이 소개 자료는 "[Proceedings of NAMRI/SME]"에 게재된 "[System for Computer Aided Cavity Layout Design for Diecasting Dies]" 논문을 기반으로 작성되었습니다.
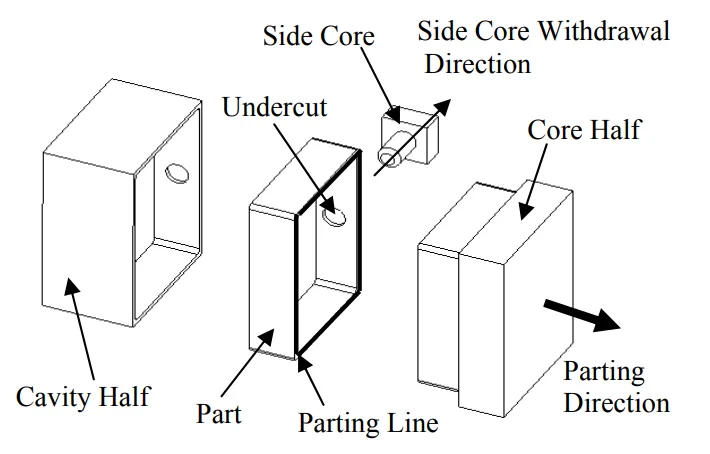
1. 개요:
- 논문 제목: System for Computer Aided Cavity Layout Design for Diecasting Dies (다이캐스팅 금형용 컴퓨터 지원 캐비티 레이아웃 설계 시스템)
- 저자: V. Kumar, J. Madan
- 발행 연도: 2011
- 게재 학술지/학회: Proceedings of NAMRI/SME, Vol. 39
- 키워드: Diecasting, Die Design, Multi Cavity Dies, Layout Patterns, Layout Design (다이캐스팅, 금형 설계, 다중 캐비티 금형, 레이아웃 패턴, 레이아웃 설계)
2. 초록:
다이캐스팅은 고압으로 금속 용탕을 금속 주형에 주입하여 표면 조도가 우수한 부품을 대량 생산하는 성형 방법 중 하나입니다. 다이캐스팅 금형 설계는 인간의 전문 지식을 필요로 하며 일반적으로 시행착오를 통해 수행되어 금전적 및 시간적 손실을 초래합니다. 초기 금형 설계 단계에서의 자동화는 생산 리드 타임을 줄이는 것 외에도 생산성을 높일 것입니다. 다이캐스팅에서 캐비티 수, 레이아웃 패턴 및 캐비티 배치에 대한 결정은 금형 설계 및 제조에 매우 중요합니다. 본 논문은 다이캐스팅 금형용 컴퓨터 지원 캐비티 레이아웃 설계 시스템과 관련된 연구 작업을 제시합니다. 제안된 시스템은 캐비티 수 결정, 레이아웃 패턴 선택 및 다이베이스 내 캐비티 배치라는 세 가지 모듈로 구성됩니다. 이를 통해 금형 설계자는 수동으로 제공되는 약간의 정보만으로 부품의 CAD(Computer Aided Design) 파일에서 자동으로 캐비티 레이아웃 설계를 생성할 수 있습니다. 최적의 캐비티 수는 경제적, 기술적, 기하학적 및 시간적 제한을 고려하여 결정된 후 레이아웃 패턴이 선택됩니다. 그 후 캐비티가 다이베이스에 배치됩니다. 개발된 시스템은 다이캐스팅 기계 및 재료 데이터베이스와 금형 설계 지식베이스에 의존합니다. 이 시스템은 여러 다이캐스팅 부품에 대해 시도되었으며 결과는 업계에서 얻은 결과와 유사한 것으로 나타났습니다. 제안된 시스템은 현재 사용 가능한 시스템보다 더 포괄적이며 다이캐스팅을 위한 설계-제조 통합 방향으로 한 걸음 더 나아간 것입니다.
3. 서론:
다이캐스팅은 용융된 금속을 고압으로 재사용 가능한 강철 주형(금형)에 주입하여 금속 부품을 생산하는 다목적 공정입니다. 이 금형은 높은 정확도와 반복성으로 복잡한 형상을 생산하도록 설계될 수 있습니다. 부품은 날카롭게 정의될 수 있으며, 매끄럽거나 질감이 있는 표면을 가질 수 있고, 다양하고 매력적이며 실용적인 마감 처리에 적합합니다 [NADCA 2010].
다이캐스팅으로 생산되는 부품의 품질은 본질적으로 금형에 의해 결정됩니다. 다이캐스팅 금형은 코어와 캐비티로 알려진 두 개의 주형 반쪽으로 구성됩니다. 고정된 상태로 유지되는 금형 부분을 캐비티 하프(또는 커버 다이)라고 하며, 움직일 수 있는 다른 쪽 반쪽을 코어 하프(또는 이젝터 다이)라고 합니다. 두 개의 주형 반쪽이 조립되어 고압으로 용융 금속이 주입됩니다. 응고 후 이 주형 반쪽이 분리되고 주조 부품은 배출 메커니즘의 도움으로 자동으로 배출됩니다. 코어 하프가 움직이는 방향을 파팅 방향이라고 합니다. 언더컷 형상은 파팅 방향 또는 음의 파팅 방향에서 접근할 수 없는 부품 영역입니다. 부품에 언더컷 형상이 있는 경우 일반적으로 사이드 코어가 사용됩니다. 그림 1은 기본 용어와 함께 다이캐스팅 공정을 보여줍니다.
다이캐스팅 금형 설계는 금형 설계자의 방대한 기술적 노하우와 경험을 필요로 하는 복잡하고 시간이 많이 걸리는 공정입니다. 캐비티 수 및 레이아웃 결정, 게이팅 시스템 설계, 다이베이스 설계, 파팅 설계, 수축 설정, 코어 및 캐비티 생성, 배출 설계, 냉각 설계, 사이드 코어 설계 및 표준 부품 설계 등이 확인된 작업입니다 [Fuh et al. 2002]. 이러한 작업은 초기 또는 개념적 금형 설계와 상세 금형 설계의 두 단계로 나눌 수 있습니다. 금형 설계의 개념 단계에서 주형 구성 유형 선택, 캐비티 수 결정 및 레이아웃은 금형 설계의 다른 작업에도 영향을 미치는 주요 작업입니다.
단일 캐비티 금형은 일반적으로 상당히 큰 부품을 위해 설계됩니다. 그러나 다중 캐비티 금형을 설계하는 것이 항상 더 경제적이어서 단일 다이캐스팅 공정 주기에서 더 많은 수의 부품을 생산할 수 있습니다. 금형 설계의 초기 단계에서 단일 캐비티 또는 다중 캐비티 금형을 가질지 결정해야 합니다. 다중 캐비티 금형을 사용하면 생산성을 높이는 것 외에도 제품 비용을 절감할 수 있습니다. Reinbacker [1980]는 캐비티당 비용 기준으로 두 개의 캐비티는 거의 절감 효과가 없으며, 8개의 캐비티는 25% 저렴하고 64개의 캐비티는 60%의 관련 비용 절감 효과가 있다고 제안했습니다.
다이캐스팅 금형의 캐비티 레이아웃을 설계하려면 설계자는 먼저 캐비티 수를 결정해야 합니다. 캐비티 수 결정은 제조 및 기하학적 제한 외에도 시간 및 비용과 관련된 여러 요인에 따라 달라집니다. 이는 다이캐스팅 전문가의 많은 주의를 필요로 하며 시간도 많이 소요됩니다. 캐비티 수가 결정되면 금형 설계에 대한 충분한 지식을 필요로 하는 특정 패턴으로 가능한 한 독창적으로 다이베이스에 배치해야 합니다. 이러한 결정은 함께 금형 설계 및 제조와 관련된 다른 하류 활동을 결정하는 데에도 중요합니다.
4. 연구 요약:
연구 주제의 배경:
다이캐스팅 금형 설계는 전통적으로 인간의 전문 지식과 시행착오 방법에 의존하는 중요한 공정으로, 비용 증가와 생산 시간 지연을 초래합니다. 특히 초기 금형 설계 단계에서의 자동화는 생산성을 향상시키고 리드 타임을 단축하는 데 필수적입니다. 이 단계에서 캐비티 수, 레이아웃 패턴 및 다이베이스 내 배치와 같은 주요 결정은 전체 금형 설계 및 제조 효율성에 큰 영향을 미칩니다. 이러한 중요한 작업을 설계자에게 지원하기 위한 자동화 시스템의 필요성이 있습니다.
이전 연구 현황:
다이캐스팅 금형 설계에 대한 대부분의 이전 연구는 파팅 라인 및 파팅 표면 결정에 중점을 두었으며, 캐비티 수 최적화 및 레이아웃에는 상대적으로 적은 관심이 기울여졌습니다. 다이캐스팅과 유사점을 공유하는 사출 성형을 포함한 캐비티 레이아웃 설계를 위한 기존 시스템에는 종종 다음과 같은 한계가 있었습니다:
- 일부 시스템은 사용자 입력으로 캐비티 수를 요구했습니다 [Hu and Masood 2002].
- 다른 시스템은 데이터베이스에 저장된 표준 캐비티 레이아웃만 사용했습니다 [Low and Lee 2003].
- 캐비티 수 결정은 종종 선택된 기계 [Ravi et al. 1994, Fuh et al. 2002], 기하학적 제약 조건을 고려하지 않은 경험적 관계 [Chan et al. 2003, Wu et al. 2007] 또는 비용 요인만 [Dewhurst and Blum 1989]과 같은 단일 요인을 기반으로 했습니다.
- 캐비티 수 선택을 위해 선택된 기계, 생산 비용, 납기일, 부품 기하학적 제약 조건과 같은 여러 요인을 포괄적으로 고려하는 것이 부족했습니다.
- 레이아웃 패턴 선택은 종종 수동이거나 대칭 유형으로 제한되었습니다.
- 게이팅 시스템 및 사이드 풀에 대한 클리어런스는 이전 시스템에서 적절하게 다루어지지 않았습니다.
- 많은 시스템이 상당한 사용자 상호 작용을 필요로 했고 높은 수준의 자동화가 부족했습니다.
연구 목적:
본 연구는 다이캐스팅 금형의 캐비티 레이아웃을 위한 컴퓨터 지원 설계 시스템을 개발하여 확인된 연구 격차를 해소하는 것을 목표로 합니다. 목표는 다음과 같습니다:
- 다이캐스팅 금형 설계 지식 기반과 다이캐스팅 기계 및 주조 합금 데이터베이스를 활용하는 세 가지 모듈로 구성된 시스템을 개발합니다.
- 기술적, 경제적, 시간적 및 기하학적 제한을 포괄적으로 고려하여 최적의 실행 가능한 캐비티 수를 결정합니다.
- 캐비티 수와 금형 설계 지식을 기반으로 금형의 레이아웃 패턴(원형, 직렬, 대칭)을 자동으로 결정합니다.
- 게이팅 시스템 및 사이드 풀에 필요한 클리어런스를 고려하여 적절한 다이베이스에 개별 캐비티를 배열하고 배치합니다.
- 수동 입력 및 전문가 의존도를 줄이는 보다 자동화된 솔루션을 제공합니다.
핵심 연구:
본 연구의 핵심은 다중 캐비티 다이캐스팅 금형을 위한 컴퓨터 지원 캐비티 레이아웃 설계를 위한 지식 기반 시스템 개발입니다. 이 시스템은 부품의 CAD 파일에서 추출한 기하학적 정보와 사용자가 제공한 데이터를 통합하고, 다이캐스팅 기계 및 재료 데이터베이스와 함께 금형 설계를 위한 전용 지식 기반을 활용하여 캐비티 수 결정, 적절한 레이아웃 패턴 선택 및 이러한 캐비티의 다이베이스 내 배치를 자동화합니다. 이 시스템은 세 가지 주요 모듈로 구성됩니다:
- 캐비티 수 결정: 경제적 실행 가능성, 기술적 허용 가능성(기계 제약), 기하학적 실행 가능성(부품 특징) 및 시간 제한(납기일)을 고려합니다.
- 레이아웃 패턴 선택: 결정된 캐비티 수와 확립된 금형 설계 원칙을 기반으로 원형, 직렬 또는 대칭 패턴 중에서 선택합니다.
- 다이베이스 내 캐비티 배치: 이송 시스템 및 사이드 풀 메커니즘에 필요한 클리어런스를 통합하여 캐비티를 정렬하고 배치합니다.
5. 연구 방법론
연구 설계:
컴퓨터 지원 캐비티 레이아웃 설계를 위한 제안된 시스템은 세 가지 주요 기능 모듈로 구성된 모듈식 접근 방식으로 설계되었습니다:
- 캐비티 수 결정: 이 모듈은 네 가지 기준에 따라 캐비티 수를 계산합니다:
- 납기일 [Ndel]: Menges et al. [2001] 및 Boothroyd et al. [1994]의 관계를 사용하여 다이캐스팅 및 트리밍 공정의 사이클 타임을 기반으로 계산됩니다.
- 부품 제조 비용 [Ncost]: Dewhurst and Blum [1989] 및 Madan et al. [2006]의 공식을 사용하여 최적의 캐비티 수가 결정됩니다.
- 기계 매개변수 [Nmac]: Herman [1996], Boothroyd et al. [1994] 및 Fuh et al. [2002]를 기반으로 형체력(Ncf), 최대 유량(Nfr) 및 기계 크기(Nms)에 의해 결정된 최소 캐비티 수입니다.
- 부품 기하학적 특징 [Ngeo]: 언더컷 및 사이드 풀과 관련된 산업 규칙을 기반으로 한 최대 캐비티 수입니다.
선택된 최종 캐비티 수는 경제적으로 수용 가능하고 기술적으로 허용 가능하며 기하학적으로 실행 가능해야 하며 시간 제약 조건을 충족해야 합니다.
- 캐비티 레이아웃 패턴 선택: 캐비티 수가 결정되면 이 모듈은 다이캐스팅 금형 설계 지식을 사용하여 적절한 레이아웃 패턴(원형, 직렬 또는 대칭)을 선택합니다. 예를 들어, 단일 캐비티는 중앙에 배치됩니다. 다중 캐비티 금형의 경우 기하학적으로 균형 잡힌 패턴이 선호됩니다. 원형 패턴은 종종 홀수 개의 캐비티에 대해 선택되며, 직렬 또는 대칭 패턴은 짝수 개의 캐비티에 사용되며, 대칭 패턴은 2의 거듭제곱에 대해 선호됩니다.
- 캐비티의 방향 설정 및 배치: 이 모듈은 다이베이스에서 캐비티의 방향을 설정하고 배치합니다. 언더컷의 수와 위치, 게이트 위치와 같은 요소를 고려합니다. 이송 시스템(비스킷, 러너, 오버플로 웰) 및 사이드 풀 메커니즘에 대한 클리어런스는 산업 관행 및 문헌 [Boothyard et al. 1994]에서 개발된 데이터베이스를 기반으로 통합됩니다.
이 시스템은 MATLAB 7을 사용하여 구현되었으며, 부품 형상은 SolidWorks 2010에서 모델링된 CAD 파일에서 추출되었습니다.
데이터 수집 및 분석 방법:
이 시스템은 여러 데이터 소스 및 분석 방법을 활용합니다:
- CAD 파일 입력: 부품의 기하학적 정보(투영 면적, 부피, 외곽 크기, 벽 두께, 가장 긴 부품 깊이)가 CAD 파일에서 추출됩니다.
- 사용자 입력: 로트 크기, 납기일, 언더컷 특징(수 및 위치), 재료 선택과 같은 세부 정보에 대한 대화형 입력이 필요합니다.
- 데이터베이스:
- 재료 데이터베이스: 주조 합금의 속성을 포함합니다 (예: 표 1. 대표 주조 합금 재료 데이터베이스 [15]).
- 기계 데이터베이스: 다이캐스팅 기계의 사양을 포함합니다 (예: 표 2. 대표 기계 데이터베이스 [15]).
- 클리어런스 데이터베이스: 캐비티 사이, 다이베이스 가장자리와 캐비티 사이, 이송 시스템 및 사이드 풀 메커니즘에 필요한 최소 클리어런스를 저장합니다.
- 지식 기반: Ngeo 결정, 레이아웃 패턴 선택, 캐비티 방향 설정 및 클리어런스 적용과 같은 의사 결정을 위해 금형 설계 지식 기반이 사용됩니다.
- 분석적 계산: 기존 문헌 및 산업 관행의 공식 및 절차를 사용하여 Ndel, Ncost, Ncf, Nfr 및 Nms를 계산합니다.
- 정보 흐름: 시스템은 흐름도(그림 2 및 그림 5)에 설명된 대로 정보를 처리하여 다양한 소스의 데이터를 통합하여 최종 캐비티 레이아웃 설계를 도출합니다.
연구 주제 및 범위:
이 연구는 다중 캐비티 다이캐스팅 금형의 캐비티 레이아웃에 대한 컴퓨터 지원 설계에 중점을 둡니다. 다루어지는 주요 연구 주제는 다음과 같습니다:
- 경제적(비용), 기술적(기계 용량), 기하학적(언더컷과 같은 부품 특징) 및 시간(납기 요구 사항)과 같은 포괄적인 요소를 고려하여 최적의 실행 가능한 캐비티 수를 자동으로 결정합니다.
- 캐비티 수와 금형 설계 지식을 기반으로 캐비티 레이아웃 패턴(원형, 직렬, 대칭)을 자동으로 선택합니다.
- 이송 시스템 및 사이드 풀 메커니즘에 필요한 클리어런스 제공을 포함하여 다이베이스 내 캐비티의 자동 방향 설정 및 배치.
시스템의 범위는 특히 캐비티 레이아웃을 위한 금형 설계의 초기 단계를 위한 자동화된 도구를 제공하는 것입니다. 수동 전문 지식 및 시행착오에 대한 의존도를 줄여 효율성을 향상시키는 것을 목표로 합니다. 시스템은 현재 파팅 방향이 알려져 있다고 가정합니다.
6. 주요 결과:
주요 결과:
본 연구는 다이캐스팅 금형을 위한 컴퓨터 지원 캐비티 레이아웃 설계 시스템 개발이라는 결과를 도출했습니다.
- 이 시스템은 납기일, 생산 비용, 기계 제약 조건 및 부품 기하학적 제한을 고려하여 캐비티 수를 자동으로 계산할 수 있습니다.
- 결정된 캐비티 수와 금형 설계 지식을 기반으로 적절한 레이아웃 패턴(원형, 직렬 또는 대칭)을 선택합니다.
- 시스템은 금형에 캐비티를 배치하고 레이아웃을 그래픽으로 표시하며, 가능한 대안과 함께 다이베이스 크기를 결정하고 최소 크기의 것을 선택합니다.
- 이 시스템은 언더컷 특징이 있는 부품을 포함하여 여러 다이캐스팅 부품에 대해 성공적으로 테스트되었습니다.
- 언더컷 특징이 있는 예제 부품(그림 6)의 경우, 시스템은 4개의 캐비티를 결정하고 대칭 레이아웃 패턴을 선택했으며 다이베이스 크기를 465mm x 585mm로 계산했습니다(그림 8).
- 언더컷 특징이 없는 예제 부품(그림 7)의 경우, 시스템은 5개의 캐비티를 결정하고 원형 레이아웃 패턴을 선택했으며 다이베이스 크기를 760mm x 760mm로 계산했습니다(그림 9).
- 제안된 시스템은 사용자 친화적이며 기계 및 재료 데이터베이스와 금형 설계 지식 기반을 활용하는 것으로 보고되었습니다.
- 이 시스템은 이전에 사용 가능했던 시스템보다 더 포괄적이며 다이캐스팅을 위한 설계-제조 통합을 향한 한 걸음을 나타냅니다.
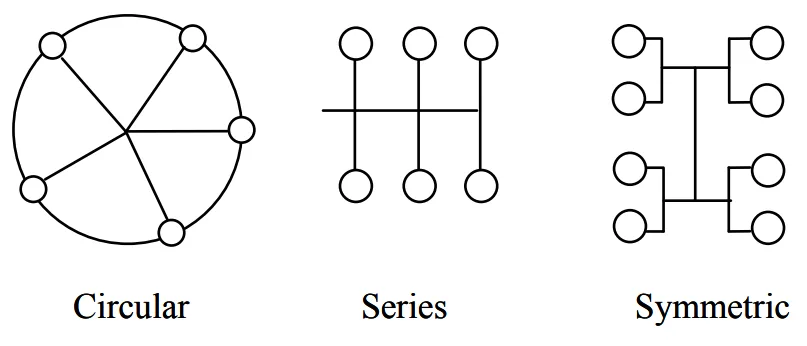
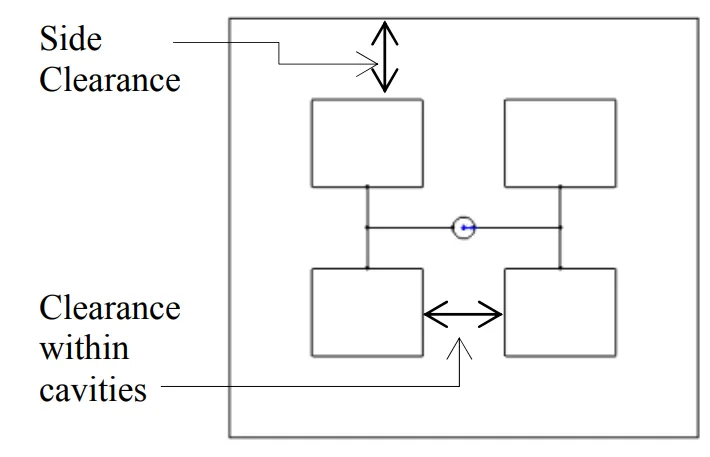
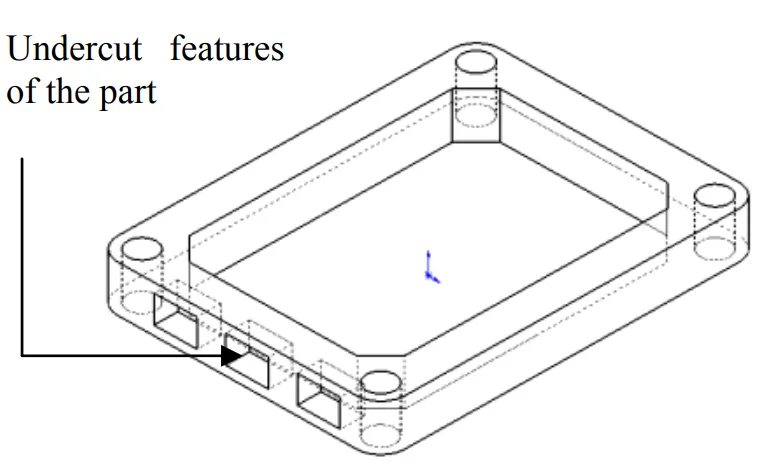
그림 이름 목록:
- Figure 1. Diecasting Process Terminology. (그림 1. 다이캐스팅 공정 용어.)
- Figure 2. Information Flow Diagram for Determination of Number of Cavities for Multi-cavity Die. (그림 2. 다중 캐비티 금형의 캐비티 수 결정을 위한 정보 흐름도.)
- Figure 3. Cavity layout patterns. (그림 3. 캐비티 레이아웃 패턴.)
- Figure 4. Arrangement of clearances in die-base (그림 4. 다이베이스 내 클리어런스 배열)
- Figure 5. Information Flow Diagram for Automatic Cavity Layout Design of Multi-cavity Die. (그림 5. 다중 캐비티 금형의 자동 캐비티 레이아웃 설계를 위한 정보 흐름도.)
- Figure 6. Example Part 1 with Undercut Feature. (그림 6. 언더컷 특징이 있는 예제 부품 1.)
- Figure 7. Example Part 2 without Undercut Feature. (그림 7. 언더컷 특징이 없는 예제 부품 2.)
- Figure 8. Cavity Layout Design for Example Part 1. (그림 8. 예제 부품 1의 캐비티 레이아웃 설계.)
- Figure 9. Cavity Layout Design for Example Part 2. (그림 9. 예제 부품 2의 캐비티 레이아웃 설계.)
7. 결론:
본 논문은 개발된 다이캐스팅용 컴퓨터 지원 캐비티 레이아웃 설계 시스템을 제시합니다. 이 시스템은 다이캐스팅 공정의 설계-제조 통합을 향한 중요한 단계입니다. 금형 설계 단계에서의 캐비티 레이아웃 선택은 다이캐스팅 산업이 직면한 주요 문제로 확인되었습니다. 개발된 시스템은 캐비티 레이아웃 선택에 대한 많은 인간의 전문 지식과 노력을 줄이는 데 도움이 되므로 다이캐스팅 산업에 매우 유용할 것입니다.
제안된 시스템은 납기일, 생산 비용, 기계 제약 조건 및 부품 기하학적 제한을 고려하여 캐비티 수를 계산할 수 있습니다. 더 나은 기하학적 균형을 위해 표준화된 레이아웃 패턴을 사용합니다. 마지막으로, 캐비티의 방향 및 배치는 언더컷의 수 및 위치와 같은 클리어런스 및 기하학적 측면을 고려하여 결정됩니다. 시스템은 캐비티의 그래픽 배열을 출력으로 표시합니다. 사용자 친화적이며 기계, 재료 데이터베이스 및 금형 설계 지식 기반을 사용합니다. 파팅 방향은 이미 사용자에게 알려져 있다고 가정합니다.
향후 연구에는 언더컷 특징 및 해당 위치의 자동 식별, 비표준 캐비티 레이아웃 패턴 사용, 공급 시스템 분석 배치 및 금형 설계의 다른 측면과의 통합이 포함될 수 있습니다.
8. 참고문헌:
- Blum C (1989) Early cost estimation of die cast components. MS Thesis, University of Rhode, Island.
- Boothroyd G, Dewhurst P, Knight W (1994) Product design for manufacture and assembly. Marcel Dekker, New York.
- Chan WM, Yan L, Xiang W, Cheok BT (2003) A 3D CAD knowledge-based assisted injection mould design system. International Journal of Advance Manufacturing Technology 22, 387–395.
- Dewhurst P, Blum C (1989) Supporting analysis for the economic assessment of diecasting in product design. Annual CIRP 38, 161–164.
- Fuh JYH, Wu SH, Lee KS (2002) Development of a semi-automated die casting die design System. Proceedings of the Institution of Mechanical Engineers, Part B: Journal of Engineering Manufacture 216 (12), 1575-1588.
- Fuh JYH, Zhang YF, Nee AYC, Fu MW (2004) Computer-aided injection mold design and manufacture, Marcel Dekker Inc., New York.
- Herman EA (1996) Designing die casting die. North American Die Casting Association (NADCA).
- Herman EA (1996) Gating system design. North American Die Casting Association (NADCA).
- Hu W, Masood S (2002) An intelligent cavity layout design system for injection moulds. International Journal of CAD/CAM, 2(1), 69-75.
- Low MLH, Lee KS (2003) A parametric-controlled cavity layout design system for a plastic injection mould. International Journal of Advance Manufacturing Technology 21, 807–819.
- Low MLH, Lee KS (2003) Application of standardization for initial design of plastic injection moulds. International Journal of Production Research, 41, 2301–2324.
- Madan J, Rao PVM, Kundra TK (2006) System for early cost estimation of die-cast parts. International Journal of Production Research, 45(20), 4823-4847.
- Menges G, Michaeli W, Mohren P (2001) How to Make Injection Molds. 3rd edition, Hanser Gardner Publications, Cincinnati.
- NADCA, North American Die Casting Association, (http://www.diecasting.org/faq) accessed on 2010-10-10.
- Ravi B, Pande SS, Reddy AP (1994) Computer aided design of die casting dies. IIF Transactions, 94(19), 239-245.
- Reinbacker WR (1980) A computer approach to mold quotations, PACTEC V, 5th Pacific Tech. Conference, Los Angeles.
- Woon YK, Lee KS (2004) Development of a die design system for die casting. International Journal of Advance Manufacturing Technology 23, 399-411.
- Wu SH, Fuh JYH, Lee KS (2007) Semi-automated parametric design of gating systems for diecasting die. Computers and Industrial Engineering, 53 (2), 222-232.
- Ye XG, Lee KS, Fuh JYH, Zhang YF, Nee AYC (2000) Automatic initial design of injection mould. International Journal Material Production Technology, 15, 503-517.
9. 저작권:
- 이 자료는 "V. Kumar, J. Madan"의 논문입니다. "System for Computer Aided Cavity Layout Design for Diecasting Dies"를 기반으로 합니다.
- 논문 출처: 논문에 DOI가 제공되지 않음. (게재 학술지: Proceedings of NAMRI/SME, Vol. 39, 2011)
이 자료는 위 논문을 바탕으로 요약되었으며, 상업적 목적의 무단 사용을 금합니다.
Copyright © 2025 CASTMAN. All rights reserved.