본 논문 요약은 ['International Journal Science and Technology']에서 발행한 ['ANALIZE DIE CASTING PROCESS AND STRUCTURE OF MOLDING FOR INTERNAL COMBUSTION ENGINE VEHICLE'] 논문을 기반으로 작성되었습니다.
1. 개요:
- 제목: 내연기관 차량용 다이캐스팅 공정 및 성형 구조 분석 (ANALIZE DIE CASTING PROCESS AND STRUCTURE OF MOLDING FOR INTERNAL COMBUSTION ENGINE VEHICLE)
- 저자: 무하마드 유수프 누르파니 (Muhammad Yusuf Nurfani), 압둘라흐만 아궁 라마단 (Abdulrahman Agung Ramadhan)
- 발행 연도: 2023년
- 발행 저널/학회: 국제 과학 기술 저널 (International Journal Science and Technology, IJST)
- 키워드: 다이캐스팅 (Die Casting), 몰딩 (Molding), 내부 연소 엔진 (Internal Combustion Engine)
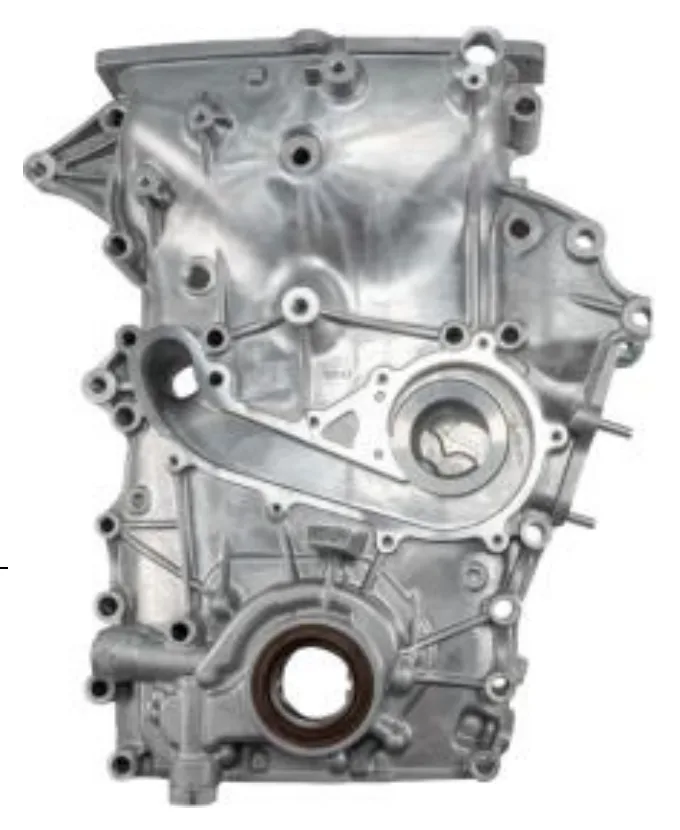
2. 초록 또는 서론
초록:
다이캐스팅은 금속 제품, 특히 차량의 내부 연소 엔진을 제조하는 공정의 일부입니다. 몰딩은 야금 공정 또는 폴리머 공정으로부터 제품을 만드는 구성 요소입니다. 기본적으로 몰딩 공정의 모든 부분은 3가지 공정 조건을 사용합니다. 첫 번째는 공정 생산을 위한 고체 원료이고, 두 번째는 몰딩을 사용하여 제품을 만들기 위한 원료 용융 공정이며, 세 번째는 공정 몰딩 공정 후 완제품 부품을 위한 고체입니다. 본 연구에서는 SUV 용량 2.7L의 내부 연소 엔진 차량용 엔진 몰딩 공정 및 구조를 분석합니다. 몰드 주조는 규사, 수지, 벤토나이트 및 해탄을 기본 원료로 사용하여 사양을 사용합니다. 결과는 기계에서 몰딩까지의 최적 압력이 109675.8 N임을 보여줍니다. 스폿 테스트 확인 결과, 다이캐스팅 공정 후 차량 엔진 10개 시편에서 균열이 발견되지 않았습니다.
키워드: 다이캐스팅 (Die Casting), 몰딩 (Molding), 내부 연소 엔진 (Internal Combustion Engine).
서론:
내부 연소 엔진 (Internal Combustion Engine, ICE)은 차량의 구성 요소 중 하나입니다. 엔진 개발 과정 중 하나가 다이캐스팅입니다. 다이캐스팅은 자동차 산업 개발의 제조 공정입니다. 기본적으로 엔진의 내구성은 설계, 구조 및 개발 시 생산 공정에 영향을 받습니다. [1]. 알루미늄 합금 기어박스 쉘의 다이캐스팅 금형 설계 및 공정 최적화 결과, 벤치 및 도로 주행 테스트 후 기어박스 쉘의 누출 문제 해결을 목표로 수치 시뮬레이션 및 산업용 CT 분석을 통해 원인을 발견하고 누출 해당 위치에 고압 점 냉각을 추가하여 문제를 해결했으며 최적화의 정확성이 검증되었습니다 [2].
자동차 부품용 압력 다이캐스팅 금형 설계 및 분석 결과, 모든 가공을 줄이고 소량 생산에 최적의 공정을 만들 수 있음을 보여줍니다 [3]. 로스트 폼 주조에서 A356 합금 주물의 기공률에 대한 내화 골재 형상의 영향 결과, 주물의 특정 위치에서 결함이 분석되고 광학 현미경을 통해 통계적으로 계산되었음을 보여줍니다.
결론적으로 팽창 흑연과 보크사이트 클링커의 조합은 A356 LFC에서 최고의 품질 주물을 생성합니다. [4]. A356 합금의 미세 구조 및 기계적 특성을 개선하기 위한 로스트 폼 주조 기술에 대한 직접 수냉 공정의 적용 결과, 최대 인장 강도 약 195 ± 3.5 MPa, 연신율 4.45 ± 0.78%, 경도 84 ± 1.77 HB에서 가장 높은 기계적 값이 발견되었습니다.
3. 연구 배경:
연구 주제 배경:
본 논문은 자동차 산업, 특히 내부 연소 엔진 (ICE) 부품 생산에 다이캐스팅을 적용하는 것을 다룹니다. 다이캐스팅은 금속 부품 생산 효율성으로 인해 엔진 개발에 중요한 제조 공정으로 강조됩니다. 엔진의 내구성은 본질적으로 설계, 구조적 무결성 및 개발 중에 사용된 제조 공정과 관련이 있습니다.
기존 연구 현황:
서론에서는 현재 연구의 맥락을 설정하기 위해 이전 연구를 참조합니다.
- [1] Mingyu, Huang, Qian Zhou, Shihua Li의 “알루미늄 합금 기어박스 쉘의 다이캐스팅 금형 설계 및 공정 최적화 (Die Casting Die Design and Process Optimization of Aluminum Alloy Gearbox Shell)”는 수치 시뮬레이션 및 산업용 CT 분석을 사용하여 기어박스 쉘의 누출 문제를 조사하고 고압 점 냉각 최적화를 통해 해결했습니다.
- [2] Y Abdulfatah, T.M Shafii, K.K Dubey, Prof U.K Gupta의 "자동차 부품용 압력 다이캐스팅 금형 설계 및 분석 (Design and Analysis of Pressure Die Casting Die for Automobile Component)"은 압력 다이캐스팅이 가공 요구 사항을 줄일 수 있으며 자동차 부품의 소량 생산에 적합함을 입증했습니다.
- [3] Chi Sun, Zhanyi Cho, Guojun Liu의 “로스트 폼 주조에서 A356 합금 주물의 기공률에 대한 내화 골재 형상의 영향 (Effect of refractory aggregate shape on the porosity of A356 alloy castings in lost Foam Casting)"은 로스트 폼 주조 내에서 A356 합금 주물의 기공률에 대한 내화 골재 형상의 영향을 탐구하여 팽창 흑연과 보크사이트 클링커의 조합이 최적의 주조 품질을 산출한다는 결론을 내렸습니다.
- [4] Ibrahim Tutuk, Serhat Acar, Kerem Altug Guler의 “A356 합금의 미세 구조 및 기계적 특성을 개선하기 위한 로스트 폼 주조 기술에 대한 직접 수냉 공정의 적용 (The Application of the Direct Water-Cooling Process on the Lost-Foam Casting Technique to Improve Microstructural and Mechanical Properties of A356 Alloy)"은 A356 합금의 미세 구조 및 기계적 특성을 향상시키기 위해 로스트 폼 주조에서 직접 수냉을 적용하는 것을 조사하여 향상된 기계적 값을 달성했습니다.
연구의 필요성:
본 연구는 ICE와 같은 중요한 자동차 부품의 제조 공정을 최적화해야 할 필요성이 지속적으로 제기됨에 따라 필요합니다. 다이캐스팅 공정 및 엔진 몰딩의 결과 구조를 분석하는 것은 이러한 부품의 품질과 신뢰성을 보장하는 데 매우 중요합니다. 본 연구는 최적의 압력 설정을 달성하고 다이캐스트 엔진 블록의 구조적 무결성을 검증하는 데 중점을 두어 엔진 제조를 위한 다이캐스팅의 기본 측면을 다룹니다.
4. 연구 목적 및 연구 질문:
연구 목적:
주요 연구 목적은 내부 연소 엔진 차량용 몰딩의 다이캐스팅 공정 및 구조를 분석하는 것입니다. 특히, 본 연구는 2.7L SUV 용량 엔진용 몰드를 개발하고 지정된 재료를 사용하여 다이캐스팅 공정에 대한 최적 압력을 결정하는 것을 목표로 합니다.
주요 연구:
주요 연구는 다음 사항에 중점을 둡니다.
- 결함 없는 엔진 몰드를 만들기 위해 유압 프레스를 사용하여 다이캐스팅에 대한 최적 압력 결정.
- 몰드 및 다이캐스팅에 사용되는 알루미늄 잉곳 (HSN 7061)의 재료 조성 분석.
- ARDROX 9814 침투제를 사용한 비파괴 검사 (Non-Destructive Testing, NDT)를 사용하여 다이캐스트 엔진 블록의 구조적 무결성 평가.
연구 가설:
가설로 명시적으로 언급되지는 않았지만, 본 연구는 최적화된 압력 조건 하에서 HSN 7061 알루미늄 합금과 규사, 벤토나이트, 해탄 및 수지로 만든 몰드를 사용하여 다이캐스팅으로 2.7L ICE용 결함 없는 엔진 블록을 생산하는 타당성을 암묵적으로 테스트합니다. 예상되는 결과는 다이캐스팅 공정 파라미터, 특히 압력을 제어하고 적절한 재료를 사용함으로써 균열이나 구조적 결함이 없는 엔진 블록을 제조할 수 있음을 입증하는 것입니다.
5. 연구 방법론
연구 설계:
본 연구는 엔진 블록을 다이캐스팅하고 이후 구조적 무결성을 평가하는 데 중점을 둔 실험 설계를 채택합니다. 이 공정에는 재료 준비, 몰드 생성, 유압 프레스를 사용한 다이캐스팅, 냉각, 마무리 및 비파괴 검사가 포함됩니다.
자료 수집 방법:
자료 수집 방법은 다음과 같습니다.
- 공정 파라미터 모니터링: 다이캐스팅 공정 중 유압 프레스의 압력 기록 및 제어.
- 육안 검사: 다이캐스트 엔진 블록에 대한 육안 검사를 실시하여 균열, 플래시 및 유동 자국과 같은 육안 결함을 식별합니다.
- 비파괴 검사 (NDT): ARDROX 9814 침투 시험 및 X선 검사를 활용하여 주조 부품의 표면 및 내부 균열 또는 구조적 결함을 감지합니다.
분석 방법:
사용된 분석 방법은 다음과 같습니다.
- 압력 계산: 공식 P = F/A를 사용하여 몰드 치수 및 원하는 단위 면적당 압력을 기준으로 유압 프레스에 필요한 압력을 계산합니다.
- 정성적 결함 분석: 육안 검사 및 NDT 결과를 통해 결함의 존재 여부를 평가합니다. NDT 결과는 균열 감지를 기반으로 "합격" 또는 "불합격"으로 기록됩니다.
연구 대상 및 범위:
- 재료:
- 다이캐스팅 재료: 알루미늄 잉곳 HSN 7061 (조성은 표 2에 자세히 설명되어 있음).
- 몰딩 재료: 규사, 벤토나이트, 해탄 및 수지 (조성은 표 1에 자세히 설명되어 있음).
- 엔진 유형: 2.7L SUV 용량 내부 연소 엔진.
- 장비: TRFD-2000T 유압 프레스.
- 범위: 본 연구는 특정 엔진 블록에 대한 단일 캐비티 몰드의 다이캐스팅 공정 및 구조 분석으로 제한되며, 압력 최적화 및 결함 감지에 중점을 둡니다.
6. 주요 연구 결과:
주요 연구 결과:
- 최적 압력: 유압 프레스에 대한 계산된 최적 압력은 109675.8 N으로 결정되었습니다.
- 성공적인 몰드 생성: 규사, 벤토나이트 및 해탄을 사용한 몰드 가공은 결함 없이 계산된 압력에서 유압 프레스를 사용하여 성공적으로 완료되었습니다.
- 결함 없는 다이캐스팅: 400°C 이상의 온도에서 알루미늄 잉곳 HSN 7061을 사용한 다이캐스팅은 균열, 플래시 또는 유동 자국과 같은 육안 결함이 없는 엔진 블록을 생성했습니다.
- NDT 확인: 비파괴 검사 (NDT)에서 ARDROX 9814를 사용하여 10개의 시편 엔진 블록을 검사한 결과 다이캐스팅 공정 후 균열이나 구조적 문제가 없는 것으로 나타났습니다 (표 4).
제시된 데이터 분석:
- 재료 조성 (표 1 및 2): 표 1은 규사 (3톤), 벤토나이트 (20kg), 해탄 (8.2kg) 및 물 (35L)을 포함한 몰드의 재료 조성을 자세히 설명합니다. 표 2는 알루미늄 80-95% 및 기타 원소 (실리콘, 아연, 철, 망간 및 마그네슘)가 더 작은 비율 (0.1-2%)로 포함된 알루미늄 잉곳 HSN 7061의 조성을 명시합니다.
- 유압 프레스 사양 (표 3): 표 3은 400mm 슬라이드 스트로크, 8-15mm/s의 작동 속도 및 35톤의 이젝팅 힘을 포함하여 사용된 Wodda TRFD-2000T 유압 프레스의 사양을 간략하게 설명합니다.
- NDT 결과 (표 4): 표 4는 10개 샘플에 대한 NDT 결과를 제시하며, 모두 균열 테스트에서 "합격"하여 검사 공정 후 균열 문제가 감지되지 않았음을 나타냅니다.
- 그림: 그림 1은 연구 방법론 순서도를 보여줍니다. 그림 2는 몰딩 재료 (규사, 벤토나이트, 해탄)를 보여줍니다. 그림 3은 알루미늄 잉곳을 보여줍니다. 그림 4는 유압 프레스를 보여줍니다. 그림 5는 몰드 공정 및 다이캐스팅을 묘사합니다. 그림 6은 내부 연소 엔진 블록 2.7L를 제시합니다. 그림 7은 NDT 공정 측정을 보여줍니다. 그림 8은 엔진 2.7L의 구조를 보여줍니다.
그림 목록:
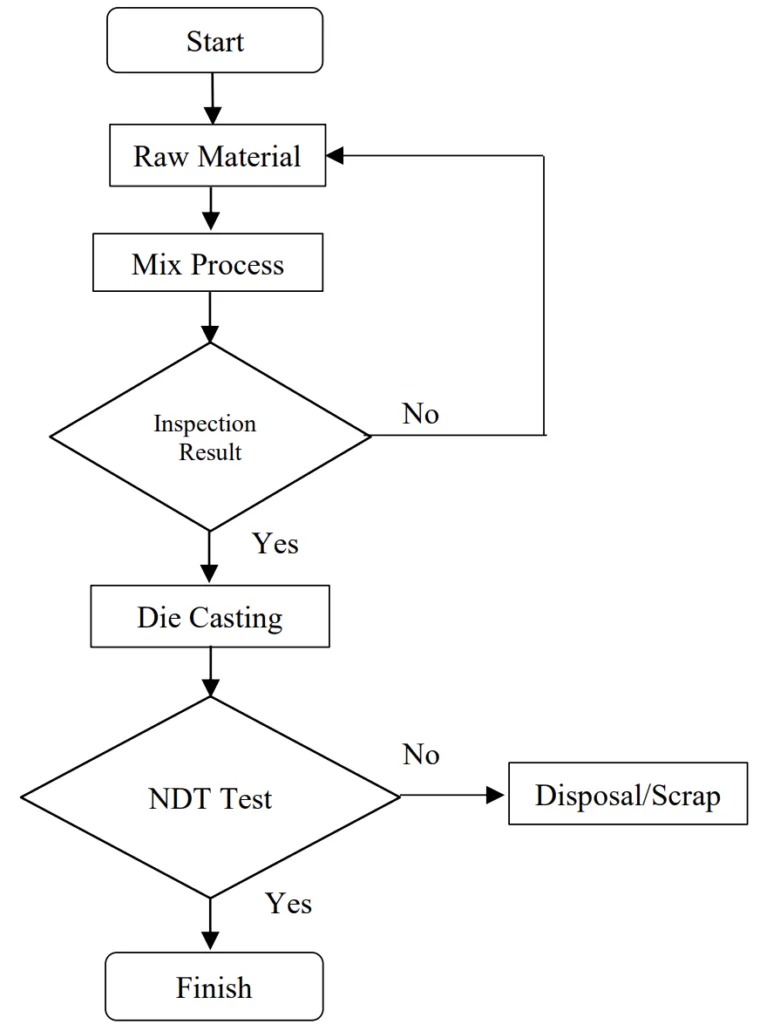
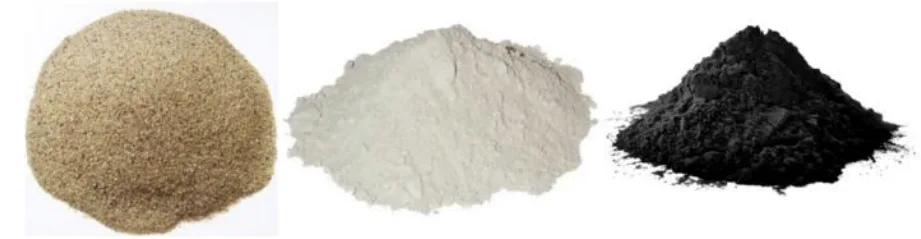
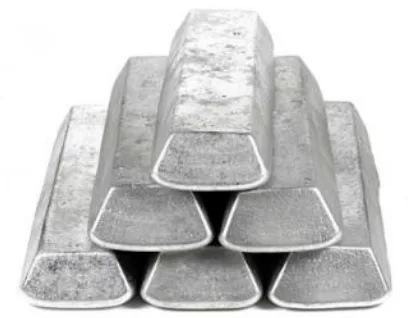
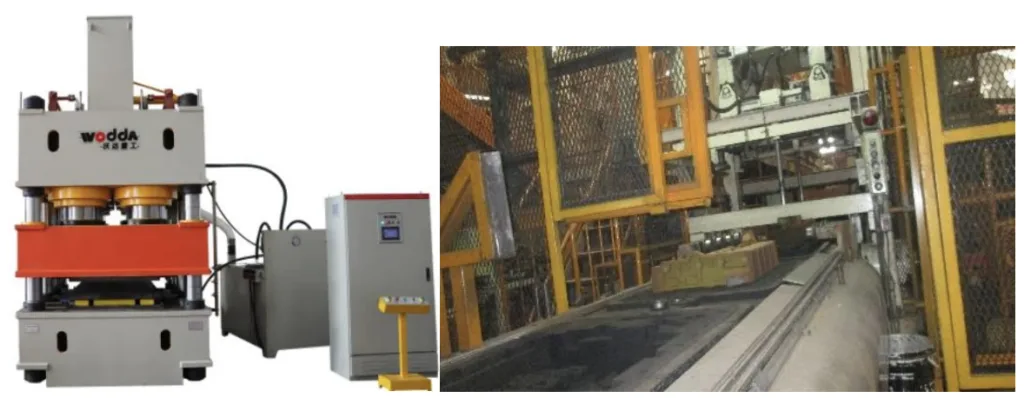
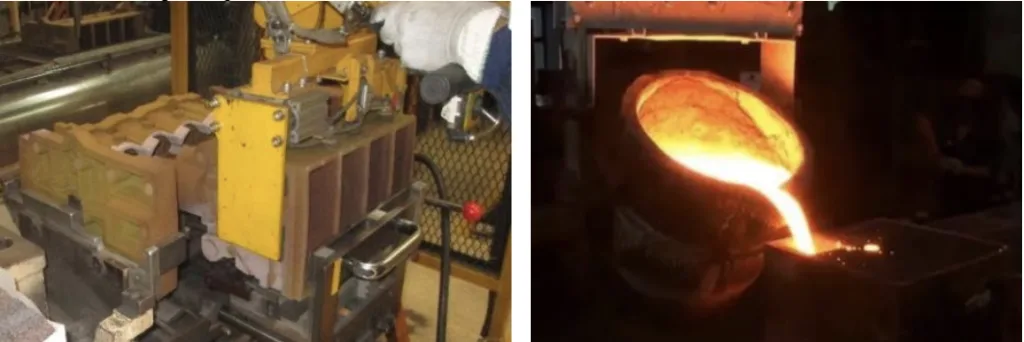
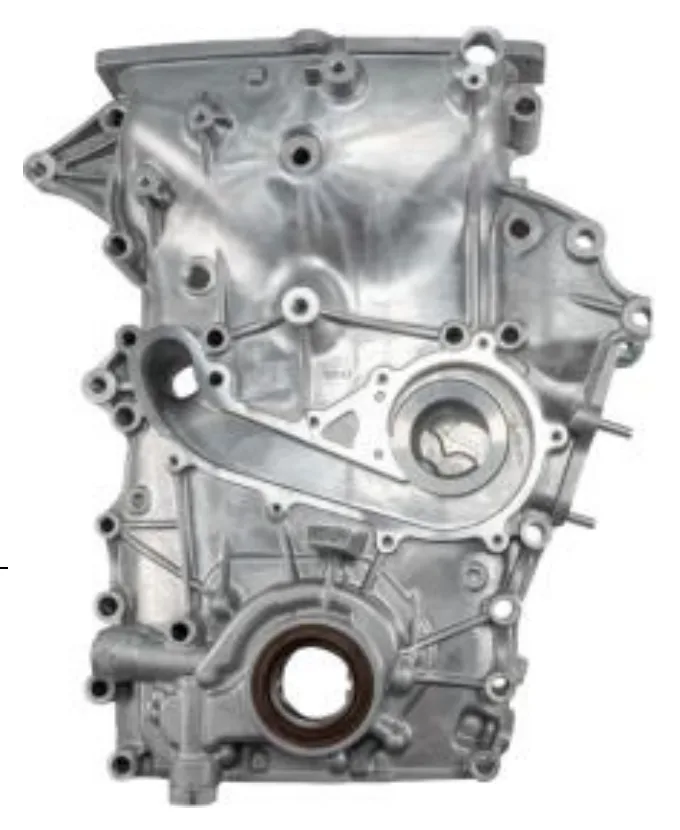
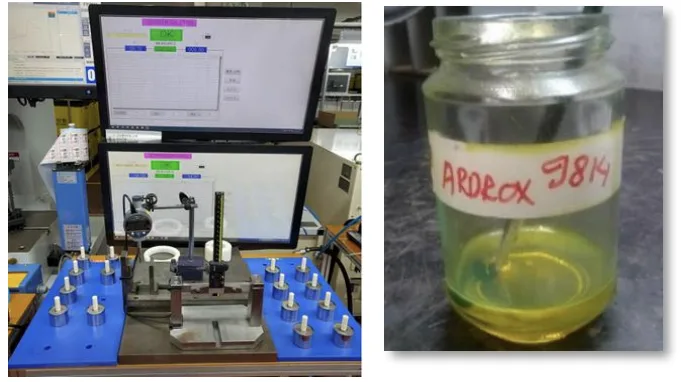
- 그림 1. 연구 방법 (Research Methods)
- 그림 2. 몰딩 재료 (규사, 벤토나이트, 해탄) (Material of Molding (Silica Sand, Bentonite, Sea Coal))
- 그림 3. 알루미늄 잉곳 (Aluminum Ingots)
- 그림 4. 유압 프레스 (Hydraulic Press)
- 그림 5. 몰드 공정 및 다이캐스팅 (Mold Process and Die Casting)
- 그림 6. 내부 연소 엔진 블록 2.7L (Internal Combustion Engine Block 2.7L)
- 그림 7. NDT 공정 측정 (NDT Process Measurement)
- 그림 8. 엔진 2.7L의 구조 (Structure of Engine 2.7L)
7. 결론:
주요 결과 요약:
본 연구는 알루미늄 잉곳 HSN 7061과 단일 캐비티 몰드를 사용한 다이캐스팅으로 2.7L 내부 연소 엔진 블록을 생산하는 타당성을 성공적으로 입증했습니다. 유압 프레스에서 최적화된 109675.8 N의 압력은 결함 없는 몰드 생성과 후속 다이캐스팅을 용이하게 했습니다. 육안 검사 및 비파괴 검사 (NDT) 모두 생산된 엔진 블록에서 균열 및 구조적 문제가 없음을 확인하여 높은 수준의 주조 품질을 나타냅니다.
연구의 학문적 의의:
본 연구는 복잡한 엔진 부품 제조에 다이캐스팅을 적용하는 것에 대한 경험적 검증을 제공함으로써 다이캐스팅 기술 분야에 기여합니다. 자동차 제조의 유사한 다이캐스팅 응용 분야에 참조할 수 있는 압력 최적화 및 재료 선택 (HSN 7061 알루미늄 합금 및 지정된 몰드 재료)에 대한 특정 파라미터를 제공합니다.
실용적 의미:
본 연구 결과는 다이캐스팅을 사용한 내구성 있는 엔진 블록의 대량 생산에 실용적인 의미를 갖습니다. 본 연구는 결정된 압력 설정 및 재료 사양을 준수함으로써 제조업체가 다이캐스트 엔진 부품에서 일관된 품질을 달성하고 결함을 최소화하여 생산 효율성과 제품 신뢰성을 향상시킬 수 있음을 시사합니다. 알루미늄 합금의 사용은 또한 차량 성능 및 연비에 유익한 더 가벼운 엔진 무게에 기여합니다.
연구의 한계 및 향후 연구 분야:
본 연구는 단일 엔진 블록 설계 (2.7L ICE)와 특정 재료 및 장비 세트로 제한됩니다. 향후 연구에서는 다음 사항을 탐구할 수 있습니다.
- 이러한 연구 결과의 다양한 엔진 크기 및 설계로의 확장성.
- 작동 조건에서 다이캐스트 엔진 블록의 장기적인 내구성 및 성능 테스트.
- 주조 품질 및 효율성을 더욱 향상시키기 위해 압력 외에 온도 제어, 사출 속도 및 냉각 속도와 같은 다른 다이캐스팅 파라미터의 최적화.
- 엔진 블록 다이캐스팅에 잠재적으로 우수한 조합을 식별하기 위한 다른 알루미늄 합금 및 몰드 재료와의 비교 연구.
8. 참고 문헌:
[1] Mingyu, Huang, Qian Zhou, Shihua Li “Die Casting Die Design and Process Optimization of Aluminum Alloy Gearbox Shell”, MDPI Journal, Vol. 14, 4 June Page 1-12, 2021
[2] Y Abdulfatah, T.M Shafii, K.K Dubey, Prof U.K Gupta "Design and Analysis of Pressure Die Casting Die for Automobile Component", Global Journal Researches in Engineering a Mechanical and Mechainc Engineering, Vol. 16, 10 November Page 01-07, 2016.
[3] Chi Sun, Zhanyi Cho, Guojun Liu, “Effect of refractory aggregate shape on the porosity of A356 alloy castings in lost Foam Casting", Springer, Vol 6, 17 November, Page 1-9, 2023.
[4] Ibrahim Tutuk, Serhat Acar, Kerem Altug Guler, “The Application of the Direct Water-Cooling Process on the Lost-Foam Casting Technique to Improve Microstructural and Mechanical Properties of A356 Alloy" Springer, Vol 1, 06 January, Page 1-12s, 2023.
[5] Alexandra Chesa " Die Casting Technology – Present and future in Automotive Applications", Institute of Automotive Engineering, June. Page 1-141, 2019
9. 저작권:
- 본 자료는 "무하마드 유수프 누르파니 (Muhammad Yusuf Nurfani) 및 압둘라흐만 아궁 라마단 (Abdulrahman Agung Ramadhan)"의 논문: "내부 연소 엔진 차량용 몰딩의 다이캐스팅 공정 및 구조 분석 (ANALIZE DIE CASTING PROCESS AND STRUCTURE OF MOLDING FOR INTERNAL COMBUSTION ENGINE VEHICLE)"을 기반으로 합니다.
- 논문 출처: https://doi.org/10.56127/ijst.v2i3.1102
본 자료는 상기 논문을 기반으로 요약되었으며, 상업적 목적으로 무단 사용하는 것을 금지합니다.
Copyright © 2025 CASTMAN. All rights reserved.