본 논문 요약은 다이캐스팅 금형에서 파팅 라인 및 캐비티 수 자동 결정 논문을 기반으로 작성되었으며, 10회 IRAJ 국제 컨퍼런스에서 발표되었습니다.
1. 개요:
- 제목: 다이캐스팅 금형에서 파팅 라인 및 캐비티 수 자동 결정 (AUTOMATIC DETERMINATION OF PARTING LINE AND NUMBER OF CAVITIES IN DIE CASTING DIE)
- 저자: 수닐 쿠마르 (SUNIL KUMAR), 란짓 싱 (RANJIT SINGH), 비제이 쿠마르 (VIJAY KUMAR), 비노드 쿠마르 (VINOD KUMAR)
- 발표 연도: 2013년
- 발표 학술지/학회: 10회 IRAJ 국제 컨퍼런스 (Proceedings of 10th IRAJ International Conference)
- 키워드: 다이캐스팅 (Die-casting), 파팅 라인 (Parting line), 파팅 방향 (Parting direction), GUI, 다중 캐비티 금형 (Multi Cavity Dies), STL 파일 (STL file)
![Fig 2: Dominations in Parting Line [3]](https://castman.co.kr/wp-content/uploads/Fig-2-Dominations-in-Parting-Line-3.webp)
2. 연구 배경:
- 연구 주제의 사회적/학문적 맥락: 다이캐스팅은 복잡한 형상, 높은 정밀도 및 반복성을 가진 엔지니어링 금속 부품 생산에 널리 사용되는 공정입니다. 다이캐스팅 금형 설계는 공정에서 매우 중요하고 시간이 많이 소요되는 단계입니다. 특히 파팅 방향, 파팅 라인, 파팅 면, 캐비티 수와 같은 매개변수 결정은 전문가 지식에 크게 의존하며 종종 반복적이고 수동적인 방식으로 이루어집니다. 이러한 수동적 접근 방식은 다이캐스팅 공정의 설계-제조 통합에 격차를 만듭니다.
- 기존 연구의 한계: 기존 금형 설계 프로세스는 자동화가 부족하여 파팅 라인 및 캐비티 수와 같은 중요한 매개변수에 대해 전문가의 직관과 수동 선택에 의존합니다. 이러한 수동적 접근 방식은 시간이 많이 걸리고 다이캐스팅 공정의 병목 현상이 될 수 있습니다. CAD 모델이 사용되지만 제조 데이터 생성 및 금형 매개변수 결정은 완전히 통합되거나 자동화되지 않았습니다.
- 연구의 필요성: 다이캐스팅 설계를 효율적으로 개선하고 소요 시간을 단축하기 위해서는 주요 금형 설계 매개변수를 자동으로 결정할 수 있는 자동화 시스템이 필요합니다. 특히 다이캐스팅 금형에서 파팅 라인과 캐비티 수를 자동으로 결정하는 것은 설계 프로세스를 크게 향상시키고 수동적인 전문가 중심 방법에 대한 의존도를 줄일 수 있습니다. 이러한 자동화는 다이캐스팅의 설계-제조 통합을 개선하는 데 기여할 것입니다.
3. 연구 목적 및 연구 질문:
- 연구 목적: 본 연구의 주요 목적은 파팅 라인 및 방향, 파팅 면을 자동으로 결정하고 다이캐스팅 금형의 캐비티 수를 계산하는 자동 시스템을 개발하는 것입니다. 이 시스템은 기계 및 제품 데이터를 입력으로 받아 캐비티 수와 파팅 라인 정보를 자동으로 출력하는 것을 목표로 합니다.
- 주요 연구 질문:
- CAD 모델을 입력으로 사용하여 다이캐스팅 금형의 파팅 라인 및 파팅 방향을 결정하는 자동 시스템을 개발할 수 있는가?
- MATLAB을 파팅 라인 및 파팅 면 결정 시스템을 구현하는 데 효과적으로 사용할 수 있는가?
- 다양한 설계 기준 및 입력 매개변수를 기반으로 다이캐스팅 금형의 최적 캐비티 수를 계산하는 자동 시스템을 개발할 수 있는가?
- MATLAB에서 GUI를 구현하여 다이캐스팅 금형 설계를 위한 자동화 시스템의 사용을 용이하게 할 수 있는가?
- 연구 가설:
- 부품의 3D CAD 모델을 분석하여 파팅 라인 및 방향의 자동 결정이 가능하다.
- MATLAB은 파팅 라인 결정 및 캐비티 수 계산을 자동화하기 위한 알고리즘 및 GUI 개발에 효과적으로 사용될 수 있다.
- 자동화 시스템은 수동 계산에 비해 캐비티 수를 결정하는 데 더 일관성 있고 효율적인 방법을 제공할 수 있다.
4. 연구 방법론
- 연구 설계: 본 연구는 MATLAB을 사용하여 자동화 시스템을 개발하는 데 중점을 둔 시스템 개발 접근 방식을 채택합니다. 여기에는 파팅 라인 결정 및 캐비티 수 계산을 위한 알고리즘 개발과 사용자 상호 작용을 위한 GUI 생성이 포함됩니다.
- 데이터 수집 방법: 시스템의 입력 데이터는 STL 파일 형식의 부품 3D CAD 모델과 다이캐스팅 기계 및 제품 데이터로 구성됩니다. CAD 모델은 SolidWorks에서 설계되었습니다. 시스템은 캐비티 수 계산을 위해 생산, 부품, 기계 및 재료 데이터베이스와 관련된 표준 공식 및 설계 기준을 사용합니다.
- 분석 방법:
- 파팅 라인 결정: 시스템은 MATLAB을 사용하여 3D CAD 모델의 STL 파일을 처리합니다. 알고리즘은 부품의 형상을 분석하여 파팅 라인을 식별합니다. 부품의 투영 면적이 최대가 되는 방향이 파팅 방향으로 선택됩니다. 파팅 라인 결정은 코어와 캐비티 몰드 면 사이의 공통 모서리에서 시작됩니다. 파팅 라인 영역은 언더컷 위치와 형상에 따라 선택됩니다.
- 캐비티 수 결정: 시스템은 납기일, 비용, 기계 매개변수, 클램핑 힘 및 최대 유량과 같은 여러 기준에 따라 캐비티 수를 계산합니다. 논문의 공식 (1)~(5)가 이러한 계산에 사용됩니다. 클램핑 힘, 유량 및 기계 크기를 기준으로 계산된 캐비티 수 중에서 최소값이 기계 매개변수 기반 캐비티 수 [Nmac]로 간주됩니다.
- 연구 대상 및 범위: 시스템은 SolidWorks에서 설계하고 STL 파일로 저장된 샘플 3D CAD 부품 모델을 사용하여 테스트되었습니다. 범위는 MATLAB 환경에서 GUI를 사용하여 구현된 다이캐스팅 금형의 파팅 라인 결정 및 캐비티 수 계산 자동화를 포함합니다.
5. 주요 연구 결과:
- 주요 연구 결과:
- 자동 파팅 라인 결정: 개발된 MATLAB 시스템은 3D CAD 모델에 대한 파팅 라인 결정을 성공적으로 자동화합니다. 그림 8과 그림 10은 MATLAB의 결과 창을 보여주며, 샘플 부품에 대해 자동으로 생성된 파팅 라인을 보여줍니다. 시스템은 최대 투영 면적을 덮는 외부 파팅 라인을 식별합니다. 샘플 부품 2 (P2)와 같은 복잡한 부품의 경우 시스템은 주조물의 코어 측에서 파팅 라인을 정확하게 식별합니다.
- 자동 캐비티 수 결정: MATLAB에서 GUI 기반 시스템이 개발되어 캐비티 수를 계산합니다. 시스템은 다양한 기준과 제약 조건을 고려합니다. 그림 11, 12, 13, 14는 다양한 경우에 대한 GUI 창을 보여주며, 시스템이 입력 매개변수를 기반으로 캐비티 수를 계산하는 능력을 보여줍니다.
- 사례 연구: 시스템은 다양한 부품 모델 및 기계 매개변수를 변경하여 다양한 경우로 테스트되었습니다. 표 1은 4가지 경우에 대한 다중 캐비티 금형의 결과를 요약합니다. 예를 들어, 기계 번호 1을 사용하는 부품 번호 1 (사례 1)의 경우 최적 캐비티 수는 2로 결정됩니다. 기계 번호 3을 사용하는 부품 번호 2 (사례 4)의 경우 최적 캐비티 수는 6입니다.
- 통계적/질적 분석 결과: 본 논문은 주로 시스템 개발 및 사례 연구 접근 방식을 제시하며 통계 분석은 포함하지 않습니다. 결과는 파팅 라인 및 캐비티 수 결정을 위한 자동화 시스템의 성공적인 구현 및 시연을 기반으로 질적으로 평가됩니다.
- 데이터 해석: 결과는 개발된 MATLAB 기반 시스템이 다이캐스팅 금형의 파팅 라인 결정 및 캐비티 수 계산을 자동화하는 데 효과적임을 나타냅니다. GUI는 매개변수를 입력하고 결과를 얻기 위한 사용자 친화적인 인터페이스를 제공합니다. 사례 연구는 시스템이 다양한 부품 형상 및 기계 구성에 적용될 수 있음을 보여줍니다.
- 그림 목록:
- Fig 2: Dominations in Parting Line [3]
- Fig 3: Automatic cavity layout design [4]
- Fig 4: Parting line regions (in blue colour) for vertical surfaces
- Fig 5: Parting line (bold black line) for different vertical surface
- Fig 6: Sample part 1 (P1)
- Fig 7: Typical window of solid works containing sample part
- Fig 8: Automatic parting line determined by proposed methodology
- Fig 9: Sample Part 2 (P2)
- Fig 10: Parting line determined for a free form part model
- Fig 11: GUI window case 1
- Fig 12: GUI window case 2
- Fig 13: GUI window case 3
- Fig 14: GUI window case 4
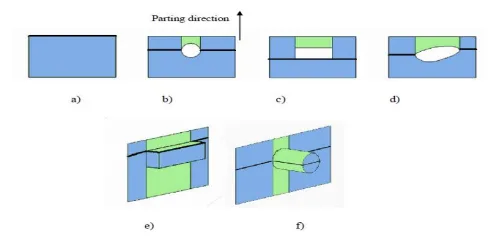
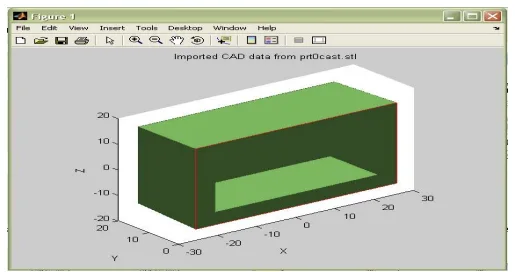
6. 결론 및 논의:
- 주요 결과 요약: 본 연구는 다이캐스팅 부품 모델의 파팅 라인을 결정하고 캐비티 수를 계산하는 자동화 시스템을 성공적으로 개발 및 구현했습니다. MATLAB과 GUI로 구축된 시스템은 3D CAD 모델 (STL 파일) 및 기계/제품 데이터를 입력으로 사용합니다. 파팅 라인을 자동으로 결정하고 다양한 설계 및 제조 제약 조건을 기반으로 최적의 캐비티 수를 계산합니다.
- 연구의 학문적 의의: 본 연구는 중요하고 시간이 많이 소요되는 설계 작업을 자동화하는 방법론과 작동 시스템을 제공함으로써 다이캐스팅 금형 설계 분야에 기여합니다. 이는 금형 설계 프로세스를 향상시키기 위한 전산 방법 및 MATLAB과 같은 소프트웨어 도구의 적용을 보여줍니다. 본 연구는 수동적인 전문가 개입에 대한 의존도를 줄임으로써 다이캐스팅의 설계-제조 통합의 격차를 해소합니다.
- 연구의 실제적 의미: 개발된 시스템은 다이캐스팅 산업에 상당한 실제적 의미를 갖습니다. 파팅 라인 결정 및 캐비티 수 계산을 자동화함으로써 다음과 같은 효과를 얻을 수 있습니다.
- 설계 시간 및 비용 절감.
- 설계 일관성 및 정확성 향상.
- 금형 설계 및 제조의 빠른 처리 시간 가능.
- 캐비티 레이아웃 및 금형 구성에 대한 정보에 입각한 의사 결정을 내리는 데 금형 설계자 지원.
- 연구의 한계: 본 논문에서는 한계에 대해 자세히 논의하지 않습니다. 그러나 잠재적인 한계는 다음과 같습니다.
- 매우 복잡한 부품 형상 또는 비표준 다이캐스팅 공정에 대한 시스템 성능은 추가 조사가 필요할 수 있습니다.
- 시스템의 정확성과 신뢰성은 입력 CAD 모델 및 데이터의 품질과 형식에 따라 달라집니다.
- 본 논문은 실제 산업 환경에서 시스템의 광범위한 검증을 제공하지 않습니다.
7. 향후 후속 연구:
- 후속 연구 방향: 향후 연구는 다음 사항에 초점을 맞출 수 있습니다.
- 더 복잡한 부품 형상 및 다이캐스팅 시나리오를 처리하도록 시스템 기능 확장.
- 원활한 워크플로우를 위해 시스템을 상용 CAD/CAM 소프트웨어와 통합.
- 광범위한 산업 사례 연구 및 사용자 피드백을 통해 시스템 성능 및 이점 검증.
- 금형 성능 및 주조 품질 향상을 위해 파팅 라인 및 캐비티 레이아웃을 더욱 개선하기 위한 최적화 알고리즘 통합.
- 시스템의 자동화 및 의사 결정 기능을 향상시키기 위해 AI 및 머신 러닝 기술의 적용 탐색.
- 추가 탐구가 필요한 영역: 다음과 같은 영역에서 추가 탐구가 필요합니다.
- 더 넓은 범위의 부품 특징 및 복잡성에 대한 파팅 라인 결정 알고리즘의 견고성.
- 입력 매개변수 및 비용 모델의 변화에 대한 캐비티 수 계산의 민감도.
- 실제 산업 응용 분야를 위한 GUI의 사용자 친화성 및 효율성.
8. 참고 문헌:
- [1] R. Khardekar and S. McMains, "Efficient computation of a near-optimal primary parting line", Joint Conference on Geometric and Physical Modeling, 2009, pp. 319-324.
- [2] Z. Zhiqiang, "Automated Parting Methodology for Injection mold", University of Singapore, 2009, pp. 59-69.
- [3] J. Madan, P.V.M. Rao and T.K. Kundra, "Die-casting feature recognition for automated parting direction and parting line determination", Journal of Computing and Information Science in Engineering, 7 (3), 2007, pp. 236-248.
- [4] Y. Xin and Y. Yanto, "Research on method choosing parting line in die NC machining", IEEE Vol. 5, 2011, pp. 2628-2631.
- [5] R. Singh, J. Madan and A. Singh, "Optimal selection of parting line for die-casting", International Journal of Applied Research, Vol.5, No. 17, 2010, pp. 2899-2906.
- [6] V. Kumar, J. Madan and P. Gupta (2010), " Development of a system for automated cavity layout design of die-casting die", Computer Aided Design & Applications, 7(a), 2013, pp. 2083-2107.
- [7] P. Chakraborty and N.V. Reddy, "Automatic determination of parting directions, parting lines and parting surfaces for two-piece permanent molds", Journal of Materials Processing Technology, 209, 2009, pp. 2464-2476.
- [8] V. Kumar, J. Madan and P. Gupta, "System for Computer Aided Cavity Layout Design of Die-Casting Die", International Journal of Production Research, Vol. 50, Issue 18, 2012, pp. 5181-5194.
- [9] W. Hu and S. Masood, "Development of an Intelligent Cavity Layout Design System for Injection Molding Dies", IJE Transactions A: Basics, Vol. 15, No. 4, 2002, pp. 339-348.
- [10] P. Dewhurst and C. Blum, "Supporting Analyses for Economic Assesment of Die-Casting in Product Design", Annals of the CIRP Vol. 38, Issue 1, 1989, pp. 161-164.
9. 저작권:
*본 자료는 수닐 쿠마르 (SUNIL KUMAR), 란짓 싱 (RANJIT SINGH), 비제이 쿠마르 (VIJAY KUMAR), 비노드 쿠마르 (VINOD KUMAR)의 논문 다이캐스팅 금형에서 파팅 라인 및 캐비티 수 자동 결정을 기반으로 합니다.
*논문 출처: https://www.researchgate.net/publication/344146489_AUTOMATIC_DETERMINATION_OF_PARTING_LINE_AND_NUMBER_OF_CAVITIES_IN_DIE_CASTING_DIE (DOI URL은 문서에 명시적으로 제공되지 않아, ResearchGate 링크를 출처로 제공)
본 자료는 상기 논문을 기반으로 요약되었으며, 상업적 목적으로 무단 사용하는 것을 금지합니다.
Copyright © 2025 CASTMAN. All rights reserved.