본 논문 요약은 [Journal of Materials Processing Technology]에 게재된 [A runner-optimization design study of a die-casting die] 논문을 기반으로 작성되었습니다.
1. 개요:
- 제목: 다이캐스팅 금형의 런너 최적화 설계 연구 (A runner-optimization design study of a die-casting die)
- 저자: C.C Tai, J.C Lin
- 발행 연도: 1998년
- 발행 학술지/학회: Journal of Materials Processing Technology, Elsevier Science S.A.
- 키워드: 런너 최적화 (Runner-optimization); 다이캐스팅 (Die-casting); 귀납적 네트워크 (Abductive network)
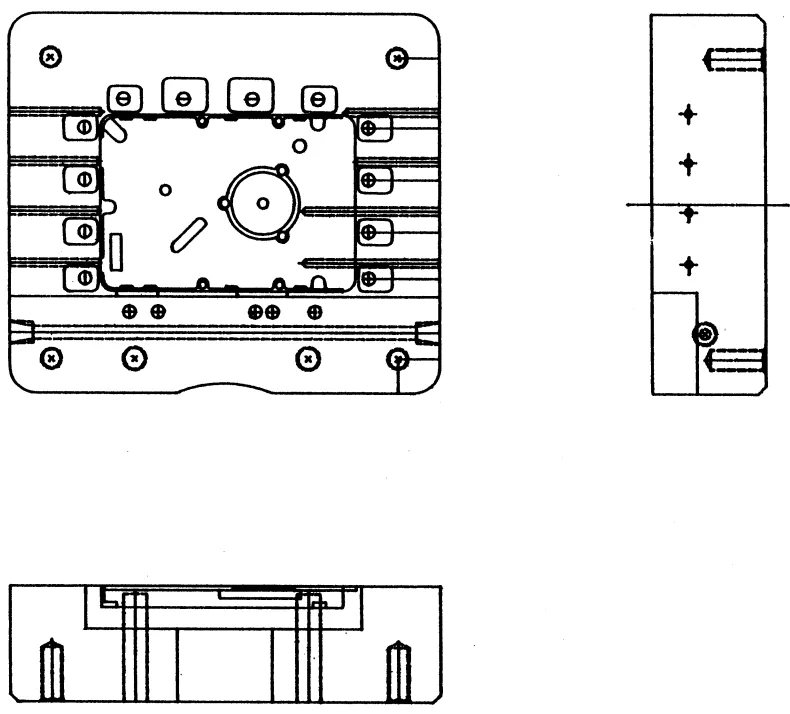
2. 연구 배경:
- 연구 주제의 사회적/학문적 맥락: 다이캐스팅은 자동차, 항공우주, 전자 제품 등 다양한 산업 분야에서 높은 강도와 우수한 외관으로 널리 사용되는 정밀 주조 방식입니다. 다이캐스팅 품질은 게이팅 시스템, 특히 런너 설계에 의해 결정적으로 좌우됩니다. 기존의 다이캐스팅 런너 설계는 다이캐스팅 시험 단계에서 반복적인 수정을 거치게 되어 공정 시간과 비용 증가를 초래합니다.
- 기존 연구의 한계: 기존 연구는 금속 유동, 냉각 시스템, 응고 과정, 금형 수명 등 다이캐스팅의 다양한 측면에 초점을 맞추었습니다. 그러나 금형 수명과 주조 품질에 중요한 영향을 미치는 잔류 응력과 온도를 최소화하기 위한 효과적인 런너 설계 방법이 필요합니다. 최적의 다이캐스팅 매개변수를 얻는 기존 방법들은 종종 상충되어 만족스러운 주조 품질과 금형 수명을 동시에 유지하는 데 어려움이 있습니다.
- 연구의 필요성: 런너 시스템 설계를 최적화하는 것은 다이캐스팅 공정 시간과 비용을 줄이는 데 매우 중요합니다. 설계 단계에서 온도 분포와 잔류 응력을 예측하면 주조 품질과 금형 수명 간의 균형을 맞출 수 있습니다. 효과적인 런너 최적화를 가능하게 하기 위해 다이캐스팅 매개변수와 성능 간의 복잡한 관계를 모델링하는 강력한 방법이 필요합니다.
3. 연구 목적 및 연구 질문:
- 연구 목적: 본 연구의 주요 목적은 잔류 응력을 최소화하고 온도를 제어하여 금형 수명과 주조 품질을 향상시키기 위해 다이캐스팅 금형용 최적화된 런너 시스템을 설계하는 것입니다. 본 연구는 이러한 최적화를 달성하기 위해 귀납적 네트워크와 시뮬레이션 어닐링 알고리즘을 사용하는 모델링 접근 방식을 개발하는 것을 목표로 합니다.
- 주요 연구 질문:
- 귀납적 네트워크는 다이캐스팅 매개변수 (고속 인젝터 위치, 런너 주입 각도, 런너 단면 비율)와 다이캐스팅 성능 (런너 잔류 응력 및 온도) 간의 복잡한 관계를 모델링하는 데 어떻게 사용될 수 있는가?
- 시뮬레이션 어닐링 알고리즘은 귀납적 네트워크 모델과 정의된 성능 지수를 기반으로 최적의 다이캐스팅 매개변수를 검색하는 데 어떻게 활용될 수 있는가?
- 제안된 런너 최적화 설계 방법은 다이캐스팅 금형에서 잔류 응력을 줄이고 온도를 제어하는 데 얼마나 효과적인가?
- 연구 가설:
- 귀납적 네트워크는 입력 매개변수를 기반으로 다이캐스팅 성능을 정확하게 예측할 수 있다.
- 시뮬레이션 어닐링 알고리즘은 잔류 응력을 최소화하고 온도를 제어하는 최적의 다이캐스팅 매개변수를 효과적으로 식별할 수 있다.
- 제안된 방법을 사용하여 도출된 최적화된 런너 설계는 기존 설계에 비해 잔류 응력 감소 및 금형 수명 향상을 가져올 것이다.
4. 연구 방법론
- 연구 설계: 본 연구는 전산 모델링과 결합된 실험 설계 접근 방식을 채택합니다. 런너 블록과 캐비티 블록을 별도로 설계 및 제작하여 다양한 다이캐스팅 조건에서 테스트할 수 있도록 했습니다. 23개의 서로 다른 런너 인서트 블록을 테스트했습니다.
- 자료 수집 방법: 알루미늄 합금을 사용하여 다이캐스팅 실험을 수행했습니다. 주조 압력 (117.6 MPa), 주입 속도 (0.2 m/s 및 2.8 m/s), 사이클 시간 (3 shots/min)과 같은 다이캐스팅 매개변수를 제어했습니다. 온도는 다이 캐비티 표면 아래 지점 (A-H 지점)에서 열전대를 사용하여 측정했습니다. 잔류 응력은 ASTM 표준에 따라 블라인드 홀 드릴링 방법을 사용하여 RS-200 드릴링 장비와 SYSTEM-4000 측정 시스템을 사용하여 런너 입구 및 게이트 근처 위치 (그림 2의 RS)에서 측정했습니다.
- 분석 방법: 귀납적 네트워크를 구성하여 다이캐스팅 공정을 모델링했습니다. 네트워크는 다이캐스팅 매개변수 (고속 인젝터 위치, 런너 주입 각도, 런너 단면 비율)를 입력으로 사용하고 다이캐스팅 성능 (런너 잔류 응력 및 온도)을 예측합니다. 시뮬레이션 어닐링 알고리즘을 사용하여 정규화된 온도와 잔류 응력을 결합한 성능 지수를 기반으로 다이캐스팅 매개변수를 최적화했습니다. 예측 제곱 오차 (PSE) 기준을 사용하여 최적의 네트워크 구조를 결정했습니다.
- 연구 대상 및 범위: 본 연구는 다이캐스팅 금형의 런너 시스템 설계에 초점을 맞춥니다. 실험 작업은 특별히 설계된 금형 및 런너 블록을 사용하여 알루미늄 합금의 다이캐스팅을 포함했습니다. 범위는 잔류 응력을 최소화하고 다이 캐비티 표면 근처의 온도를 제어하기 위해 런너 설계 매개변수 (런너 주입 각도 및 런너 단면 비율) 및 고속 인젝터 위치의 최적화로 제한됩니다.
5. 주요 연구 결과:
- 주요 연구 결과:
- 귀납적 네트워크는 다이캐스팅 공정을 모델링하고 온도와 잔류 응력을 정확하게 예측하기 위해 성공적으로 개발되었습니다. 예측 오차는 실험 측정값과 비교했을 때 5% 이내였습니다 (표 5).
- 시뮬레이션 어닐링 알고리즘은 최적의 다이캐스팅 매개변수를 효과적으로 검색했습니다.
- 게이트 근처 위치의 잔류 응력은 런너 입구보다 약 100 MPa 더 커서 게이트 영역이 손상되기 쉽다는 것을 나타냅니다.
- 최대 잔류 응력 값은 항상 표면층 아래 0.1 mm 이내의 위치에서 발견되었습니다.
- 주조 결함, 주로 수축 기공 및 냉간 접합이 다양한 실험 매개변수에서 관찰되었습니다 (표 2).
- 최적화 결과, 런너 단면 비율 2.3 및 가중 함수 w₁=0, w₂=1의 경우 최적의 고속 주입 위치는 95.51 mm이고 런너 주입 각도는 69.1°이며, 이는 최저 잔류 응력 403.1 MPa을 가져왔습니다 (표 6).
- 속도 주입 위치 105 mm 및 w₁=0, w₂=1의 경우 최적의 주입 각도는 72.16°이고 런너 단면 비율은 2.85이며, 최소 잔류 응력 409 MPa을 나타냈습니다.
- 통계적/정성적 분석 결과:
- 귀납적 네트워크는 온도에 대해 4.2%, 잔류 응력에 대해 3.8% 이내의 오차로 높은 예측 정확도를 입증했습니다.
- 시뮬레이션 어닐링 알고리즘은 최적의 매개변수로 수렴하여 최적화 효과를 입증했습니다.
- 실험 결과 (표 3 및 4)는 온도 및 잔류 응력에 대한 측정값과 예측값 간의 양호한 일치를 보여줍니다.
- 데이터 해석: 결과는 귀납적 네트워크 및 시뮬레이션 어닐링 접근 방식이 다이캐스팅의 런너 설계 최적화를 위한 실행 가능한 방법임을 나타냅니다. 최적화 결과를 기반으로 다이캐스팅 매개변수를 조정함으로써 금형 수명과 주조 품질 향상에 중요한 잔류 응력을 줄이고 온도를 제어할 수 있습니다. 가중 함수 (w₁, w₂)를 통해 온도와 잔류 응력 최소화 간의 균형을 조정할 수 있습니다.
- 그림 목록:
- Fig. 1. 이동 캐비티 블록 (Moving cavity block).
- Fig. 2. 인서트 런너 블록 (Insert runner block).
- Fig. 3. 시뮬레이션 어닐링 검색의 흐름도 (Flow chart for the simulated annealing searching).
- Fig. 4. 주입 위치 조정 시 일반 조건에서 최적화된 다이캐스팅 매개변수의 효과 (Effect of die-casting parameters in optimization under general conditions, when adjusting the injected position).
- Fig. 5. 주입 각도 조정 시 일반 조건에서 최적화된 다이캐스팅 매개변수의 효과 (Effect of die-casting parameters in optimization under general conditions, when adjusting the injected angle).
- Fig. 6. 런너 단면 비율 조정 시 일반 조건에서 최적화된 다이캐스팅 매개변수의 효과 (Effect of die casting parameters in optimization under general condition, when adjusting the runner section ratio).
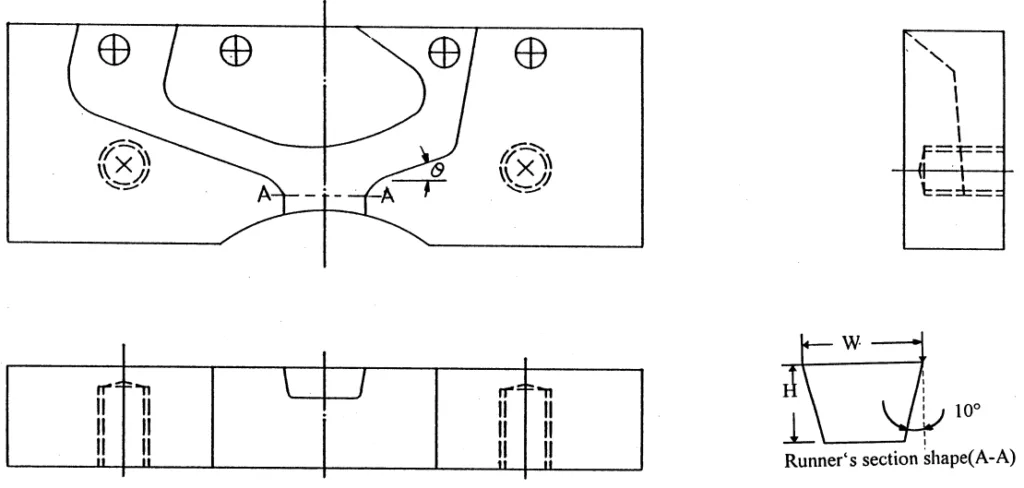

6. 결론 및 논의:
- 주요 결과 요약: 본 연구는 귀납적 네트워크와 시뮬레이션 어닐링 알고리즘을 사용하여 다이캐스팅 금형용 런너 최적화 설계 방법을 성공적으로 개발하고 검증했습니다. 이 방법은 다이캐스팅 공정을 효과적으로 모델링하고 온도와 잔류 응력을 예측하며 잔류 응력을 최소화하고 온도를 제어하기 위한 최적의 다이캐스팅 매개변수를 식별합니다. 실험적 검증은 모델의 정확성과 최적화 접근 방식의 효과를 확인했습니다.
- 연구의 학문적 의의: 본 연구는 런너 시스템 설계 최적화를 위한 새로운 접근 방식을 제공함으로써 다이캐스팅 분야에 기여합니다. 이러한 맥락에서 귀납적 네트워크와 시뮬레이션 어닐링의 적용은 복잡한 제조 공정을 모델링하고 최적화하는 강력한 방법론을 입증합니다. 또한 본 연구는 금형 수명과 주조 품질 향상을 위해 금형 설계 시 온도와 잔류 응력을 모두 고려하는 것의 중요성을 강조합니다.
- 연구의 실제적 의미: 제안된 방법은 다이캐스터에게 런너 설계를 최적화하는 실용적인 도구를 제공하여 비용이 많이 들고 시간이 많이 소요되는 시행착오식 다이캐스팅 테스트의 필요성을 줄입니다. 이 방법을 사용하면 제조업체는 수명이 길고 주조 품질이 향상되며 생산 비용이 절감되는 금형을 설계할 수 있습니다. 입서트 스타일 런너 블록의 사용은 입증된 바와 같이 런너 시스템의 쉽고 비용 효율적인 수정 및 최적화를 가능하게 합니다.
- 연구의 한계: 본 연구는 특정 다이캐스팅 매개변수 및 재료로 제한됩니다. 더 넓은 범위의 다이캐스팅 조건, 재료 및 금형 형상에 걸쳐 방법을 검증하기 위한 추가 연구가 필요합니다. 귀납적 네트워크 모델의 복잡성과 시뮬레이션 어닐링 알고리즘의 계산 비용은 실시간 응용 프로그램 또는 매우 복잡한 금형 설계에 대한 제한 사항으로 간주될 수 있습니다.
7. 향후 후속 연구:
- 후속 연구 방향:
- 제안된 방법의 적용을 다양한 다이캐스팅 합금 및 금형 형상으로 확장합니다.
- 게이트 설계 및 냉각 시스템 매개변수와 같은 다른 다이캐스팅 매개변수가 최적화 프로세스에 미치는 영향을 조사합니다.
- 계산 효율성을 개선하고 잠재적으로 더 나은 최적화 결과를 얻기 위해 보다 진보된 최적화 알고리즘의 사용을 모색합니다.
- 산업 환경에서의 채택을 용이하게 하기 위해 제안된 방법을 기반으로 사용자 친화적인 소프트웨어 도구를 개발합니다.
- 추가 탐구가 필요한 영역:
- 최적화된 런너 설계를 사용하여 달성한 장기적인 금형 수명 개선은 장기간의 다이캐스팅 실험을 통해 추가로 조사해야 합니다.
- 예측된 잔류 응력과 실제 금형 파손 메커니즘 (예: 열간 균열, 균열) 간의 관계를 보다 자세히 탐구해야 합니다.
- 목적 함수의 가중 인자 (w₁, w₂)에 대한 최적화 결과의 민감도는 다양한 응용 시나리오에서 선택 지침을 제공하기 위해 추가 조사가 필요합니다.
8. 참고 문헌:
- [1] T.P. Groeneveld, W.D. Kaiser, Effects of metal velocity and die temperature on metal-flow distance and casting quality, Die Casting Eng. 23 (5) (1979) 44-49.
- [2] R.L. Trueloved, Die casting temperature control: a new locating waterlines, Die Casting Eng. 26 (1) (1979) 28-31.
- [3] S.H. Jong, H.Y. Chou, C.R.Li and W.S. Hwang,@ Application of mold filling analysis in the design of die casting die, Chukung Q. 73 (1992) 1-9.
- [4] S.H. Jong, M.S. Poon, H.Y. Chouand and W.S.Hwang,@ The application of solidification analysis in die casting, Chukung Q. 74 (1992) 1-11.
- [5] M. Hihara (1992) paper in Japanese. (일본어 논문)
- [6] G.J. Montgomery, K.C. Drake, Abductive reasoning network, Neurocomputing 2 (1991) 97-104.
- [7] S. Kirkpartick, C.D. Gelatt, M.P. Vecchi, Optimization by simulated annealing, Science 220 (4958) (1983) 671-680.
- [8] S. Geman, D. Geman, Stochastic relaxation, Gibbs distributions and the Bayesian restoration of images, IEEE Trans. Pattern Anal. Mach. Intell. 6 (6) (1984) 721-741.
- [9] B.W. Lee, B.J. Sheu, Hardware Annealing in Analog VLSI Neurocomputing, Kluwer, Dordrecht, 1991.
- [10] C. Zhang, H.P. Wang, The discrete tolerance optimal problem, ASME Manuf. Rev. 6 (1) (1991) 60–71.
- [11] Y.S. Trang, S.C. Ma, L.K. Chung, Determination of optimal cutting parameters in wire electrical discharge machining, Int. J. Mach. Tools Manuf. 35 (12) (1995) 1693-1701.
- [12] G.A. Miller, The magic number seven, plus or minus two: some limits on our capacity for processing information, Philos. Rev. 63 (8) (1956) 81-87.
- [13] A.R. Barron, in: S.J. Farlow (Ed.), Predicted Square Error: A Criterion for Automatic Model Selection, Self-Organizing Methods in Modeling: GMDH Type Algorithms, Marcel-Dekker, New York, 1984.
- [14] N. Metropolis, A. Rosenbluth, M. Rosenbluth, A. Teller, E. Teller, Equation of state calculation by fast computing machines, J. Chem. Phys. 21 (1953) 187-1092.
9. 저작권:
- 본 자료는 "C.C Tai, J.C Lin"의 논문 "A runner-optimization design study of a die-casting die"를 기반으로 작성되었습니다.
- 논문 출처: https://doi.org/10.1016/S0924-0136(98)00031-4
본 자료는 상기 논문을 기반으로 요약되었으며, 상업적 목적으로 무단 사용하는 것을 금지합니다.
Copyright © 2025 CASTMAN. All rights reserved.