본 페이지는 "다이캐스팅 부품의 사이드 코어 설계를 위한 복잡한 언더컷 형상의 자동 식별"이라는 제목의 연구 논문을 요약한 내용입니다.
1. 개요:
- 제목: 다이캐스팅 부품의 사이드 코어 설계를 위한 복잡한 언더컷 형상의 자동 식별 (Automated identification of complex undercut features for side-core design for die-casting parts)
- 저자: 란짓 싱 (Ranjit Singh), 자틴더 마단 (Jatinder Madan), 라제쉬 쿠마르 (Rajesh Kumar)
- 발행 연도: 2014년
- 발행 저널/학회: Proc IMechE Part B: Journal of Engineering Manufacture
- 키워드: 다이캐스팅, 복잡한 언더컷 형상, 형상 인식, 사이드 코어 설계, 이형 방향 (Die casting, complex undercut features, feature recognition, side-core design, release direction)
2. 연구 배경:
- 연구 주제의 사회적/학문적 맥락:
- 다이캐스팅은 용융 금속을 코어 및 캐비티 반쪽으로 구성된 다이(금형)에 압력을 가하여 주입하는 중요한 제조 공정입니다.
- 다이 설계는 다이캐스팅 부품의 리드 타임과 제조 비용에 큰 영향을 미치는 복잡하고 시간이 많이 걸리는 프로세스입니다.
- 언더컷 형상 식별은 다이 설계의 중요한 단계이며, 파팅 라인 결정과 코어 및 캐비티 설계에 직접적인 영향을 미칩니다.
- 사이드 코어는 언더컷 형상을 성형하는 데 사용되는 특수 공구 구성 요소이며, 이러한 형상이 식별된 후에 설계됩니다.
- 전통적으로 언더컷 형상 식별은 다이 설계 전문가가 수동으로 수행합니다.
- 기존 연구의 한계:
- 형상 인식 및 언더컷 형상 감지에 대한 이전의 귀중한 연구에도 불구하고, 문헌 검토 결과 복잡한 언더컷 형상 처리에 대한 격차가 드러났습니다.
- 특히, 이전 연구에서는 다음 사항을 완전히 다루지 못했습니다.
- 복잡한 언더컷 형상의 인식.
- 복잡한 언더컷 형상의 분류.
- 복잡한 언더컷 형상을 단순한 형상으로 분할.
- 연구의 필요성:
- 수동적인 언더컷 형상 식별은 다이캐스팅 공정 내 설계-제조 통합의 병목 현상 및 격차를 나타냅니다.
- 본 연구는 복잡한 언더컷 형상을 자동으로 식별하는 시스템을 개발하여 이러한 격차를 해소해야 할 필요성에 의해 동기 부여되었습니다.
- 또한, 후속 사이드 코어 설계를 용이하게 하기 위해 복잡한 언더컷 형상을 더 단순한 구성 요소로 분할하는 방법론이 필요합니다.
3. 연구 목적 및 연구 질문:
- 연구 목적:
- 본 연구의 주요 목적은 다이캐스팅 부품의 복잡한 언더컷 형상의 식별, 분류, 분할 및 이형 방향 결정을 위한 자동화 시스템을 개발하는 것입니다.
- 제안된 시스템은 이러한 목표를 달성하기 위해 가시성 및 접근성 개념을 활용합니다.
- 주요 연구 질문:
- B-rep 모델에서 다이캐스팅 부품의 복잡한 언더컷 형상을 자동으로 식별하는 방법은 무엇입니까?
- 식별된 복잡한 언더컷 형상을 효과적으로 분류하는 방법은 무엇입니까?
- 복잡한 언더컷 형상을 더 단순하고 관리하기 쉬운 언더컷 형상으로 분할하는 방법은 무엇입니까?
- 각 단순 언더컷 형상의 이형 방향을 결정하고 효율적인 사이드 코어 설계를 위해 그룹화하는 방법은 무엇입니까?
- 연구 가설:
- 가시성 및 접근성 개념을 활용하는 시스템을 개발하여 다이캐스팅 부품의 복잡한 언더컷 형상의 식별, 분류, 분할 및 이형 방향 결정을 자동화할 수 있다고 가정합니다.
- 본 연구에서 제안된 규칙 기반 알고리즘은 언더컷 형상을 효과적으로 분류하고 분할하여 자동화된 사이드 코어 설계를 가능하게 할 수 있습니다.
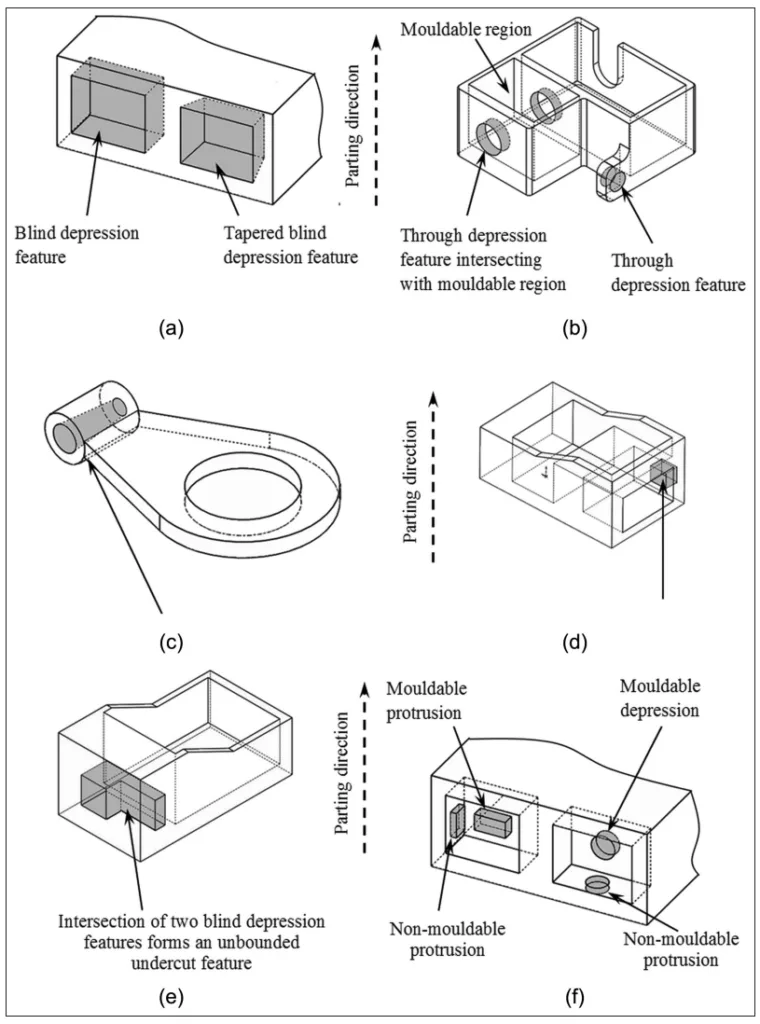
4. 연구 방법론:
- 연구 설계:
- 본 연구는 언더컷 형상 처리를 위한 자동화 시스템을 만드는 데 중점을 둔 시스템 개발 접근 방식을 채택합니다.
- 언더컷 형상을 분류하고 분할하기 위해 규칙 기반 알고리즘이 설계 및 구현되었습니다.
- 제안된 시스템의 효과는 예시 다이캐스팅 부품을 사용한 사례 연구를 통해 평가됩니다.
- 시스템에서 얻은 결과는 정확성과 실제 적용 가능성을 보장하기 위해 검증됩니다.
- 데이터 수집 방법:
- 주요 입력 데이터는 다이캐스팅 부품의 B-rep (Boundary Representation, 경계 표현) 파일로 구성됩니다.
- 이러한 B-rep 모델은 복잡한 언더컷 형상을 포함하여 다이캐스팅 부품의 기하학적 정보를 나타냅니다.
- 예시 다이캐스팅 부품은 제안된 시스템을 테스트하고 검증하기 위한 사례 연구로 사용됩니다.
- 분석 방법:
- 핵심 분석 방법은 가시성 및 접근성 개념을 활용하는 규칙 기반 알고리즘을 기반으로 합니다.
- 가시성: 국부적 가시성이 고려되며, 표면의 한 점에서의 법선은 국부적으로 보이는 방향을 나타냅니다. 가시성 맵(V-map)이 사용되며, 이는 반구입니다.
- 접근성: 비볼록 표면(Non-Convex Surface, NCS)의 접근성은 동일한 비볼록 영역(Non-Convex Region, NCR) 내의 다른 표면과의 장애물을 확인하여 결정됩니다.
- 모서리, 표면 및 이들의 관계를 식별하기 위해 부품의 기하학적 및 위상학적 데이터가 분석됩니다.
- 파팅 방향과 표면 법선의 내적(Dot product, DP)은 표면을 상향, 하향 및 중립 표면으로 분류하는 데 사용됩니다.
- 연구 대상 및 범위:
- 본 연구는 B-rep 모델로 표현할 수 있는 복잡한 언더컷 형상을 가진 다이캐스팅 부품에 중점을 둡니다.
- 범위는 "복잡한 언더컷 형상은 평면 표면만 가집니다."라는 가정에서 명시된 바와 같이 평면 표면을 가진 복잡한 언더컷 형상으로 제한됩니다.
- 시스템은 "다이캐스팅 부품은 성형 가능합니다."라는 가정을 바탕으로 성형 가능한 다이캐스팅 부품을 위해 설계되었습니다.
5. 주요 연구 결과:
- 주요 연구 결과:
- 본 연구는 다음을 수행할 수 있는 자동화 시스템을 성공적으로 개발했습니다.
- 복잡한 언더컷 형상의 자동 식별.
- 이러한 형상을 다양한 유형(예: 블라인드 디프레션, 관통 디프레션, 무한 언더컷 형상 등)으로 분류.
- 복잡한 언더컷 형상을 단순 언더컷 형상으로 분할.
- 각 단순 언더컷 형상의 이형 방향 결정.
- 시스템은 구현되어 예시 다이캐스팅 부품에서 테스트되었으며, 기능과 효율성을 입증했습니다.
- 결과는 검증되었으며, 다이캐스팅 설계 맥락에서 시스템의 정확성과 실제 적용 가능성을 나타냅니다.
- 본 연구는 다음을 수행할 수 있는 자동화 시스템을 성공적으로 개발했습니다.
- 통계적/질적 분석 결과:
- 본 논문은 전통적인 의미의 통계 분석을 제시하지는 않지만, 사례 연구 구현을 기반으로 한 질적 결과를 제공합니다.
- 시스템의 성능은 언더컷 형상 분석에 수동으로 걸리는 시간과 자동화 시스템을 사용하는 시간을 비교하여 평가됩니다.
- "다이캐스팅 다이 설계 전문가는 복잡한 언더컷 형상을 단순한 형상으로 식별, 분류 및 분리하고 이형 방향을 결정하는 데 평균 30-40분이 소요됩니다. 그러나 개발된 시스템의 도움으로 동일한 활동에 1-2분밖에 걸리지 않습니다." 이는 자동화 시스템을 사용하여 시간이 크게 단축되었음을 보여줍니다.
- 데이터 해석:
- 시스템은 다이캐스팅 부품 설계에서 복잡하고 시간이 많이 걸리는 언더컷 형상 분석 작업을 효과적으로 자동화합니다.
- 복잡한 언더컷 형상을 자동으로 식별, 분류 및 분할함으로써 시스템은 후속 사이드 코어 설계에 유용한 정보를 제공합니다.
- 단순 언더컷 형상의 이형 방향 결정은 사이드 코어의 자동화된 설계를 더욱 용이하게 하고 설계-제조 통합 격차를 해소하는 데 기여합니다.
- 그림 목록:
- 그림 1. 다이캐스팅 다이 용어에 대한 그림 표현
- 그림 2. 다이캐스팅 부품 표면의 분류.
- 그림 3. 비볼록 영역의 개략도
- 그림 4. 부분적으로 접근 가능한 표면의 성형성.
- 그림 5. 언더컷 형상 식별을 위한 정보 흐름도.
- 그림 6. 다이캐스팅 언더컷 형상의 분류 트리.
- 그림 7. 언더컷 형상의 예
- 그림 8. 무한 언더컷 형상의 분할
- 그림 9. 복잡한 교차 언더컷 형상의 분할
- 그림 10. 언더컷 형상 및 교차 성형 가능 영역의 분할
- 그림 11. 단순 언더컷 형상의 이형 방향 결정을 위한 정보 흐름도.
- 그림 12. 이형 방향 결정.
- 그림 13. 예시 부품 No. 1에 대한 결과
- 그림 14. 예시 부품 No. 2에 대한 결과
6. 결론 및 논의:
- 주요 결과 요약:
- 본 연구는 특히 사이드 코어 설계를 위해 다이캐스팅 부품의 복잡한 언더컷 형상의 자동 인식 시스템을 성공적으로 개발하고 구현했습니다.
- 시스템은 복잡한 언더컷 형상을 식별, 분류 및 더 단순한 구성 요소로 분할하는 프로세스를 자동화합니다.
- 또한 사이드 코어 설계에 중요한 이러한 단순 형상의 이형 방향을 결정합니다.
- 시스템의 효율성은 예시 다이캐스팅 부품에 대한 사례 연구를 통해 입증되고 검증되었습니다.
- 연구의 학문적 의의:
- 본 연구는 복잡한 언더컷 형상의 인식 및 처리와 관련하여 이전 연구에서 확인된 중요한 격차를 해결합니다.
- 복잡한 언더컷 형상을 식별, 분류 및 분할하는 새로운 방법론을 도입하여 형상 인식 및 다이 설계 자동화 분야의 지식 체계에 기여합니다.
- 제안된 시스템은 자동화된 다이 설계 및 제조 통합에 대한 추가 연구를 위한 귀중한 프레임워크를 제공합니다.
- 실용적 의미:
- 개발된 시스템은 다이캐스팅 산업에 상당한 실용적 의미를 갖습니다.
- 다이 설계 프로세스의 자동화를 촉진하여 리드 타임 및 설계 비용을 절감합니다.
- 시스템은 코어 및 캐비티 설계 및 사이드 코어 설계를 포함한 다운스트림 활동에 필수적인 정보를 생성합니다.
- 언더컷 형상 분석을 자동화함으로써 시스템은 다이캐스팅의 설계-제조 통합 실현에 기여합니다.
- 분석 시간의 상당한 단축 (수동으로 30-40분에서 시스템 사용 시 1-2분으로) 은 실용적인 효율성을 강조합니다.
- 연구의 한계:
- 현재 시스템은 평면 표면을 가진 다이캐스팅 부품 및 복잡한 언더컷 형상으로 제한됩니다. "제안된 시스템은 평면 표면을 가진 다이캐스팅 부품 및 복잡한 언더컷 형상을 식별할 수 있습니다."
- 시스템의 적용 가능성은 특정 기하학적 모양의 언더컷 형상에서 입증되었지만, 알고리즘은 일반적이고 적응 가능한 것으로 언급됩니다.
7. 향후 후속 연구:
- 후속 연구 방향:
- 향후 연구는 시스템의 기능을 비평면 표면을 가진 다이캐스팅 부품을 처리하도록 확장하는 데 초점을 맞춰야 합니다. "향후 연구에서는 비평면 표면을 가진 부품을 포함할 수 있습니다."
- 언더컷 형상 처리 시스템을 자동화된 사이드 코어 설계와 통합하는 것이 가치 있는 다음 단계가 될 것입니다. "복잡한 언더컷 형상의 식별과 단순 언더컷 형상으로의 분할을 통해 본 논문에 제시된 연구는 자동화된 사이드 코어 설계로 확장될 수 있습니다."
- 추가 탐구가 필요한 영역:
- 더 넓은 범위의 기하학적 모양 및 형상 복잡성에 알고리즘을 적용하려면 추가 탐구가 필요하며, 약간의 수정이 필요할 수 있습니다. "다른 형상의 경우 알고리즘의 약간의 수정이 목적에 부합할 것입니다."
- 보다 포괄적인 자동화된 다이캐스팅 설계 워크플로를 달성하기 위해 이 시스템을 다른 다이 설계 및 제조 프로세스와 통합하는 것을 조사합니다.
8. 참고 문헌:
- Kalpakjian S and Schmid SR. Manufacturing engineering and technology. 4th ed. New Delhi: Pearson Education, 2011.
- Singh R and Madan J. Systematic approach for automated determination of parting line for die-cast parts. Robot Cim: Int Manuf 2013; 29: 346-366.
- Kumar V, Madan J and Gupta P. A system for design of multicavity die casting dies from part product model. Int J Adv Manuf Tech 2013; 67: 2083-2107.
- Gan GH, Woo TC and Tang K. Spherical maps: their construction, properties and approximation. J Mech Des: T ASME 1994; 116: 357-363.
- Elber G and Cohen E. Arbitrarily precise computation of Gauss maps and visibility sets for freeform surface. In: Proceedings of the third ACM symposium on solid modeling and applications (SMA ‘95), Salt Lake City, UT, 17–19 May 1995, pp.271–279. New York: ACM.
- Fuh JYH, Wu SH and Lee KS. Development of a semi-automated die casting die design system. Proc IMechE, Part B: J Engineering Manufacture 2002; 216: 1575-1588.
- Dhaliwal S, Gupta SK, Huang J, et al. Algorithms for computing global accessibility cones. J Comput Inf Sci Eng 2003; 3(3): 200-209.
- Surti A and Reddy NV. Non-discretized approach to visibility analysis for automatic mold feature recognition using step part model. J Adv Manuf Syst 2012; 12(1): 1-16.
- Liu M and Ramani K. Computing an exact spherical visibility map for meshed polyhedral. In: Proceedings of the 2007 ACM symposium on solid and physical modelling, Beijing, China, 4–6 June 2007, pp.367–372. New York: ACM.
- Chen YH. Determination of parting direction based on minimum bonding box and fuzzy logic. Int J Mach Tool Manu 1997; 37(9): 1189-1199.
- Hui KC and Tan ST. Mould design with sweep operations a heuristic search approach. Comput Aided Design 1992; 24(2): 81-92.
- Wong T, Tan ST and Sze WS. Parting line formation by slicing a 3D CAD model. Eng Comput 1998; 14: 330-343.
- Fu MW, Fuh JYH and Nee AYC. Generation of optimal parting direction based on undercut features in injection moulded parts. IIE Trans 1999; 31: 947-955.
- Lu HY and Lee WB. Detection of interference elements and release directions in die-cast and injection-moulded components. Proc IMechE, Part B: J Engineering Manufacture 2000; 214(6): 431-441.
- Yin Z, Ding H and Xiong Y. Virtual prototyping of mould design: geometric mouldability analysis for near net shape manufactured parts by feature recognition and geometric reasoning. Comput Aided Design 2001; 33: 137-157.
- Ye XG, Fuh JYH and Lee KS. A hybrid method for recognition of undercut features from moulded parts. Comput Aided Design 2001; 33: 1023-1034.
- Ye XG, Fuh JYH and Lee KS. Automatic undercut feature recognition for side core design of injection molds. J Mech Design 2004; 126(3): 519-526.
- Khardekar R, Burton G and McMains S. Finding feasible mold parting directions using graphics hardware. Comput Aided Design 2006; 38: 327-341.
- Banerjee AG and Gupta SK. Geometrical algorithms for automated design of side actions in injection moulding of complex parts. Comput Aided Design 2007; 39: 882-897.
- Kumar N, Ranjan R and Tiwari MK. Recognition of undercut features and parting surface of moulded parts using polyhedron face adjacency graph. Int J Adv Manuf Tech 2007; 34(1-2): 47-55.
- Madan J, Rao PVM and Kundra TK. Die-casting feature recognition for automated parting direction and parting line determination. J Comput Inf Sci Eng 2007; 7(3): 236-248.
- Fu MW. The application of surface demoldability and moldability to side-core designing die and mold CAD. Comput Aided Design 2008; 40: 567-575.
- Madan J, Singh A and Kumar S. Recognition of intersecting features and identification of separable regions for design-manufacturing integration. In: Proceedings of the international conference on digital factory (ICDF), Trichy, India, 11-13 August 2008, pp.60-67.
- Huang TS. Algorithms for recognizing undercut feature. J Technol 2008; 23(1): 61-69.
- Bidkar RA and McAdams DA. Methods for automated manufacturability analysis of injection-molded and die-cast parts. Res Eng Des 2010; 21: 1-24.
- Bassi R, Reddy NV and Bedi S. Automatic recognition of intersecting features for side-core design in two piece permanent molds. Int J Adv Manuf Tech 2010; 50: 421-439.
- Ran JQ and Fu MW. Design of internal pins in injection mold CAD via the automatic recognition of undercut features. Comput Aided Design 2010; 42(7): 582-597.
- Sunil VB and Pande SS. Automatic recognition of features from freeform surface CAD models. Comput Aided Design 2008; 40: 502-517.
- Tan ST, Yuen MF, Sze WS, et al. Parting lines and parting surfaces of injection moulded parts. Proc IMechE, Part B: J Engineering Manufacture 1990; 204: 211-221.
9. 저작권:
- 본 자료는 란짓 싱, 자틴더 마단, 라제쉬 쿠마르의 논문: "다이캐스팅 부품의 사이드 코어 설계를 위한 복잡한 언더컷 형상의 자동 식별"을 기반으로 합니다.
- 논문 출처: DOI: 10.1177/0954405413514744
본 자료는 상기 논문을 기반으로 요약되었으며, 상업적 목적으로 무단 사용하는 것을 금지합니다.
Copyright © 2025 CASTMAN. All rights reserved.