1. 개요:
- 제목: 다이 변형에 대한 구조 다이 및 기계 변수 효과 연구 (STUDY OF THE EFFECT OF STRUCTURAL DIE AND MACHINE VARIABLES ON DIE DEFLECTIONS)
- 저자: 지스 자비에르 키나팅갈, B.E. (Jeeth Xavier Kinatingal, B.E.)
- 발행 연도: 2005년
- 발행 저널/학회: 오하이오 주립대학교 (The Ohio State University)
- 키워드: 다이캐스팅, 다이 변형, 구조 다이 변수, 기계 변수, 파팅면 분리 (Die Casting, Die Deflection, Structural Die Variables, Machine Variables, Parting Plane Separation)
2. 연구 배경:
- 연구 주제의 사회적/학문적 맥락:
- 고압 다이캐스팅은 기능성 제품의 대량 생산을 위한 주요 생산 옵션 중 하나입니다.
- 다이캐스팅은 복잡한 설계 세부 사항과 정밀한 공차를 유지하면서 부품을 고속으로 주조할 수 있게 합니다.
- 고품질 주조품 생산을 위해서는 다이캐스팅 다이의 치수 무결성을 유지하는 것이 중요합니다.
- 다이캐스팅 다이는 다이캐스팅 사이클 동안 작용하는 열적 및 기계적 하중으로 인해 변형됩니다.
- 기존 연구의 한계:
- 이전 연구에서는 플래시 위치와 관련하여 시뮬레이션 결과와 현장 관찰을 성공적으로 일치시켰습니다.
- 그러나 핫 다이의 일부 응력 결과는 예상과 달라 불일치가 나타났습니다.
- 어떤 다이 및 기계 매개변수가 다이 변형에 유의미한 영향을 미치는지, 그리고 그 정도가 어느 정도인지 불분명했습니다.
- 연구의 필요성:
- 다이 및 기계 매개변수가 다이 변형에 미치는 영향을 이해하는 것이 필수적입니다.
- 다이 변형 및 왜곡을 최소화하기 위한 구조적 수정 사항을 구현하려면 이러한 이해가 필요합니다.
- 다이 변형 및 왜곡을 최소화하는 것은 궁극적으로 부품 왜곡을 최소화하고 다이캐스트 제품의 품질을 향상시키는 데 기여합니다.
3. 연구 목적 및 연구 질문:
- 연구 목적:
- 구조 다이 및 기계 변수가 다이 변형에 미치는 영향을 연구합니다.
- 상업용 다이캐스팅 다이의 이전 응력 분석 결과에서 관찰된 불일치를 명확히 합니다.
- 주요 연구 질문:
- 다이 및 기계 변수는 최대 파팅면 분리에 어떤 영향을 미치는가?
- 어떤 주요 변수가 파팅면 분리에 가장 큰 영향을 미치는가?
- 연구 가설:
- 본 연구는 다양한 변수와 그 상호 작용의 영향을 이해하기 위해 최대 파팅면 분리에 대한 예측 모델을 생성하는 것을 목표로 합니다.
- 또한, 연구 결과에 기반하여 다이 설계 및 기계 선택에 대한 지침을 설정하고자 합니다.
4. 연구 방법론
- 연구 설계:
- 본 연구는 두 부분으로 나뉩니다:
- 상업용 다이캐스팅 다이에 대한 연구의 지속 및 결론.
- 구조 다이 및 기계 변수가 다이 변형에 미치는 영향을 조사하기 위한 전산 매개변수 연구.
- 본 연구는 두 부분으로 나뉩니다:
- 자료 수집 방법:
- ABAQUS 시뮬레이션을 사용하여 연구의 두 부분 모두에 대한 데이터를 생성했습니다.
- 매개변수 연구를 위해 다이 및 기계 변수를 체계적으로 변경하는 실험 배열을 설계했습니다.
- 분석 방법:
- ABAQUS 버전 6.3을 사용한 유한 요소 해석(FEA)을 시뮬레이션에 사용했습니다.
- 시뮬레이션 결과를 분석하고 예측 모델을 개발하기 위해 MINITAB [28] 및 SPSS [29]를 사용하여 회귀 분석을 수행했습니다.
- 개별 변수가 다이 변형에 미치는 영향을 평가하기 위해 민감도 분석을 수행했습니다.
- 연구 대상 및 범위:
- 1부: 상업용 다이캐스팅 다이를 채널 플레이트 응력 분석에 사용했습니다.
- 2부: 다음 구조 다이 및 기계 변수를 변경하여 매개변수 연구를 수행했습니다:
- 다이 크기 (A)
- 다이 두께 (B)
- 플래튼 두께 (C)
- 두께 비율 (D), 숄더 두께 대 다이 두께의 비율로 정의
- 다이 위치 (E), 다이 압력 중심과 플래튼 중심선 사이의 거리로 정의
5. 주요 연구 결과:
- 주요 연구 결과:
- "결과는 작은 박형 다이가 큰 후육 다이보다 성능이 더 좋다는 것을 나타냅니다."
- "또한 변수 간에 유의미한 상호 작용이 있으며 시스템 성능을 결정하는 것은 변수 자체가 아니라 이러한 상호 작용이라는 것을 보여줍니다."
- 다양한 다이 크기, 다이 두께 및 플래튼 두께에 대해 파팅면 분리를 최소화하기 위한 최적의 요인 설정이 확인되었습니다.
- 통계적/질적 분석 결과:
- 최대 파팅면 분리(Y) 및 캐비티 주변의 최대 분리(Yc)를 예측하기 위한 회귀 모델을 개발했습니다.
- 최대 파팅면 분리(Y)의 경우, 코딩된 단위의 편집된 예측 모델은 다음과 같습니다:
- Ypred = 10.9608 + 0.8755A + 1.2277B - 1.7718C - 0.7501D + 1.8216A2 - 2.6985AB - 1.9871AC + 0.6837B*C
- 캐비티 주변의 최대 분리(Yc)의 경우, 코딩된 단위의 편집된 예측 모델은 다음과 같습니다:
- Ycpred = -14.0273 + 1.9853A + 3.6203B - 4.0056C + 24.158D + 0.1913C2 - 0.1065AB - 0.0776AC + 0.1536BC - 5.0826B*D
- 민감도 분석은 특정 작동 지점에서 각 변수에 대한 파팅면 분리의 상대적 민감도를 밝혔습니다.
- 파워 법칙 모델도 탐색되었지만 2차 모델만큼 데이터에 잘 맞지 않았습니다.
- 데이터 해석:
- 다이 크기, 다이 두께 및 플래튼 두께 간의 상호 작용은 다이 변형을 결정하는 데 매우 중요합니다.
- 기계 강성은 다이 변형에 영향을 미치는 지배적인 요인입니다.
- "두꺼운 플래튼이 얇은 플래튼보다 항상 더 나은 것으로 밝혀졌습니다."
- "플래튼 면적 적용 범위가 최대 50%인 다이가 더 큰 다이보다 성능이 더 좋았습니다."
- "인서트 뒤의 두꺼운 다이 강철은 파팅면 분리를 감소시켰습니다."
- Figure Name List:
- Figure Name List:
- Figure 1.1: Schematic showing the principal components of a hot chamber die casting machine [6]
- Figure 1.2: Schematic showing the principal components of a cold chamber die casting machine [6]
- Figure 2.1: The loads acting in different stages of a die casting operation [16]
- Figure 2.2: Dimensional changes in the various steps of the die casting process [18]
- Figure 2.3: Die distortion process in a die casting cycle
- Figure 2.4: Schematic of the machine model used by Choudhary, et al [26]
- Figure 3.1: Machine model used for simulation
- Figure 3.2: Cover die with pillars that have been added in the new model
- Figure 3.3: Contour plot for maximum principal stresses in the cover insert for the "cold die" case
- Figure 3.4: Contour plot for maximum principal stresses in the cover insert for the "hot die" case
- Figure 3.5: Contour plot for maximum principal stresses in the ejector insert for the "cold die" case
- Figure 3.6: Contour plot for maximum principal stresses in the ejector insert for the "hot die" case
- Figure 3.7: Contour plot for maximum principal stresses in the cover die for the "cold die" case
- Figure 3.8: Contour plot for maximum principal stresses in the cover die for the "hot die" case
- Figure 3.9: Contour plot for maximum principal stresses in the ejector die for the "cold die" case
- Figure 3.10: Contour plot for maximum principal stresses in the ejector die for the "hot die" case
- Figure 3.11: Contour plot for the displacement pattern in the inserts for the "hot die" case
- Figure 3.12: A schematic showing the location of pillars and cooling lines on (a) cover die and (b) ejector die
- Figure 3.13: Contour plot for the cover die displacement pattern for the "hot die" case
- Figure 3.14: Contour plot for the ejector die displacement pattern for the "hot die" case
- Figure 3.15: Contour plot for parting plane separation for "hot die" case with (a) clamp only and (b) clamp plus intensification
- Figure 3.16: Contour plot for contact pressure for "cold die" case with (a) clamp only and (b) clamp plus intensification
- Figure 3.17: Contour plot for contact pressure for "hot die" case with (a) clamp only and (b) clamp plus intensification
- Figure 4.1: Schematic of die geometry
- Figure 4.2: Layout of machine platen
- Figure 4.3: Casting used for the study
- Figure 4.4: Boundary conditions [10]
- Figure 4.4: Parting plane separation pattern for case 1 (Note: Figure number duplication in source)
- Figure 4.5: Parting plane separation pattern for case 2
- Figure 4.6: Plot of Y and Yc for the design runs
- Figure 4.7: Interaction between die size and die thickness
- Figure 4.8: Interaction between die size and platen thickness
- Figure 4.9: Interaction between die thickness and platen thickness
- Figure 4.10: Interaction between die size and thickness ratio
- Figure 4.11: Interaction between die thickness and thickness ratio
- Figure 4.12: Interaction between platen thickness and thickness ratio
- Figure 4.17: Interaction between die size and die thickness (Ycpred)
- Figure 4.18: Interaction between die size and platen thickness (Ycpred)
- Figure 4.19: Interaction between die size and thickness ratio (Ycpred)
- Figure 4.20: Interaction between die thickness and platen thickness (Ycpred)
- Figure 4.21: Interaction between die thickness and thickness ratio (Ycpred)
- Figure 4.22: Interaction between platen thickness and thickness ratio (Ycpred)
- Figure 4.23: Contour plot of dY/dA at C = -1
- Figure 4.24: Contour plot of dY/dA at C = 0
- Figure 4.25: Contour plot of dY/dA at C = 1
- Figure 4.26: Contour plot of dY/dB
- Figure 4.27: Contour plot of dY/dC
- Figure 4.28: Contour plot of dYc/dA
- Figure 4.29: Contour plot of dYc/dB
- Figure 4.30: Contour plot of dYc/dC
- Figure A.1: Parting plane separation plot for case 1
- Figure A.2: Parting plane separation plot for case 2
- Figure A.3: Parting plane separation plot for case 3
- Figure A.4: Parting plane separation plot for case 4
- Figure A.5: Parting plane separation plot for case 5
- Figure A.6: Parting plane separation plot for case 6
- Figure A.7: Parting plane separation plot for case 7
- Figure A.8: Parting plane separation plot for case 8
- Figure A.9: Parting plane separation plot for case 9
- Figure A.10: Parting plane separation plot for case 10
- Figure A.11: Parting plane separation plot for case 11
- Figure A.12: Parting plane separation plot for case 12
- Figure A.13: Parting plane separation plot for case 13
- Figure A.14: Parting plane separation plot for case 14
- Figure A.15: Parting plane separation plot for case 15
- Figure A.16: Parting plane separation plot for case 16
- Figure A.17: Parting plane separation plot for case 17
- Figure A.18: Parting plane separation plot for case 18
- Figure A.19: Parting plane separation plot for case 19
- Figure A.20: Parting plane separation plot for case 20
- Figure A.21: Parting plane separation plot for case 21
- Figure A.22: Parting plane separation plot for case 22
- Figure A.23: Parting plane separation plot for case 23
- Figure A.24: Parting plane separation plot for case 24
- Figure A.25: Parting plane separation plot for case 25
- Figure A.26: Parting plane separation plot for case 26
- Figure A.27: Parting plane separation plot for case 27
- Figure A.28: Parting plane separation plot for case 28
- Figure A.29: Parting plane separation plot for case 29
- Figure A.30: Parting plane separation plot for case 30
- Figure A.31: Parting plane separation plot for case 31
![Figure 1.1: Schematic showing the principal components of a hot chamber die casting machine [6]](https://castman.co.kr/wp-content/uploads/image-144-png.webp)
![Figure 2.1: The loads acting in different stages of a die casting operation [16]](https://castman.co.kr/wp-content/uploads/Figure-2.1-The-loads-acting-in-different-stages-of-a-die-casting-operation-16-.webp)
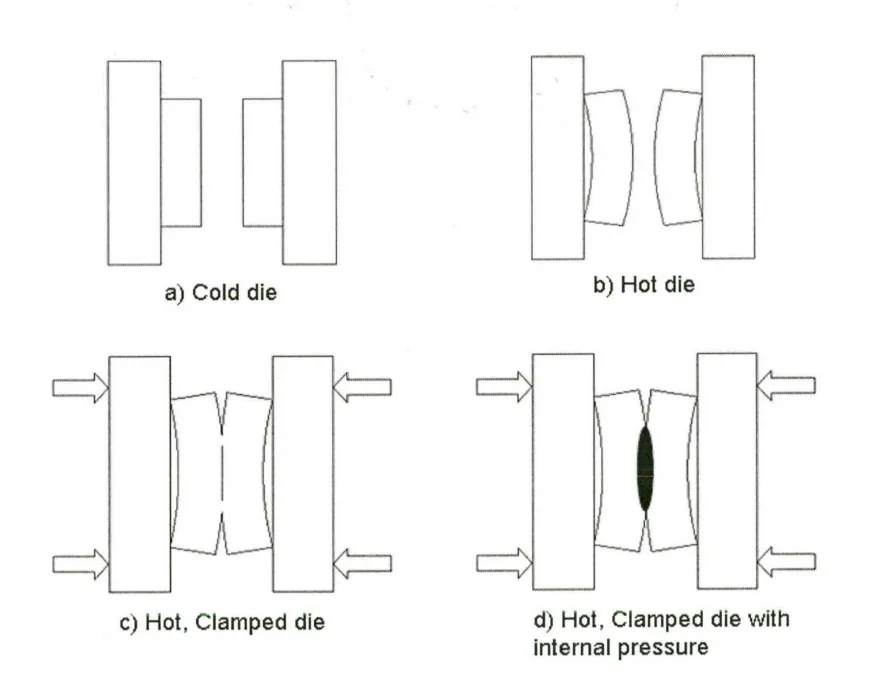
6. 결론 및 논의:
- 주요 결과 요약:
- 채널 플레이트 응력 분석은 이전 시뮬레이션 결과의 불일치를 명확히 하고 높은 응력을 열팽창 및 인서트 크라운에 기인했습니다.
- 구조 다이 및 기계 변수에 대한 매개변수 연구는 "작은 박형 다이가 큰 후육 다이보다" 파팅면 분리를 최소화하는 데 더 나은 성능을 보인다는 것을 나타냅니다.
- 변수, 특히 다이 크기, 다이 두께 및 플래튼 두께 간의 유의미한 상호 작용은 다이 변형의 중요한 결정 요인입니다.
- 파팅면 분리를 최소화하기 위한 최적 설정이 확인되었으며, 일반적으로 두꺼운 플래튼과 높은 두께 비율이 분리를 감소시키는 것으로 나타났습니다.
- 연구의 학문적 의의:
- 본 연구는 다이캐스팅 공정에서 다이 변형의 복잡한 거동에 대한 귀중한 통찰력을 제공합니다.
- FEA 및 회귀 분석과 같은 컴퓨터 지원 분석 도구를 효과적으로 사용하여 다이 거동을 이해하고 예측하는 방법을 보여줍니다.
- 본 연구는 다이캐스팅의 다이 설계 및 최적화에 대한 지식 체계에 기여합니다.
- 연구의 실제적 의미:
- 본 연구 결과는 다이 설계자와 기계 운영자가 다이 변형을 최소화하기 위한 실질적인 지침을 제공합니다.
- 지침에는 최적의 성능을 위해 다이 크기 및 두께를 플래튼 두께 및 두께 비율과 함께 고려하는 것이 포함됩니다.
- 본 연구는 소형에서 중형 다이의 경우 박형 다이가 바람직하고, 대형 다이의 경우 후육 다이가 필요할 수 있음을 시사합니다.
- 일반적으로 두꺼운 플래튼과 높은 두께 비율을 활용하면 (더 강한 기계를 의미) 파팅면 분리가 감소합니다.
- 연구의 한계:
- 이전 분석의 경계 조건의 불일치는 해결되었지만 복잡한 FEA 모델링의 어려움을 강조합니다.
- 파워 법칙 모델은 더 나은 이해를 위해 탐색되었지만 예측에는 2차 모델만큼 정확하지 않았습니다.
- 후면 플래튼이 명시적으로 모델링되지 않아 파팅면 분리에 대한 영향이 간과되었을 수 있습니다.
7. 향후 후속 연구:
- 후속 연구 방향:
- 커버 및 이젝터 다이 두께를 별도의 변수로 변경하는 효과를 조사합니다.
- 다이 변형에 대한 필러 수와 분포의 영향을 연구합니다.
- 파팅면 분리에 대한 후면 플래튼 굽힘의 영향을 포착하기 위해 후면 플래튼을 명시적으로 모델링합니다.
- 실제 시나리오에서 전산 결과를 검증하기 위해 실험 계획법을 사용한 유사한 분석을 수행합니다.
- 추가 탐구가 필요한 영역:
- 다양한 다이 및 기계 변수의 복잡한 상호 작용을 고려하여 다이 설계를 최적화하기 위한 추가 탐구가 필요합니다.
- 다양한 다이 크기 및 주조 매개변수에 대한 다이 컴플라이언스와 강성의 최적 균형을 조사하는 것은 추가 연구가 필요합니다.
8. 참고 문헌:
- [1] Chase, H., "Die Castings", John Wiley & Sons Inc., 1934
- [2] Idra-Prince, Die Casting Process Control course. Course notes, 2002, Idra-Prince, Holland, Michigan
- [3] Ahhuet-Garza, H., Miller, R.A., Mobley, C, "Die Casting", Modeling for casting and solidification processing. Marcel Dekker Inc., 2002
- [4] Doehler,H.H., "Die Casting", First Edition, McGraw-Hill Company Inc., 1951
- [5] Bradley, E.F., "High Performance Castings - A Technical Guide", ASM International, 1989
- [6] Sully, L.J.D., "Die Casting", ASM Metals Handbook, Vol.15, Casting, Ninth Edition, 1988
- [7] NADCA, "NADCA Product Specification Standards for Die Casting", Third Edition, NADCA, 1997
- [8] Ashish Vashist, "A study of industrial die casting die to predict parting plane separation and location of flash with different support setups". The Ohio State University, 2003
- [9] Vashist, A., Kabiri-Bamoradian, K., Miller, R.A., "Die casting die distortion: Case study to predict parting plane separation and flash location", NADCA Transactions of the Congress & Table Exposition, Rosemont, Illinois, 2002
- [10] Abhijith Chayapathi, "Study of the effect of structural die and machine variables on die deflections". The Ohio State University, 2000
- [11] Chayapathi, A., Kesavan, V., Miller, R.A., "The effects of structural die and machine variables on die deflection". Transactions of the 20th NADCA Congress & Exposition, Cleveland, Ohio, 1999
- [12] Abhay Tewari, "Study of the effect of structural variables of die and die casting machine on die deflections". The Ohio State University, 2000
- [13] Miller, R.A., Chakravarthi, V., Kabiri-Bamoradian, K., Kulkami, Y., Tewari, A., "Modeling the Distortion and Mechanical Performances of Dies", NADCA Transactions, 2000
- [14] Yogesh S Kulkami, "Study of the effect of structural variables of die and die casting machine on die deflections", The Ohio State University, 2001
- [15] Miller, R.A., "Die deflection modeling: Empirical validation and tech transfer". Final report. Center for Die Casting, The Ohio State University, 2003
- [16] Ahuett-Garza, H., Miller, R.A., "Die casting die deflections: Computer simulation of causes and effects", NADCA Transactions, 1997
- [17] Kaye, A., Street, A., "Die Casting Metallurgy", Butterworth Scientific, 1982
- [18] Barone, M.R., Caulk, D.A., "Analysis of Thermo-Mechanical Distortion in Die Casting", NADCA Transactions, 1999
- [19] Ahuett-Garza, H., Hedge, K., Padiyar, G., Miller, R.A., "FEM analysis of die casting die deflections: Part I, Modeling and Simulation", NADCA Transactions, 1995
- [20] Ahuett-Garza, H., Hedge, K., Padiyar, G., Miller, R.A, "FEM analysis of die casting die deflections: Part II, Results", NADCA Transactions, 1995
- [21] Papai, J., Mobley, C; "Die thermal fields and heat fluxes during die casting of 380 aluminum alloy in H-13 steel dies"; NADCA Transactions, 1991
- [22] MAGMAsoft, User's manual, 3.2 ed; MAGMA Foundry Technologies, Inc., 1998
- [23] IDEAS Version 10, Online Help Manual, Structural Dynamics Research Corporation
- [24] ABAQUS Version 6.3, Online Documentation, Hibbitt, Karlsson and Sorrensen, Inc.
- [25] Dedhia, S., Ahuett-Garza, H., Choudhury, A.K., and R.A. Miller, "Analysis of proud inserts in Die Deflections and Slide Blowback in Die Casting Dies", Transactions, 19th NADCA Congress & Exposition, Minneapolis, MN, 1997
- [26] Choudhury, A.K., Dedhia, S., Ahuett-Garza, H., and R.A. Miller, "Study of the effects of platen size on die deflections". Transactions, 19th NADCA Congress & Exposition, Minneapolis, MN, 1997
- [27] Venkat, G, R., Shah, V., Ahuett-Garza, H., Miller, R.A., "Parametric design applied to die casting", NADCA Transactions, 1995
- [28] MINITAB version 14, Minitab Inc.
- [29] SPSS version 12, SPSS Inc.
9. 저작권:
- 본 자료는 지스 자비에르 키나팅갈의 논문: 다이 변형에 대한 구조 다이 및 기계 변수 효과 연구 (STUDY OF THE EFFECT OF STRUCTURAL DIE AND MACHINE VARIABLES ON DIE DEFLECTIONS)를 기반으로 합니다.
- 본 자료는 위 논문을 기반으로 요약되었으며, 상업적 목적으로 무단 사용하는 것을 금지합니다.
Copyright © 2025 CASTMAN. All rights reserved.