본 논문 요약은 Jamee Gray가 캔자스 대학교에 2020년에 제출한 논문 "내연 기관을 위한 금속 적층 제조의 타당성 연구"를 기반으로 작성되었습니다.
1. 개요:
- 제목: 내연 기관을 위한 금속 적층 제조의 타당성 연구 (Feasibility of Metal Additive Manufacturing for Internal Combustion Engines)
- 저자: Jamee Gray
- 발행 연도: 2020년
- 발행 저널/학술 단체: 캔자스 대학교 (석사 학위 논문)
- 키워드: 금속 적층 제조 (metal additive manufacturing), AM, 내연 기관 (internal combustion engines), IC 엔진, LPBF, 경량화 (lightweighting), 역설계 (reverse engineering), 동력계 시험 (dynamometer testing), 기공률 (porosity), AlSi12, Ti-6Al-4V
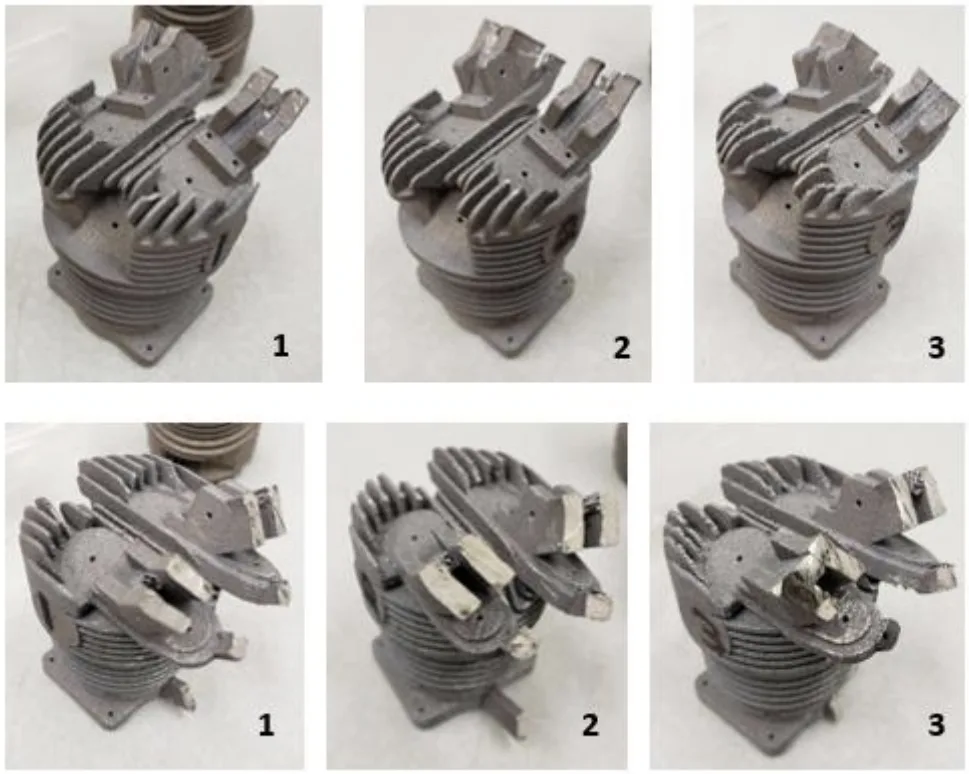
2. 연구 배경:
- 연구 주제의 사회적/학문적 맥락: 금속 적층 제조(AM) 기술의 발전은 자동차 및 방위 산업과 같은 산업 분야에서 혁신과 경쟁력 유지를 위한 기회를 제공합니다. 내연 기관(IC 엔진)에 AM을 구현하는 것은 경량화 및 최적화된 설계를 통해 연비 향상을 위한 잠재적인 방법입니다. 차량 무게를 줄이는 것은 연비 효율성을 개선하고 배기가스 배출을 줄이는 데 매우 중요하며, 파워트레인 부품은 전체 차량 무게에 상당한 기여를 합니다.
- 기존 연구의 한계: AM이 IC 엔진 부품에 적용되는 연구가 진행되고 있지만, 현재 대부분의 응용 분야는 시제품 제작 및 툴링에 국한되어 있으며, 실제 부품 생산은 연구, 모터스포츠 및 고급 차량에 집중되어 있습니다. 틈새 시장을 넘어 더 넓은 응용 분야를 위해 기능성 IC 엔진 부품 생산에 AM의 타당성을 입증할 필요가 있습니다. 기존의 재료 대체 방식의 무게 감량 전략은 비용 및 달성 가능한 무게 감량에 한계가 있습니다.
- 연구의 필요성: 본 연구는 IC 엔진 부품의 실행 가능한 제조 방법으로서 AM을 탐구할 필요성을 다룹니다. 기능성 부품 생산에 레이저 파우더 베드 융합(LPBF) 기술을 사용하는 타당성을 조사하고, 특히 Saito FG-11 엔진의 크랭크케이스와 실린더 헤드의 설계, 제조 및 테스트 프로세스에 중점을 둡니다. 본 연구는 실용적인 엔진 응용 분야에서 AM의 이해와 발전에 기여하는 것을 목표로 합니다.
3. 연구 목적 및 연구 질문:
- 연구 목적: 금속 적층 제조(AM), 특히 레이저 파우더 베드 융합(LPBF) 기술을 사용하여 작동 가능한 내연 기관(IC 엔진) 부품을 생산하는 타당성을 입증하는 것입니다. 본 논문은 AM을 IC 엔진 부품에 대한 실행 가능한 옵션으로 입증하는 것을 목표로 하며, 설계, 제조 및 테스트 프로세스에 중점을 둡니다.
- 주요 연구 질문:
- LPBF를 사용하여 기능성 IC 엔진 부품(크랭크케이스 및 실린더 헤드)을 생산할 수 있는가?
- IC 엔진 부품의 AM 생산을 위한 중요한 공차 및 설계 고려 사항은 무엇인가?
- AM으로 생산된 IC 엔진은 작동 특성 측면에서 기존 엔진과 비교하여 성능이 어떠한가?
- AM으로 생산된 엔진 부품의 재료 특성(기공률, 치수 정확도, 표면 조도)은 어떠하며, 기존 제조 부품과 어떻게 비교되는가?
- 연구 가설:
- LPBF는 소형 IC 엔진용 기능성 크랭크케이스 및 실린더 헤드 부품을 제조하는 데 사용될 수 있다.
- AM으로 생산된 엔진 부품은 기존 부품에 비해 성능이 다소 저하될 수 있지만, 작동 가능한 성능을 나타낼 것이다.
- 기계 가공 및 호닝과 같은 후처리 기술은 필요한 공차 및 표면 조도를 갖춘 기능성 AM 엔진 부품을 달성하는 데 중요하다.
4. 연구 방법론
- 연구 설계: 역설계, AM 제조, 후처리 및 IC 엔진 부품의 성능 테스트를 포함하는 실험 연구. AM 생산 엔진과 기존 엔진 부품의 비교 분석.
- 데이터 수집 방법:
- 역설계: 기존 Saito FG-11 엔진 크랭크케이스 및 실린더 헤드의 측정 및 모델링. 치수 검증을 위한 CT 스캔.
- AM 제조: 크랭크케이스용 Ti-6Al-4V 및 실린더 헤드용 AlSi12를 사용한 LPBF 공정.
- 후처리: 응력 제거, 열처리, 기계 가공 및 실린더 호닝. AM 및 기계 가공 후 기공률 및 치수 정확도를 평가하기 위한 CT 스캔. 프로필로미터를 사용한 표면 조도 측정.
- 엔진 성능 테스트: 동력계 및 프로펠러 테스트를 통해 엔진 속도, 토크, 온도(실린더 헤드, 크랭크케이스, 배기, 흡기), 압력(흡기, 배기), 공기 흐름 및 연료 소비량 측정.
- 분석 방법:
- 치수 분석: Volume Graphics Software를 사용한 공칭/실제 치수 비교를 통해 AM 부품과 CAD 모델 및 주조 부품 비교.
- 기공률 분석: AM 및 주조 부품의 기공률을 정량화하기 위해 Volume Graphics 및 CTAn 소프트웨어를 사용한 CT 데이터 분석.
- 성능 비교: 프로펠러 및 동력계 부하에서 기존 엔진과 AM 수정 엔진 간의 엔진 성능 매개변수(체적 효율, 공기-연료비, 당량비, 토크, 속도, 온도)의 비교 분석. 평균 및 표준 편차를 계산하기 위한 통계 분석.
- 연구 대상 및 범위: Saito FG-11 4행정 10.9cc 엔진. 크랭크케이스 및 실린더 헤드 부품에 초점. 재료 범위: AM 부품용 Ti-6Al-4V 및 AlSi12, 기존 부품용 다이캐스트 알루미늄.
5. 주요 연구 결과:
- 주요 연구 결과:
- Saito FG-11 엔진용 기능성 크랭크케이스 및 실린더 헤드가 LPBF를 사용하여 성공적으로 생산되었습니다.
- AM 엔진은 작동 가능했으며 테스트 중 3.5시간 이상 고장 없이 작동했습니다.
- AM 엔진은 기존 엔진에 비해 성능이 저하되었지만 여전히 기능적이었습니다.
- 성능 저하는 AM 공정 자체가 아닌 조립 변동 또는 불충분한 호닝으로 인한 마찰 증가 때문인 것으로 가설을 세웠습니다.
- AM 부품의 기공률은 정량화되었으며 특정 지지 영역을 제외하고 기계 가공 후 다이캐스트 부품보다 비슷하거나 더 나은 것으로 나타났습니다.
- AM 부품의 치수 정확도는 후처리 후 기능성 엔진 부품에 허용 가능한 범위 내에 있었습니다.
- 통계적/정성적 분석 결과:
- 기공률: AM 부품은 기계 가공 후 다이캐스트 부품보다 비슷하거나 낮은 기공률 수준을 보였습니다. AM 크랭크케이스의 평균 기공률 면적은 0.0027%였으며, 다이캐스트 크랭크케이스는 0.0280%였습니다.
- 치수 정확도: 공칭/실제 치수 분석 결과, 대부분의 중요 기능이 기계 가공 후 ±0.005" 공차 내에 있는 것으로 나타났습니다.
- 엔진 성능: AM 엔진(ACAH 및 ACS 구성)은 일반적으로 프로펠러 및 동력계 테스트 모두에서 기존 엔진(SE)에 비해 낮은 체적 효율 및 토크를 보였습니다. ACS 구성은 프로펠러 테스트에서 SE 및 ACAH에 비해 더 높은 엔진 속도와 배기 온도를 보였습니다.
- 데이터 해석:
- AM 엔진 성능이 약간 저하되었지만, 성공적인 작동 및 내구성은 IC 엔진 부품에 AM의 타당성을 입증했습니다.
- AM 공정은 후처리와 결합하여 엔진 기능에 적합한 치수 정확도와 기공률을 가진 부품을 생산할 수 있습니다.
- 재료 선택 및 설계 최적화는 잠재적인 성능 차이를 완화하고 AM의 이점을 최대한 활용하는 데 중요합니다.
- 그림 목록:
- 그림 3.13: 기존 크랭크케이스 설계 제작 결과 (Original crankcase design build results)
- 그림 3.14: 수정된 크랭크케이스 설계 제작 결과 (Modified crankcase build results)
- 그림 3.15: 실린더 헤드 빌드 플레이트 결과 (Cylinder head build plate result)
- 그림 3.16: AM 실린더 헤드 결과 (AM cylinder head results)
- 그림 3.18: 기존 및 수정된 크랭크케이스 설계를 위한 AM 부품과 CAD 파일의 공칭 실제 치수 분석 (Nominal actual dimensional analysis of AM parts vs. CAD files for original and modified crankcase designs)
- 그림 3.19: AM 부품과 CAD 파일의 실린더 헤드 공칭 실제 치수 분석 (Nominal actual dimensional analysis of AM parts vs. CAD files for cylinder head)
- 그림 3.21: AM 크랭크케이스 1(기존, 왼쪽) 및 크랭크케이스 2(수정, 오른쪽) 설계의 기공률 시각적 표현 (Visual representation of porosity in AM crankcase 1 (original, left) and crankcase 2 (modified, right) designs)
- 그림 3.23: 실린더 헤드의 기공률 시각적 표현 (Visual representation of porosity in cylinder head)
- 그림 3.24: AM 실린더 헤드 2의 기공률 시각적 표현 (Visual representation of porosity in AM cylinder head 2)
- 그림 3.25: AM 크랭크케이스 기존 설계 번호 1의 균열 결함 (Crack defect in AM crankcase original design number 1)
- 그림 3.26: AM 실린더 헤드 번호 2의 균열 결함 (Crack defect in AM cylinder head number 2)
- 그림 5.7: 프로펠러 테스트 중 흡기 공기 흐름 속도 결과 (Intake air flow rate results during prop testing)
- 그림 5.8: 프로펠러 테스트 중 연료 소비량 결과 (Fuel consumption results during prop testing)
- 그림 5.9: 프로펠러 테스트 중 엔진 속도 결과 (Engine speed results during prop testing)
- 그림 5.10: 프로펠러 테스트 중 배기 온도 결과 (Exhaust temperature results during prop testing)
- 그림 5.11: 프로펠러 테스트 중 실린더 헤드 온도 결과 (Cylinder head temperature results during prop testing)
- 그림 5.12: 프로펠러 테스트 중 크랭크케이스 온도 결과 (Crankcase temperature results during prop testing)
- 그림 5.13: 동력계 테스트 중 흡기 공기 흐름 속도 결과 (Air intake flow rates results during dyno testing)
- 그림 5.14: 동력계 테스트 중 연료 소비량 결과 (Fuel consumption results during dyno testing)
- 그림 5.15: 동력계 테스트 중 배기 온도 결과 (Exhaust temperatures results during dyno testing)
- 그림 5.16: 동력계 테스트 중 실린더 헤드 온도 결과 (Cylinder head temperatures results during dyno testing)
- 그림 5.17: 동력계 테스트 중 크랭크케이스 온도 결과 (Crankcase temperatures results during dyno testing)
- 그림 5.18: 동력계 테스트 중 엔진 토크 생산 결과 (Engine torques produced results during dyno testing)
6. 결론 및 논의:
- 주요 결과 요약: 본 연구는 LPBF를 사용하여 기능성 IC 엔진 부품(크랭크케이스 및 실린더 헤드)을 제조하는 타당성을 성공적으로 입증했습니다. AM 엔진은 기존 엔진에 비해 성능이 약간 저하되었지만 3.5시간 이상 고장 없이 작동했습니다. 기계 가공 및 호닝을 포함한 후처리는 기능성 부품을 달성하는 데 매우 중요했습니다.
- 연구의 학문적 의의: 본 논문은 IC 엔진의 AM 응용 분야에 대한 지식 기반을 확장하는 데 기여합니다. 중요한 엔진 부품에 대한 설계 및 제조부터 테스트 및 검증에 이르기까지 전체 AM 프로세스에 대한 자세한 사례 연구를 제공합니다. 본 연구는 까다로운 응용 분야에서 기능성 부품에 AM을 사용할 가능성과 과제를 강조합니다.
- 실용적 의미: 본 연구 결과는 AM이 IC 엔진 부품의 실행 가능한 제조 방법이 될 수 있음을 시사하며, 특히 신속한 시제품 제작, 설계 최적화 또는 군용 UAV 응용 분야와 같이 주문형 부품 교체가 필요한 시나리오에서 유용합니다. LPBF의 확장성은 더 큰 엔진 부품에도 적용될 수 있음을 시사합니다.
- 연구의 한계: 본 연구는 소형 단기통 엔진에 초점을 맞추었습니다. 성능 저하가 관찰되었으며, 원인을 완전히 이해하고 완화하기 위한 추가 연구가 필요합니다. 또한, 연구에서는 수동 조립 및 태핏 조정으로 인한 잠재적인 변동성을 인정하며, 이는 성능 비교에 영향을 미칠 수 있습니다.
7. 향후 후속 연구:
- 후속 연구 방향:
- 토폴로지 최적화를 포함한 설계 최적화를 구현하여 AM 엔진 부품의 무게를 더욱 줄이고 성능을 향상시킵니다.
- 엔진 성능을 이론적 계산과 비교하여 검증하고 설계 수정을 안내하기 위해 시뮬레이션을 수행합니다.
- AM 실린더 헤드에 실린더 라이너를 사용하여 내마모성 및 성능을 향상시킬 가능성을 조사합니다.
- 비교 테스트의 변동성을 최소화하기 위해 부품 교체 및 엔진 설정에 대한 더 엄격한 절차를 개발합니다.
- 엔진 부품 특성 및 성능을 최적화하기 위해 다양한 AM 재료 및 후처리 기술을 탐구합니다.
- 추가 탐구가 필요한 영역:
- AM 엔진의 연소 특성을 더 잘 이해하기 위한 실린더 내 압력 측정.
- AM 엔진 부품의 장기적인 신뢰성을 평가하기 위한 장기간 작동 내구성 테스트.
- AM 재료의 열적 특성을 고려하여 AM 엔진의 냉각 전략 최적화.
- 더 넓은 IC 엔진 분야에 AM의 적용 가능성을 확대하기 위해 다양한 엔진 크기 및 구성 조사.
8. 참고 문헌:
- 참고 문헌은 원본 논문에서 확인할 수 있습니다.
9. 저작권:
- 본 자료는 Jamee Gray의 논문: Feasibility of Metal Additive Manufacturing for Internal Combustion Engines를 기반으로 합니다.
- 논문 출처: [DOI URL - 제공된 문서에 DOI URL이 없으므로, 사용 가능한 경우 DOI URL 삽입]
본 자료는 위 논문을 기반으로 요약되었으며, 상업적 목적으로 무단 사용하는 것을 금지합니다.
Copyright © 2025 CASTMAN. All rights reserved.