본 소개 내용은 "[Laserax Inc., Université Laval, Viami International]" 소속 연구진이 발표한 "[Review of technologies for identification of die casting parts]" 논문을 기반으로 작성되었습니다.
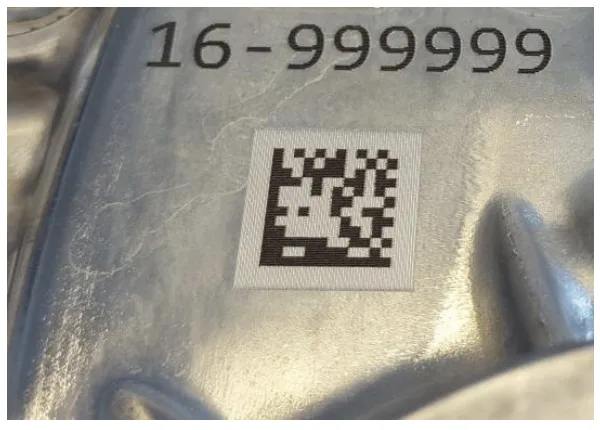
1. 개요:
- 제목: Review of technologies for identification of die casting parts
- 저자: A. Fraser, J. Maltais¹, M. Hartlieb³, C. Frayssinous², R. Vallée² and X. P. Godmaire¹ (소속: ¹Laserax Inc, ²Université Laval, ³Viami International)
- 발행 연도: 제공된 문서에 명시되지 않음.
- 발행 학술지/학회: 명시되지 않음; 소속 기관은 Laserax Inc., Université Laval, Viami International 포함.
- 키워드: 논문에 키워드가 제공되지 않음.
2. 초록 (Abstract):
부품 추적성은 안전 필수 애플리케이션뿐만 아니라 다양한 산업 분야에서 점차 요구되고 있습니다. 다이캐스팅도 예외는 아니며, 구조/고신뢰성 시장이 가장 빠르게 성장하는 분야임을 고려할 때 다이캐스팅의 추적성과 마킹이 뜨거운 주제가 되는 것은 당연합니다. 고신뢰성 부품은 일반적으로 생산된 부품의 100%에 대한 식별 요구사항을 가집니다. 이는 부품 관련 사고 발생 시 합금 및 공정 데이터에 즉시 접근할 수 있게 할 뿐만 아니라, 부품 품질 및 관리 개선에도 도움이 됩니다. 시장에는 다양한 기술이 존재하며 각각 고유한 장단점을 가지고 있습니다. 다이캐스팅 산업은 올바른 마킹 기술을 선택할 때 고려해야 할 매우 중요한 몇 가지 측면을 제시합니다. 불균일한 표면을 가진 복잡한 부품, 마킹 시 종종 높은 온도 상태, 짧은 사이클 타임, 쇼트 블라스트 처리와 같은 마킹 후 공정 등이 가장 중요한 요소들입니다. 부품 마킹은 주조품 생산 공정에서 필수적인 단계이지만, 공정의 병목 현상을 유발하거나 불량률 증가의 원인이 되어서는 안 됩니다. 본 논문은 사용 가능한 다양한 마킹 방법을 분석하고 다이캐스팅 부품의 인라인 마킹에 가장 적합한 방법을 제시하는 것을 목표로 합니다. 온도, 사이클 타임, 쇼트 블라스트 후처리의 영향에 중점을 둔 일부 마킹 결과가 제시됩니다. 결과는 레이저 기반 기술이 다이캐스팅 산업의 모든 요구사항을 해결하는 데 매우 적합함을 보여줍니다.
3. 서론 (Introduction):
추적성 및 개별화된 주조품 마킹은 개발 과정(공정상의 결함을 신속하게 식별하고 수정해야 할 공정 매개변수를 파악하는 데 도움)과 고신뢰성 부품의 양산[1] 모두에서 점차 요구사항이 증가하고 있습니다. 산업 다이캐스팅 환경에서의 명백한 과제는 (a) 빠른 사이클 타임(그리고 부품 마킹은 이 매우 자본 집약적인 공정에서 병목이 되어서는 안 됨), (b) 완벽하게 평평하지 않은 표면에 마킹, (c) 마킹 시 일반적으로 여전히 고온 상태이며, 윤활제나 먼지 잔여물로 덮여 완벽하게 깨끗하지 않은 부품, (d) 열처리, 쇼트 블라스팅, 세척, 에칭, 전환 코팅 등과 같은 추가 공정을 견딜 수 있는 마킹의 능력입니다. 마지막으로, 마킹은 전체 작동 수명 동안 부품에 안전하게 남아 있어야 합니다.
전통적으로 부품 마킹은 완벽하게 반복적인 마킹을 얻기 위해 부품을 정밀한 위치에 클램핑해야 했습니다. 사이클 타임이 중요하고 공정 복잡성과 투자를 최소화해야 할 때, 이상적으로는 거리와 특정 공차 내에서도 완벽하게 작동하는 마킹 시스템을 원합니다(예: 마커에서 1피트 거리에서 양방향으로 1~2인치 공차, 따라서 부품을 특정 지점에 클램핑할 필요 없이 추출 로봇이 마커 앞에 단순히 잡고 있는 상태). 본 논문은 다이캐스팅 부품을 식별하는 데 사용 가능한 기술들을 검토할 것입니다. 다양한 기술의 장단점과 어떤 용도에 적합한지를 제시할 것입니다. 그런 다음 온도, 마킹 속도, 쇼트 블라스트와 같은 후처리의 영향에 대한 결과를 제시할 것입니다.
4. 연구 요약:
연구 주제 배경:
다양한 산업, 특히 안전 필수 및 고신뢰성 다이캐스팅 부품에서 부품 추적성에 대한 요구가 증가함에 따라 신뢰성 있고 효율적인 식별 방법이 필요합니다. 추적성은 품질 관리, 공정 최적화에 기여하며 부품 사고 발생 시 중요한 데이터 접근을 제공합니다.
기존 연구 현황:
부품 식별을 위한 여러 기술이 존재하지만, 다이캐스팅 환경에서는 각각 한계가 있습니다:
- 라벨 및 명판 (Labels and Nameplates): 공정 중 또는 사용 중에 떨어지기 쉽고, 소모품 및 인건비가 발생하며, 고온 및 불균일한 표면에 부적합합니다.
- 핀 스탬핑 / 도트 핀 (Pin Stamping / Dot Peen): 깊고 영구적인 마크를 생성하지만 상대적으로 느리고, 근접 접촉 및 정밀한 위치 지정이 필요하며, 대비(contrast)를 제공하지 못할 수 있고, 표면 변형이 고신뢰성 부품의 품질 사양을 초과할 수 있습니다.
- 잉크젯 프린팅 (Inkjet Printing): 컬러 마크를 제공하지만, 기계 가공, 쇼트 블라스팅, 세척/에칭과 같은 후속 공정에 대한 내구성이 부족합니다.
- 금형 직접 마킹 (Direct Mold Marking): 합금, 생산 시설, 캐비티와 같은 정적 정보에는 적합하지만, 특정 공정 매개변수와 연결된 개별 부품 데이터나 2D 바코드에는 사용되지 않습니다.
연구 목적:
본 연구는 다이캐스팅 부품에 사용 가능한 마킹 기술을 분석하고, 산업별 과제(사이클 타임, 온도, 표면 상태, 후처리)를 고려하여 인라인 마킹에 가장 적합한 방법을 식별하며, 특히 레이저 마킹의 성능, 쇼트 블라스트 후처리에 대한 내성을 중점적으로 조사하는 것을 목표로 합니다.
핵심 연구:
연구의 핵심은 잠재적 이점(속도, 견고성, 비접촉, 고온 처리 능력, 불균일 표면에서의 정밀도) 때문에 레이저 마킹 기술에 초점을 맞춥니다. 확인된 주요 과제는 표준 레이저 블랙 마킹(표면보다 약간 위에 위치)이 쇼트 블라스팅에 의해 제거되기 쉽다는 점입니다. 본 연구는 쇼트 블라스트 저항성을 향상시키기 위해, 이 함몰 부위 내에 블랙 마크를 적용하기 전에 레이저로 크레이터(crater)를 사전 에칭하는 전략(그림 6)을 제안하고 조사합니다. 실험은 알루미늄 다이캐스팅 표면에 100W 파이버 레이저를 사용하여 수행되었으며, 사전 에칭 매개변수(패스 수, 속도, 라인 간격) 및 코드 크기를 변경했습니다. 마킹된 샘플은 두 가지 다른 강철 볼 크기(S170 및 S460)를 사용하여 쇼트 블라스팅 처리되었습니다. 효과는 표면 프로파일로미터(Dektak 150)와 육안 검사를 사용하여 평가되었습니다.
5. 연구 방법론
연구 설계:
본 연구는 두 부분으로 구성된 설계를 사용했습니다:
- 기존 부품 식별 기술(라벨, 핀 스탬핑, 잉크젯 프린팅, 금형 직접 마킹, 레이저 마킹)의 비교 검토를 통해 내구성, 속도, 비용, 공정 조건과의 호환성 등의 기준에 따라 다이캐스팅 산업에 대한 적합성을 평가했습니다.
- 레이저 마킹에 초점을 맞춘 실험적 조사를 통해, 특히 쇼트 블라스트 후처리가 마크 내구성에 미치는 영향을 조사하고 저항성을 개선하기 위한 사전 에칭 전략을 탐색했습니다.
데이터 수집 및 분석 방법:
- 레이저 마킹: 1.06 µm 파이버 레이저(평균 출력 100W, 펄스 지속 시간 100 ns, 주파수 100 kHz)를 사용하여 알루미늄 샘플에 데이터 매트릭스 코드를 마킹했습니다. 변경된 매개변수에는 사전 에칭 패스 수(3~15회), 사전 에칭 속도(3000-7000 mm/s), 라인 간격(0.025-0.125 mm), 코드 크기(4x4 mm, 6x6 mm)가 포함되었습니다. 블랙 마킹 매개변수는 일정하게 유지되었습니다(속도 400 mm/s, 라인 간격 0.125 mm).
- 쇼트 블라스트 처리: 마킹된 샘플은 S170(직경 0.355 mm) 및 S460(직경 1 mm) 강철 볼을 사용하여 쇼트 블라스팅 처리되었습니다. 처리 시간은 다양하게 적용되었습니다.
- 표면 분석: Dektak 150 표면 프로파일로미터를 사용하여 쇼트 블라스트 처리 전후의 표면 프로파일을 측정하여 재료 제거 및 표면 변형을 정량화했습니다. 3D 표면 매핑도 수행되었습니다.
- 육안 검사: 처리 전후의 마킹 외관을 기록하기 위해 사진을 촬영했습니다. 마크 가독성은 육안으로 평가되었습니다.
연구 주제 및 범위:
본 연구는 다음을 포함합니다:
- 다이캐스팅용 다양한 부품 식별 기술 검토 및 비교.
- 다이캐스팅 환경에 적합한 기술로서 레이저 마킹 평가.
- 쇼트 블라스트 후처리가 레이저 마킹에 미치는 영향 조사.
- 레이저 마킹의 쇼트 블라스트 저항성 향상을 위한 사전 에칭 전략 개발 및 테스트.
- 레이저 매개변수(사전 에칭 깊이) 및 쇼트 블라스트 매개변수(볼 크기, 시간)가 마크 생존성 및 가독성에 미치는 영향 분석.
- 알루미늄 다이캐스팅 합금에 대한 마킹 평가.
6. 주요 결과:
주요 결과:
- 레이저 마킹은 속도, 정밀도, 고온 및 불균일 표면 마킹 능력으로 인해 다이캐스팅에 유망해 보이지만, 돌출된 특징을 생성하는 표준 블랙 마킹은 쇼트 블라스팅에 취약합니다.
- 마크를 보호하기 위해 블랙 마킹 전에 함몰 부위를 생성하는 사전 에칭 전략이 조사되었습니다. 표면 프로파일은 여러 번의 레이저 패스가 원래 알루미늄 레벨 아래로 함몰 부위를 생성할 수 있음을 확인했습니다 (Figure 7).
- 쇼트 블라스팅은 표면 프로파일을 크게 변경하여 블랙 마킹과 관련된 피크 및 잠재적으로 주변 에칭된 가장자리를 제거합니다 (Figure 8).
- 더 큰 S460 볼(더 높은 운동 에너지)을 사용한 쇼트 블라스팅은 깊은 표면 충격(약 48 µm 깊이의 구멍)을 초래하고 레이저 마킹을 완전히 파괴했습니다 (Figure 10, Figure 12).
- 더 작은 S170 볼(더 낮은 운동 에너지)을 사용한 쇼트 블라스팅은 더 얕은 충격(약 20 µm 깊이의 구멍)과 더 매끄러운 표면을 초래했습니다. 블랙 대비는 완전히 지워졌지만, 코드 구조의 잔해가 때때로 보였으나 일반적으로 알고리즘으로 읽을 수 없었습니다 (Figure 9).
- 사전 에칭 전략의 효과는 쇼트 블라스트 충격 및 볼 크기에 비해 충분한 깊이를 달성하는 데 결정적으로 의존합니다. 테스트된 매개변수는 여러 번의 사전 에칭 패스에도 불구하고, 특히 S460 볼에 대해 테스트된 쇼트 블라스트 조건에 대해 마킹을 완전히 보호하기에는 불충분했습니다.
- 마크 생존성은 부품이 쇼트 블라스트 스트림에 머무는 시간 및 부품 특징에 대한 마크 위치(예: 돌출부 근처의 마크는 보호될 수 있음)와 같은 무작위 요인에 의해 영향을 받습니다.
- 더 작은 코드 셀 크기(예: 0.25 mm 너비)와 더 깊은 사전 에칭(약 100 µm 깊이)을 결합하여 표준 S170 볼이 에칭된 셀 바닥의 흑색화(blackening)를 파괴하지 않고 통과할 수 있도록 최적화할 가능성이 있습니다.
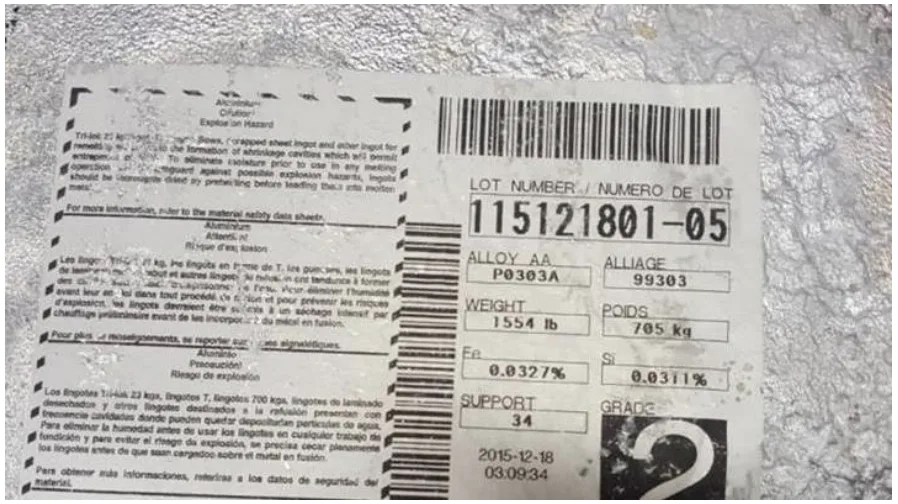
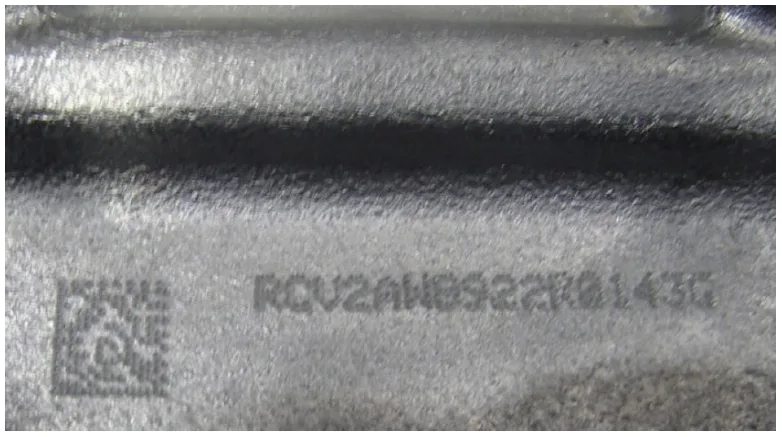
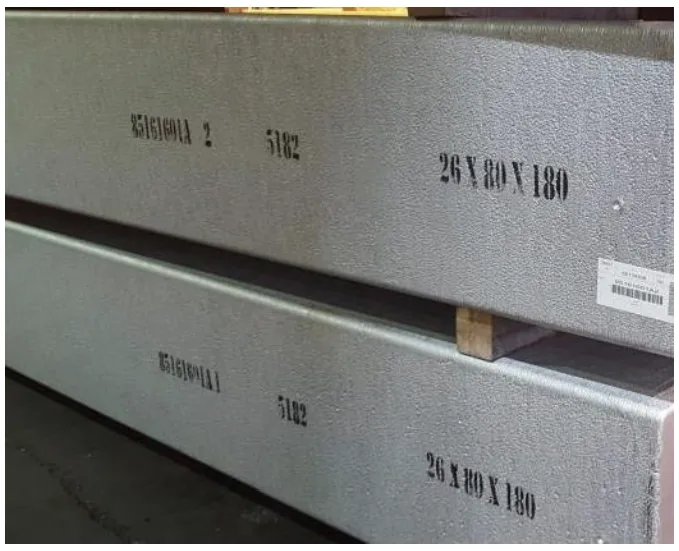
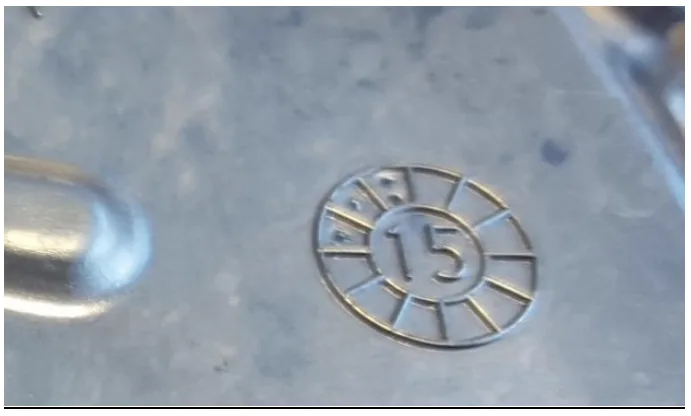
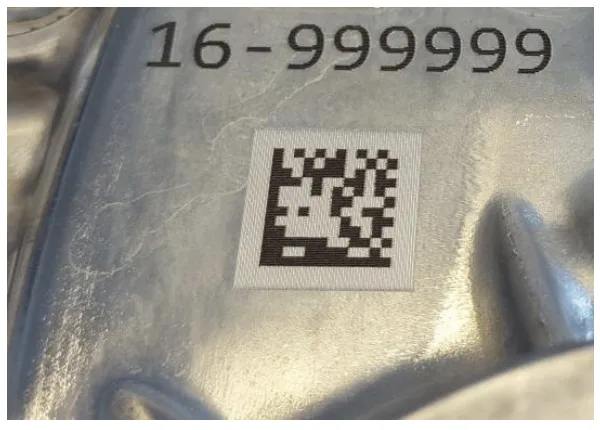
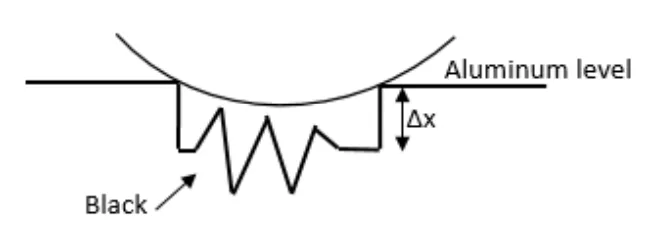
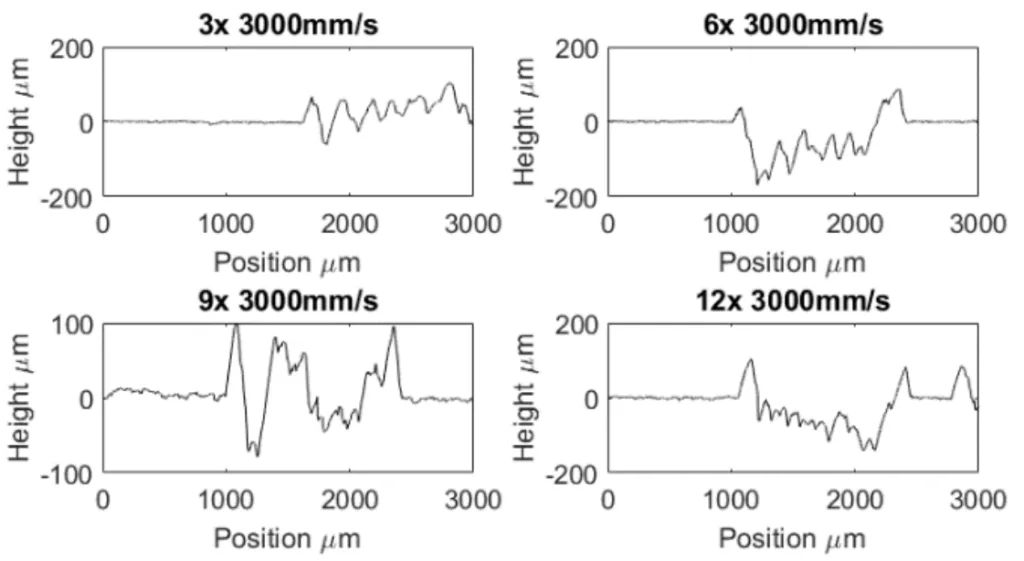
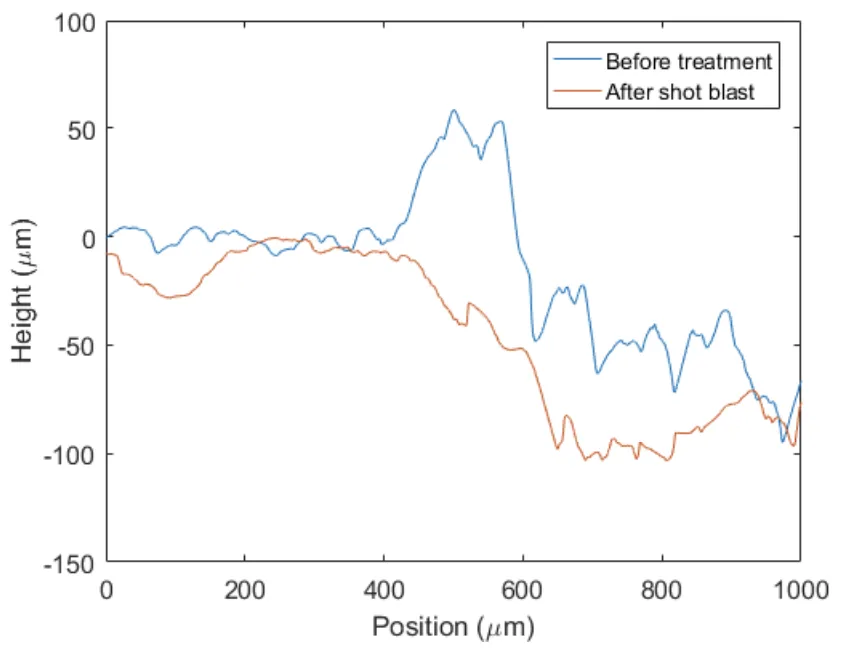
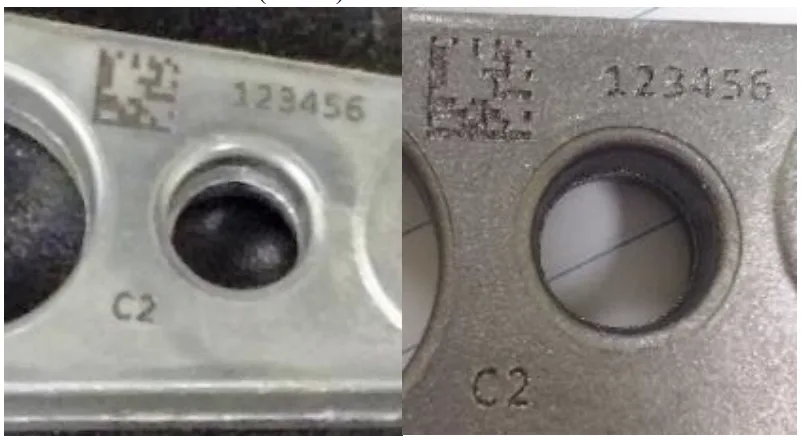
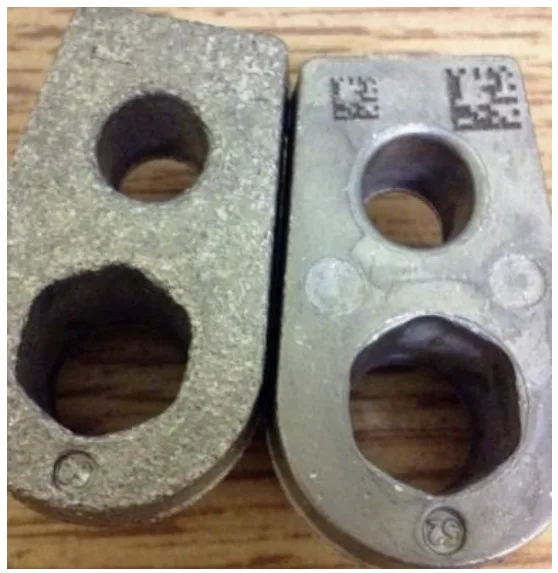
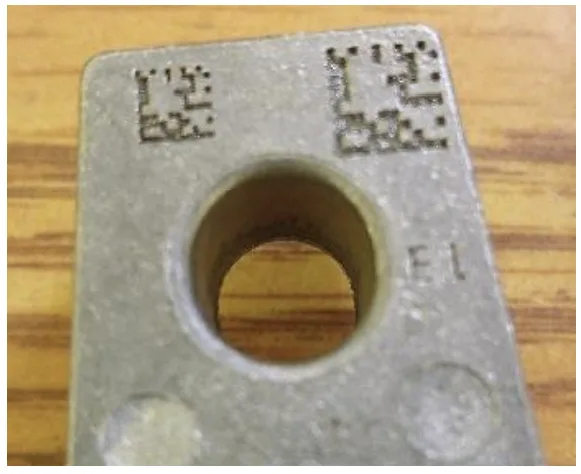
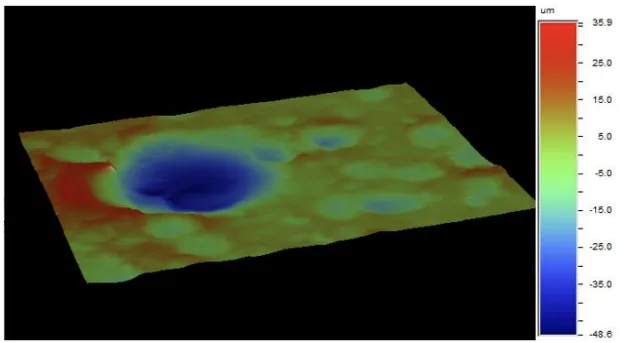
그림 목록 (Figure Name List):
- Figure 1: Printed label (sticker)
- Figure 2: Pinstamp®/Dot peen marked die casting.
- Figure 3: Inkjet printing.
- Figure 4: Direct mold marking and punch
- Figure 5: Laser marked identifier on aluminum die casting alloy.
- Figure 6: Sketch of the idea behind the protected marking.
- Figure 7: Surface profile of samples before treatment where the laser was passed multiple times before marking the black.
- Figure 8: Surface profile measured with Dektak 150 of a marking before and after treatment with S170 balls.
- Figure 9: Photo of a marking before treatment (left) and after shot blast with S170 balls (center).
- Figure 10: Photo of 2 samples after 20 seconds shot blast with S460 balls.
- Figure 11: Photo of sample after a treatment of 20 seconds with S460 balls and another 20 seconds with S170 balls.
- Figure 12: 3D profile of surface after being hit by S470 and S170 balls.
7. 결론 (Conclusion):
레이저 마킹은 다이캐스팅 부품을 영구적으로 마킹하는 데 가장 적합한 공정입니다. 원하는 사이클 타임, 품질 및 반복성을 달성할 수 있습니다. 다이캐스팅에 일반적으로 적용되는 거의 모든 표면 처리를 쉽게 견딜 수 있습니다. 주요 과제는 쇼트 블라스팅이며, 이에 대해 심층적으로 연구되었습니다.
이전에 제시된 모든 쇼트 블라스팅 매개변수는 코드의 저항성에 영향을 미칩니다. 적절한 쇼트 블라스팅 조건 하에서는, 우리의 의견으로는, 다이캐스팅 부품에 쇼트 블라스트 처리 후에도 읽을 수 있는 코드를 보존하는 것이 가능해야 합니다. 여기에는 상대적으로 짧은 공정 시간도 포함됩니다. 알루미늄 표면을 파괴하는 것을 보았기 때문에 너무 크지 않은 볼을 사용하는 것도 중요합니다.
블랙 표면을 그대로 유지하기 위해서는 볼이 케이스(cases) 바닥에 닿지 않을 만큼 충분히 커야 합니다. 코드의 치수 또한 결정적인 매개변수입니다. 더 작은 케이스가 처리 후 읽을 수 있는 코드를 얻을 가능성을 높인다고 생각합니다. 레이저 공정은 약 0.25 mm 너비와 약 100 µm 깊이의 셀 크기를 달성하도록 최적화되어야 합니다. 이는 표준 S170 볼을 사용하고 바닥의 흑색화를 손상시키지 않으면서 유지할 수 있게 할 것이라고 생각합니다. 이를 입증하기 위한 추가 테스트가 수행될 것이며 NADCA 컨퍼런스에서 발표될 것입니다.
다양성 덕분에 레이저 기술은 다이캐스팅 산업에서 매우 흔한 처리에 대한 저항성 강화를 포함하여 여러 요구사항에 적응할 수 있습니다. 레이저 마킹은 견고성, 속도, 불균일한 표면 및 고온에서의 마킹 능력 등 많은 산업적 요구를 충족합니다.
8. 참고 문헌 (References):
- [1] S. Desrosiers et Al., Alloy and heat treatment development for weldable structure parts, 2014 Die Casting ongress conference proceedings
- [2] J. Maltais and al., Surface analysis study of laser marking of aluminum, submitted to ICSOBA 2016 conference proceedings
- [3] Alex Fraser and al., Important considerations for laser marking an identifier on aluminum, Light metals 2016 (Proceedings of TMS 2016), p. 261-264
- [4] J. Benes, The lowdown on laser marking, americanmachinist.com, March 25th 2008
9. 저작권 (Copyright):
- 본 자료는 "A. Fraser, J. Maltais, M. Hartlieb, C. Frayssinous, R. Vallée and X. P. Godmaire"의 논문을 요약한 것입니다. 기반 논문: "Review of technologies for identification of die casting parts".
- 논문 출처: 논문에 DOI가 제공되지 않음.
본 자료는 상기 논문을 기반으로 요약되었으며, 상업적 목적의 무단 사용을 금지합니다.
Copyright © 2025 CASTMAN. All rights reserved.