1. 개요:
- 제목: Cradle-to-Gate Impact Assessment of a High-Pressure Die-Casting Safety-Relevant Automotive Component
- 저자:
- Silvia Cecchel
- Giovanna Cornacchia
- Andrea Panvini
- 발행 연도: 2016
- 발행 학술지/학회: JOM (The Minerals, Metals & Materials Society)
- Keywords:
- Life cycle assessment (LCA)
- High-pressure die casting (HPDC)
- Aluminum
- Automotive component
- Energy analysis
2. 연구 배경:
- 연구 주제의 사회적/학문적 맥락:
- 자동차 부품 경량화는 경제적 및 환경적 이유로 중요성이 증가하고 있음.
- 차량 경량화는 연료 소비 및 배기가스 감소에 직접적인 영향을 미침.
- 알루미늄 합금과 같은 저밀도 재료를 차량에 적용하는 추세가 증가하고 있으며, 기존의 강철 및 주철 부품을 대체하고 있음.
- 자동차 산업에서 알루미늄 합금 사용량이 급증하고 있으며, 이러한 추세는 지속될 것으로 예상됨.
- 알루미늄 자동차 부품은 주로 단조 또는 주조 형태로 생산되며, 특히 고압 다이캐스팅(HPDC)은 대량 생산에 널리 사용되는 공정임.
- HPDC는 경량 알루미늄 부품을 효율적으로 제조하며, 강철 대비 30%~50%의 무게 감소 효과를 제공함.
- 제품의 전 과정(원료 추출부터 폐기까지)을 고려한 LCA 분석을 통해 실제 환경적 이점을 평가해야 함.
- LCA는 제품의 전 과정에서 발생하는 환경적 부담을 연구하는 도구로, 자원 추출, 재료 제조, 부품 사용, 재활용 또는 폐기 단계를 포함함.
- LCA의 중요한 역할 중 하나는 검토 대상 사례의 올바른 친환경 설계를 지원하는 것임.
- 알루미늄 사용으로 차량 무게를 줄이면 연료 소비는 감소하지만, 알루미늄 합금 부품 생산에 더 많은 에너지가 필요할 수 있음.
- 기존 연구의 한계점:
- 기존 자동차 부품 LCA 연구는 많지만, 실제 부품 생산 공정을 상세히 연구한 사례는 부족함.
- Dalquist et al. (16)은 국가 집계 데이터 및 대표 기계를 기반으로 일반적인 정보를 제공하지만, 특정 부품 생산 평가에는 정확도가 낮음.
- Singh et al. (17)은 다이캐스팅 부품의 설계 단계에서 지속 가능성을 평가하는 모델을 개발했지만, 제조 공정의 일부(용융 및 유지)만을 이론적 방정식 기반으로 분석함.
- Gunasegaram et al. (18)은 소형 자동차 부품(컨버터 하우징, 약 3kg)의 알루미늄 및 마그네슘 생산을 비교했지만, 본 연구의 대상 부품(안전 관련 자동차 부품, 약 15kg)에는 적용하기 어려움. 대상 부품은 더 큰 치수, 다른 공정 변수 및 툴링(압력, 속도, 클램핑 힘 등)을 필요로 함.
- 연구의 필요성:
- 알루미늄 HPDC 공정은 에너지 집약적인 제조 단계로 구성되어 단계별 평가가 필요함.
- 자동차 부품의 환경 영향에 대한 정확한 평가를 위해 실제 데이터를 기반으로 한 심층 분석이 필요함.
- 특히 안전 관련 자동차 부품과 같이 중요도가 높은 부품의 환경 영향 평가 연구가 중요함.
3. 연구 목적 및 연구 질문:
- 연구 목적:
- 상용차용 안전 관련 알루미늄 HPDC 부품(서스펜션 크로스 빔) 생산의 전 과정(cradle-to-gate)에 대한 환경 영향 평가.
- 에너지 사용량 측면에서 환경 영향을 평가하는 LCA 모델 개발 및 적용.
- 알루미늄 재활용의 환경적 이점 분석.
- 핵심 연구 질문:
- 알루미늄 HPDC 안전 관련 자동차 부품 생산의 각 단계별 에너지 소비량은 얼마인가?
- 알루미늄 재활용이 전체 에너지 소비량에 미치는 영향은 어느 정도인가?
- 알루미늄 HPDC 부품 생산의 환경적 부담을 줄이기 위한 개선 방안은 무엇인가?
- 연구 가설:
- 알루미늄 HPDC 부품 생산 과정 중 원재료 추출 및 알루미늄 제련 단계에서 에너지 소비량이 가장 클 것이다.
- 알루미늄 재활용은 전체 에너지 소비량을 크게 감소시키는 데 기여할 것이다.
4. 연구 방법론:
- 연구 설계:
- Cradle-to-gate LCA 방법론 적용 (ISO 14040:2006 표준 준수).
- 누적 에너지 사용량 평가 방법 사용.
- 새로운 LCA 모델 개발 및 적용.
- 데이터 수집 방법:
- 자동차 부품 공급 업체와의 협력을 통해 실제 생산 현장의 1차 데이터 수집.
- EAA (European Aluminium Association) 데이터 활용 (원재료 추출 ~ 알루미늄 1차 잉곳 단계).
- 문헌 연구 및 산업 데이터베이스 활용.
- 분석 방법:
- 수집된 데이터를 기반으로 LCA 모델 구축.
- 각 단계별 에너지 소비량 계산 및 분석.
- 알루미늄 재활용 시나리오 분석.
- 에너지 소비량 비교 (재활용 포함 vs. 미포함).
- 연구 대상 및 범위:
- 대상 부품: 상용차용 알루미늄 HPDC 서스펜션 크로스 빔 (안전 관련 부품).
- 기능 단위: HPDC 알루미늄 서스펜션 빔 250개 생산 배치.
- 시스템 경계: Cradle-to-gate (원료 추출, 알루미늄 1차 잉곳 제조, 부품 주조, 가공, 재활용).
- 공정 단계:
- 원료 추출 ~ 알루미늄 1차 잉곳 제조: 보크사이트 채굴, 알루미나 생산 (Bayer 공정), 알루미늄 전해 (Hall-Héroult 공정), 주조 공장.
- 알루미늄 1차 잉곳 ~ 부품 주조: 용융, 유지, 주조 (HPDC).
- 가공: 5축 머시닝.
- 재활용: 알루미늄 스크랩 재활용.
5. 주요 연구 결과:
- 핵심 연구 결과:
- 전체 에너지 소비량 중 알루미늄 1차 생산 단계가 가장 큰 비중을 차지함 (Table I, Fig. 2).
- 부품 주조 단계가 두 번째로 큰 에너지 소비 단계임 (Table I, Fig. 2).
- 가공 단계의 에너지 기여도는 미미함 (Table I, Fig. 2).
- 알루미늄 재활용 단계(EOL)는 전체 에너지 소비량의 약 42%를 회수하는 효과를 보임 (Table I, Fig. 3, Fig. 4).
- 통계적/정성적 분석 결과:
- Table I. Energy by life cycle stages:
- Primary aluminum: 68,211 kWh
- Casting: 15,005 kWh
- Finishing: 800 kWh
- EOL: -47,751 kWh
- Total: 84,016 kWh
- Total EOL: 36,265 kWh
- 알루미늄 1차 생산 단계는 액체 알루미늄 전해 공정과 밀접하게 관련되어 높은 에너지 소비량을 나타냄.
- 부품 주조 단계는 전체 에너지의 약 18%를 차지하며, 이는 주조 공정의 에너지 집약성을 보여줌.
- 알루미늄 재활용은 에너지 회수에 상당한 기여를 함.
- Table I. Energy by life cycle stages:
- 데이터 해석:
- 알루미늄 HPDC 부품의 환경 영향은 주로 알루미늄 1차 생산 단계에서 발생함.
- 주조 공정 또한 에너지 소비량이 높으므로, 공정 효율 개선 노력이 필요함.
- 알루미늄 재활용률을 높이는 것이 환경 영향 감소에 매우 효과적임.
- Figure Name List:
- Fig. 1. Life cycle assessment flow-chart.
- Fig. 2. Energy by life cycle stages without EOL.
- Fig. 3. Energy by life cycle stages with EOL.
- Fig. 4. Total energy comparison.
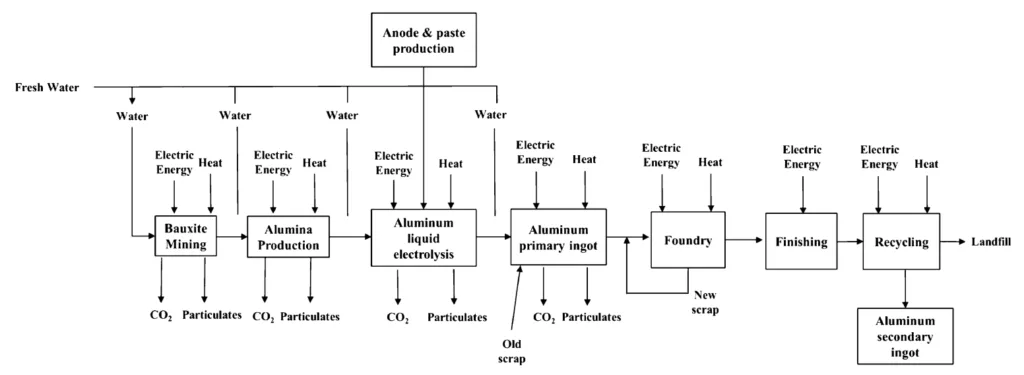
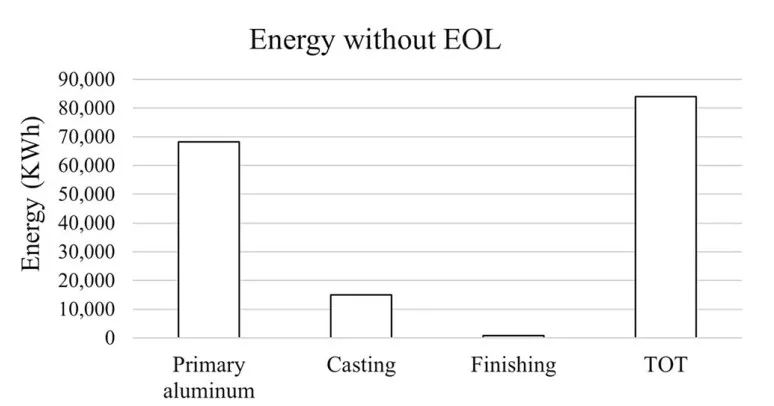
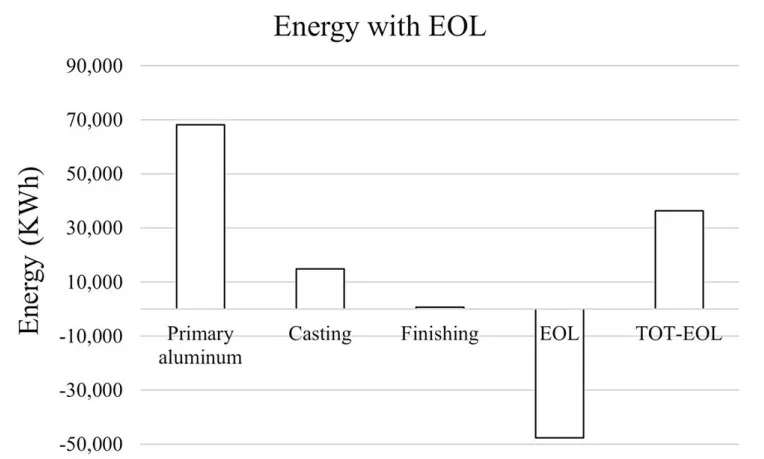
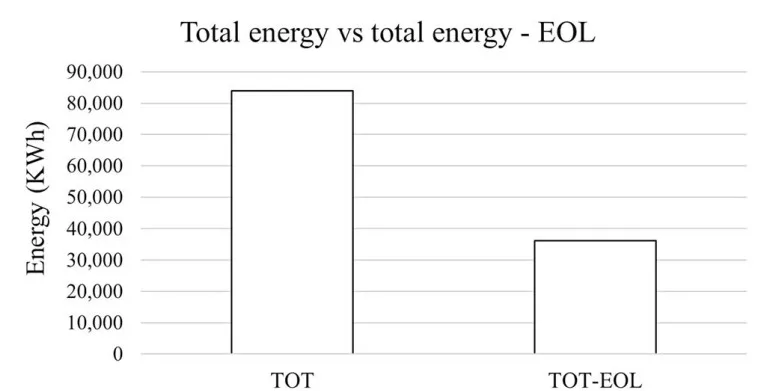
6. 결론 및 논의:
- 주요 결과 요약:
- 본 연구는 상용차용 안전 관련 알루미늄 HPDC 서스펜션 크로스 빔의 cradle-to-gate LCA를 수행하여 에너지 소비량을 분석함.
- 알루미늄 1차 생산 단계가 가장 에너지 집약적이며, 부품 주조 단계가 그 다음으로 에너지 소비량이 큼.
- 가공 단계의 에너지 소비량은 미미함.
- 알루미늄 재활용은 전체 에너지 소비량의 상당 부분을 회수하여 환경적 이점을 제공함.
- 연구의 학술적 의의:
- 알루미늄 HPDC 공정의 환경 영향에 대한 심층적인 분석을 제공함.
- 실제 산업 데이터를 기반으로 한 LCA 모델 개발 및 적용 사례를 제시함.
- 알루미늄 재활용의 중요성을 정량적으로 입증함.
- 실무적 시사점:
- 알루미늄 HPDC 부품 생산의 환경 영향을 줄이기 위해 알루미늄 재활용률을 높이는 것이 중요함.
- 주조 공정의 에너지 효율을 개선하기 위한 기술 개발 및 적용이 필요함.
- 제품 설계 단계에서부터 LCA 결과를 고려하여 친환경적인 설계를 유도해야 함.
- 연구의 한계점:
- 본 연구는 특정 알루미늄 HPDC 부품에 대한 사례 연구이며, 다른 부품이나 공정에 대한 일반화에는 한계가 있을 수 있음.
- LCA 모델의 데이터는 특정 시점 및 기업의 데이터를 기반으로 하므로, 시간 및 지역적 변화에 따라 결과가 달라질 수 있음.
- 본 연구는 에너지 소비량 측면의 환경 영향만을 평가하였으며, 다른 환경 영향 범주(예: 지구 온난화, 자원 고갈 등)는 고려하지 않음.
7. 향후 후속 연구:
- 후속 연구 방향:
- 다양한 종류의 알루미늄 HPDC 부품 및 공정에 대한 LCA 연구 확대.
- 에너지 소비량 외에 다른 환경 영향 범주를 포함하는 LCA 평가 수행.
- 주조 공정의 에너지 효율 개선 기술 개발 및 LCA 기반 평가.
- 알루미늄 재활용 시스템 효율성 향상 방안 연구.
- 타 제조 공법(예: 강철 프레스 성형)과 알루미늄 HPDC 공법의 환경 영향 비교 연구 (논문에서 언급된 future works).
- 추가 탐구가 필요한 영역:
- 알루미늄 HPDC 공정의 최적화 및 에너지 절감 기술.
- 알루미늄 재활용률 향상을 위한 정책 및 기술 개발.
- LCA 방법론의 지속적인 개선 및 데이터베이스 확충.
8. 참고문헌:
- H. Helms and U. Lambrecht, Int. J. LCA (2006). doi:10. 1065/lca2006.07258.
- S. Das, JOM 52, 41 (2000).
- J. Hirsch, Mater. Forum 28, 15 (2004).
- J. Kasai, JSAE Rev. 20, 387 (1999).
- G.S. Cole and A.M. Sherman, Mater. Charact. 35, 3 (1995).
- S.W. Hadley, S. Das, and J.W. Mille, Oak Ridge National Laboratory (2000). doi:10.2172/814613.
- A.A. Luo, A.K. Sachdev and B.R. Powell, China Foundry 7, 463 (2010).
- D.R. Gunasegaram and A. Tharumarajah, Metal. Trans. B 40, 605 (2009).
- J.B. Guine´e, Int. J. Life Cycle Assess. 7, 311 (2002).
- International Standard Organisation (ISO), ISO14040: Environmental Management—Life Cycle Assessment: Principles and Framework (Geneva: ISO, 2006), pp. 1–20.
- J. Green, Aluminum Recycling and Processing for Energy Conservation and Sustainability (Novelty, OH: ASM International, 2007), pp. 1–14.
- H.C. Kim and T.J. Wallington, Environ. Sci. Technol. 47, 6089 (2013).
- H. Kim, C. McMillan, G.A. Keoleian and S.J. Skerlos, J. Ind. Ecol. 14, 929 (2010).
- C. Wagner, J. Provo, and C. Koffler, Comparative Life Cycle assessment of Aluminum and Steel Truck Wheels (Alcoa, 2012). http://www.alcoawheels.com/alcoawheels/north_ america/en/pdf/Alcoa_Comparative_LCA_of_Truck_ Wheels_with_CR_statement.pdf. Accessed 20 Sept 2012.
- C.A. Ungureanu, S. Das and I.S. Jawahir, in Aluminum Alloys Transport, Package, Aerospace. Other Applications, Proceedings Symposium, ed. S.K. Das and W. Yin (Warrendale, PA: TMS, 2007), pp. 11–24.
- S. Dalquist and T. Gutowski, Life Cycle Analysis of Conventional Manufacturing Techniques: Die Casting (Massachusetts Institute of Technology, Paper no. LMPMIT-TGG-03-12-09-2004). http://web.mit.edu/ebm/Publica tions/Die%20Casting%20Dalquist%20Gutowski.pdf. Accessed 8 June 2014.
- R. Singh, C.D. Singh and S. Singh Sidhu, IJMDEBM 1, 21 (2013).
- D.R. Gunasegaram and A. Tharumarajah, Metal. Trans. B 40B, 605 (2009).
- F. Mathieux and D. Brissaud, Resour. Conserv. Recycl. 55, 92 (2010).
- European Aluminium Association, Environmental Profile Report for the European Aluminium Industry (European Aluminum Association, 2013). http://european-aluminium. eu/media/1329/environmental-profile-report-for-the-eur opean-aluminium-industry.pdf. Accessed Apr 2013.
- C. Panseri, Manuale di fonderia dell’alluminio (Milan, IT: Hoelpi, 1966), p. 439.
- S. Nagendra Parashar and R.K. Mittal, in Elements of Manufacturing Processes (New Delhi, IN: Prentice-Hall of India Private Limited, 2006), p. 233.
- H. Bakemeyer, Report No. E-902 (NADCA, Arlington Heights, IL, 2008).
- M. Bertram, M. Hryniuk, G. Kirchner and F. Pruvost, Aluminium Recycling in Europe (Brussels, BL: EAA/OEA Recycling Division), p. 1.
- R. Dhingra and S. Das, J. Clean. Prod. 85, 347 (2014).
9. Copyright:
- 본 자료는 Silvia Cecchel, Giovanna Cornacchia, and Andrea Panvini의 논문: Cradle-to-Gate Impact Assessment of a High-Pressure Die-Casting Safety-Relevant Automotive Component을 기반으로 작성되었습니다.
- 논문 출처: DOI: 10.1007/s11837-016-2046-3
본 자료는 위 논문을 바탕으로 요약 작성되었으며, 상업적 목적으로 무단 사용이 금지됩니다.
Copyright © 2025 CASTMAN. All rights reserved.
Cradle-to-Gate Impact Assessment of a High-Pressure Die-Casting Safety-Relevant Automotive ComponentDownload