선 순위를 둘 불량 제품 유형을 결정하는 데 사용됩니다. 특성 요인도는 실린더 부품의 언더컷 및 기공 문제의 원인 요인을 이해하는 데 사용됩니다.
연구 대상 및 범위:
본 연구의 문제 범위는 다이캐스팅 섹션에서 생산된 실린더 부품에만 국한되며, 마감 방법은 PDCA 및 7가지 도구인 품질 보조 도구와 개선 조치를 사용합니다.
6. 주요 연구 결과:
핵심 연구 결과:
예비 데이터는 10개월 동안의 실린더 부품 불량률이 4.47%로 목표인 3.6%를 초과하는 것으로 나타났습니다. 파레토 다이어그램은 총 67.57%의 불량률을 나타내는 4가지 불량 유형을 보여줍니다: 슬리브 윤활 볼트 누설 (26.92%), 슬리브-레그 실드 누설 (18.06%), 오일 파이프-레그 실드 누설 (14.24%), 누설 시험기 누설 (8.35%). 분석 결과 문제의 원인은 실린더 부품의 언더컷 및 기공으로 나타났습니다. 실린더 부품의 누설 결함을 유발할 수 있는 모든 요인을 해결하기 위해 개선 조치가 수행되었습니다. 개선 조치 후 5개월 동안 불량 데이터를 수집한 결과, 5개월 동안의 총 불량 실린더 부품률은 3.17%로 나타났으며, 이는 최대 제한 불량률인 3.60% 미만입니다.
제시된 데이터 분석:
표-1. 실린더 부품 제조 결함.
결함 | 수량 | % |
---|---|---|
슬리브 윤활 볼트 누설 | 7426 | 1.20 |
슬리브-레그 실드 누설 | 4984 | 0.81 |
오일 파이프-레그 실드 누설 | 3930 | 0.64 |
부품 분리 | 3068 | 0.50 |
누설 시험기 누설 | 2303 | 0.37 |
기타 * | 5879 | 0.95 |
합계 | 27590 | 4.47 |
그림-2. 실린더 부품 결함의 파레토 다이어그램.
[그림-2. 실린더 부품 결함의 파레토 다이어그램. 은 논문에 설명된 대로 여기에 제시됩니다.]
그림-3. 실린더 부품 누설 장애의 주요 원인 분석.
[그림-3. 실린더 부품 누설 장애의 주요 원인 분석. 은 논문에 설명된 대로 여기에 제시됩니다.]
그림-4. 언더컷 실린더 부품의 원인-결과 다이어그램.
[그림-4. 언더컷 실린더 부품의 원인-결과 다이어그램. 은 논문에 설명된 대로 여기에 제시됩니다.]
그림-5. 기공 실린더 부품의 원인-결과 다이어그램.
[그림-5. 기공 실린더 부품의 원인-결과 다이어그램. 은 논문에 설명된 대로 여기에 제시됩니다.]
표-2. 누설 실린더 부품의 예방 조치.
유지 보수 항목 | 주기 | 담당자 |
---|---|---|
재료 | ||
유지로 온도 제어 | 1시간 | 용해 작업자 |
유지로 청소 | 2주 | 용해 작업자 |
유지로 교체 | 2년 | 공정 엔지니어링 |
기계 | ||
질소 압력 점검 | 1개월 | 기술자 |
유압유 점검 | 매 생산 시작 시 | 다이캐스팅 작업자 |
유압유 교체 | 1년 | 공정 엔지니어링 |
플런저 팁 교체 | 7,000 샷/NG | 기술자 |
플런저 슬리브 교체 | 60,000 샷/NG | 기술자 |
자동 스프레이 교체 | 10,000 샷 | 기술자 |
자동 스프레이 청소 | 10,000 샷 | 기술자 |
스프레이 펌프 점검 | 1개월 | 공정 엔지니어링 |
다이 | ||
슬라이드 코어 및 다이 핀 유지보수 | 3,000 샷 | 다이 유지보수 |
다이 유지보수 및 교체 | 10,000 샷 | 다이 유지보수 |
작업자 | ||
기술 역량 업그레이드 | 6개월 | 섹션 책임자 |
표-3. 수리 후 실린더 부품 결함 데이터.
결함 | 수량 | % |
---|---|---|
슬리브-레그 실드 누설 | 2,683 | 0.92 |
슬리브 윤활 볼트 누설 | 1,288 | 0.44 |
오일 파이프-레그 실드 누설 | 559 | 0.19 |
부품 분리 | 1,117 | 0.38 |
누설 시험기 누설 | 695 | 0.24 |
기타 | 2,922 | 1.00 |
합계 | 9,264 | 3.17 |
그림 목록:
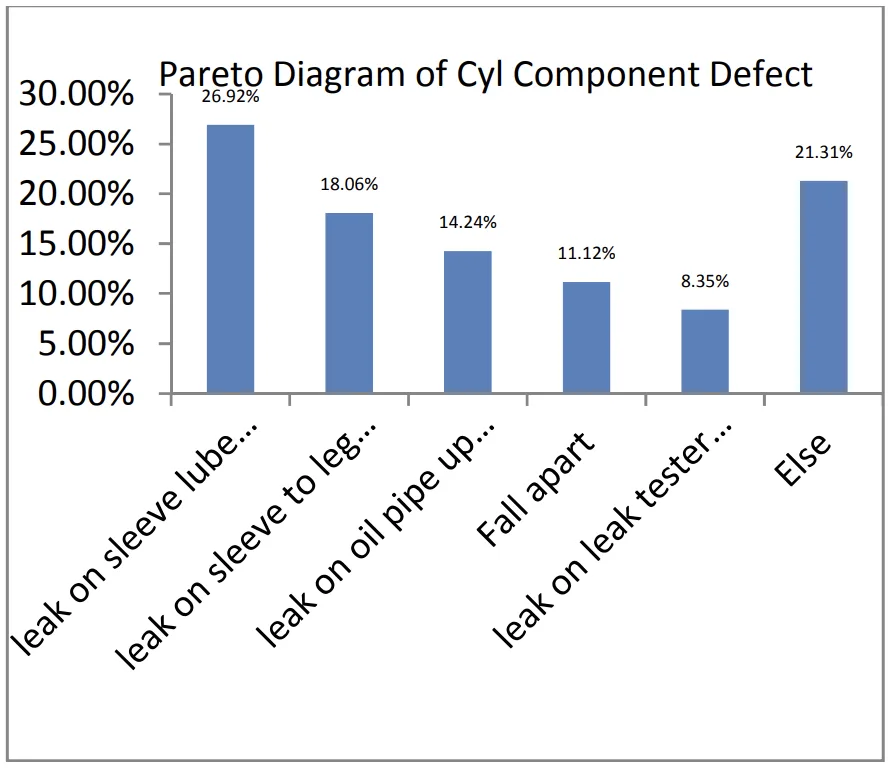
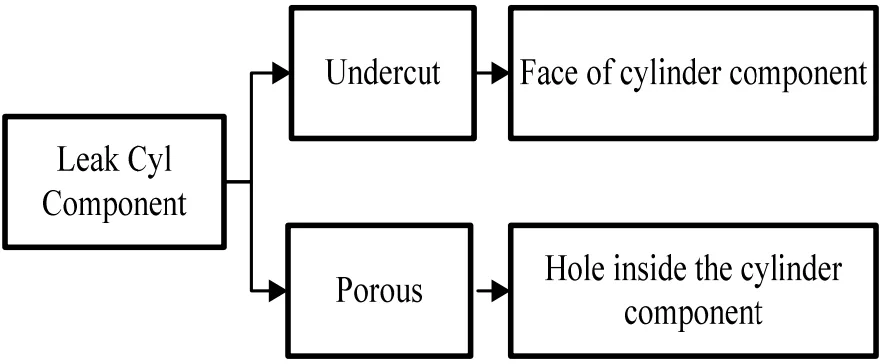
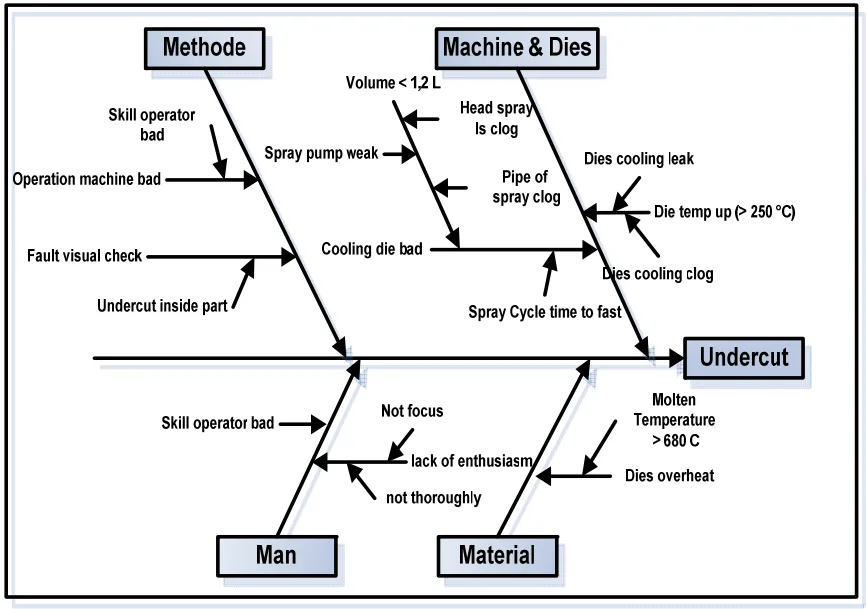
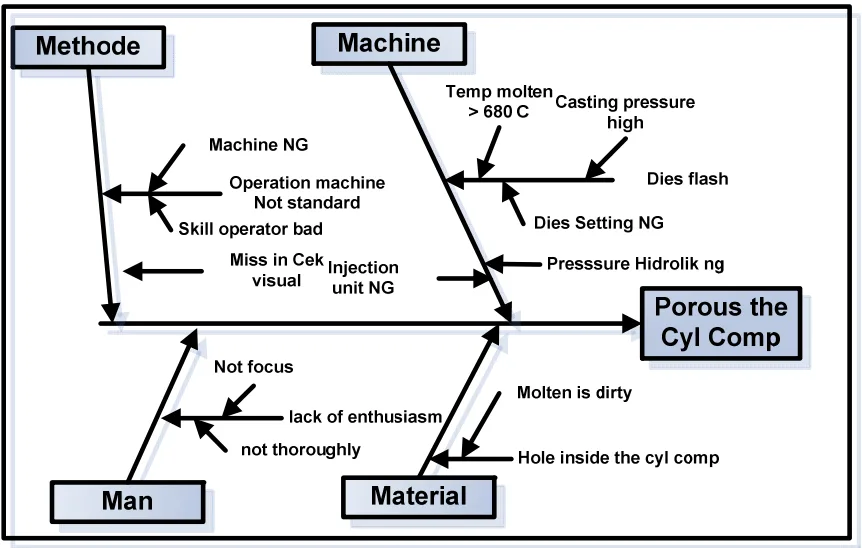
- 그림-1. 지속 가능한 개선의 PDCA 사이클.
- 그림-2. 실린더 부품 결함의 파레토 다이어그램.
- 그림-3. 실린더 부품 누설 장애의 주요 원인 분석.
- 그림-4. 언더컷 실린더 부품의 원인-결과 다이어그램.
- 그림-5. 기공 실린더 부품의 원인-결과 다이어그램.
7. 결론:
주요 결과 요약:
본 연구는 PDCA 및 7가지 품질 도구를 사용한 개선 및 예방 조치가 실린더 부품의 불량률을 4.47%에서 3.17%로 감소시켜 목표인 3.6% 이하를 달성하는 데 효과적이었다는 결론을 내렸습니다. 주요 결함 원인은 재료 품질 (오염된 용융 재료, 온도), 기계 상태 (자동 스프레이 장치, 사출 압력, 다이 오버헤드) 및 작업자 기술과 관련된 문제에서 비롯된 언더컷 및 기공으로 확인되었습니다.
연구의 학문적 의의:
본 연구는 다이캐스팅 공정에서 PDCA 및 7가지 품질 도구를 사용하여 품질 문제를 체계적으로 분석하고 해결하는 실제 적용 사례를 보여줍니다. 이는 제조, 특히 다이캐스팅 및 모터사이클 부품 생산 분야에서 품질 경영에 대한 지식 체계에 기여합니다.
실용적 의미:
본 연구 결과는 다이캐스팅 산업이 제품 품질을 개선하고 불량률을 줄이기 위한 실용적인 프레임워크를 제공합니다. 용융 금속 온도 유지, 스프레이 장치 성능 최적화, 정기적인 다이 유지 보수와 같이 본 논문에서 확인된 특정 개선 및 예방 조치는 실린더 부품의 누설 결함을 해결하기 위해 직접적으로 구현될 수 있습니다. 본 논문에 제시된 PICA-PA (문제 식별 개선 조치 및 예방 조치) 접근 방식은 ISO 9000 표준에 부합하는 생산 공정의 문제 해결 및 문서화를 위한 구조화된 방법을 제공합니다.
연구의 한계 및 향후 연구 분야:
본 연구에서는 작업자 일관성, 기계 안정성, 다이 설계 등 일부 요인이 완전히 분석되지 않았음을 인정합니다. 향후 연구에서는 다이캐스팅 공정을 더욱 최적화하고 결함을 최소화하기 위해 이러한 요인을 더 깊이 탐구할 수 있습니다. 누설 결함 감지를 위한 고급 검사 방법에 대한 추가 연구도 유익할 수 있습니다.
8. 참고 문헌:
- Baldwin R.M. Corrective/Preventive Actio (CAPA) Guide lines. http://www.rmbimedical.com/regulatoryAffairs/CAPAMai n.aspx.
- Bhat, V. And J Cozzolino. 1993. Total Quality: An Effective Management Tool. www.casact.org.pp. 101-123. Agustus 2005.
- Dahlgaard Jens J., Kanji, Gopal K and Kristensen Kai. 2002. Fundamentals of Total Quality Management. London and New York: Taylor and Francis Group.
- Feigenbaum, A.V.1991. Total Quality Control. New York: McGraw-Hill.
- ISO. 2008. Quality Management System Requirement (4th edition). Switzerland: Author.
- Montgomery, Douglas. 2005. Introduction to Statistical Quality Control. Hoboken, New Jersey: John Wiley andSons, Inc.
- Nazlina. 2005. Studi Pengendalian Jumlah Cacat dengan Menggunakan Metode Poka Yoke di PT. Morawa Electric Transbuana. Jurnal Sistem Teknik Industri. 6(4).
- Pipan K. Kern., Pavletic D. and Sokovic M. 2010. Quality Improvement Methodologies – PDCA Cycle, RADAR Matrix, DMAIC and DFSS. Journal of Achievements in Materials and Manufacturing Engineering. 1: 476-483.
- Schneiderman Arthur M. 1998. Are There Limits to Total Quality Management. Journal of Strategy Management Competition. (11): 35-45.
- Sokovic M., Pavletic, D. and Krulcic D. 2006. Six Sigma Process Improvements in Automotive Parts Production. Journal of Achievements in Materials and Manufacturing Engineering. 19: 96-102.
9. 저작권:
- 본 자료는 "[Rahmat Nurcahyo]"의 논문: "[모터사이클 실린더 부품 누설 문제의 주조 공정 개선 및 예방 조치]"를 기반으로 합니다.
- 논문 출처: https://www.researchgate.net/publication/312062708
본 자료는 위 논문을 소개하기 위해 제작되었으며, 상업적 목적으로 무단 사용하는 것을 금지합니다.
Copyright © 2025 CASTMAN. All rights reserved.