본 요약은 [Springer]에서 발행한 논문 "[다이캐스팅 다이용 멀티 게이트 게이팅 시스템 설계를 위한 컴퓨터 지원 시스템]"을 기반으로 작성되었습니다.
1. 개요:
- 제목: 다이캐스팅 다이용 멀티 게이트 게이팅 시스템 설계를 위한 컴퓨터 지원 시스템 (A computer-aided system for multi-gate gating-system design for die-casting dies)
- 저자: 란짓 싱 (Ranjit Singh), 자틴더 마단 (Jatinder Madan)
- 발행 연도: 2018년
- 발행 저널/학회: 국제 첨단 제조 기술 저널 (The International Journal of Advanced Manufacturing Technology)
- 키워드: 다이캐스팅, 다이 설계, 공정 변수, 게이팅 시스템 설계, 멀티 게이트 (Die-casting, Die-design, Process parameters, Gating-system design, Multi-gates)
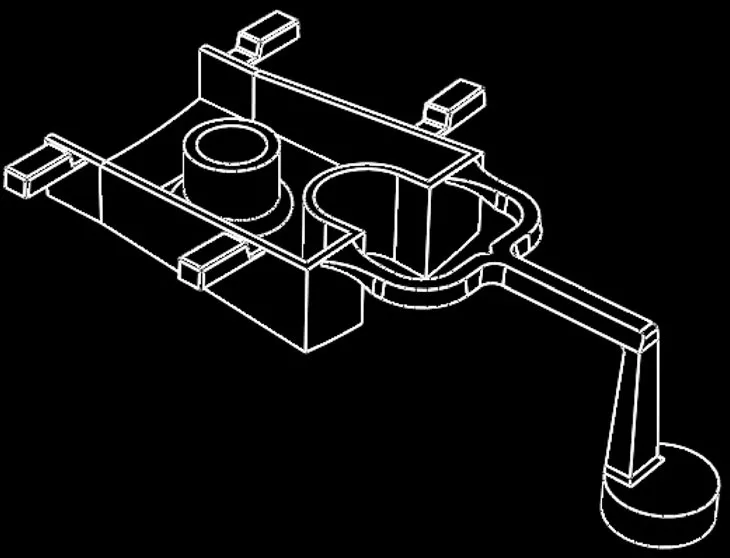
2. 연구 배경:
다이캐스팅 산업의 현재 관행은 게이팅 시스템 설계를 위해 다이캐스팅 전문가의 상당한 개입을 필요로 합니다. 전문가들은 산업 최고 관행과 공정 물리학에 대한 지식뿐만 아니라 수많은 데이터베이스를 참조해야 하므로 매우 시간 소모적이고 번거로운 작업입니다. 따라서 다이캐스팅 산업은 숙련된 다이캐스팅 전문가의 수동적이고 시간 소모적인 작업 부담을 덜어줄 수 있는 시스템을 필요로 합니다.
기존의 다이캐스팅 다이 설계용 컴퓨터 지원 시스템은 종종 전체 게이팅 시스템 설계 프로세스를 자동화하는 데 부족함이 있습니다. 많은 상용 CAD 시스템은 공정 변수 및 게이팅 시스템 사양을 수동으로 상당 부분 입력해야 합니다. 더욱이 이러한 시스템은 복잡한 다이캐스팅 부품에 점점 더 필요해지는 멀티 게이트 게이팅 시스템 설계의 복잡성을 처리하는 데 종종 부족합니다.
따라서 본 연구는 수동적인 전문가 주도 프로세스에 대한 의존도를 줄이고 다이캐스팅 산업의 설계 효율성을 향상시켜 멀티 게이트 게이팅 시스템을 설계할 수 있는 컴퓨터 지원 시스템 개발의 필요성에 의해 동기 부여되었습니다.
3. 연구 목적 및 연구 질문:
주요 연구 목적은 다이캐스팅 다이에서 멀티 게이트 게이팅 시스템 설계를 위한 컴퓨터 지원 시스템을 개발하고 구현하는 것입니다.
본 연구에서 다루는 주요 연구 질문은 다음과 같습니다.
- 컴퓨터 지원 시스템은 중요한 다이캐스팅 공정 변수 결정을 어떻게 자동화할 수 있는가?
- 이러한 시스템은 특히 멀티 게이트 구성에서 게이팅 시스템 변수의 효율적인 설계를 어떻게 촉진할 수 있는가?
- 피처 라이브러리는 시스템에서 결정된 변수를 기반으로 게이팅 시스템의 CAD 모델을 자동으로 생성하는 데 어떻게 활용될 수 있는가?
명시적으로 가설로 진술되지는 않았지만, 본 연구는 다음과 같은 암묵적인 연구 가설 하에 진행됩니다.
- 산업 최고 관행과 피처 라이브러리를 통합한 컴퓨터 지원 시스템은 멀티 게이트 게이팅 시스템 설계 프로세스의 상당 부분을 효과적으로 자동화할 수 있다.
- 이러한 시스템은 다이캐스팅 전문가가 필요로 하는 시간과 노력을 줄이면서 설계 품질과 산업 표준 준수를 유지할 수 있다.
4. 연구 방법론:
본 연구는 컴퓨터 지원 설계 도구의 생성 및 구현에 초점을 맞춘 시스템 개발 접근 방식을 채택합니다. 시스템 설계는 세 가지 주요 모듈을 포함하는 구조화된 방법론을 기반으로 합니다.
- 모듈 1: 다이캐스팅 공정 변수 결정: 이 모듈은 "캐비티 충전 시간, 게이트 속도 및 입력 정보로부터 다이캐스팅 기계 자동 선택"과 같은 변수 결정을 자동화합니다.
- 모듈 2: 컴퓨터 지원 게이팅 시스템 변수 결정: 이 모듈은 "게이트 두께, 게이트 길이, 러너 길이 등과 같은 게이팅 시스템 변수를 입력 정보를 사용하여" 계산합니다.
- 모듈 3: CAD 모델 생성: 이 모듈은 "피처 라이브러리"의 게이팅 시스템 구성 요소를 활용하여 이전 모듈에서 파생된 변수를 기반으로 "피처 라이브러리에서 게이팅 시스템 피처를 업데이트하여 게이팅 시스템의 CAD 모델을 생성"합니다.
데이터 수집 방법: 시스템은 "부품, 공정, 기계 및 재료 정보"를 입력으로 활용합니다. 또한 Ward의 게이팅 시스템 매뉴얼 [24]에 요약된 것과 같은 산업 최고 관행 및 경험적 공식을 변수 결정에 통합합니다. 게이팅 시스템 구성 요소의 피처 라이브러리도 CAD 모델 생성에 활용됩니다.
분석 방법: 시스템은 MATLAB을 사용하여 구현되었습니다. 시스템의 효과에 대한 검증은 "예시 다이캐스팅 부품에 대한 테스트"를 통해 수행되었습니다. 결과는 "산업 관행"과 비교하여 평가되었으며, 이는 시스템 출력에 대한 질적 평가를 나타냅니다.
연구 대상 및 범위: 본 연구는 "다이캐스팅 다이용 멀티 게이트 게이팅 시스템 설계"를 위한 컴퓨터 지원 시스템 개발에 중점을 둡니다. 범위는 게이팅 시스템의 설계 및 CAD 모델 생성으로 제한되며, 변수 결정 자동화 및 피처 라이브러리 활용에 중점을 둡니다. "유동 시뮬레이션 연구는 본 연구의 범위에 포함되지 않습니다."
5. 주요 연구 결과:
본 연구의 주요 결과는 멀티 게이트 게이팅 시스템 설계를 위한 기능적인 컴퓨터 지원 시스템 개발입니다. 시스템은 세 가지 모듈로 작동하며 설계 프로세스의 주요 측면을 성공적으로 자동화합니다.
- 자동화된 공정 변수 결정: 첫 번째 모듈은 다이캐스팅 공정 변수를 효과적으로 결정하여 "캐비티 충전 시간, 게이트 속도 및 입력 정보로부터 다이캐스팅 기계 선택"을 지원합니다.
- 컴퓨터 지원 게이팅 시스템 변수 계산: 두 번째 모듈은 게이팅 시스템 변수를 성공적으로 계산하여 "게이트 두께, 게이트 길이, 러너 길이 등과 같은 게이팅 시스템 변수를 입력 정보를 사용하여 컴퓨터 지원 결정"을 가능하게 합니다.
- 자동화된 CAD 모델 생성: 세 번째 모듈은 이전 모듈에서 파생된 변수를 사용하여 "피처 라이브러리에서 게이팅 시스템 피처를 업데이트하여 게이팅 시스템의 CAD 모델을 생성"하는 기능을 입증합니다.
통계적/질적 분석 결과: 논문에서는 "시스템은 예시 다이캐스팅 부품에 대해 테스트되었으며, 시스템에서 얻은 결과는 산업 관행과 일치합니다."라고 명시합니다. 이는 시스템의 출력이 확립된 산업 표준 및 전문가 기대치와 일치함을 시사하는 질적 검증을 나타냅니다.
데이터 해석: 결과는 멀티 게이트 게이팅 시스템 설계를 위한 제안된 컴퓨터 지원 시스템의 타당성과 효과를 입증합니다. 시스템은 공정 변수 결정, 게이팅 시스템 설계 및 CAD 모델 생성을 성공적으로 통합하여 전통적으로 복잡한 작업에 대한 간소화된 접근 방식을 제공합니다. 산업 관행에 대한 질적 검증은 시스템의 실용적인 적용 가능성과 다이캐스팅 다이 설계의 효율성을 향상시킬 수 있는 잠재력을 시사합니다.
그림 목록:
- 그림 1. 게이팅 시스템에서 사용되는 중요한 용어 설명
- 그림 2. 식별 가능한 세그먼트 및 게이트 위치를 갖는 부품에 대한 멀티 게이트의 예
- 그림 3. 식별 불가능한 세그먼트를 갖는 부품에 대한 멀티 게이트의 예
- 그림 4. 분산 유동 패턴의 개략도
- 그림 5. 유도 유동 패턴의 개략도
- 그림 6. 최단 금속 유동 경로의 개략도
- 그림 7. 끌 게이트의 치수 변수 (Johal et al. [26])
- 그림 8. 게이팅 시스템 피처 라이브러리에서 사용 가능한 피처 설명
- 그림 9. 컴퓨터 지원 게이팅 시스템 설계 시스템 아키텍처
- 그림 10. 컴퓨터 지원 게이팅 시스템 설계 정보 흐름도
- 그림 11. 엔진 커버 케이스 스터디 다이캐스팅 부품 스냅샷
- 그림 12. 엔진 커버 케이스 스터디의 게이팅 시스템 및 캐비티 조립체 스냅샷
- 그림 13. 크랭크 케이스 커버 케이스 스터디 다이캐스팅 부품 스냅샷
- 그림 14. 게이팅 시스템을 갖춘 크랭크 케이스 커버 케이스 스터디 다이캐스팅 부품 스냅샷
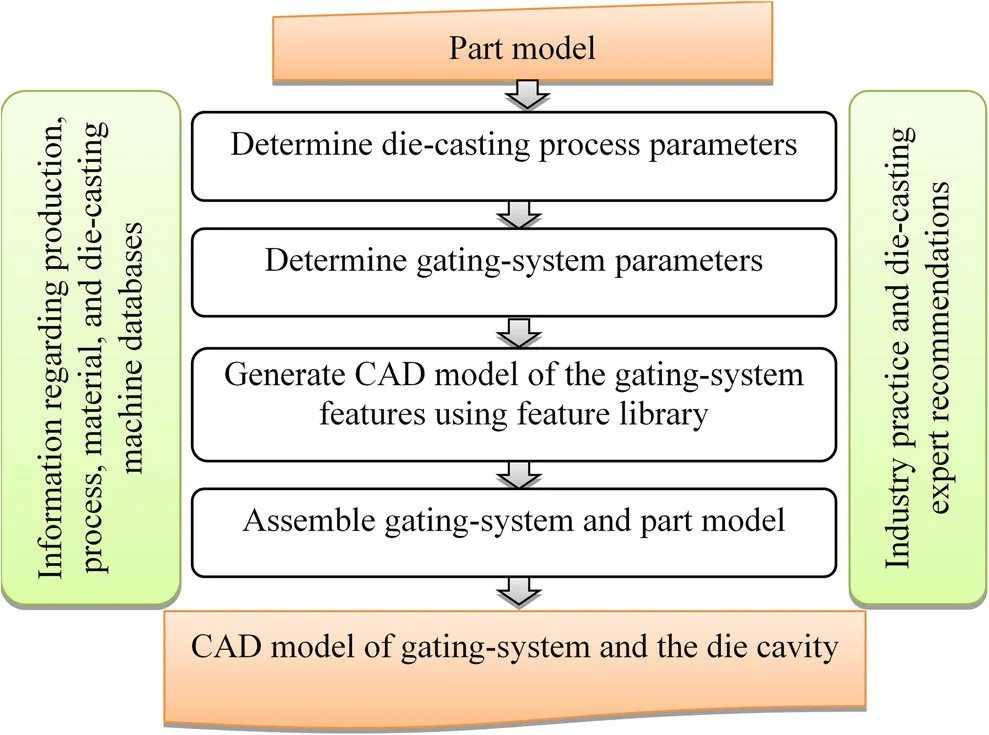
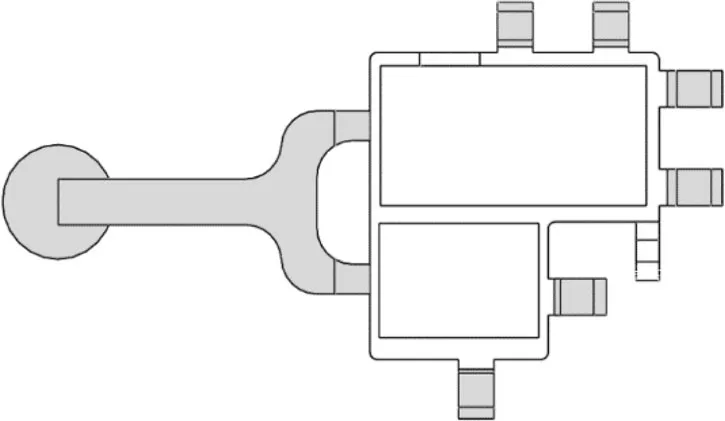
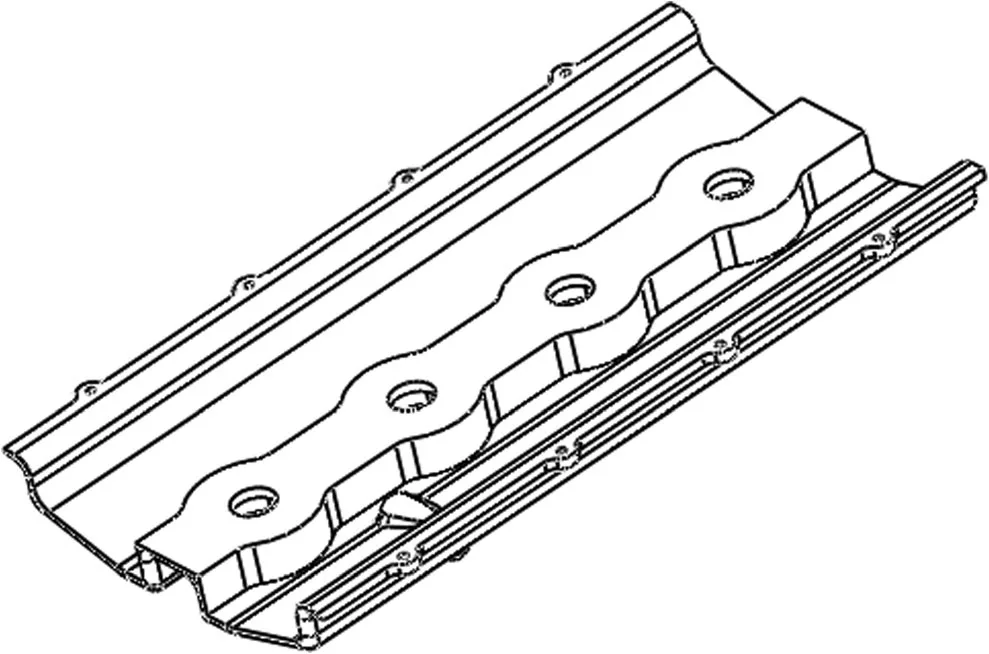
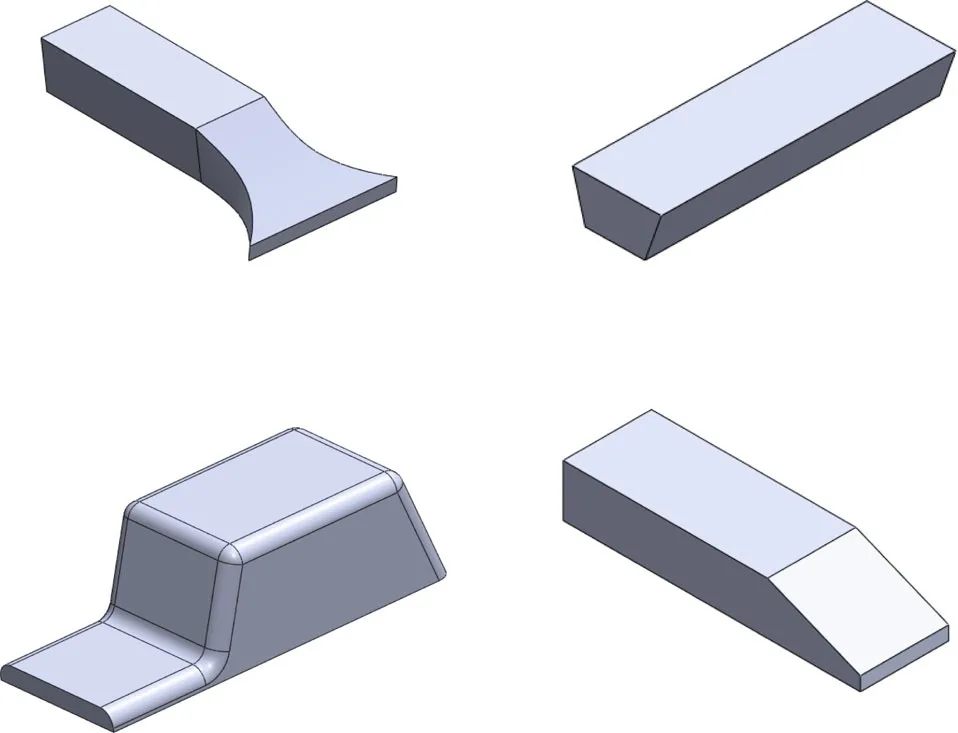
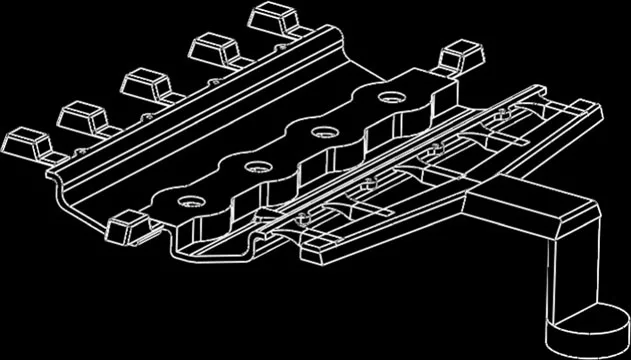
![Fig. 7 Dimensional parameters of a chisel gate (Johal et al. [26])](https://castman.co.kr/wp-content/uploads/image_6-2.webp)
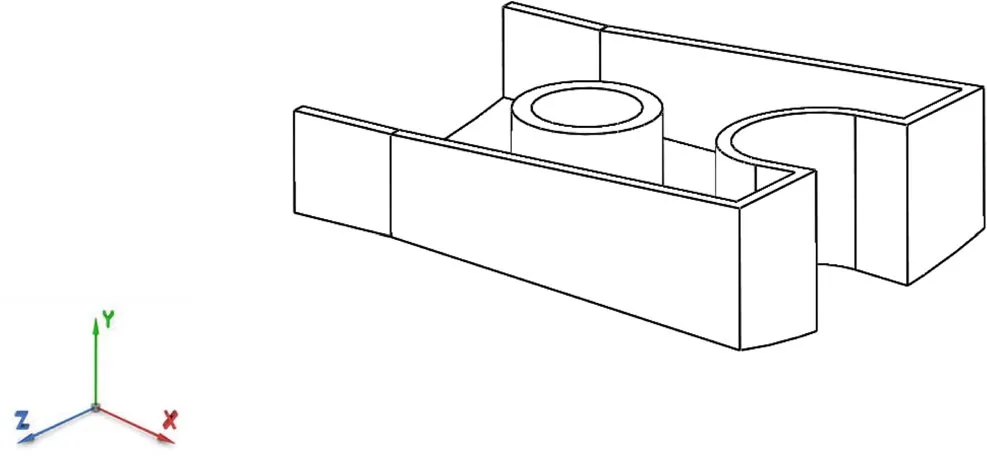
6. 결론 및 논의:
주요 결과 요약: 본 연구는 다이캐스팅의 멀티 게이트 게이팅 시스템 설계를 위한 컴퓨터 지원 시스템을 성공적으로 개발했습니다. 시스템은 공정 변수, 게이팅 시스템 변수 및 피처 라이브러리를 사용하는 CAD 모델 생성을 자동화하는 세 가지 모듈로 구성됩니다. 예시 다이캐스팅 부품에 대한 테스트 결과 시스템 결과가 산업 관행과 일치하는 것으로 나타났습니다.
연구의 학문적 의의: 본 연구는 멀티 게이트 게이팅 시스템을 위한 자동화된 설계 시스템의 격차를 해소함으로써 학문 분야에 기여합니다. 산업 최고 관행을 통합하고 중요한 변수 결정 및 CAD 모델링 단계를 자동화하는 체계적인 접근 방식을 제시합니다.
실용적 의미: 개발된 시스템은 다이캐스팅 산업에 상당한 실용적 이점을 제공합니다. 다이캐스팅 엔지니어의 작업량을 줄이고 설계 리드 타임을 단축하며 특히 멀티 게이트가 필요한 복잡한 부품의 경우 게이팅 시스템 설계의 일관성을 향상시킬 수 있는 잠재력이 있습니다. 멀티 게이트 설계를 처리하는 시스템의 능력은 산업 응용 분야의 핵심 이점으로 강조됩니다.
연구의 한계: 연구 범위는 게이팅 시스템의 설계 및 CAD 모델 생성으로 제한됩니다. "열적 측면 및 공정 물리학은 본 논문에 명시적으로 포함되지 않았지만" 저자는 "본 논문에 사용된 산업 최고 관행이 공정 물리학을 암묵적으로 고려한다"고 제안합니다. 또한 게이트 유형, 게이트 수 및 부품 분할 선택과 같이 여전히 사용자 입력이 필요한 특정 단계가 있습니다. 유동 시뮬레이션 또한 현재 범위 외에 있는 것으로 언급됩니다.
7. 향후 후속 연구:
저자는 시스템 기능을 향상시키고 한계를 해결하기 위해 향후 후속 연구를 위한 여러 방향을 제시합니다.
- CAD/CAM 소프트웨어와의 통합: 설계 워크플로를 간소화하고 리드 타임을 단축하기 위해 기존 CAD/CAM 소프트웨어용 애드온 애플리케이션으로 시스템을 개발합니다.
- 유동 시각화 통합: 게이트 배치 및 설계 최적화를 더욱 지원하기 위해 유동 시각화 기능을 통합하여 유동 패턴 예측에 대한 사용자 경험 의존도를 잠재적으로 줄입니다.
- 열 및 공정 시뮬레이션을 포함하도록 확장: 보다 포괄적인 설계 솔루션을 제공하기 위해 시스템 범위를 확장하여 열적 측면 및 공정 시뮬레이션을 명시적으로 통합합니다.
- 사용자 의존적 단계 자동화: 게이트 유형 및 수 선택, 부품 분할과 같이 현재 사용자 입력이 필요한 단계를 더욱 자동화하여 사용자 개입을 최소화하고 시스템 자율성을 향상시킵니다.
추가 탐구가 필요한 영역: 향후 연구는 공정 물리학의 심층적인 통합, 사용자 의존적인 설계 선택의 추가 자동화, 그리고 더 넓은 범위의 다이캐스팅 부품 및 산업 환경에서 시스템의 광범위한 검증에 초점을 맞춰야 합니다.
8. 참고 문헌:
- Sulaiman S, Keen TC (1997) Flow analysis along the runner and gating-system of a casting process. J Mater Process Technol 63: 690-695
- Hu BH, Tong KK, Niu XP, Pinwill I (2000) Design and optimiza-tion of runner and gating systems for the die-casting of thin-walled magnesium telecommunication parts through numerical simulation.
J Mater Process Technol 105:128-133 - Kim CH, Kwon TH (2001) A runner - gate system for die casting dies. Mater Manuf Process 16:789-801
- Fuh JYH, Wu SH, Lee KS (2002) Development of semi-automated die-casting die design system. Proc Instn Mech Engrs, Part B J Eng Manuf 216:1557-1588
- Wu SH, Fuh JYH, Lee KS (2007) Semi-automated parametric design of gating systems for die-casting die. Comput Ind Eng 53(2):222-232
- Kim YC, Kang CS, Cho JI, Jeong CY, Choi SW, Hong SK (2008) Die-casting Mold Design of the Thin-walled Aluminum Case by computational solidification simulation. J Mater Sci Technol 24(3):
383-388 - NADCA, "Die-casting glossary," NADCA, 2010. [Online]. Available: http://www.diecasting.org/faq/. [Accessed: 19-Jan-2010]
- "SolidWorks." [Online]. Available: http://www.solidworks.in/sw/products/3d-cad/packages.htm. [Accessed: 26-Jun-2013]
- PTC, "No Title," 2018. [Online]. Available: https://www.ptc.com/en/products/cad. [Accessed: 17-Feb-2018]
- "CATIA." [Online]. Available: http://www.3ds.com/products/catia/. [Accessed: 03-Jul-2013]
- c3p, "No Title," 2018. [Online]. Available: ref: http://www.cast-designer.com/casting-solutions/cast-designer-for-die-casting/
gating-system-design-hpdc. [Accessed: 17-Feb-2018] Huang TS (2008) Algorithms for recognizing undercut feature. J Technol 23(1):61-69 - Singh R, Madan J (2013) Systematic approach for automated de-termination of parting line for die-cast parts. Robot Comput Integr Manuf 29:346-366
- Singh R, Madan J, Kumar R (2014) Automated identification of complex undercut features for side-core design for die-casting parts.
Proc IMechE Part B J Eng Manuf 228(9):1138-1152 - Tan ST, Yuen MF, Sze WS, Kwong KW (1990) Parting lines and parting surfaces of injection moulded parts. Proc Inst Mech Eng Part B J Eng Manuf 204(4):211-221
- Wong T, Tan ST, Sze WS (1998) Parting line formation by slicing a 3D CAD model. Eng Comput 14:330-343
- Li W, Martin RR, Langbein FC (2009) Molds for meshes: comput-ing smooth parting lines and undercut removal. IEEE Trans Autom Sci Eng 6(3):423-432
- Khardekar R and McMains S (2009) "Efficient computation of a near-optimal primary parting line," in Joint conference on geomet-ric and physical modeling (SPM '09), pp. 319-324
- Madan J, Rao PVM, Kundra TK (2007) Die-casting feature recog-nition for automated parting direction and parting line determina-tion. J Comput Inf Sci Eng 7(3):236-248
- Sunil VB, Pande SS (2008) Automatic recognition of features from freeform surface CAD models. Comput Des 40(4):502-517
- Madan J, Singh A, and Kumar S (2008) "Recognition of intersecting features and identification of separable regions for
design-manufacturing integration," in Proceedings of the interna-tional conference on digital factory, pp. 60-67 - Kumar N, Ranjan R, Tiwari MK (2007) Recognition of undercut feature and parting surface of moulded parts using polyhedron face adjacency graph. Int J Adv Manuf Technol 34(1-2):47-55
- Lu HY, Lee WB (2000) Detection of interference elements and release direction in die-cast and injection-moulded components. Proc Instn Mech Engrs 214:431-441
- Ward M )2006) Gating manual. Wheeling, Illinois, USA: North American Die-casting Association
- Kumar V and Madan J (2015) "A System for Computer-Aided Gating Design for Multi-Cavity Die-Casting Dies. "Proc Inst Mech Eng Part B J Eng Manuf
- Johal AS, Khanna K, and Singh R (2013) "An automated system to determine gate parameters for die-casting dies," in Proceedings of 3rd International Conference on Production and Industrial
Engineering NIT Jalandhar India, 29th to 31st March. pp 176-183 - Singh CD, Madan J, Singh A (2013) Computer aided design of gating-system for a die-casting die. Int J Comput Appl Technol 46:113-127
- Singh R, Kumar R, and Madan J (2016) “A systematic approach for computer-aided gating-system design for die casting dies," in Proceedings of the ASME International Manufacturing Science
- El-Fotouh MRA, Shash AY, Gadallah MH (2018) Semi-automated gating system design with optimum gate and overflow positions for aluminum HPDC. In: Improved Performance of Materials. springer,
Cham, pp 37-51 - Ferencz P, Lucian G, Ioan S, Cristian C (2010) Studies concerning the design of the runner, gate and venting systems in the case of the high pressure die-casting technology. Ann oradea Univ fascicle
Manag Technol Eng IX(XIX):3-177 - Yen C, Lin JC, Li W, Huang MF (2006) An abductive neural net-work approach to the design of runner dimensions for the minimi-zation of wrappage in injection mouldings. J Mater Process Technol
178(1-3):1-8 - Hahn I, Hartmann G (2008) Automatic computerized optimization in die casting processes. Cast Plant Technol 4:54-61
- Hsu F-Y, Jolly MR, Campbell J (2009) A multiple-gate runner system for gravity casting. J Mater Process Technol 209(17):
5736-5750 - Kim C-H, Kwon TH (2001) A runner-gate design system for die casting. Mater Manuf Process 16(6):789-801
- Lee BD, Baek UH, Han JW (2012) Optimization of gating-system design for die-casting of thin magnesium alloy-based multi-cavity LCD housing. J Mater Eng Perform 21:1893–1903
- Lee KS, Lin JC (2006) Design of the runner and gating system parameters for a multi-cavity injection mould using FEM and neu-ral network. Int J Adv Manuf Technol 27(11-12):1089-1096
- Lin JC (2002) Selection of the optimal gate location for a die-casting die with a freeform surface. Int J Adv Manuf Technol 19(4):278-284
- Tai CC, Lin JC (1999) The optimal position for the injection gate of a die-casting die. J Mater Process Technol 86(1):87-100
- Sun Z, Hu H, Chen X (2008) Numerical optimization of gating system parameters for a magnesium alloy casting with multiple performance characteristics. J Mater Process Technol 199(1-3):
256-264 - Seong I, Jeong CK, Jin HY, Seo JDK, Kang CG (2016) Mold structure design and casting simulation of the high-pressure die casting for aluminum automotive clutch housing manufacturing.
Int J Adv Manuf Technol 84(5-8):1561-1572 - Armillotta A, Fasoli S, Guarinoni A (2016) Cold flow defects in zinc die casting: prevention criteria using simulation and experi-mental investigations. Int J Adv Manuf Technol 85(1-4):605-622
- Woon YK, Lee KS (2004) Development of a die design system for die casting. Adv Manuf Technol 23(5-6):399-411
9. 저작권:
본 자료는 [란짓 싱 및 자틴더 마단]의 논문: [다이캐스팅 다이용 멀티 게이트 게이팅 시스템 설계를 위한 컴퓨터 지원 시스템]을 기반으로 합니다.
논문 출처: [https://doi.org/10.1007/s00170-018-2980-z]
본 자료는 상기 논문을 기반으로 요약되었으며, 상업적 목적으로 무단 사용하는 것을 금지합니다.
Copyright © 2025 CASTMAN. All rights reserved.