본 논문 요약은 ['Design of Three Cavity Diecasting Die for Rotors'] 논문을 기반으로 작성되었으며, 발행처는 ['International Journal of Engineering Research & Technology (IJERT)'] 입니다.
1. 개요:
- 제목: 로터용 3 캐비티 다이캐스팅 금형 설계 (Design of Three Cavity Diecasting Die for Rotors)
- 저자: S Chandra Sekhar, Sk.Surjan, M.S. Phani Deep Kumar
- 발행 연도: 2017년
- 발행 저널/학술 단체: International Journal of Engineering Research & Technology (IJERT)
- 키워드: 설계, 다이캐스팅, CATIA, 로터
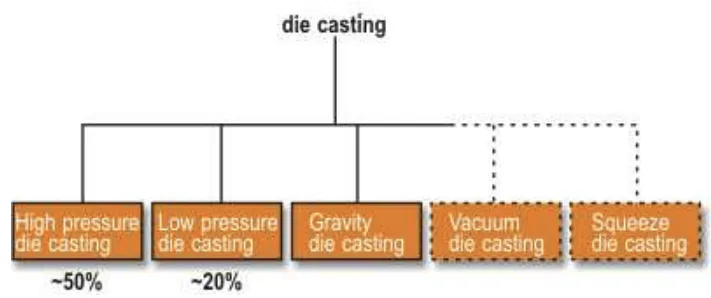
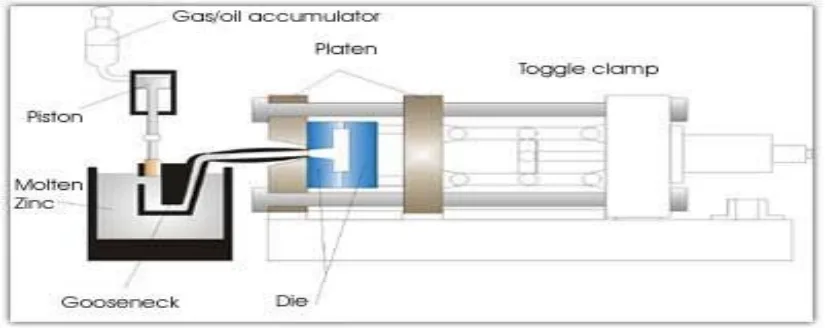
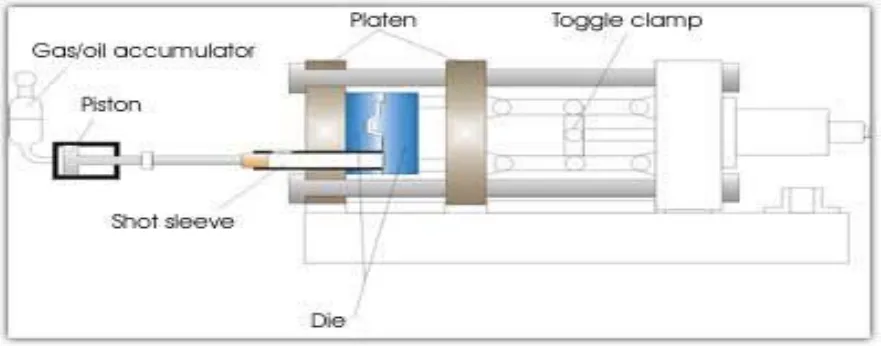
2. 초록 또는 서론
초록
"다이캐스팅 부품은 현대 세계의 모든 측면에서 중요한 역할을 합니다. 그 영향력은 가정용 기구부터 자동차 부품까지 다양합니다. 오늘날 세계의 요구 사항은 생산, 정확성 및 호환성으로, 이는 경쟁에 부응하는 데 도움이 됩니다. 이러한 과제를 충족하기 위해 다이캐스팅 공정은 생산에서 중요한 역할을 합니다. 대량 생산은 단위 비용을 줄이고 쉬운 조립을 용이하게 하기 위해 높은 생산성을 목표로 합니다. 다이캐스팅 부품의 경우 추가 가공이 필요 없고 표면 마감이 양호한 부품을 얻을 수 있습니다. 설계 및 생산 리드 타임을 단축하는 데 도움이 되는 컴퓨터 지원 설계. 본 논문은 로터용 다이캐스팅 금형 설계에 대한 공학적 접근 방식을 제시하고 CATIA V5 소프트웨어를 사용하여 3 캐비티 다이캐스팅 금형 설계를 다룹니다. 본 연구에서는 컴퓨터 지원 3 캐비티 다이캐스팅 금형 설계가 기존의 로터용 2 캐비티 다이캐스팅 금형 설계를 대체합니다. 본 논문에서는 hcher 블록의 캐비티 및 코어 인상을 hchcr 인서트로 대체합니다.
키워드- 설계, 다이캐스팅, CATIA, 로터"
I. 서론
"다이캐스팅은 금속 가공 산업에서 제조되는 가장 많은 양의 대량 생산 품목이며, 수천 가지의 소비재, 상업용 및 산업용 제품에서 찾아볼 수 있습니다. 다이캐스팅 부품은 자동차에서 장난감에 이르기까지 제품의 중요한 구성 요소입니다. 부품은 싱크대 수도꼭지처럼 단순하거나 커넥터 하우징처럼 복잡할 수 있습니다. 중력 압력 주조와 반대되는 압력 주입에 의한 다이캐스팅의 가장 초기 사례는 1800년대 중반에 발생했습니다. 1849년에 Sturges에게 인쇄 활자 주조용 최초의 수동 작동 기계에 대한 특허가 수여되었습니다. 이 공정은 향후 20년 동안 프린터 활자에 국한되었지만, 세기말을 향해 다른 모양의 개발이 증가하기 시작했습니다. 1892년까지 상업적 응용 분야에는 축음기 및 금전 등록기 부품이 포함되었으며, 1900년대 초에 많은 유형의 부품의 대량 생산이 시작되었습니다. 최초의 다이캐스팅 합금은 다양한 주석 및 납 조성물이었지만, 1914년에 아연 및 알루미늄 합금이 도입되면서 사용이 감소했습니다. 마그네슘 및 구리 합금이 빠르게 뒤따랐고, 1930년대에는 많은 현대 합금이 존재하게 되어 사용 가능하게 되었습니다. 다이캐스팅 공정은 원래의 저압 주입 방식에서 제곱인치당 4500파운드를 초과하는 힘으로 고압 주조, 스퀴즈 주조 및 반고체 다이캐스팅을 포함한 기술로 발전했습니다. 이러한 현대적인 공정은 우수한 표면 마감으로 높은 무결성, 네트 셰이프에 가까운 주조품을 생산할 수 있습니다. 다이캐스팅에 사용되는 합금과 공정 자체 모두에서 개선이 계속되어 다이캐스팅 응용 분야가 거의 모든 알려진 시장으로 확장되고 있습니다. 한때 단순한 납 활자에 국한되었던 오늘날의 다이캐스터는 다양한 크기, 모양 및 두께의 주조품을 생산할 수 있으며, 이는 강하고 내구성이 뛰어나며 치수적으로 정확합니다."
3. 연구 배경:
연구 주제 배경:
본 논문은 현대 제조에서 다이캐스팅의 중요한 역할을 강조하며, 가정용품부터 자동차 부품에 이르기까지 광범위한 적용 가능성을 강조합니다. 현대 산업의 요구 사항은 높은 생산량, 치수 정확도 및 부품 호환성입니다. 다이캐스팅은 생산성 향상, 단위 비용 최소화 및 쉬운 조립 보장을 통해 대량 생산 시나리오에서 이러한 요구 사항을 효과적으로 해결합니다. 또한 다이캐스팅 부품은 몰드에서 직접 원하는 표면 마감을 얻어 광범위한 후처리 가공의 필요성을 없애는 경우가 많습니다. CAD(Computer-Aided Design)의 통합은 설계 및 생산 단계를 간소화하고 리드 타임을 단축하며 전반적인 효율성을 향상시키는 데 중추적인 요소로 강조됩니다.
기존 연구 현황:
본 연구 이전에는 로터 생산을 위한 일반적인 금형 설계는 2 캐비티 구성을 사용했습니다. 이러한 전통적인 접근 방식은 기능적이지만, 증가하는 산업 수요를 충족하는 데 필요한 더 높은 생산 속도를 달성하는 데 한계가 있었습니다.
연구의 필요성:
본 연구의 동기는 로터 다이캐스팅의 생산성을 향상시켜야 할 필요성에서 비롯됩니다. 본 연구는 기존의 2 캐비티 금형에서 보다 효율적인 3 캐비티 금형 설계로 전환할 것을 제안함으로써 이를 해결합니다. 또한, 본 논문은 볼스터 블록의 일체형 캐비티 및 코어 인상을 경화 및 템퍼링된 크롬 열간 금형강(HCHCr) 인서트로 대체함으로써 금형 수명을 최적화하고 제조 비용을 절감하는 것을 목표로 합니다. 이러한 모듈식 접근 방식은 마모가 심한 부품의 유지 보수 및 교체를 용이하게 하여 금형의 작동 수명을 연장하고 전체 툴링 비용을 절감합니다.
4. 연구 목적 및 연구 질문:
연구 목적:
본 연구의 주요 목적은 CATIA V5 소프트웨어의 설계 및 시뮬레이션 기능을 활용하여 로터용 3 캐비티 다이캐스팅 금형을 엔지니어링하는 것입니다. 이 설계는 기존의 2 캐비티 금형 패러다임을 대체하여 향상된 생산 효율성을 제공하는 것을 목표로 합니다. 두 번째이지만 중요한 목적은 캐비티 및 코어 영역에 HCHCr 인서트를 통합하는 것입니다. 이러한 전략적 재료 선택 및 설계 수정은 금형 내구성을 개선하고 유지 보수를 단순화하며 금형 마모 및 교체와 관련된 장기적인 운영 비용을 절감하기 위한 것입니다.
주요 연구:
본 연구는 3 캐비티 다이캐스팅 금형의 설계 및 분석에 중점을 둡니다. 주요 연구 분야는 다음과 같습니다.
- 다중 캐비티 금형 설계: 사이클당 생산량 증가를 위해 3개의 로터 캐비티를 수용하는 금형 구성 개발.
- CAD 응용: 개념화부터 상세 엔지니어링 도면 및 조립 모델링에 이르기까지 전체 설계 프로세스에 CATIA V5 소프트웨어 활용.
- 2-3 캐비티 금형 전환: 기존 2 캐비티 금형을 직접 대체하도록 엔지니어링하여 생산성을 향상시키면서 현재 다이캐스팅 기계와의 호환성 보장.
- HCHCr 인서트 구현: 금형 수명을 개선하고 유지 보수를 줄이기 위해 중요한 마모 부품(캐비티 및 코어)에 HCHCr 인서트를 설계 및 통합.
연구 가설:
공식적인 가설로 명시되지는 않았지만, 본 연구는 다음과 같은 예상 결과에 기반합니다.
- 생산성 향상: 3 캐비티 금형은 2 캐비티 금형에 비해 사이클당 생산되는 로터 주조품 수를 눈에 띄게 증가시켜 전반적인 생산 속도를 높일 것입니다.
- 운영 비용 절감: HCHCr 인서트의 사용은 인서트의 향상된 내마모성 및 교체 가능성으로 인해 금형 유지 보수 빈도 및 비용을 줄일 것입니다.
- 설계 효율성 향상: CATIA V5를 사용하면 설계 프로세스를 간소화하고 설계 오류를 줄이며 금형 개발 및 제조 리드 타임을 단축할 수 있습니다.
5. 연구 방법론
연구 설계:
본 연구는 CAD(Computer-Aided Design) 기반 접근 방식을 사용합니다. 개별 부품 및 다중 캐비티 구성을 포함한 전체 금형 어셈블리는 CATIA V5 소프트웨어를 사용하여 설계 및 가상 조립됩니다. 이 방법론을 통해 물리적 제조 전에 정확한 치수 제어, 간섭 검사 및 전체 금형 구조 시각화가 가능합니다.
자료 수집 방법:
본 연구의 주요 자료는 설계 과정 자체를 통해 생성됩니다. 여기에는 다음이 포함됩니다.
- CAD 모델: CATIA V5 내에서 모든 금형 부품(고정 금형 반쪽, 이동 금형 반쪽, 캐비티 인서트, 코어 인서트, 러너, 게이트 등)의 상세 3D 모델 생성.
- 엔지니어링 도면: 제조를 위한 치수, 공차, 재료 및 열처리 요구 사항을 지정하는 3D 모델에서 파생된 2D 엔지니어링 도면 제작.
- 계산된 매개변수: 게이트 속도, 게이트 면적, 러너 치수, 사출 압력 및 금형 체결력과 같은 중요한 다이캐스팅 매개변수를 확립된 경험적 공식 및 다이캐스팅 원리를 통해 결정. 이러한 계산은 알루미늄 합금의 재료 속성 및 로터 부품의 형상을 기반으로 합니다.
분석 방법:
본 연구의 분석은 주로 엔지니어링 계산 및 CAD 소프트웨어 기능을 기반으로 합니다.
- 체적 및 면적 계산: CATIA V5는 주조품, 러너 시스템 및 비스킷의 체적과 체결력 결정을 위한 투영 면적을 계산하는 데 사용됩니다.
- 경험적 공식 적용: 확립된 다이캐스팅 방정식 및 경험적 데이터(표 I. 벽 두께에 따른 일반적인 캐비티 충전 시간 및 표 II. 게이트 속도)는 게이트 크기, 러너 치수, 사출 매개변수 및 체결력을 계산하는 데 활용됩니다.
- 소프트웨어 시각화 및 검증: CATIA V5의 시각화 도구는 적절한 조립을 보장하고 잠재적인 설계 결함을 식별하며 물리적 구현 전에 전체 금형 설계를 검증하는 데 사용됩니다.
연구 대상 및 범위:
본 연구의 주제는 로터용 다이캐스팅 금형 설계입니다. 범위는 다음으로 제한됩니다.
- 금형 설계: 3 캐비티 냉간 챔버 다이캐스팅 금형의 전체 설계에 중점.
- 부품 재료: 로터 주조용 99.6% 순수 알루미늄 및 0.4% 기타 금속을 함유한 알루미늄 단조 합금 활용.
- 금형 재료 선택: 캐비티 및 코어 인서트용 H13 강, 기타 금형 부품용 EN-31, EN-36, OHNS 및 M.S.를 포함하여 금형 부품용 재료 지정(표 V. 재료 명세서에 자세히 설명).
- 기계 호환성: 400 T Buhler 수평 냉간 챔버 다이캐스팅 기계와 호환되도록 금형 설계.
6. 주요 연구 결과:
주요 연구 결과:
본 연구의 주요 결과는 CATIA V5 소프트웨어를 사용하여 달성한 로터용 3 캐비티 다이캐스팅 금형의 완전한 CAD 설계입니다. 주요 결과는 다음과 같습니다.
- 3 캐비티 금형 설계: 기존의 2 캐비티 설정을 대체하는 3 캐비티 금형에 대한 완전한 상세 설계가 등각 투영도 및 단면도(Fig: 8 3 캐비티 금형 고정 금형 반쪽 조립도, Fig: 9 3 캐비티 금형 이동 금형 반쪽 조립도, Fig: 10 3 캐비티 금형 전체 조립도, Fig: 11 3 캐비티 금형 전체 조립도 도면)를 통해 제시됩니다.
- 상세 부품 설계: 캐비티 인서트, 코어 인서트, 러너 시스템, 게이팅, 이젝터 시스템 및 볼스터 플레이트를 포함한 금형의 개별 부품이 표 V. 재료 명세서에 나열된 재료 및 치수로 설계 및 지정됩니다.
- 계산된 다이캐스팅 매개변수: 다음과 같은 중요한 공정 매개변수가 계산되었습니다.
- 게이트 속도: 3760cm/sec
- 충전 속도: 8130 cm³/sec
- 사출 압력: 700 kg/cm²
- 체결력: 202.65 톤
- 생산 속도 증가: 설계된 3 캐비티 금형은 사이클 시간 분석을 기반으로 하루 2160개 부품(2 캐비티 금형의 경우)에서 하루 3240개 부품으로 생산량을 늘릴 것으로 예상됩니다.
제시된 데이터 분석:
본 논문은 설계 및 분석을 뒷받침하기 위해 다양한 그림과 표를 제시합니다.
- Fig: 1 다이캐스팅 유형: 다양한 다이캐스팅 공정을 보여주며, 고압 다이캐스팅의 보급률을 강조합니다.
- Fig: 2 열간 챔버 다이캐스팅 기계 & Fig: 3 냉간 챔버 다이캐스팅 기계: 알루미늄에 대한 선택된 냉간 챔버 접근 방식과 관련된 열간 및 냉간 챔버 다이캐스팅 공정의 개략도를 묘사합니다.
- Fig: 4 기존 2 캐비티 고정 금형 반쪽 & Fig: 5 기존 2 캐비티 이동 금형 반쪽: 기존 2 캐비티 금형의 단면도를 보여주며, 비교를 위한 기준선을 제공합니다.
- Fig: 6 로터 라미네이션 부품 & Fig: 7 로터 다이캐스팅 부품: 로터 부품을 라미네이션 및 최종 다이캐스팅으로 보여줍니다.
- Fig: 8 3 캐비티 금형 고정 금형 반쪽 조립도 & Fig: 9 3 캐비티 금형 이동 금형 반쪽 조립도: 설계된 3 캐비티 금형 반쪽의 등각 투영도를 제시합니다.
- Fig: 10 3 캐비티 금형 전체 조립도 & Fig: 11 3 캐비티 금형 전체 조립도 도면: 전체 조립된 금형을 등각 투영도 및 단면도로 보여주며, 부품 배열을 자세히 설명합니다.
- 표 I. 벽 두께에 따른 일반적인 캐비티 충전 시간 & 표 II. 게이트 속도: 벽 두께 및 합금 유형에 따라 게이트 매개변수를 계산하는 데 사용되는 경험적 데이터를 제공합니다.
- 표 III. 수평 냉간 챔버 압력 다이캐스팅 기계 400 T Buhler 사양 & 표 IV. 생산 데이터: 금형 설계 및 성능 계산과 관련된 기계 매개변수 및 생산 데이터를 지정합니다.
- 표 V. 재료 명세서: 제조를 위한 재료, 치수 및 열처리 사양과 함께 모든 금형 부품을 나열합니다.
제시된 데이터는 기능적이고 효율적인 3 캐비티 금형을 달성하기 위해 경험적 데이터와 엔지니어링 계산을 통합한 체계적인 금형 설계 접근 방식을 보여줍니다. 2160개에서 3240개 부품으로 예상되는 생산량 증가는 3 캐비티 설계로 인한 효율성 향상을 강조합니다.
그림 이름 목록:
- Fig: 1 다이캐스팅 유형
- Fig: 2 열간 챔버 다이캐스팅 기계
- Fig: 3 냉간 챔버 다이캐스팅 기계
- Fig: 4 기존 2 캐비티 고정 금형 반쪽
- Fig: 5 기존 2 캐비티 이동 금형 반쪽
- Fig: 6 로터 라미네이션 부품
- Fig: 7 로터 다이캐스팅 부품
- Fig: 8 3 캐비티 금형 고정 금형 반쪽 조립도
- Fig: 9 3 캐비티 금형 이동 금형 반쪽 조립도
- Fig: 10 3 캐비티 금형 전체 조립도
- Fig: 11 3 캐비티 금형 전체 조립도 도면
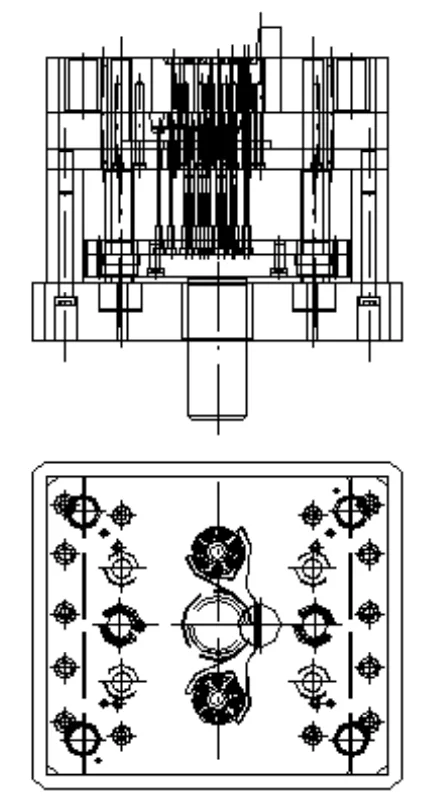
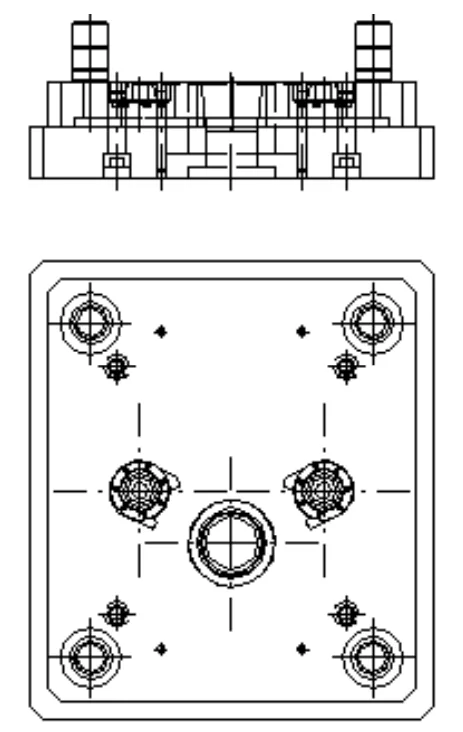
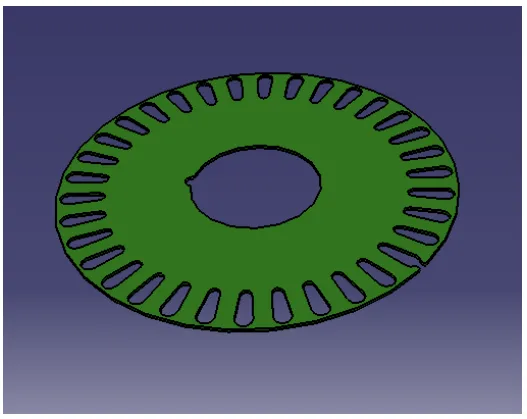
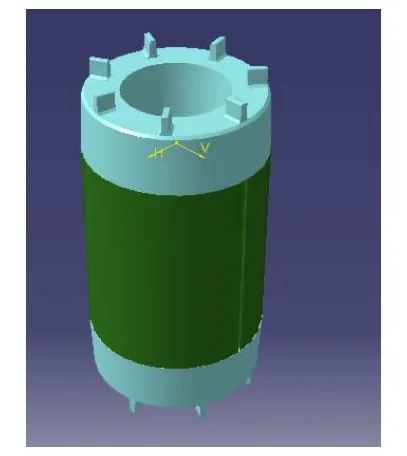
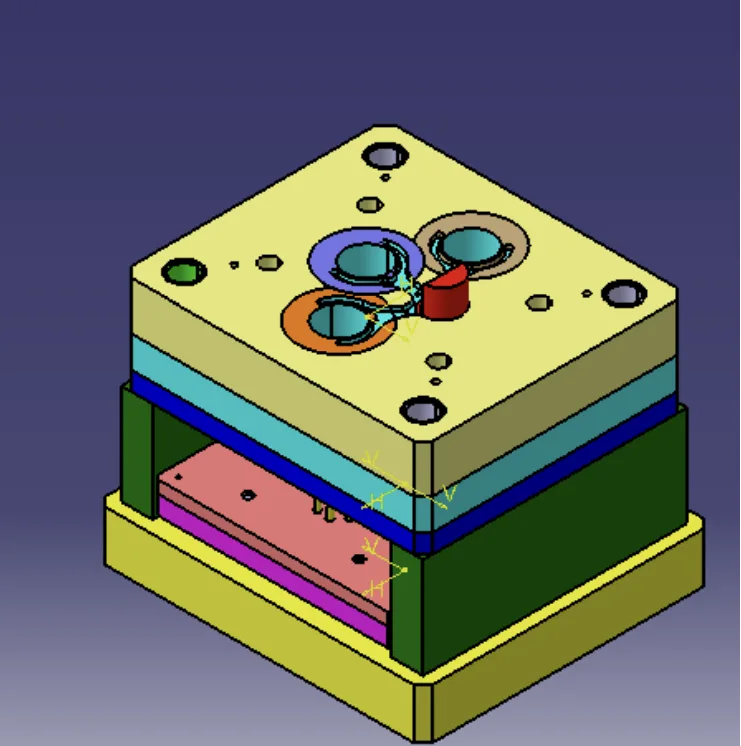
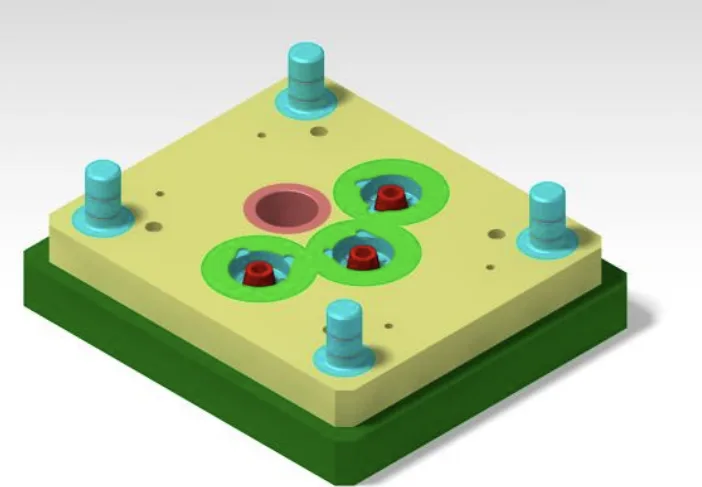
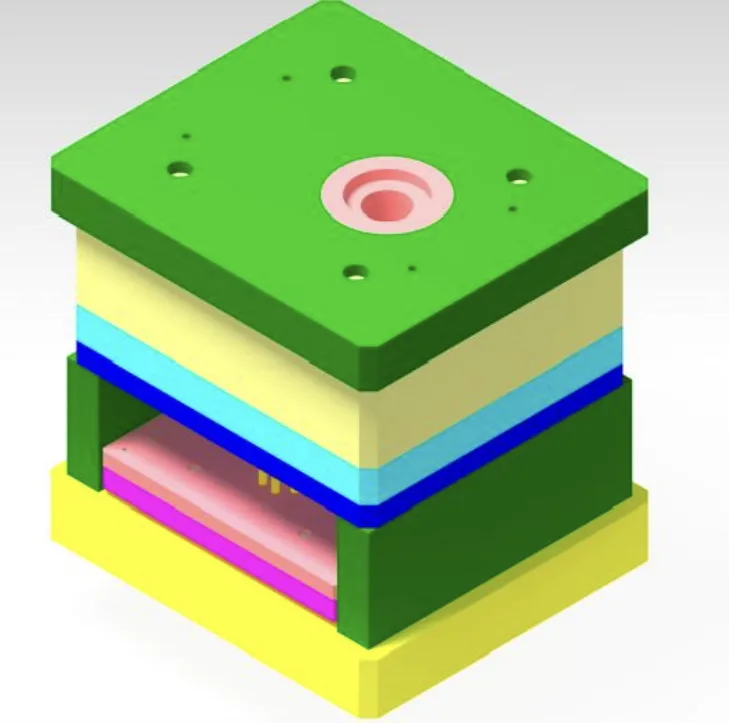
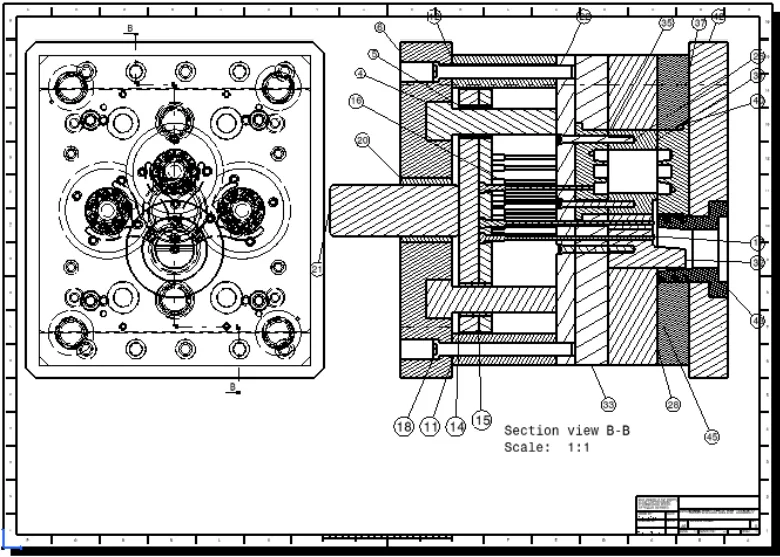
7. 결론:
주요 연구 결과 요약:
본 연구는 CAD 기술을 사용하여 로터용 3 캐비티 다이캐스팅 금형 설계를 성공적으로 입증했습니다. 주요 연구 결과는 다음과 같습니다.
- CAD 기반 설계 향상: CAD 구현은 기존 방법에 비해 설계 정확도를 크게 향상시키고 설계 리드 타임을 단축합니다.
- 생산성 향상: 3 캐비티 금형 구성으로의 전환은 주조 사이클당 생산되는 부품 수를 눈에 띄게 증가시켜 생산성 향상으로 이어집니다.
- 비용 및 유지 보수 감소: 3 캐비티 금형을 사용하면 2 캐비티 금형 시스템에 비해 단위 생산량당 인건비 및 유지 보수 비용이 절감될 것으로 예상됩니다.
- 인서트가 있는 모듈식 금형 설계: HCHCr 강철로 만든 교체 가능한 캐비티 및 코어 인서트를 통합하면 금형 제조 비용이 절감되고 유지 보수가 간소화됩니다. 중요한 영역의 손상은 인서트 교체만 필요로 하며, 전체 금형 플레이트를 교체하는 비용을 피할 수 있습니다.
연구의 학문적 의의:
본 연구는 다이캐스팅 분야에 다음과 같은 기여를 합니다.
- CAD 응용 사례 제시: 복잡한 다이캐스팅 툴링의 포괄적인 설계를 위해 CAD 소프트웨어(CATIA V5)를 적용하는 실제 사례 제공.
- 다중 캐비티 금형의 이점 입증: 대량 생산 시나리오에서 다중 캐비티 금형 구현을 통해 달성할 수 있는 생산성 향상 정량화.
- 모듈식 금형 설계의 장점 강조: 유지 보수성 및 비용 효율성 향상을 위해 인서트를 사용하는 모듈식 금형 설계의 장점 강조.
실용적 의미:
본 연구의 결과는 다이캐스팅 산업에 중요한 실용적 의미를 제공합니다.
- 산업 적용: 다이캐스팅 제조업체는 로터 생산을 위해 제시된 3 캐비티 금형 설계를 직접 채택하여 생산 능력 향상 가능.
- CAD 구현 장려: 본 연구는 효율성 및 정확성 향상을 위해 CAD 도구를 금형 설계 워크플로에 통합하는 것의 가치를 강조합니다.
- 모듈식 툴링 전략: 캐비티 및 코어 인서트의 사용은 툴링 비용을 최소화하고 유지 보수 및 수리와 관련된 가동 중지 시간을 줄이기 위해 금형 설계의 표준 관행으로 고려해야 합니다.
연구의 한계 및 향후 연구 분야:
본 연구는 주로 설계 단계 및 관련 계산에 중점을 둡니다. 한계는 다음과 같습니다.
- 실험적 검증 부족: 본 연구에는 설계된 3 캐비티 금형의 물리적 제조 및 테스트가 포함되어 있지 않습니다. 예상 생산량 증가는 경험적 테스트가 아닌 계산 및 사이클 시간 추정을 기반으로 합니다.
- 시뮬레이션 범위: CAD 설계는 포괄적이지만, 본 논문은 금형 설계 및 공정 매개변수를 더욱 최적화하기 위한 고급 시뮬레이션(예: 금형 충전, 열 분석)에 대해 자세히 설명하지 않습니다.
향후 연구 방향은 다음과 같습니다.
- 금형 제조 및 테스트: 설계된 3 캐비티 금형을 제작하고 물리적 다이캐스팅 시험을 수행하여 예측된 성능을 검증하고 개선 영역을 식별합니다.
- 공정 최적화: 금형 충전 및 열 시뮬레이션을 수행하여 향상된 주조 품질 및 사이클 시간 단축을 위해 게이트 설계, 러너 시스템, 냉각 채널 및 공정 매개변수를 최적화합니다.
- 재료 및 공정 탐색: 로터 주조 생산을 더욱 개선하기 위해 대체 금형 재료 및 고급 다이캐스팅 공정(예: 진공 다이캐스팅, 스퀴즈 다이캐스팅)을 조사합니다.
8. 참고 문헌:
- [1] A. P.Wadekar1, B.A.Ahire, L.G.Navalel, S.H.Gawande, R.Mathai, R.Mishra "Die Casting Defect Analysis & Experimental Validation for Compressor Housing" IOSR Journal of Mechanical and Civil Engineering (IOSR-JMCE) ISSN(e): 2278- 1684, ISSN(p): 2320-334X, PP: 55-61
- [2] M.R. Barone, D.A. Caulk, "Analysis of liquid metal flow in die casting", International Journal of Engineering Science 38 (24), (2000), pp. 1279-1302
- [3] RyosukeKimuraa, Haruaki Hatayamaa, Kenji Shinozakia, Izumi Murashimab, Jo Asadab, Makoto Yoshidac, "Effect of grain refiner and grain size on the susceptibility of Al-Mg die casting alloy to cracking during solidification", journal of materials processing technology 209 (1) (2009) pp.210-219.
- [4] PenghuaiFua, Alan A. Luob, HaiyanJianga, Liming Penga, YandongYua, ChunquanZhaia, Anil K. Sachdev, "Low-pressure die casting of magnesium alloy AM50: Response to process parameters", journal of materials processing technology 205 (2008) pp.224-234.
- [5] B.S. Sunga, I.S. Kimb, "The molding analysis of automobile parts using the die-casting system", journal of materials processing technology 201 (2009) pp. 635-639.
- [6] H.D. Zhao, F. Wang, "Modeling of mold filling of Al gravity casting and validation with X-ray in-situ observation", Journal of Materials Processing Technology 209 (2009) pp. 4537-4542.
- [7] Paul Cleary, Joseph Ha, Vladimir Alguine, Thang Nguyen "Flow modelling in casting processes", Applied Mathematical Modelling 26 (2002), pp.171-190.
9. 저작권:
- 본 자료는 "S Chandra Sekhar, Sk.Surjan, M.S. Phani Deep Kumar"의 논문: "로터용 3 캐비티 다이캐스팅 금형 설계"를 기반으로 합니다.
- 논문 출처: https://www.ijert.org/research/design-of-three-cavity-diecasting-die-for-rotors-IJERTV6IS020017.pdf
본 자료는 위 논문을 기반으로 요약되었으며, 상업적 목적으로 무단 사용하는 것을 금지합니다.
Copyright © 2025 CASTMAN. All rights reserved.